UBS Axcera 840A 10,000-watt UHF solid state television transmitter User Manual Chapter 4
UBS-Axcera 10,000-watt UHF solid state television transmitter Chapter 4
Contents
Chapter 4
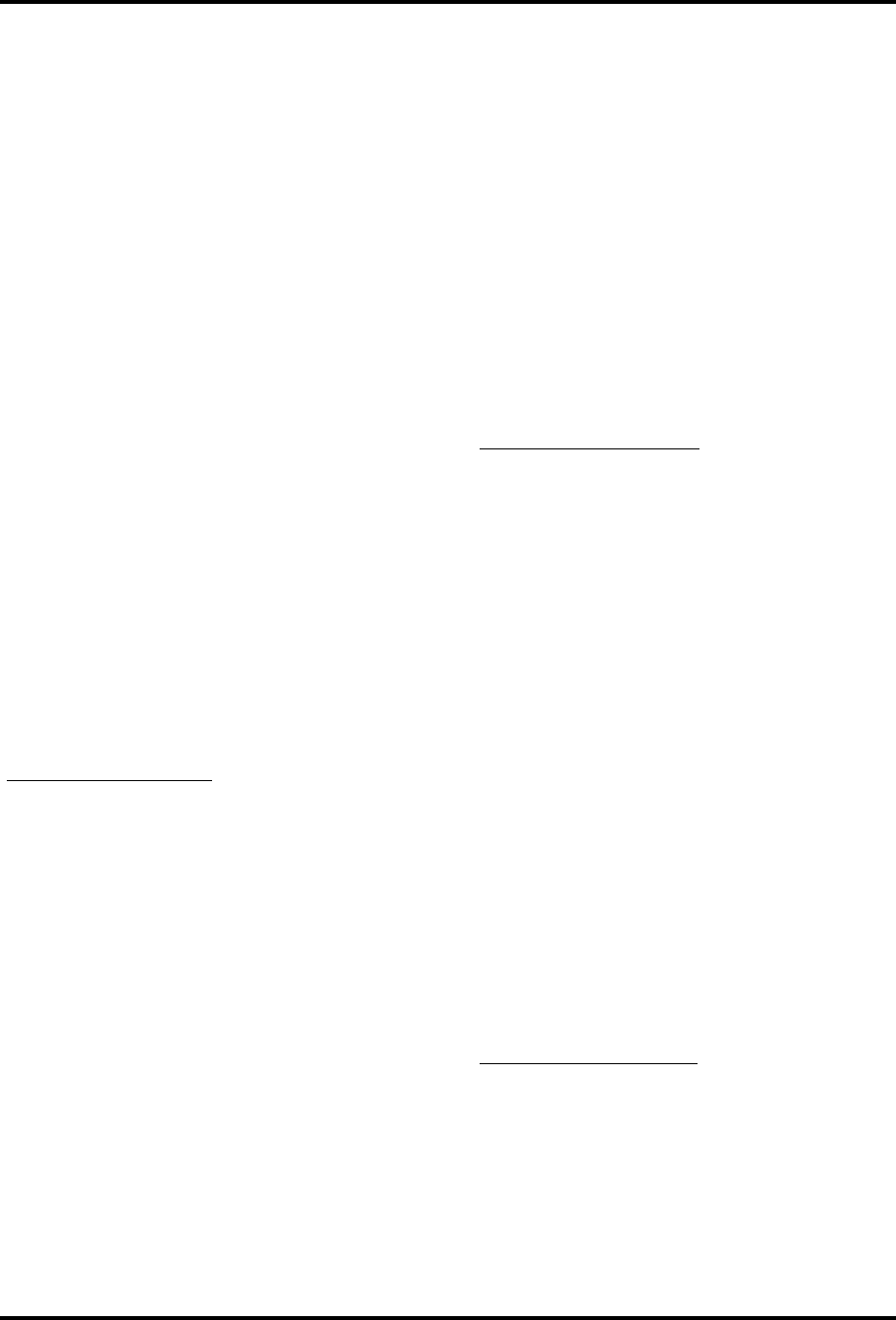
10-kW UHF Transmitter with Chapter 4, Circuit
Feedforward Drive Descriptions
840A, Rev. 0 4-1
Chapter 4
Circuit Descriptions
4.1. (A1) Dual 250-Watt
Driver/Amplifier Assembly
(1094334; Appendix A)
4.1.1 (A1-A4) UHF Exciter Tray
(1094019; Appendix A)
4.1.1.1 (A4) Aural IF Synthesizer Board,
4.5 MHz (1265-1303; Appendix B)
The aural IF synthesizer board amplifies
each of the three possible audio inputs
and the amplifier circuits that supply the
single audio output. The balanced audio
or the composite audio input is connected
to the board while the subcarrier audio
(SCA) input can be connected at the
same time as either of the other two
inputs. The board has the 4.5-MHz
voltage-controlled oscillator (VCO) and
the aural modulation circuitry that
produces the modulated 4.5-MHz output.
The board also contains a phase lock loop
(PLL) circuit that maintains the precise
4.5-MHz separation between the aural
(41.25 MHz) and the visual (45.75 MHz)
IF frequencies.
Balanced Audio Input
The first of the three possible baseband
inputs to the board is a 600Ω-balanced
audio input (+10 dBm) that enters
through jack J2, pins 1 (+), 2 (GND), and
3 (-), and is buffered by U1B and U1C.
Diodes CR1 to CR4 protect the input
stages of U1B and U1C if an excessive
signal level is present on the input leads
of jack J2. The outputs of U1B and U1C
are applied to differential amplifier U1A;
U1A eliminates the common mode
signals (hum) on its input leads. A
pre-emphasis of 75 ms is provided by
R11, C11, and R10 and can be eliminated
by removing jumper W5 on J5. The signal
is then applied to amplifier U1D whose
gain is controlled by jumper W3 on J11.
Jumper W3 on jack J11 is positioned
according to the input level of the audio
signal (0 or +10 dBm). If the input level
is approximately 0 dBm, the mini-jumper
should be in the high gain position
between pins 1 and 2 of jack J11. If the
input level is approximately +10 dBm,
the mini-jumper should be in low gain
position between pins 2 and 3 of jack
J11. The balanced audio is then
connected to buffer amplifier U2A whose
input level is determined by the setting of
balanced audio gain pot R13. The output
of the amplifier stage is wired to the
summing point at U2D, pin 13.
Composite Audio Input
The second possible audio input to the
board is the composite audio (stereo)
input at BNC jacks J3 and J13. The two
jacks are loop-through connected; as a
result, the audio can be used in another
application by connecting the unused
jack and removing W4 from J12. Jumper
W4 on jack J12 provides a 75Ω-input
impedance when the jumper is between
pins 1 and 2 of jack J12 and a high
impedance when it is between pins 2 and
3. Diodes CR9 to CR12 protect the input
stages of U6A and U6B if an excessive
signal level is applied to the board. The
outputs of U6A and U6B are applied to
differential amplifier U2C, which
eliminates common mode signals (hum)
on its input leads. The composite input
signal is then applied to amplifier U2B;
the gain of this amplifier is controlled by
composite audio gain pot R17. The
composite audio signal is connected to
the summing point at U2D, pin 13.
Subcarrier Audio Input
The third possible input to the board is
the SCA input at BNC jack J4. The SCA
input has an input impedance of 75Ω that
can be eliminated by removing jumper
W2 from pins 1 and 2 of J14. The SCA
input is bandpass filtered by C66, C14,
R22, C15, C67, and R23 and is fed to
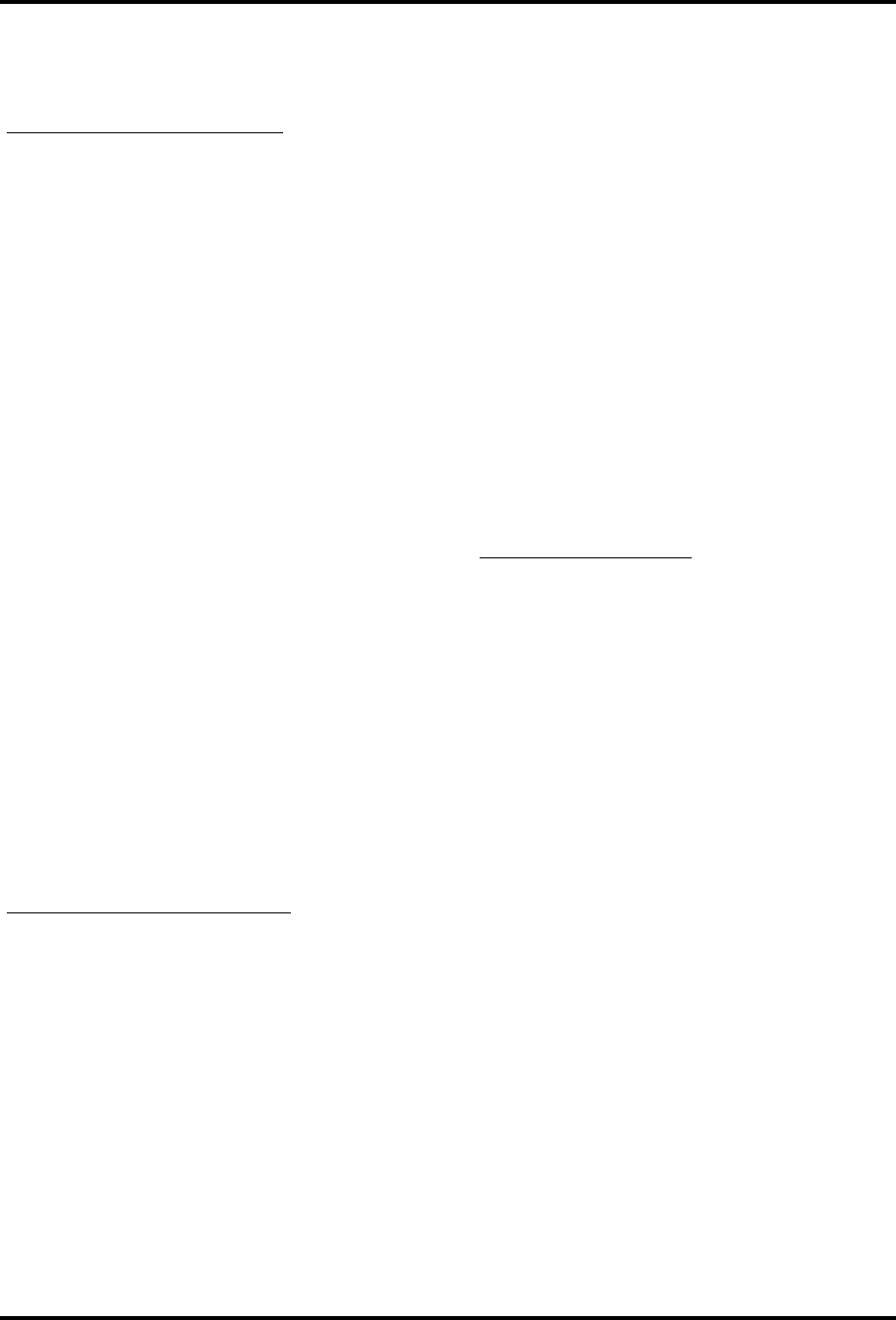
10-kW UHF Transmitter with Chapter 4, Circuit
Feedforward Drive Descriptions
840A, Rev. 0 4-2
buffer amplifier U3A. The amplified signal
is then applied though SCA gain pot R24
to the summing point at pin 13 of U2D.
Audio Modulation of the VCO
The balanced audio, or the composite
audio and/or the SCA-buffered audio
signals, are fed to the common junction
of resistors R14, R20, and R27 that
connect to pin 13 of amplifier U2D. The
output audio signal at pin 14 of U2D is
typically .8 Vpk-pk at a ±25-kHz
deviation for balanced or .8 Vpk-pk at
±75-kHz deviation for composite as
measured at TP1. This signal is applied to
VCO U10. A sample of the deviation level
is amplified, detected by U7A and U7B,
and connected to J10 on the board. This
audio-deviation level is connected to the
front panel meter through the transmitter
control board.
The audio is connected to CR13 to CR16;
these are varactor diodes that frequency
modulate the audio signal onto the
generated 4.5-MHz signal in U10. U10 is
the 4.5-MHz VCO that generates the 4.5-
MHz continuous wave (CW) signal. The
output frequency of this signal is
maintained and controlled by the
correction voltage output of U5 PLL IC.
The audio-modulated, 4.5-MHz signal is
fed to amplifiers U11A and U11B. The
output of U11B is connected to the 4.5-
MHz output jacks at J7 and J8.
Phase Lock Loop (PLL) Circuit
A sample of the signal from the 4.5-MHz
aural VCO at the output of U11A is
applied to PLL IC U5 at the Fin
connection. In U5, the signal is divided
down to 50 kHz and is compared to a 50-
kHz reference signal. The reference
signal is a divided-down sample of the
visual IF, 45.75-MHz signal that is
applied to the oscillator-in connection on
the PLL chip through jack J6 on the
board. These two 50-kHz signals are
compared in the IC and the fV, and fR is
applied to the differential amplifier U3B.
The output of U3B is fed back through
CR17 to the 4.5-MHz VCO IC U10; this
sets up a PLL circuit. The 4.5-MHz VCO
will maintain the extremely accurate 4.5-
MHz separation between the visual and
aural IF signals; any change in frequency
will be corrected by the AFC error
voltage.
PLL chip U5 also contains an internal lock
detector that indicates the status of the
PLL circuit. When U5 is in a "locked"
state, pin 28 goes high and causes the
green LED DS1 to illuminate. If the 4.5-
MHz VCO and the 45.75-MHz oscillator
become "unlocked," out of the capture
range of the PLL circuit, pin 28 of U5 will
go to a logic low and cause the red LED
DS2 to light. A mute output signal from
Q3 (unlock mute) will be applied to jack
J9. This mute is connected to the
transmitter control board.
Voltage Requirements
The ±12 VDC needed for the operation of
the board enters through jack J1. The
+12 VDC is connected to J1-3 and
filtered by L2, C3, and C4 before it is
connected to the rest of the board. The -
12 VDC is connected to J1-5 and filtered
by L1, C1, and C2 before it is connected
to the rest of the board. +12 VDC is
connected to U8 and U9; these are 5-volt
regulator ICs that provide the voltage to
the U10 and U5 ICs.
4.1.1.2 (A5) Sync Tip Clamp/Modulator
Board (1265-1302; Appendix B)
The sync tip clamp/modulator board can
be divided into five circuits: the main
video circuit, the sync tip clamp circuit,
the visual modulator circuit, the aural IF
mixer circuit, and the diplexer circuit.
The sync tip clamp/modulator board
takes the baseband video or 4.5-MHz
composite input that is connected to the
video input jack (either J1 or J2, which
are loop-through connected), and
produces a modulated visual IF + aural
IF output at output jack J20 on the
board. The clamp portion of the board
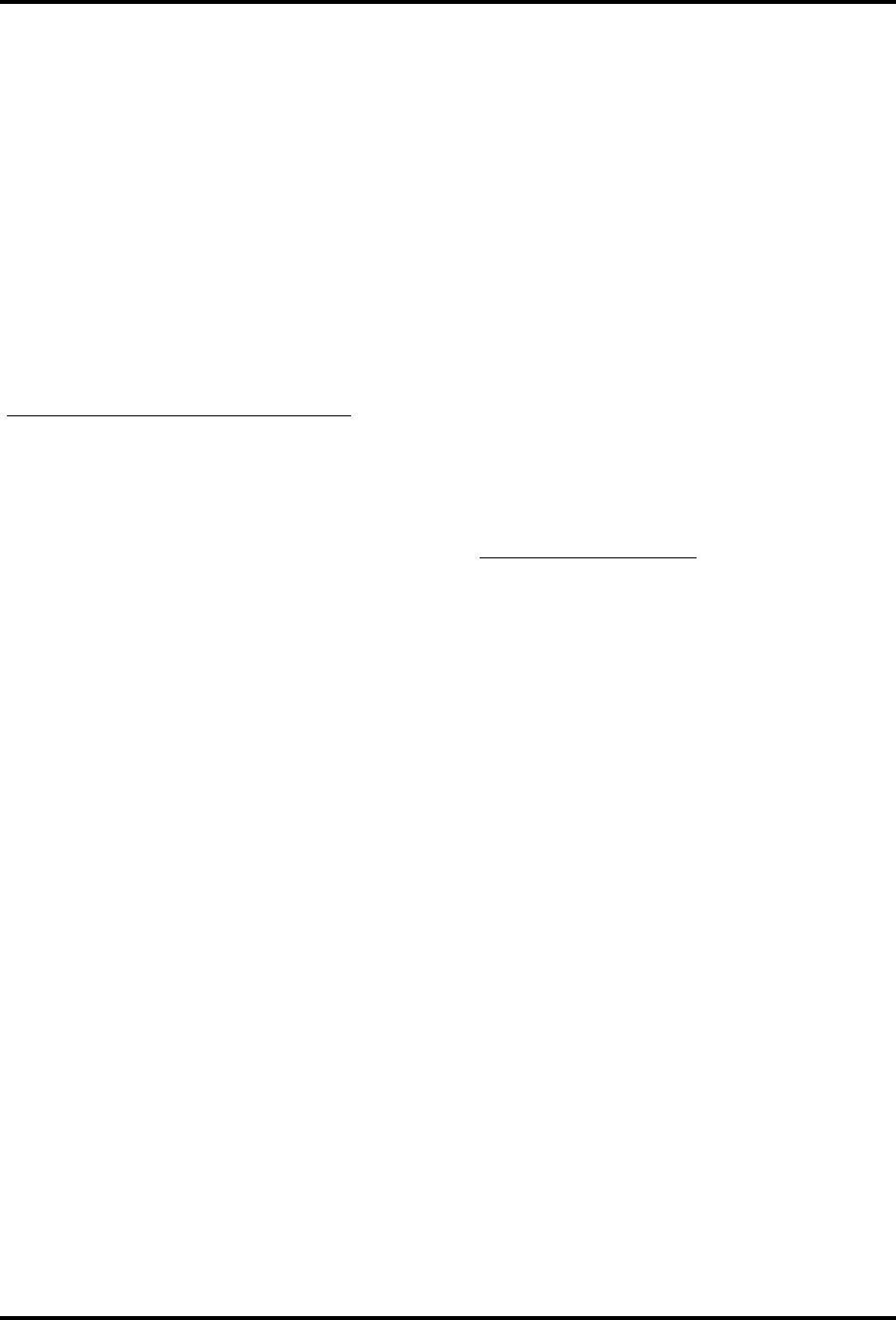
10-kW UHF Transmitter with Chapter 4, Circuit
Feedforward Drive Descriptions
840A, Rev. 0 4-3
maintains a constant peak of sync level
over varying average picture levels
(APL). The modulator portion of the
board contains the circuitry that
generates an amplitude-modulated
vestigial sideband visual IF signal output
that is made up of the baseband video
input signal (1 Vpk-pk) modulated onto
an externally generated 45.75-MHz IF
carrier frequency. The visual IF signal
and the aural IF signal are then
combined in the diplexer circuit to
produce the visual IF + aural IF output
that is connected to J20, the IF output
jack of the board.
Main Video Signal Path (Part 1 of 2)
The baseband video or the 4.5-MHz
composite input connects to the board at
J2. J2 is loop-through connected to J1
and terminated to 75 watts if jumper W4
is on jack J3. With jumper W4 removed,
the input can be connected to another
transmitter through J1; J1 is loop-
through connected to J2.
Test point TP1 is provided to monitor the
level of the input. The input is fed to the
non-inverting and inverting inputs of
U1A, a differential amplifier that
minimizes any common-mode hum that
may be present on the incoming signal.
Diodes CR1 to CR4 form a voltage-limiter
network in which, if the input voltages
exceed the supply voltages for U1A, the
diodes conduct, preventing damage to
U1A. CR1 and CR3 conduct if the input
voltage exceeds the negative supply and
CR2 and CR4 conduct if the input voltage
exceeds the positive supply voltage.
The video output of U1A is connected to
J22 on the board. Normally, the video at
J22 is jumpered to J27 on the board. If
the 4.5-MHz composite input kit is
purchased, the 4.5-MHz composite signal
at J22 connects to the external composite
4.5-MHz filter board and the 4.5-MHz
bandpass filter board. These two boards
provide the video-only signal to J27 and
the 4.5-MHz intercarrier signal to J28
from the 4.5-MHz composite input. The
video through the video gain pot R12
(adjusted for 1 Vpk-pk at TP2) connects
to amplifier U1B.
The output of U1B, if the delay equalizer
board is present in the tray, connects the
video from J6, pin 2, to the external
delay equalizer board and back to the
sync tip clamp/modulator board at J6,
pin 4. If the delay equalizer is not
present, the video connects through
jumper W1 on J5, pins 1 and 2. The
delay equalizer board plugs directly to J6
on the sync tip clamp/modulator board.
The video from J6, pin 4, is then
connected through jumper W1 on J5,
pins 2 and 3, to the amplifier Q1. The
output of Q1 connects to Q2; the base
voltage of Q2 is set by the DC offset
voltage output of the sync tip clamp
circuit.
Sync Tip Clamp Circuit
The automatic sync tip clamp circuit is
made up of U4A, Q7, U3B, and
associated components. The circuit
begins with a sample of the clamped
video that is split off from the main video
path at the emitter of Q3. The video
sample is buffered by U3A and connected
to U4A. The level at which the tip of sync
is clamped, approximately -1.04 VDC as
measured at TP2, is set by the voltage-
divider network connected to U4A. If the
video level changes, the sample applied
to U4A changes. If jumper W7 on J4 is in
the Clamp-On position, the voltage from
the clamp circuit that is applied to the
summing circuit at the base of Q2 will
change; this will bring the sync tip level
back to approximately -1.04 VDC. Q7 will
be turned off and on according to the
peak of sync voltage level that is applied
to U4A. The capacitors C14, C51, C77,
and C41 will charge or discharge to the
new voltage level, which biases U3B
more or less, through jumper W7 on J4
in the Auto Clamp-On position. U3 will
increase or decrease its output, as
needed, to bring the peak of sync back to
the correct level as set by R152 and R12.
This voltage level is applied through U3B
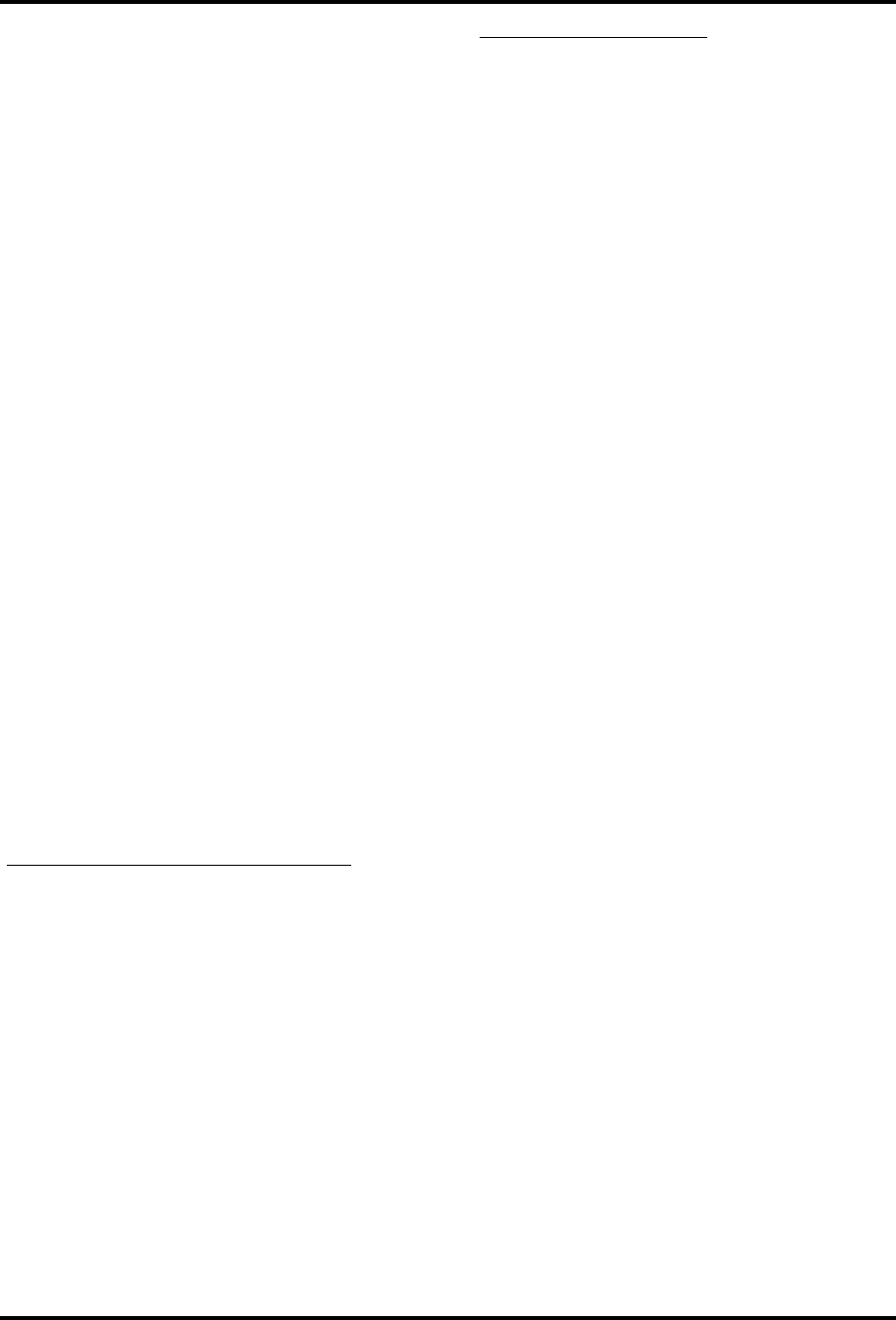
10-kW UHF Transmitter with Chapter 4, Circuit
Feedforward Drive Descriptions
840A, Rev. 0 4-4
to Q2. In the Manual position, jumper W7
on J4 is in the Clamp-Off position,
between pins 1 and 2, and adjustable
resistor R41 provides the manual clamp
bias adjustment for the video that
connects to Q2.
Jumper W6 on jack J35 must be in the
Normal position, between pins 2 and 3,
for the clamp circuit to operate with a
normal non-scrambled signal. If a
scrambled signal is used, the tray is
operated with jumper W6 in the Encoded
position, connected between pins 1 and
2. The clamp circuit is set by adjusting
depth of modulation pot R152 for the
correct depth of modulation as measured
at TP2.
Depending on the input video level, the
waveform as measured at TP2 may not
be 1 Vpk-pk. If W7 on J4 is moved to the
Clamp-Off (Manual) position, between
pins 1 and 2, the clamp level is adjusted
by R41 and will not automatically be
clamped to the set level. The output of
buffer amplifier U3A drives the sync tip
clamp circuit consisting of differential
amplifier U4A, FET Q7, and buffer
amplifier U3B. U4A is biased by R124,
R125, R184, R152, and R126 so that the
clamped voltage level at peak of sync is
approximately -1.04 VDC as measured at
TP2.
Main Video Signal Path (Part 2 of 2)
The clamped video from Q2 is connected
to white clipper circuit Q3. Q3 is adjusted
with R20 and set to prevent video
transients from overmodulating the video
carrier. The clamped video is connected
to sync clipper circuit Q4 (adjusted by
R24); Q4 limits the sync to -40 IRE units.
The corrected video connects to emitter
follower Q4 whose output is wired to
unity gain amplifier U2A and provides a
low-impedance, clamped video output at
pin 1.
Visual Modulator Circuit
The clamped video signal from U2A is
split. One part connects to a metering
circuit, consisting of U20 and associated
components, that produces a video
output sample at J8-6 and connects
through the transmitter control board to
the front panel meter for monitoring. The
other clamped video path from U2A is
through a sync-stretch circuit that
consists of Q5 and Q6. The sync-stretch
circuit contains R48; R48 adjusts the
sync stretch magnitude (amount) and
R45 adjusts the cut-in. This sync-stretch
adjustment should not be used to correct
for output sync problems, but it can be
used for video input sync problems. The
output of the sync-stretch circuit
connects to pin 5, the I input of mixer
Z1.
The video signal is heterodyned in mixer
Z1 with the visual IF CW signal (45.75
MHz). The visual IF CW signal enters the
board at jack J15 and is connected to U9,
where it is amplified and wired to pin 1,
the L input of mixer Z1. The adjustable
capacitor C78 and resistor R53 are set up
to add a small amount of incidental
carrier phase modulation (ICPM)
correction to the output of the mixer
stage to compensate for any non-
linearities generated by the mixer.
The modulated 45.75-MHz RF output of
mixer Z1 is amplified by U5 and is fed to
double-sideband visual IF output jack
J18. The level of this output jack is
adjusted by R70. J18 is the visual IF
loop-through output jack that is normally
jumpered to J19 on the board. If the
optional visual IF loop-through kit is
purchased, the visual is connected out of
the board to any external IF processor
trays.
After any external processing, the
modulated visual IF, double-sideband
signal re-enters the board through J19.
The visual IF from J19 is amplified by
U10 and U11 and routed through the
vestigial sideband filter network,
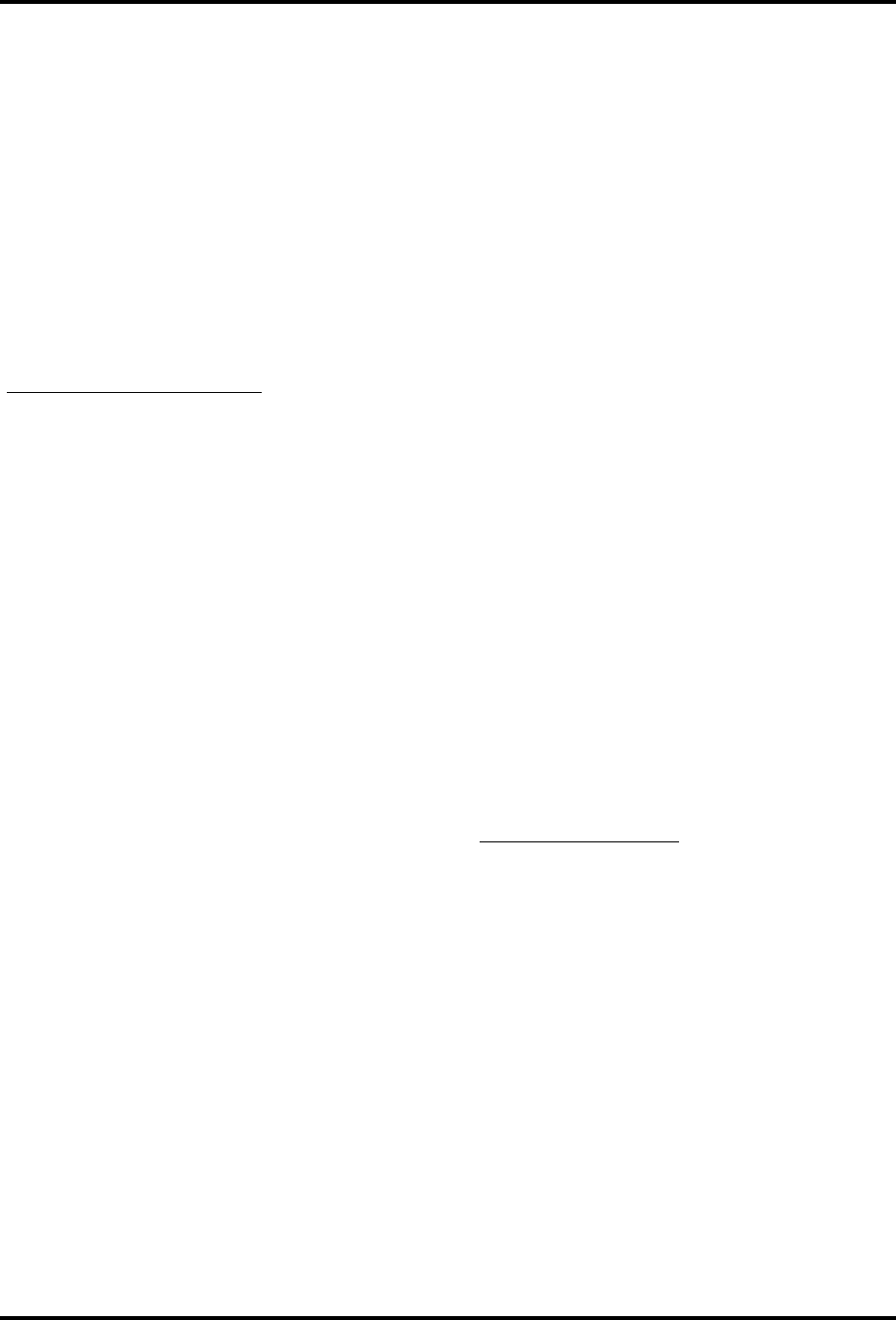
10-kW UHF Transmitter with Chapter 4, Circuit
Feedforward Drive Descriptions
840A, Rev. 0 4-5
consisting of T1, FL1, and T2, and
produces a vestigial sideband visual IF
signal output. The filtered vestigial
sideband visual IF is amplified by U7 and
connected to a T-type attenuator. R62
can be adjusted to set the visual IF gain;
this is the amount of visual IF signal that
is coupled to amplifier IC U8. R63 and
C30 are adjusted for the best VSBF
frequency response. The amplified IF
signal is fed to the input of the diplexer
circuit that consists of R76, L13, and L12.
A detected voltage sample of the visual
IF is available at test point TP5.
41.25-MHz Aural IF Circuit
On this board, the 41.25-MHz aural IF is
created by mixing the modulated 4.5-
MHz aural intercarrier signal, produced
by the aural IF synthesizer board or from
the composite 4.5-MHz filter board, with
the 45.75-MHz CW signal produced by
the 45.75-MHz IF carrier oven oscillator
board. The modulated 4.5-MHz aural
intercarrier signal enters the board at J14
or J28 and is connected to IF relay K1.
Jumper W3 on J7 determines whether
the 4.5-MHz used by the board is
internally generated or from an external
source. With jumper W3 connected
between pins 2 and 3, the 4.5 MHz from
the aural IF synthesizer board or from
the 4.5-MHz composite input is
connected to mixer Z2. If an external
4.5-MHz signal is used, it enters the
board at J12 and is fed through gain pot
R88 to amplifier IC U13A. The amplified
4.5 MHz is then connected to J7 and, if
jumper W3 is between pins 1 and 2, the
4.5-MHz signal from the external source
is connected to the mixer. Mixer Z2
heterodynes the aural-modulated, 4.5-
MHz signal with the 45.75-MHz CW signal
to produce the modulated 41.25-MHz
aural IF signal.
The output of the mixer is fed to a
bandpass filter that is tuned to pass only
the modulated 41.25-MHz aural IF signal
that is fed to jack J16, the 41.25-MHz
loop-through out jack of the board.
For normal operation, the 41.25-MHz
signal is jumpered by a coaxial cable
from J16 to J17 on the board. If the
(optional) aural IF loop-through kit is
purchased, the 41.25-MHz signal is
connected to the rear of the tray, to
which any processing trays can be
connected, and then back to jack J17 on
the board. The modulated 41.25-MHz
aural IF signal from J17 is connected
through amplifier ICs U15 and U16. The
amplified output is connected to the
attenuator-matching circuit that is
adjusted by R85. R85 increases or
decreases the level of the 41.25 MHz that
sets the A/V ratio for the diplexer circuit.
