Nokia Solutions and Networks T5GX1 UBS CDMA XMI Transceiver at 800 MHz User Manual Exhibit 121b
Nokia Solutions and Networks UBS CDMA XMI Transceiver at 800 MHz Exhibit 121b
Contents
Exhibit 121b

T ask 4: R ack Mounting the Optional PSM Shelf Chapter 2: UBS Macro B T S Installation Procedure
Task 4: Rack Mounting the Optional PSM Shelf■■■■■■■■■■■■■■■■■■■■■■■■■■■■■■■■■■■■■■■■■■■■■■■■■■■■■■■■■■■■■■
■
■
Objectives
The objectives of this procedure are as follows:
•F or -48 V DC or 220 V AC UBS only .
Install the PSM shelf to the bottom of the rack. The site configuration/characteristics will
determine if a PSM shelf is to be installed.
•Install the appropriate, -48 V DC or 220 V AC , PSMs into PSM shelf slots 1 and 2. F or
the low capacity frame, either two -48 V DC or two 220 V AC PSMs are installed in the
shelf . The second PSM is for redundancy .
Required items
The following items are required:
•Either a -48 V DC or a 220 V AC PSM shelf (whichever is applicable)
•Either two -48 V DC or two 220 V AC PSMs (whichever is applicable)
•Eight (8) M5 x 12 mm screws for mounting the PSM shelf - these screws are packaged
with the PSM shelf
•T ape measure with millimeter scale, capable measuring up to 1200 mm or with inch scale,
capable measuring up to 48 inches; for measuring screw location heights on rack
•TORX T25 bit and driver
•T orque driver
Procedure
Procedure 2 -3 gives the procedure for performing T ask 4.
Procedure 2 -3 Procedure for T ask 4
1
Locate the bottom RU that is to be used for the installation of the PSM shelf .
2
Using a tape measure, measure mounting screw location heights on each
side of the rack. Measure from the bottom of the RU determined in step 1
(Refer to Figure 2-13 ). Mark the following screw locations:
Continued
2 -32 68P09283A62 -3
PRELIMINARY A UG 2007
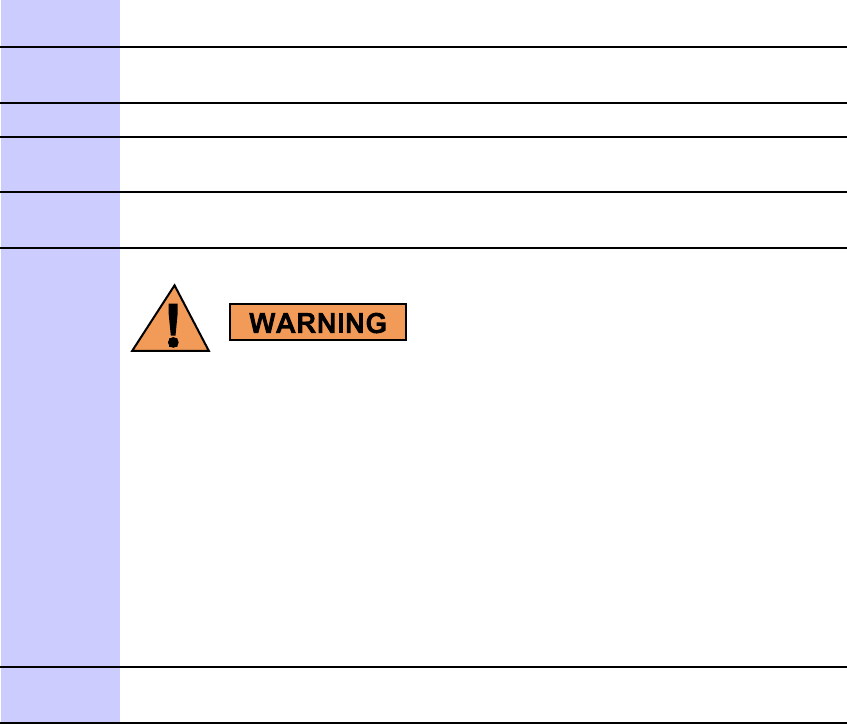
R20 1X UBS Macro B T S Hardw are Installation T ask 4: R ack Mounting the Optional PSM Shelf
Procedure 2 -3 Procedure for T ask 4 (Continued)
•136 mm (5.35 inches) for PSM shelf
3
P artially insert an M5 x 12 mm screw into each location marked on the rack.
Leave the screw heads extending 7 mm out from the rack surface.
4
Remove the PSM shelf from its packaging.
5
Align the keyhole slots in the PSM shelf with the bottom screws, installed in
step 3 above (Refer to Figure 2-14 ).
6
Insert screws in the 6 open slots of the PSM shelf . Using TORX T25 driver ,
tighten all 8 PSM shelf screws to 4.77 N-m (42 in-lb).
7
PSM weighs appro ximately 5 kg. Be careful when handling the
PSM to prev ent damage to the equipment and personal injury .
Install the appropriate PSMs into PSM shelf slots 1 and 2 as follows:
1. Grasp the handle on the front panel of the PSM with one hand while
carefully supporting the bottom of the module with the other hand.
2. Properly orient the PSM and insert it into the slot.
3. Slowly slide the module into the shelf until the rear connectors are
fully seated. Make sure that the PSM is fully engaged with the shelf
backplane slot connectors.
8
Using a T25 TORX bit and torque driver , tighten the PSM captive retaining
thumbscrew to 2.37 N-m (21 in-lb).
68P09283A62 -3 2 -33
PRELIMINARY A UG 2007
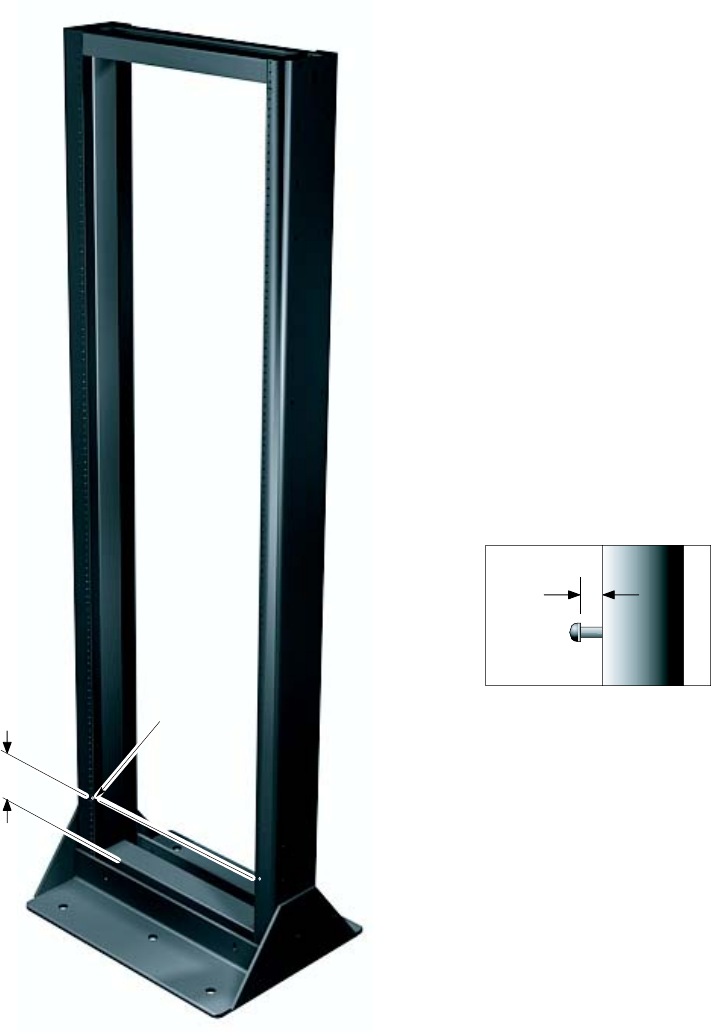
T ask 4: R ack Mounting the Optional PSM Shelf Chapter 2: UBS Macro B T S Installation Procedure
Procedural reference diagrams
The following diagrams help clarify certain steps in Procedure 2 -3 .
Figure 2 -13 Hanger screw la y out for the optional PSM shelf
136
Hanger Screw Layout for optional PSM Shelf
Hanger Screw
(Detail A)
NOTE
1. All dimensions are in millimeters
2. 1800 mm high rack shown. Dimension and hanger screw locations
are also applicable for the 1400 mm rack. ti-cdma-06011.eps
Detail A
Hanger Screw Extension
7
2 -34 68P09283A62 -3
PRELIMINARY A UG 2007
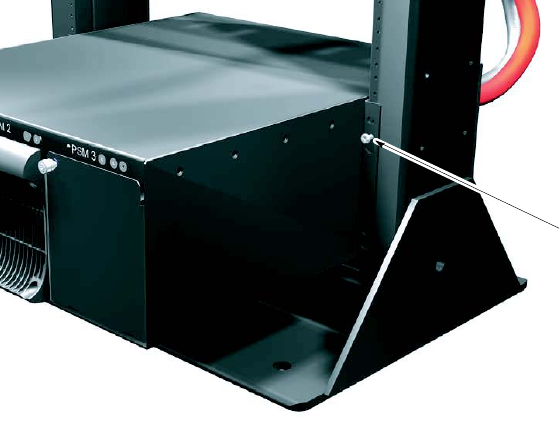
R20 1X UBS Macro B T S Hardw are Installation T ask 4: R ack Mounting the Optional PSM Shelf
Figure 2 -14 Hanging the PSM shelf
ti-cdma-05869.eps
PSM shelf keyhole
located on hanger screw
NOTE
1. A keyhole/hanger screw is located on both the right and left sides.
Both keyholes/hanger screws should be engaged at the same time.
68P09283A62 -3 2 -35
PRELIMINARY A UG 2007
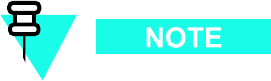
T ask 5: R ack Mounting for Low -Capacit y Fr ame Chapter 2: UBS Macro B T S Installation Procedure
Task 5: Rack Mounting for Low -Capacity Frame■■■■■■■■■■■■■■■■■■■■■■■■■■■■■■■■■■■■■■■■■■■■■■■■■■■■■■■■■■■■■■
■
■
Objective
The objective of T ask 5 is to install the UBS Macro carrier strip assembly into an EIA 19 -inch
rack.
The UBS Macro carrier strip assembly contains all of the equipment required for configuring a
low -capacity , +27 V DC starter frame. The layout of the equipment on the carrier strips allows
capacity expansion of the frame.
The most common and preferred method is to install the UBS Macro carrier strip assembly into
an 1800 mm or 1400 mm high rack. This method requires that there be 600 mm of clearance on
the left and right sides of the rack.
The UBS Macro carrier strip assembly requires a minimum of 27 R ack Units (RUs) of
continuous space.
Required items
The following items are required:
•UBS Macro carrier strip assembly
•T ape measure with millimeter scale, capable measuring up to 1200 mm or with inch scale,
capable measuring up to 48 inches; for measuring screw location heights on rack
•T wenty -six (26) M5 x 12 mm screws for mounting the UBS carrier strip assembly - these
screws are included in the STGN4034 Installation Kit that is packaged with the UBS Macro
carrier strip assembly
•TORX T25 bit and driver
•T orque driver
•10 mm socket and ratchet
2 -36 68P09283A62 -3
PRELIMINARY A UG 2007
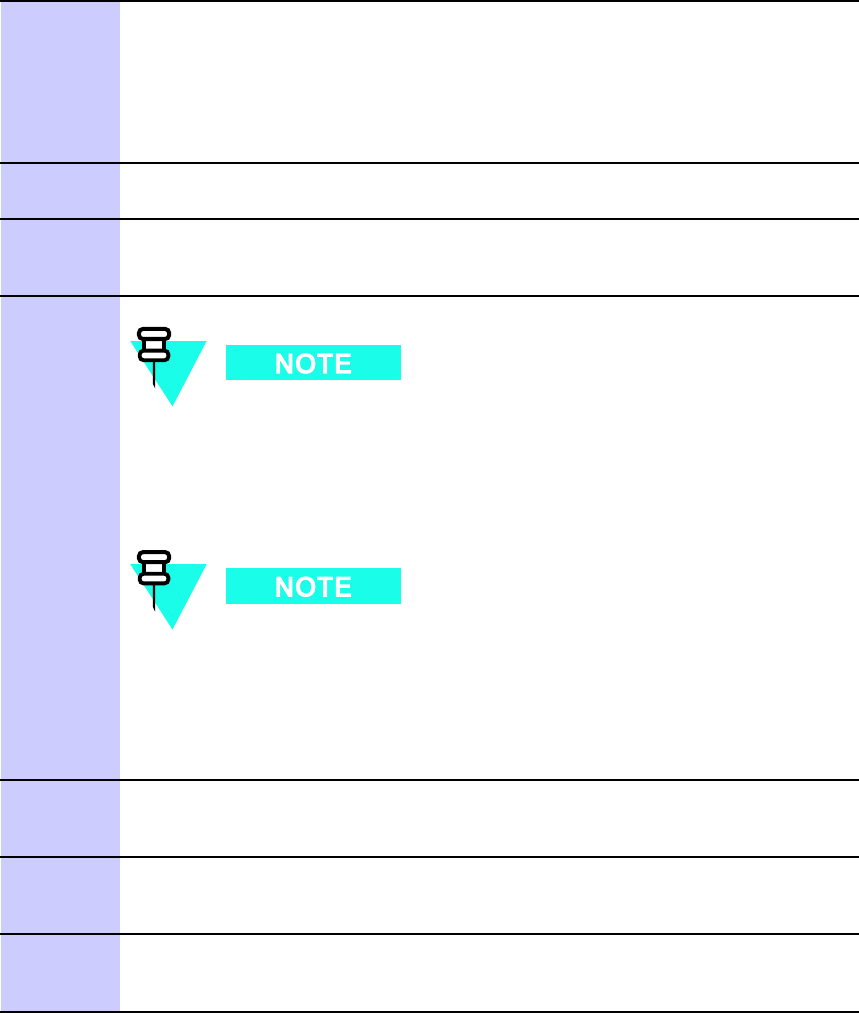
R20 1X UBS Macro B T S Hardw are Installation T ask 5: R ack Mounting for Low -Capacit y Fr ame
Procedure
Procedure 2 -4 gives the procedure for performing T ask 5.
Procedure 2 -4 R ack Mounting the Low -Capacit y , +27 V DC UBS Macro B T S Assembly
1
Using a tape measure, measure mounting hanger screw location heights on
each side of the rack (see Figure 2-15 Hanger screw layout for UBS Macro
carrier strip assembly on page 2- 39 ). Measure down from the very top of the
rack. Mark the following screw locations:
•95.25 mm (3.75 inches) for the top of the UBS Macro carrier strip
assembly
2
P artially insert an M5 x 12 mm screw into each location marked on the rack.
Leave the screw heads extending 7 mm out from the rack surface.
3
Move the pallet with the unpacked UBS Macro carrier strip assembly and
support near the rack so as to allow movement on both sides of the support
and in front of the rack. Leave the carrier strip assembly on the support.
4
The carrier strips allow four people to carefully lift the UBS Macro
carrier strip assembly off the support and onto the rack. The
assembly can also be lifted via some mechanical aid (hoist, etc.)
attached to the lifting loops on the ends of the carrier strips.
F our people, two on each side, are needed to lift the carrier strip
assembly .
Lift the UBS Macro carrier strip assembly up and off of the support and hang
it on the rack (see Figure 2-16 Lifting and hanging the carrier strip assembly
on the rack on page 2- 40 ).
5
Using the carrier strip hanger screws previously installed in the rack, align
the top carrier strip keyhole slots with the two hanger screws. Hang the
carrier strip assembly on these two screws.
6
Insert a screw in the two bottom carrier strip keyhole slots (see Figure 2-17
Carrier strip assembly keyhole screw locations on page 2- 41 ). Do not tighten
the screws in carrier strip keyhole slots.
7
Insert screws in the 22 open slots of the various shelves of the carrier strip
assembly . Using a T25 TORX driver , tighten these 22 screws to 4.77 N-m
(42 in-lb).
Continued
68P09283A62 -3 2 -37
PRELIMINARY A UG 2007
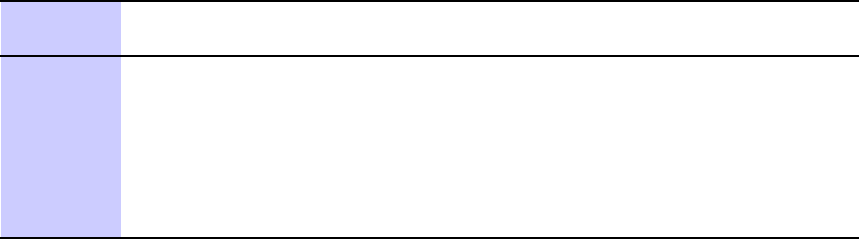
T ask 5: R ack Mounting for Low -Capacit y Fr ame Chapter 2: UBS Macro B T S Installation Procedure
Procedure 2 -4 R ack Mounting the Low -Capacit y , +27 V DC UBS Macro B T S Assembly
(Continued)
8
Using a T25 TORX driver , tighten the four screws in carrier strip keyhole
slots to 4.77 N-m (42 in-lb).
9
This step is optional and is only performed if there is
a desire to remove the carrier strips from the frame.
Remove the carrier strips from the frame as follows:
•Using a 10 mm socket and ratchet, loosen and remove the 8 nuts that
secure each carrier strip to the frame.
•Remove the carrier strip.
Procedural reference diagrams
The following diagrams help clarify certain steps in Procedure 2 -4 .
•Figure 2 -15 Hanger screw layout for UBS Macro carrier strip assembly on page 2 - 39
•Figure 2 -16 Lifting and hanging the carrier strip assembly on the rack on page 2 - 40
•Figure 2 -17 Carrier strip assembly keyhole screw locations on page 2 - 41
2 -38 68P09283A62 -3
PRELIMINARY A UG 2007
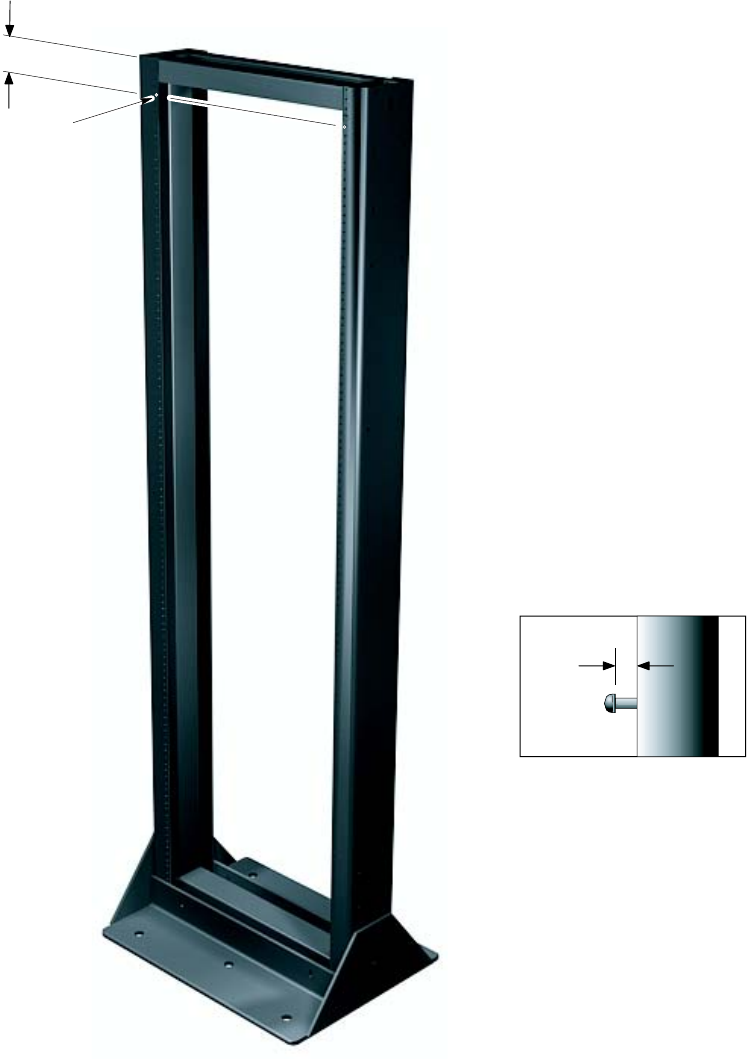
R20 1X UBS Macro B T S Hardw are Installation T ask 5: R ack Mounting for Low -Capacit y Fr ame
Figure 2 -15 shows hanger screw layout used for mounting the UBS Macro carrier strip assembly
onto a 1400 mm or 1800 mm high EIA 19 -inch rack.
Figure 2 -15 Hanger screw la y out for UBS Macro carrier strip assembly
Hanger Screw Layout for UBS
Carrier Strip Assembly
Hanger Screw
(Detail A)
NOTE
1. All dimensions are in millimeters
2. 1800 mm high rack shown. Dimension and hanger screw locations are also applicable for the 1400 mm rack ti-cdma-06012.eps
Detail A
Hanger Screw Extension
95.25
7
68P09283A62 -3 2 -39
PRELIMINARY A UG 2007
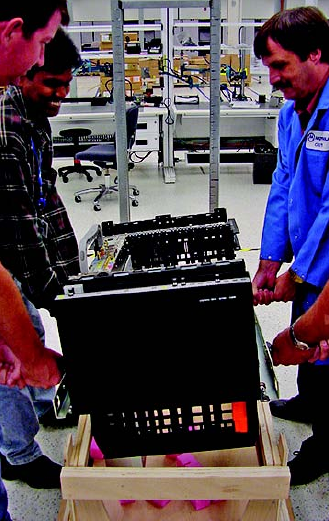
T ask 5: R ack Mounting for Low -Capacit y Fr ame Chapter 2: UBS Macro B T S Installation Procedure
Figure 2 -16 shows four people lifting and hanging the UBS Macro carrier strip assembly on
the rack.
Figure 2 -16 Lifting and hanging the carrier strip assembly on the r ack
ti-cdma-06386.eps
UBS Macro BTS Handles
2 -40 68P09283A62 -3
PRELIMINARY A UG 2007
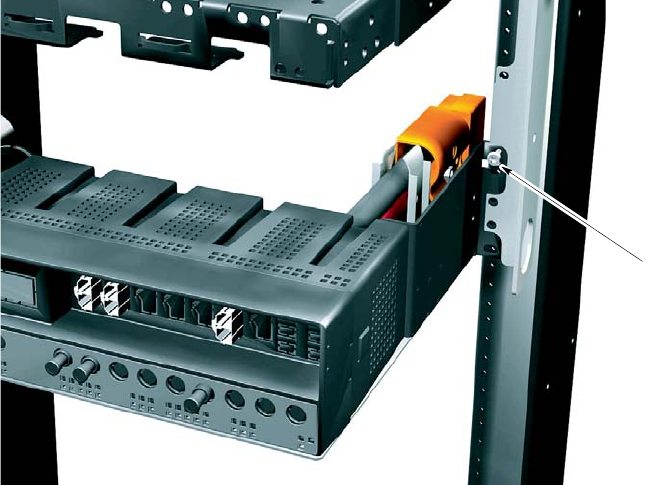
R20 1X UBS Macro B T S Hardw are Installation T ask 5: R ack Mounting for Low -Capacit y Fr ame
Figure 2 -17 shows the keyhole screw locations in a rack mounted UBS Macro carrier strip
assembly .
Figure 2 -17 Carrier strip assembly k eyhole screw locations
ti-cdma-05870.eps
Bottom keyhole of carrier strip
located on hanger screw
NOTE
1. Another carrier strip keyhole/hanger screw is located at the top of the right side carrier strip/rack rail.
The left side carrier strip/rack rail has a top and bottom keyholes/hanger screws at the same heights as the right side.
All four keyholes/hanger screws should be engaged at the same time.
68P09283A62 -3 2 -41
PRELIMINARY A UG 2007
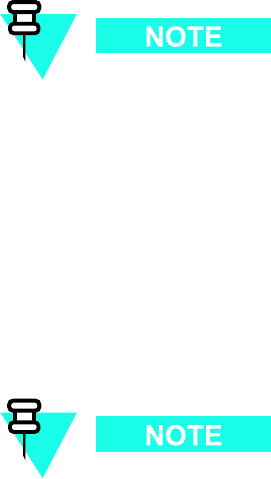
T ask 6: Expanding the Low -capacit y Fr ame Chapter 2: UBS Macro B T S Installation Procedure
Task 6: Expanding the Low -capacity Frame■■■■■■■■■■■■■■■■■■■■■■■■■■■■■■■■■■■■■■■■■■■■■■■■■■■■■■■■■■■■■■
■
■
If the initial UBS Macro BTS installation is for a low -capacity frame configuration,
skip this task and go to T ask 7: Cabling the Optional PSM Shelf on page 2 - 43 .