The diplexer circuit takes the modulated
45.75-MHz visual IF and the modulated
aural IF and combines them to produce
the 45.75-MHz + 41.25-MHz IF output.
The combined 45.75-MHz + 41.25-MHz
IF signal is amplified by U12 and
connected to combined IF output jack
J20 on the board. A sample of the
combined IF output is provided at J21 on
the board. If a NICAM input is used, it
connects to J36 on the board. The level
of the NICAM signal is set by R109 before
it is fed to the diplexer circuit consisting
of L28, L29, and R115. This circuit
combines the NICAM signal with the
45.75-MHz visual IF + 41.25-MHz aural
IF signal.
Operational Voltages
The +12 VDC needed to operate the
transmitter control board enters the
board at J23, pin 3, and is filtered by
L26, L33, and C73 before it is fed to the
rest of the board.
The -12 VDC needed to operate the
board enters the board at J23, pin 5, and
is filtered by L27 and C74 before being
fed to the rest of the board.
4.1.1.3 (A6) Delay Equalizer Board
(1227-1204; Appendix B)
The delay equalizer board provides a
delay to the video signal, correction to
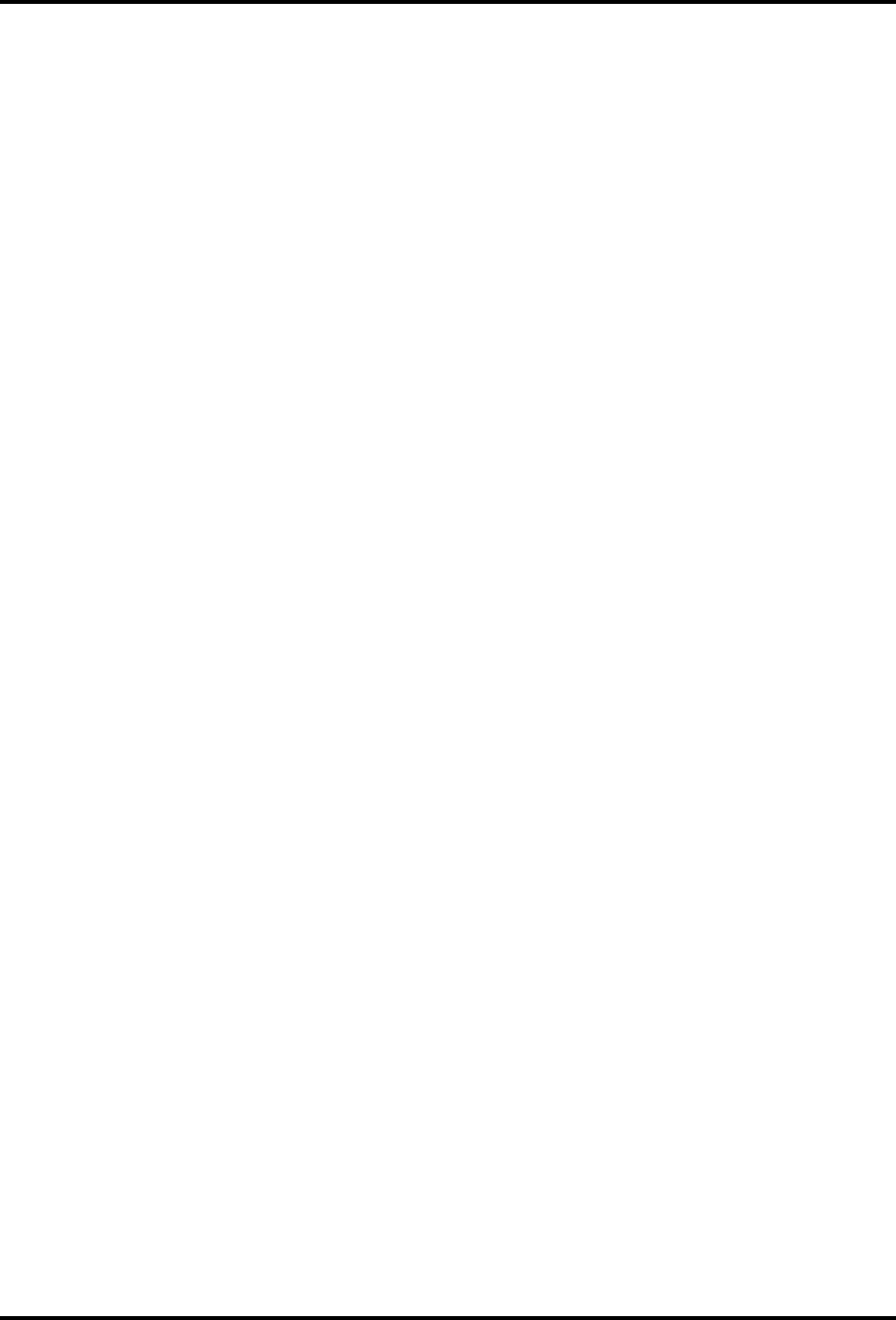
10-kW UHF Transmitter with Chapter 4, Circuit
Feedforward Drive Descriptions
840A, Rev. 0 4-6
the frequency response, and
amplification of the video signal.
The video signal enters the board at J1-2
and is connected to a pi-type, low-pass
filter consisting of C16, L7, and C17. This
filter eliminates any unwanted higher
frequencies from entering the board. The
output of the filter is connected to
amplifier stage U1; the gain is controlled
by R29. The video output of the amplifier
stage is wired to the first of four delay-
equalizing circuits that shape the video
signal to the FCC specification for delay
equalization or to the desired shape
needed for the system. The board has
been factory-adjusted to this FCC
specification and should not be
readjusted without the proper
equipment.
Resistors R7, R12, R17, and R22 adjust
the sharpness of the response curve
while inductors L1, L2, L3, and L4 adjust
the position of the curve. With a delay
equalizer test generator signal or a sine
x/x video test pattern input, the resistors
and inductors can be adjusted, while
monitoring a Tektronix VM700 test
measurement set, until the desired FCC
delay equalization curve or system curve
is attained. The delay-equalized video
signal is connected to J1-4, the video
output of the board. A sample of the
delayed video signal is connected to J2
on the board and can be used for testing
purposes.
The ±12 VDC needed to operate the
board enters the board at J1. The +12
VDC connects to J1-9, which is filtered by
L5 and C11 before it is directed to the
rest of the board. The -12 VDC connects
to J1-6, which is filtered by L6 and C12
before it is directed to the rest of the
board.
4.1.1.4 (A7) IF Carrier Oven Oscillator
Board (1191-1404; Appendix B)
The IF carrier oven oscillator board
generates the visual IF CW signal at
45.75 MHz for NTSC system "M" usage.
The +12 VDC is applied through jack J10
to crystal oven HR1; HR1 is preset to
operate at 60° C. The oven encloses
crystal Y1 and stabilizes the crystal
temperature. The crystal is the primary
device that determines the operating
frequency and is the most sensitive in
terms of temperature stability.
Crystal Y1 is operating in an oscillator
circuit consisting of transistor Q1 and its
associated components. Feedback is
provided through a capacitor-voltage
divider, consisting of C5 and C6, that
operates the crystal in a common-base
amplifier configuration using Q1. The
operating frequency of the oscillator can
be adjusted by variable capacitor C17.
The oscillator circuit around Q1 has a
separately regulated voltage, 6.8 VDC,
which is produced by a combination of
dropping resistor R4 and zener diode
VR1. The output of the oscillator at the
collector of Q1 is capacitively coupled
through C8 to the base of Q2. The small
value of C8, 10 pF, keeps the oscillator
from being loaded down by Q2.
Q2 is operated as a common-emitter
amplifier stage whose bias is provided
through R8 from the +12 VDC line. The
output of Q2, at its collector, is split
between two emitter-follower transistor
stages, Q3 and Q4. The output of Q3 is
taken from its emitter through R11 to
establish an approximately 50-ohm
source impedance through C11 to main
output jack J3. This 45.75-MHz signal is
at a power level of approximately +5
dBm. In most systems this output is
either directed to a visual modulator
board or to some splitting and amplifying
arrangement that distributes the visual IF
carrier for other needs. The second
output from the collector of Q2 is fed to
the base of emitter-follower transistor
Q4.
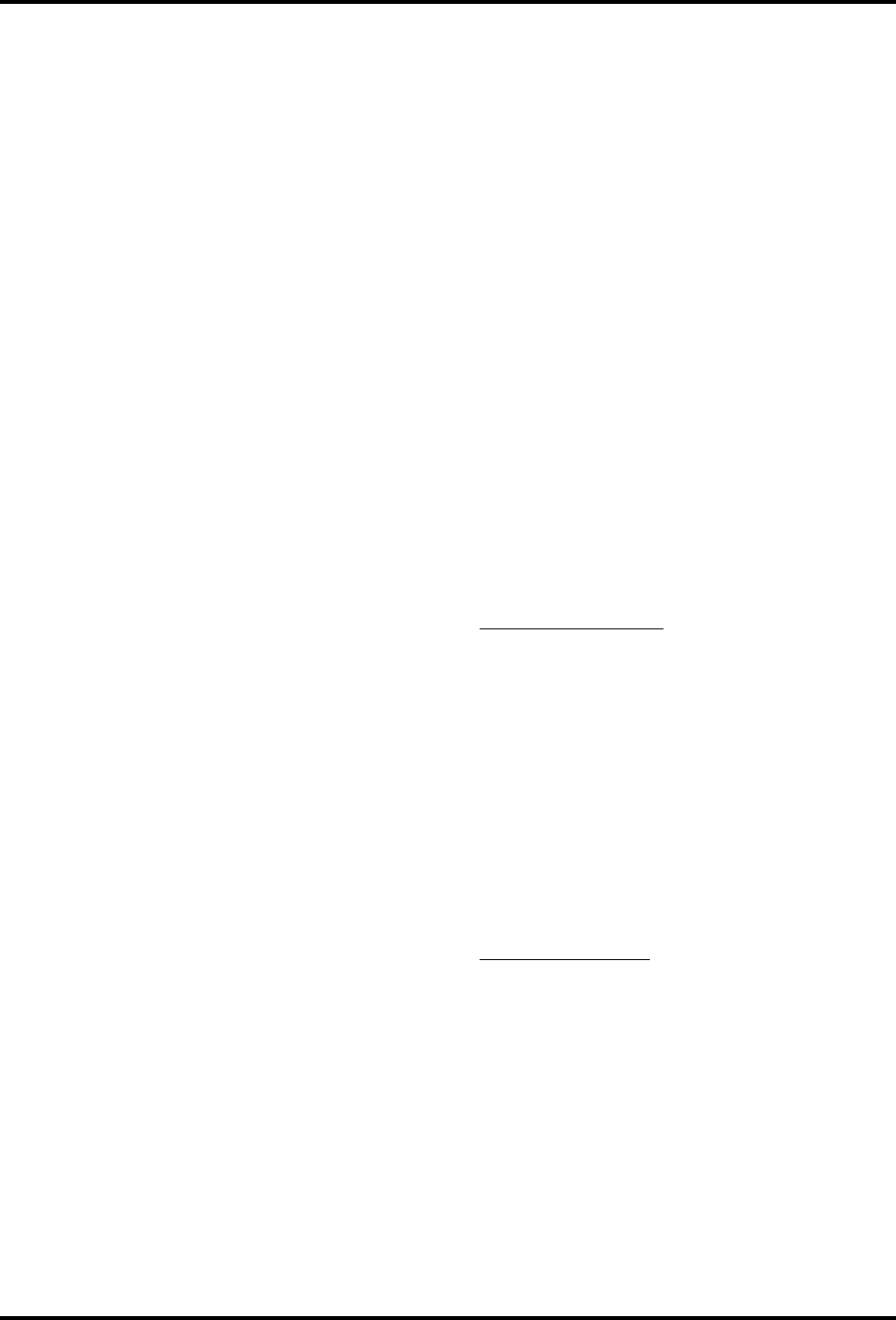
10-kW UHF Transmitter with Chapter 4, Circuit
Feedforward Drive Descriptions
840A, Rev. 0 4-7
Q4 drives two different output circuits.
One output is directed through voltage
divider R14 and R15 to jack J2 and is fed
to a frequency counter. While monitoring
J2, the oscillator can be set exactly on
the operating frequency (45.75 MHz) by
adjusting C17. The output at J2 is at a
power level of approximately -2 dBm,
which is sufficient to drive most
frequency counters. The other output of
Q4 connects to U1, a prescaler chip that
divides the signal by 15. The output of
U1 is applied to U2, a programmable
divider IC. U2 is programmed through
pins 11 to 20 to divide by 61. This results
in a 50-kHz signal at pin 9 that is
available as an output at J1. The output
of 50 kHz is generally used in systems
where the visual IF carrier oven VCXO is
used as the reference for a PLL circuit. An
example of this is a PLL circuit used on
the aural IF synthesizer board, the aural
VCO, or the precise frequency control
tray. The 50-kHz CMOS output at jack J1
is not capable of providing enough drive
level for a long coaxial cable length; as a
result, when a long coaxial cable is
needed, the output at jack J5 is utilized.
The push-pull transistor stage Q5 and
Q6, along with emitter resistor R18,
provides a large-load output capability at
J5.
The stages U1, U2, Q5, and Q6 are
powered by +5.1 VDC. The +5.1 VDC is
obtained by using the +12 VDC line
voltage and voltage-dropping resistor
R16 and zener diode VR2.
The +12 VDC power is applied to the
board through jack J4, pin 3, and is
isolated from RF signals that may occur
in the +12 VDC line through the use of
RF choke L2 and filter capacitor C10.
4.1.1.5 (A8) ALC Board, NTSC (1265-
1305; Appendix B)
The automatic level control (ALC) board
provides the ALC and amplitude linearity
correction of the IF signal. The ALC
adjusts the level of the IF signal through
the board to control the output power of
the transmitter.
The visual + aural IF input (0 dBm)
signal from the modulator enters the
board at modulator IF input jack J32. If
the (optional) receiver tray is present,
the visual + aural IF input (0 dBm) from
the receiver tray connects to receiver IF
input jack J1. The modulator IF input
connects to relay K3 and the receiver IF
input connects to relay K4. The two
relays are controlled by the Modulator
Select command that is connected to J30
on the board. Modulator select
enable/disable jumper W11 on J29
controls whether the Modulator Select
command at J30 controls the operation of
the relays or not. With jumper W11 on
J29, pins 1 and 2, the Modulator Select
command at J30 controls the operation of
the relays; with jumper W11 on J29, pins
2 and 3, the modulator is selected all of
the time.
Modulator Selected
With the modulator selected, J11-10 and
J11-28 on the rear of the UHF exciter
tray are connected together; this makes
J30 low and causes relays K3 and K4 to
de-energize. When K4 is de-energized, it
connects the receiver IF input at J1, if
present, to 50 watts. When K3 is de-
energized, it connects the modulator IF
input at J32 to the rest of the board;
Modulator Enable LED DS5 will be
illuminated.
Receiver Selected
With the receiver selected, which is J11-
10 and J11-28 on the rear of the UHF
exciter tray (connected to J30 on the
board) not connected together, relays K3
and K4 are energized. When K4 is
energized, it connects the receiver IF
input at J1, if present, to the rest of the
board. When K3 is energized, it connects
to the modulator IF input at J32 to 50
watts; Modulator Enable LED DS5 will be
illuminated.
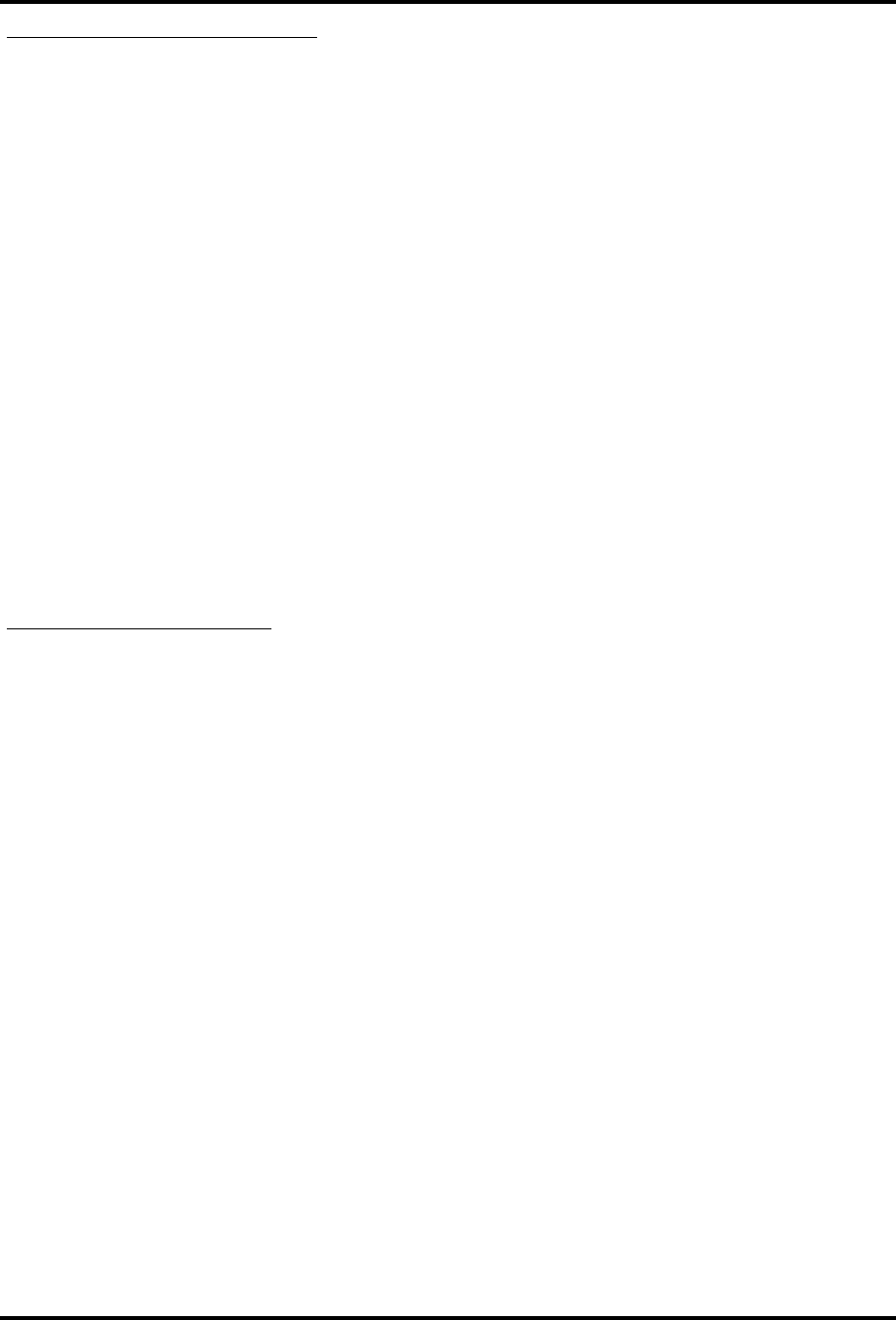
10-kW UHF Transmitter with Chapter 4, Circuit
Feedforward Drive Descriptions
840A, Rev. 0 4-8
Main IF Signal Path (Part 1 of 3)
The selected visual + aural IF input (0
dBm) signal is split, with one half of the
signal entering a bandpass filter that
consists of L3, L4, C4, L5, and L6. This
bandpass filter can be tuned with C4 and
is substantially broader than the IF signal
bandwidth. It is used to slightly steer the
frequency response of the IF to make up
for any small discrepancies in the
frequency response in the stages that
precede this point. The filter also serves
the additional function of rejecting
unwanted frequencies that may occur if
the tray cover is off and the tray is in a
high RF environment (if this is the case,
the transmitter will have to be serviced
with the tray cover off in spite of the
presence of other RF signals). The
filtered IF signal is fed through a pi-type
matching pad consisting of R2, R3, and
R4 to the pin-diode attenuator circuit
consisting of CR1, CR2, and CR3.
Input Level Detector Circuit
The other part of the split IF input is
connected through L2 and C44 to U7; U7
is an IC amplifier that is the input to the
input level detector circuit. The amplified
IF is fed to T4; T4 is a step-up
transformer that feeds diode detector
CR14. The positive-going detected signal
is then low-pass filtered by C49, L18, and
C50. This allows only the video with
positive sync to be applied through
emitter follower Q1. The signal is then
connected to detector CR15 to produce a
peak-sync voltage that is applied to op-
amp U9A. There is a test point at TP3
that provides a voltage reference check
of the input level. The detector serves
the dual function of providing a reference
that determines the input IF signal level
to the board and also serves as an input
threshold detector.
The input threshold detector prevents the
automatic level control from reducing the
attenuation of the pin-diode attenuator to
minimum (the maximum signal) if the IF
input to the board is removed. The ALC,
video loss cutback, and the threshold
detector circuits will only operate when
jumper W3 on jack J6 is in the Auto
position, between pins 1 and 2. Without
the threshold detector, and with the pin-
diode attenuator at minimum, when the
signal is restored it will overdrive the
stages following this board.
As part of the threshold detector
operation, the minimum IF input level at
TP3 is fed through detector CR15 to op-
amp IC U9A, pin 2. The reference voltage
for the op-amp is determined by the
voltage divider that consists of R50 and
R51 (off the +12 VDC line). When the
detected-input signal level at U9A, pin 2,
falls below this reference threshold
(approximately 10 dB below the normal
input level), the output of U9A at pin 1
goes to the +12 VDC rail. This high is
connected to the base of Q2. At this
point, Q2 is forward biased and creates a
current path from the -12 VDC line and
through red LED DS1, the input level
fault indicator, which becomes lit, resistor
R54, and transistor Q2 to +12 VDC. The
high from U9A also connects through
diode CR16 to U9B, pin 5, whose output
at pin 7 goes high. The high connects
through range adjust pot R74 to J20,
which connects to the front panel-
mounted power adjust pot. This high
connects to U10A, pin 2, and causes it to
go low at output U10A, pin 1. The low is
applied through jumper W3 on J6 to the
pin-diode attenuator circuit that cuts
back the IF level and, therefore, the
output power level, to 0. When the input
signal level increases above the threshold
level, the output power will raise, as the
input level increases, until normal output
power is reached.
The video input level at TP3 is also fed to
a sync-separator circuit, consisting of IC
U8, CR17, Q3, and associated
components, and then to a comparator
circuit made up of U9C and U9D. The
reference voltage for the comparators is
determined by a voltage divider
consisting of R129, R64, R65, R66, and
R130 (off the -12 VDC line). When the

10-kW UHF Transmitter with Chapter 4, Circuit
Feedforward Drive Descriptions
840A, Rev. 0 4-9
input signal level to the detector at TP3
falls below this reference threshold,
which acts as a loss of sync detector
circuit, the output of U9C and U9D goes
towards the -12 VDC rail and is split, with
one part biasing on transistor Q5. A
current path is then established from the
+12 VDC line through Q5, the resistors
R69, R137, and the red LED DS3 (video
loss indicator), which becomes lit. When
Q5 is on, it applies a high to the gates of
Q6 and Q7. This causes them to conduct
and apply video loss fault pull-down
outputs to J18, pins 5 and 2.
The other low output of U9C and U9D is
connected through CR20 to jack J5.
Jumper W2 on J5, in the Cutback Enable
position (between pins 2 and 3),
connects the low to the base of the
forward-biased Q4. If jumper W2 is in
the Disable position, between pins 1 and
2, the auto cutback will not operate. With
Q4 biased on, a level determined by the
setting of cutback level pot R71, which is
set at the factory to cut back the output
to approximately 25%, is applied to U9B,
pin 5. The output of U9B at pin 7 goes
low and is applied through the power
adjust pot to U10A, pin 2, whose output
goes low. This low is applied to the pin-
diode attenuator to cut back the level of
the output to approximately 25%.
Pin-Diode Attenuator Circuit
The input IF signal is fed to a pin-diode
attenuator circuit that consists of CR1 to
CR3. Each of the pin diodes contain a
wide intrinsic region; this makes the
diodes function as voltage-variable
resistors at this intermediate frequency.
The value of the resistance is controlled
by the DC bias supplied to the diode. The
pin diodes are configured in a pi-type
attenuator configuration where CR1 is
the first shunt element, CR3 is the series
element, and CR2 is the second shunt
element. The control voltage, which can
be measured at TP1, originates either
from the ALC circuit when jumper W3 on
J6 is in the ALC Auto position, between
pins 1 and 2, or from pot R87 when the
jumper is in the Manual Gain position.
On the pin-diode attenuator circuit, a
current path exists from J6 through R6
and then through the diodes of the pin
attenuator. Changing the amount of
current through the diodes by forward
biasing them changes the IF output level
of the board. There are two extremes of
attenuation ranges for the pin-diode
attenuators. In the minimum attenuation
case, the voltage, measured at TP1,
approaches the +12 VDC line. There is a
current path created through R6, through
series diode CR3, and finally through R9
to ground. This path forward biases CR3
and causes it to act as a relatively low-
value resistor. In addition, the larger
current flow increases the voltage drop
across R9 that tends to turn off diodes
CR1 and CR2 and causes them to act as
high-value resistors. In this case, the
shunt elements act as a high resistance
and the series element acts as a low
resistance to represent the minimum loss
condition of the attenuator (maximum
signal output). The other extreme case
occurs as the voltage at TP1 is reduced
and goes towards ground or even slightly
negative. This tends to turn off (reverse
bias) diode CR3, the series element,
causing it to act as a high-value resistor.
An existing fixed current path from the
+12 VDC line, and through R5, CR1,
CR2, and R9, biases series element CR3
off and shunt elements, diodes CR1 and
CR2 on, causing them to act as relatively
low-value resistors. This represents the
maximum attenuation case of the pin
attenuator (minimum signal output). By
controlling the value of the voltage
applied to the pin diodes, the IF signal
level is maintained at the set level.
Main IF Signal Path (Part 2 of 3)
When the IF signal passes out of the pin-
diode attenuator through C11, it is
applied to modular amplifier U1. This
device includes within it the biasing and
impedance matching circuits that makes
it operate as a wide-band IF amplifier.
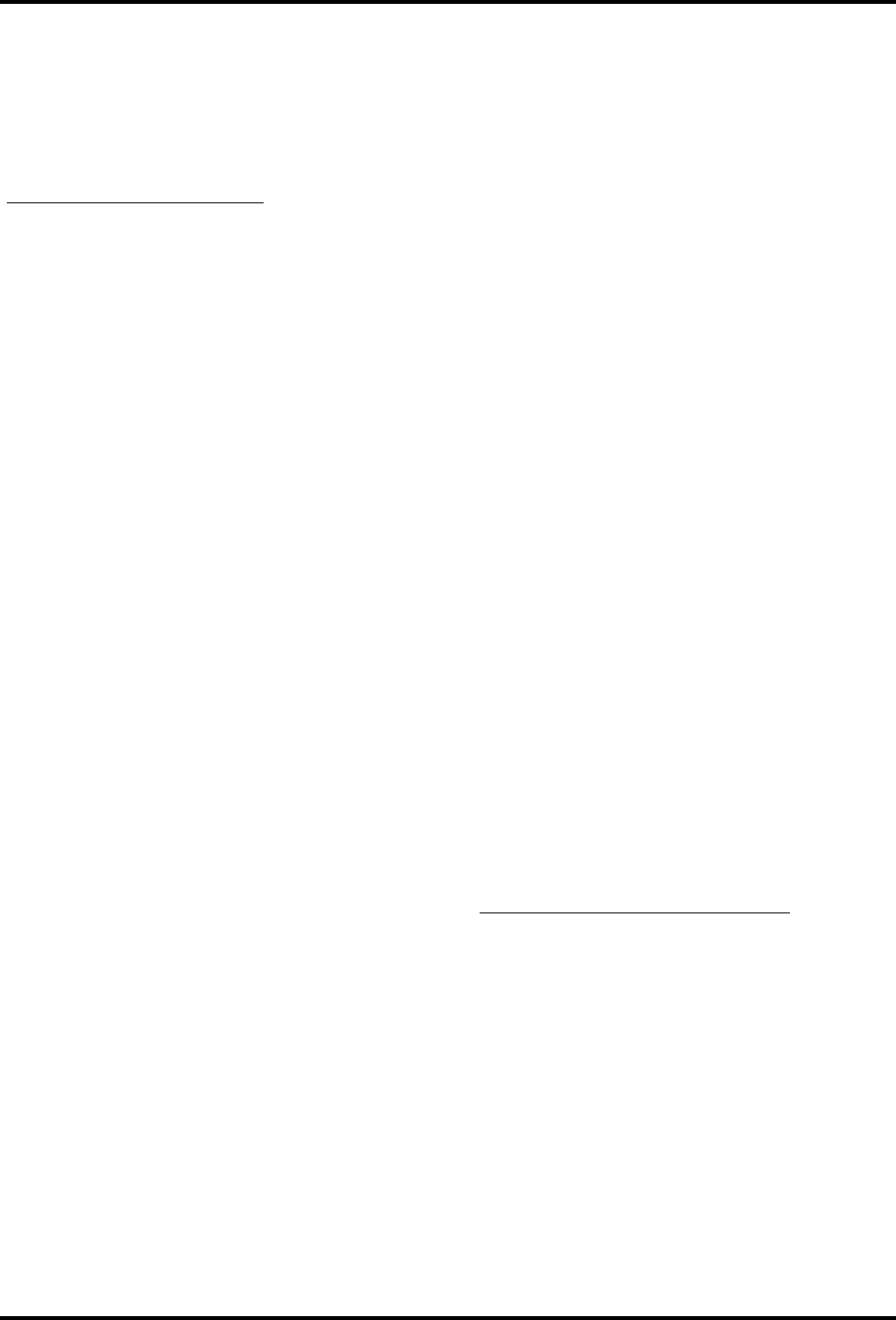
10-kW UHF Transmitter with Chapter 4, Circuit
Feedforward Drive Descriptions
840A, Rev. 0 4-10
The output of U1 is available, as a
sample of the pre-correction IF for
troubleshooting purposes and system
setup, at jack J2. The IF signal is then
connected to the linearity corrector
portion of the board.
Linearity Corrector Circuits
The linearity corrector circuits use three
stages of correction to correct for any
amplitude non-linearities of the IF signal.
Each stage has a variable threshold
control adjustment, R34, R37, or R40,
and a variable magnitude control
adjustment, R13, R18, or R23. The
threshold control determines the point at
which the gain is changed and the
magnitude control determines the
amount of gain change that occurs once
the breakpoint is reached. Two reference
voltages are needed for the operation of
the corrector circuits. Zener diode VR1,
with R33 and R135, provides a +6.8 VDC
reference and the diodes CR11 and CR12
provide a .9 VDC reference that
temperature compensates for the two
diodes in each corrector stage.
For the linearity correctors to operate, an
IF signal is applied to transformer T1,
which doubles the voltage swing by
means of a 1:4 impedance
transformation. Resistors R14, R15, and
R16 form an L-pad that lowers the level
of the signal. The amount that the level
is lowered is adjusted by adding more or
less resistance, using R13, in parallel
with the L-pad resistors. R13 is only in
parallel when the signal reaches a level
large enough to turn on the diodes CR4
and CR5. When the diodes turn on,
current flows through R13, putting it in
parallel with the L-pad.
When R13 is put in parallel with the
resistors, the attenuation through the
L-pad is lowered, causing signal stretch
(the amount determined by the
adjustment of R13). The signal is next
applied to amplifier U2 to compensate for
the loss through the L-pad. The
breakpoint, or cut-in point, for the first
corrector is set by controlling where CR4
and CR5 turn on. This is accomplished by
adjusting cut-in resistor R34; R34 forms
a voltage-divider network from +6.8 VDC
to ground. The voltage at the wiper arm
of R34 is buffered by unity-gain amplifier
U5D. This reference voltage is then
applied to R35, R36, and C39 through
L12 to the CR4 diode. C39 keeps the
reference from sagging during the
vertical interval. The .9 VDC reference
created by CR11 and CR12 is applied to
unity-gain amplifier U5B. The reference
voltage is then connected to diode CR5
through choke L11. The two chokes L11
and L12 form a high impedance for RF
that serves to isolate the op-amp ICs
from the IF.
After the signal is amplified by U2, it is
applied to the second corrector stage
through T2. This corrector and the third
corrector operate in the same fashion as
the first. All three corrector stages are
independent and do not interact with
each other.
The correctors can be disabled by moving
jumper W1 on J4 to the Disable position,
between pins 2 and 3; this moves all of
the breakpoints past the tip of sync so
that they will have no affect. The IF
signal exits the board at IF output jack J3
after passing through the three corrector
stages and is normally connected to an
external IF phase corrector board.
Main IF Signal Path (Part 3 of 3)
After the IF signal passes through the
external IF phase corrector board, it
returns to the ALC board at IF input jack
J7. The IF then passes through a
bandpass filter consisting of L20, C97,
C62, L21, C63, L22, L23, C64, and C99.
This bandpass filter is identical in both
form and function to the one described in
Section 4.3 of this chapter. In this case,
the filter is intended to make up for small
errors in frequency response that are
incurred by the signal while being
processed through the linearity and
incidental phase correction circuits.
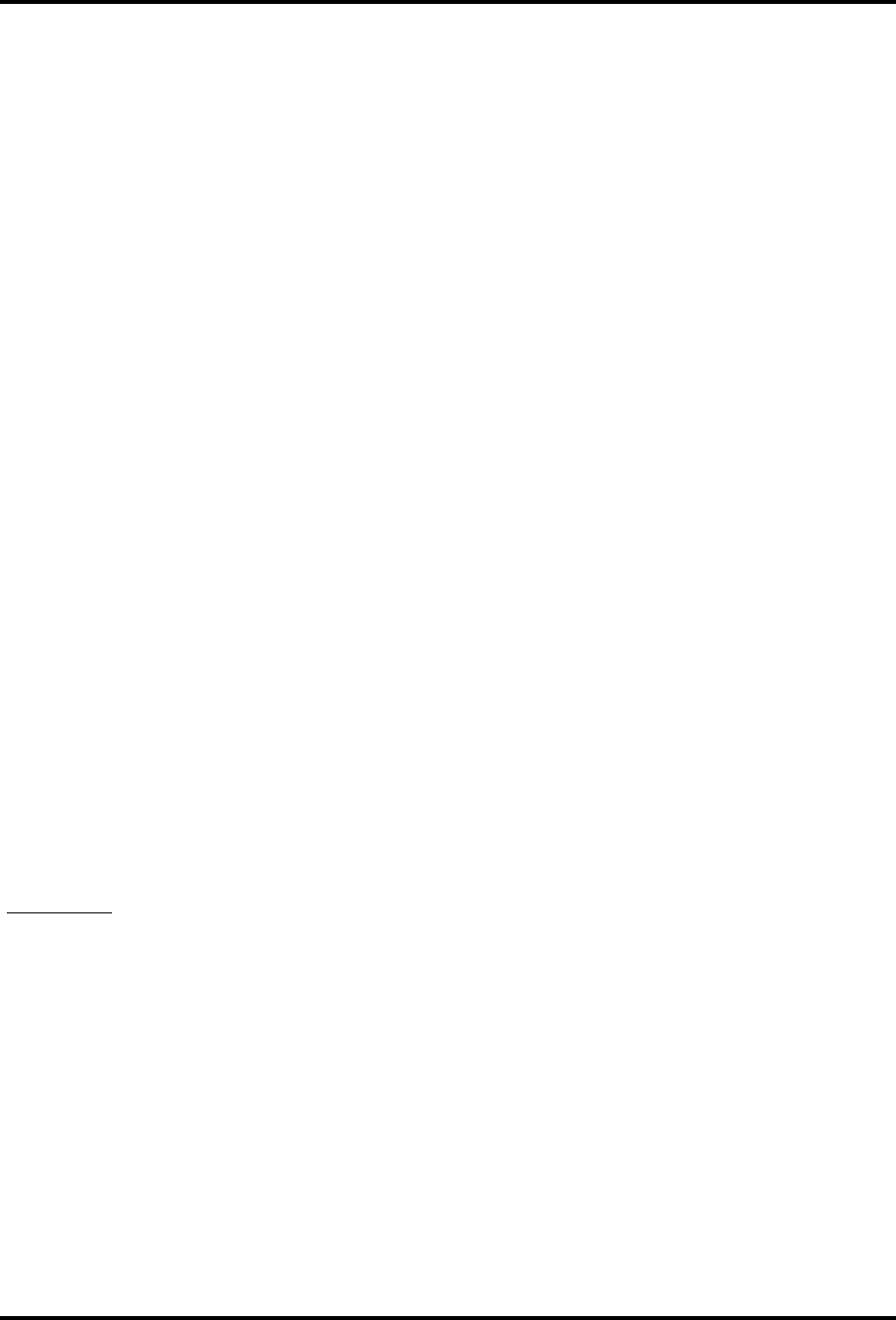
10-kW UHF Transmitter with Chapter 4, Circuit
Feedforward Drive Descriptions
840A, Rev. 0 4-11
Following the bandpass filter, the signal
is split using L24, L25, and R89. The
signal passing through L24 is the main IF
path through the board. A sample of the
corrected IF signal is split off and
connected to J10, the IF sample jack.