P erform this task only if the initial UBS Macro BTS installation is for a mid -capacity
frame configuration.
Objective
The objective of T ask 6 is to install the additional equipment required to expand the UBS Macro
BTS low -capacity starter/expansion frame to the mid -capacity frame configuration.
Currently a UBS Macro BTS low -capacity starter/expansion frame can only be
expanded to mid -capacity . In the future, the low -capacity starter/expansion frames
and mid -capacity frames will be expandable to high -capacity .
Procedure
Go to Chapter 3 Low -to -Mid Capacity Frame Expansion Procedures and perform all of the
applicable procedures for expanding the low -capacity UBS Macro BTS starter/expansion frame
to the mid -capacity frame configuration.
A fter all of the additional expansion equipment is installed, go to T ask 7: Cabling the Optional
PSM Shelf on page 2 - 43 and continue performing the remaining tasks in sequential order .
2 -42 68P09283A62 -3
PRELIMINARY A UG 2007
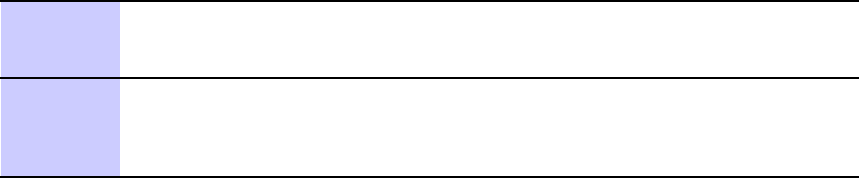
R20 1X UBS Macro B T S Hardw are Installation T ask 7: Cabling the Optional PSM Shelf
Task 7: Cabling the Optional PSM Shelf■■■■■■■■■■■■■■■■■■■■■■■■■■■■■■■■■■■■■■■■■■■■■■■■■■■■■■■■■■■■■■
■
■
Objectives
The objectives of this procedure are as follows:
•F or -48 V DC or 220 V AC UBS only .
Connect the +27 V DC power output cable from the rear of the PSM shelf to the +27 V DC
power input cable on the rear of the PDU .
•F or -48 V DC or 220 V AC UBS only
Connect the 50 -conductor cable (supplied with PSM shelf) between the PSM shelf front
panel ALARM/CONTROL connector and S SI front panel PSM connector .
Required items
The following items are required:
•50 -conductor cable (supplied with PSM shelf)
•Flat blade screw driver
Procedure
Procedure 2 -5 gives the procedure for performing T ask 7.
Procedure 2 -5 Procedure for T ask 7
1
Connect the +27 V DC power output cable from the rear of the PSM shelf
to the +27 V DC power input cable on the rear of the PDU . Mate Orange
connectors together .
2
Connect the 50-conductor cable (supplied with PSM shelf) between the PSM
shelf front panel ALARM/CONTROL connector and S SI front panel PSM
connector . Refer to Figure 2-3 and Figure 2-4 for the connector locations on
the PSM shelf front panel and on the S SI.
68P09283A62 -3 2 -43
PRELIMINARY A UG 2007

T asks 8 -9: Connecting TX/RX Antennas Chapter 2: UBS Macro B T S Installation Procedure
Tasks 8 -9: Connecting TX/RX Antennas■■■■■■■■■■■■■■■■■■■■■■■■■■■■■■■■■■■■■■■■■■■■■■■■■■■■■■■■■■■■■■
■
■
Objectives
The objectives of performing T asks 8 -9 are as follows:
•Install the external antenna cables to the Integrated Duplexer RX Filters (IDRFs).
•Install terminators on the IDRFs.
The site configuration/characteristics determines the IDRF usage.
Required items
The following items are required:
•External TX and RX 50 Ohm coaxial cables with type N connectors (customer supplied)
•0.25 W , 50 Ohm, SMA -type male terminators (customer supplied) for unused directional
coupler port connectors
•50 W N -type male terminator (customer supplied) for unused TX/RX connectors
•SMA breakover wrench
•19 mm open–end hex wrench (N–type connector)
Location of antenna connectors
The top view of Figure 2 -1 and Figure 2 -2 show the location of the UBS Macro BTS antenna
connectors on the top of the IDRF .
Procedure
The procedure for performing T asks 8 -9 is as follows.
Procedure 2 -6 Procedure for T asks 8 -9
1
Route the customer supplied TX/RX main and RX diversity antenna cables
to the top of the Integrated Duplexer RX Filters (IDRFs), located at the
top of the frame.
Continued
2 -44 68P09283A62 -3
PRELIMINARY A UG 2007
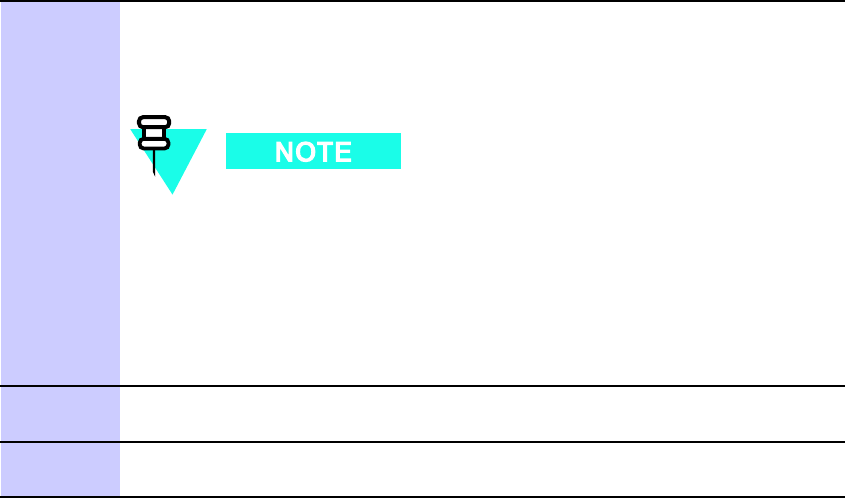
R20 1X UBS Macro B T S Hardw are Installation T asks 8 -9: Connecting TX/RX Antennas
Procedure 2 -6 Procedure for T asks 8 -9 (Continued)
2
Connect each antenna cable to the corresponding IDRF type N connector .
Refer to Figure 2-1 or Figure 2-2 , whichever is applicable, for the location of
the UBS Macro BTS antenna connectors on the top of the IDRF . Using a 19
mm open–end hex wrench, tighten the cable connectors to 4.3 N-m (38 in-lb).
The IDRFs are not labeled for a sector . T o determine the sector
for each IDRF , look at the color code of the XMI TX and RX cables
connected to the bottom of the IDRF . Refer to T able 2-2 for the
mapping of the cable color to the sector (Red = sector 1, Blue =
sector 2, Y ellow = sector 3). The sectors can also be determined
by tracing those XMI cables back to the XMI TX and RX ports,
which are labeled as TX1 and RX1 for sector 1, TX2 and RX2 for
sector 2, and TX3 and RX3 for sector 3.
3
Connect customer supplied 0.25 W , 50 Ohm, SMA-type terminators to any
unused directional coupler port connectors on the top of the IDRFs.
4
F or any unused TX/RX connector on an IDRF , install a 50 W N-type
terminator (customer supplied).
68P09283A62 -3 2 -45
PRELIMINARY A UG 2007
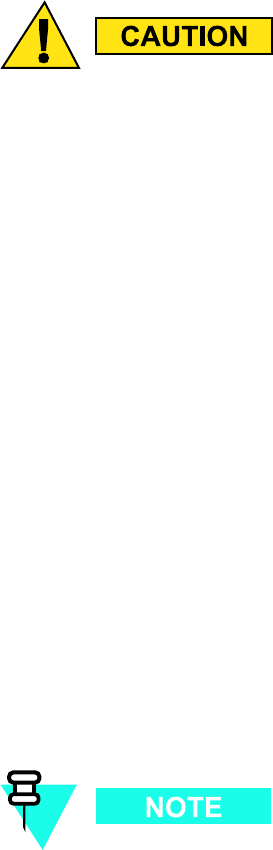
T asks 10 -13: Connecting RGPS , Spans, Customer Alarms Chapter 2: UBS Macro B T S Installation Procedure
Tasks 10 -13: Connecting RGPS, Spans, Customer
Alarms
■■■■■■■■■■■■■■■■■■■■■■■■■■■■■■■■■■■■■■■■■■■■■■■■■■■■■■■■■■■■■■
■
■
Objectives
The S SI pro vides only secondary surge protection for the RGPS and T1/E1 span
connections. The customer is responsible for pro viding primary surge protection.
The objectives of performing T asks 10–13 are as follows:
•Install RGPS cable (AA) between the RGPS cable lightning arrester and the UBS Macro
BTS .
•Install T1/E1 balanced Span I/O cable (W) between the UBS Macro BTS and the site span
line interconnect equipment.
•Install E1 unbalanced Span I/O coaxial cables (customer supplied) between the UBS Macro
BTS and the site span line interconnect equipment.
•Install Customer Alarm Input/Output (IP/OP) cables (X) between the UBS Macro BTS and
the Customer IP/OP interconnect equipment.
The site configuration/characteristics determines whether the cables in T asks 10 -13 are to be
installed.
Cabling options
The site characteristics determine the use of cables AA, W and X.
The RGPS cable (AA) is optional and used only when the optional RGPS head is used.
The T1/E1 balanced Span I/O cable (W) can carry up to 8 spans, but the UBS Macro BTS
currently supports only up to 4 spans. This is also true for E1 unbalanced Span I/O coaxial
cables (customer supplied).
F or Span I/O cable (W), the minimum size of span line wires is 26 A WG .
The usage and quantity of Customer Alarm Input/Output (IP/OP) cables (X) is determined by the
customer .
2 -46 68P09283A62 -3
PRELIMINARY A UG 2007
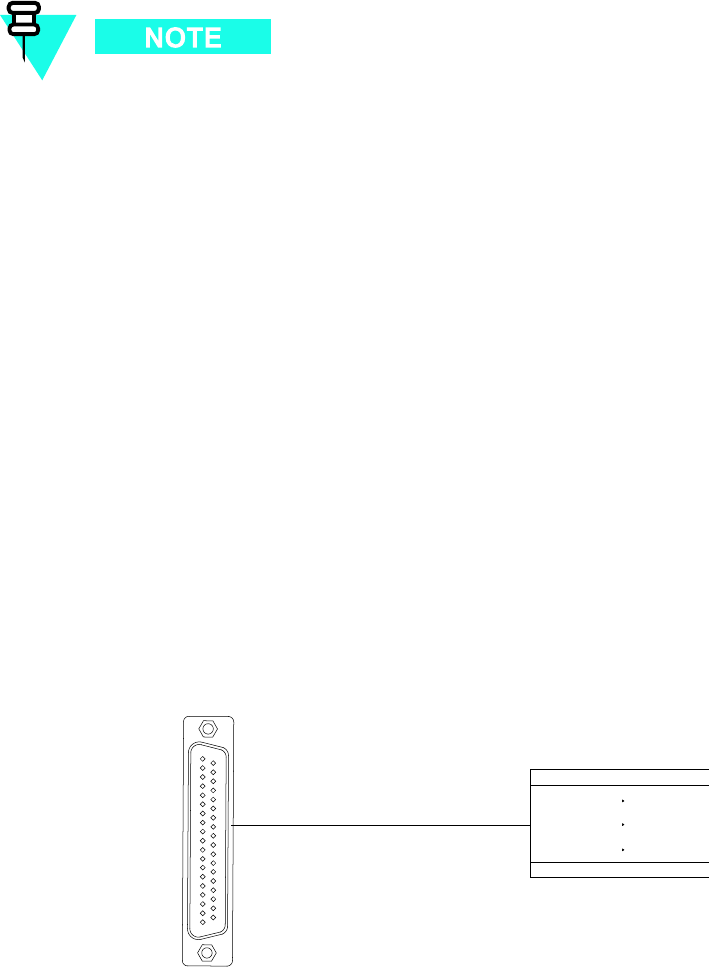
R20 1X UBS Macro B T S Hardw are Installation T asks 10 -13: Connecting RGPS , Spans, Customer Alarms
Required items
The following items are required:
•Cable AA - P art number 3086433H12
•Cable W - P art number CGDS19797321
•Cable X - P art number CGDS19797321
All S SI cable connectors with jack -screws require a flat -blade driver and should be
tightened to 1.02 N -m (9 in -lb).
Location of cables AA, W and X
Figure 2 -3 S SI front panel connectors on page 2 - 9 shows the connector locations on the front
panel of the S SI for: RGPS cable (AA), T1/E1 balanced span line cable (W), E1 unbalanced span
line coaxial cables, and customer alarm cable (X).
The optional RGPS cable (AA) has a 15 -pin D -connector on one end that connects to the RGPS
connector , located on the front of the S SI. The other cable end has loose wires. This end is
routed to the RGPS lightning arrester , where the wires connect. Refer to Figure 2 -6 through
Figure 2 -11 ,T able 2 -9 and T able 2 -10 for RGPS cable (AA) details.
Details for cables (W) and (X ) are provided in this task section.
Balanced T1/E1 cable (W) details
Figure 2 -18 and T able 2 -11 show the pin and signal information for cable W .
Figure 2 -18 T1/E1 balanced span line cable (W) pin numbering
ti-cdma-05692.eps
LOOSE WIRES, NO CONNECTOR
37-Pin-Type
(Male)
1
19 37
20
68P09283A62 -3 2 -47
PRELIMINARY A UG 2007
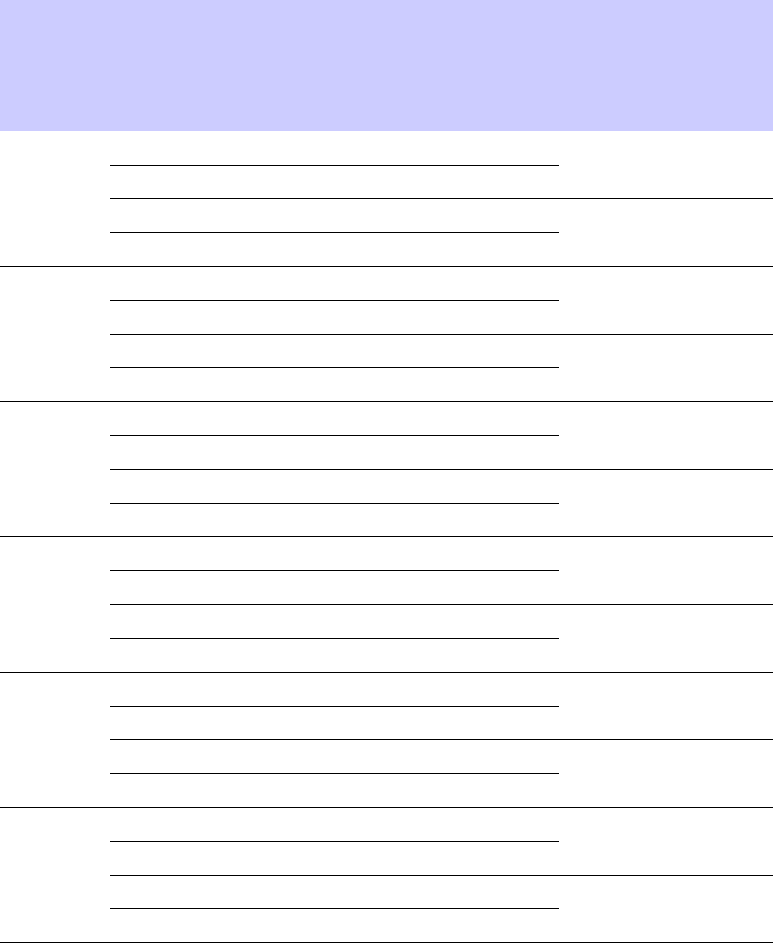
T asks 10 -13: Connecting RGPS , Spans, Customer Alarms Chapter 2: UBS Macro B T S Installation Procedure
F or E1 unbalanced 75 -Ohm BNC connector locations and labeling on the daughter card, refer to
Figure 2 -3 S SI front panel connectors on page 2 - 9 .
T able 2 -11 also shows the correlation between spans and the E1 unbalanced Span I/O coaxial
BNC connectors.
Table 2 -11 T1/E1 I/O cable W (span) signal and pin information
T1/E1 Balanced Span 36-Cond
Shielded T wisted Pair Cable (W)
37-Pin D-Sub Connector
E1 Unbalanced
75-Ohm Coaxial Cable
BNC Connection
(RING is GND/shield)
Span
number
Signal name
Pin
W ire Color
TX1_TIP 1
White/Blue
TX1_RING 20
Blue/White
TX1
RX1_TIP 12
Black/Orange
1
RX1_RING 30
Orange/Black
RX1
TX2_TIP 2
White/Orange
TX2_RING 21
Orange/White
TX2
RX2_TIP 13
Black/Green
2
RX2_RING 31
Green/Black
RX2
TX3_TIP 3
White/Green
TX3_RING 22
Green/White
TX3
RX3_TIP 14
Black/Brown
3
RX3_RING 32
Brown/Black
RX3
TX4_TIP 4
White/Brown
TX4_RING 23
Brown/White
TX4
RX4_TIP 15
Black/Gray
4
RX4_RING 33
Gray/Black
RX4
TX5_TIP 5
White/Gray
TX5_RING 24
Gray/White
TX5
RX5_TIP
16
Y ellow/Blue
5
RX5_RING 34
Blue/Y ellow
RX5
TX6_TIP 6
Red/Blue
TX6_RING 25
Blue/Red
TX6
RX6_TIP 17
Y ellow/Orange
6
RX6_RING 35
Orange/Y ellow
RX6
Continued
2 -48 68P09283A62 -3
PRELIMINARY A UG 2007
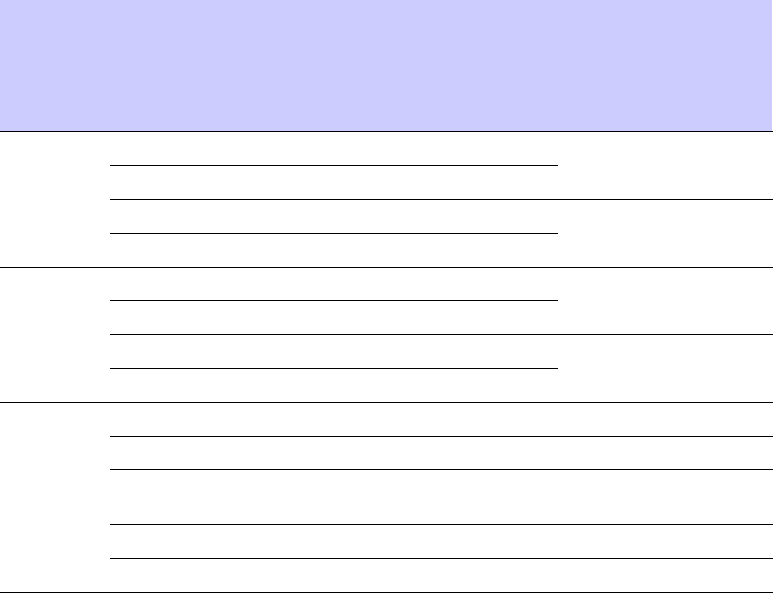
R20 1X UBS Macro B T S Hardw are Installation T asks 10 -13: Connecting RGPS , Spans, Customer Alarms
Table 2 -11 T1/E1 I/O cable W (span) signal and pin information (Continued)
T1/E1 Balanced Span 36-Cond
Shielded T wisted Pair Cable (W)
37-Pin D-Sub Connector
E1 Unbalanced
75-Ohm Coaxial Cable
BNC Connection
(RING is GND/shield)
Span
number
Signal name
Pin
W ire Color
TX7_TIP 7
Red/Orange
TX7_RING 26
Orange/Red
TX7
RX7_TIP
18
Y ellow/Green
7
RX7_RING 36
Green/Y ellow
RX7
TX8_TIP 8
Red/Green
TX8_RING 27
Green/Red
TX8
RX8_TIP 19
Y ellow/Brown
8
RX8_RING 37
Brown/Y ellow
RX8
Ground
9
Red/Brown
Ground
28
Brown/Red
Not
Connected
10
Ground
11
Black/Blue
Ground
29
Blue/Black
Customer alarm input/output (IP/OP) cable (X) details
Alarm connectors
There are two ALARM connectors on the UBS Macro S SI:
•CUSTOMER IP 1 -12 OP 1 -4 connector
•CUSTOMER IP 13 -24 OP 5 -8 connector
Each ALARM connector provides 12 inputs and 4 outputs. A total of 24 inputs and 8 outputs are
available.
68P09283A62 -3 2 -49
PRELIMINARY A UG 2007
T asks 10 -13: Connecting RGPS , Spans, Customer Alarms Chapter 2: UBS Macro B T S Installation Procedure
Function
ALARM connectors provide for Customer Defined Alarm Inputs and Outputs. The customer can
connect BTS site alarm input sensors and output devices to the UBS Macro BTS , thus providing
alarm reporting of active sensors as well as controlling output devices.
The S SI detects signals from customer input sensors and reports the detected signals to the
DMI controller , which in turn reports the detected alarm to the OMC -R, where it is displayed as
defined by the customer .
The S SI also provides switched relay contacts to customer output devices. The S SI controls
relay contacts according to output control signals from the DMI controller , in response to
customer defined commands entered at the OMC -R.
Input connections
Each input consists of a wire/pin pair (that is, input/Gnd). T o ensure proper operation, each
pair to be used must be connected to an external sensor that provides a dry -contact closure.
The customer sensor output connects between an optically isolated 5 V DC signal and an
isolated return.
F or an OPEN circuit (logic 0) between pins:
•There is 10 K Ohms or greater across the input pair .
•The signal to ground voltage is +5 V DC .
F or a CLOSED circuit (logic 1) between pins:
•There is 1 K Ohms or less across the input pair .
•The signal to ground current is a maximum of 9 mA.
Either of the above states can be defined by the customer in system software as an alarm
condition.
Output connections
Each output consists of 3 -wires/pins:
•COM
•NC
•NO
The customer output device control inputs connect between the common (COM) and either the
normally closed (NC) or normally open (NO) contacts of a relay . The NC and NO state for relay
contacts occurs when the relay coil is not energized.
Relay contacts are load rated for a maximum of 1 A at 24 V DC and 0.5 A at 50 V DC .
The toggling of relay contacts to the opposite state is controlled by system software.
Pins and signals
Figure 2 -19 ,T able 2 -12 and T able 2 -13 show the pin and signal information for cable X.