The IF connects to jacks J27 and J28.
These jacks control whether a 6-dB pad
is included in the circuit by the
positioning of jumpers W9 and W10. The
6-dB pad-in is when jumpers W9 and
W10 are connected between pins 2 and 3
on J27 and J28. The 6-dB pad-out is
when jumpers W9 and W10 are
connected between pins 1 and 2 on J27
and J28. Normally, the pad is out. The IF
signal is then applied to a two-stage,
frequency-response corrector circuit that
is adjusted as needed.
Variable resistors R103 and R106 adjust
the depth and gain of the notches and
variable caps C71 and C72 adjust the
frequency position of the notches. The IF
signal is amplified by U13 and U14 before
it is connected to J12, the IF output jack
of the board. R99 is an output level
adjustment that is set to provide
approximately 0 dBm of IF output at J12.
A sample of the IF is fed to J11 to
provide an IF sample point that can be
monitored without breaking the signal
path and gives an indication of the IF
signal after the linearity and the
frequency-response correction takes
place.
ALC Circuit
The other path of the corrected IF signal
is used in the ALC circuit. The IF is wired
out of the splitter through L25 and
connects to op-amp U12. The output of
U12 is wired to jacks J8 and J9 on which
jumpers W4 and W8 control the normal
or encoded operation of the ALC circuitry.
For normal operation, jumper W4 on J8 is
between pins 1 and 2 and jumper W8 on
J9 is between pins 1 and 2. The IF signal
is applied to transformer T5; T5 doubles
the voltage swing by means of a 1:4
impedance transformation before it is
connected to the ALC detector circuit on
the board and amplified by U10B.
For normal operation, jumper W7 on J26
is between pins 1 and 2 and jumper W5
on J21 is between pins 1 and 2. The
detected ALC voltage is wired to U10A,
pin 2, where it is summed with the front
panel power control setting. The output
power adjustment for the transmitter is
achieved, if the (optional) remote power
raise/lower kit (1227-1039) is purchased,
by R75, a motor-driven pot controlled by
switch S1 on the board, or screwdriver
adjust pot R1 on the front panel of the
UHF exciter tray. An external power
raise/lower switch can be used by
connecting it to jack J10, at J10-11
power raise, J10-13 power raise/lower
return, and J10-12 power lower, on the
rear of the UHF exciter tray. S1, or the
remote switch, controls relays K1 and K2,
which control motor M1 that moves
variable resistor R75. If the (optional)
remote power raise/lower kit is not
purchased, the ALC voltage is controlled
only by screwdriver adjust pot R1 on the
front panel of the UHF exciter tray. The
ALC voltage is set for .8 VDC at TP4 with
a 0 dBm output at J12 of the board. A
sample of the ALC at J19, pin 2, is wired
to the transmitter control board where it
is used on the front panel meter and in
the AGC circuits.
This ALC voltage, and the DC level
corresponding to the IF level after signal
correction, are fed to U10A, pin 2, whose
output at pin 1 connects to the ALC pin-
diode attenuator circuit. If there is a loss
of gain somewhere in an IF circuit, the
output power of the transmitter will drop.
The ALC circuit senses this drop at U10A
and automatically lowers the loss of the
pin-diode attenuator circuit to
compensate by increasing the gain.
The ALC action starts with the ALC
detector level that is monitored at TP4.
The detector output at TP4 is nominally
+.8 VDC and is applied through resistor
R77 to a summing point at op-amp
U10A, pin 2. The current available from

10-kW UHF Transmitter with Chapter 4, Circuit
Feedforward Drive Descriptions
840A, Rev. 0 4-12
the ALC detector is offset, or
complemented, by current taken away
from the summing junction. In normal
operation, U10A, pin 2, is at 0 VDC when
the loop is satisfied. If the recovered or
peak-detected IF signal at IF input jack
J7 of this board should drop in level,
which normally means that the output
power is decreasing, the null condition
would no longer occur at U10A, pin 2.
When the level drops, the output of
U10A, pin 1, will go more positive. If
jumper W3 on J6 is in the Automatic
position, it will cause the ALC pin-diode
attenuators CR1, CR2, and CR3 to have
less attenuation and increase the IF
level; this will act to compensate for the
decrease in level. If the ALC cannot
increase the input level enough to satisfy
the ALC loop, due to there not being
enough range, an ALC fault will occur.
The fault is generated because U10D, pin
12, increases above the trip point set by
R84 and R83 until it conducts. This
makes U10D, pin 14, high and causes the
red ALC Fault LED DS2 to light.
Scrambled Operation with Encoding
For encoded, scrambled operation,
jumper W4 on J8 must be connected
between pins 2 and 3, jumper W8 on J9
must be between pins 3 and 2, jumper
W7 on J26 must be between pins 2 and
3, and jumper W5 on J21 must be
between pins 2 and 3. The IF is
connected through W4 on J8 to the sync
regeneration circuits.
If this board is operated with scrambling,
using suppressed sync, the ALC circuit
operates differently than described above
because there is no peak of sync present
on the IF input. A timing pulse from the
scrambling encoder connects to the
board at J24. This timing pulse is
converted to sync pulses by U17A and
U17B, which control the operation of Q8.
The sync amplitude is controlled by R149
and is then applied to U15A, where it is
added to the detected IF signal to
produce a peak of sync level. The output
of U15A is peak detected by CR26 and
fed to U15B. If necessary, intercarrier
notch L39 can be placed in the circuit by
placing W6 on J22. The intercarrier notch
is adjusted to filter any aural and 4.5-
MHz intercarrier frequencies. The peak of
sync signal is fed through R162, the ALC
calibration control, to amplifier U15C. The
amplified peak of sync output is
connected through J21, pins 2 and 3, to
U10A, where it is used as the reference
for the ALC circuit and the AGC reference
to the transmitter control board. Voltage
TP4 should be the same in either the
normal or the encoded video mode.
Monitor J9, pins 3 and 4, with a spectrum
analyzer, check that the board is in the
AGC mode, and tune C103 to notch-out
the aural IF carrier.
Fault Command
The ALC board also has circuitry for an
external mute fault input at J19, pin 6.
This is a Mute command and, in most
systems, it is involved in the protection
of the circuits of high-gain output
amplifier devices. The Mute command is
intended to protect the amplifier devices
against VSWR faults. In this case, the
action should occur faster than just
pulling the ALC reference down. Two
different mechanisms are employed: one
is a very fast-acting circuit to increase
the attenuation of the pin-diode
attenuator, CR3, CR1, and CR2, and the
second is the reference voltage being
pulled away from the ALC amplifier
device. An external Mute is a pull-down
applied to J19, pin 6, to provide a current
path from the +12 VDC line through R78
and R139, the LED DS4 (Mute indicator),
and the LED section of opto-isolator U11.
These actions turn on the transistor
section of U11 that applies -12 VDC
through CR21 to U10A, pin 3, and pulls
down the reference voltage. This is a
fairly slow action that is kept at this pace
by the low-pass filter function of R81 and
C61. When the transistor section of U11
is on, -12 VDC is also connected through
CR22 to the pin-diode attenuator circuit.
This establishes a very fast muting
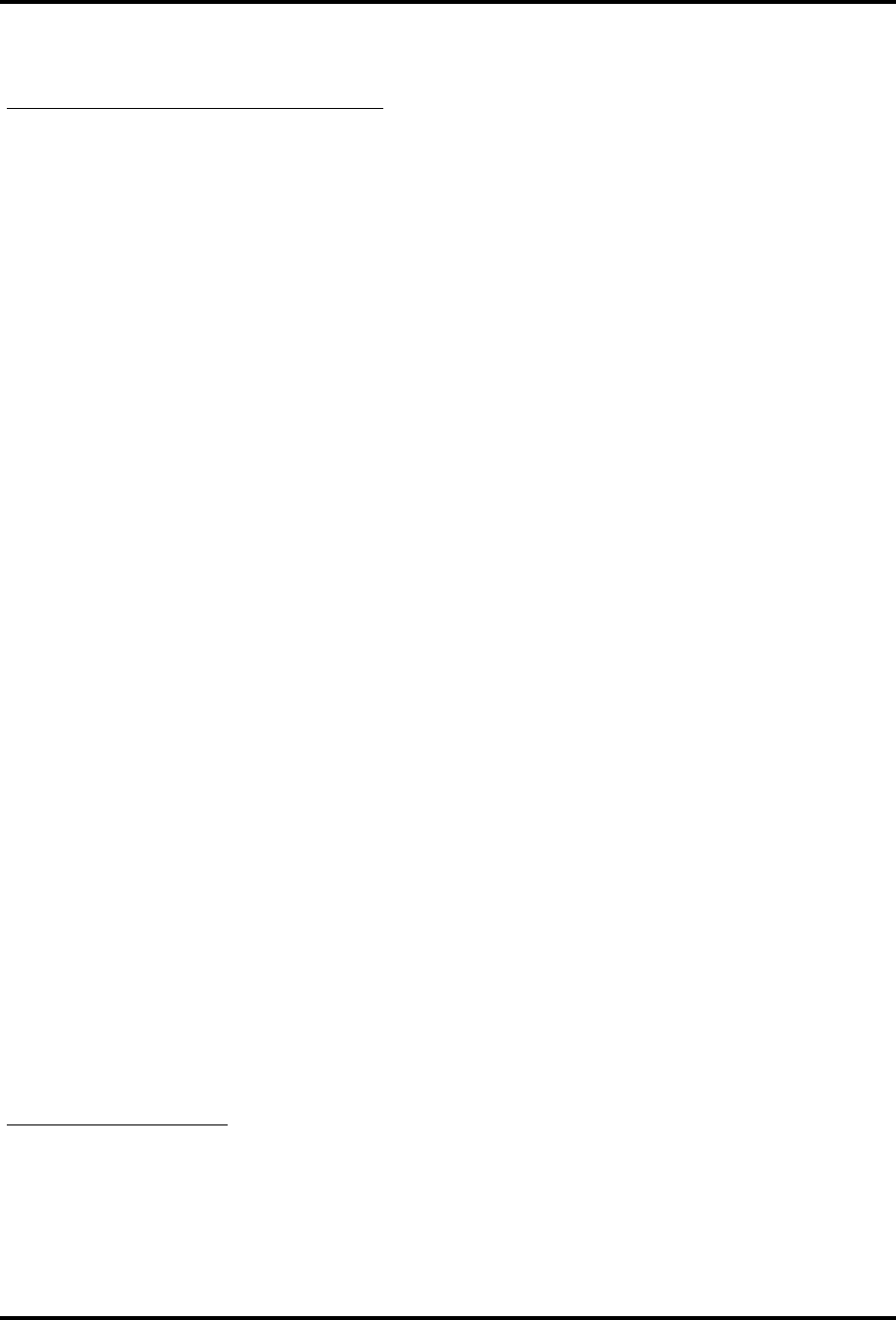
10-kW UHF Transmitter with Chapter 4, Circuit
Feedforward Drive Descriptions
840A, Rev. 0 4-13
action, by reverse biasing CR3, in the
event of an external VSWR fault.
±12 VDC Needed to Operate the Board
The ±12 VDC connects to the board at
J14. The +12 VDC connects to J14-3 and
is filtered by L30, L41, and C80 before it
is applied to the rest of the board. The
-12 VDC connects to J14-5 and is filtered
by L31 and C81 before it is applied to the
rest of the board.
The +12 VDC also connects to U16, a 5-
VDC regulator IC, that produces the +5
VDC needed to operate timing IC U17.
4.1.1.6 (A9) IF Phase Corrector Board
(1227-1250; Appendix B)
The IF phase corrector board has
adjustments that pre-correct for any IF
phase modulation distortion that may
occur in output amplifier devices such as
Klystron power tubes and solid-state
amplifiers. Two separate, adjustable IF
paths are on the board: a quadrature IF
path and an in-phase IF path. The
quadrature IF is 90° out of phase and
much larger in amplitude than the in-
phase IF. When they are combined in Z1,
it provides the required adjustable phase
correction to the IF signal.
The IF input signal enters at J1 and is AC
coupled to U1. U1 amplifies the IF before
it is connected to Z1, a splitter that
creates two equal IF outputs: IF output 1
is connected to J2 and IF output 2 is
connected to J3. The IF output 1 at J2 is
jumpered through coaxial cable W4 to
jack J6, the quadrature input, on the
board. The IF output 2 at J3 is jumpered
through coaxial cable W5 to jack J7, the
in-phase input, on the board.
Phase Corrector Circuit
The phase corrector circuit corrects for
any amplitude nonlinearities of the IF
signal. It is designed to work at IF and
has three stages of correction. Each
stage has a variable threshold and
magnitude control. The threshold control
determines the point at which the gain is
changed and the magnitude control
determines the gain change once the
breakpoint is reached. The second stage
has a jumper that determines the
direction of correction, so that the gain
can increased either above or below the
threshold, and either black or white
stretch can be achieved.
In the phase corrector circuit, the IF
signal from J6 is applied to transformer
T1; T1 doubles the voltage swing using a
1:4 impedance transformation. Resistors
R8, R61, R9, and R48 form an L-pad that
attenuates the signal. This attenuation is
adjusted by adding R7, a variable
resistor, in parallel with the L-pad. R7 is
only in parallel when the signal reaches a
level large enough to bias on CR1 and
CR2 and allow current to flow through
R7. When R7 is put in parallel with the L-
pad, the attenuation through the L-pad is
lowered, causing black stretch.
Two reference voltages are utilized in the
corrector stages and both are derived
from the +12 VDC line. Zener diode VR1,
with R46 as a dropping resistor, provides
+6.8 VDC from the +12 VDC line. Diodes
CR11 and CR12 provide a .9 VDC
reference to temperature compensate
the corrector circuits from the effects of
the two diodes in each corrector stage.
The threshold for the first corrector stage
is set by controlling where CR1 and CR2
turn on. This is accomplished by
adjusting R3 to form a voltage divider
from +6.8 VDC to ground. The voltage at
the wiper of R3 is buffered by U9C, a
unity-gain amplifier, and applied to CR1.
The .9 VDC reference is connected to
U9D, a unity-gain amplifier, whose
output is wired to CR2. These two
references are connected to diodes CR1
and CR2 through chokes L2 and L3. The
two chokes form a high impedance for RF
to isolate the op-amps from the RF. The
adjusted signal is next applied to
amplifier U2 to compensate for the loss
through the L-pad. U2 is powered
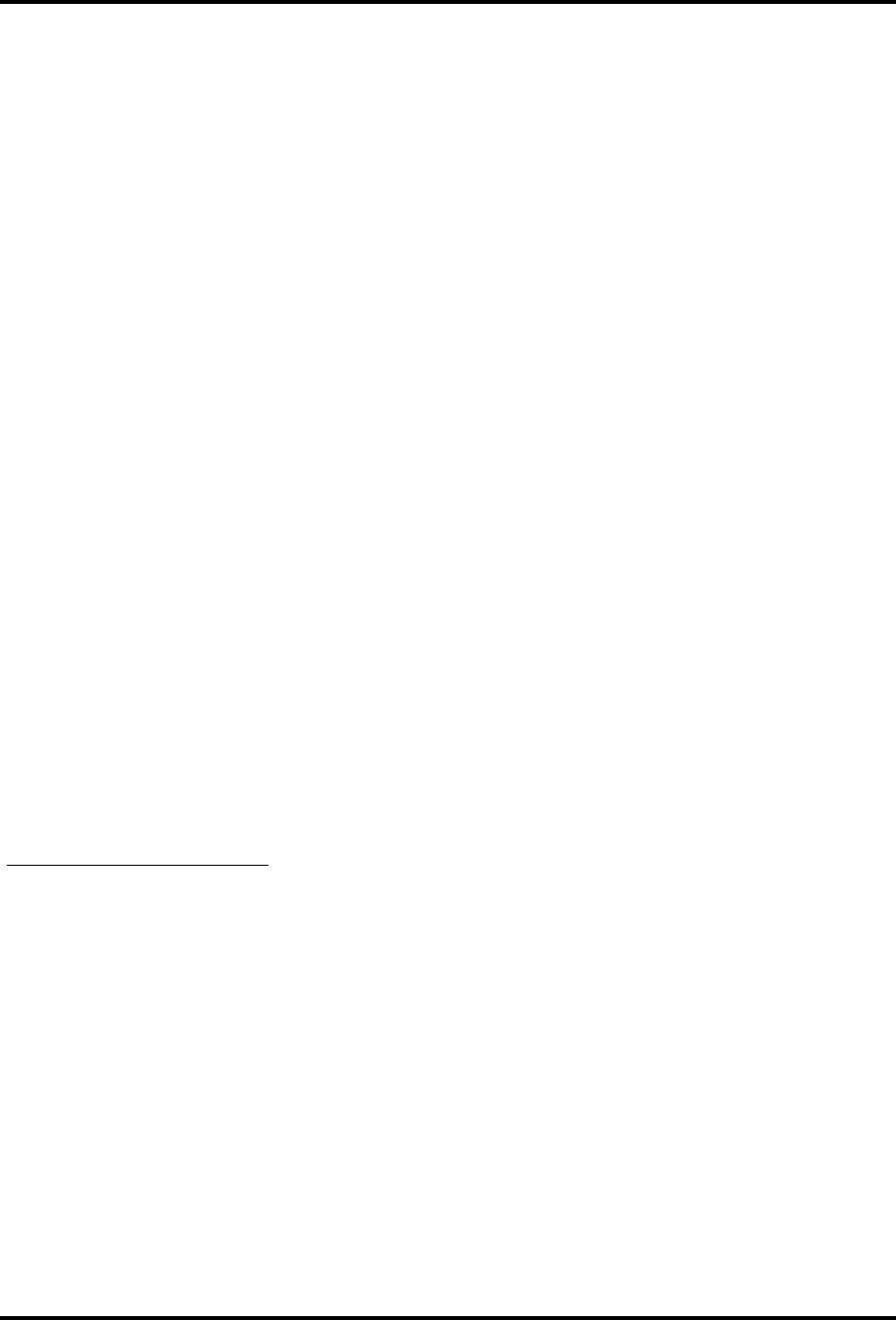
10-kW UHF Transmitter with Chapter 4, Circuit
Feedforward Drive Descriptions
840A, Rev. 0 4-14
through L4 and R10 from the +12 VDC
line. After the signal is amplified by U2, it
is applied to the second corrector stage
through T2 and then to a third corrector
stage through T3. The other two
corrector stages operate in the same
manner as the first; they are
independent and do not interact with
each other.
When jumper W1 on J8 is connected
from center to ground, R15 is put in
series with ground. In this configuration,
black stretch (white compression) is
applied to the IF signal by controlling the
attenuation through the path. When W1
is connected from the center pin to the
end that connects to T2, R15 is put in
parallel with the L-pad. In this
configuration, black compression (white
stretch) is applied to the IF signal by
controlling the attenuation through the
path.
The phase correctors can be bypassed by
moving jumper W2 on J9 to the Disable
position. This action will move all of the
threshold points past sync tip so that
they will have no effect. R68 can be
adjusted and set for the correction range
that is needed. TP2 is a test point that
gives the operator a place to measure
the level of the quadrature IF signal that
is connected to pin 6 on combiner Z2.
Amplitude Corrector Circuit
The amplitude corrector circuit uses one
stage of correction to correct for any
amplitude nonlinearities of the IF signal.
The stage has a variable threshold
control, R31, and a variable magnitude
control, R35. The threshold control
determines the point at which the gain is
changed and the magnitude control
determines the amount of gain change
once the breakpoint is reached.
Two reference voltages are needed for
the operation of the corrector circuit.
Zener diode VR1 with R46 provides +6.8
VDC and the diodes CR11 and CR12
provide a .9 VDC reference voltage to
temperature compensate for the two
diodes in the corrector stage. In the
amplitude corrector circuit, the IF signal
from J7 is applied to transformer T4 to
double the voltage swing by means of a
1:4 impedance transformation. Resistors
R36, R55, R56, and R37 form an L-pad
that lowers the level of the signal. The
amount that the level is lowered is
adjusted by adding more, or less,
resistance, using R35 in parallel with the
L-pad resistors. R35 is only in parallel
when the signal reaches a level large
enough to turn on diodes CR8 and CR9.
When the diodes turn on, current flows
through R35 and puts it in parallel with
the L-pad. When R35 is in parallel with
the resistors, the attenuation through the
L-pad is lowered, causing signal stretch
(the amount of stretch determined by the
adjustment of R35).
The signal is next applied to amplifier U5
to compensate for the loss in level
through the L-pad. The breakpoint, or
cut-in point, for the corrector stage is set
by controlling where CR8 and CR9 turn
on. This is achieved by adjusting cut-in
resistor R31 to form a voltage divider
from +6.8 VDC to ground. The voltage at
the wiper arm of R31 is buffered by
unity-gain amplifier U8B. This voltage is
then applied to R34 through L11 to the
CR9 diode. The .9 VDC reference created
by CR11 and CR12 is applied to unity-
gain amplifier U8A. C36 keeps the
reference from sagging during the
vertical interval. The reference voltage is
then connected to diode CR8 through
choke L12. The two chokes L11 and L12
form a high impedance for RF to isolate
the op-amp ICs from the IF.
After the signal is amplified by U5, it is
applied to a second stage through T5.
The transformer doubles the voltage
swing by means of a 1:4 impedance
transformation. Resistors R39, R57, R58,
and R40 form an L-pad that lowers the
level of the signal. The signal is applied
to amplifier U6 to compensate for the
loss in level through the L-pad. After the
signal is amplified by U6, it is applied to a
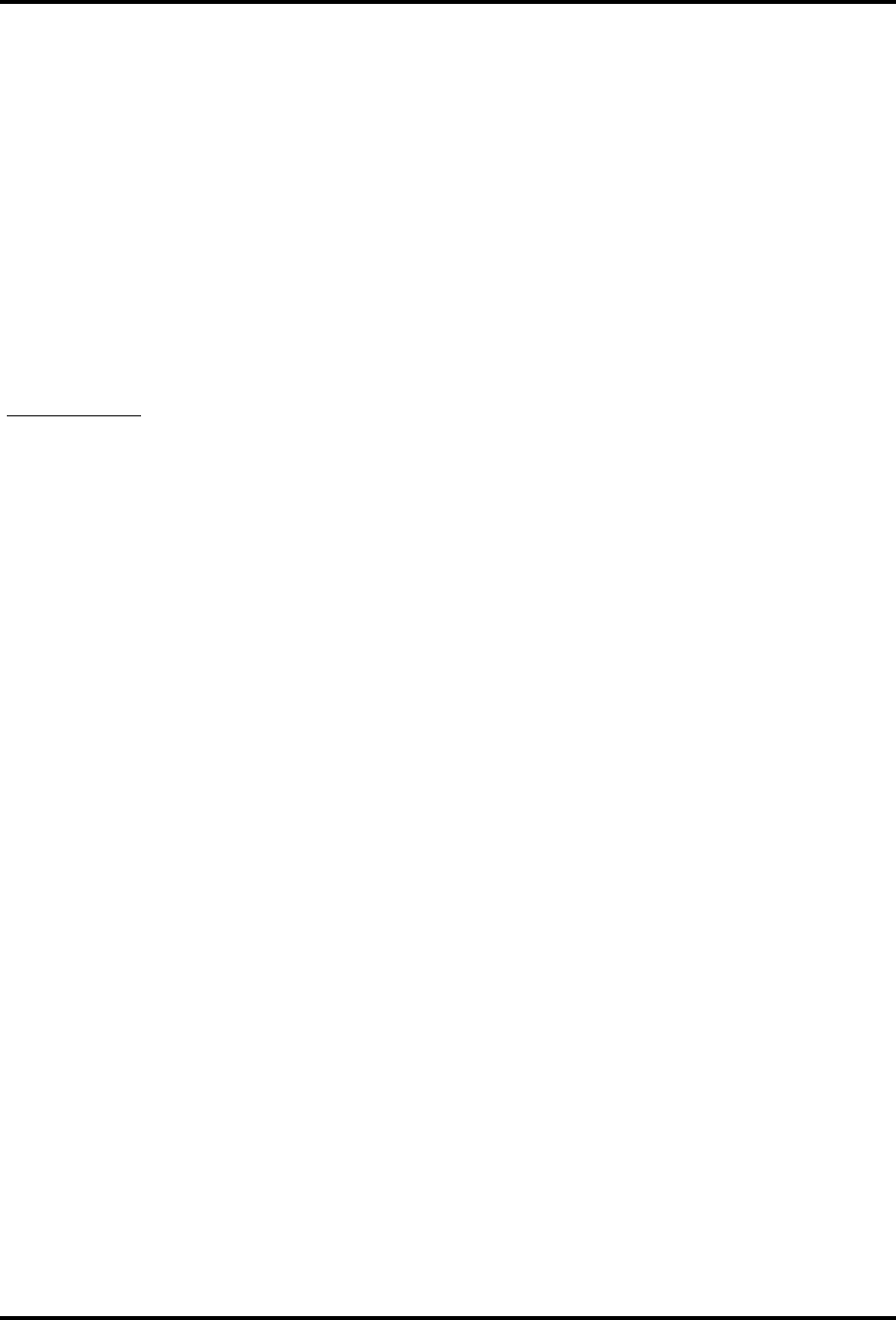
10-kW UHF Transmitter with Chapter 4, Circuit
Feedforward Drive Descriptions
840A, Rev. 0 4-15
third stage through T6. The transformer
doubles the voltage swing by means of a
1:4 impedance transformation. Resistors
R42, R59, R60, and R43 form an L-pad to
lower the level of the signal. The signal is
applied to amplifier U7 to compensate for
the loss in level through the L-pad. TP1 is
a test point that gives the operator a
place to measure the level of the in-
phase IF signal that is connected to
mixer stage Z2. The amplitude corrector
can be disabled by moving jumper W3 on
J10 to the Disable position; this will move
the breakpoint past sync tip and will have
no effect on the signal.
Output Circuit
The phase-corrected signal from pin 1 on
combiner Z2 exits the board at IF output
jack J4 after passing through a matching
network consisting of six resistors.
4.1.1.7 (A11) UHF Upconverter Board
(1265-1310; Appendix B)
The UHF upconverter board provides
upconversion for the transmitter by
mixing the IF and local oscillator (LO)
signals in mixer Z1 to produce the
desired RF frequency output. The RF
output is connected through J3 to an
external filter and applied back to the
board at J4 where the gain is set by R10.
The RF is amplified and connected to the
RF output jack of the board at J5.
The IF signal (0 dBm) enters the board at
J1, an SMA connector, and is applied
through a filter circuit (L10 and C25 to
C28) to a matching pad that consists of
R1, R2, and R3. The matching pad
presents a relatively good source
impedance to the I input of mixer Z1,
which is made up of pins 3 and 4. The LO
signal (+13 dBm) from the x8 multiplier
connects to the board at jack J2, an SMA
connector, through a UHF channel filter
and is connected directly to pin 8, the L
input of the mixer. The frequency of the
LO is the sum of the IF frequency above
the desired visual carrier. For instance, in
system M, the IF visual frequency is at
45.75 MHz and the relative location of
the aural would be 4.5 MHz lower (41.25
MHz). By choosing the local oscillator to
be 45.75 MHz above the visual carrier, a
conversion in frequency occurs with the
selection of the difference product. The
difference product, which is the local
oscillator minus the IF, will be at the
chosen visual carrier frequency output.
There will also be other signals present at
RF output connector J3 at a lower level.
These are the sum conversion product,
the LO, and the IF frequencies. Usually,
the output product that is selected by the
tuning of the external filter is the
difference product (LO minus the 45.75-
MHz IF). The difference product has the
sidebands flipped so that the visual
carrier is lower in frequency than the
aural carrier.
If a bad reactive load is connected to the
mixer, the LO signal fed through it can be
increased because the mixer no longer
serves as a double-balanced mixer. The
mixer suppresses signals that may leak
from one input port to any of the other
ports. This activity is enhanced by having
inputs and outputs of the mixer at a 50Ω
impedance.
The reactive filter, which is externally
connected to J3 of the board, does not
appear as a good 50Ω-load at all
frequencies. The pad, in the output line
of the board, consists of R5, R4, R6, and
R7. It buffers the bad effects of the
reactive filter load and makes it appear
as a 50Ω impedance. The RF signal is
amplified by U1, a modular amplifier that
contains biasing and impedance matching
networks that make U1 act as a
wideband RF amplifier device. This
amplifier, in a 50Ω system, has
approximately 12 dB of gain. U1 is
powered from the +12 VDC line through
RF decoupling components R27, R28,
C30, R8, and L1. The inductor L1 is a
broadband RF choke, resonance free
through the UHF band. The amplified RF
connects to SMA RF output jack J3 which
is cabled to the external filter.
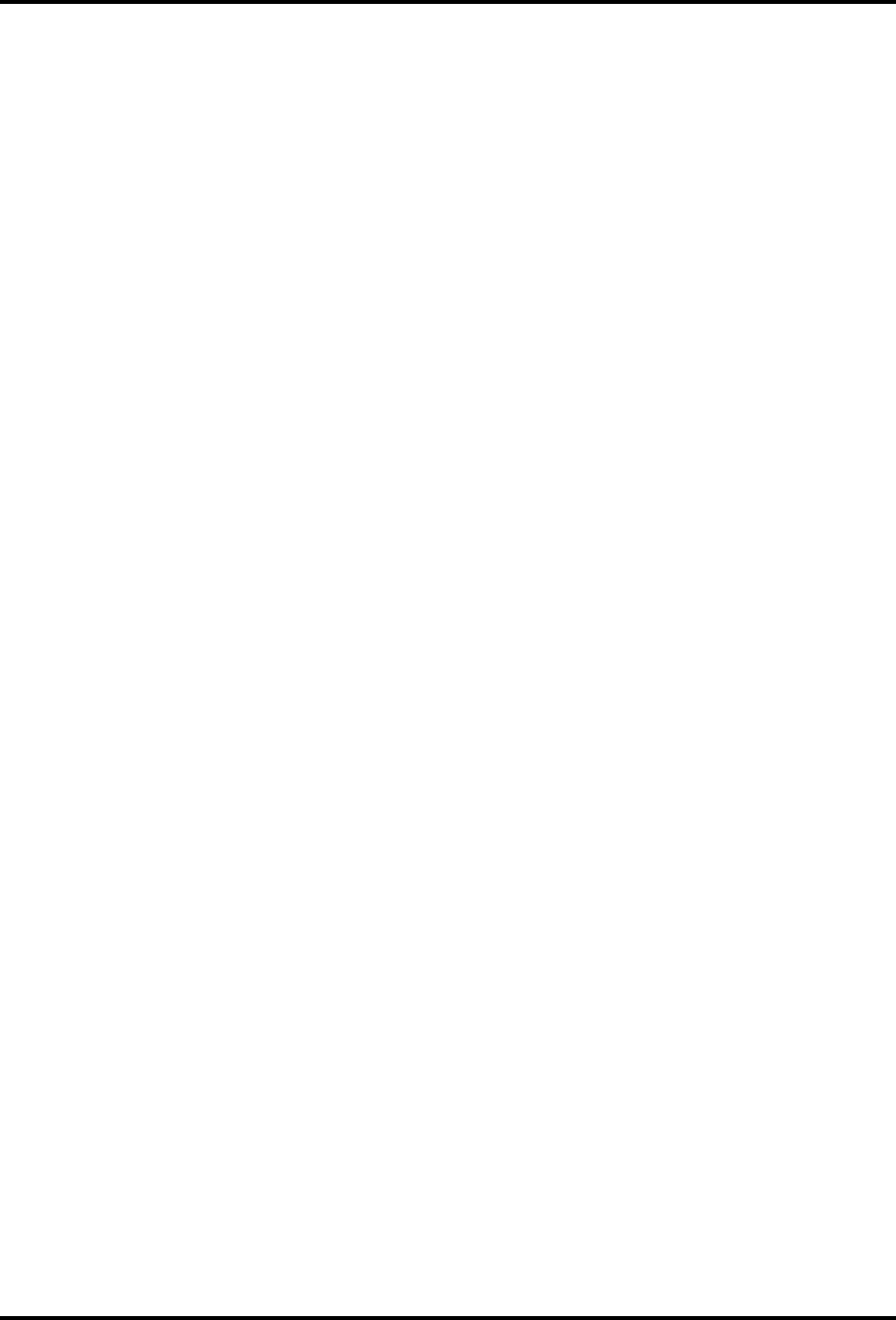
10-kW UHF Transmitter with Chapter 4, Circuit
Feedforward Drive Descriptions
840A, Rev. 0 4-16
The RF input signal from the external
filter re-enters the board at J4 (-11 to -
14 dBm) and is capacitively coupled to
the pin-diode attenuator circuit that
consists of CR1, CR2, and CR5. The pin-
diode attenuator acts as a voltage-
variable attenuator in which each pin
diode functions as a voltage-variable
resistor and depends on the DC bias
supplied to the diode for the resistance
value. The pin diodes, because of a large,
intrinsic region, cannot rectify signals at
this RF frequency; they act as a linear
voltage-variable resistor. The pin diodes
are configured in a shunt configuration
where CR1 is the first shunt element,
CR2 is the second shunt element, and
CR5 is the series element. In most cases,
the manual gain AGC, W1 on J10
between pins 1 and 2, is used. The
control voltage from manual gain pot R10
sets up a current path through R11 and
the diodes in the pin attenuator.
The level-controlled RF signal from the
pin-diode attenuator circuit is amplified
by wideband-hybrid amplifier IC U2; U2
is configured in the same way as U1. The
RF signal is buffered by Q1 and applied to
the push-pull class A amplifier circuit that
consists of Q2 and Q3. At the input to the
transistors, the RF is converted to a
balanced dual feed by a balun L4 made
from a short length of UT-141 coaxial
cable. Capacitors C12 and C13 provide
DC blocking for the input signal to the
amplifier devices. The RF outputs at the
collectors of the transistors are applied
through C19 and C20, which provide DC
blocking for the output signals. The RF
signals connect to L7, which consists of
UT-141 coaxial cable, that combines the
RF back to a single RF output at a 50Ω
impedance to L8; L8 provides a sample
of the RF.
The main path through L10 is to J5, the
RF output jack of the board (+10 to +20
dBm). The sample of the RF connects to
a splitter that provides a sample output
(0 dBm) at J6 of the board. The other
output of the splitter connects to a peak-
detector circuit, consisting of CR3 and
U3, that provides a DC level at J7
representing the RF output of the UHF
exciter to the front panel meter. R29 sets
up the calibration of the front panel
meter for 100% in the UHF exciter
position when the output power of the
exciter is at +17 dBm peak visual.
The upconverter board is powered by
±12 VDC that is produced by an external
power supply. +12 VDC enters through
J8, pin 3, and is filtered and isolated by
RF choke L9 and shunt capacitors C24
and C33. This circuit isolates the RF
signals of the board from those of other
devices connected to the same +12 VDC
line external to the upconverter board.
The +12 VDC is then applied to the rest
of the board.
4.1.1.8 (A15) x8 Multiplier Board (1227-
1002; Appendix B)
The x8 multiplier board multiplies the
frequency of an RF input signal by a
factor of eight. The board is made up of
three identical x2 broadband frequency
doublers.
The input signal (+5 dBm) at the
fundamental frequency enters through
SMA jack J1 and is fed through a 3-dB
matching pad, consisting of R1, R2, and
R3, to amplifier IC U1. The output of the
amplifier stage is directed through a
bandpass filter, consisting of L2 and C4,
which is tuned to the fundamental
frequency (87 to 114 MHz). The voltage
measured at TP1 is typically +.6 VDC.
The first doubler stage consists of Z1
with bandpass filter L3 and C6 tuned to
the second harmonic (174 to 228 MHz).
The harmonic is amplified by U2 and
again bandpass filtered at the second
harmonic frequency by C10 and L5 (174
to 228 MHz). The voltage measured at
TP2 is typically +1.2 VDC.
The next doubler stage consists of Z2
with bandpass filter C12 and L6 tuned to
the fourth harmonic of the fundamental
frequency (348 to 456 MHz). The fourth

10-kW UHF Transmitter with Chapter 4, Circuit
Feedforward Drive Descriptions
840A, Rev. 0 4-17
harmonic is then amplified by U3 and fed
through another bandpass filter tuned to
the fourth harmonic consisting of L11 and
C18 (348 to 456 MHz). The voltage
measured at TP3 is typically +2.0 VDC.
The final doubler stage consists of Z3
with bandpass filter C20 and L12 tuned
to the eighth harmonic of the
fundamental frequency (696 to 912
MHz). The signal is amplified by U4, U5,
and U6 to a typical value of from +2 to
+4 VDC as measured at test point TP4.
The amplified eighth harmonic is then fed
to the SMA output jack of the board at
J2.
The typical LO signal output level is +15
dBm nominal. The detected sample of
the output of the x8 multiplier board at
TP4 is also fed to the base of Q1, which
forward biases it and lights the green
LED DS1 on the board to indicate that
the LO signal is present.
The +12 VDC for the board enters
through jack J3-3 and is filtered by L7
and C16 before being distributed to the
circuits on the board.
4.1.1.9 (A17) Transmitter Control Board
(1293-1221; Appendix B)
The transmitter control board (1293-
1221) provides the system control
functions and the operational LED
indications that can be viewed on the
front panel of the transmitter. The main
control functions of the board are for
Operate/Standby and Auto/Manual
selection. When the transmitter is
switched to Operate, the board supplies
the enables to any external amplifier
trays. The board also performs the
automatic switching of the transmitter to
Standby upon the loss of the video input
when the transmitter is in Auto. The
board contains a VSWR cutback circuit
which, if the VSWR of the transmitter
increases above 12.5%, will cut back the
output level of the transmitter, as
needed, to maintain a maximum of
12.5% VSWR. An interlock (low) must be
present at J8-24 for the transmitter to be
switched to Operate and, when the
interlock is present, the green Interlock
LED DS5 will be lit.
Operate/Standby Switch S1
K1 is a magnetic latching relay that
controls the switching of the transmitter
from Operate to Standby. When the
Operate/Standby switch S1 on the front
panel of the tray is moved to Operate,
one coil of relay K1 energizes and causes
the contacts to close and apply a low to
U4B-9. If the transmitter interlock is
present, and there is no overtemperature
fault, lows will also be applied to U4B-10,
U4B-11, and U4B-12. With all the inputs
to U4B low, the output at U4B-13 will
also be low. The low biases off Q1, which
turns off the amber Standby LED DS1 on
the front panel, and applies a high to Q2.
This action turns on and lights the green
Operate LED DS2 on the front panel.
When Q2 is biased on, it connects a low
to Q12 and biases it off. This allows the
ALC to be applied to J1, which connects
to any external amplifier trays. The low
from U4B-13 is also applied to Q4 and
Q24, which are biased off, and removes
the disables from J1-4 and J18-1. The
low from U4B-13 connects to Q10, which
is biased on, and to Q6, Q7, Q8, and Q9,
which are also biased on. In addition, it
applies -12 VDC enables at J8-2, J8-3,
J8-4, and J8-5 that connect to any
external amplifier trays. The high applied
to Q2 is connected to Q5 and Q26, which
are biased on, and applies a low enable
to J1-3, which can connect to a remote
operate indicator. The transmitter is now
in the Operate mode.
When the Operate/Standby switch S1 is
moved to Standby, the other coil of relay
K1 energizes; this causes the contacts to
open and a high, +12 VDC, to be applied
to U4B-9. The high at the input causes
the output at U4B-13 to go high. The
high biases on Q1 and applies a low to
the amber Standby LED DS1 on the front
panel. The indicator turns on and applies
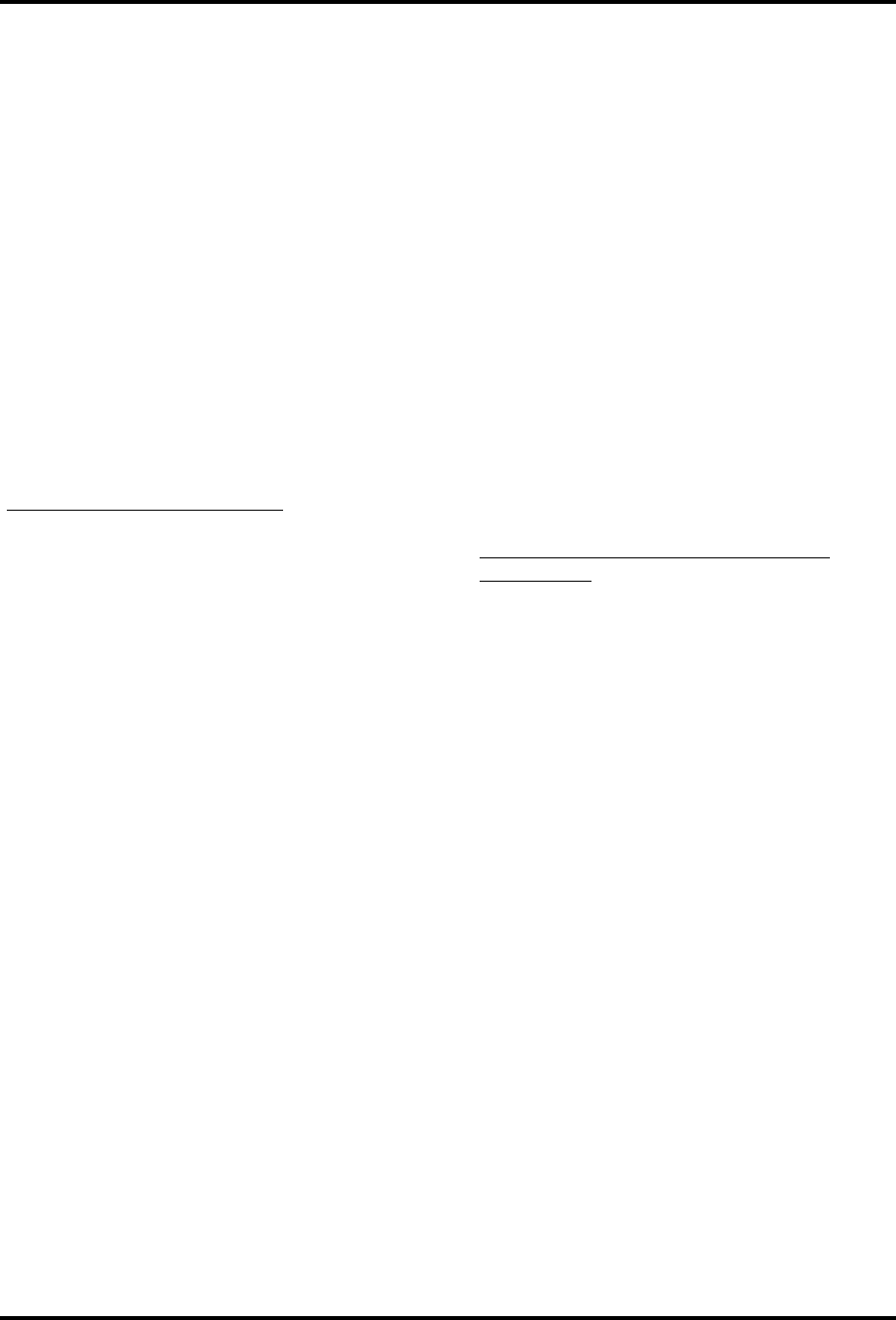
10-kW UHF Transmitter with Chapter 4, Circuit
Feedforward Drive Descriptions
840A, Rev. 0 4-18
a low to Q2, which turns off and
extinguishes the green Operate LED DS2.
In addition, Q12 is biased on; it connects
to U2C, whose output goes low and pulls
the ALC voltages at J1 low, lowering the
gain of the external amplifier trays. The
high from U4B-13 is also applied to Q4
and Q24, which are biased on and apply
disables at J1-4 and J18-1. The high from
U4B-13 connects to Q10, which is biased
off. Q10 Off removes the high from Q6,
Q7, Q8, and Q9, which are biased off,
and removes the -12 VDC enables at J8-
2, J8-3, J8-4, and J8-5 that connect to
the external amplifier trays. The low
applied to Q2 is connected to Q5 and
Q26, which are biased off, and removes
the remote enable at J1-3. The
transmitter is now in the Standby mode.
Automatic/Manual Switch S2
K2 is a magnetic latching relay that
switches the operation of the transmitter
to Automatic or Manual by using
Auto/Manual switch S2 on the front panel
of the tray.
When the S2 switch is set to the Auto
position, the operation of the transmitter
is controlled by the fault circuits and will
stay in Operate even if Operate/Standby
switch S1 is moved to Standby. With the
S2 switch in Auto, a low is applied to one
coil in the relay; this energizes and closes
the contacts. The closed contacts apply a
low to the green Automatic LED DS3,
causing it to illuminate. The low from the
relay connects to U5A, pin 2; U5D, pin
13; Q21; and Q23. Q21 and Q23 are
biased off, which causes their outputs to
go high. The high from Q21 connects to
the amber Manual LED DS4 on the front
panel, biasing it off, and to Q22, biasing
it on. The drain of Q22 goes low and is
applied to J8-7, which will enable any
remote auto indicator connected to it.
The low to Q23 biases it off and removes
the enable to any remote manual
indicator connected to J8-6.
When the S2 switch is set to the Manual
position, the operation of the transmitter
is no longer controlled by the fault
circuits and is controlled by
Operate/Standby switch S1. With the S2
switch in Manual, a low is applied to the
other coil in the relay to energize and
open the contacts. The open contacts
remove the low from the green
Automatic LED DS3 on the front panel
and cause it to not light. The high
connects to U5A, pin 2; U5D, pin 13;
Q21; and Q23. Q21 and Q23 are biased
on, which causes their outputs to go low.
The low from Q21 connects to the amber
Manual LED DS4 on the front panel,
biasing it on, and to Q22, biasing it off.
The drain of Q22 goes high and the high
is applied to J8-7, which will disable any
remote auto indicator connected to it.
Q23 is biased on, which applies a low
enable to any remote manual indicator
connected to J8-6.
Automatic Turning On and Off of the
Transmitter
The transmitter control board also allows
the transmitter to be turned on and off
by the presence of video when the
transmitter is in Auto. When a video fault
occurs due to the loss of video, J7-5 goes
low. The low is applied through W1 on
J10 to Q16, which is biased off, and to
the red Video Loss Fault LED DS9 on the
front panel, which will light. The drain of
Q16 goes high and connects to U5B, pin
5, causing the output at pin 4 to go low.
The low connects to Q18, which is biased
off, and causes the drain of Q18 to go
high. The high connects to U3D, pin 12,
whose output at pin 14 goes high. The
high connects to U5C, pins 8 and 9,
which causes its output at pin 10 to go
low, and to U5A, pin 1, which causes its
output at pin 3 to go low. With switch S2
set to Automatic, a low is applied to U5A,
pin 2, and to U5D, pin 13. When U5A, pin
1, is high and U5A, pin 2, is low, it
causes the output at pin 3 to go low.
When U5D, pin 12, is low and U5D, pin
13, is low, it causes the output to go
high. When U5A, pin 3, is low, it biases
off Q20, which removes any pulldown to
the Operate switch. A high at U5D, pin
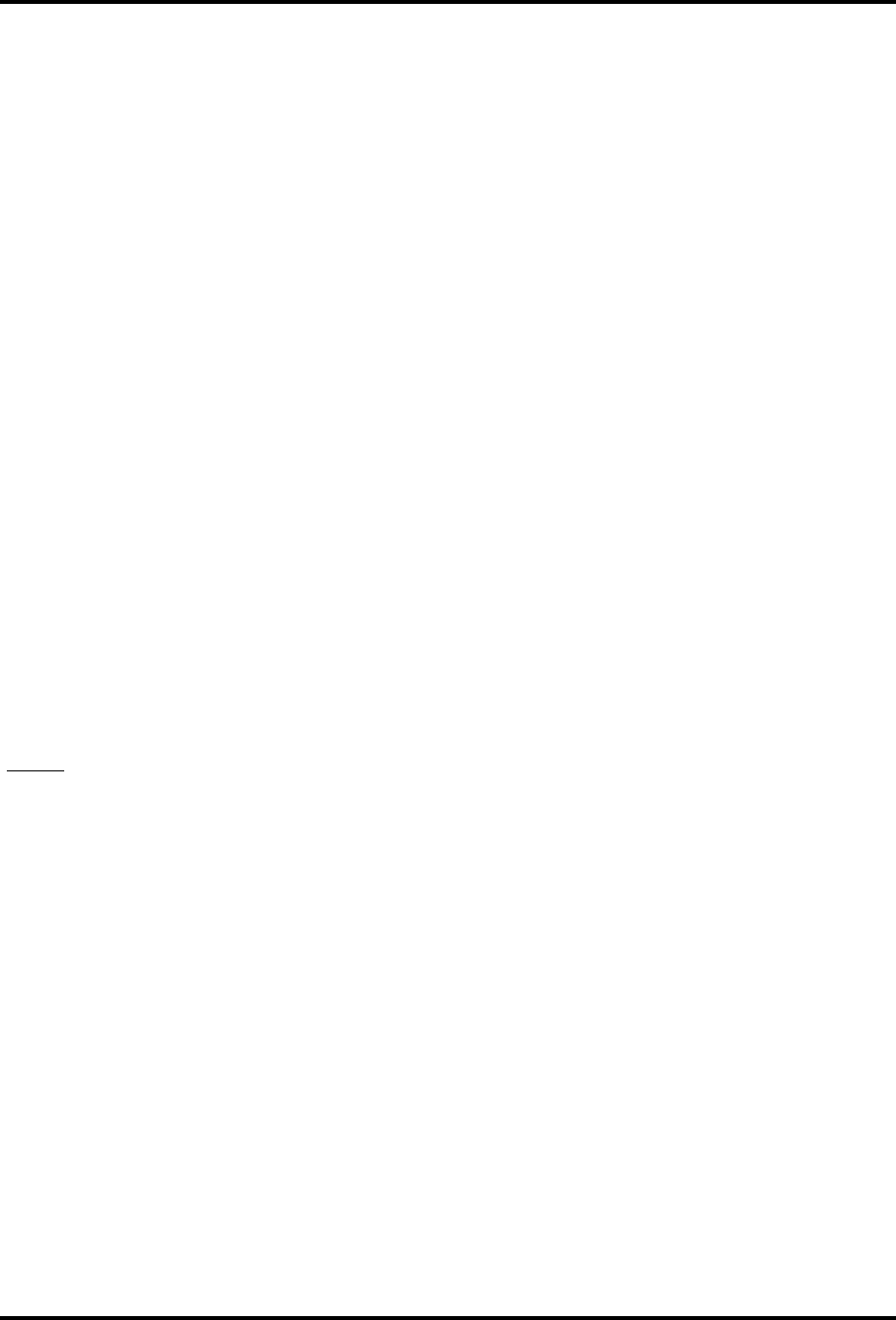
10-kW UHF Transmitter with Chapter 4, Circuit
Feedforward Drive Descriptions
840A, Rev. 0 4-19
11, biases on Q19, which applies a low
enable to the Standby switch; this places
the transmitter in the Standby mode.
When the video is returned, J7-5 goes
high. The high is applied to Q16, which is
biased on, and to the red Video Fault LED
DS9, which is extinguished. The output of
Q16 goes low and connects to U5B, pin
5. If there is no receiver ALC fault, U5B,
pin 6, is also low, which causes the
output at pin 4 to go high. The high
connects to Q18, which is biased on,
causing the drain of Q18 to go low. The
low connects to U3D, pin 12, whose
output at pin 14 goes low. The low
connects to U5C, pins 8 and 9, which
causes its output at pin 10 to go high,
and to U5A, pin 1. With Auto/Manual
switch S2 in Auto, a low is applied to
U5A, pin 2, and to U5D, pin 13. With
U5A, pins 1 and 2, low, its output at pin
3 goes high. With pin 12 of U5D high,
the output of U5D at pin 11 goes low.
With U5A, pin 3, high, it biases on Q20,
which applies a pulldown enable to the
Operate switch. A low at U5D, pin 11,
biases off Q19, which removes any
pulldown to the Standby switch. The
transmitter is switched to Operate.
Faults
There are four possible faults that may
occur in the transmitter and are applied
to the transmitter control board: video
loss fault, VSWR cutback fault,
overtemperature fault, and ALC fault.
There will be no faults to the board
during normal transmitter operations.
The receiver ALC fault circuit will only
function if a receiver tray is part of the
system.
Video Loss Fault. If a video loss occurs,
the transmitter, while in Auto, will go to
Standby after a few seconds, until the
video is returned; at that point it will
immediately revert to Operate. A video
loss fault applies a low from the ALC
board to the video fault input at J7-5 on
the board.
With jumper W1 in place on J10, the
video fault is connected to the red Video
Loss Fault LED DS9 and to Q16. The LED
DS9 on the front panel will light and Q16
will be biased off, causing its drain to go
high. The high is wired to U5B, pin 5,
whose output at U5B, pin 4, goes low.
The low is wired to Q18, which is biased
off; this causes the drain to go high. The
high is connected to U3D, pin 12, which
causes its output at U3D, pin 14, to go
high. The high connects to U5A, pin 1,
and, if the transmitter is in Auto, pin 2 of
U5A is low. With pin 1 high and pin 2
low, the output of U5A goes low and
reverse biases Q20, shutting it off. The
high at U5C, pins 8 and 9, causes its
output at pin 10 to go low. This low is
connected to U5D, pin 12, and, if the
transmitter is in Auto, pin 13 of U5D is
also low. The lows on pins 12 and 13
cause the output to go high, which
forward biases Q19. The drain of Q19
goes low and connects the coil in relay
K1, causing it to switch to Standby.
When the video returns, the video loss
fault is removed from the video fault
input at J7-5. With jumper W1 in place
on J10, the base of Q16 goes high. The
red Video Loss Fault LED DS9 on the
front panel will go out. Q16 is biased on,
causing its drain to go low. The low is
wired to U5B, pin 5, and U5B, pin 6, will
be low if no ALC fault occurs. The two
lows at the inputs make the output at
U5B, pin 4, go high. The high is wired to
Q18, which is biased on and causes the
drain to go low. The low is connected to
U3D, pin 12, which causes its output at
U3D, pin 14, to go low. The low connects
to U5A, pin 1, and, if the transmitter is in
Auto, pin 2 of U5A is also low. With both
inputs low, the output of U5A at pin 3
goes high. The high forward biases Q20
and causes its drain to go low. The low
connects to the operate coil on relay K1
that switches the transmitter to Operate.
The low at U5C, pins 8 and 9, causes the
output at pin 10 to go high. This high is
connected to U5D, pin 12, and, if the
transmitter is in Auto, pin 13 of U5D is
low. The high on pin 12 causes the
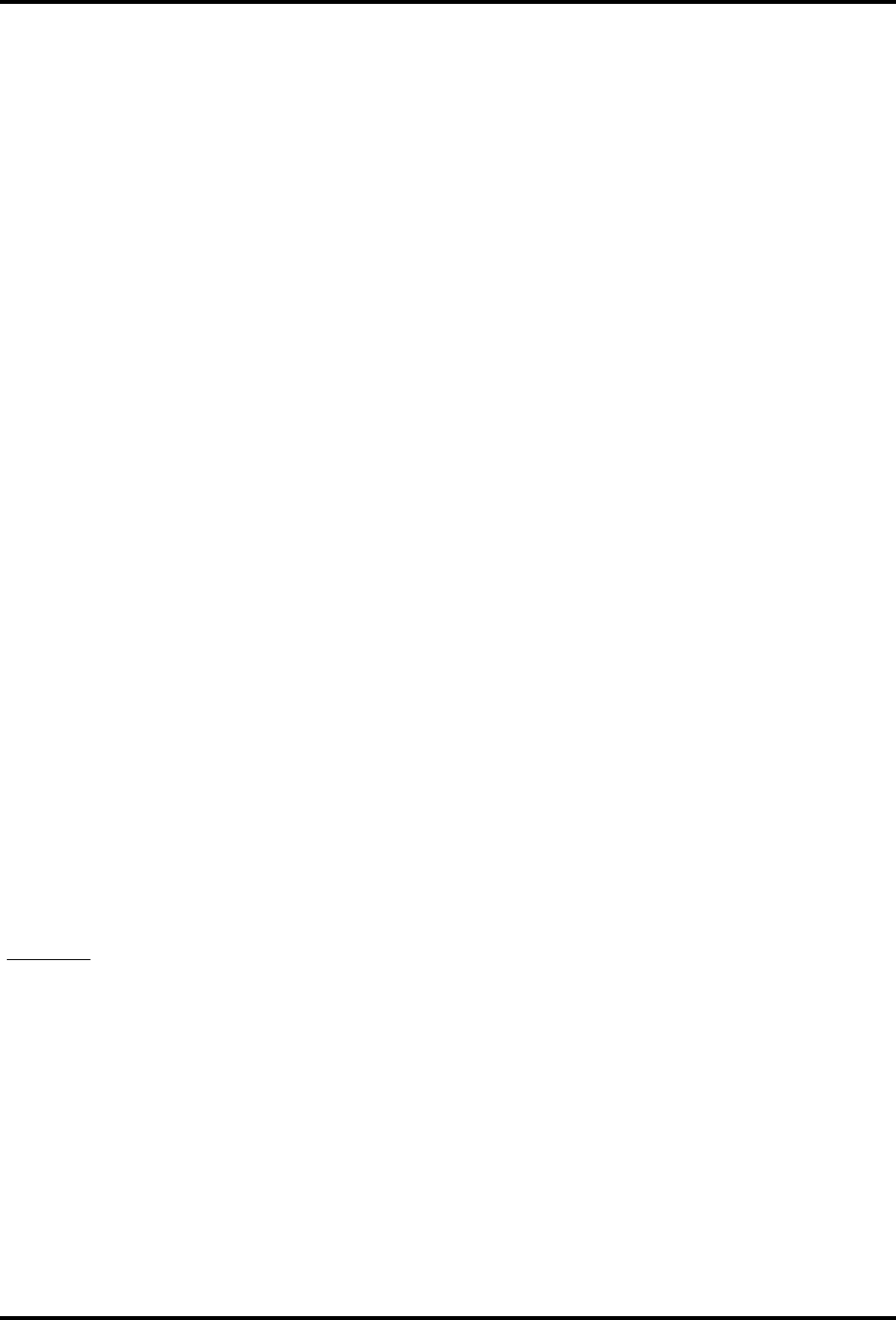
10-kW UHF Transmitter with Chapter 4, Circuit
Feedforward Drive Descriptions
840A, Rev. 0 4-20
output of U5D to go low and reverse bias
Q19. The drain of Q19 goes high and
removes the low from the standby coil in
relay K1.
VSWR Cutback Fault. The reflected
power sample of the RF output of the
diacrode transmitter is connected to J2,
pin 9, of the board. The sample connects
to op-amp U1B, pin 5, which buffers the
signal. The remote reflected sample
connects to U2B, pin 5. If the reflected
sample level increases above the level
set by R22, the VSWR cutback pot, the
output of U2B at pin 7 goes high. The
high is connected to Q11 through CR11,
which is biased on and makes U2C, pin
10, low; this causes U2C, pin 8, to go
low. This low is split and fed out of the
tray at J1-6, J1-7, J1-8, and J1-9. These
are ALC outputs to the amplifier trays
that cut back the output power of those
trays. The low from U2C, pin 8, is also
fed through the coaxial jumper W2 on
J13 and J14 to R73. R73 is a bias adjust
pot that sets the level of the pin
attenuator bias that is available as an
output at J16.
The high at U2B, pin 7, is fed to the base
of Q14 and Q13, which are forward
biased, and produces a low at the drains.
The low connects to the front panel
amber VSWR Cutback LED DS7, causing
it to light and indicate that the tray is in
cutback, and to output jack J8-37 for the
connection to a remote VSWR cutback
indicator.
Metering
The front panel meter connects to J3-1
(-) and J3-2 (+) on the board; these are
the outputs of Front Panel Meter switch
S3. The front panel meter has six
metering positions that are controlled by
S3: Audio, Video, % Aural Power, %
Visual Power, % Exciter, and ALC.
The video sample connects to the board
at J5-4 and is connected through R20,
the video calibration pot, to position 6 of
switch S3. The audio sample enters the
board at J5-6 and is connected through
R19, the audio calibration pot, to position
7 of switch S3. The visual sample
connects to the board at J2-5 and is
connected through buffer amplifier U1D
and 100Ω resistor R86 to position 4 of
switch S3. The aural sample connects to
the board at J2-7 and is connected
through buffer amplifier U1C and 100W
resistor R85 to position 5 of switch S3.
The exciter sample connects to the board
at J2-3 and is connected through buffer
amplifier U1A and 100Ω resistor R87 to
position 2 of switch S3. The ALC sample
connects to the board at J6-1 and is
connected through buffer amplifier U2C,
and R15, the ALC calibration pot, which
adjusts the output of U2A, pin 1, through
a 100Ω resistor R18 to position 1 on
switch S3.
Typical readings on the meter are:
• Video = 1 Vpk-pk at white
• % Visual Power = 60% to 90%
• % Aural Power = 60% to 90%
• % Exciter = The level on the meter
needed to attain 100% output power
from the transmitter
Refer to the test specifications sheet for
the transmitter for the actual reading:
• ALC = .8 VDC
• Audio = ±25 kHz with a balanced
audio input or ±75 kHz with a
composite audio input
Samples of the exciter at J1-10, the
visual at J8-26, the aural at J8-27, and
the reflected at J1-5 are provided for
remote metering.
U6 is a temperature-sensor IC that gives
the operator the ability to measure the
temperature inside the tray by measuring
the voltage at TP1. The sensor is set up
for +10 mV equals 1° F (for example,
750 mV equals 75° F.)

10-kW UHF Transmitter with Chapter 4, Circuit
Feedforward Drive Descriptions
840A, Rev. 0 4-21
Operational Voltages
The +12 VDC needed for the operation of
the transmitter control board enters the
board at jack J4, pin 3. C28, L1, and L3
are for the filtering and isolation of the
+12 VDC before it is split and applied to
the rest of the board. The -12 VDC
needed for the operation of the board
enters the board at jack J4, pin 5. C29
and L2 are for the filtering and isolation
of the -12 VDC before it is split and
applied to the rest of the board.
When the +12 VDC is connected to the
board, it is split; four of the +12 VDC
outputs are fed out of the board at J8-16,
J8-17, J8-18, and J8-19 through diode
CR7, CR8, CR9, or CR10 and resistor
R50, R51, R52, or R53 to any external
amplifier trays for use in their logic
circuits. The resistors are for current
limiting and the diodes are to prevent
voltage feedback from the external
amplifier trays.
4.1.1.10 (A19) Visual/Aural Metering
Board (1265-1309; Appendix B)
The visual/aural metering board provides
detected outputs of the visual and aural
output samples that are used for
monitoring on the front panel meter. The
board also provides adjustments for the
calibration of the readings on the meter.
These readings are attained from
samples of the forward power and
reflected power outputs of the tray.
A forward power sample, visual + aural,
is applied to SMA jack J1 on the board.
The input signal is split, with one path
connected to forward power sample SMA
jack J2 for monitoring purposes. The
other path is connected through C1 to
CR2, R4, R5, R6, C4, and CR1, which
make up a detector circuit. The detected
visual + aural signal is amplified by U6B
and its output is split. One amplified
output of U6B connects to the aural level
circuit and the other output connects to
the visual level circuit.
Aural Level Circuit
One of the detected visual + aural level
outputs of U6B connects through C6 to
the intercarrier filter circuit that consists
of R13, R14, L1, C7, and C8; C8 and L1,
the intercarrier filter, can be adjusted for
a maximum aural reading. The filter
notches out the video + aural and only
leaves the 4.5-MHz difference frequency
between the visual and aural, which is a
good representation of the aural level.
The 4.5-MHz signal is fed to buffer
amplifier U6A. The output of U6A is
detected by diode detector CR3 and U1A
and then fed through aural calibration
control R20 to amplifier U2D. The
amplified output of U2D is split, with the
main output connected through R21 to
J6, pin 1, which supplies the aural level
output to the front panel meter for
monitoring. The other output of U2D is
connected to aural null adjust R51 and
offset null adjust R48, which are adjusted
to set up the visual power calibration.
Visual Level Circuit
The other detected visual + aural level
output from U6B is connected to U1C
and, if there is no scrambling, connects
directly to intercarrier notch L3, which is
adjusted to filter out the aural and the
4.5-MHz intercarrier frequencies, leaving
only a visual-with-sync output. The
visual-with-sync output is fed to a peak-
detector circuit consisting of CR5 and
U2A. The signal is then fed through visual
calibration control R28, which is adjusted
for a 100% visual reading with no aural,
to amplifier U2B. The amplified visual
peak of sync output is connected to
comparator U2C. The other input to U2C
is the level set by aural null adjust R51,
which is adjusted for 100% visual power
after the aural is added and the peak
power is adjusted back to the reference
level. Inputs to U2C also come from
offset null adjust R48, which is adjusted
for 0% visual power with the transmitter
in Standby. The adjusted output is
amplified by U3D and connected to the
other input of U2C. The output of U2C
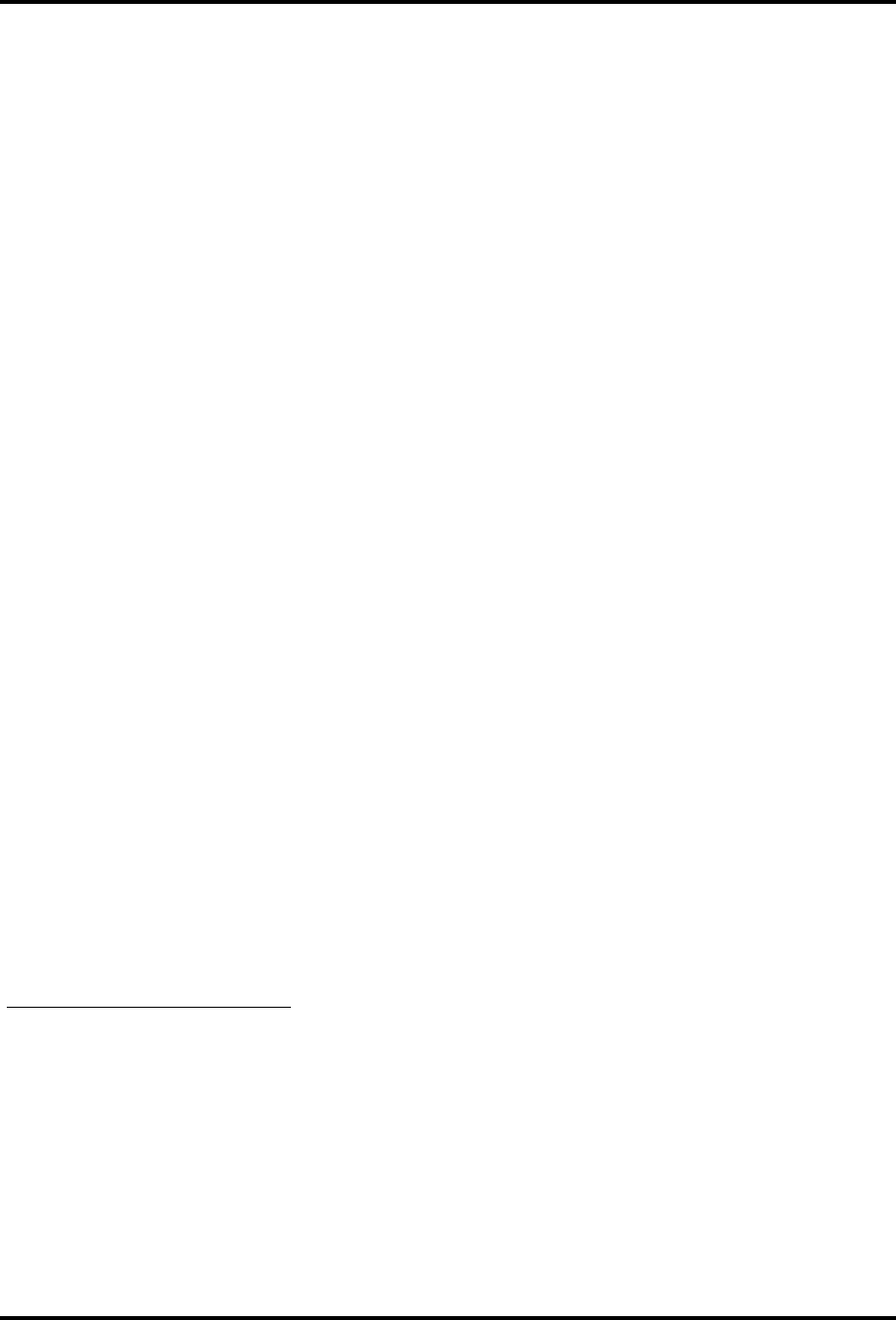
10-kW UHF Transmitter with Chapter 4, Circuit
Feedforward Drive Descriptions
840A, Rev. 0 4-22
connects to J6, pins 2 and 3, which
supply the peak of sync visual level
output to the front panel meter for
monitoring.
If this board is operated with scrambling,
using suppressed sync, the visual level
circuit operates differently than described
above because there is no peak of sync
present on the forward sample input. For
the board to operate properly, a timing
pulse from the scrambling encoder must
connect to the board at J4. This timing
pulse is converted to sync pulses by U4A
and U4B, which control the operation of
Q2. Intercarrier notch L2 is tuned to
remove any visual + aural signal that
may remain.