2 -50 68P09283A62 -3
PRELIMINARY A UG 2007
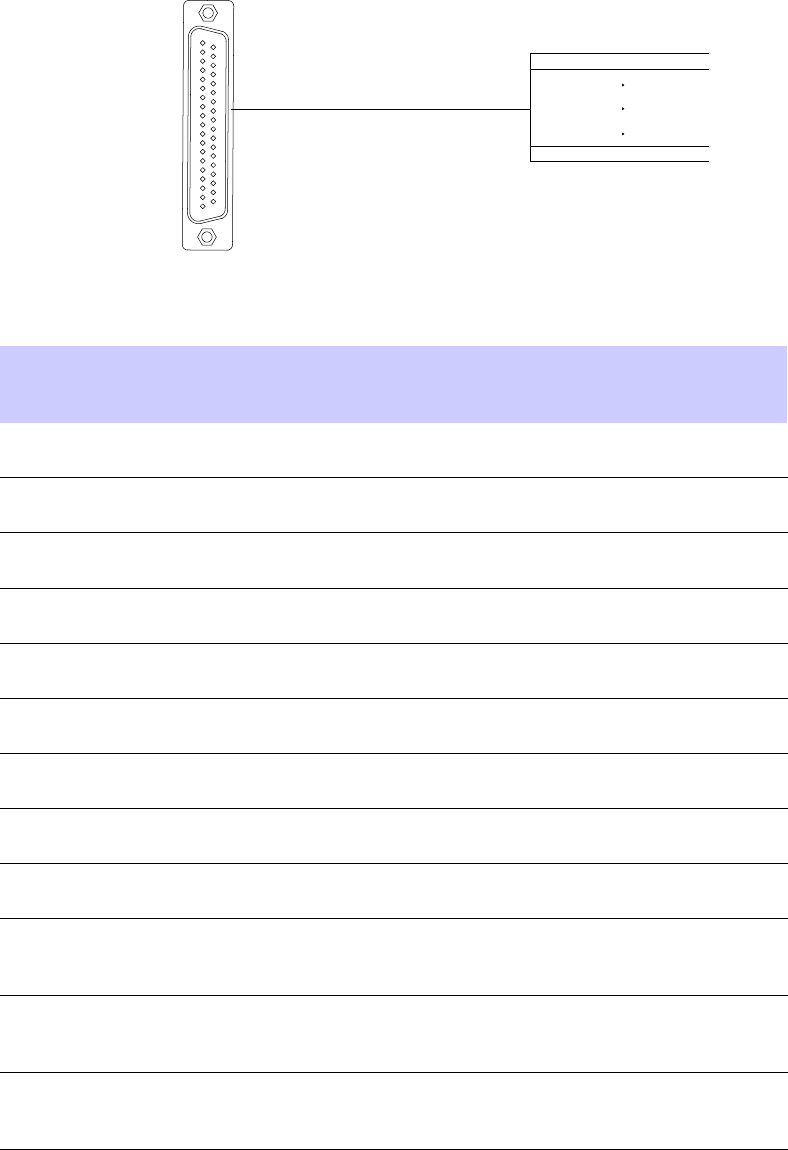
R20 1X UBS Macro B T S Hardw are Installation T asks 10 -13: Connecting RGPS , Spans, Customer Alarms
Figure 2 -19 Customer alarm cable (X) pin numbering
ti-cdma-05692.eps
LOOSE WIRES, NO CONNECTOR
37-Pin-Type
(Male)
1
19 37
20
Table 2 -12 Customer alarm cable (X) pinout for customer IP 1 -12 OP 1 -4
37-Pin
D-Sub Pin
number
Signal
Description
W ire Color
37Pin
D-Sub Pin
number
Signal
Description
W ire Color
1 Customer
Input 1
White/Blue
20
Input 1 Gnd Blue/White
2 Customer
Input 2
White/Orange
21
Input 2 Gnd Orange/White
3 Customer
Input 3
White/Green
22
Input 3 Gnd Green/White
4 Customer
Input 4
White/Brown
23
Input 4 Gnd Brown/White
5
Customer
Input 5
White/Gray
24
Input 5 Gnd Gray/White
6 Customer
Input 6
Red/Blue
25
Input 6 Gnd Blue/Red
7
Customer
Input 7
Red/Orange
26
Input 7 Gnd Orange/Red
8 Customer
Input 8
Red/Green
27
Input 8 Gnd Green/Red
9 Customer
Input 9
Red/Brown
28
Input 9 Gnd Brown/Red
10
Not
Connected
29 Customer
Output NC
1
Blue/Black
11 Customer
Output
NO 1
Black/Blue
30 Customer
Output
Common 1
Orange/Black
12 Customer
Output
NO 2
Black/Orange
31 Customer
Output
Common 2
Green/Black
Continued
68P09283A62 -3 2 -51
PRELIMINARY A UG 2007
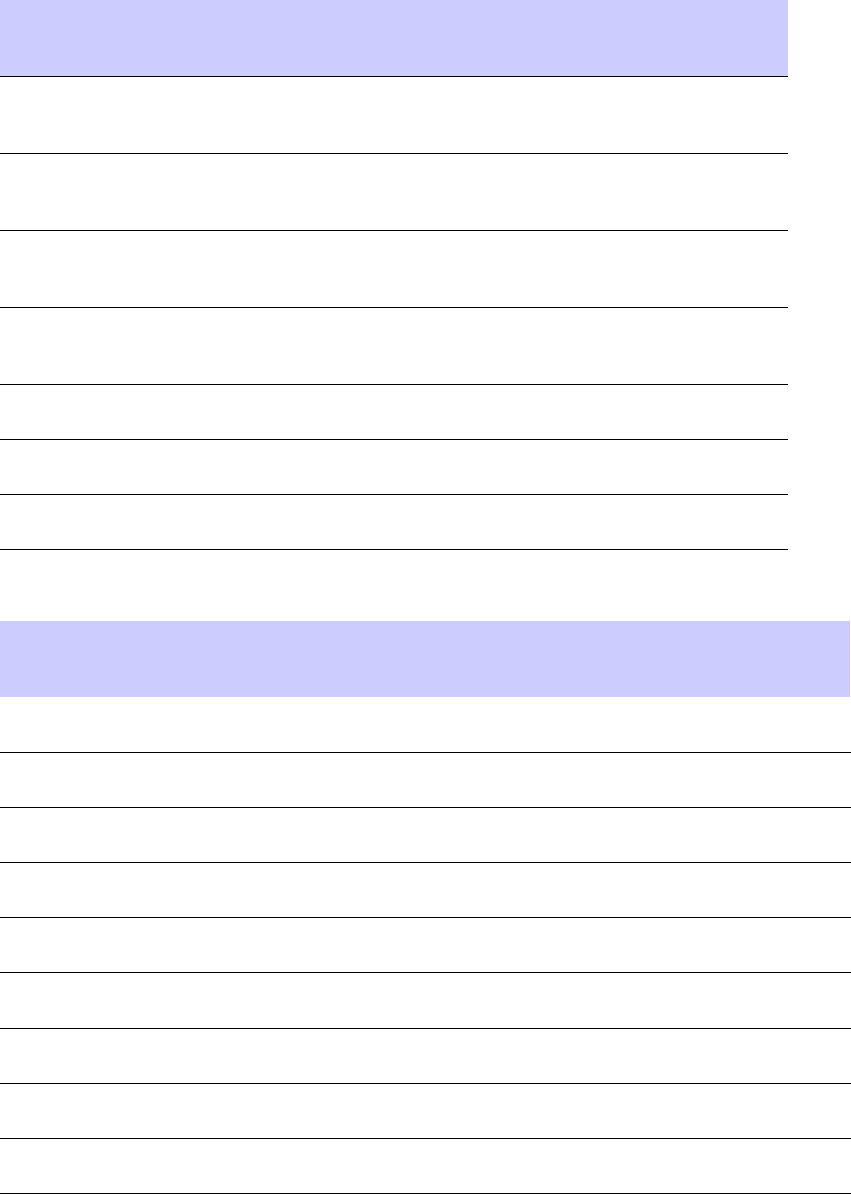
T asks 10 -13: Connecting RGPS , Spans, Customer Alarms Chapter 2: UBS Macro B T S Installation Procedure
Table 2 -12 Customer alarm cable (X) pinout for customer IP 1 -12 OP 1 -4 (Continued)
37-Pin
D-Sub Pin
number
Signal
Description
W ire Color
37Pin
D-Sub Pin
number
Signal
Description
W ire Color
13 Customer
Output
NC 2
Black/Green
32 Customer
Output NC
3
Brown/Black
14 Customer
Output
NO 3
Black/Brown
33 Customer
Output
Common 3
Gray/Black
15 Customer
Output
NO 4
Black/Gray
34 Customer
Output
Common 4
Blue/Y ellow
16 Customer
Output
NC 4
Y ellow/Blue
17 Customer
Input 10
Y ellow/Orange
35 Input 10
Gnd
Orange/Y ellow
18 Customer
Input 11
Y ellow/Green
36 Input 11
Gnd
Green/Y ellow
19 Customer
Input 12
Y ellow/Brown
37 Input 12
Gnd
Brown/Y ellow
Table 2 -13 Customer alarm cable (X) pinout for customer IP 13 -24 OP 5 -8
37-Pin
D-Sub Pin
number
Signal
Description
W ire Color
37-Pin
D-Sub Pin
number
Signal
Description
W ire Color
1 Customer
Input 13
White/Blue
20 Input 13
Gnd
Blue/White
2 Customer
Input 14
White/Orange
21 Input 14
Gnd
Orange/White
3 Customer
Input 15
White/Green
22 Input 15
Gnd
Green/White
4 Customer
Input 16
White/Brown
23 Input 16
Gnd
Brown/White
5
Customer
Input 17
White/Gray
24 Input 17
Gnd
Gray/White
6 Customer
Input 18
Red/Blue
25 Input 18
Gnd
Blue/Red
7
Customer
Input 19
Red/Orange
26 Input 19
Gnd
Orange/Red
8 Customer
Input 20
Red/Green
27 Input 20
Gnd
Green/Red
9 Customer
Input 21
Red/Brown
28 Input 21
Gnd
Brown/Red
Continued
2 -52 68P09283A62 -3
PRELIMINARY A UG 2007
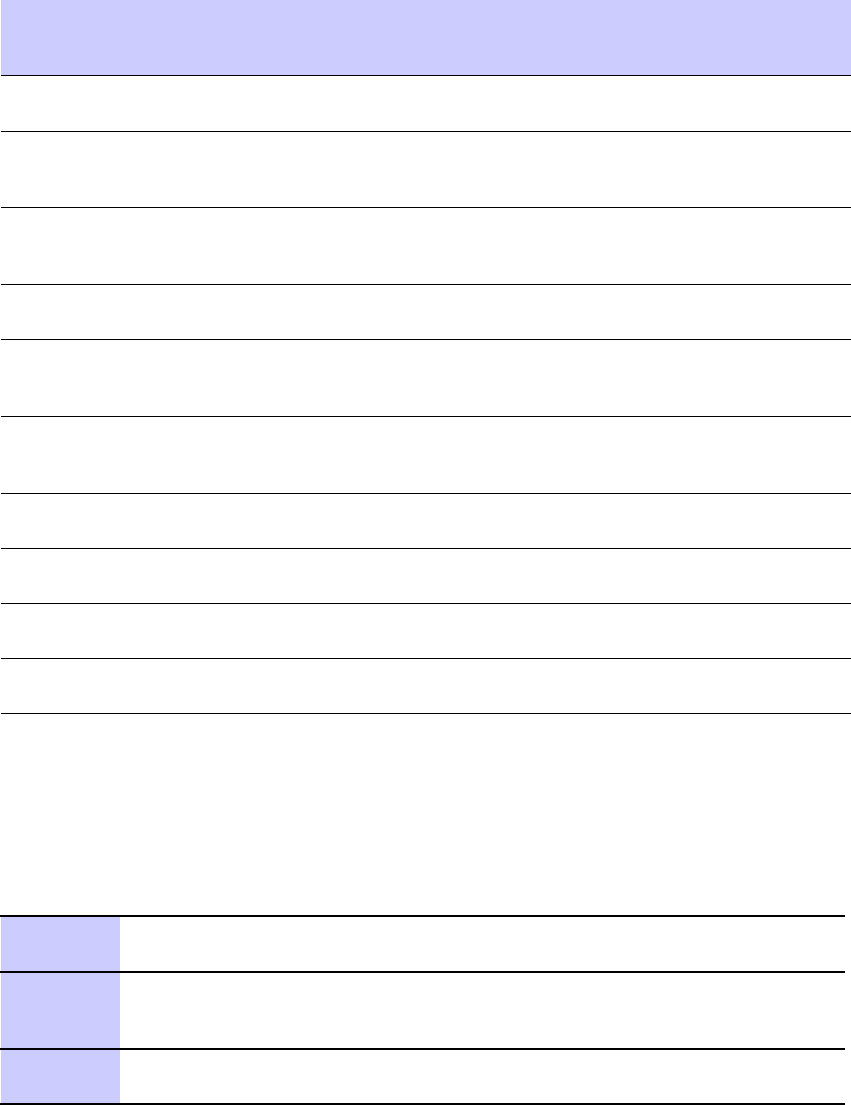
R20 1X UBS Macro B T S Hardw are Installation T asks 10 -13: Connecting RGPS , Spans, Customer Alarms
Table 2 -13 Customer alarm cable (X) pinout for customer IP 13 -24 OP 5 -8
(Continued)
37-Pin
D-Sub Pin
number
Signal
Description
W ire Color
37-Pin
D-Sub Pin
number
Signal
Description
W ire Color
10
Not
Connected
29 Customer
Output NC 5
Blue/Black
11 Customer
Output NO 5
Black/Blue
30 Customer
Output
Common 5
Orange/Black
12 Customer
Output NO 6
Black/Orange
31 Customer
Output
Common 6
Green/Black
13 Customer
Output NC 6
Black/Green
32 Customer
Output NC 7
Brown/Black
14 Customer
Output NO 7
Black/Brown
33 Customer
Output
Common 7
Gray/Black
15 Customer
Output NO 8
Black/Gray
34 Customer
Output
Common 8
Blue/Y ellow
16 Customer
Output NC 8
Y ellow/Blue
17 Customer
Input 22
Y ellow/Orange
35 Input 22
Gnd
Orange/Y ellow
18 Customer
Input 23
Y ellow/Green
36 Input 23
Gnd
Green/Y ellow
19 Customer
Input 24
Y ellow/Brown
37 Input 24
Gnd
Brown/Y ellow
Procedure
P erform T asks 10 -13 as given in Procedure 2 -7 .
Procedure 2 -7 Procedure for T asks 10 -13
1
Connect the 15-pin D -connector end of cable (AA) to the RGPS connector on
the front of the S SI. Refer to Figure 2-3 for the connector location on the S SI.
2
Route the loose end of cable (AA) to the RGPS lightning arrester and connect
the wires there. Refer to Figure 2-6 through Figure 2-11 ,T able 2-9 and
T able 2-10 .
3
F or T1/E1 balanced span line connections, go to step 4 . F or E1 unbalanced
span line connections, go to step 7 .
Continued
68P09283A62 -3 2 -53
PRELIMINARY A UG 2007
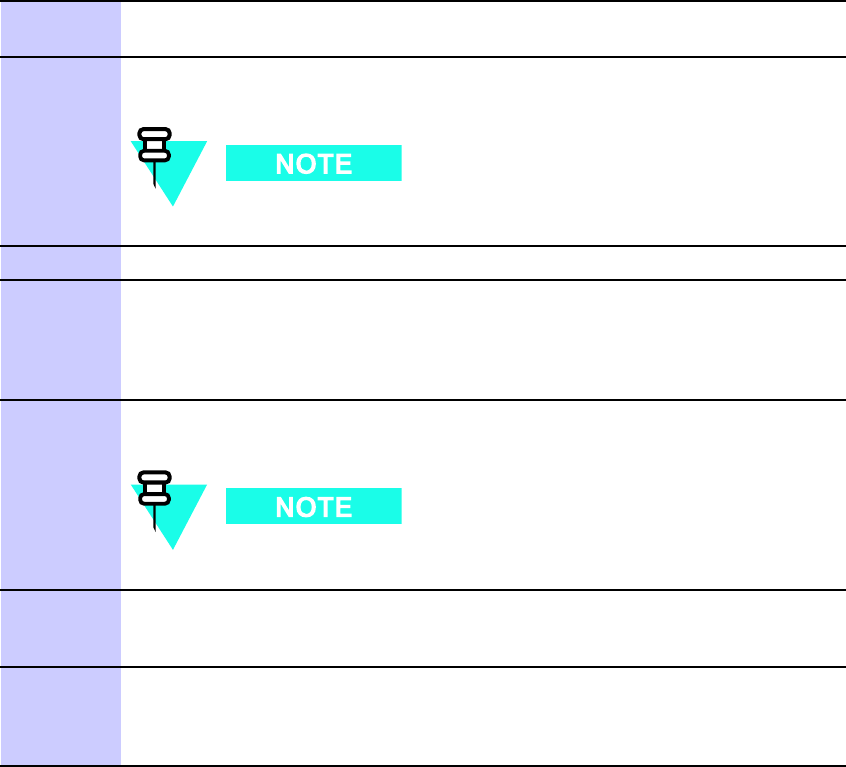
T asks 10 -13: Connecting RGPS , Spans, Customer Alarms Chapter 2: UBS Macro B T S Installation Procedure
Procedure 2 -7 Procedure for T asks 10 -13 (Continued)
4
Connect the 37-pin D -connector end of cable (W) to the SP AN connector on
the front of the S SI. Refer to Figure 2-3 for the connector location on the S SI.
5
Route the loose end of cable (W) to the customer span line interconnect
equipment and connect the wires. Refer to T able 2-11 .
The UBS Macro BTS currently supports only up to 4 spans.
6
Go to step 9 .
7
Connect E1 unbalanced Span I/O coaxial cables (customer supplied) to
the corresponding BNC connector on the S SI E1 daughter card. Refer
to Figure 2-3 for the BNC connector locations on the S SI. Also, refer to
T able 2-11 for correlation between spans and the E1 unbalanced span I/O
coaxial BNC connectors.
8
Route the other ends of the span I/O coaxial cables to the customer span line
interconnect equipment and connect the cables.
The UBS Macro BTS currently only supports up to 4 spans.
9
Connect the 37-pin D -connector of the Customer Alarm Input/Output (IP/OP)
cables (X) to the corresponding CUSTOMER IP 1-12 OP 1-4 connector and
CUSTOMER IP 13-24 OP 5-8 connector on the front of the S SI.
10
Route the loose end of cable (X) to the Customer IP/OP interconnect
equipment and connect the wires. Refer to Figure 2-3 for the CUSTOMER
IP/OP connector locations on the S SI. Also, refer to T able 2-12 and
T able 2-13 .
2 -54 68P09283A62 -3
PRELIMINARY A UG 2007
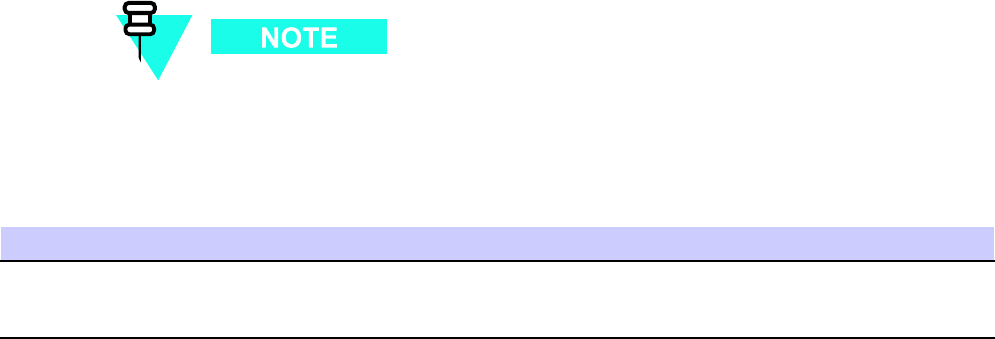
R20 1X UBS Macro B T S Hardw are Installation T ask 14: Connecting +27 V DC P ower
Task 14: Connecting +27 V DC Power■■■■■■■■■■■■■■■■■■■■■■■■■■■■■■■■■■■■■■■■■■■■■■■■■■■■■■■■■■■■■■
■
■
Objectives
T ask 14 is performed for +27 V DC UBS Macro BTS only .
The objectives of this procedure are as follows:
•A ttaching the contact/lugs, connector and cable clamp on the +27 V DC power input
cable wires.
•Connecting the +27 V DC input power cable to the rear of the PDU .
•Routing the loose ends of the wires to the site +27 V DC source for connection.
Frame power cables and connector information
The wire gauge (that is, diameter) depends on the required length of the DC power cable (DC).
Refer to T able 2 -8 for the correct wire size.
The DC connector contact/lug size depends on the wire gauge used for the DC power cable (DC).
Refer to T able 2 -14 for DC connector contact/lug part information.
In order to minimize current imbalance between the feed (+V) and return ( -V) wires used in
the cable:
•Ensure that the wire size, length and gage, of each wire used in the cable are the same.
•Ensure that contacts/lugs used in the connector are identical and match the gauge of
the wire.
Motorola recommends using 2/0 A WG cables for short cable runs; less than 661.11
cm (21.69 ft).
Table 2 -14 +27 V DC connector (Or ange) parts information
Item Description Part Number
Qty
Orange DC connector housing Anderson P ower Products Mfr
P art# 932, or Allied Electronics
Stk# 803-0097
1 per +27 V DC power feed
Continued
68P09283A62 -3 2 -55
PRELIMINARY A UG 2007
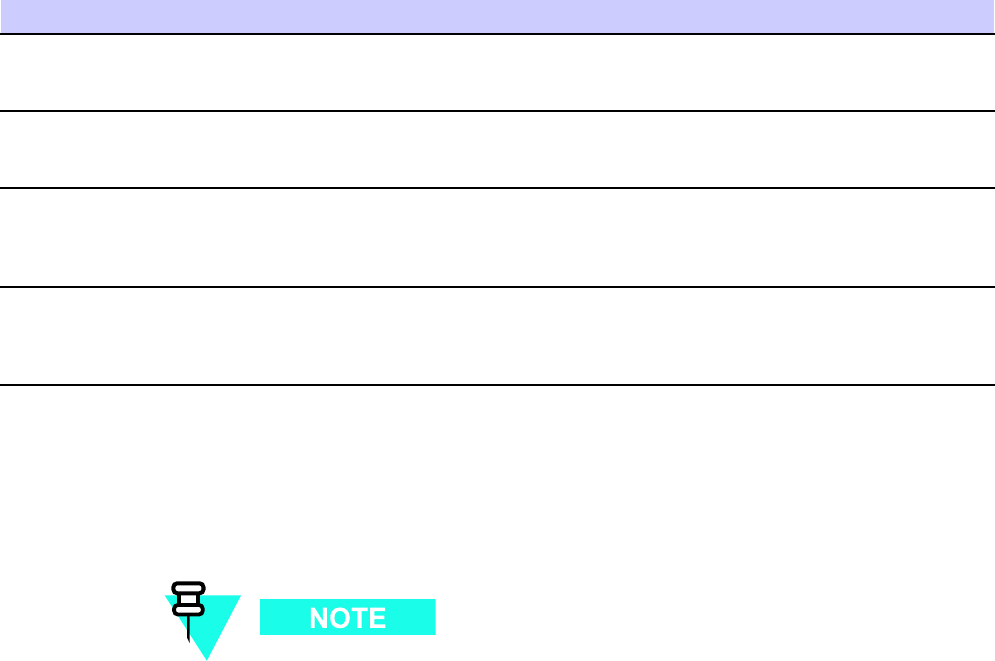
T ask 14: Connecting +27 V DC P ower Chapter 2: UBS Macro B T S Installation Procedure
Table 2 -14 +27 V DC connector (Or ange) parts information (Continued)
Item Description Part Number
Qty
A WG 2/0 connector contact/lug Anderson P ower Products Mfr
P art# 907, or Allied Electronics
Stk# 803-0500
2 per DC connector housing
A WG 3/0 connector contact/lug Anderson P ower Products Mfr
P art# 916, or Allied Electronics
Stk# 803-0502
2 per DC connector housing
A WG 4/0 connector contact/lug Anderson P ower Products Mfr
P art# 908, or Allied Electronics
Stk# 803-0504
2 per DC connector housing
Cable clamp for two single
conductors with hardware
Anderson P ower Products Mfr
P art# 996G1
1 per +27 V DC power feed
Required items
The following items are required:
•One +27 V DC P ower Input Cable (DC) - customer supplied. The wire size, length and
gauge, used for cable (DC) depends on site characteristics (see T able 2 -8 ).
Motorola recommends the use of Red wire for feed (+V) and Black wire for
return ( -V).
•T wo contacts/lugs – customer supplied. Contact/lug fastens to wire end and is inserted into
DC connector housing. F or contact/lug part number (refer to T able 2 -14 ). Contact/lug size
must match the gauge of the wire being used.
•One DC connector housing – customer supplied. Use Anderson SB350 connector housing
(Orange color) or equivalent.
•DC connector cable clamps for power cable (see T able 2 -14 or T able 2 -15 for part
information).
•Crimper tool - Anderson P ower Products part number 1368 - Hydraulic hand tool,
maximum cable size of 300 MCM
•W ire stripper/cutters.
•Digital Multi -Meter (DMM) Fluke Model 8062A with Y8134 test lead kit or equivalent; used
for precision DC and AC measurements, requiring 4 -1/2 digits.
2 -56 68P09283A62 -3
PRELIMINARY A UG 2007
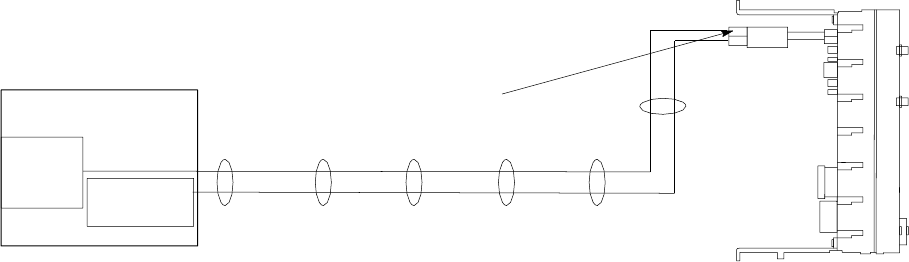
R20 1X UBS Macro B T S Hardw are Installation T ask 14: Connecting +27 V DC P ower
Power cabling and tie down requirements
T o control the inductance at the BTS DC power input due to the spacing between wires used
in the +27 V DC P ower Input Cable (DC), the feed (+V) and return ( -V) wires must be bound
together at intervals of 1 meter or less. Refer to Figure 2 -20 .
Figure 2 -20 +27 V DC power input cable (DC) wire tie -wr ap example
ti-cdma-05693.eps
TIE ALL CABLES AT 1 METER INTERVALS
+27 V Power Source
BREAKER 1
+27 V DC
PDU (Top View)
FRONT
REAR
+27 V DC
- 0 V DC
+27 V DC Power Input
Connector (ORANGE)
- 0 V DC
Contact/lug, DC connector housing and PDU input power
Figure 2 -21 shows the lugs and DC connector housing. This figure also shows the location at
which the +27 V DC Input P ower Cable (DC) connects to the rear of the PDU .
68P09283A62 -3 2 -57
PRELIMINARY A UG 2007
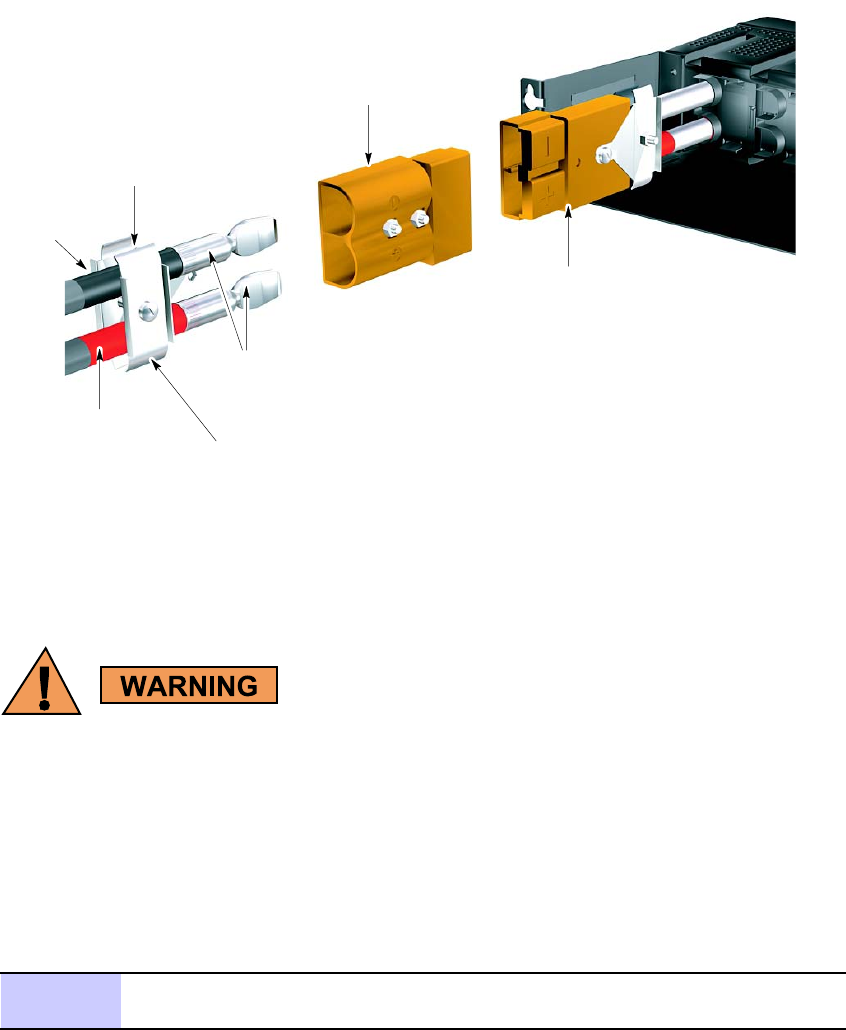
T ask 14: Connecting +27 V DC P ower Chapter 2: UBS Macro B T S Installation Procedure
Figure 2 -21 +27 V DC power input cable (DC) connector and connection to PDU
ti-cdma-05694.eps
PDU
(rear view, shown
partially cut away)
Connector
Housing
(Orange)
(+)
(-)
(-)
Crimp-on
Contact/Lugs
+27 VDC Power
Input (Orange)
RED Wire
(Typical)
(+)
2-Wire +27 VDC
Power Cable
(Customer Supplied)
BLACK WIRE
(Typical)
Cable Clamp
Procedure
P erform the T ask 14 as given in Procedure 2 -8 .
•Do not wear a wrist str ap when servicing the power supplies or power distribution
cabling.
•Ensure that the source for the DC power is in the OFF position.
•Ensure that all of the PDU circuit break ers are OFF .
Procedure 2 -8 Procedure for T ask 14
1
Ensure that the BTS ground cable (DD) is connected between the rack and
the Master Ground Bar (refer to T ask 3).
Continued
2 -58 68P09283A62 -3
PRELIMINARY A UG 2007
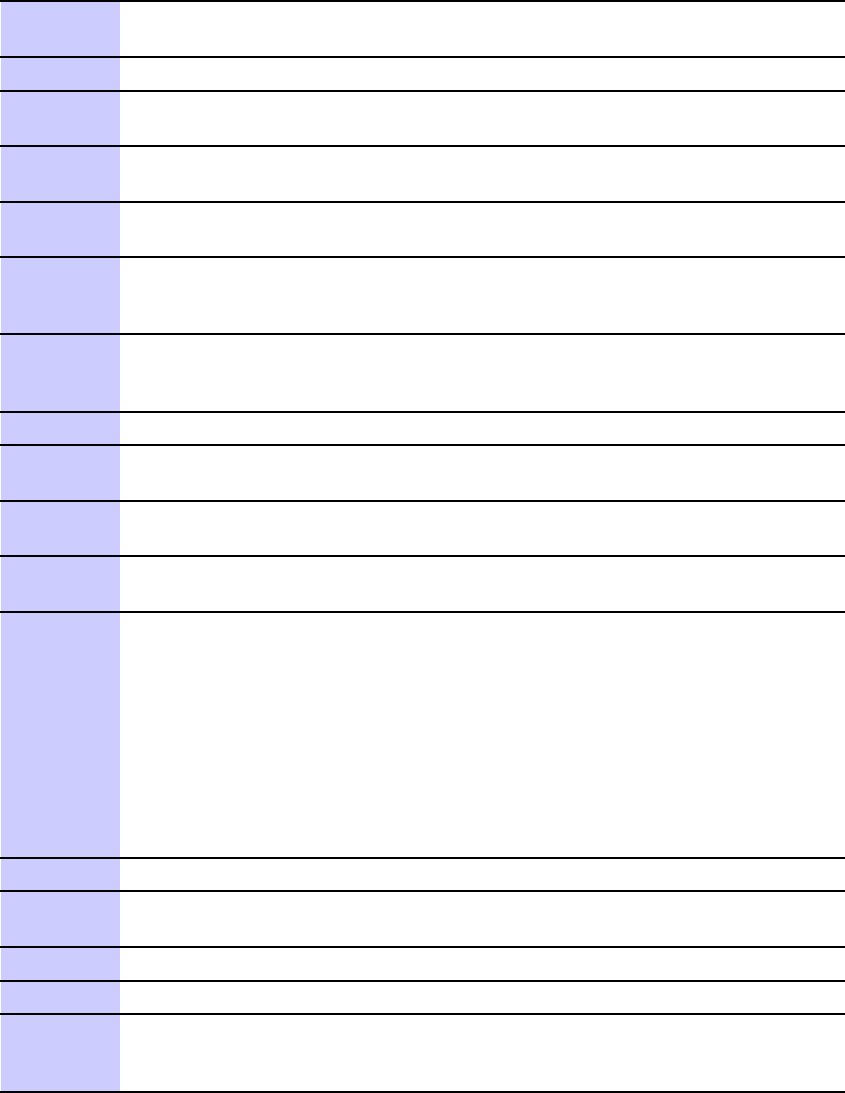
R20 1X UBS Macro B T S Hardw are Installation T ask 14: Connecting +27 V DC P ower
Procedure 2 -8 Procedure for T ask 14 (Continued)
2
Ensure that the +27 V DC P ower Input Cable (DC) is NOT connected to the
main +27 V DC power source. Turn OFF the main +27 V DC power source.
3
Remove the components from the DC connector package.
4
Strip 35 mm of insulation from the negative (- V) and positive (+V) wires of
the power cable.
5
Place a DC contact/lug on the negative (- V) and positive (+V) wires of the
power cable. Refer to Figure 2-21 .
6
Using the appropriate crimping tool, crimp the DC contact/lug on to the
wires.
7
Observe the negative (- V) and positive (+V) wire polarities and insert the
DC contacts/lugs into the DC connector housing until an audible click is
heard. Refer to Figure 2-21 .
8
V erify the positive (+V) wire is installed in the positive position and the
negative (- V) wire is installed in the negative (-) position on the connector
housing.
9
Ensure that the wires are firmly fastened to the DC connector housing.
10
Tie the positive (+V) and negative (- V) wires of the cable together as shown
in Figure 2-20 .
1 1
Route the loose end of the +27 V DC P ower Input Cable (DC) to the site +27
V DC source and connect the wires to the source.
12
V erify that proper polarity is maintained from the +27 V DC power source to
the UBS Macro BTS .
13
Use a Digital Multi-Meter (DMM) to measure the voltage
of the DC connector housing that was installed in step 7 .
P erform the following:
•Set the DMM to measure 27 V DC .
•Connect the DMM negative (GND/common) lead to the (-) terminal of
the cable connector .
•Connect the DMM positive lead to the (+) terminal of the cable
connector .
14
Turn on the main +27 V DC power source.
15
Observe the DMM and verify that the voltage is nominally +27 V (range =
+26 to +28 V).
16
Turn off the main +27 V DC power source.
17
Disconnect the DMM from the cable connector .
18
Connect +27 V DC P ower Input Cable (DC) connector to the +27 V DC
input power cable on the rear of the PDU ; Orange connectors mate. Refer
to Figure 2-21 .
68P09283A62 -3 2 -59
PRELIMINARY A UG 2007
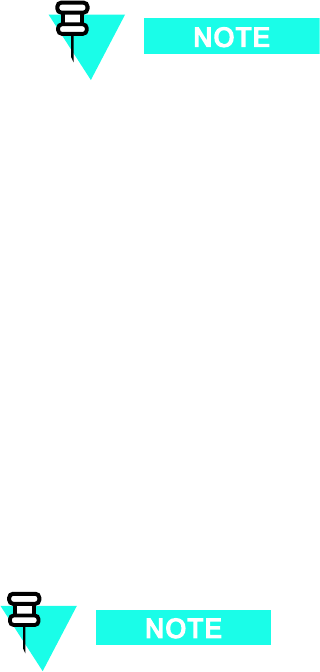
T ask 15: Connecting -48 V DC P ower Chapter 2: UBS Macro B T S Installation Procedure
Task 15: Connecting -48 V DC Power■■■■■■■■■■■■■■■■■■■■■■■■■■■■■■■■■■■■■■■■■■■■■■■■■■■■■■■■■■■■■■
■
■
Objectives
T ask 15 is performed for -48 V DC UBS Macro BTS only .
The objectives of this procedure are as follows:
•A ttaching the contact/lugs and connector on the -48 V DC power input cable wires.
•Connecting the -48 V DC input power cable to the rear of the -48 V DC PSM shelf .
•Routing the loose ends of the wires to the site -48 V DC source for connection to the source.
V erify that the +27 V DC output power cable from the PSM shelf is already
connected to the PDU +27 V DC input power cable. This was performed during
T asks 4 -7.
Frame power cables and connector information
The wire gauge (that is, diameter) depends on the required length of the DC power cable (CC).
Refer to T able 2 -8 for the correct wire size.
The DC connector contact/lug size depends on the wire gauge used for the DC power cable (CC).
Refer to T able 2 -15 for DC connector contact/lug part information.
In order to minimize current imbalance between the feed ( -V) and return (+V) wires used in
the cable:
•Ensure that the wire size, length and gauge, of each wire used in the cable are the same.
•Ensure that contacts/lugs used in the connector are identical and match the gauge of
the wire.
Motorola recommends using 2/0 A WG cables for short cable runs; less than 661.11
cm (21.69 ft).
2 -60 68P09283A62 -3
PRELIMINARY A UG 2007
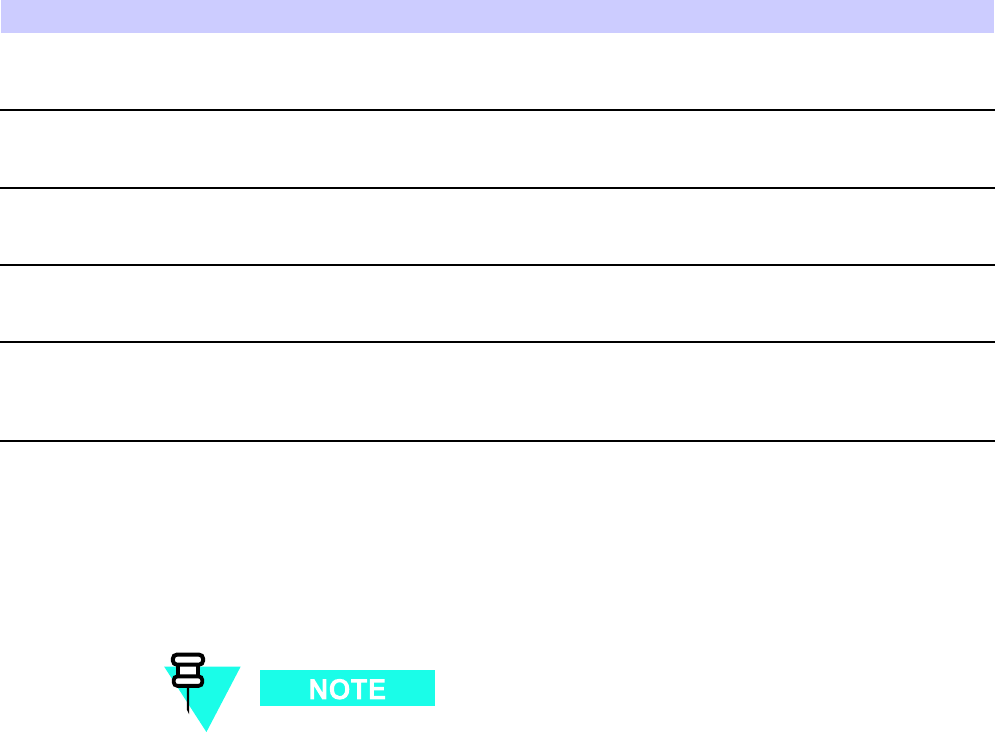
R20 1X UBS Macro B T S Hardw are Installation T ask 15: Connecting -48 V DC P ower
Table 2 -15 –48 V DC connector (Blue) parts information
Item Description Part Number
Qty
Blue DC connector housing Anderson P ower Products Mfr
P art# 912, or Allied Electronics
Stk# 803-0492
1 per –48 V DC power feed
A WG 2/0 connector contact/lug Anderson P ower Products Mfr
P art# 907, or Allied Electronics
Stk# 803-0500
2 per DC connector housing
A WG 3/0 connector contact/lug Anderson P ower Products Mfr
P art# 916, or Allied Electronics
Stk# 803-0502
2 per DC connector housing
A WG 4/0 connector contact/lug Anderson P ower Products Mfr
P art# 908, or Allied Electronics
Stk# 803-0504
2 per DC connector housing
Cable clamp for two single
conductors with hardware
Anderson P ower Products Mfr
P art# 996G1
1 per –48 V DC power feed
Required items
The following items are required:
•One -48 V DC P ower Input Cable (CC) - customer supplied. The wire size, length and
gauge, used for cable (CC) depends on site characteristics (see T able 2 -8 ).
Motorola recommends the use of blue wire for feed ( -V) and black wire for
return (+V).
•T wo Contacts/Lugs – customer supplied. Contact/lug fastens to wire end and is inserted
into DC connector housing. F or contact/lug part number (refer to T able 2 -15 ). Contact/lug
size must match the gage of the wire being used.
•One DC Connector Housing – supplied with UBS BTS . Use Anderson SB350 connector
housing (blue color) or equivalent.
•Crimper tool - Anderson P ower Products part number 1368 - Hydraulic hand tool,
maximum cable size of 300 MCM
•W ire stripper/cutters.
•Digital Multi -Meter (DMM) Fluke Model 8062A with Y8134 test lead kit or equivalent; used
for precision DC and AC measurements, requiring 4 -1/2 digits.
68P09283A62 -3 2 -61
PRELIMINARY A UG 2007
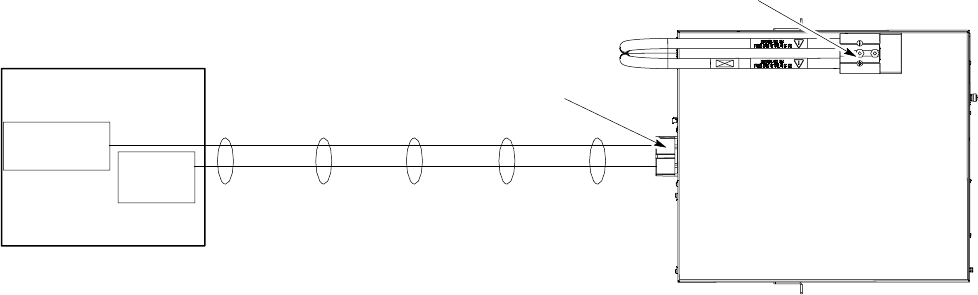
T ask 15: Connecting -48 V DC P ower Chapter 2: UBS Macro B T S Installation Procedure
Power cabling and tie down requirements
T o control the inductance at the BTS DC power input due to the spacing between wires used
in the -48 V DC P ower Input Cable (CC), the feed ( -V) and return (+V) wires must be bound
together at intervals of 1 meter or less. Refer to Figure 2 -22 .
Figure 2 -22 48 V DC power input cable (CC) wire tie -wr ap example
ti-cdma-05695.eps
TIE ALL CABLES AT 1 METER INTERVALS
-48 V Power Source
BREAKER 1
-48 V DC -48 V DC PSM SHELF
(Top View)
-48 V DC Power Input
Connector (BLUE)
+27 V DC Power Output Connector (ORANGE)
+0 V DC
+0 V DC
REAR
FRONT
-48 V DC
Contact/lug, DC connector housing and PDU input power
Figure 2 -23 shows the lugs and DC connector housing. This figure also shows the location at
which the -48 V DC Input P ower Cable (CC) connects to the rear of the PDU .
2 -62 68P09283A62 -3
PRELIMINARY A UG 2007
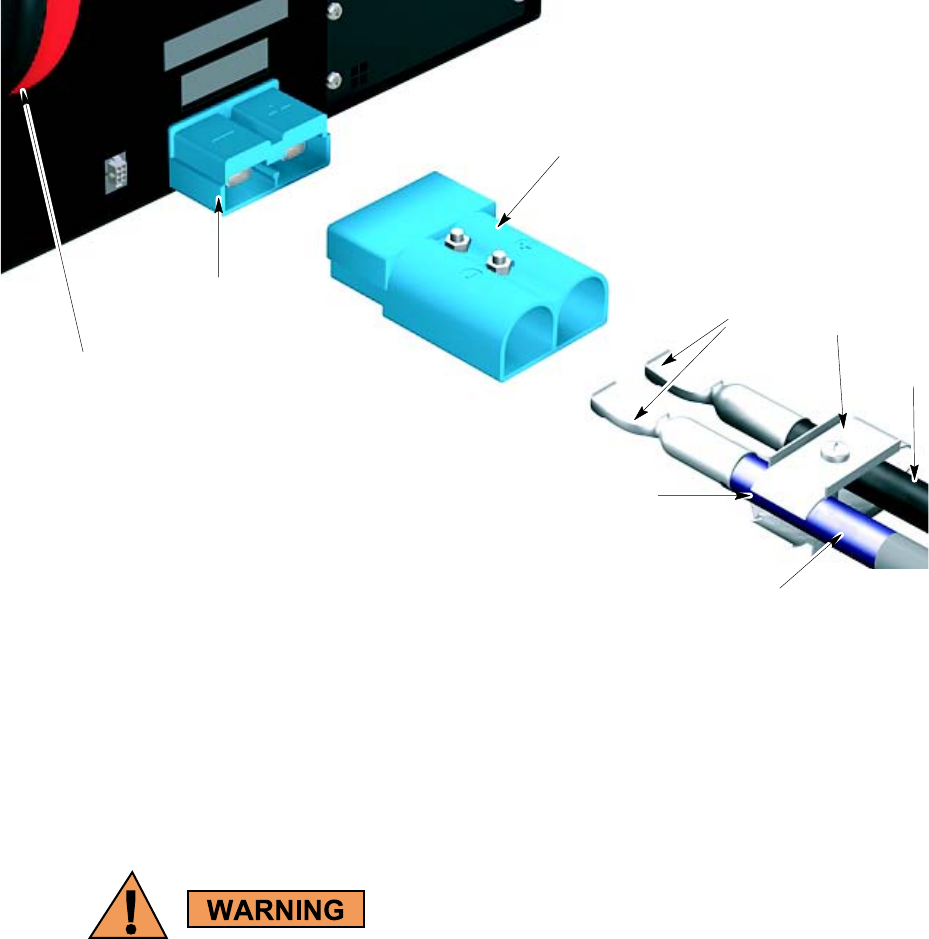
R20 1X UBS Macro B T S Hardw are Installation T ask 15: Connecting -48 V DC P ower
Figure 2 -23 48 V DC power input cable (CC) connector and connection to PSM shelf
ti-cdma-05696.eps
-48 VDC PSM SHELF
(rear view, shown partially cut away)
Connector
Housing (Blue)
(+)
(-)
(-)
???
Crimp-on
Contact/Lugs
-48 VDC Power
Input (Blue)
(+)
2-Wire -48 VDC
Power Cable
(Customer Supplied)
BLACK Wire
(Typical)
BLUE Wire
(Typical)
+27 VDC Power
Output Cable (To PDU)
Cable Clamp
Procedure
P erforming T ask 15 as given in Procedure 2 -9 .
•Do not wear a wrist str ap when servicing the power supplies or power distribution
cabling.
•Ensure that the source for the DC power is in the OFF position.
•Ensure that all of the PDU circuit break ers are OFF .
68P09283A62 -3 2 -63
PRELIMINARY A UG 2007
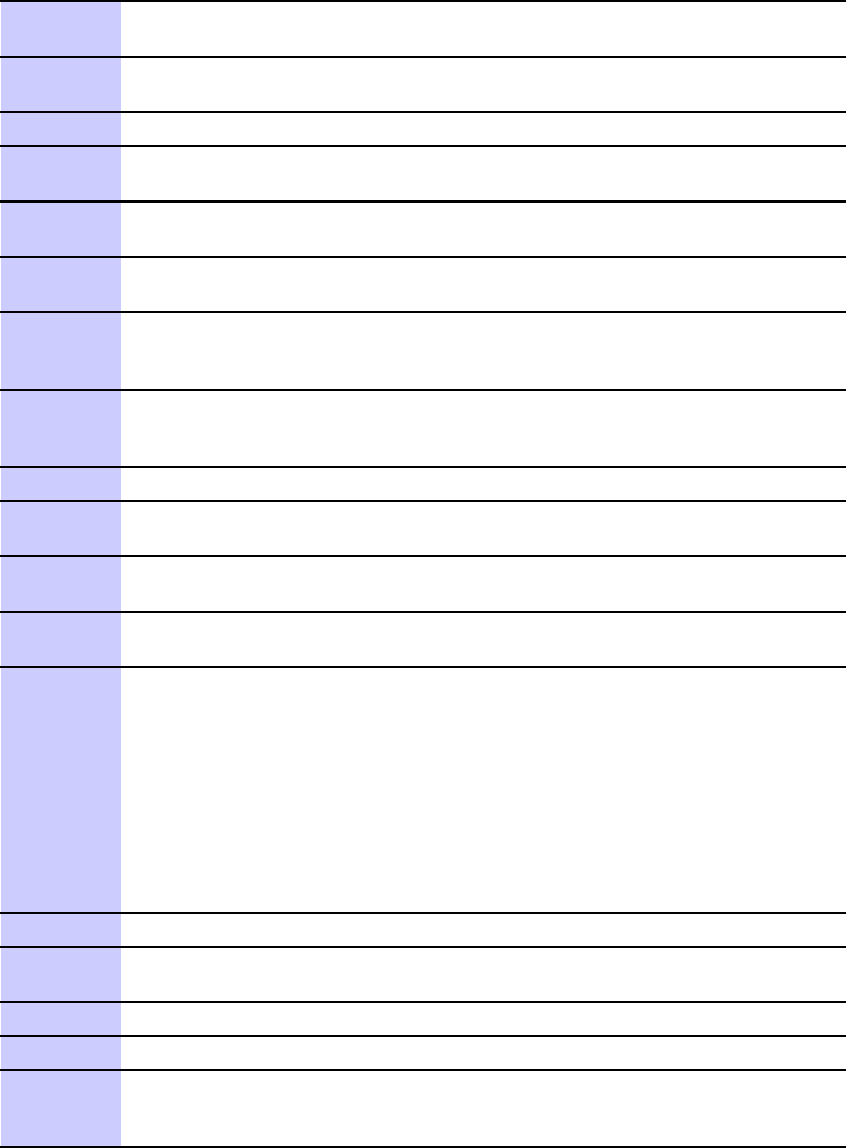
T ask 15: Connecting -48 V DC P ower Chapter 2: UBS Macro B T S Installation Procedure
Procedure 2 -9 Procedure for T ask 15
1
Ensure that the BTS ground cable (DD) is connected between the rack and
the Master Ground Bar (refer to T ask 3).