The sync amplitude is controlled by gate
amplitude adjust R25 and then applied to
the minus input of U1C. At this point, it is
inserted into the visual + aural signal
that is connected to the plus input of
U1C, producing a peak of sync in the
signal. The output of U1C is connected to
intercarrier notch L3, which is adjusted to
filter out the aural and the 4.5-MHz
intercarrier frequencies. The visual-with-
sync output is fed to a peak-detector
circuit, consisting of CR5 and U2A, and
then fed through visual calibration control
R28 to amplifier U2B. The amplified
visual peak of sync output is connected
to J6, pins 2 and 3, that supply the peak
of sync visual level output to the front
panel meter for monitoring. R32 moves
the pulse to where the sync should be
and R25 sets the visual metering
calibration with no sync present.
Voltages for Circuit Operation
The ±12 VDC is applied to the board at
J5. The +12 VDC is connected to J5, pin
3, and is isolated and filtered by L4 and
C34 before it is connected to the rest of
the board. The +12 VDC also connects to
U5, a 5-VDC regulator that provides the
voltage needed to operate U4. The -12
VDC is applied to J5, pin 1, and is
isolated and filtered by L5 and C35
before it is connected to the rest of the
board.
4.1.1.11 (A4-A14) Channel Oscillator
Assembly, Dual Oven (1145-1202;
Appendix B)
The channel oscillator assembly contains
the channel oscillator board (1145-1201)
that generates a stable frequency-
reference signal of approximately 100
MHz. The channel oscillator assembly is
an enclosure that provides temperature
stability for the crystal oscillator. An SMA
output at jack J1 and an RF sample at
BNC connector jack J2 are also part of
the assembly.
Adjustments can be made through access
holes in the top cover of the assembly.
These adjustments are set at the factory
and should not be tampered with unless
it is absolutely necessary and the proper,
calibrated equipment is available. R1 is
the temperature adjustment; C11 is the
course-frequency adjustment; and C6,
C18, L2, and L4 are adjusted for the
maximum output of the frequency as
measured at jack J1. C9 is the fine-
frequency adjustment.
The +12 VDC for the assembly enters
through FL1 and the circuit-ground
connection is made at E1.
4.1.2 (A1-A9) 3-Watt UHF Amplifier
Tray (1068203; Appendix A)
The modulated RF carrier signal (+8
dBm) from the 3-watt UHF amplifier
enters through J1 and is filtered by (A1)
a bandpass filter (1007-1101). The signal
(+7 dBm) is then fed to (A2) the AGC
board (1007-1201). The AGC board
controls the overall gain of the amplifier
tray by comparing a sample of the output
signal from the dual peak detector board
through the AGC control board. An AGC
reference voltage is generated either
externally or internally depending on the
system operation and the position of the
jumper on J7. The jumper should be
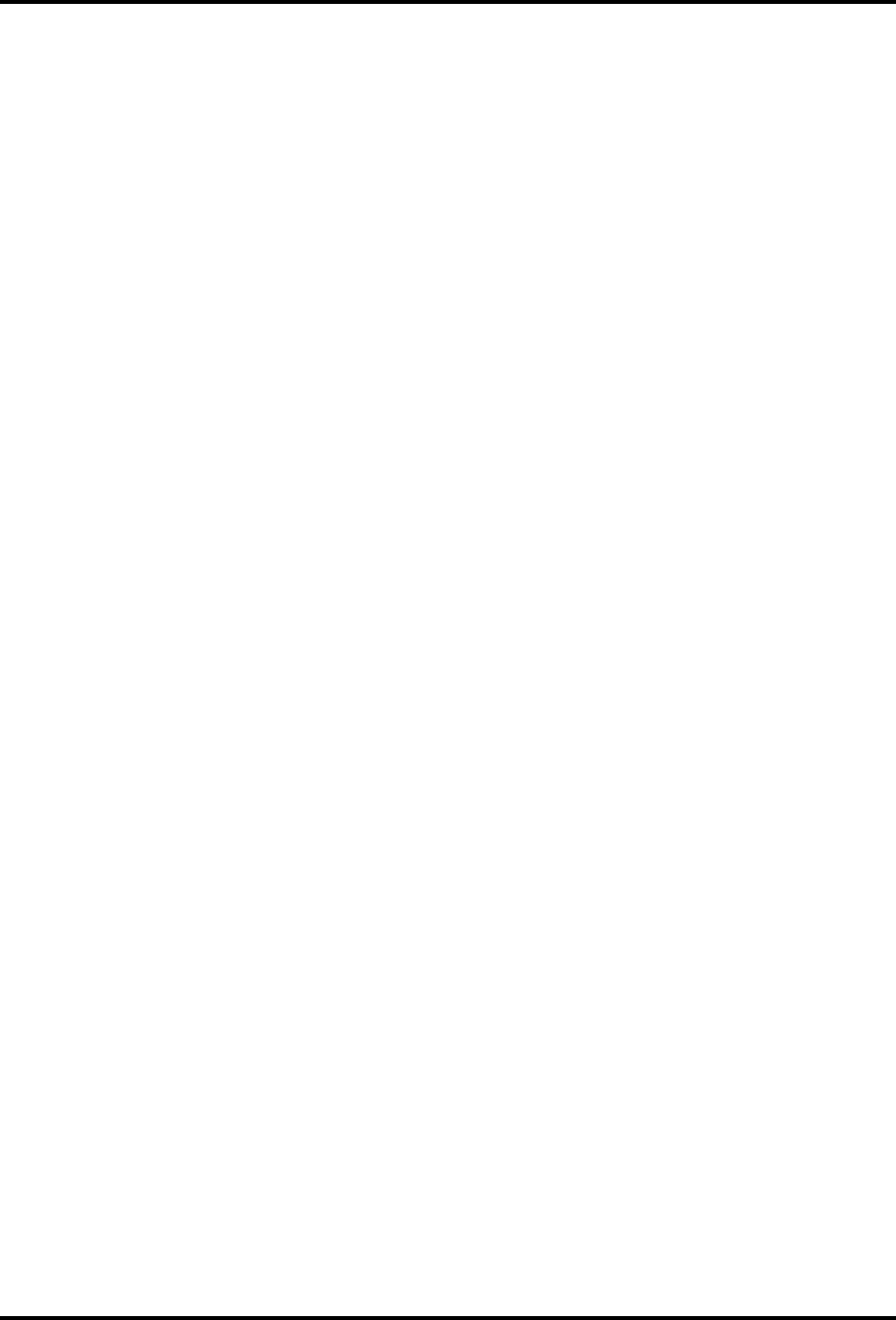
10-kW UHF Transmitter with Chapter 4, Circuit
Feedforward Drive Descriptions
840A, Rev. 0 4-23
between J7-1 and J7-2 for the operation
of the diacrode (external reference).
The (A25) AGC control board (1137-
1201) compares a sample of the output
of the diacrode with a sample of the 3-
watt tray. The front panel gain control R2
adjusts the overall gain of the tray. The
output voltage of the comparator drives a
pin attenuator circuit that corrects for
drift by maintaining a constant output
even though temperatures, therefore
gain, of the amplifier devices in A3, A5,
or A7 may vary.
The AGC board also contains circuitry
that monitors the AGC level and provides
for an AGC override detector. If the final
3-watt amplifier stage is overdriven, the
AGC override LED DS2 on the front panel
will light to indicate a cutback of the AGC
that cuts the gain of the tray. The AGC
override detector is also used as the
system Mute (Standby, VSWR fault, and
other faults). There is also a ramp control
signal input to the AGC control board.
When the 3-watt amplifier is externally
enabled, the drive output of the amplifier
ramps up over a time frame of several
seconds. The output of the pin attenuator
is amplified to approximately 0 dBm and
fed to output jack J2 of the board.
The RF from the AGC board is fed to
(A27) the UHF phase shifter board
(1142-1315). The phase-corrected signal
is then amplified by (A3) the UHF
amplifier/regulator board (1007-1204)
that has a nominal gain of +17 dB. Next,
the signal (+17 dBm typical) is amplified
by (A5) the 3-watt amplifier board #1
(1007-1211) that has a nominal gain of
+9 dB. The operating drive current, no
RF input, for the 3-watt amplifier board
#1 is set by the (A6) opto-bias board
(1002-1109). The signal (+26 dBm
typical) is amplified further by (A7) the
3-watt amplifier board #2 (1007-1211)
that also has a nominal gain of +9 dB.
The operating drive current for the 3-
watt amplifier board #2 is set by (A8) the
opto-bias board (1002-1109).
The output (typically +35 dBm) of the
second 3-watt amplifier board is fed to
(A29) the overdrive protection board
(1142-1626). The signal enters the board
at J4 and is connected directly out of the
board at J5. A sample of the RF signal is
coupled off the input and fed to a
detector circuit to set up the AGC
override level. If the RF output level of
the transmitter increases to 120%, the
override circuit will cut back the output of
the 3-watt tray to prevent damage to the
amplifier devices.
The output of the overdrive protection
board is fed to (A9) a dual coupler
assembly (1007-1208) that supplies a
forward and reverse power sample to
(A10) the dual peak detector board
(1137-1510). The dual peak detector
drives the front panel meter for a %
Reflected Power reading and also
provides a forward power sample (inner
loop AGC) to (A25) the AGC control
board (1137-1201). The AGC control
board provides an output to the front
panel meter for the % Forward Power
reading and also provides an output to
the AGC board that is used as the AGC
sample of the output. If an outer loop
AGC is used from an external amplifier
tray, it is fed to the AGC control board
through J5 on the rear of the tray. The
output from the dual coupler is directed
to the RF output jack J2 on the rear of
the tray (+35 dBm).
Two power supplies are used in the tray.
The (A16) +24V power supply board
(1007-1207) supplies power for the
amplifier devices through the opto-bias
boards in the 3-watt amplifiers and the
UHF amplifier/regulator board. The (A22)
general purpose ±12V power supply
board (1062-1013) supplies voltage to
the rest of the boards in the tray.
AC is applied to the tray through J4 on
the rear panel and is connected to
terminal block TB2. MOVs VR1 and VR2
are provided as protection from
transients or surges on the AC input line.
When CB1, the 2.5-amp circuit breaker,
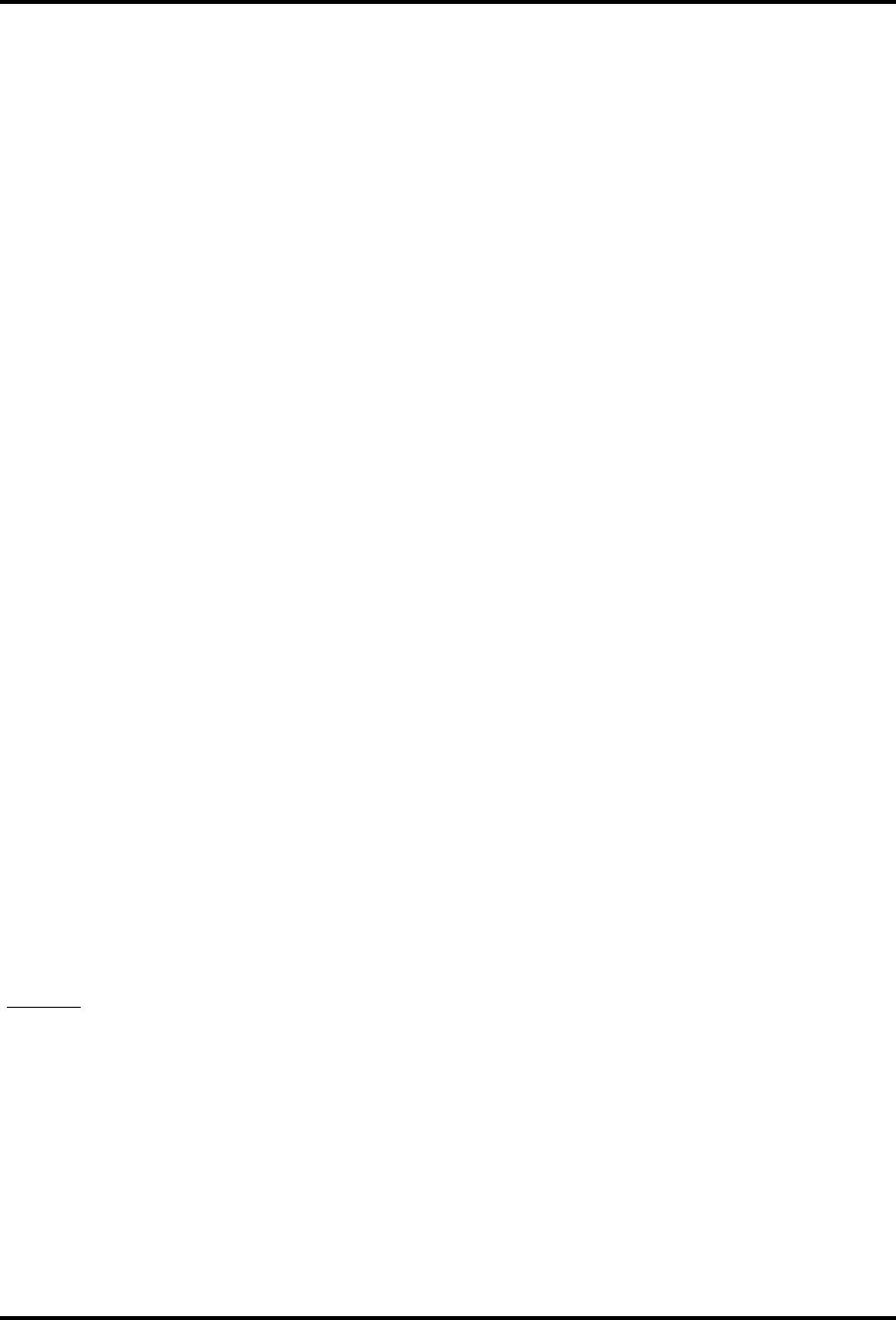
10-kW UHF Transmitter with Chapter 4, Circuit
Feedforward Drive Descriptions
840A, Rev. 0 4-24
is switched on, AC is applied to fans A19
and A20 and also to (A21) the step-down
transformer for the ±12V power supply.
The stepped-down AC is applied to (A22)
the ±12V power supply board (1062-
1013) that supplies the regulated ±12V
to the rest of the boards in the tray. LEDs
DS1 for +12V and DS2 for -12V on the
board will light to indicate that the power
supply is operational.
Even with the circuit breaker switched
on, the +24V power supply will not turn
on until the power supply enable control
line J3-8 is taken Low (Enabled). This
occurs by jumpering J3-8 to J3-7 or by
an external pull-down, which is normally
provided by the power supply Enable
from the metering control panel.
With the pull-down present, (A11) the
power supply control board (1007-1202)
will energize (A12) the isolation relay
board (1002-1108). The 120 VAC is then
applied to (A13) the toroid and then to
(A14) the full-wave bridge rectifier
network that supplies approximately 40
volts to the +24 volt power supply board.
4.1.3 (A1-A6 and A1-A7) 250-Watt
Amplifier Trays (1044027, low
band/1044028, mid band/1044029,
high band; Appendix A)
The 250-watt amplifier tray, with an RF
input of +24 dBm peak visual and 10%
aural, provides an average output power
level of +54 dBm peak visual. The
amplifier utilizes feedforward circuitry to
minimize distortion and increase output.
RF Path
The input to the 250-watt amplifier tray
at the BNC-type connector jack J1 is the
diplexed on-channel visual + aural signal.
The input RF is connected to J1 of (A1-
A1) the single stage amplifier assembly
that is mounted on (A1) the amplifier
enclosure. The (A1-A1) single stage
amplifier assembly, which contains a
generic single stage amplifier board
(1265-1415) and the required frequency
determining kit, is a class A amplifier
supplying 11.5 dBm of gain at J2. The
output is fed to (A1-A3) the stripline
coupler board. The coupler board
supplies a –10 dB sample for (A3) the
phase/gain adjust module at J3. This
sample is the linear portion of the
feedforward signal. The output of the
stripline coupler board is fed to (A1-A5)
the single stage amplifier assembly, class
AB. The single stage amplifier assembly
is mounted on (A1) the amplifier
enclosure and consists of a generic single
stage amplifier board, class AB (1286-
1234), with the required frequency
determining kit. This assembly has a
minimum gain of approximately 8 dB.
The (A1-A5) amplifier assembly output is
connected to (A19-A6) the splitter board.
The splitter board is a two-way wilkinson
splitter that feeds the inputs of (A19-A7,
A19-A8) the dual output power amplifier
assemblies, class AB. The dual output
power amplifier assembly, class AB, is
made using a generic dual stage
amplifier board, class AB (1265-1404),
and the appropriate frequency dependent
kit. The two assemblies, A1-A7 and A1-
A8, are identical. The dual output power
amplifier board uses two PTB20101
transistors in parallel-biased class AB to
amplify the signal. The bias adjust R106
sets the operating current for Q101 and
the bias adjust R206 sets the operating
current for Q201. The output of both
assemblies is soldered directly to (A19-
A9) the 2-way combiner board. The total
gain through the splitter board, amplifier
assemblies, and combiner board is a
minimum of 8 dB.
The (A19-A9) 2-way combiner board is
frequency dependent for low-band,
middle-band, and high-band. The
combiner board also has a –40 dB
coupler for forward and reflected power
samples. The forward port J1 is cabled to
(A5) the dual stripline coupler board as a
sample for the feedforward circuit. This is
the non-linear portion of the feedforward
signal and is used as a reference to
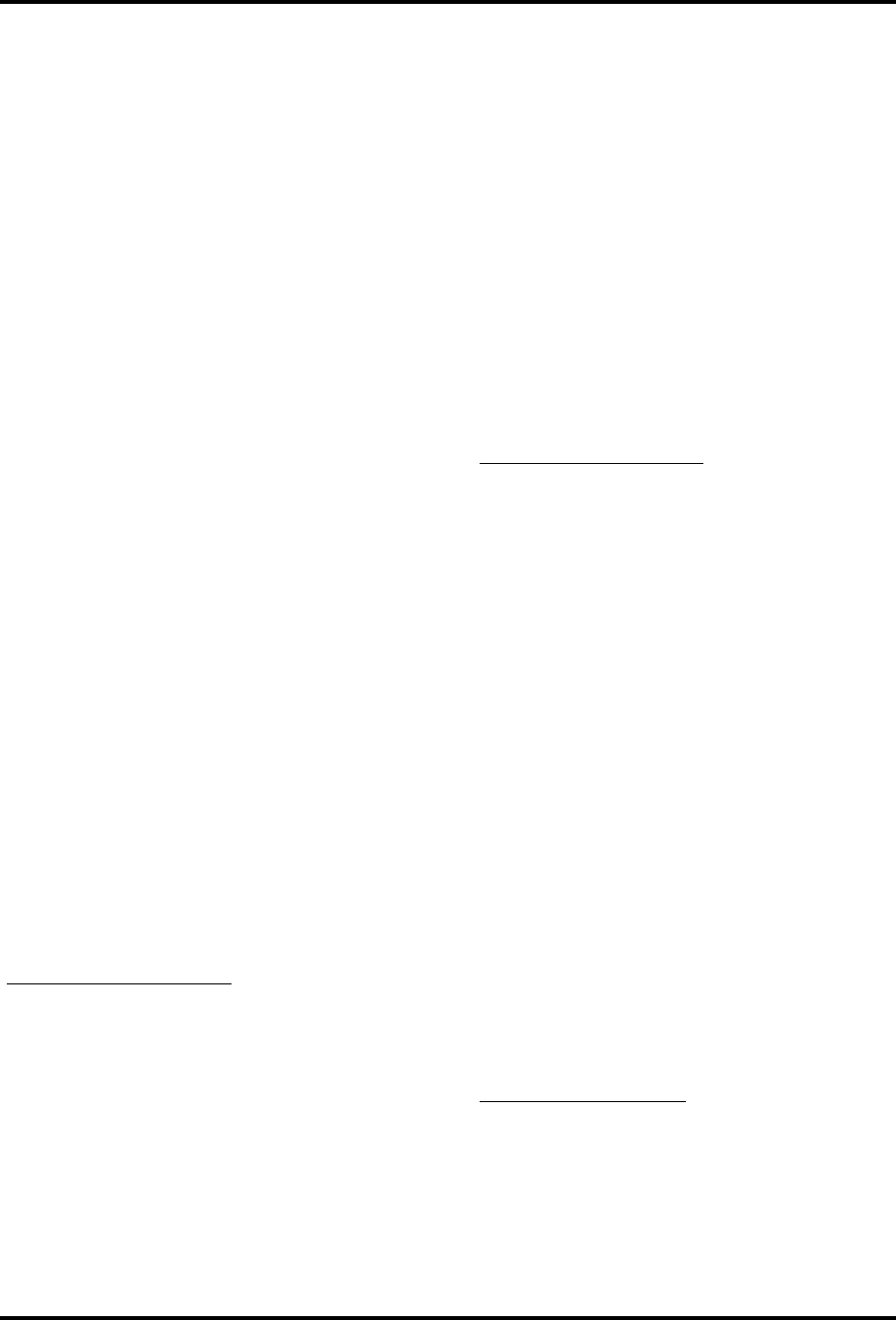
10-kW UHF Transmitter with Chapter 4, Circuit
Feedforward Drive Descriptions
840A, Rev. 0 4-25
cancel any remaining non-linear
distortion at the output.
The reflected port is terminated into a 1-
watt, 50Ω load (A19-A10). After the
linear and non-linear samples have been
matched for gain and delay, and their
phases have been adjusted to a 180°
difference, they are summed together in
the (A5) dual stripline coupler board.
From A5-J2, the mixed signals are fed to
the (A20) correction phase/gain
enclosure at J1. The (A20-A1) error
amplifier phase/gain module is used to
match the gain of the correction path to
the output level of the main amplifier at
the RF O/P part of the (A7) 7 dB coupler.
The phase/gain module also sets the
180° phase imbalance between the two
signals. These two signals, when
combined, cancel most of the distortion
in the signal at the RF output connection.
The A20 module is terminated in the
reject load (A19-A18) in (A19) the
amplifier enclosure. The RF output from
the coupler output is fed to the input, J1,
of (A8) the UHF coupler assembly. J3,
the forward sample on the coupler board,
is fed to J1 of (A17) the peak detector
board. The reflected sample at J4 is
terminated into a 1-watt, 50Ω load. The
output, J2, is fed to (A10) the circulator,
which protects the tray from high-
reflected power, to the output of the tray
at the N-type connector J2. Any reflected
power at J2 is fed to (A2-A6) the reject
load/coupler board mounted inside (A1)
the correction amplifier enclosure.
Feedforward Correction
The feedforward correction circuits
consist of phase and gain adjustment
boards, delay lines, and amplifiers to
sample and cancel any non-linear
distortions introduced into the RF signal
by the power amplifiers. A sample of the
linear RF signal sampled at (A19-A3) the
stripline coupler board is adjusted and
amplified to be of equal gain and 180°
out of phase with the non-linear sample
from the (A19-A9) 2-way combiner
board. The linear sample is phase
adjusted through the use of C1 and C2
on the (A3) phase/gain adjust module.
The gain for the module is set by R22 on
the (A16) amplifier control board. This
linear signal is combined with the non-
linear signal at (A5) the stripline coupler
board. The combined out-of-phase non-
linear and in-phase linear signal is
amplified and then combined with the RF
signal at the 7-dB coupler board. The
gain of the combined signals is controlled
on the amplifier control board by R20 and
they are phase adjusted by R29 on the
same board. The resulting output signal
will have a 20 dB cancellation of non-
linearities.
Amplifier Control Board
The (A16) amplifier control board
provides output level sample inputs to
(A12) the meter and protection of the
tray against overheating. The (A8) UHF
coupler board and (A2-A6) the reject
load/coupler board supply forward and a
reflected output power samples to (A17)
the dual peak detector board. The dual
peak detector board takes the forward
and reflected output power samples and
provides peak-detected DC levels to the
amplifier control board and uses them for
metering purposes. If an
overtemperature fault occurs because
one of (A1-A13 or A1-A14) the thermal
switches closes due to the overheating of
the output amplifier heatsink, the +5
VDC inhibit to the switching power supply
will be applied. This will disable the
switching power supply. The amplifier
control board can be adjusted to set the
calibration of the front panel meter for
the Forward, Reflected, and Power
Supply positions.
Operation of the Tray
The 220 VAC input needed to operate the
tray connects to the tray at J3 and is
supplied to the rest of the tray when the
circuit breaker, CB1, is switched on. The
input AC connects to (A11) a
+26.5V/1500W switching power supply
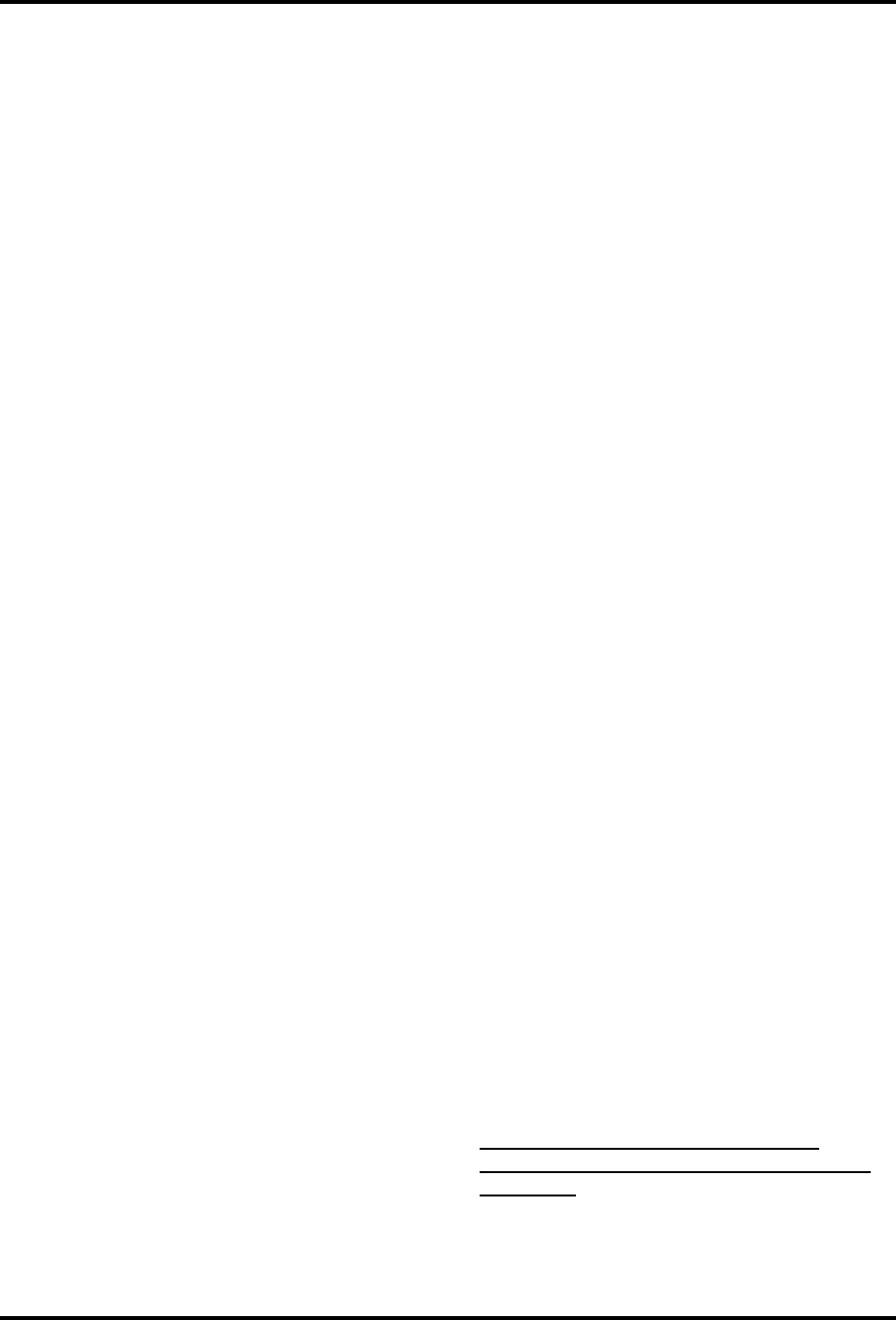
10-kW UHF Transmitter with Chapter 4, Circuit
Feedforward Drive Descriptions
840A, Rev. 0 4-26
that provides the +26.5 VDC to the two
cooling fans and, when the tray is
enabled, through the amplifier protection
board to the rest of the boards in the
tray. The enable is applied to the tray at
J4-5 on the back of the tray. The output
of the switching power supply is
connected to (A15) the amplifier
protection board and also to (A13 and
A14), which are two fans used for cooling
the tray. The amplifier protection board
provides 7-amp fused protection of the
+26.5 VDC outputs before they are
distributed to the amplifier boards in the
tray. An external +12 VDC needed for
the operation of the status LEDs mounted
on the amplifier control board is applied
to the 250-watt amplifier tray, from the
UHF upconverter tray, through J4-7. The
+12 VDC is present when the main AC is
applied to the UHF upconverter tray.
4.2 (A2) 10-kW Diacrode Amplifier
(1299-1100; Appendix A)
4.2.1 10-kW Bias Power Supply
Board, 230 VAC Input (1181- 1001;
Appendix B)
The 10-kW bias power supply board
provides the -80 VDC bias voltage,
typical setting, that is applied to the
control grid of the TH610 diacrode power
tube. This tube is mounted in the
TH18610 cavity assembly in the 10-kW
amplifier assembly.
The bias power supply board (1181-
1001) has a 230 VAC input that is
applied to J1, pins 1 and 4, when the bias
circuit breaker on the AC distribution
panel is switched on, and (A3) the
isolation relay board, part of the control
and bias power supply assembly, is
energized. The 230 VAC is applied to a
full-wave bridge network, consisting of
CR1 to CR4, that rectifies the AC. The
output of the full-wave bridge is filtered
by capacitors C1 and C10 and applied to
a shunt-regulator circuit that utilizes
comparator IC U1. The shunt path
includes VR1, Q1, and U1; R10 is the
bias adjust that applies the control
voltage to the (+) terminal of U1 at pin
12. The negative output of IC U1 at pin
14 connects to the base of Q1 and sets
up the biasing for the transistor. The
amount of forward bias that is applied to
the transistor determines the voltage
drop across the transistor. The value of
the output voltage, as measured across
zener diode VR1 and Q1, is variable
because of the changes in the voltage
drop across the transistor. The bias
voltage output of the board at J3, pins 1
and 2, is typically adjusted for -80 VDC.
The supply voltages to U1 are set at
approximately -1 VDC and -11 VDC by
zener diode VR2. The main current path
to the tube is from ground through R4,
R17, and R8 to the tube.
VR8 and VR9 are protection zener diodes
that prevent the output voltage from
rising above -174 VDC. CR7 prevents the
output from going positive and causing
damage to the tube. VR10 and VR11 are
zener diodes that prevent voltage spikes
above +10 VDC or below -10 VDC from
entering the voltage metering circuit if an
arc occurs in the tube or in the tube
cavity assembly. VR6 and VR7 are zener
diodes that prevent voltage spikes above
+10 VDC or below -10 VDC from entering
the current metering circuit if an arc
occurs in the tube or in the tube cavity
assembly. If R4 opens, VR4 and VR5
prevent the voltage on the floating
ground from rising above a maximum of
4 VDC.
The 5 kΩ bias adjust pot R10 is located
on the front, left-hand side of the
amplifier assembly, behind the swing-out
panel. It connects to J2, pins 3, 5, and 6,
on the board. The bias adjust pot sets
the bias (grid) voltage output level, -80
VDC (typical). The bias is adjusted for
1.5 amps of static plate current.
Note: The static plate current is
adjusted without RF drive applied to
the tube.
R14 calibrates the bias voltage reading at
J2, pin 8, that is applied to the voltage
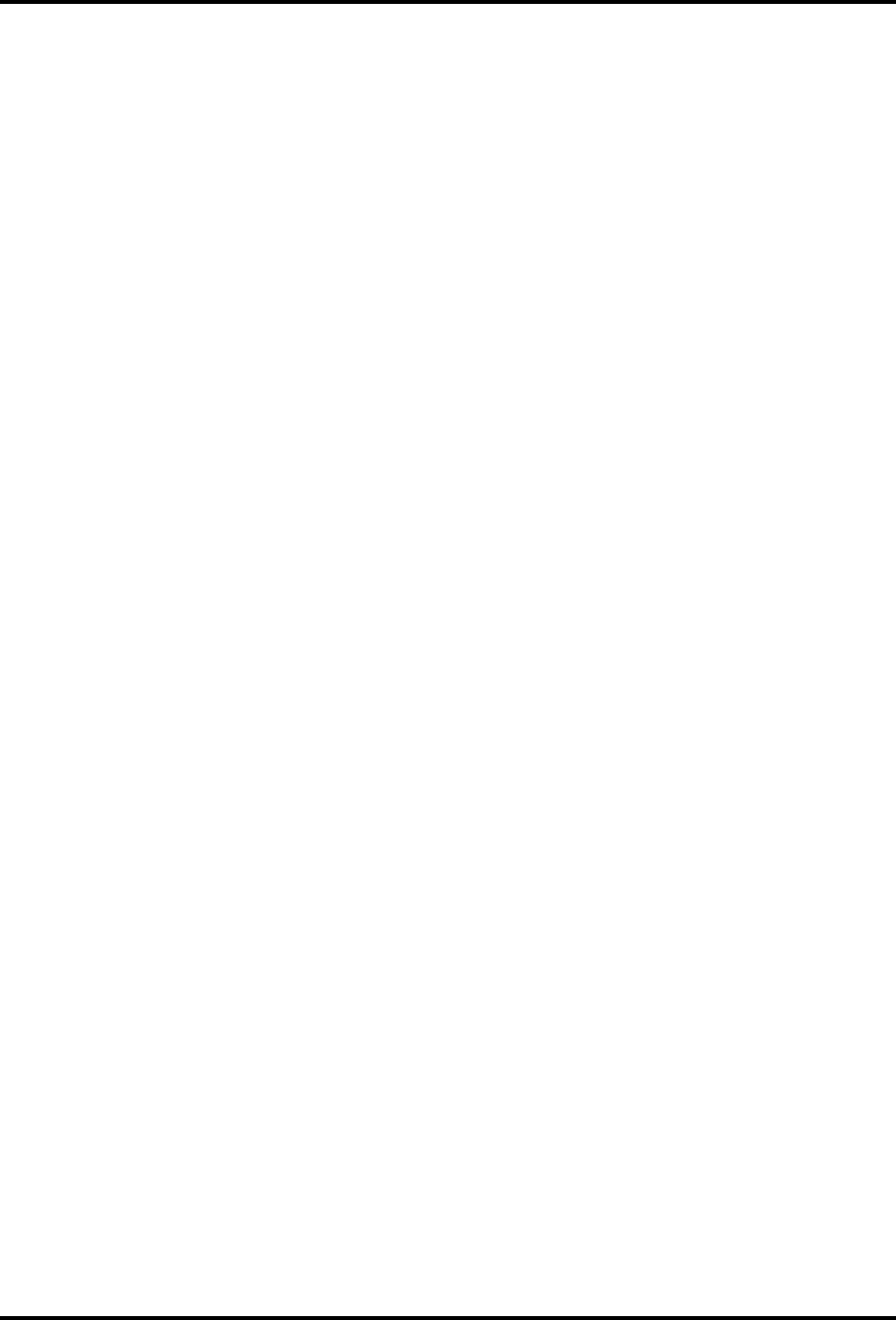
10-kW UHF Transmitter with Chapter 4, Circuit
Feedforward Drive Descriptions
840A, Rev. 0 4-27
meter on the metering control panel. R6
calibrates the bias (control grid) current
meter reading at J2, pins 1 and 2, that is
applied to the current meter on the
metering control panel. These meter
calibration adjustments were set at the
factory for typical operation and should
not need adjustments at this time.
4.2.2 Control and Bias Power Supply
Assembly
The control and bias power supply
assembly (1181-1402) contains two
separate power supplies. The control
power supply consists of input terminal
block TB2; T1, a step-down transformer;
(A1) a ±12 VDC power supply board
(1092-1206; Appendix B); and TB4, an
output terminal block. The bias power
supply consists of input terminal block
TB1; (A3) an isolation relay board
(1002-1108; Appendix B); (A2) a bias
power supply board (1181-1001;
Appendix B); and TB3, an output
terminal block.
The 220 VAC main input to the control
power supply connects to terminal block
TB2, terminals 1A and 3A (neutral) and
4A (ground). VR3 and VR4 are metal-
oxide varistors (MOVs) that protect the
supply from any AC input line surges.
The 220 VAC is applied to the terminal
block as long as the control circuit
breaker on the AC control assembly is
switched on. The AC is directed to T1, a
step-down transformer, that produces
two AC outputs. The two stepped-down
AC outputs connect to J1, pins 1 and 4,
and J1, pins 7 and 8, on (A1) the ±12
VDC power supply board. The AC inputs
are full-wave bridge rectified and filtered
and regulated to produce the ±12 VDC
outputs at TB4 that connect to the
control circuits in the metering control
panel. This also produces the +12 VDC
that is sent to the isolation relays in the
power supplies and the blower
assembly.
The 220 VAC main input to the bias
power supply connects to terminal block
TB1, terminals 1A and 2A (neutral) and
3A (ground). VR1 and VR2 are MOVs
that protect the supply from any AC
input line surges. The 220 VAC is
applied through the closed contacts of
(A3) the isolation relay to (A2) the bias
power supply board as long as the bias
circuit breaker on the AC control
assembly is switched on. The bias-on
command is applied to TB1-6 and the
control power supply is on to produce
the +12 VDC applied to TB1-5. The AC
is connected to J1, pins 1 and 4, of (A2)
the bias power supply board. The AC
input is full-wave bridge rectified and
filtered and regulated to produce the
bias output at TB3-6 and TB3-7 that
connect to the grid of the TH610
diacrode tube (typically –80 VDC).
4.2.3 Screen Power Supply
Assembly
The (A6) screen power supply assembly,
60 Hz (1293-1321), provides the 500
VDC at 30 mA screen voltage to the
tube mounted in the 10-kW diacrode
amplifier assembly. The automatic turn-
on procedure applies the screen voltage
to the tube after it has applied the high
voltage to prevent damage to the tube.
The assembly consists of TB1, an input
terminal block; (A7) an isolation relay
board (1002-1108; Appendix B); (A8) a
Sola 60-Hz regulator assembly; T1, a
step-up transformer; (A6-A1) a screen
power supply board (1293-1319;
Appendix B); (A6-A3) a fan; and the
output connections to the tube and the
metering control panel.
The 220 VAC main input to the screen
power supply connects to terminal block
TB1, terminals 1A and 2A and 3A
(ground). VR1 and VR2 are metal-oxide
varistors (MOVs) that protect the supply
from any AC input line surges. The 220
VAC is applied to the terminal block as
long as the screen circuit breaker on the
AC control assembly is switched on. The
(A6-A3) fan will operate as long as the
AC is applied to the terminal block. In
addition, the red LED DS1 will be lit.
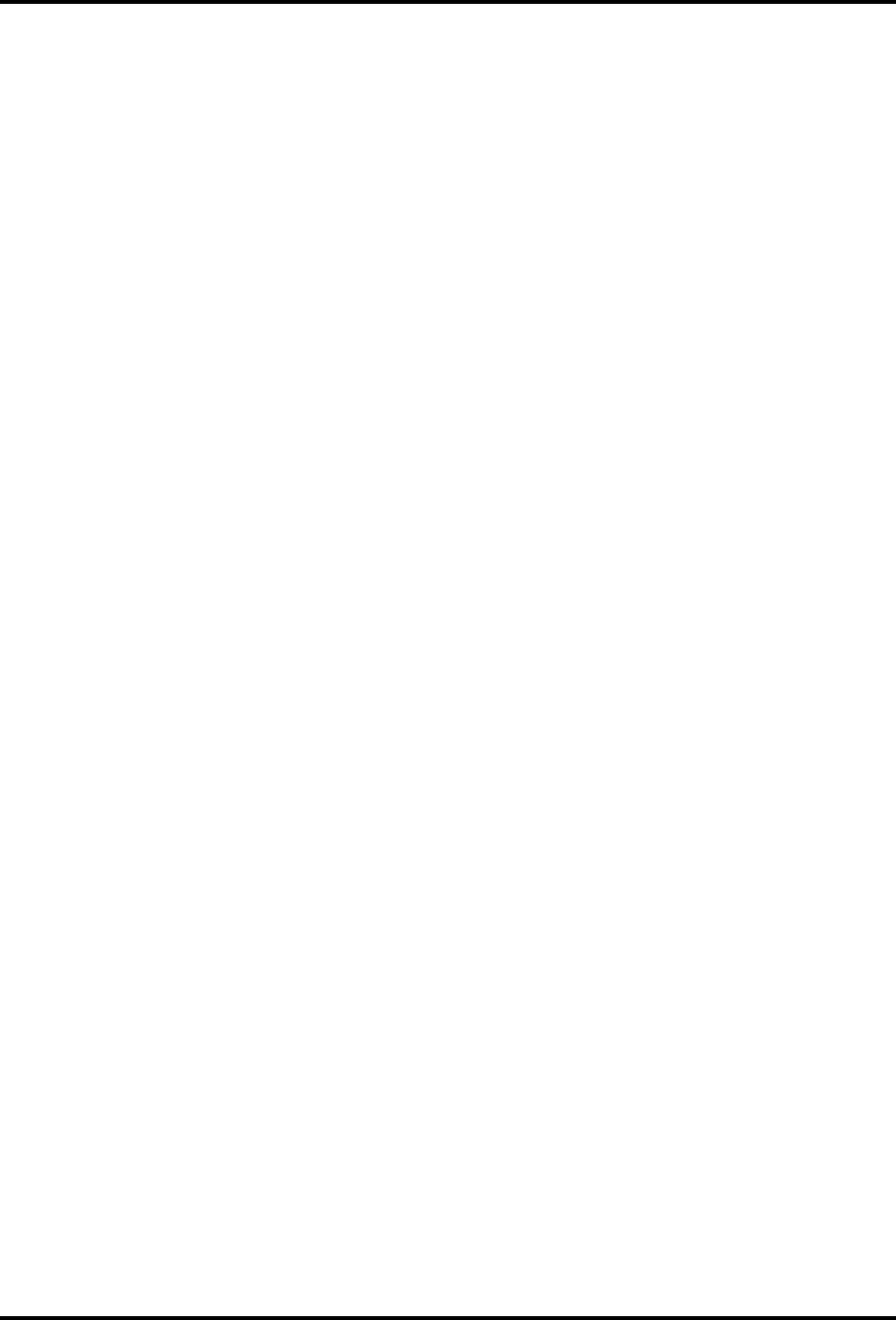
10-kW UHF Transmitter with Chapter 4, Circuit
Feedforward Drive Descriptions
840A, Rev. 0 4-28
The 220 VAC is applied through the
closed contacts of (A7) the isolation
relay board, to (A8) the Sola regulator
assembly, and to transformer T1 as long
as the screen circuit breaker on the AC
control assembly is switched on. The
screen-on command is applied to TB1-6
and the control power supply is on to
produce the +12 VDC that is applied to
TB1-5.
The 220 VAC is connected to step-up
transformer T1 to produce an
approximately 540 VAC output that is
applied to J1, pins 1 and 4, of (A6-A1)
the screen power supply board. The AC
input is full-wave bridge rectified, each
path with four diodes in series; filtered
by four 8-uF capacitors; and regulated
by the zener diodes to produce the
screen output at J3-1 and J3-5 that
connects to the screen of the TH610
tube (typically 500 VDC). SCR-1
provides a crowbar protection circuit
that eliminates the screen voltage, if it
increases beyond the preset limit, to
prevent damage to the tube. SCR-1 also
causes a screen current fault condition
and sends this information to the
transmitter.
4.2.3.1 Screen Power Supply Board
(1293-1319; Appendix B)
The screen power supply board provides
the screen voltage (nominal 500 VDC) to
the TH610 diacrode tube mounted in the
cavity assembly of the 10-kW amplifier.
The screen power supply board operates
when the screen circuit breaker on the
AC control assembly is switched on and
the (A7) isolation relay board, part of the
screen power supply assembly, is
energized by the screen-on command.
The output of T1, the step-down
transformer that is part of the screen
power supply assembly, provides 550
VAC to J1-1 and J1-4 of the screen power
supply board. The 550 VAC is applied to
a full-wave bridge network that consists
of CR1 to CR16. The diodes are in sets of
four per leg for high-current and over-
voltage protection. The output of the full-
wave rectifier connects to four capacitors,
C1 and C14 to C16, that are used for
filtering. The filtered 780 VDC connects
through the loading resistors R5 and R24
to the output regulating circuitry. If the
output voltage increases above
approximately 750 VDC, SCR-1 will
energize and pull the output down to
protect the tube from damage.
Zener diode VR21 prevents the output
voltage from going negative. VR19 and
VR20 protect the current metering circuit
from damage in case of an arc in the
tube or in the cavity assembly. VR22 and
VR23 protect the voltage metering circuit
from damage in case of overvoltage or
an arc in the tube or in the cavity
assembly. The voltage and current
regulated DC (nominal +500 VDC) output
of the board at J3, pins 1 and 5, is fed to
the screen input connector of the 10-kW
tube cavity assembly.
The screen voltage output can be
adjusted by using variable resistor R14
on the board. Together, U1A and Q1
provide a voltage-regulator circuit for the
screen voltage. U1A acts as a comparator
that monitors the voltage setting of R14
at U1A, pin 12, and the voltage of the
input at U1A, pin 13. The voltage levels
that are applied to U1A will determine
the amount of bias that is applied to Q1
as well as the output voltage level.
R20 can be adjusted and is used to
calibrate the screen voltage at J4, pins 4
and 5, that connects to the voltage meter
on the metering control panel. R9 can be
adjusted and is used to calibrate the
screen current reading at J4, pins 1 and
2, that connects to the current meter on
the metering control panel. These
adjustments were calibrated at the
factory for typical operation and should
not be readjusted.
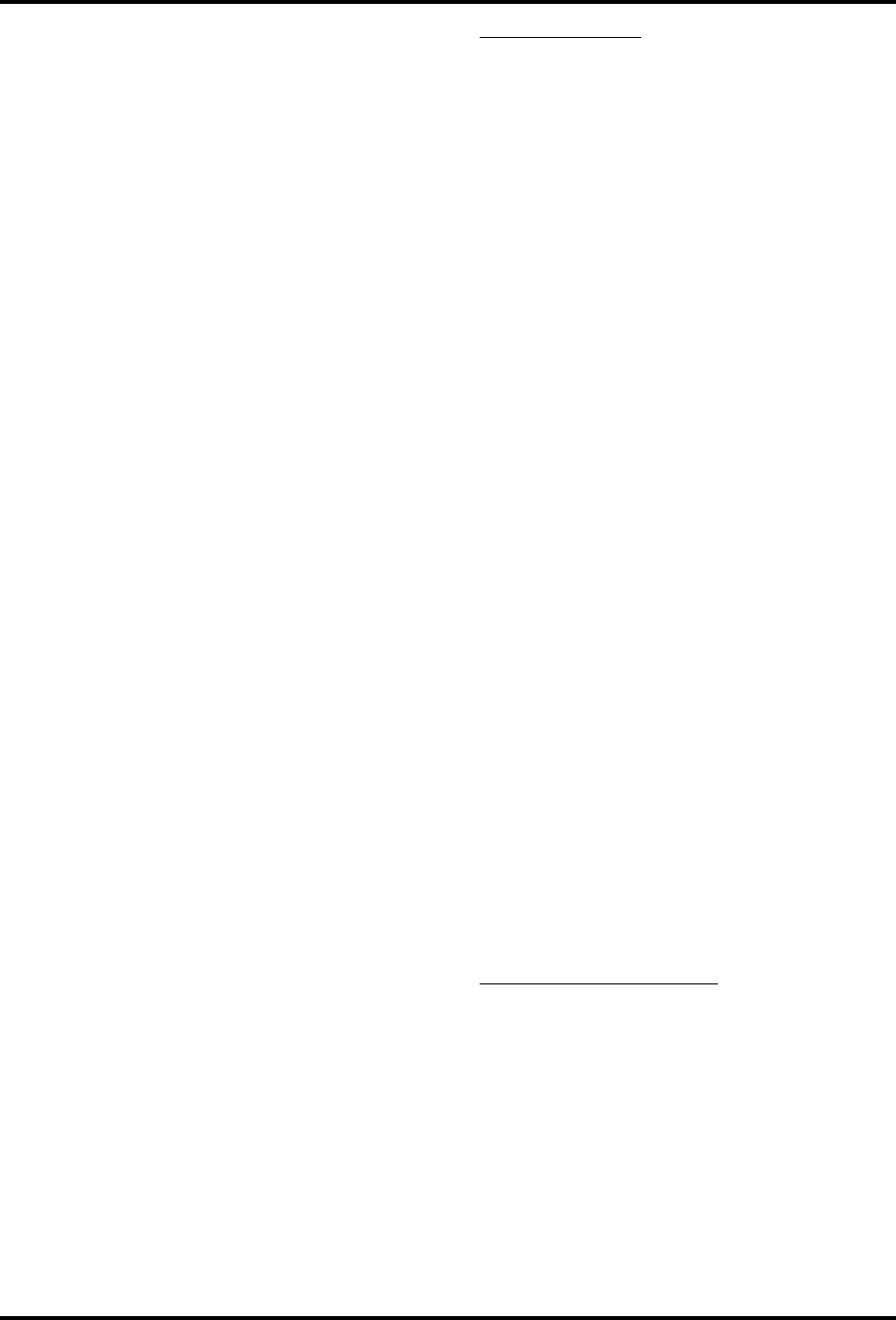
10-kW UHF Transmitter with Chapter 4, Circuit
Feedforward Drive Descriptions
840A, Rev. 0 4-29
4.2.4 Filament Power Supply
Assembly
The filament power supply assembly
(1299-1107) consists of input terminal
block TB2, status and control terminal
block TB1, the (A1) filament power
supply control board (1293-1304;
Appendix B), and the (A2) programmable
filament power supply (1293-6302).
The 220 VAC is supplied at TB2-1A and
TB2-2A and ground at TB2-3A. There are
three MOVs (VR1 to VR3) mounted on
the terminal block to protect against
voltage spikes and transients. The 220
VAC is fed from TB2-1B, TB2-2B, and
TB2-3B to (A2) the programmable
filament power supply at TB1-L, TB1-N,
and TB1-GND. The output of the power
supply is fed to the filament of (A2-A1)
the diacrode tube.
4.2.4.1 (A1) Filament Power Supply
Control Board (1293-1304; Appendix B)
The filament power supply control board
has five functions:
• Control and status of the three
states of filament voltage (float,
ramp, and operate) for the filament
power supply
• Provide two on-board LEDs for status
indication
• Provide adjustments to the operate
voltage
• Monitor the operate status through
monitoring the +12 VDC supply and
220 VAC power
• Adjust the front panel metering for
the filament voltage and the tube
run-time hour meter control
These functions are controlled through
the software programming in U4, a
Motorola MC68 microcontroller.
Filament Control
When the filament circuit breaker on the
front panel is activated, the filament
control board sets the program control
at J3-1 to achieve an output from the
power supply of 1.5 VDC. The output
from U4 PA0-PA7 controls the DAC U3
voltage output at pin 16, which is
buffered by U5 and sent to J3-1. After
ten minutes of valid power supply
operation, the control board sends a
filament-ready signal at J4-2 out to the
transmitter control board (1137-1003),
allowing the transmitter to be placed in
the Operate mode. Once the Operate
switch has been enabled at the front
panel, the power supply controller
gradually increases the filament
operating voltage. During the ramp-up
phase, every 0.80 seconds the DAC
output at J3-1 to the filament power
supply is increased by one bit. Assuming
no faults, the tube voltage reaches the
operating range three minutes after
closure of the Operate switch. J4-2
(filament OK) is a logic output to the
transmitter control board. Logic 1
indicates that the filament power supply
is at the operate or ramp-down voltage
(-5.0 VDC). Logic 0 indicates that the
power supply is at the float or ramp-up
voltage (- less than 5.0 VDC). During
ramp-down, this logic level is held high
to direct the transmitter control board to
keep the blower operating. The blower
will continue to operate for three
minutes after the float voltage level is
reached.
On-board LED indicators
The on-board visual indication of the
controller state is provided by LED DS1.
This LED is off if the power supply is
disabled; blinking at about 1 Hz if the
float voltage is being held for ten
minutes; blinking at about 2 Hz if the
controller is ready to ramp up the
filament voltage; blinking at 4 Hz if the
controller is ramping the voltage up or
down; and continuously on when the
filament is at operate voltage levels. The

10-kW UHF Transmitter with Chapter 4, Circuit
Feedforward Drive Descriptions
840A, Rev. 0 4-30
control for DS1 is from U4, PLMA, pin
20, to FET Q2.
DS2 is the Output Verified LED. It is
used to indicate system status and is
activated through pin 35 of U4 and FET
Q3. Table 4-1 below lists the state,
condition and flash-rate of the LED.
Table 4-1. State, Condition, and Flash Rate of LED DS2
STATE CONDITION LED FLASH RATE
Normal Condition --
1.0 second on, 1.0 second
off (0.5 Hz; 50% duty
cycle)
AC Fault J4-1 <4 VDC One flash (0.2 second on),
then pause 5 seconds
DC Fault J1-3 <9 VDC Two flashes (0.2 second
on), then pause 5 seconds
DAC Fault DAC = 4.625 Vout
DAC = 0.0 Vout
Three flashes or four
flashes (0.2 second on),
then pause 5 seconds
Power Supply Fault Power supply not regulating
at float voltage
Five flashes (0.2 second
on), then pause 5 seconds
Manual Operate Voltage Adjustment
Adjustment of the filament power supply
is a two-step process. The system
calibration of DAC, U3, using variable
resistor R6 must first be verified. With
the ten-minute ramp-up time complete
and the transmitter still in stand-by,
place SW1-7 in the On position. Verify
that the output at J3-1 is 5.0 VDC; if it
is not, adjust R6 until this voltage is
achieved.
Note: Do not make the above
adjustments with the transmitter in
the Operate mode.
Once the system calibration voltage has
been verified, monitor the output of the
filament power supply during full power
operation. This value should be 5.0 VDC.
Adjust R28 on the filament control board
to set this voltage.
Power Monitoring
Both the +12 VDC and the 220 VAC
supply voltages are monitored. If the
220 VAC power is lost, the logic low at
J4-1 will go high. This logic high is seen
at PD1 of U4, which directs the
microcontroller to ramp the filament
control back to the float voltage. If the
+12 VDC supply at J1-3 drops below
nine volts, the filament control also
ramps back to the float voltage. The
+12 VDC voltage is monitored at U4, pin
3.
Front Panel Metering Control
The front panel metering adjustment is
controlled by R15. Verify that the
metering control rotary switch below the
left-hand meter on the front panel is set
to Filament. Monitor the filament power
supply output and adjust R15 to obtain
the same reading. The current metering
adjustment on the control board is not
used.
Tube Run-Time Hour Metering
When the operator closes the operate
switch, J4-6 changes from a voltage
level of twelve volts to approximately
two volts. With J4-6 at two volts, relay
R1 on the controller board is closed. This
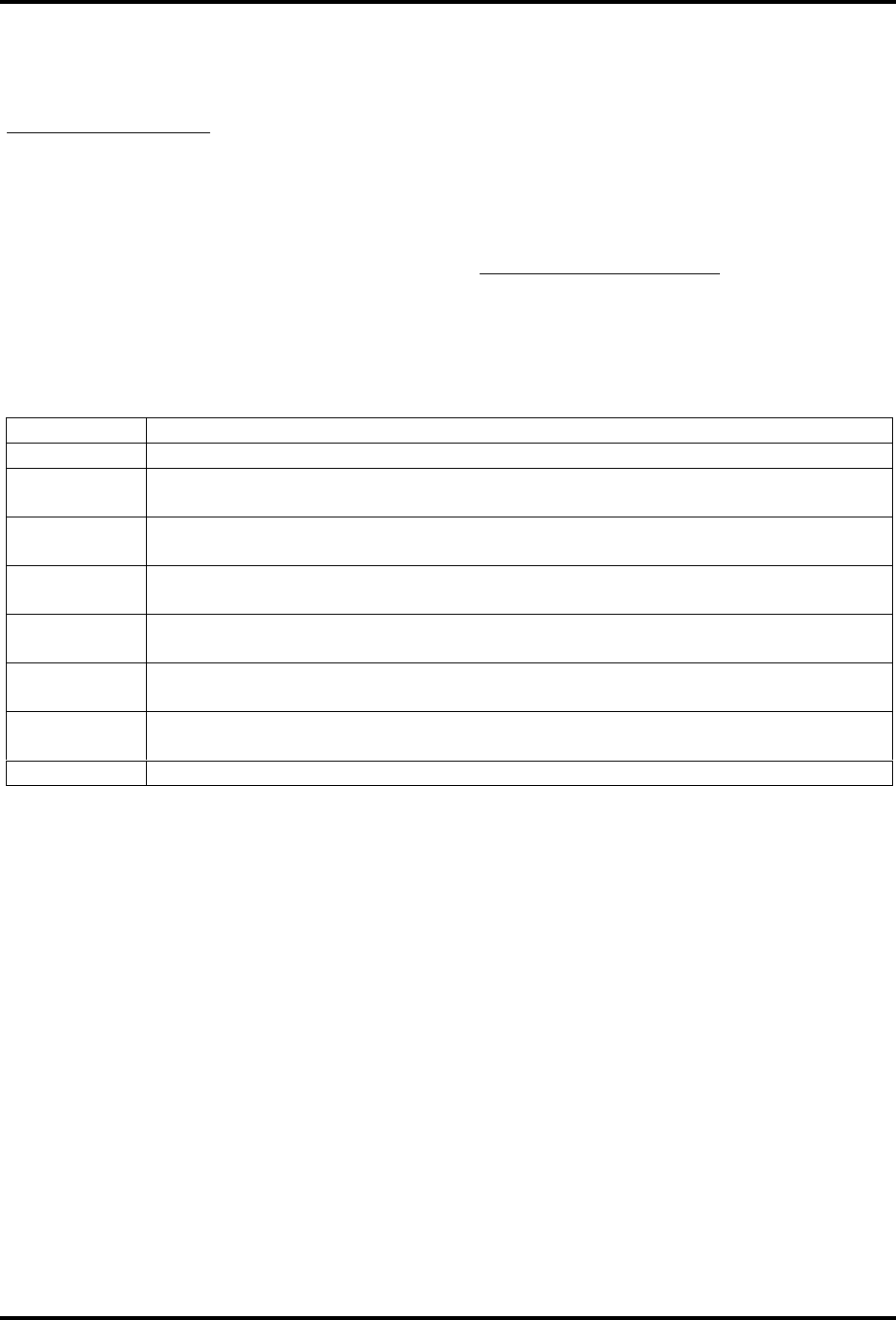
10-kW UHF Transmitter with Chapter 4, Circuit
Feedforward Drive Descriptions
840A, Rev. 0 4-31
enables the tube hour counter that is
connected through connector J7-1 and
J7-5.
Operational Voltages
The +12 VDC needed to operate the
board enters at J1, pin 3, and is filtered
by L1, C1, and C4 before it is fed to the
rest of the board.
The -12 VDC needed to operate the
board enters at J1, pin 5, and is filtered
by L2 and C21 and C22 before being fed
to the rest of the board.
The +5 VDC is supplied by 5-VDC
regulator U1 and is filtered by C1 and C3
before being fed to the rest of the board.
C3 is used to maintain power on the +5-
VDC line for short duration power losses.
DIP Switch Configuration
The DIP switch configurations for the
board are shown in Table 4-2.
Table 4-2. DIP Switch Configurations for the Filament Power Supply Control Board
POSITION FUNCTION
SW1-1 Not connected
SW1-2 Accelerate timers: When set high, the ramp-up, ramp-down, and blower
delay timers operate four times faster
SW1-3 Ten-minute by-pass: When set high, and all other DIP switch settings are
low except SW1-5, the ten-minute warm-up is skipped
SW1-4 SCADA: When set high, SCADA interrupts will be processed
(future development)
SW1-5 Set DAC 0.0 VDC: When in the Standby mode, setting this switch high
causes the DAC to output 0.0 VDC
SW1-6 Set DAC 4.625 VDC: When in the Standby mode, setting this switch high
causes the DAC to output 4.625 VDC
SW1-7 Set DAC 5.0 VDC: When in the Standby mode, setting this switch high
causes the DAC to output 5.0 VDC
SW1-8 Micro reset: When this is set high, the microcontroller is held in reset
4.2.5 Metering Control Panel
The (A7) metering control panel (1293-
1308) contains three meters: one for
voltages, one for currents, and one for
power output. The voltage meter displays
the plate, screen, bias, and filament
voltages that are applied to the tube. The
current meter displays the plate, screen,
and grid currents that are produced by
the tube. The power meter displays the
% Aural Output power, % Visual Output
power, and % Reflected Output power of
the 10-kW amplifier. The metering
control panel also provides the system
control functions for the 10-kW
transmitter.
The metering control panel consists of
(A1) the control logic board (1137-1402),
(A7) the transmitter control board (1137-
1003), (A2 and A3) two differential buffer
boards (1008-1017), (A4) fault sensing
board, diacrode (1293-1307), (A5) fault
sensing board, inverting (1016-1401),
and (A6) the fault sensing board, dual
polarity (1016-1402). The panel also has
(M1) a front panel voltage meter with
(S1) the meter control switch; (M2) a
front panel current meter with (S2) the
meter control switch and (S3) the meter
reverse switch; and (M3) a front panel
power meter with (S4) the meter control
switch. The panel has (S5) the
Operate/Standby switch, (S6) the
Auto/Manual Mode Select switch, (S7)
the High-Voltage Enable/Disable switch,
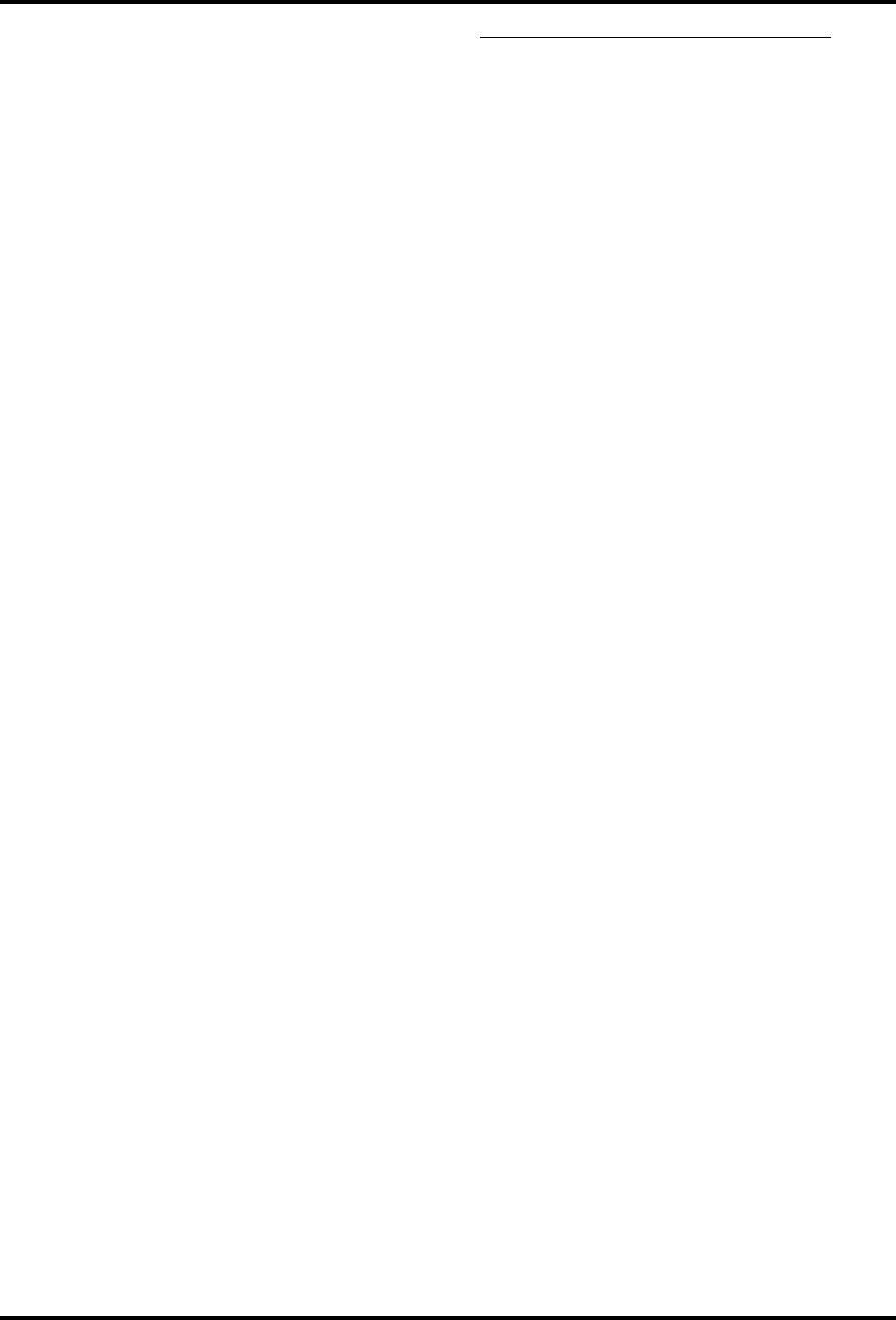
10-kW UHF Transmitter with Chapter 4, Circuit
Feedforward Drive Descriptions
840A, Rev. 0 4-32
(S10) the Driver Mode Normal/Test
switch, (S9) the Fault Reset switch, and
(S8) the Power Output Raise/Lower
switch.
The ±12 VDC needed to operate the
boards in the metering control panel are
provided to J2-1 (+12 VDC), J2-2 (±12
VDC Return), and J1-50 (-12 VDC) by
the control section of (A5) the control
and bias power supply assembly. The ±12
VDC is applied to the metering control
panel when the control circuit breaker is
switched on. The ±12 VDC connects to
terminal block TB1 that, using jumpers,
splits the ±12 VDC which is then fed to
the boards in the metering control panel.
4.2.5.1 (A1) Control Logic Board (1137-
1402; Appendix B)
The control logic board in the metering
control panel provides the circuitry
needed for the control of the automatic
on/off sequence of the transmitter and
the monitoring of the operation of the
transmitter for fault conditions. An
Operate command and the interlocks for
the transmitter are also connected to the
board. The board monitors the Air-On
Sense, the Filament-On Sense, the Bias-
On Sense, the High Voltage-On Sense,
and the Screen-On Sense commands
during each step of the automatic turn-
on procedure. The board provides the On
command outputs in the proper sequence
as well as the enables to the Command
Status and Operating Status LEDs on the
front panel. The fault circuits monitor the
operation of the power supplies and the
tube, the air flow to the tube, and the
temperature of the transmitter and will
shut down the transmitter if any of these
faults occur.
The board supplies the Air-On, Filament-
On, Bias-On, Screen-On, High Voltage-
On, and RF-On commands to the
transmitter. The control logic board is
connected to the High Voltage
Enable/Disable switch and provides the
commands to K1, the magnetic latching
relay mounted on the board.
Operation of the Control Logic Board
When the Operate/Standby switch on the
front panel of the metering control panel
is switched to Operate, a Low Operate
command from the transmitter control
board is applied to J2-1 and lights the
Operate LED connected to J12-1 and J12-
2. The low at J2-1 is connected to the
OR gate at U1-1. An external, total-
shutdown interlock must be closed for
the transmitter to operate. The low of the
total-shutdown interlock is wired to J2-3,
and connects to the board-mounted
Total-Shutdown Interlock LED at J12-4
and J12-5, which will light. The low is
also connected to OR gate U1-2 and, with
both U1-1 and U1-2 low, the output at
U1-3 will be low. The low from U1-3
connects to AND gates U2-1, U2-5, and
U2-8. The low also connects to the OR
gate U6-9. The IC U2, pins 1, 2, and 3, is
located in the Blower-On command
circuit. The U2-1 low causes the output
at U2-3 to go low. This low connects to
inverter IC U4, whose output at U4-2
goes high. The high forward biases Q1,
whose collector goes low and applies the
Low Blower, Air, On command at J17-1 of
the board. The Blower, Air, On command
connects through the front panel-
mounted Command Status LED DS8,
which will light. The blower control relay
that energizes and turns on the blower is
controlled by Q1. The operation of the
blower causes air flow through the tube
cavity assembly which is monitored by an
air-flow switch mounted in the chimney.
If the air flow is adequate, the switch
closes and applies a low, air-on sense, to
J2-5 of the board. This lights the front
panel-mounted Operating Status Blower
LED DS16.