2
Ensure that the -48 V DC P ower Input Cable (CC) is NOT connected to the
main -48 V DC power source. Turn OFF the main -48 V DC power source.
3
Remove the components from the DC connector package.
4
Strip 35 mm of insulation from the negative (- V) and positive (+V) wires of
the power cable.
5
Place a DC contact/lug on the negative (- V) and positive (+V) wires of the
power cable. Refer to Figure 2-23 .
6
Using the appropriate crimping tool, crimp the DC contact/lug on to the
wires.
7
Observe the negative (- V) and positive (+V) wire polarities and insert the
DC contacts/lugs into the DC connector housing until a click sound is heard.
Refer to Figure 2-23 .
8
V erify the positive (+V) wire is installed in the positive position and the
negative (- V) wire is installed in the negative (-) position on the connector
housing.
9
Ensure that the wires are firmly fastened to the DC connector housing.
10
Tie the positive (+V) and negative (- V) wires of the cable together as shown
in Figure 2-22 .
1 1
Route the loose end of the -48 V DC P ower Input Cable (CC) to the site -48 V
DC source and connect the wires to the source.
12
V erify that proper polarity is maintained from the -48 V DC power source to
the UBS Macro BTS .
13
Use a Digital Multi-Meter (DMM) to measure the voltage
of the DC connector housing that was installed in step 7 .
P erform the following:
•Set the DMM to measure 48 V DC .
•Connect the DMM negative (GND/common) lead to the (-) terminal of
the cable connector .
•Connect the DMM positive lead to the (+) terminal of the cable
connector .
14
Turn on the main –48 V DC power source.
15
Observe the DMM and verify that the voltage is nominally +48 V (range =
+40 to +60 V).
16
Turn off the main –48 V DC power source.
17
Disconnect the DMM from the cable connector .
18
Connect -48 V DC P ower Input Cable (CC) connector to the -48 V DC input
power connector on the rear of the PSM shelf; blue connectors mate. Refer
to Figure 2-23 .
2 -64 68P09283A62 -3
PRELIMINARY A UG 2007
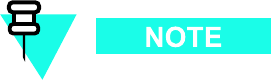
R20 1X UBS Macro B T S Hardw are Installation T ask 16: Connecting 220 V AC P ower
Task 16: Connecting 220 V AC Power■■■■■■■■■■■■■■■■■■■■■■■■■■■■■■■■■■■■■■■■■■■■■■■■■■■■■■■■■■■■■■
■
■
Objectives
T ask 16 is performed for 220 V AC UBS Macro BTS only .
The objectives of this procedure are as follows:
•A ttaching customer supplied wiring and conduit for 220 V AC lines.
•Connecting wires and required insertion bridges to the AC INP UT terminal block on the
rear of the AC PSM shelf .
•Routing the loose ends of the wires to the site 220 V AC source for connection to the source.
V erify that the +27 V DC output power cable from the PSM shelf is already
connected to the PDU +27 V DC input power cable. This was performed during
T asks 4 -7.
Frame AC power cables and wiring information
The AC PSM shelf and AC PSMs can operate with the following AC power inputs:
•Input AC V oltage R ange: 154 V AC to 300 V AC
•Single -Phase
•3 -Phase ST AR
•3 -Phase DEL T A
Consider the following AC power input circuit characteristics:
•The AC PSM shelf terminal block has seven terminals; one for Ground plus six for AC
line wires and insertion bridges.
•The AC PSM shelf terminal block Ground terminal can accommodate a wire size range of
2 A WG to 10 A WG .
•The AC PSM shelf terminal block AC line terminals can accommodate a wire size range of
2 A WG to 10 A WG .
68P09283A62 -3 2 -65
PRELIMINARY A UG 2007
T ask 16: Connecting 220 V AC P ower Chapter 2: UBS Macro B T S Installation Procedure
•Input AC cable sizing should be determined by Local Electrical Codes, using 90 C minimum
rated conductors, and de–rating for 50 C operation.
•The customer must provide a disconnect device and an over current protection device for
the AC circuit supplying the UBS Macro BTS . A circuit breaker size of 30 Amperes is
recommended, or as appropriate set by Local Electrical Code.
Required items
The following items are required:
•Conduit - customer supplied
•W ire for Ground and AC lines - customer supplied
•Insertion bridges – supplied with AC PSM shelf; two 3 -position bridges and three 2 -position
bridges
•T20 TORX bit with 12 -inch extension
•Flat blade screwdriver
•W ire stripper/cutters
AC PSM shelf AC power input detail
Figure 2 -24 shows the location of the AC PSM shelf AC power input terminals and wiring
details for:
•Single -Phase
•3 -Phase ST AR
•3 -Phase DEL T A
2 -66 68P09283A62 -3
PRELIMINARY A UG 2007
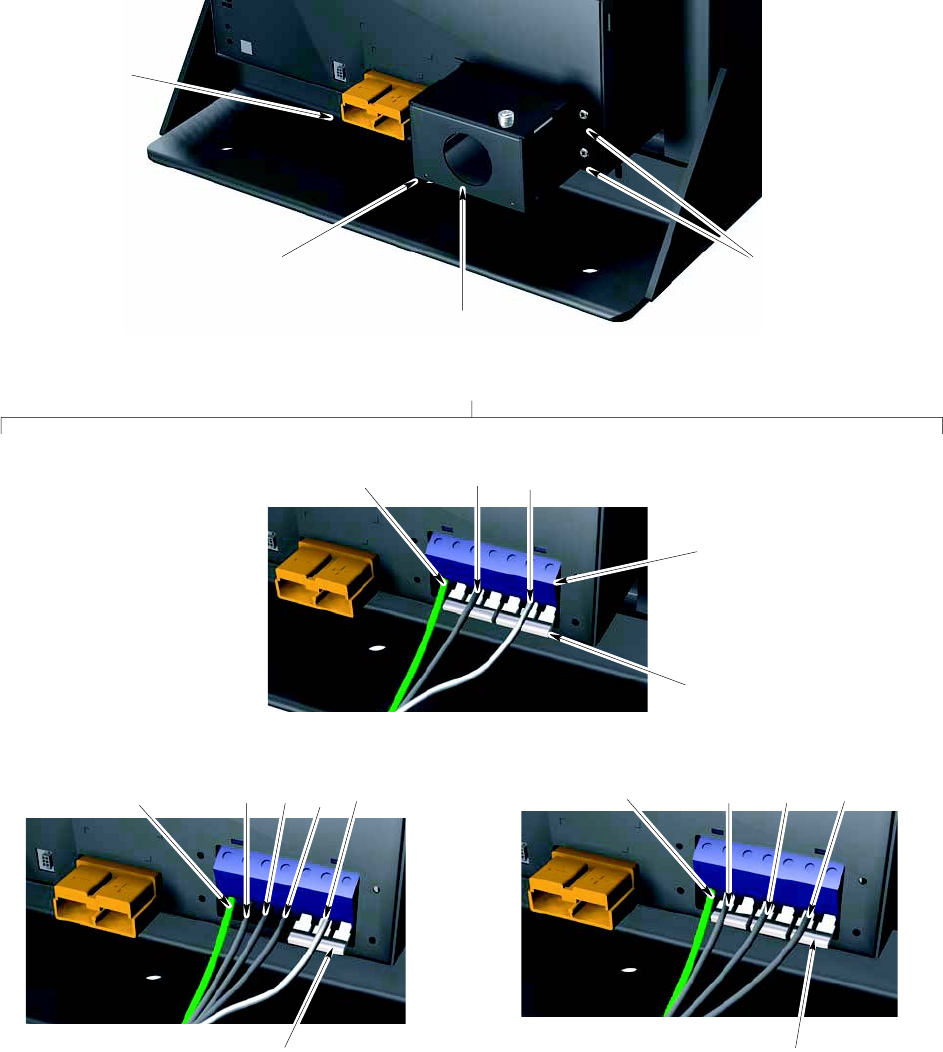
R20 1X UBS Macro B T S Hardw are Installation T ask 16: Connecting 220 V AC P ower
Figure 2 -24 AC PSM shelf AC power input terminal block and wiring details
ti-cdma-05697.eps
AC PSM Shelf
(rack mounted, rear view, shown partially cut away)
+27 VDC Power
Output Connector
for Battery Backup
AC Input Terminal Block Protective
Cover Box
(See Detail A for Wiring Configurations)
Conduit/Wire
Entry Hole
2 Screws On Each Side
Secure Protective Cover
Box To PSM Shelf
Detail A - AC Input Terminal Wiring Configurations (protective cover box removed)
Single-Phase
Ground
GroundGround
AC Input Terminal Block
(terminal screw access
holes on top)
Two 3-position
Insertion Bridges
One 3-position
Insertion Bridge
Three 2-position
Insertion Bridges
3-Phase STAR3-Phase DELTA
L3 L2 L1 NL3 L1 L2
L1 N
68P09283A62 -3 2 -67
PRELIMINARY A UG 2007
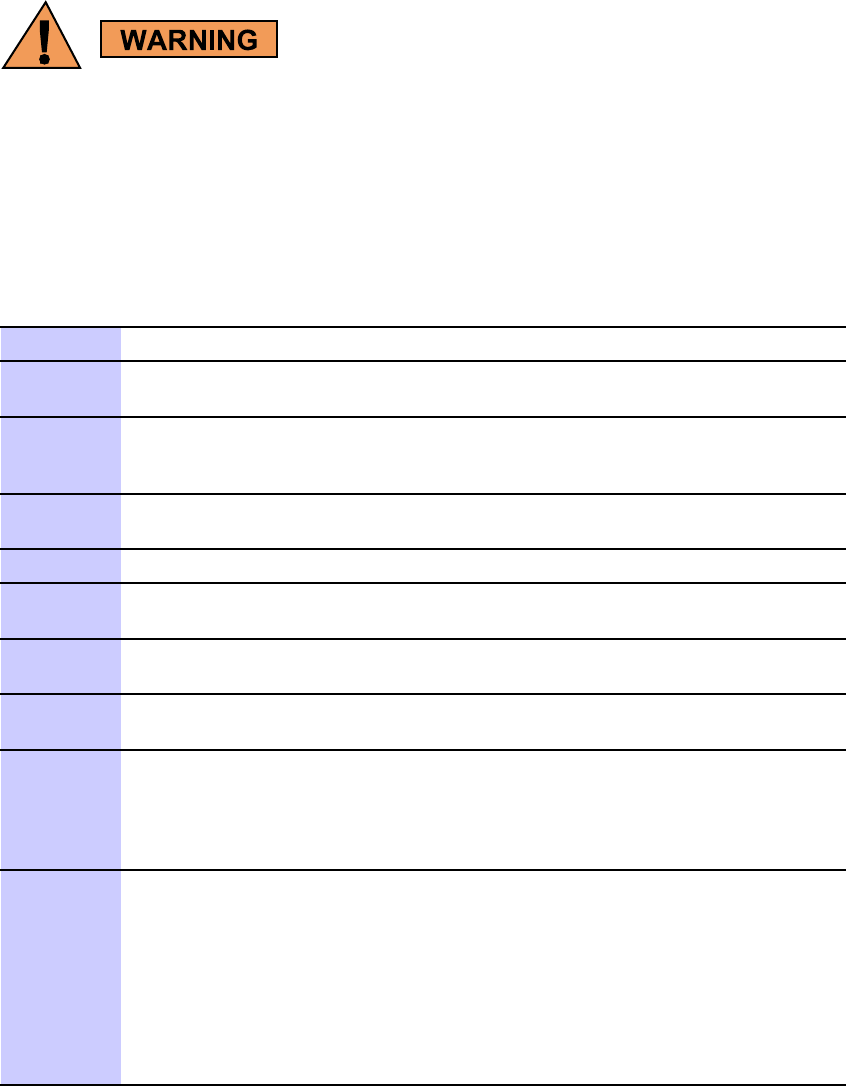
T ask 16: Connecting 220 V AC P ower Chapter 2: UBS Macro B T S Installation Procedure
Procedure
P erform T ask 16 as given in Procedure 2 -10 .
•Do not wear a wrist str ap while servicing the power supplies or power distribution
cabling.
•Ensure that the source for the AC power is in the OFF position.
•Ensure that all of the PDU circuit break ers are OFF .
Procedure 2 -10 Procedure for T ask 16
1
Set the source for the AC voltage to the OFF position.
2
Ensure that the BTS ground cable (DD) is connected between the rack and
the Master Ground Bar (refer to T ask 3).
3
On the rear of the PSM shelf , locate the AC input terminal block cover box.
Using a TORX T20 bit and driver , remove the 4 screws securing the cover
box to the PSM shelf (refer to Figure 2-24 ).
4
Remove the cover box from the PSM shelf to expose the AC input terminal
block.
5
A ttach conduit to the cover box.
6
Route the AC wires and the earth ground wire through the conduit and the
cover box. Leave wires extending to reach the AC input terminal block.
7
Strip 25 mm of insulation from each of the AC supply line wires and the
earth ground wire.
8
Locate the ground terminal on the AC input terminal block (refer to
Figure 2-23 ).
9
Using a flat blade screwdriver , turn the ground terminal screw counter
clockwise (CCW) until the terminal is fully open. Insert the earth ground
wire into the ground terminal. Turn the ground terminal screw clockwise
(CW) to close the terminal and secure the wire. Tighten the terminal screw
to 4.0 - 4.5 N-m (35 - 40 in-lb).
10
Determine if the AC input terminal block already has insertion bridges
properly installed for the desired AC supply configuration:
•Single-Phase
•3-Phase ST AR
•3-Phase DEL T A
Refer to Figure 2-24 as needed.
Continued
2 -68 68P09283A62 -3
PRELIMINARY A UG 2007
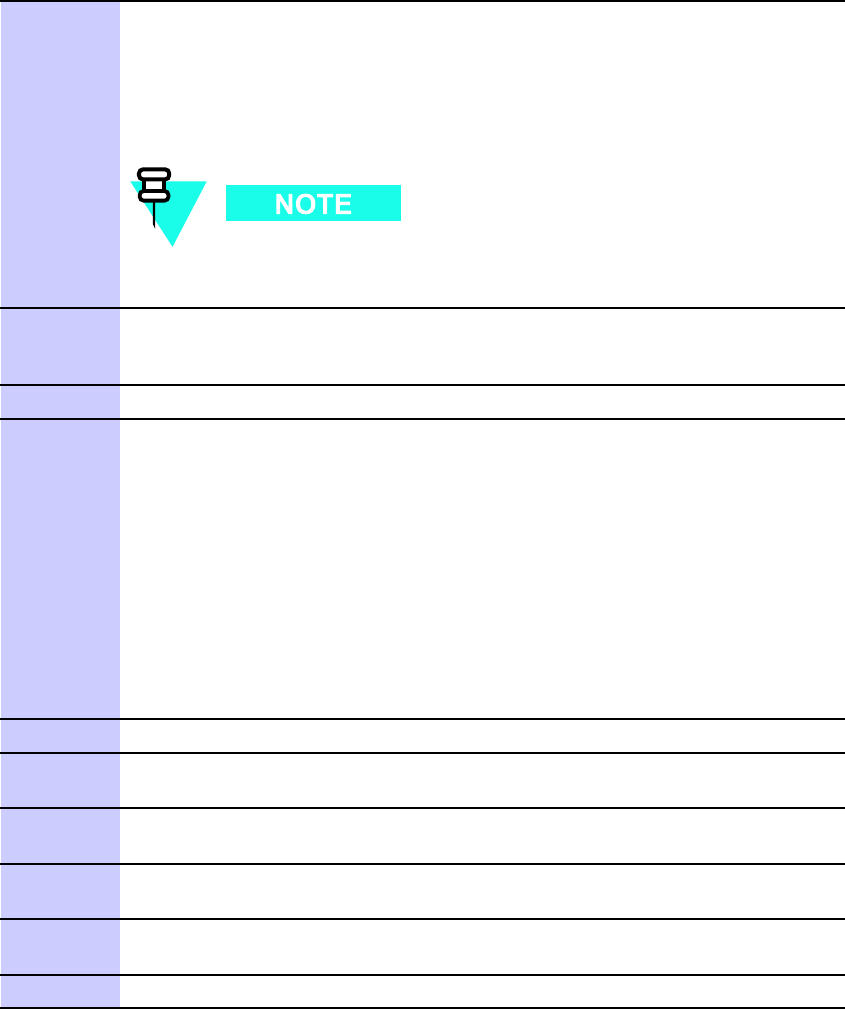
R20 1X UBS Macro B T S Hardw are Installation T ask 16: Connecting 220 V AC P ower
Procedure 2 -10 Procedure for T ask 16 (Continued)
1 1
Open the six line terminals as follows:
•Insert a flat blade screwdriver into each screw hole on top of the
terminal block.
•Turn the terminal screw CCW until the terminal is fully open..
F ailure to fully open the terminals can cause improper placement
of the insertion bridges in later steps.
12
Place an insertion bridge into the proper terminals. While holding the
bridge with one hand, turn the corresponding terminal screws CW until the
bridge is securely clamped.
13
Repeat step 12 for any remaining terminals requiring an insertion bridge.
14
Connect the AC supply line wires to the proper terminals as follows:
•Insert a flat blade screwdriver into the appropriate screw hole on top
of the terminal block.
•Turn the terminal screw CCW until the terminal is fully open.
•Insert the appropriate wire into the terminal.
•While holding the wire with one hand, turn the corresponding terminal
screw CW until the wire is securely clamped. Tighten the terminal
screw to 4.0 - 4.5 N-m (35 - 40 in-lb).
Refer to Figure 2-24 as needed.
15
Repeat step 14 for any unconnected AC supply line wires.
16
V isually inspect all insertion bridge(s) and wires for proper placement. All
conductors must be inside the clamp of each terminal block.
17
Place the cover box, with conduit attached, in position over the AC input
terminal block.
18
Insert the 4 screws to secure the cover box to the PSM shelf . Ensure that
the wires are not pinched.
19
Using a TORX T20 bit and driver , tighten the 4 screws to 1.6 - 1.8 N-m (14 -
16 in-lb).
20
Complete the installation of the AC wiring at the AC P ower source.
68P09283A62 -3 2 -69
A UG 2007 PRELIMINARY
T ask 16: Connecting 220 V AC P ower Chapter 2: UBS Macro B T S Installation Procedure
2 -70 68P09283A62 -3
PRELIMINARY A UG 2007
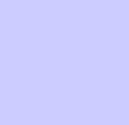
C h a p t e r
3
Low -to -Mid Capacity Frame Expansion
Procedures
■■■■■■■■■■■■■■■■■■■■■■■■■■■■■■■■■■■■■■■■■■■■■■■■■■■■■■■■■■■■■■
■
■
■
■
68P09283A62 -3 3 -1
A UG 2007 PRELIMINARY
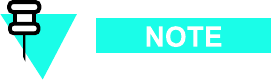
Low -to -Mid Capacit y Fr ame Expansion Ov erview Chapter 3: Low -to -Mid Capacit y Fr ame Expansion Procedures
Low -to -Mid Capacity Frame Expansion Overview■■■■■■■■■■■■■■■■■■■■■■■■■■■■■■■■■■■■■■■■■■■■■■■■■■■■■■■■■■■■■■
■
■
The R20 UBS Macro BTS supports single band 800 MHz or 1.9 GHz RF band, up to
two XMIs, up to two DMIs and one S SI. UBS Macro BTS Frame configurations with
up to four XMIs and up to five DMIs will be available in the future.
This chapter provides information and procedures needed for expanding the low -capacity UBS
Macro BTS starter/expansion frame to the mid -capacity frame configuration.
The mid -capacity frame consists of the low -capacity frame equipment plus the following
additional expansion equipment:
•second XMI, required.
•second DMI, required.
•circuit breaker/output power connector assemblies; one required for each of the following:
second XMI and second DMI.
•second set of IDRFs, required.
•optional RX splitter or RX share cable.
•third PSM, required for –48 V or 220 V AC only . Three PSMs are required for the mid
capacity configuration. The third PSM is for redundancy .
Cabling of the RX splitter to the XMIs will be performed after all of the additional expansion
equipment (i.e., XMI, DMI, S SI, circuit breaker/output power connector assemblies, etc.) is
installed in the frame.
How to use this chapter
Typically the installer is directed to this chapter via T ask 6: Expanding the Low -capacity Frame
on page 2 - 42 of Chapter 2 UBS Macro BTS Installation Procedure .
P erform all of the applicable procedures, in this chapter , for expanding the low -capacity UBS
Macro BTS starter/expansion frame to the mid -capacity frame configuration.
A fter all of the additional expansion equipment is installed, go to T ask 7: Cabling the Optional
PSM Shelf on page 2 - 43 of Chapter 2 UBS Macro BTS Installation Procedure , and continue
performing the remaining tasks in sequential order .
3 -2 68P09283A62 -3
PRELIMINARY A UG 2007

R20 1X UBS Macro B T S Hardw are Installation Adding Circuit Break ers/Connectors to PDU
Adding Circuit Breakers/Connectors to PDU■■■■■■■■■■■■■■■■■■■■■■■■■■■■■■■■■■■■■■■■■■■■■■■■■■■■■■■■■■■■■■
■
■
Objective
The objective of this section is to install additional circuit breaker/output power connector
assemblies in the PDU . These additional circuit breaker/output power connector assemblies are
required to allow the PDU to provide DC power to the expansion equipment being added to
the UBS Macro BTS frame.
The circuit breaker/output power connector assemblies are located on the PDU front panel.
Each circuit breaker/output power connector assembly is arranged so that the circuit breaker
is just below the corresponding DC output power connector .
The PDU can be equipped with the following circuit breaker/output power connector assemblies:
•up to four 90A for XMI 1 – XMI 4
•up to five 20A for DMI 1 – DMI 5
•up to two 20A for S SI 1 – S SI 2
•up to two 10A for accessory groups ACC 1 – ACC 2
The PDU in the UBS Macro BTS low -capacity starter/expansion frame is already equipped with
the following circuit breaker/output power connector assemblies:
•one 90A for XMI 1
•two 20A for DMI 1 – DMI 2
•one 20A for S SI 1
•zero 10A for no accessories
The type and quantity of circuit breaker/output power connector assemblies required depends
on which circuit breaker/output power connector assemblies are not already equipped in the
PDU , but are needed to support the additional expansion equipment.
Required items
The following items are required:
•Appropriate type and quantity of circuit breaker/output power connector assemblies to
be added for expansion purposes
90A circuit breaker/output power connector assembly (Motorola model STLN4093)
20A circuit breaker/output power connector assembly (Motorola model STLN6472)
68P09283A62 -3 3 -3
PRELIMINARY A UG 2007
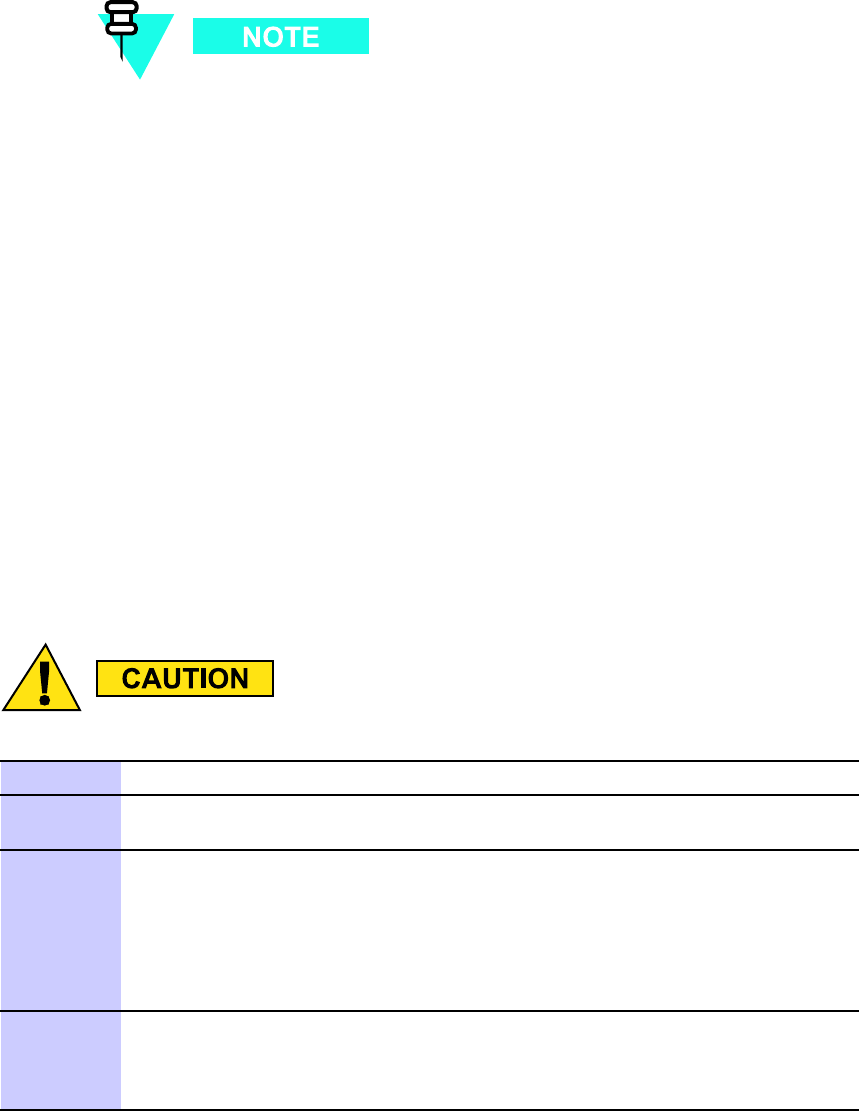
Adding Circuit Break ers/Connectors to PDU Chapter 3: Low -to -Mid Capacit y Fr ame Expansion Procedures
Mounting screws are provided with each circuit breaker/output power
connector assembly; four screws with the 90A assembly and two screws
with the 20A assembly .
•Side cutters; diagonal pliers or wire cutter
•Small knife
•TORX T25 bit and driver
•T orque driver
Procedure
Procedure 3 -1 contains the steps for adding a circuit breaker/output power connector assembly
to the PDU .
Procedure 3 -1 Adding a Circuit Break er/Output P ower Connector Assembly to the
PDU
Mak e sure DC input power is not applied to the PDU before performing Procedure 3 -1 .
1
Set all PDU front panel circuit breakers to the off (pulled out) position.
2
Disconnect all DC power cables from the PDU front panel. Dress these cables
away from the PDU front panel.
3
Remove the PDU front panel as follows:
•See Figure 3-1 Adding a Breaker Assembly Module to the PDU on page
3- 6 photograph A.
•While depressing the retaining tab on the left and right front ends of the
PDU , slide the PDU front panel forward and off of the PDU .
4
Install the additional circuit breaker/output power connector assemblies in
the required locations on the PDU front panel DC output power bus (see
Figure 3-1 Adding a Breaker Assembly Module to the PDU on page 3- 6
photograph B.
Continued
3 -4 68P09283A62 -3
PRELIMINARY A UG 2007
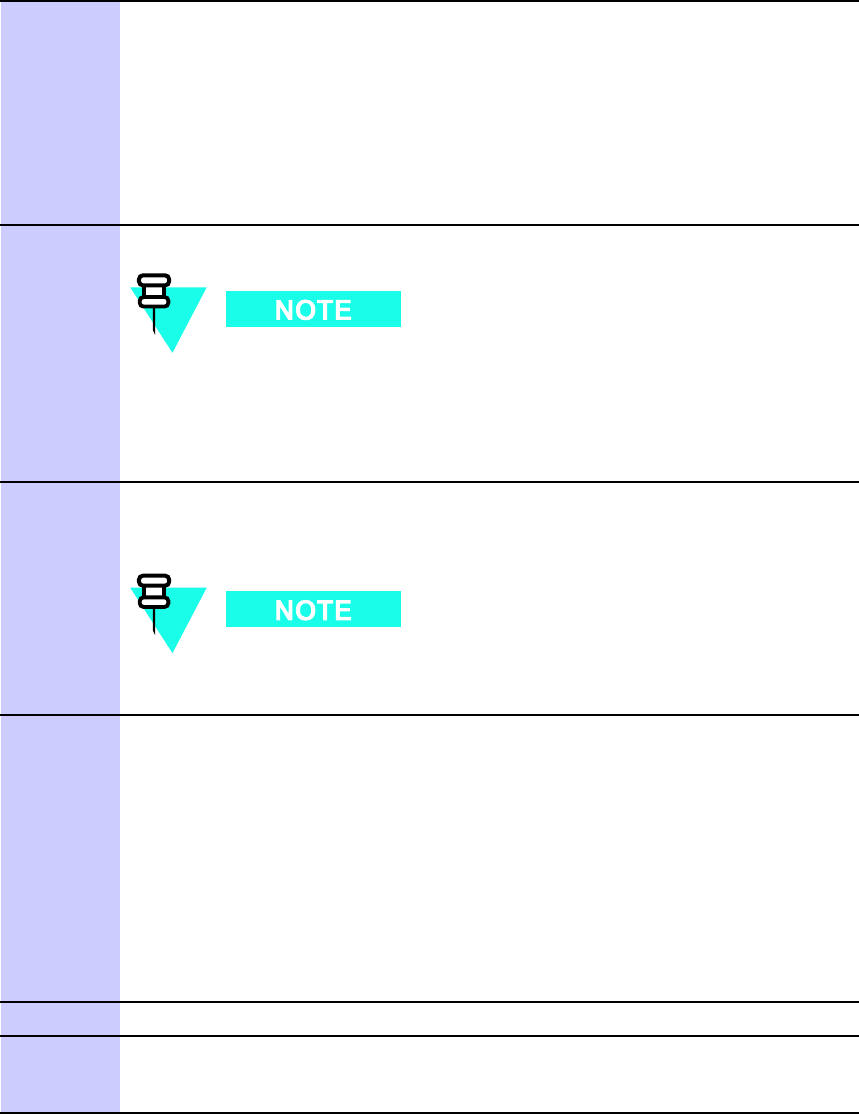
R20 1X UBS Macro B T S Hardw are Installation Adding Circuit Break ers/Connectors to PDU
Procedure 3 -1 Adding a Circuit Break er/Output P ower Connector Assembly to the
PDU (Continued)
5
P osition the circuit breaker/output power connector assembly as follows:
•Circuit breaker actuator at the bottom and the DC output power
connector at the top
•Circuit breaker actuator facing toward the front of the frame
•Align mounting screw holes of the circuit breaker/output power
connector assembly with the corresponding screw holes on the PDU
front panel DC output power bus.
6
Insert the supplied mounting screws into the screw holes.
T wo screws on top and bottom for the 90A assembly . One screw on
top and bottom for the 20A assembly .
Using a TORX T25 driver , tighten the mounting screws to 4.8 N-m (42.25
in-lb) ±10%.
7
Using side cutters, cut out the applicable circuit breaker actuator and the
corresponding connector covers on the PDU front panel (see Figure 3-1
Adding a Breaker Assembly Module to the PDU on page 3- 6 photograph C.
It may be necessary to use a small knife to remove any of the tabs
that do not cut cleanly .
8
Reattach the PDU front panel to the PDU as follows:
•See Figure 3-1 Adding a Breaker Assembly Module to the PDU on page
3- 6 photograph D.
•Align the PDU front panel with the PDU circuit breaker actuators and
power connectors while inserting the PDU front panel retaining tabs into
the retainer on the left and right front ends of the PDU .
•Slide the PDU front panel onto the front of the PDU .
•Firmly press on the ends of the PDU front panel until each end tab snaps
into place.
9
Set all PDU front panel circuit breakers to the off (pulled out) position.
10
Reconnect all DC power cables that were disconnected in step 2 of this
procedure. Make sure that each cable is connected to the proper PDU front
panel power connector .
68P09283A62 -3 3 -5
PRELIMINARY A UG 2007
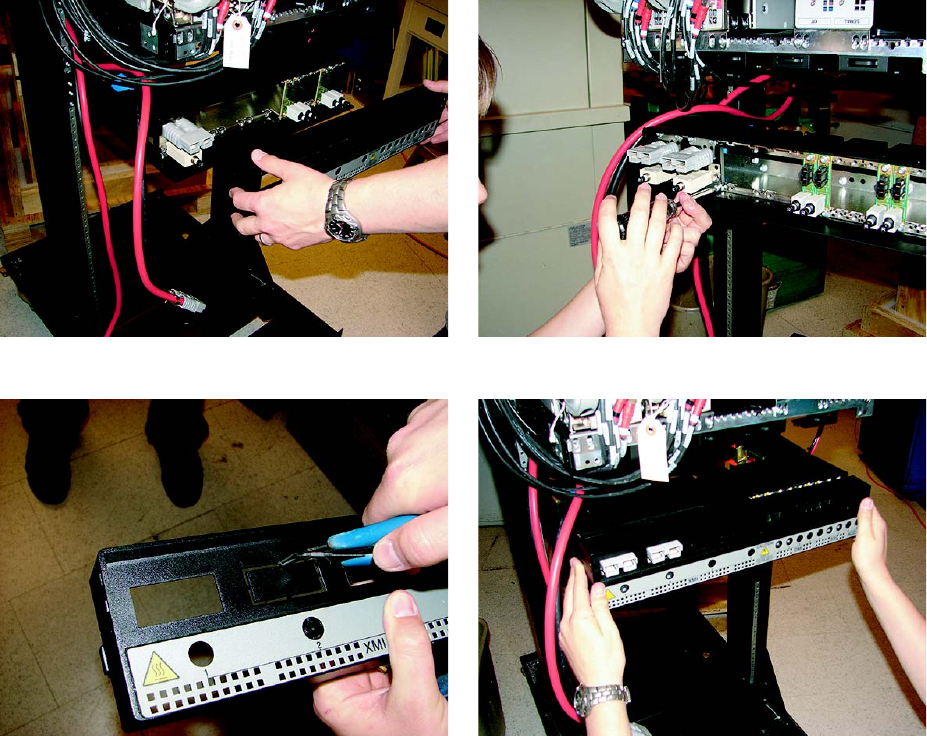
Adding Circuit Break ers/Connectors to PDU Chapter 3: Low -to -Mid Capacit y Fr ame Expansion Procedures
Procedural reference diagram
The following diagram helps clarify certain steps in Procedure 3 -1 .
Figure 3 -1 Adding a Break er Assembly Module to the PDU
ti-cdma-06031.eps
A B
C D
3 -6 68P09283A62 -3
PRELIMINARY A UG 2007
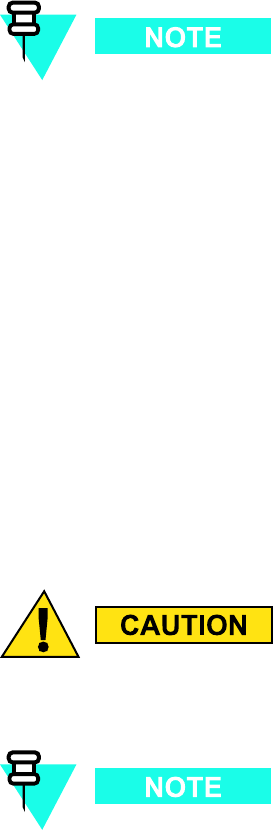
R20 1X UBS Macro B T S Hardw are Installation Adding an XMI
Adding an XMI■■■■■■■■■■■■■■■■■■■■■■■■■■■■■■■■■■■■■■■■■■■■■■■■■■■■■■■■■■■■■■
■
■
Objective
The objective of this section is to mount an additional XMI into the XMI shelf .
Cabling of the additional XMI will be performed after all of the additional expansion
equipment (i.e., IDRFs, DMI, circuit breaker/output power connector assemblies, etc.)
that connects to the additional XMI is installed in the frame.
Required items
Parts
The following applicable additional XMI is required:
•800 MHz XMI assembly with removable XMI handle attached (Motorola model SGTF4194).
•1.9 GHz XMI assembly with removable XMI handle attached (Motorola model STWG4000).
Manpower
The XMI module is hea vy . T wo people are required to lift, carry , or handle the XMI
module.
The XMI weighs 23 -28 kg (50.7 -61.7 lb) depending on the RF band.
68P09283A62 -3 3 -7
PRELIMINARY A UG 2007
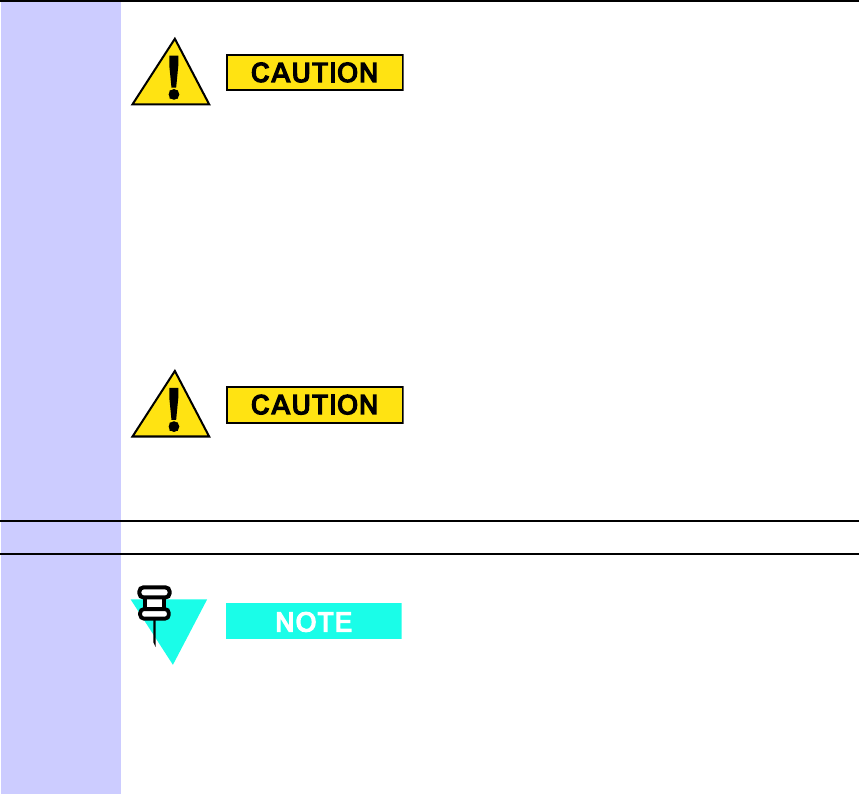
Adding an XMI Chapter 3: Low -to -Mid Capacit y Fr ame Expansion Procedures
Tools
The following tools are required:
•TORX T25 bit and driver
•T orque driver
Procedure
Procedure 3 -2 contains the steps for adding a 2nd XMI to the XMI shelf .
Procedure 3 -2 Adding a 2nd XMI to the XMI Shelf
The XMI module is hea vy . T wo people are required to lift, carry , or
handle the XMI module.
•Be sure the remo v able XMI handle is attached to the front of
the XMI before ph ysically handling the module.
•Be sure two people use both hands and wear protectiv e
footwear when handling the XMI.
•Be sure to use two people to support the module while sliding
the module out of or into the shelf slot.
An XMI module that is not in a shelf should alw a ys be set on its
side and nev er on its edge. This will prev ent the XMI module from
tipping o v er and causing damage or injury .
1
Remove the XMI from its packaging and inspect it for damage.
2
XMI 2 mounts in the XMI shelf slot just to the right of XMI 1. XMI
3 mounts in the XMI shelf slot just to the right of XMI 2. XMI 4
mounts in the XMI shelf slot just to the right of XMI 3.
This step requires two people. P erform the following:
Continued
3 -8 68P09283A62 -3
PRELIMINARY A UG 2007
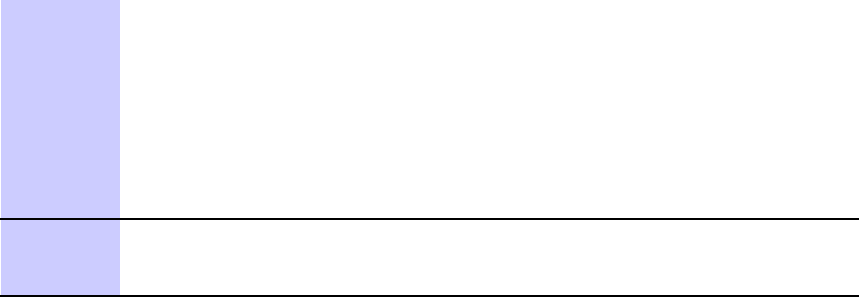
R20 1X UBS Macro B T S Hardw are Installation Adding an XMI
Procedure 3 -2 Adding a 2nd XMI to the XMI Shelf (Continued)
•One person grasp the XMI by the handle with both hands. The second
person grasp the XMI fan tray sides with both hands. Using safe lifting
technique (i.e. lift with your legs not your back), pick up the XMI and
carry it over to the front of the frame.
•While one person holds the XMI by the handle with both hands, the
second person supports the bottom of the module with one hand and the
top of the module with the other hand. Lift the XMI into the appropriate
XMI shelf slot rails and gently slide it all of the way into the shelf slot.
3
Insert the four XMI mounting screws; two screws at each of the top and
bottom mounting tabs on the front of the module. Using a T25 TORX driver ,
tighten the screws to 4.8 N-m (42.25 in-lb) ±10%.
Procedural reference diagram
The following diagram helps clarify certain steps in Procedure 3 -2 .
68P09283A62 -3 3 -9
PRELIMINARY A UG 2007
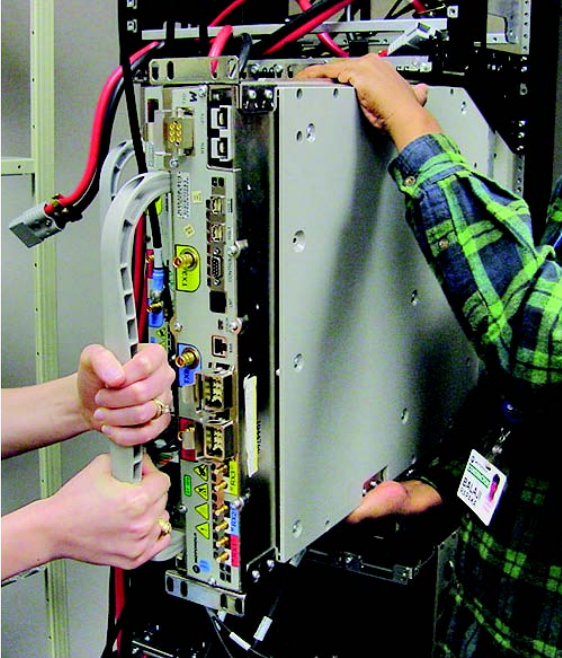
Adding an XMI Chapter 3: Low -to -Mid Capacit y Fr ame Expansion Procedures
Figure 3 -2 Installing a 2nd XMI
ti-cdma-06375.eps
3 -10 68P09283A62 -3
PRELIMINARY A UG 2007
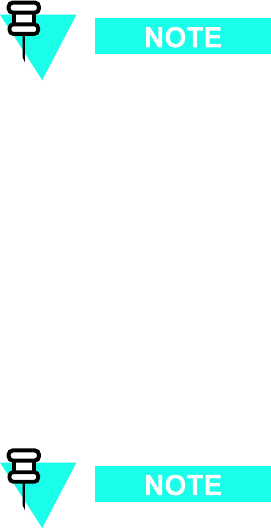
R20 1X UBS Macro B T S Hardw are Installation Adding a DMI
Adding a DMI■■■■■■■■■■■■■■■■■■■■■■■■■■■■■■■■■■■■■■■■■■■■■■■■■■■■■■■■■■■■■■
■
■
Objective
The objective of this section is to mount an additional DMI into the XMI shelf .
Cabling of the additional DMI will be performed after all of the additional expansion
equipment (i.e., XMI, circuit breaker/output power connector assemblies, etc.) that
connects to the additional DMI is installed in the frame.
Required items
Parts
The additional DMI is application dependent. Use one of the following factory built DMI
assemblies as applicable:
All models of DMI assemblies include: DMI chassis with controller board, fans and
front panel.
•DMI assembly with one 1X CDMA modem board (Motorola model STLN6681).
•DMI assembly with one EV -DO modem board (Motorola model STLN6682).
•DMI assembly with two 1X CDMA modem boards (Motorola model STLN6683).
•DMI assembly with one 1X CDMA modem board and one EV -DO modem board (Motorola
model STLN6684).
•DMI assembly with two EV -DO modem boards (Motorola model STLN6679).
68P09283A62 -3 3 -11
PRELIMINARY A UG 2007
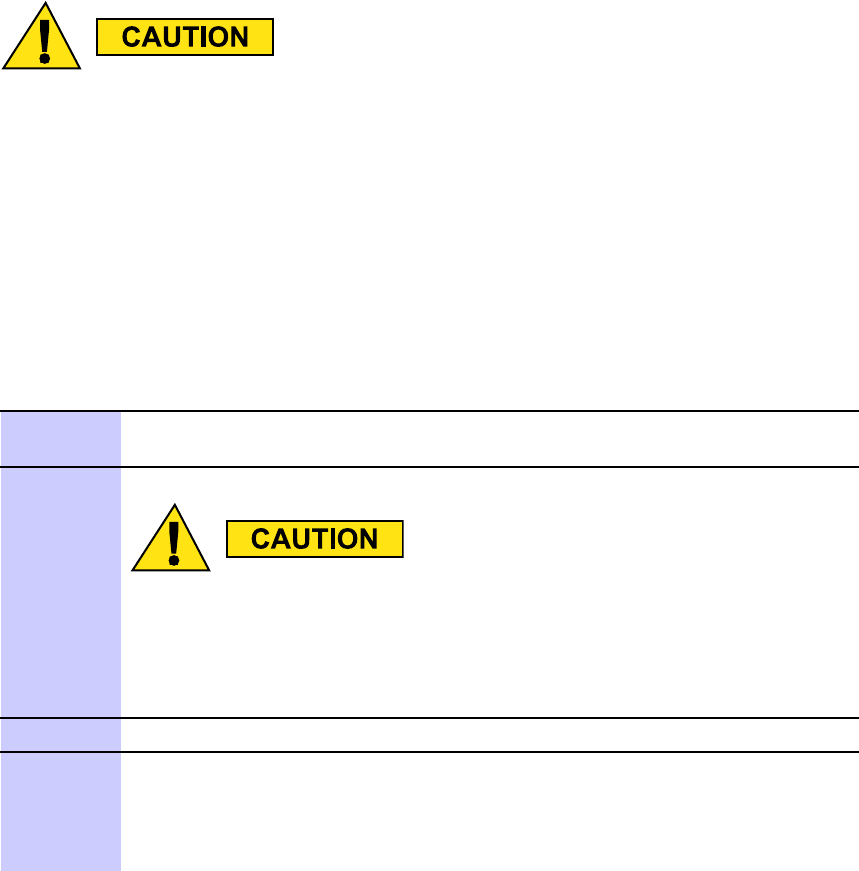
Adding a DMI Chapter 3: Low -to -Mid Capacit y Fr ame Expansion Procedures
Tools
The following tools are required:
•TORX T25 bit and driver
•T orque driver
•ESD wrist strap
Prerequisite
ESD handling precautions must be adhered to when handling the DMI assembly . W ear
a conductiv e, high impedance wrist str ap during handling.