The low, air-on sense at J2-5 connects to
U1-5 in the Filament-On command circuit
and lights the Blower, Air, On LED
connected to J12-7 and J12-8. U2-5 is
low and causes the output at U2-6 to be
low. U1-6 and U1-5 are both low, which
causes the output to go low. The low
connects to inverter U4, whose output at
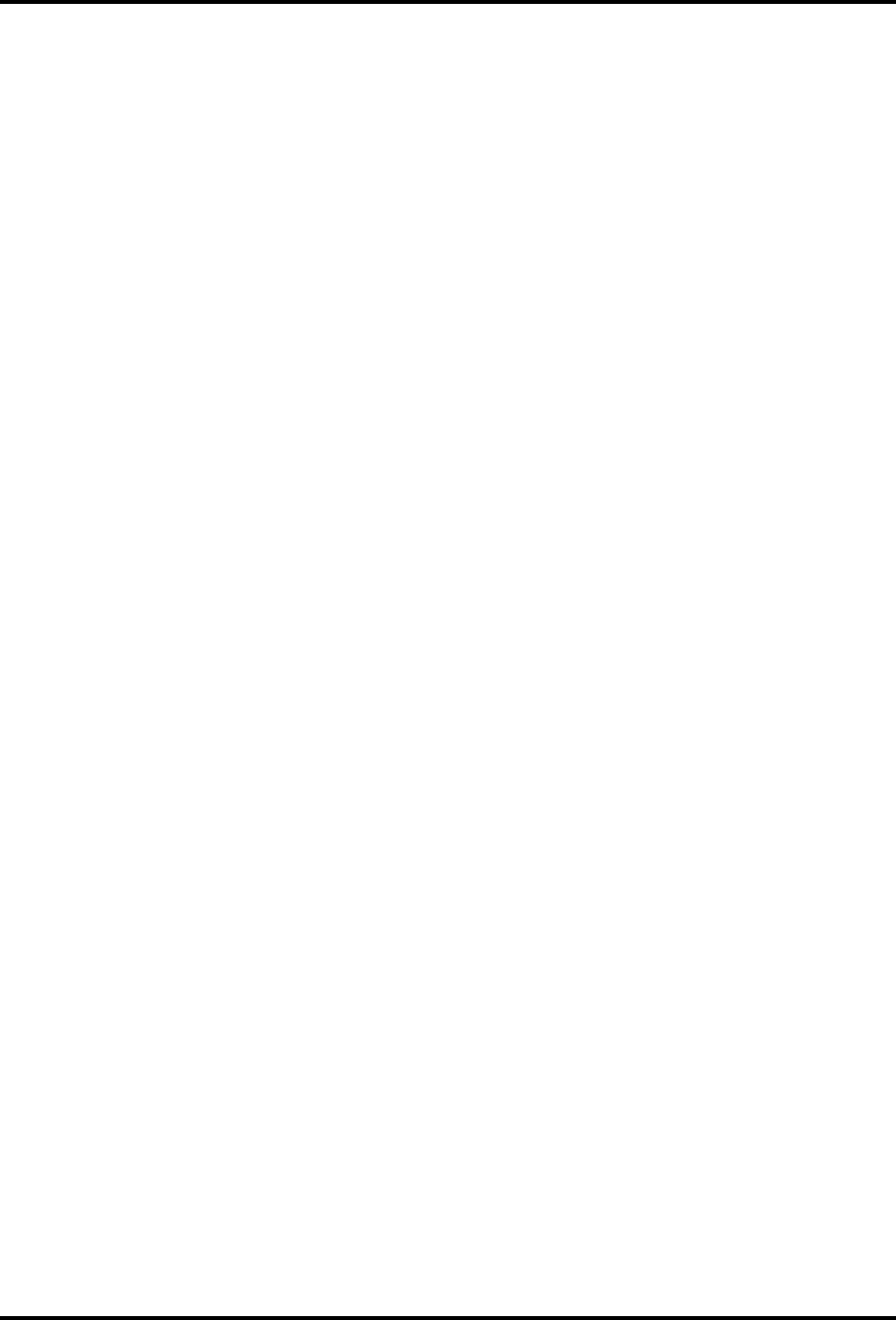
10-kW UHF Transmitter with Chapter 4, Circuit
Feedforward Drive Descriptions
840A, Rev. 0 4-33
pin 4 goes high. The high forward biases
Q2, whose collector goes low and applies
the Low Filament-On command through
the front panel-mounted Command
Status Filament LED DS9, which will
light, to the Filament Control Relay. The
low energizes the relay and turns On the
filament power supply. The output
voltage from the filament power supply is
monitored and produces a low, filament-
on sense input to the board at J2-7. This
action lights the front panel-mounted
Operating Status Filament LED DS17.
The low, filament-on sense at J2-7 is
applied to U8, a clock IC that times out
at approximately two minutes to allow
the tube to preheat before the rest of the
voltages are applied. Moving jumper W1
on J11 changes the timer from two
minutes to approximately 18 seconds.
When the timer clocks out, a high is
applied to inverter U7-5, whose output at
U7-4 goes low and connects to U6-2 in
the Bias-On command circuit. As long as
the filament voltage stays above 3.5
VDC, the filament under-voltage input at
J2-9 will be low and is applied to U6-3.
U6-4 will be a low as long as the
transmitter is in Operate or the bias
voltage is present to the tube. Since U2
is an AND gate, either input low will
cause the output to be low. With all
inputs to U6 low, the output at U6-1 will
be low. The low is connected to inverter
U4-7, whose output at U4-6 goes high.
The high is applied to Q3, which is
forward biased, and causes the collector
to go low. The Low Bias-On command
output at J7-6 connects through the front
panel-mounted Command Status Bias
LED DS12, causing it to light, to the bias
control relay, which energizes and turns
on the bias power supply. The output
voltage from the bias power supply is
monitored and produces a low, bias on
sense input to the board at J3-3, which
lights the front panel-mounted Operating
Status Bias LED DS18, connected to J13-
1 and J13-2.
The low, bias on sense at J3-3 is applied
to U3-3 in the High Voltage-On command
circuit and to U2-6 in the Filament-On
command circuit. U3-4 connects to the
fault circuit on the board and will be low
unless a fault occurs. U3-5 will be low
unless both the high voltage is disabled
and the screen voltage is removed from
the tube. With U3-3, U3-4, and U3-5 all
low, this causes a low at U3-6 that is
connected to inverter IC U4-9, whose
output at U4-10 goes high. The high
forward biases Q4 and causes its
collector to go low and apply the High
Voltage-On command through the front
panel-mounted Command Status High
Voltage LED DS11, which will light, to the
high-voltage control relay. The relay
energizes and turns on the high-voltage
power supply. The output voltage from
the high-voltage power supply is
monitored and produces a low, high
voltage-on sense input to the board at
J3-7 and lights the front panel-mounted
Operating Status High Voltage LED DS19.
The low, high voltage on sense at J3-7 is
applied to U21-6 in the Screen Voltage-
On Command circuit and to U2-9 in the
Bias On command circuit. U21-5 will be a
low if both the high voltage is enabled,
U21-8 low, and the screen interlock is
closed, U21-9 low. When U21-5 and U21-
6 are both low, this causes a low at U21-
4 that is connected to inverter IC U13-3,
whose output at U13-2 goes high. The
high forward biases Q5 and causes its
collector to go low, which applies the
Screen-On command through the front
panel-mounted Command Status Screen
LED DS12, causing it to light, to the
screen control relay. The relay energizes
and turns on the screen power supply.
This logic circuit prevents the screen
power supply from turning on unless the
high voltage is present to the tube. The
output voltage from the screen power
supply is monitored and produces a low,
screen on sense input to the board at J3-
11, which lights the front panel-mounted
Operating Status Screen LED DS20.
The low, screen voltage-on sense at J3-
11 is applied to U21-2 in the RF-On
command circuit and to U2-13 in the
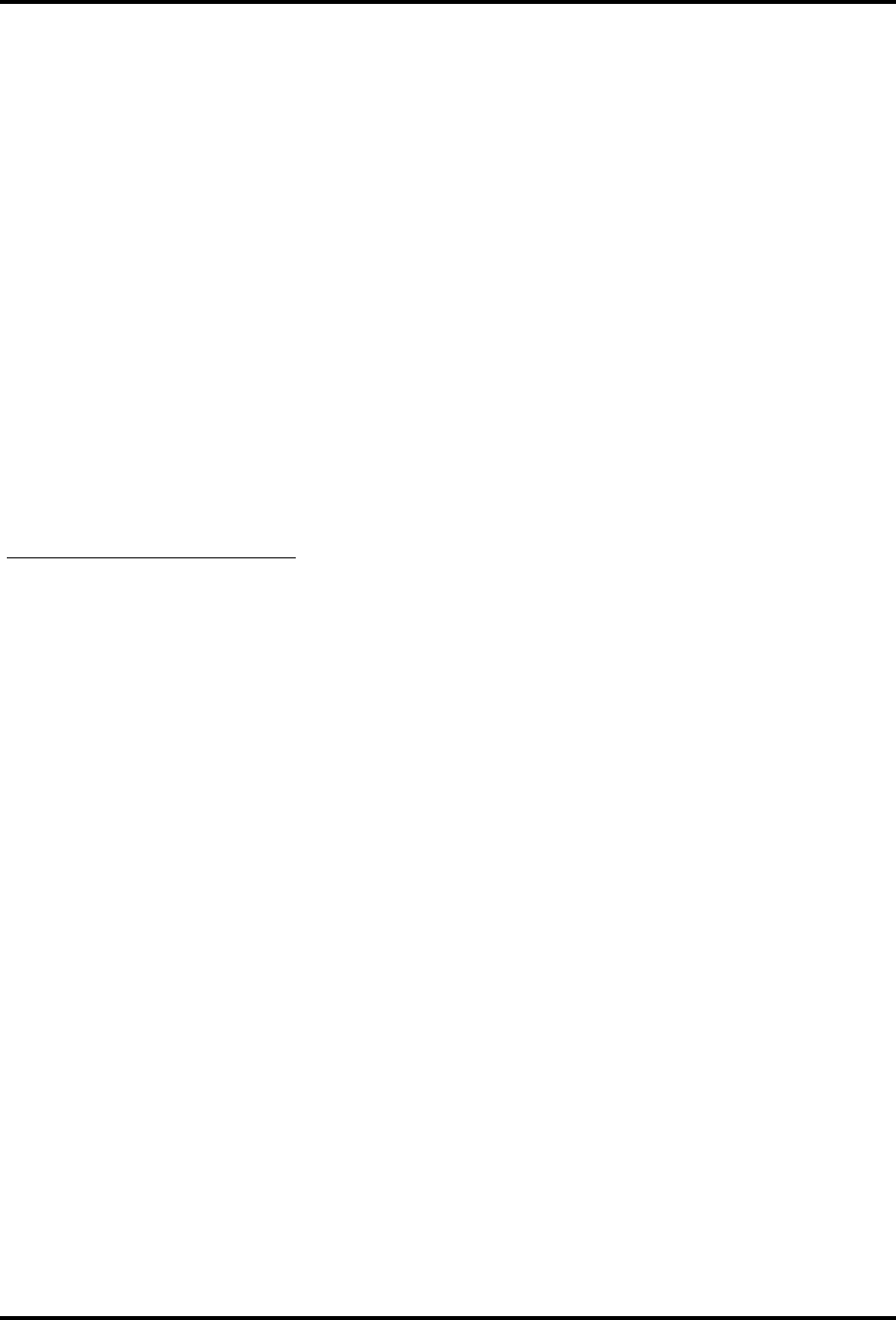
10-kW UHF Transmitter with Chapter 4, Circuit
Feedforward Drive Descriptions
840A, Rev. 0 4-34
High Voltage-On command circuit. U21-
1, which connects to U21-10, will be a
low if both the high voltage is enabled,
U21-8 low, and the screen interlock is
closed, U21-9 low. When U21-1 and U21-
2 are both low, this causes a low at U21-
3, which is connected to inverter IC U13-
5, and whose output at U13-4 goes high.
The high forward biases Q7, causing its
collector at J9-11 to go low and apply the
RF-On command to the exciter. J9-10
also goes low and lights the front panel-
mounted Command Status RF Request
LED DS13. The low at U21-3 is also
connected to the base of Q6, which
reverse biases it and removes the mute
from the 3-watt amplifier tray.
The transmitter should be fully
operational at this time with an RF
output.
Operation of the Fault Circuits
The control logic board monitors thermal
switch A11-S1, control grid I, cathode I,
and the reflected power, VSWR, for
faults. If a fault occurs in any of the
circuits monitored, a low from the
thermal switch and/or the cathode
current and/or a high from the control
grid current, screen I, or VSWR is applied
to the board. The fault causes the
transmitter to reset itself three times,
each time trying to go back on the air, to
make sure that the fault is real. After
three resets, the transmitter switches to
Standby.
If thermal switch A11-S1, mounted in the
exhaust stack of the tube cavity
assembly, closes due to overheating, a
low is connected to J5-3. The low
connects to inverter IC U7-11, whose
output at U11-12 goes high. The high
connects to pin 6, the S1 set input, to
one of four quad R-S latches that make
up U16. The output of the latch at pin 9
goes high and connects to U1-9 and also
to the base of Q8. Q8 is forward biased
and its collector goes low, lighting the
Overtemperature LED DS22 on the front
panel. The output of the OR gate U1-10
goes high and connects to U6-12. The
output of U6 goes high and removes the
high voltage enable from the logic circuit
that removes the enables to the screen
voltage and the high-voltage power
supplies.
If a problem occurs with the control grid
current, a high is connected to J5-5. The
fault high connects to pin 4 the S0 set
input to one of four quad R-S latches that
make up U16. The output of the latch at
pin 2 goes high and connects to U3-11,
whose output at pin 10 goes high. The
high connects to U15-1, the three-fault
counter, and also to U19-8 and U19-9.
U19-10 goes high and forward biases Q9,
whose collector goes low, lighting the
Fault Indicator LED DS7 on the front
panel.
The fault high at J5-5 also connects to
the set S3 input at pin 14 to one of four
quad R-S latches that make up U20 and
to U11-5. The output of the latch at U20-
1 goes high and is inverted by U18. The
low is applied to DS12, the Bias Fault
LED, on the board, which will light.
Because the input to U11 at pin 5 is high,
the output of U11 at pin 1 goes high,
which resets clock IC U9. The Q1 and Q0
outputs of U9 go low during reset, then
back to high, and are applied to U14,
whose output will be high when both
inputs are high. The high from U14-4 is
connected to U14-2 and, when U14-1
goes high, the output at U14-3 goes high
and resets three of the R-S latches that
make up U16. The transmitter will reset
three times to confirm that a fault has
actually occurred and counter IC U15 will
count each time a high is applied to pin
1. After the third fault, the U15 IC will
latch and produce a low at U7-15 that
connects to the Three Fault LED DS11,
causing it to light.
If a problem occurs with reflected power,
VSWR, a high is connected to J5-7. The
fault high connects to pin 14, the S3 set
input, to one of four quad R-S latches
that make up U16. The output of the
latch at pin 1 goes high and connects to
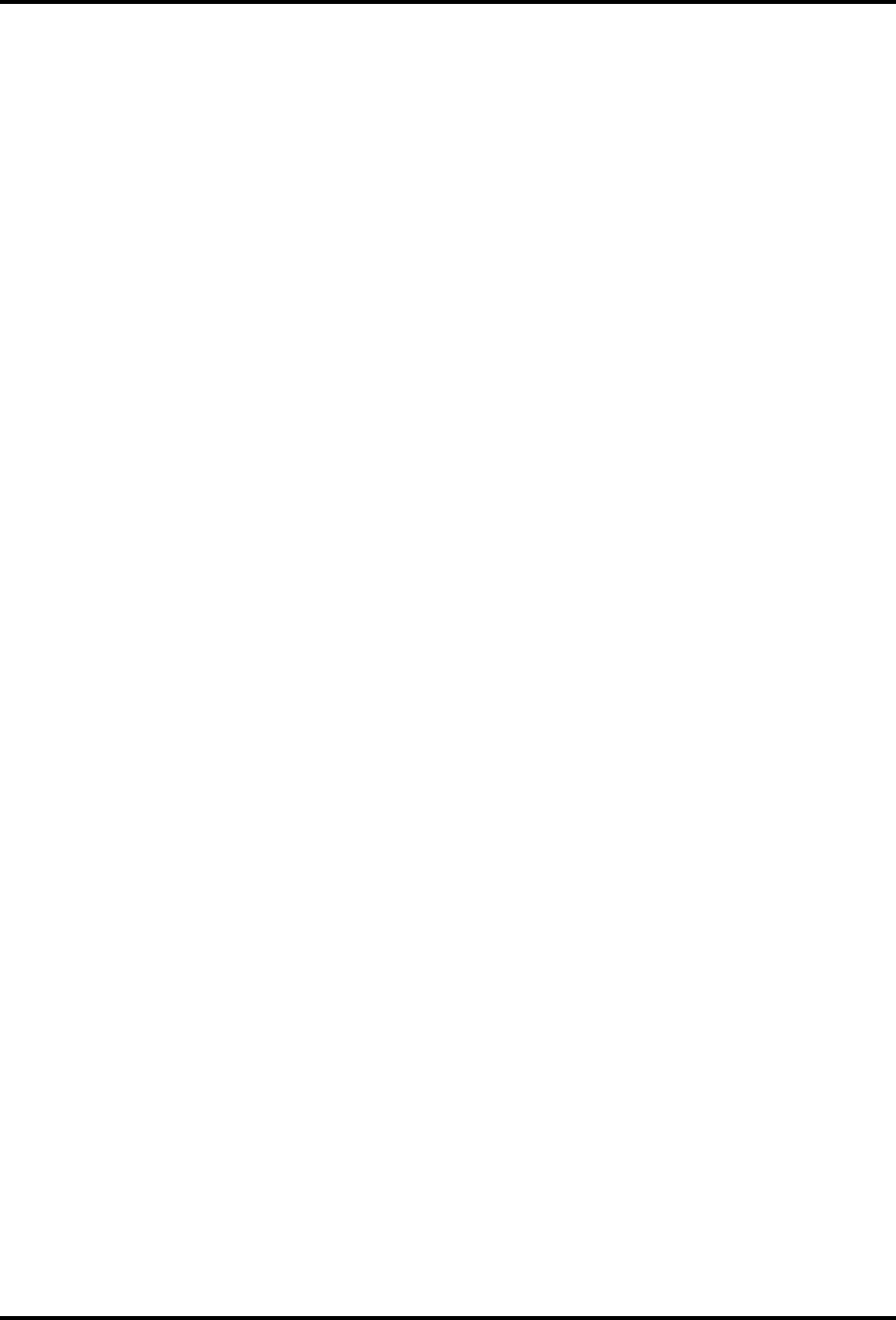
10-kW UHF Transmitter with Chapter 4, Circuit
Feedforward Drive Descriptions
840A, Rev. 0 4-35
U3-12, whose output at pin 10 goes high.
The high connects to U15-1, the three
fault counter IC, and also to U19-8 and
U19-9. U19-10 goes high and forward
biases Q9, whose collector goes low and
lights the Fault Indicator LED DS7 on the
front panel. The fault high at J5-7 also
connects to the set S1 input at pin 6, to
one of four quad R-S latches that make
up U20, and to U11-4. The output of the
latch at U20-9 goes high and is inverted
by U18. The low is applied to DS13, the
VSWR Fault LED on the board, which will
light. Because the input of U11 at pin 4 is
high, the output of U11 at pin 1 goes
high and resets clock IC U9. The Q1 and
Q0 outputs of U9 go low during reset,
then back to high, and are applied to
U14, whose output will be high when
both inputs are high. The high from U14-
4 is connected to U14-2 and, when U14-
1 also goes high, the output at U14-3
goes high, resetting the three R-S latches
that make up U16. The transmitter will
reset three times to confirm that a fault
has actually occurred and counter IC U15
will count each time a high is applied to
pin 1. After the third fault, the U15 IC will
latch and produce a low at U7-15, which
connects to the Three Fault LED DS11,
causing it to light.
If a problem occurs with screen I, a high
is connected to J6-1. The fault high
connects to pin 12 of U12, whose output
at pin 11 goes high. The high connects to
pin 12, the S2 set input of one of four
quad R-S latches that make up U16, and
to U11-3. The output of the latch at pin
10 goes high and connects to U3-13 and
U3-4. The U3-4 high causes the output of
U3 at pin 6 to go high and be inverted by
U4. The low output at pin 10 connects to
Q4, which turns the transistor off and
removes the High Voltage-On command.
With U3-13 high, the output of U3 at pin
10 goes high. The high connects to U15-
1, the three fault counter, and also to
U19-8 and U19-9. U19-10 goes high and
forward biases Q9, whose collector goes
low and lights the Fault Indicator LED
DS7 on the front panel. The fault high at
J6-1 also connects to the set S2 input at
pin 12 and to one of four quad R-S
latches that make up U20. U20-10 goes
high and is inverted by U18 and applied
to DS14, the Screen I Fault LED on the
Board, causing it to light.
Because of the high on its input at U11-
3, the output of U11 at pin 1 goes high
and resets clock IC U9. The Q1 and Q0
outputs of U9 go low during reset, then
back to high, and are applied to U14,
whose output will be high when both
inputs are high. The high is connected to
U14-2 and, when U14-1 goes high, the
output at U14-3 also goes high and
resets the three R-S latches that make
up U16. The transmitter will reset three
times to confirm that a fault has actually
occurred and counter IC U15 will count
each time a high is applied to pin 1. After
the third fault, the U15 IC will latch. It
produces a low at U7-15 and connects to
the Three Fault LED DS11, causing it to
light.
If a problem occurs with cathode I, a low
is connected to J6-6. The fault low is
inverted to a high by U18 and then
connects to pin 13 of U12, whose output
at pin 11 goes high. The high connects to
pin 12, the S2 set input of one of four
quad R-S latches that make up U16, and
to U11-3. The output of the latch at pin
10 goes high and connects to U3-13 and
to U3-4. When U3-4 is high, it causes the
output of U3 at pin 6 to go high and be
inverted by U4. The low output at pin 10
connects to Q4; this turns the transistor
off and removes the High Voltage-On
command. A high on U3-13 causes the
output at pin 10 to go high. The high
connects to U15-1, the three fault
counter, and to U19-8 and U19-9. U19-
10 goes high and forward biases Q9,
whose collector goes low and lights the
Fault Indicator LED DS7 on the front
panel.
The fault high from U18 connects to the
set S0 input at pin 4 and to one of four
quad R-S latches that make up U20.
U20-2 goes high and is inverted by U18;
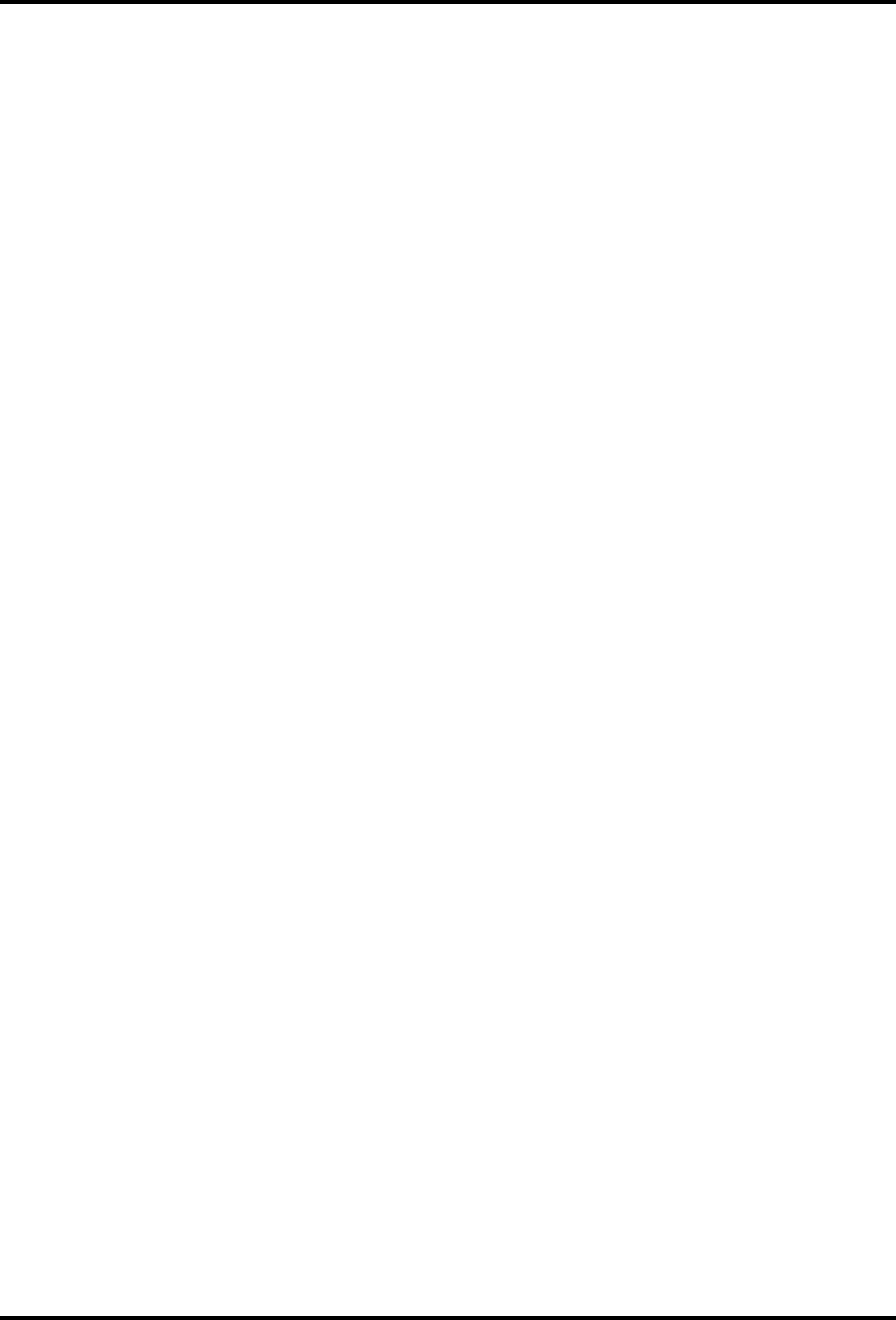
10-kW UHF Transmitter with Chapter 4, Circuit
Feedforward Drive Descriptions
840A, Rev. 0 4-36
this is applied to DS15, the Cathode I
Fault LED on the board, causing it to
light. Because of the high on its input at
U11-3, the output of U11 at pin 1 goes
high and resets clock IC U9. The Q1 and
Q0 outputs of U9 go low during reset,
then back to high, and are applied to
U14, whose output will be high when
both inputs are high. The high is
connected to U14-2 and, when U14-1
goes high, the output at U14-3 also goes
high and resets the three R-S latches
that make up U16. The transmitter will
reset three times, to confirm that a fault
has actually occurred, and counter IC
U15 will count each time a high is applied
to pin 1. After the third fault, the U15 IC
will latch and produce a low at U7-15
that connects to the Three Fault LED
DS11, causing it to light.
After the problem that caused the fault is
corrected, the fault circuit is reset by
switching the front panel-mounted reset
switch S9. This places a low at J6-9 on
the board that is inverted by U18. The
high is connected to pin 7, the R1 reset
input of one of four quad R-S latches that
make up U16, and to U12-8. The high at
pin 7 of U16 resets the temperature fault
circuit. The high at U12-8 causes the
output of U12 at pin 10 to go high and
connects to the reset input at pin 7 of
U15. U15 then resets the front panel-
mounted fault indicator and the fault
circuits associated with U16. The three-
fault indicator and the other fault
indicators that are lit on the board are
reset by switching S1.
The +12 VDC needed for the operation of
the board enters at jack J1, pin 1. C1, C2
and C3, and L1 are for the filtering and
isolation of the +12 VDC before it is
applied to the rest of the board.
4.2.5.2 Transmitter Control Board (1137-
1003; Appendix B)
The transmitter control board in the
metering control panel provides the
system control functions for the
transmitter. The board supplies the
interlock to the exciter tray and also
provides the outputs to the function
indicator LEDs on the front panel of the
metering control panel. The transmitter
control board will switch the transmitter
to Standby upon the loss of the video
input from the modulator or from the
receiver tray, if present, when the
transmitter is in Automatic.
When the Operate/Standby switch on the
front panel of the metering control panel
is switched to Operate (J11-8 low), and
the Normal/Exciter Test switch is in
Normal (K4 energized), K3 energizes and
applies a low to inverter U8F, causing its
output to go high. The low from K3 also
biases off Q23 and Q24; this removes the
Standby commands. The high output of
U8F, at pin 15, forward biases Q18 to
Q22 and applies the Operate commands
to the control logic board. The low is also
applied through diode CR12 to pin 11 of
inverter U8E, causing its output to go
high. The high forward biases Q26 and
Q27; this causes the drains to go low and
lights DS14, the front panel Normal LED
connected to J14, pins 8 and 6. The high
output of U8E also connects to pin 5, the
input to inverter U8B, causing the output
at pin 4 to go low. The low is applied to
Q28 to Q33, biasing them off and
removing the exciter test functions.
When the Operate/Standby switch on the
front panel of the metering control panel
is switched to Standby (J11-2 low), and
the Normal/Exciter Test switch is in
Normal (K4 energized), K3 de-energizes
and applies a high to inverter U8F, pin
14, and also to Q23 and Q24. As a result,
Q23 and Q24 are forward biased; this
produces a low at J12, pin 3, and lights
DS2, the front panel-mounted Standby
LED. The high on inverter U8F, pin 14,
causes the output at pin 15 to go low.
The low reverse biases Q18 to Q22 and
removes the Operate commands to the
control logic board and the amplifier
trays. The high from K3 is also applied to
diode CR12, causing it to reverse bias.
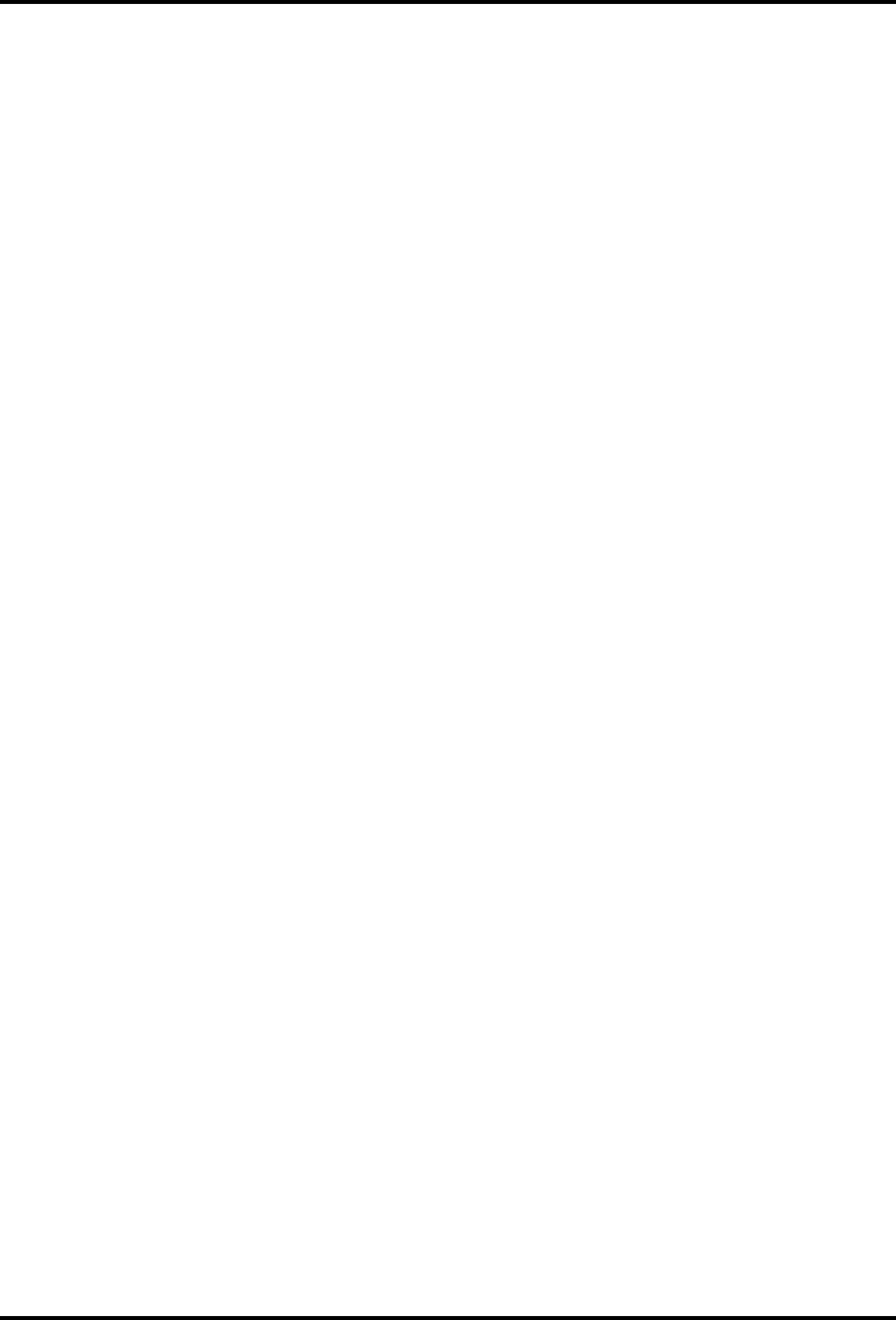
10-kW UHF Transmitter with Chapter 4, Circuit
Feedforward Drive Descriptions
840A, Rev. 0 4-37
When the Exciter Test switch is in
Normal, with K4 energized, it applies a
low to CR13 and then to inverter U8E,
pin 11, whose output at pin 12 then goes
high. The high also forward biases Q26
and Q27 and lights DS14, the front
panel-mounted Normal LED connected to
J14, pins 8 and 6. The high input to
inverter U8B, pin 5, causes the output at
pin 4 to go low. The low is applied to Q28
to Q33, biasing them off and removing
the exciter test functions.
The exciter can be operated without
using the 10-kW amplifier by switching
the Normal/Exciter Test switch on the
front panel of the metering control panel
to the Exciter Test position. With the
switch in this position, K4 is de-energized
and a high is applied to diode CR13,
causing it to reverse bias. The high from
K4 is also applied to Q25, which forward
biases it and produces a low at pin 4 of
the K3 relay. The low at pin 4 de-
energizes the relay and produces a high
that is applied to diode CR12, causing it
to reverse bias. Both CR12 and CR13 are
reverse biased; as a result, a high from
+12 VDC and R61 is applied to pin 11 of
U8E and causes its output at pin 12 to go
low. The low connects to Q26 and Q27
and biases them off. The low is also
applied to inverter U8B, pin 5, whose
output at pin 4 goes high. The high
connects to Q28 to Q33, forward biases
them, applies a low to the exciter tray,
lights the Exciter Test LED, and sets up
the exciter to operate without the need
for the 10-kW amplifier.
The Auto/Manual Test switch S6 on the
front panel controls K1, the magnetic
latching relay, by connecting a low input
to the board at J2, pins 7 and 8, for
Manual or to J2, pins 4 and 3, for
Automatic. When the Test switch is
moved to the Auto position, a low is
applied to K1, pin 6, that energizes the
relay and applies a low to U7F, pin 14,
causing its output to go high. The high is
applied to Q5 and Q7, forward biasing
them, and produces a low at their drain.
The low lights the front panel Automatic
LED. With the Test switch in the Manual
position, a low is applied to K1, pin 4;
this de-energizes the relay and connects
a high from K1, pin 2, to Q6, forward
biasing it and producing a low at its
drain. The low lights the front panel-
mounted Manual LED DS4. The high
output of K1 is also applied to U7F, pin
14, whose output goes low. The low is
applied to Q5 and Q7, which reverse
biases them, and extinguishes the front
panel Automatic LED.
The board also supplies the option that
allows for the automatic switching of the
transmitter between a receiver tray or a
modulator tray that is used as the input
tray based on the presence of video to
the modulator or the receiver tray. A
receiver tray, a modulator tray, and an IF
relay, to switch between the two outputs,
must be present in the transmitter for
the automatic switching to take place.
For automatic switching, jumper W2 on
J17 must be in Auto, between pins 1 and
2. Jumper W1 on J18 determines which
tray will be in control. The modulator tray
will be in control if W1 is between pins 1
and 2.
If a modulator and a receiver tray are in
place, the jumpers are set as stated
above, and the video input to the
modulator is present, a high will be
present at J2, pin 11. The high connects
to inverter U7B, pin 5, whose output at
pin 4 goes low. The low turns off the red
Video Fault LED DS3. The high also
connects to timer U1A, pin 5, and directly
to NOR gate U5C, pin 9. The high at the
NOR gate produces a low output at U5C,
pin 10; this low is applied through
jumper W1 on J18 and jumper W2 on J17
to the bases of Q8 to Q11. Q8 to Q11 are
reversed biased and apply the disables to
the IF relay to keep the output of the
modulator tray connected to the input of
the upconverter tray. In addition,
because Q11 is biased off, Q12 to Q14
will have highs applied to their bases to
bias them on. DS5, the green Modulator
On LED, will be lit.
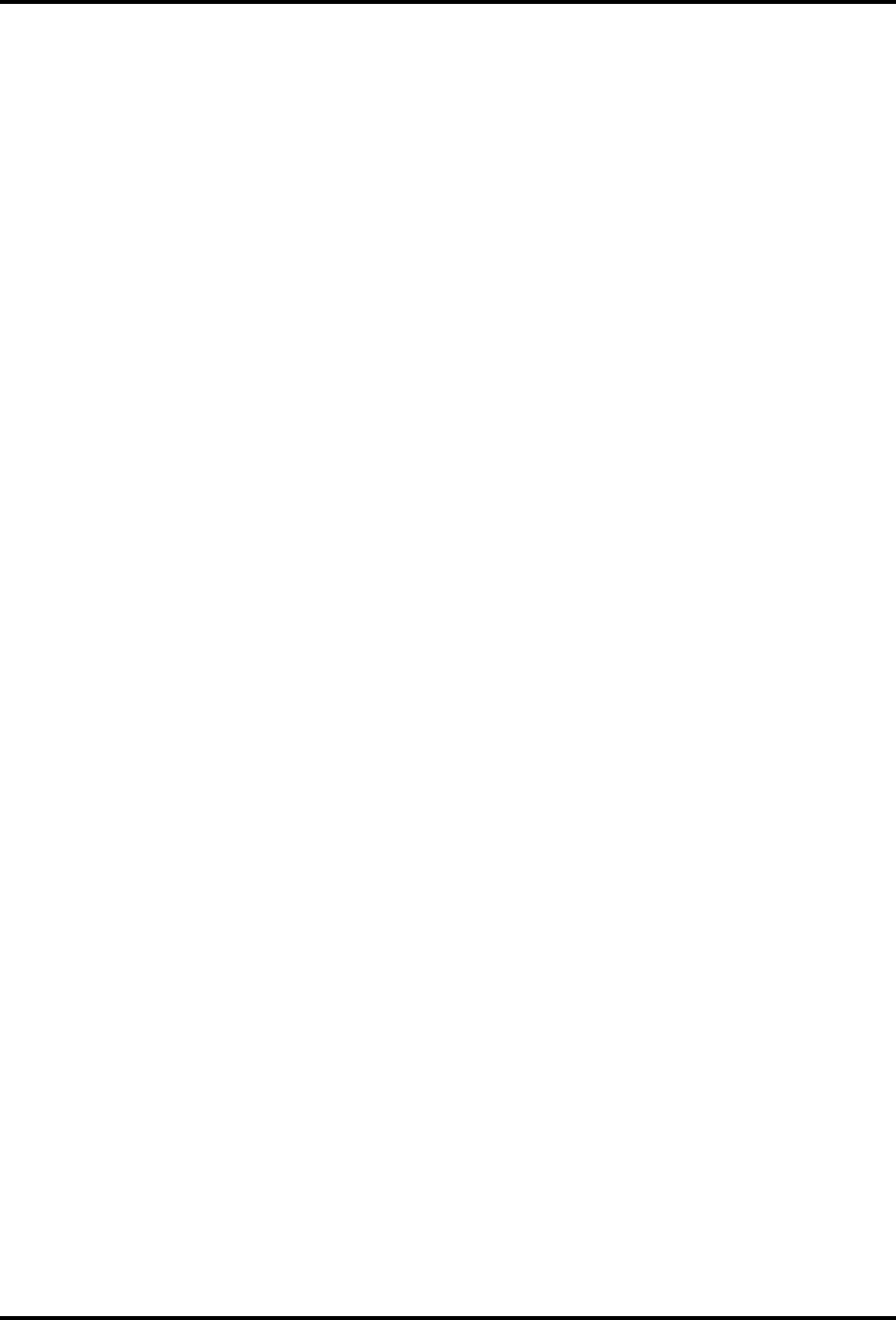
10-kW UHF Transmitter with Chapter 4, Circuit
Feedforward Drive Descriptions
840A, Rev. 0 4-38
If the video input to the modulator is
removed, a video fault low is applied to
J2, pin 11. The low connects to inverter
U7B, pin 5, whose output at pin 4 goes
high. The high lights the red Video Fault
LED DS3. The low connects to timer U1A,
pin 5, and also connects directly to NOR
gate U5C, pin 9. After 5 seconds, enough
time for the loss of video to be
determined as permanent, the output of
U1A at pin 8 will go low; the low is
applied to U5C, pin 8. With U5C pins 8
and 9 both low, the output of U5C at pin
10 will go high. The high is applied
through jumper W1 on J18 and jumper
W2 on J17 to the bases of Q8 to Q11. Q8
to Q11 are forward biased and apply the
low enables to the IF relay to connect the
output of the receiver tray to the input of
the upconverter tray and also to the
green Receiver On LED DS4 and the
external Receiver On LED.
During normal operation, there is no
video fault input from the exciter tray
and there is a high at J16, pin 1. The
high is applied to inverter U7C, pin 7,
whose output at pin 6 goes low and
extinguishes the red Video Fault LED
DS2. The high is also applied to AND gate
U6B, pin 6. Pin 5 of U6B will be a high
during normal operation. A high on pins 5
and 6 of U6B produces a high output at
pin 4. The high is applied immediately to
pin 6 of NOR gate U5B and to pin 11 of
counter U1B. After approximately 6
seconds, enough time to determine that
a genuine fault has occurred, a high is
applied to pin 5 of U5B. The high on pin 5
and pin 6 of U5B produces a low on pin
4. The low is applied to NOR gate U5D,
pin 12, and, if the Automatic/Manual
switch is in Auto, a low will also be on
U5D, pin 13. Lows on pins 12 and 13 of
U5D will cause the output at pin 11 to go
high and forward bias Q2. The drain of
Q2 will go low and is applied to J11, pin
8, and then to Operate/Standby relay K3.
The relay stays energized and in
Operate. The low from pin 4 of U5B is
also fed through inverter U7E, whose
output at pin 12 is now high. The high
connects to NOR gate U5A, pin 2. If
either pin 1 or 2, or both pin 1 and 2, are
high, a low is produced at the output of
U5A, pin 3. The low reverse biases Q3
and removes the low from the drain and
from J4, pin 4.
If a video fault from the exciter tray
occurs due to the loss of video, J16, pin
1, goes low. This low is applied to
inverter U7C, pin 7, whose output at pin
6 goes high and lights the red Video Fault
LED DS2. The low video fault is also
applied to AND gate U6B, pin 6. The level
of the ALC voltage from the receiver tray
is fed through op-amp U3D and produces
a high output as long as the ALC level
from the receiver tray is above the
reference set by R3. This normally high
output from U3D connects to pin 5 of
AND gate U6B.
If the ALC level drops below the
threshold set by R3, pin 5 of U6B will go
low. A low on pin 5 or pin 6, or both pin 5
and pin 6, will produce a low on U6B, pin
4. The low is applied immediately to pin 6
of NOR gate U5B and to pin 11 of counter
U1B. After approximately 6 seconds,
enough time to determine that a genuine
fault has occurred, the low is applied to
pin 5 of U5B. The low on pin 5 and pin 6
of NOR gate U5B produces a high output
on pin 4. The high is applied to NOR gate
U5D, pin 12, and causes the output at
pin 11 to go low and reverse bias Q2.
The drain of Q2 will go high and the high
is applied to J11, pin 8, and then to the
Operate/Standby relay K3. The high from
pin 4 of U5B is also fed through inverter
U7E whose output at pin 12 is now low.
The low connects to NOR gate U5A, pin
2. If the Auto/Manual switch is in Auto,
U5A, pin 1, will be low. When pins 1 and
2 on U5A are both low, it produces a high
at pin 3 that forward biases Q3. The
drain of Q3 goes low and is applied to
J11, pin 2, and then to the Operate/
Standby switch, which switches the
transmitter to Standby. If the
Auto/Manual switch is in Manual, U5A,
pin 1, will be high and the output of U5A
at pin 3 will be low; this does not affect
the operation of the transmitter.
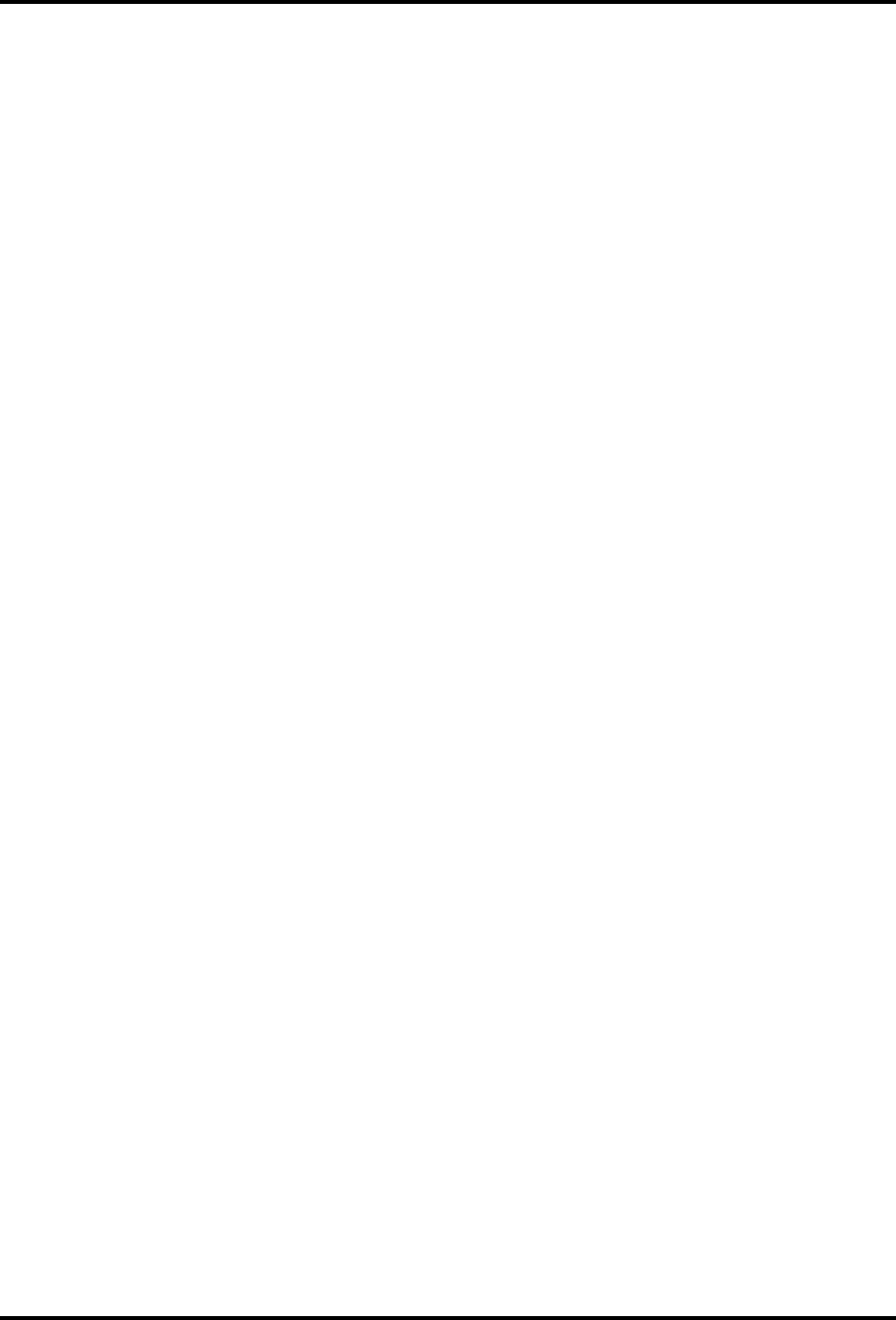
10-kW UHF Transmitter with Chapter 4, Circuit
Feedforward Drive Descriptions
840A, Rev. 0 4-39
A forward power sample of the RF output
of the transmitter is connected to J15,
pin 7, of the board. The sample connects
to op-amp U3A, pin 3. If the input
sample level stays above the level set by
R38, the output of U3A at pin 1 will be
high. The high forward biases Q15 and
Q16 and causes their drains to go low.
J14, pin 2, is low and connects to the
front panel RF Present LED DS21,
causing it to light.
A reflected power sample of the RF
output of the transmitter is connected to
J15, pin 1, of the board. The sample
connects to op-amp U3C, pin 10. If the
input sample level increases above the
level set by R44, the output of U3C at pin
8 will go high. The high is fed out of the
board at J16, pins 10 and 9, to the 3-
watt tray. This cuts back the output of
the tray and, in turn, the output power of
the transmitter. The high is also fed to
the base of Q17 and forward biases the
transistor to produce a low at J16, pin 7.
The low connects to the front panel
VSWR Cutback LED DS23 and causes it
to light.
The +12 VDC needed for the operation of
the board enters the board at jack J1, pin
3. C18 and L1 are for the filtering and
isolation of the +12 VDC before it is
applied to the rest of the board.
4.2.5.3 (A2) Differential Buffer Board
(1008-1017; Appendix B)
The (A2) differential buffer board (1008-
1017) takes the sample voltage readings
from the external power supplies and
provides readings to the voltage panel
meter and the metering control panel
interface for remote monitoring. The
differential buffer board also supplies
screen-on sense and filament-on sense
readings to (A4) the fault sensing board,
diacrode. The fault sensing board,
inverting, supplies the high voltage-on
sense, the screen-on sense, the filament-
on sense, and the filament under-voltage
readings to the control logic board. In
addition, the differential buffer board
supplies a bias-on sense to (A5) the fault
sensing board.
The (A3) differential buffer board (1008-
1017) takes the sample current readings
from the external power supplies and
provides readings to the current panel
meter and the metering control panel
interface for remote monitoring.
The (A3) differential buffer board also
supplies screen current and grid current
readings to (A6) the fault sensing board,
dual polarity. The fault sensing board,
dual polarity, supplies the screen current
and grid current fault readings to the
control logic board. The (A3) differential
buffer board supplies cathode-on sense
readings to (A5) the fault sensing board,
inverting. The fault sensing board,
inverting, supplies the cathode current
fault readings to the control logic board.
4.2.5.4 Fault Sense Board, Diacrode
(1293-1307; Appendix B)
The fault sense board, diacrode, provides
an inverted output for a sample input.
All the circuits on the board are the
same. A filament-on sense sample is
applied to J1-8 of the board. This high,
which indicates that the filament is
operating, is fed to comparator IC U1,
pin 9, and is compared to a reference
level set by R18. If the sample filament
voltage level is greater than this
reference level, a high output from U1,
pin 14, is connected to U2, pin 7, an
inverting amplifier. The high is inverted
to a low at U2, pin 6. The low output of
the board at J4, pin 8, is connected to
the control logic board where it provides
the low filament-on sense to the
automatic on/off sequence. If the sample
input is less than the reference set by the
pot, a low output from U1, pin 14, is
connected to U2, pin 7, which is an
inverting amplifier. The low is inverted to
a high at U2, pin 6. The high output of
the board at J4, pin 8, is connected to
the control logic board. The control logic
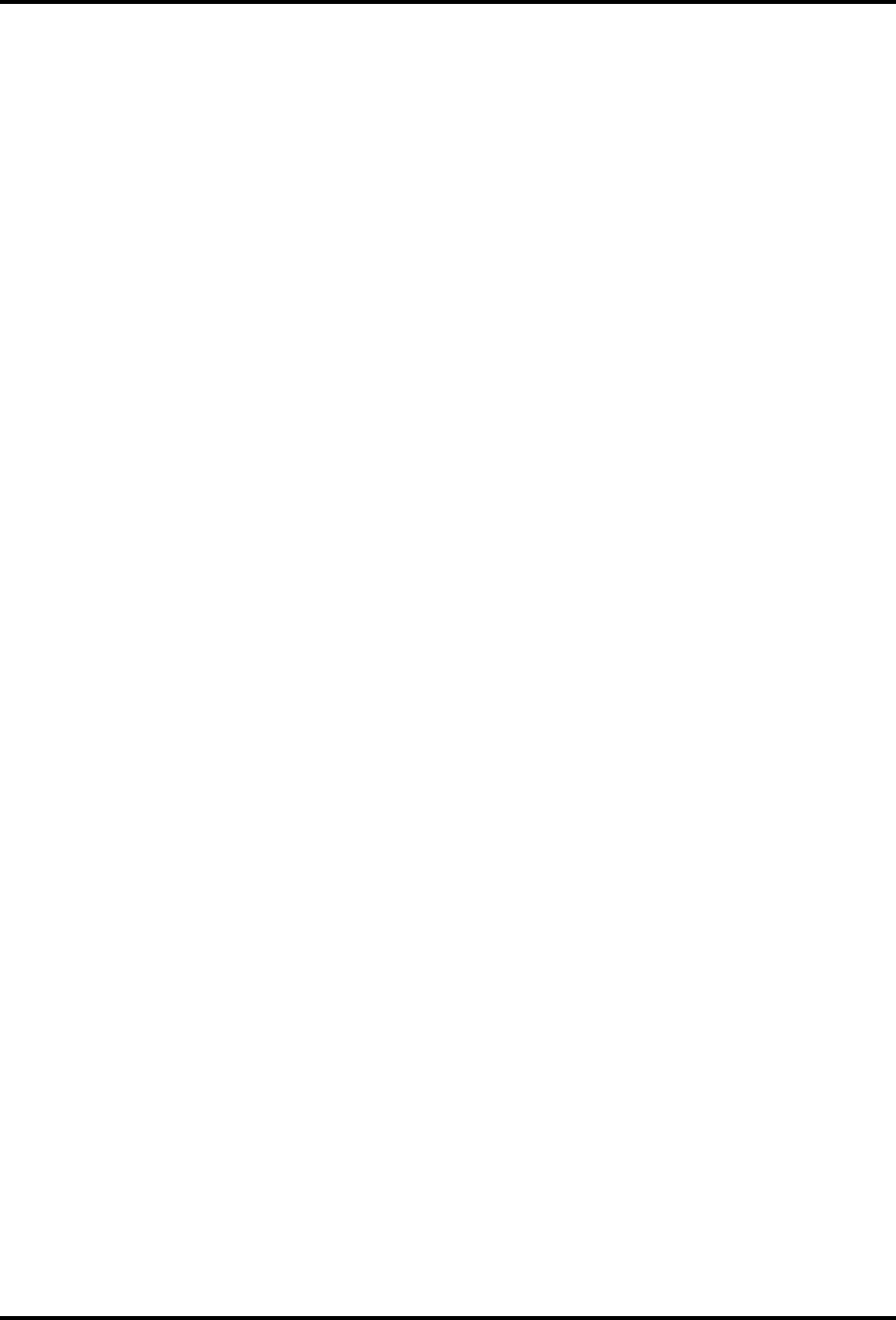
10-kW UHF Transmitter with Chapter 4, Circuit
Feedforward Drive Descriptions
840A, Rev. 0 4-40
board removes the filament-on sense to
the automatic on/off sequence.
The fault sense board is supplied by a
+12VDC source at J3-3. The capacitors
C1 and C2 provide filtering.
4.2.5.5 Inverting Fault Sense Board
(1016-1401; Appendix B)
The inverting fault sense board provides
an inverted output for a sample input,
generally from the differential buffer
board.
For example, a filament-on sense sample
is applied to J1-8 of the board. This high,
which indicates that the filament is
operating, is fed to comparator IC U1,
pin 9, and compared to a reference level
set by R18. If the sample filament
voltage level is greater than this
reference level, a high output from U1,
pin 14, is connected to U2, pin 7, which
is an inverting amplifier. The high is
inverted to a low at U2, pin 6. The low
output of the board at J4, pin 8, is
connected to the control logic board
where it provides the low filament-on
sense to the automatic on/off sequence.
If the sample input is less than the
reference set by the pot, a low output
from U1, pin 14, is connected to U2, pin
7, the inverting amplifier. The low is
inverted to a high at U2, pin 6. The high
output of the board at J4, pin 8, is
connected to the control logic board. The
control logic board removes the filament-
on sense to the automatic on/off
sequence.
The other inputs to the board are
handled in the same way.
4.2.5.6 Dual Polarity Fault Sensing Board
(1016-1402; Appendix B)
The dual polarity fault sensing board
provides a high-fault output or a low-
normal output at J2-5 or J2-4 that is
typically connected to the control logic
board. When this board is used in the 10-
kW amplifier, J4-1 is jumpered to J4-4
and J1-3 is jumpered to J1-6. The
jumpering provides an upper and lower
limit circuit for the two current sample
inputs.
A sample of the screen current is applied
to J4-2 on the board. From J4-2, the
screen current sample is connected to
comparator U1, pin 5. R6 sets the upper
limit trip point for this section of the IC.
If the screen current remains below this
reference level, U1, pin 2, will go low and
the low is applied to NAND gate U2, pins
1 and 2. U2, pin 3, will go high and the
high is applied to NAND gate U2, pin 5.
Because J4-1 is jumpered to J4-4, the
input sample of the screen current is also
applied to U1, pin 7. R12 sets the lower
limit trip point for this section of the IC.
If the screen current remains above this
reference level, U1, pin 1, will go high
and the high is applied to NAND gate U2,
pin 6. U2, pin 5, is high and U2, pin 6, is
also high during normal operation; this
causes NAND gate U2, pin 4, to be low.
During normal operation, there is a low
output on the board at J2, pin 5.
If the screen current sample applied to
comparator U1, pin 5, increases above
the upper limit trip point set by R6, U1,
pin 2, will go high. The high is applied to
NAND gate U2, pins 1 and 2. U2, pin 3,
will go low and the low is applied to
NAND gate U2, pin 5. Because J4-1 is
jumpered to J4-4, the input sample of
the screen current is also applied to U1,
pin 7. R12 sets the lower limit trip point
for this section of the IC. If the screen
current remains above this reference
level, U1, pin 1, will go high and the high
is applied to NAND gate U2, pin 6. U2,
pin 5, is now low and U2, pin 6, is high;
this causes NAND gate U2, pin 4, to be
high. A high output of the board at J2,
pin 5, is a screen current fault condition.
The screen current sample is applied to
J4-2 of the board and jumpered to J4-4.
From J4-2, the current sample is
connected to comparator U1, pin 5. R6
sets the upper limit trip point for this
section of the IC. If the screen current
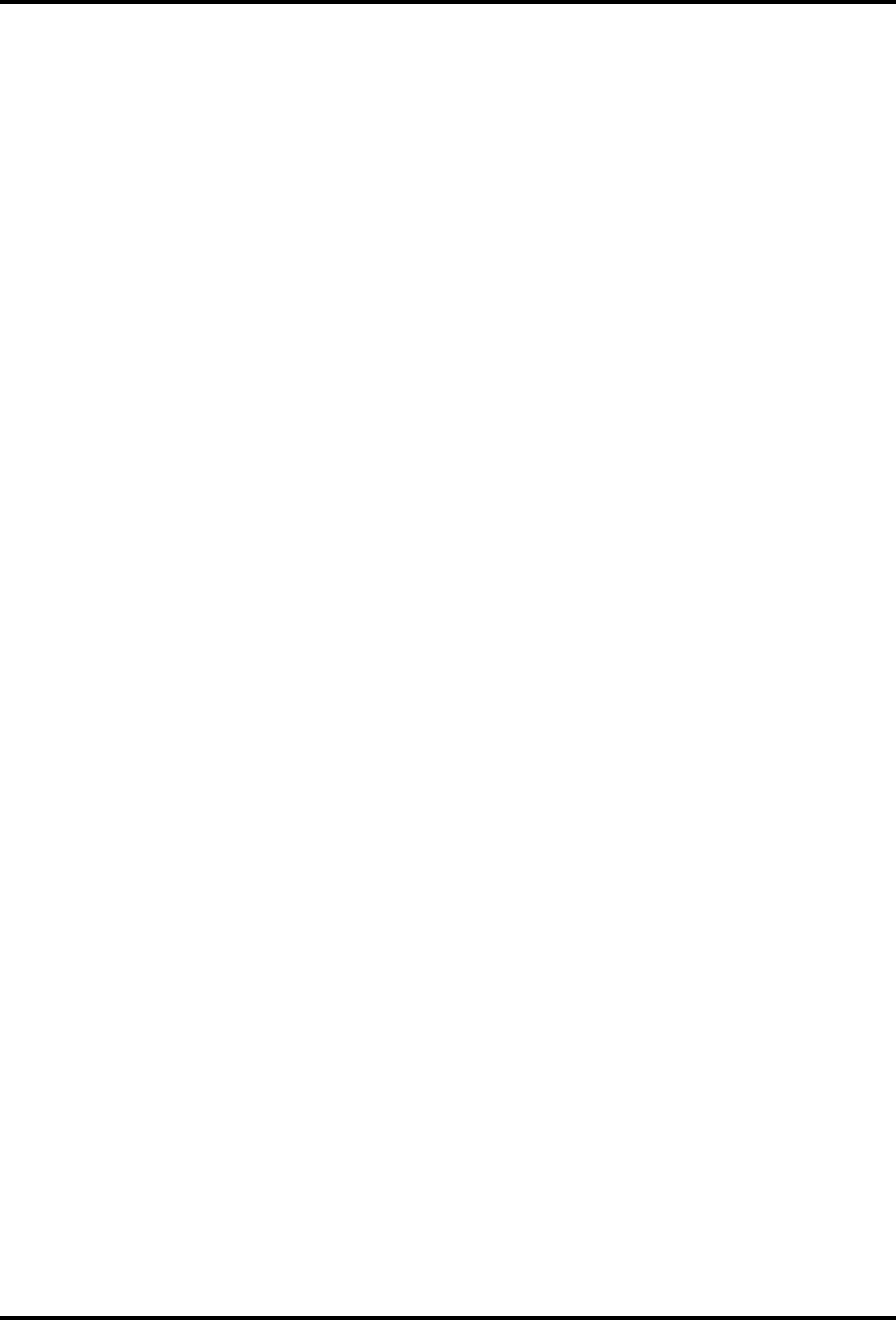
10-kW UHF Transmitter with Chapter 4, Circuit
Feedforward Drive Descriptions
840A, Rev. 0 4-41
remains below this reference level, U1,
pin 2, will go low and the low is applied
to NAND gate U2, pins 1 and 2. U2, pin
3, will go high and the high is applied to
NAND gate U2, pin 5. Because J4-1 is
jumpered to J4-4, the input sample of
the low screen current is also applied to
U1, pin 7. R12 sets the lower limit trip
point for this section of the IC. If the
screen current decreases below this
reference level, U1, pin 1, will go low and
the low is applied to NAND gate U2, pin
6. At this point, U2, pin 5, is high and U2,
pin 6, is low, causing NAND gate U2, pin
4, to be high. A high output from the
board at J2, pin 5, is a screen current
fault condition.
A sample of the grid current is applied to
J1-4 of the board. From J1-4, the current
sample is connected to comparator U1,
pin 9. R18 sets the upper limit trip point
for this section of the IC. If the grid
current remains below this reference
level, U1, pin 14, will go low and the low
is applied to NAND gate U2, pins 8 and 9.
U2, pin 10, will go high and the high is
applied to NAND gate U2, pin 12.
Because J1-3 is jumpered to J1-6, the
input sample of the grid current is also
applied to U1, pin 11. R25 sets the lower
limit trip point for this section of the IC.
If the grid current remains above this
reference level, U1, pin 13, will go high
and the high is applied to NAND gate U2,
pin 13. During normal operation, U2, pin
12, and U2, pin 13, are both high. This
causes NAND gate U2, pin 11, to be low.
A low output from the board at J2, pin 4,
occurs during normal operation.
If the grid current sample applied to
comparator U1, pin 9, increases above
the upper limit trip point set by R18, U1,
pin 14, will go high. The high is applied
to NAND gate U2, pins 8 and 9. U2, pin
10, will go low and the low is applied to
NAND gate U2, pin 12. Because J1-3 is
jumpered to J1-6, the input sample of
the grid current is also applied to U1, pin
11. R25 sets the lower limit trip point for
this section of the IC. If the grid current
remains above this reference level, U1,
pin 13, will go high and the high is
applied to NAND gate U2, pin 13. U2, pin
12, is now low and U2, pin 13, is high;
this causes NAND gate U2, pin 11, to be
high. A high output from the board at J2,
pin 4, is a grid current fault condition.
The grid current sample is applied to J1-4
on the board and jumpered to J1-7. From
J1-4, the current sample is connected to
comparator U1, pin 9. R18 sets the upper
limit trip point for this section of the IC.
If the grid current remains below this
reference level, U1, pin 14, will go low
and the low is applied to NAND gate U2,
pins 8 and 9. U2, pin 10, will go high and
the high is applied to NAND gate U2, pin
12. Because J1-3 is jumpered to J1-6,
the input sample of the low grid current
is also applied to U1, pin 11. R25 sets the
lower limit trip point for this section of
the IC. If the grid current decreases
below this reference level, U1, pin 13,
will go low and the low is applied to
NAND gate U2, pin 13. At this point, U2,
pin 12, is high and U2, pin 13, is low,
causing NAND gate U2, pin 11, to be
high. A high output from the board at J2,
pin 4, is a grid current fault condition.
4.3 (A3) High-Voltage Power Supply
Assembly, 208/240 VAC (1068022;
Appendix A)
4.3.1 Current Metering Board (1084-
1205; Appendix B)
The current metering board takes a
voltage sample from an operating power
supply and provides an output level that
can be used in a current metering circuit.
The sample voltage input is applied at J1,
pins 1 and 3, and is fed to a pi-
attenuator network consisting of R1, R2,
R3, and R4. The value of R1 can be
changed to increase or lower the value of
the input voltage for the desired current
meter reading. R3 can be adjusted to
calibrate the output level and display an
accurate meter reading of the current
value.
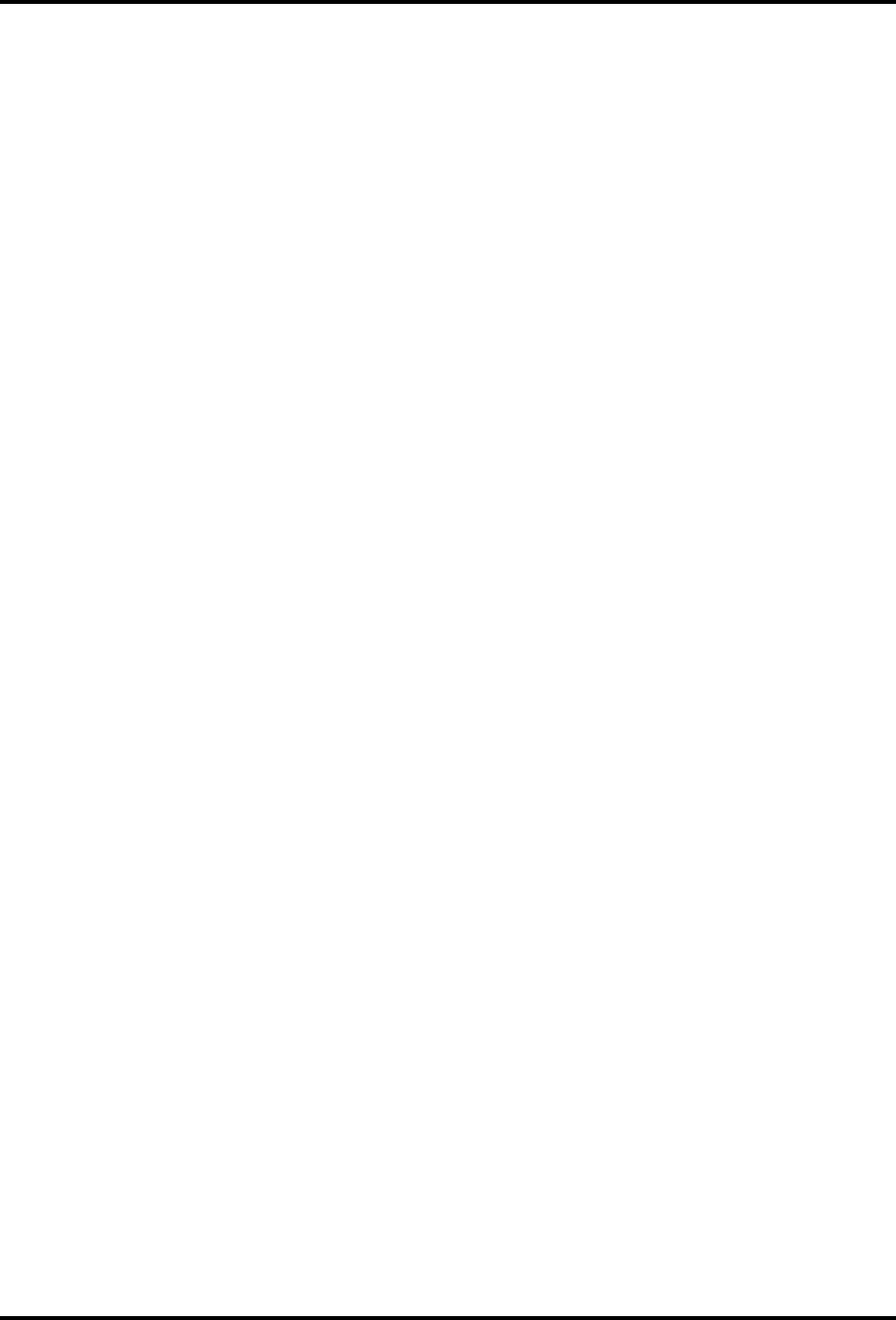
10-kW UHF Transmitter with Chapter 4, Circuit
Feedforward Drive Descriptions
840A, Rev. 0 4-42
VR1 and VR2 are back-to-back 10 VDC
zener diodes that protect the external
metering circuits from a high-voltage
problem by shunting out the higher
voltage and allowing only a maximum of
±10 VDC to be present at the output.
C1 is an AC bypass capacitor for the
reduction of any AC ripple at the output.
The external current metering circuit
connects to J2, pins 1 and 3.
4.3.2 (A10 and A11) Power Supply
Metering Boards (1084-1213 and
1016-1028; Appendix B)
The power supply metering board takes a
voltage sample from an operating power
supply and provides an output level that
is used in a metering circuit.
The sample voltage input is applied at J1,
pins 1 and 3, and is fed to a pi-
attenuator network consisting of R1, R2,
R3, and R4. The value of R1 can be
changed to increase or lower the value of
the input voltage for the chosen output
meter reading. R3 can be adjusted to
calibrate the output level to allow an
accurate meter reading of the value to be
displayed.
VR1 and VR2 are back-to-back 10-VDC
zener diodes that protect the external
metering circuits from a high-voltage
problem by shunting out the higher
voltage and allowing only a maximum of
±10 VDC to be present at the output.
C1 is an AC bypass capacitor for the
reduction of any AC ripple at the output.
The external metering circuit connects to
J2, pins 1 and 3.
4.3.3 (A5, A6, and A7) High-Voltage
Rectifier Board (1293-1101;
Appendix B)
The high-voltage rectifier board provides
a full-wave rectifier for the AC input. A
total of three high-voltage rectifier
boards are used with a three-phase AC
input: one for each of the three 2.6 kVAC
output legs of the high-voltage
transformer.
The high-voltage rectifier board has a 4-
amp fuse mounted at the (E1) AC input
to protect the board from surges or
spikes on the AC input line. The input AC
is applied to two rows of diodes: one for
positive and one for negative
rectification. Each row contains 17 diodes
in series that provide for peak inverse
hi gh-voltage protection. Each diode has a
1 MW/½-W resistor and a .001 mF/3-kV
capacitor, mounted in parallel, that
creates equal distribution of the voltage
across each diode.
The positive leg of diodes connects to the
E2 (+) terminal. The negative leg of
diodes connects to the E3 (-) terminal.
The positive and negative outputs of one
high-voltage rectifier board connects to
the positive and negative outputs of the
other two high-voltage rectifier boards.