The procedures in this chapter requires working on or around circuitry that is extremely
sensitive to ESD .
Procedure
Procedure 3 -3 contains the steps for adding a 2nd DMI to the XMI shelf .
Procedure 3 -3 Adding a 2nd DMI to the XMI Shelf
1
Set the additional DMI assembly , in its packaging, near the UBS Macro BTS
frame.
2
ESD handling precautions must be adhered to during this
procedure. W ear a conductiv e, high impedance wrist str ap .
Plug the end of the ESD wrist strap into the UBS Macro BTS frame ESD jack
This jack is located in the middle of the upper XMI shelf bracket. A ttach
the wrist strap to your wrist.
3
Remove the additional DMI from its packaging and inspect it for damage.
4
Install the DMI assembly into the appropriate empty DMI housing in the UBS
Macro BTS frame by performing the following:
1. P osition the DMI assembly on its bottom edge so that the front panel
handle is on the right and the retaining fastener is at the top.
Continued
3 -12 68P09283A62 -3
PRELIMINARY A UG 2007
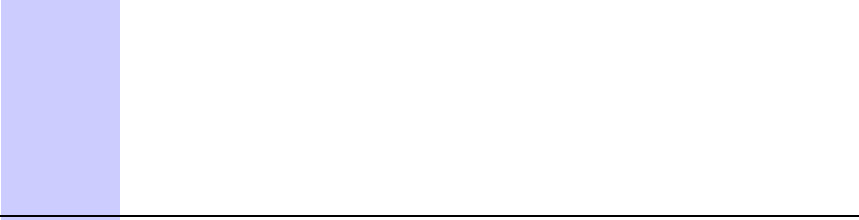
R20 1X UBS Macro B T S Hardw are Installation Adding a DMI
Procedure 3 -3 Adding a 2nd DMI to the XMI Shelf (Continued)
2. Pick up the DMI assembly with two hands.
3. Insert the rear of the DMI assembly into the empty housing.
4. Slide the DMI assembly completely into the housing (see Figure 3-3
Installing a 2nd DMI on page 3- 14 .
5. Turn the retaining fastener CW (Clockwise) until finger tight to secure
the DMI assembly in the housing.
68P09283A62 -3 3 -13
PRELIMINARY A UG 2007
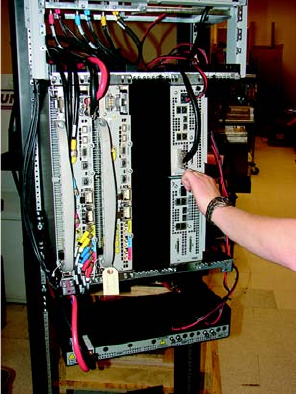
Adding a DMI Chapter 3: Low -to -Mid Capacit y Fr ame Expansion Procedures
Procedural reference diagram
The following diagram helps clarify certain steps in Procedure 3 -3 .
Figure 3 -3 Installing a 2nd DMI
ti-cdma-06033.eps
3 -14 68P09283A62 -3
PRELIMINARY A UG 2007
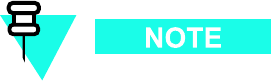
R20 1X UBS Macro B T S Hardw are Installation Adding a Second Set of IDRFs
Adding a Second Set of IDRFs■■■■■■■■■■■■■■■■■■■■■■■■■■■■■■■■■■■■■■■■■■■■■■■■■■■■■■■■■■■■■■
■
■
Objective
The objective of this section is to mount a second set of IDRFs into the IDRF shelf .
Cabling of the second set of IDRFs to the second XMI will be performed after all of
the additional expansion equipment (i.e., XMI, DMI, circuit breaker/output power
connector assemblies, etc.) is installed in the frame.
The second set of IDRFs consists of:
•one IDRF for an omni antenna configuration.
•three IDRFs, one per sector , for a 3 -sector antenna configuration.
The second set of IDRFs mounts in the right -half of the IDRF shelf . The second set of IDRFs are
designated as sector 1, 2 and 3 from left to right.
Required items
Parts
The proper quantity , for omni or 3 -sector antenna configuration, of the following applicable
IDRF is required:
•China Full Band 800 MHz IDRF (Motorola model STFN4009)
•India Full Band 800 MHz IDRF (Motorola model STFN4010)
•US Full Band 800 MHz IDRF (Motorola model STFN4015)
•US A -band 800 MHz IDRF (Motorola model STFN4016)
•US B -band 800 MHz IDRF (Motorola model STFN4017)
•1.9 GHz IDRF (Motorola model STFG4055)
68P09283A62 -3 3 -15
PRELIMINARY A UG 2007
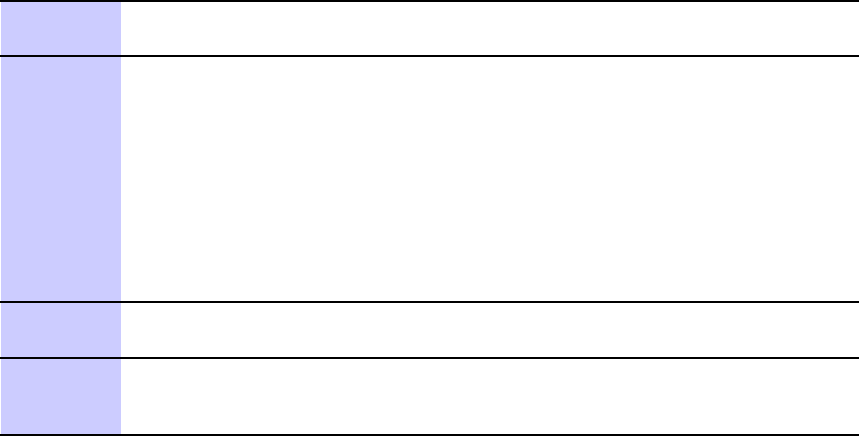
Adding a Second Set of IDRFs Chapter 3: Low -to -Mid Capacit y Fr ame Expansion Procedures
Tools
The following tools are required:
•TORX T25 bit and driver
•T orque driver
Procedure
Procedure 3 -4 contains the steps for adding a second set of IDRFs to the IDRF shelf .
Procedure 3 -4 Adding a second set of IDRFs to the IDRF shelf
1
Remove the additional IDRFs from their packaging and inspect them for
damage.
2
While working at the front/top of the UBS Macro BTS frame, pick up an
additional IDRF and mount it into the IDRF shelf as follows:
•P osition the IDRF with the IDRF mounting plate on top/facing upward
and the mounting plate flange is on the right side (see Figure 3-4
Installing the second set of IDRFs on page 3- 17 photograph B).
•Insert the first IDRF into the sector 1 position on the right half of the top
of the IDRF shelf (see photograph A).
•Slide the IDRF down into the IDRF shelf .
3
Repeat step 2 for the remaining IDRFs, but insert them in sector 2 and sector
3 positions.
4
Insert four mounting screws through each IDRF mounting plate and into the
IDRF shelf . Using a T25 TORX driver , tighten the mounting screws for all of
the additional IDRFs to 4.8 N-m (42.25 in-lb) ±10%.
3 -16 68P09283A62 -3
PRELIMINARY A UG 2007
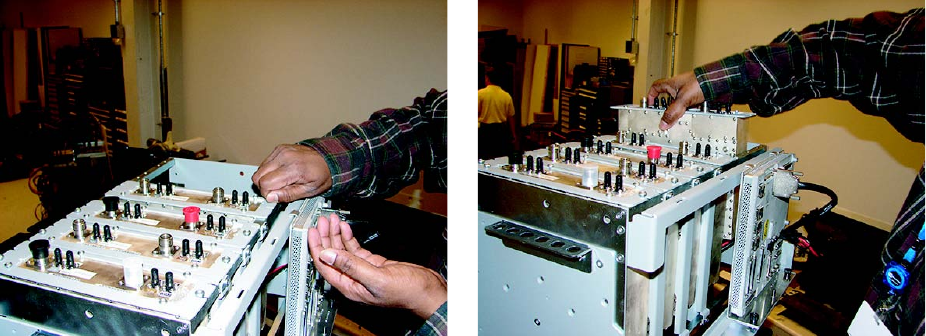
R20 1X UBS Macro B T S Hardw are Installation Adding a Second Set of IDRFs
Procedural reference diagram
The following diagram helps clarify certain steps in Procedure 3 -4 .
Figure 3 -4 Installing the second set of IDRFs
ti-cdma-06035.eps
A B
68P09283A62 -3 3 -17
PRELIMINARY A UG 2007
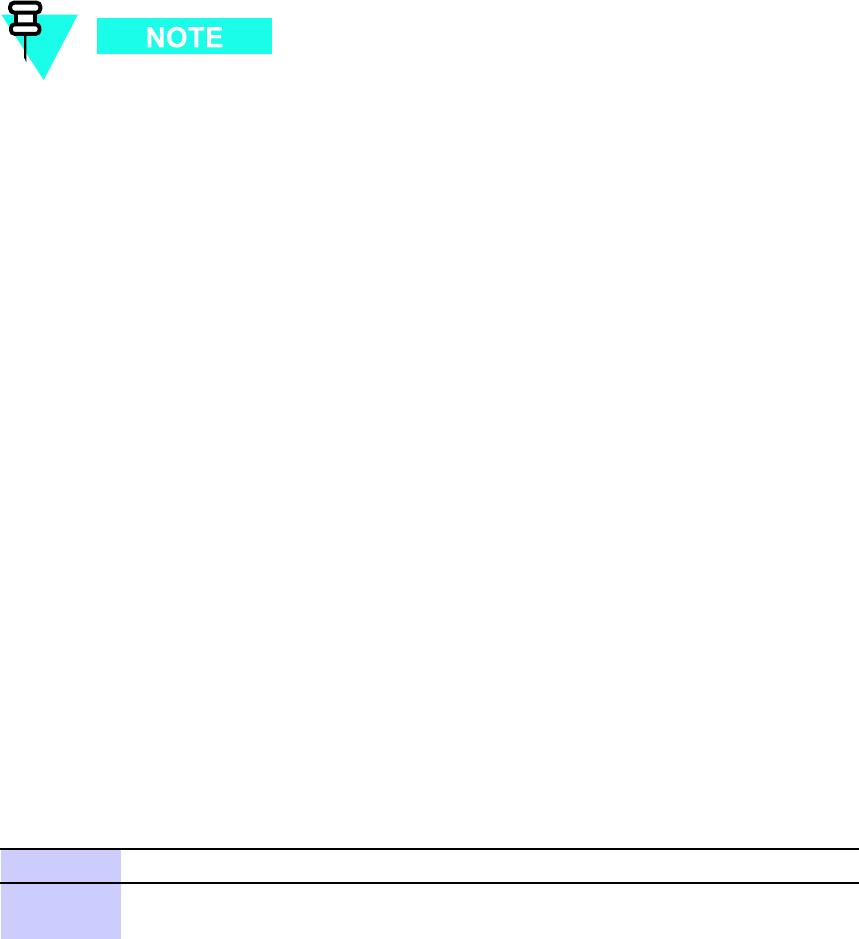
Adding an Optional RX Splitter Chapter 3: Low -to -Mid Capacit y Fr ame Expansion Procedures
Adding an Optional RX Splitter■■■■■■■■■■■■■■■■■■■■■■■■■■■■■■■■■■■■■■■■■■■■■■■■■■■■■■■■■■■■■■
■
■
Objective
The objective of this section is to mount the optional RX splitter onto the bottom of the XMI shelf .
Cabling of the RX splitter to the XMIs will be performed after all of the additional
expansion equipment (i.e., XMI, DMI, circuit breaker/output power connector
assemblies, etc.) is installed in the frame.
Required items
Parts
The following part is required:
•W ide band (800 MHz through 2.1 GHz RF bands) RX splitter (Motorola model STRG4029)
Tools
The following tools are required:
•TORX T25 bit and driver
•T orque driver
Procedure
Procedure 3 -5 contains the steps for adding the RX splitter to the bottom of the XMI shelf .
Procedure 3 -5 Adding an RX splitter to the XMI shelf
1
Remove the RX splitter from its packaging and inspect it for damage.
2
While working at the front of the UBS Macro BTS frame, pick up the RX
splitter and mount it onto the bottom of the XMI shelf as follows:
Continued
3 -18 68P09283A62 -3
PRELIMINARY A UG 2007
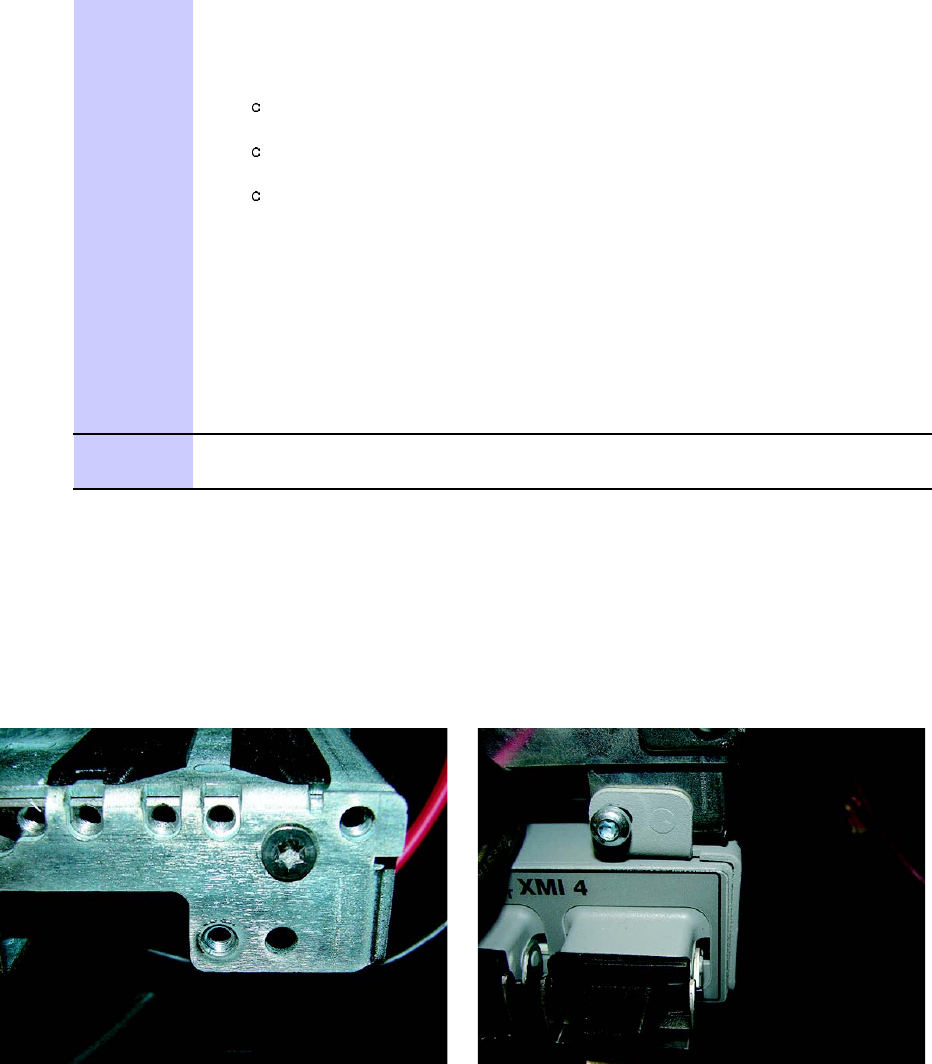
R20 1X UBS Macro B T S Hardw are Installation Adding an Optional RX Splitter
Procedure 3 -5 Adding an RX splitter to the XMI shelf (Continued)
•See Figure 3-5 Mounting the RX splitter on page 3- 19 .
•P osition the RX splitter as follows:
RX splitter I/O connectors facing toward front of the frame.
RX splitter mounting tabs, one on each end of splitter , facing up.
In front of the XMI shelf bottom bracket.
•Align the guide pins on each RX splitter mounting tab with the
corresponding hole located on the XMI shelf bottom bracket (see
photograph A).
•Insert the guide pins into the holes and hold the RX splitter mounting
tabs against the XMI shelf bottom bracket.
•Insert a mounting screw through each RX splitter mounting tab and into
the XMI shelf bottom bracket. (see photograph B).
3
Using a T25 TORX driver , tighten the mounting screws to 4.8 N-m (42.25
in-lb) ±10%.
Procedural reference diagram
The following diagram helps clarify certain steps in Procedure 3 -5 .
Figure 3 -5 Mounting the RX splitter
ti-cdma-06036.eps
A B
68P09283A62 -3 3 -19
PRELIMINARY A UG 2007
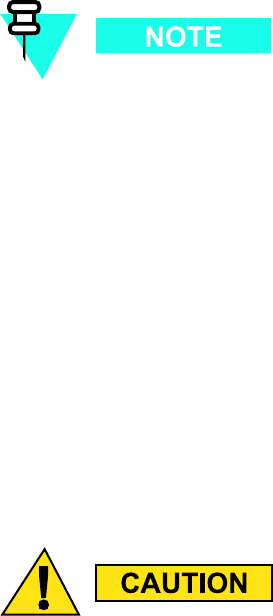
Adding a third PSM (–48 V or 220 V AC only) Chapter 3: Low -to -Mid Capacit y Fr ame Expansion Procedures
Adding a third PSM (–48 V or 220 V AC only)■■■■■■■■■■■■■■■■■■■■■■■■■■■■■■■■■■■■■■■■■■■■■■■■■■■■■■■■■■■■■■
■
■
A third PSM is required when expanding a –48 V DC or 220 V AC UBS Macro BTS
frame from low capacity to mid capacity . The third PSM is for redundancy .
Objective
F or –48 V or 220 V AC only , install the appropriate PSM into slot 3 of the PSM shelf . If
applicable, remove the filler plate that covers slot 3 of the PSM shelf and then install the
appropriate PSM into slot 3.
Required items
Parts
Nev er plug a –48 V DC PSM into a 220 V AC PSM shelf .
Nev er plug a 220 V AC PSM into a -–48 V DC PSM shelf .
One of either the following parts is required:
•–48 V DC P ower Supply Module (–48 V DC PSM) — Motorola model STPN4037
•220 V AC P ower Supply Module (220 V AC PSM) — Motorola model STPN4036
Tools
The following tools are required:
•TORX T25 bit and driver
•T orque driver
3 -20 68P09283A62 -3
PRELIMINARY A UG 2007
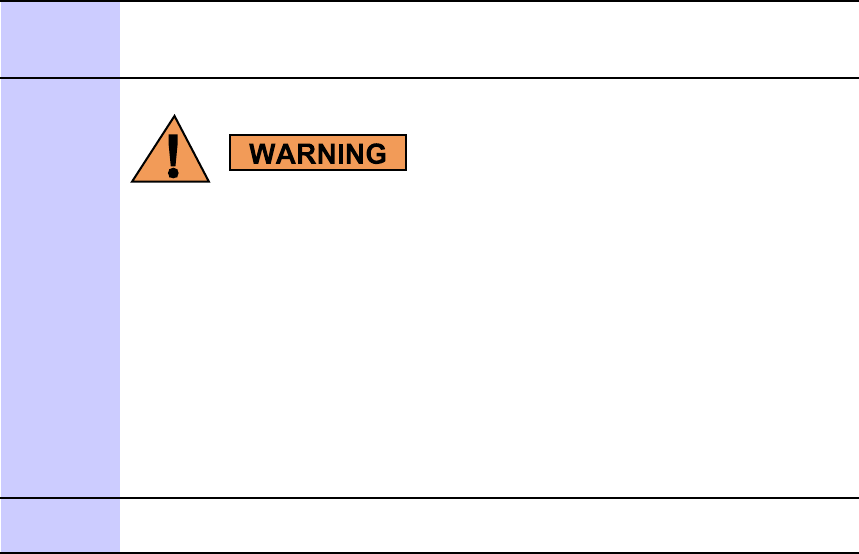
R20 1X UBS Macro B T S Hardw are Installation Adding a third PSM (–48 V or 220 V AC only)
Procedure
Procedure 3 -6 contains the steps for adding a third PSM to the PSM shelf .
Procedure 3 -6 Adding a 3rd PSM to the PSM shelf
1
Use a T25 TORX bit and driver to completely loosen the captive retaining
thumbscrew on the filler plate that covers slot 3 of the PSM shelf . Remove
the filler plate.
2
PSM weighs appro ximately 5 kg. Be careful when handling the PSM
to prev ent damage to the equipment and personal injury .
Install the appropriate PSM into PSM shelf slot 3 as follows:
1. Grasp the handle on the front panel of the PSM with one hand while
carefully supporting the bottom of the module with the other hand.
2. Properly orient the PSM and insert it into the slot.
3. Slowly slide the module into the shelf until the rear connectors are
fully seated. Make sure that the PSM is fully engaged with the shelf
backplane slot connectors.
3
Using a T25 TORX bit and torque driver , tighten the captive retaining
thumbscrew to 2.37 N-m (21 in-lb).
68P09283A62 -3 3 -21
PRELIMINARY A UG 2007
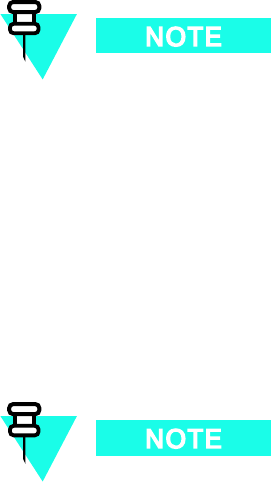
Mid -capacit y Expansion Interconnect Cabling Chapter 3: Low -to -Mid Capacit y Fr ame Expansion Procedures
Mid -capacity Expansion Interconnect Cabling■■■■■■■■■■■■■■■■■■■■■■■■■■■■■■■■■■■■■■■■■■■■■■■■■■■■■■■■■■■■■■
■
■
Remember – A fter all of the additional expansion equipment is installed and cabled,
you
must
go to T ask 7: Cabling the Optional PSM Shelf on page 2 - 43 of Chapter 2
UBS Macro BTS Installation Procedure , and continue performing the remaining
installation tasks in sequential order .
Objective
The objective of this section is to route and connect all required cabling between the additional
mid -capacity expansion equipment (i.e., 2nd XMI, 2nd DMI, optional RX splitter , circuit
breaker/output power connector assemblies) that is installed in the frame.
The RX splitter is optional equipment for expansion to mid -capacity . An RX share
cable can be used instead of the RX splitter for interconnecting RX RF signals
between XMI 1 and XMI 2.
Installing DC power cables
Locate the required DC power cables and then perform Procedure 3 -7 through Procedure 3 -8
as needed.
Required DC power cables
•XMI DC power cable (Motorola part number 3088319T03)
•DMI DC power cable (Motorola part number 3088961T05)
3 -22 68P09283A62 -3
PRELIMINARY A UG 2007

R20 1X UBS Macro B T S Hardw are Installation Mid -capacit y Expansion Interconnect Cabling
DC power cabling procedures
Procedure 3 -7 Installing the XMI 2 DC power cable
1
Locate the XMI DC power cable (Motorola part number 3088319T03).
2
Connect the appropriate end of the XMI DC power cable to the +27 V DC
input power connector on the top of XMI 2 front panel.
Continued
68P09283A62 -3 3 -23
PRELIMINARY A UG 2007

Mid -capacit y Expansion Interconnect Cabling Chapter 3: Low -to -Mid Capacit y Fr ame Expansion Procedures
Procedure 3 -7 Installing the XMI 2 DC power cable (Continued)
3
Route the loose end of the XMI DC power cable as follows:
1. Through the opening above XMI 2 between the XMI shelf and the IDRF
shelf to the back of the XMI shelf .
2. Down and around the left side of the rear of XMI 2.
T o avoid blocking exhaust air from the XMI, the XMI DC power
cable must not be routed directly behind the XMI.
3. Down to the PDU and over the top of the PDU to the PDU front panel.
4
Connect the loose end of the XMI DC power cable to the XMI 2 DC output
power connector on the PDU front panel.
Procedure 3 -8 Installing the DMI 2 DC power cable
1
Locate the DMI DC power cable (Motorola part number 3088961T05).
2
Connect the appropriate end of the DMI DC power cable to the DMI 2 DC
output power connector on the PDU front panel.
Continued
3 -24 68P09283A62 -3
PRELIMINARY A UG 2007
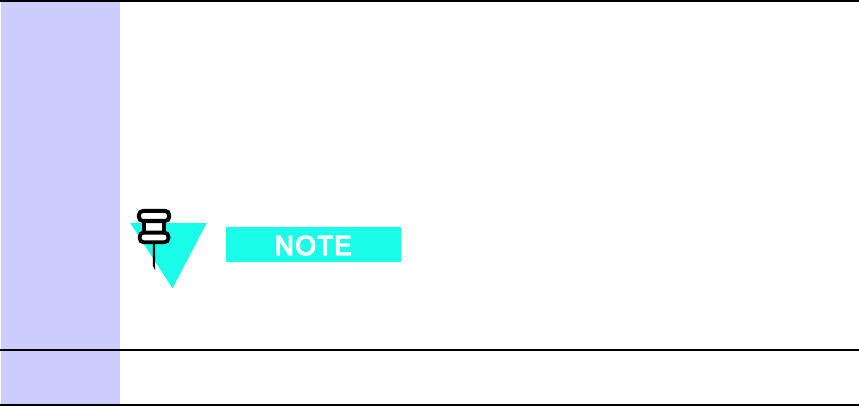
R20 1X UBS Macro B T S Hardw are Installation Mid -capacit y Expansion Interconnect Cabling
Procedure 3 -8 Installing the DMI 2 DC power cable (Continued)
3
Route the loose end of the DMI DC power cable as follows:
1. Up the right side of the frame/rack and around to the back of the frame.
2. Through the opening between the XMI shelf and the IDRF shelf and over
the XMI shelf top bracket.
3. Down to the front panel of the appropriate DMI.
Excess cable should be coiled up and placed on top of the XMI
shelf top bracket.
4
Connect the loose end of the DMI DC power cable to the +27 V DC input
power connector on the front panel of DMI 2.
Installing/Connecting RF cables (XMI to IDRF)
Locate the required RF cables and then perform Procedure 3 -9 and Procedure 3 -10 as needed.
Required RF cables
The required TX RF cables are as follows:
•TX sector -1 RF cable (Motorola part number 3088160T73)
•TX sector -2 RF cable (Motorola part number 3088160T74)
•TX sector -3 RF cable (Motorola part number 3088160T75)
68P09283A62 -3 3 -25
PRELIMINARY A UG 2007
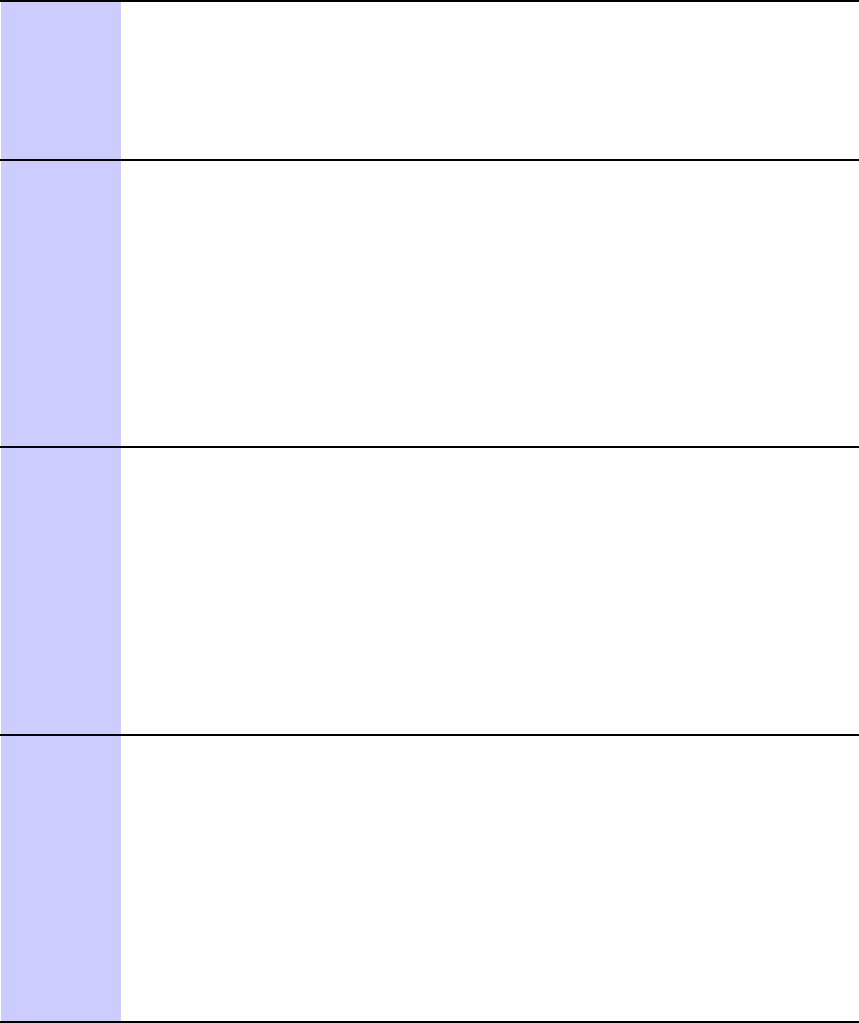
Mid -capacit y Expansion Interconnect Cabling Chapter 3: Low -to -Mid Capacit y Fr ame Expansion Procedures
RF cabling procedures
P erform Procedure 3 -9 to install the TX RF cables between XMI 2 and the second set of IDRFs.
Procedure 3 -9 Installing TX RF cables
1
Locate the following TX RF cables:
•TX sector-1 RF cable (Motorola part number 3088160T73)
•TX sector-2 RF cable (Motorola part number 3088160T74)
•TX sector-3 RF cable (Motorola part number 3088160T75)
2
Install the TX sector-1 RF cable as follows:
1. Connect one end of the cable to the TX1 connector on the XMI 2 front
panel.
2. Route the loose end of the cable through the opening between the XMI
shelf and the IDRF shelf .
3. Loop the cable around under the second set of IDRFs.
4. Connect the loose end of the TX sector-1 RF cable to the TX input
connector on the bottom panel of the sector-1 IDRF of the second set of
IDRFs.
3
Install the TX sector-2 RF cable as follows:
1. Connect one end of the cable to the TX2 connector on the XMI 2 front
panel.
2. Route the loose end of the cable through the opening between the XMI
shelf and the IDRF shelf .
3. Loop the cable around under the second set of IDRFs.
4. Connect the loose end of the TX sector-2 RF cable to the TX input
connector on the bottom panel of the sector-2 IDRF of the second set of
IDRFs.
4
Install the TX sector-3 RF cable as follows:
1. Connect one end of the cable to the TX3 connector on the XMI 2 front
panel.
2. Route the loose end of the cable through the opening between the XMI
shelf and the IDRF shelf .
3. Loop the cable around under the second set of IDRFs.
4. Connect the loose end of the TX sector-3 RF cable to the TX input
connector on the bottom panel of the sector-3 IDRF of the second set of
IDRFs.
3 -26 68P09283A62 -3
PRELIMINARY A UG 2007
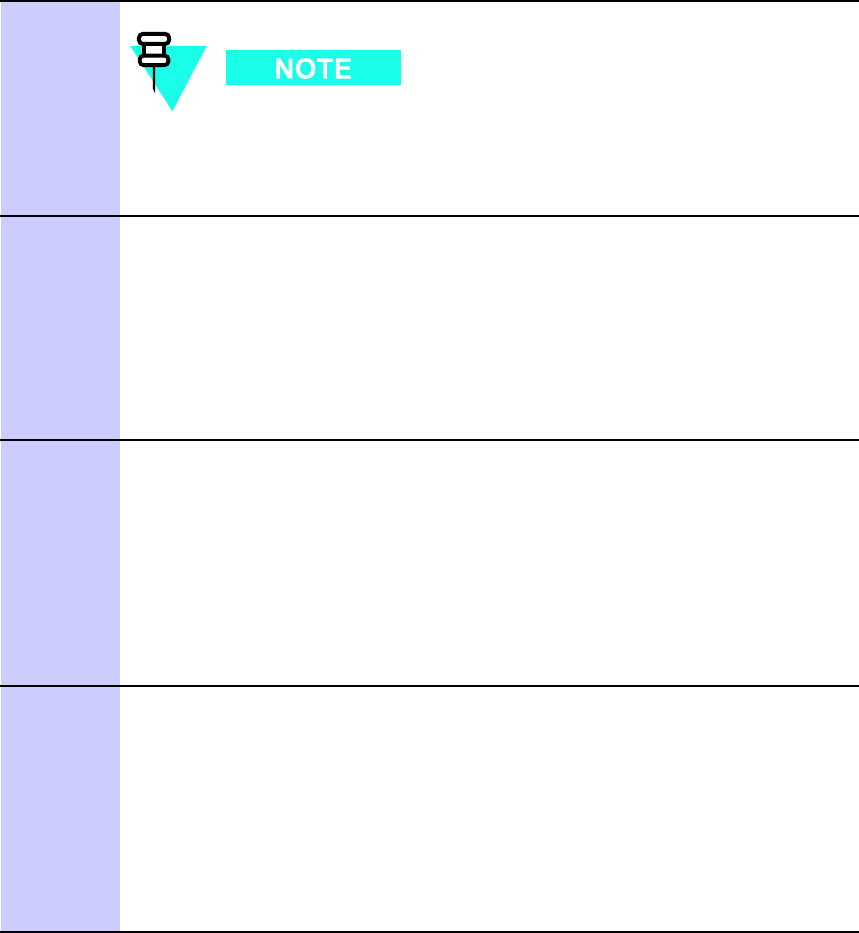
R20 1X UBS Macro B T S Hardw are Installation Mid -capacit y Expansion Interconnect Cabling
P erform Procedure 3 -10 to connect the RX RF cables between XMI 2 and the second set of IDRFs.
Procedure 3 -10 Connecting RX RF cables
On frames with more than one XMI, the XMIs have unused RX input
ports. These unused RX inputs ports
must not
be terminated.
T erminating these unused RX inputs ports will cause improper
operation of the XMIs.
1
Disconnect the following RX RF cables from the front panel of XMI 1:
1. Disconnect the end of the 3088160T79 cable from the RX1 D connector
on the XMI 1 front panel.
2. Disconnect the end of the 3088160T80 cable from the RX2 D connector
on the XMI 1 front panel.
3. Disconnect the end of the 3088160T81 cable from the RX3 D connector
on the XMI 1 front panel.
2
Connect the RX RF cables that were disconnected in step 1 to the front panel
of XMI 2 as follows:
1. Connect the loose end of the 3088160T79 cable to the RX1 D connector
on the XMI 2 front panel.
2. Connect the loose end of the 3088160T80 cable to the RX2 D connector
on the XMI 2 front panel.
3. Connect the loose end of the 3088160T81 cable to the RX3 D connector
on the XMI 2 front panel.
3
Disconnect the following RX RF cables from the bottom of the first (original)
set of IDRFs as follows:
1. Disconnect the end of the 3088160T79 cable from the RX DIV connector
on the bottom panel of the sector-1 IDRF of the first set of IDRFs.
2. Disconnect the end of the 3088160T80 cable from the RX DIV connector
on the bottom panel of the sector-2 IDRF of the first set of IDRFs.
3. Disconnect the end of the 3088160T81 cable from the RX DIV connector
on the bottom panel of the sector-3 IDRF of the first set of IDRFs.
Continued
68P09283A62 -3 3 -27
PRELIMINARY A UG 2007
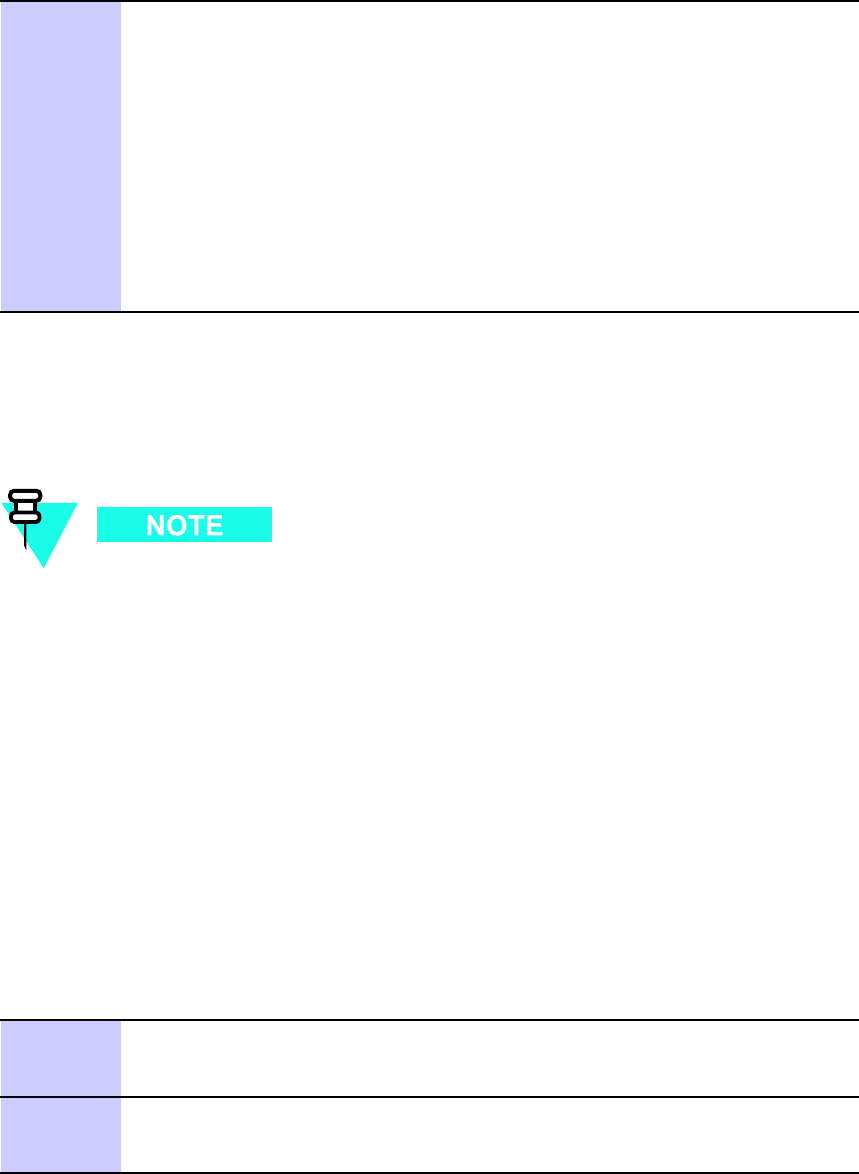
Mid -capacit y Expansion Interconnect Cabling Chapter 3: Low -to -Mid Capacit y Fr ame Expansion Procedures
Procedure 3 -10 Connecting RX RF cables (Continued)
4
Connect the RX RF cables that were disconnected in step 3 to the bottom
panel of the second set of IDRFs as follows:
1. Connect the loose end of the 3088160T79 cable to the RX MAIN
connector on the bottom panel of the sector-1 IDRF of the second set of
IDRFs.
2. Connect the loose end of the 3088160T80 cable to the RX MAIN
connector on the bottom panel of the sector-2 IDRF of the second set of
IDRFs.
3. Connect the loose end of the 3088160T81 cable to the RX MAIN
connector on the bottom panel of the sector-3 IDRF of the second set of
IDRFs.
Installing XMI to DMI cables
Locate the required XMI to DMI cables and then perform Procedure 3 -11 .
F or the mid -capacity frame, there are four 3088791T02 cables used to interconnect
XMIs to DMIs. One of these cables is already installed/connected in the low -capacity
configuration.
Required XMI to DMI cables
The required XMI to DMI cables are as follows:
•Three XMI to DMI cables (Motorola part number 3088791T02)
XMI to DMI cabling procedure
P erform Procedure 3 -11 to install the XMI to DMI cables between two XMIs and two DMIs.
Procedure 3 -11 Installing XMI to DMI cables
1
V erify that an XMI to DMI cable (Motorola part number 3088791T02) is
already installed/connected between XMI 1 front panel connector HSL 1 and
DMI 1 front panel connector XMI 1/BSI.
2
Locate the following cables:
•Three XMI to DMI cables (Motorola part number 3088791T02)
Continued
3 -28 68P09283A62 -3
PRELIMINARY A UG 2007
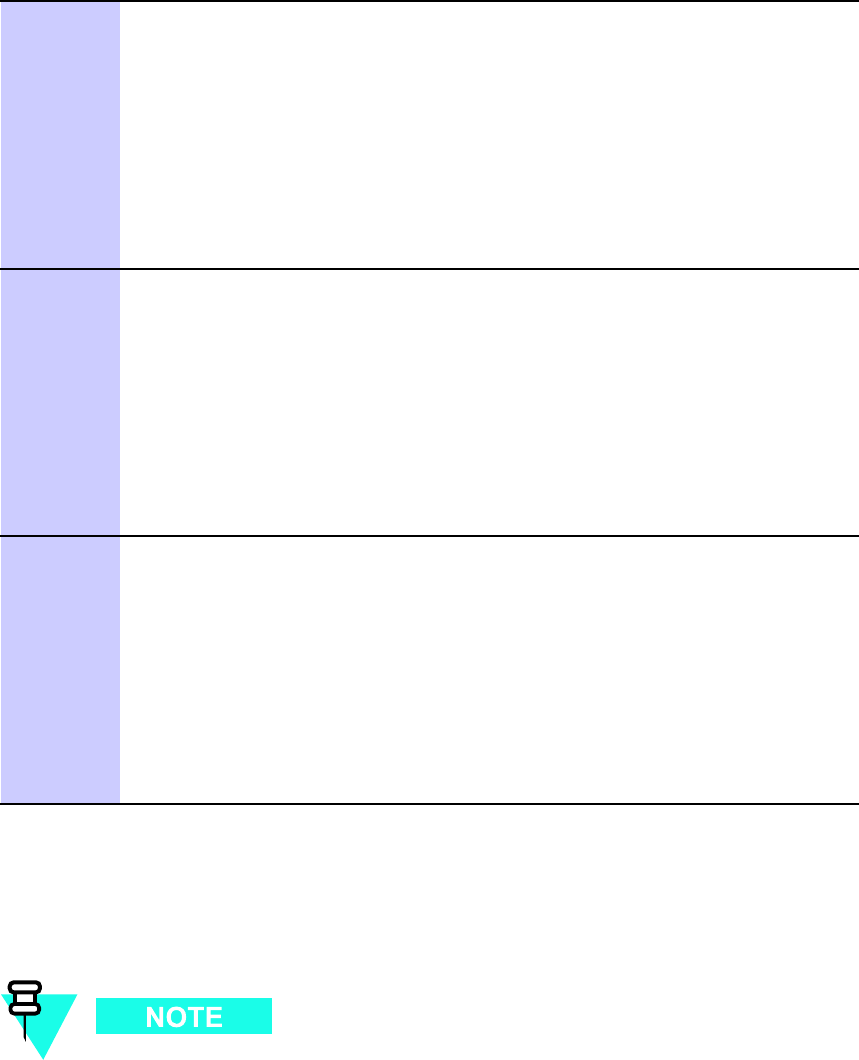
R20 1X UBS Macro B T S Hardw are Installation Mid -capacit y Expansion Interconnect Cabling
Procedure 3 -11 Installing XMI to DMI cables (Continued)
3
Install an XMI to DMI cable between XMI 1 and DMI 2 as follows:
1. Connect the appropriate end of the 3088791T02 cable to the HSL 2
connector on the XMI 1 front panel.
2. Route the loose end of the cable up above XMI 1, through the opening
between the XMI shelf and IDRF shelf , and behind the hooks on the
top XMI shelf bracket. Continue routing over to the XMI shelf DMI slot
and then down to DMI 2.
3. Connect the loose end of the 3088791T02 cable to the XMI 1/BSI
connector on the DMI 2 front panel.
4
Install an XMI to DMI cable between XMI 2 and DMI 1 as follows:
1. Connect the appropriate end of the 3088791T02 cable to the HSL 1
connector on the XMI 2 front panel.
2. Route the loose end of the cable up above XMI 2 through the opening
between the XMI shelf and IDRF shelf , and behind the hooks on the
top XMI shelf bracket. Continue routing over to the XMI shelf DMI slot
and then down to DMI 1.
3. Connect the loose end of the 3088791T02 cable to the XMI 2 connector
on the DMI 1 front panel.
5
Install an XMI to DMI cable between XMI 2 and DMI 2 as follows:
1. Connect the appropriate end of the 3088791T02 cable to the HSL 2
connector on the XMI 2 front panel.
2. Route the loose end of the cable up above XMI 2 through the opening
between the XMI shelf and IDRF shelf , and behind the hooks on the
top XMI shelf bracket. Continue routing over to the XMI shelf DMI slot
and then down to DMI 2.
3. Connect the loose end of the 3088791T02 cable to the XMI 2 connector
on the DMI 2 front panel.
Installing DMI to SSI cables
Locate the required DMI to S SI cables and then perform Procedure 3 -12 .
F or the mid -capacity frame, there are two 3088792T01 cables used to interconnect
S SI 1 to DMI 1 and DMI 2. One of these cables is already installed/connected in
the low -capacity configuration.
68P09283A62 -3 3 -29
PRELIMINARY A UG 2007
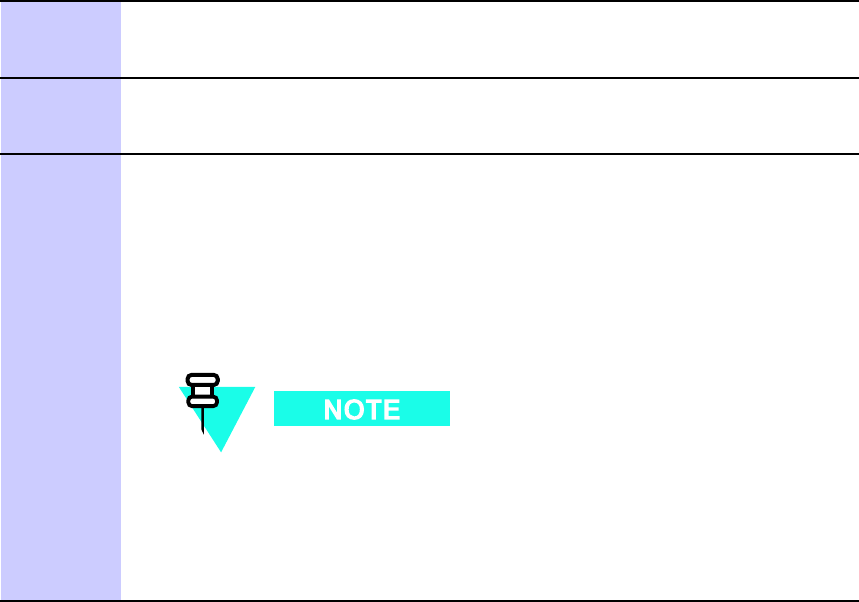
Mid -capacit y Expansion Interconnect Cabling Chapter 3: Low -to -Mid Capacit y Fr ame Expansion Procedures
Required DMI to SSI cables
The required DMI to S SI cable is as follows:
•One DMI to S SI cable (Motorola part number 3088792T01)
DMI to SSI cabling procedure
P erform Procedure 3 -12 to install the DMI to S SI cable between S SI 1 and DMI 2.
Procedure 3 -12 Installing DMI 2 to S SI 1 cable
1
V erify that a DMI to S SI cable (Motorola part number 3088792T01) is already
installed/connected between DMI 1 front panel connector IDI/S SI 1 and S SI
1 front panel connector DMI 1/IDI .
2
Locate the following cables:
•One DMI to S SI cable (Motorola part number 3088792T01)
3
Install the DMI to S SI cable between DMI 2 and S SI 1 as follows:
1. Connect the appropriate end of the 3088792T01 cable to the IDI/S SI 1
connector on the DMI 2 front panel.
2. Route the loose end of the cable up above the XMI shelf DMI slot,
through the opening between the XMI shelf and the IDRF shelf , and
out the right side of the opening. Continue routing upwards along the
right rack rail and over in to S SI 1.
Excess cable should be coiled up and placed on top of the
XMI shelf top bracket.
3. Connect the loose end of the 3088792T01 cable to the DMI 2 connector
on the S SI 1 front panel.
Installing RX splitter to XMI RX RF cables or RX share cable
Expansion to mid -capacity requires interconnection of RX RF signals between XMI 1 and XMI 2.
This can be accomplished by using an optional RX splitter or RX share cable.
If the optional RX splitter is used, locate the required RX splitter to XMI RX RF cables and then
perform Procedure 3 -13 .
If the optional RX splitter is not used, locate the required RX share cable and then perform
Procedure 3 -14 .
3 -30 68P09283A62 -3
PRELIMINARY A UG 2007
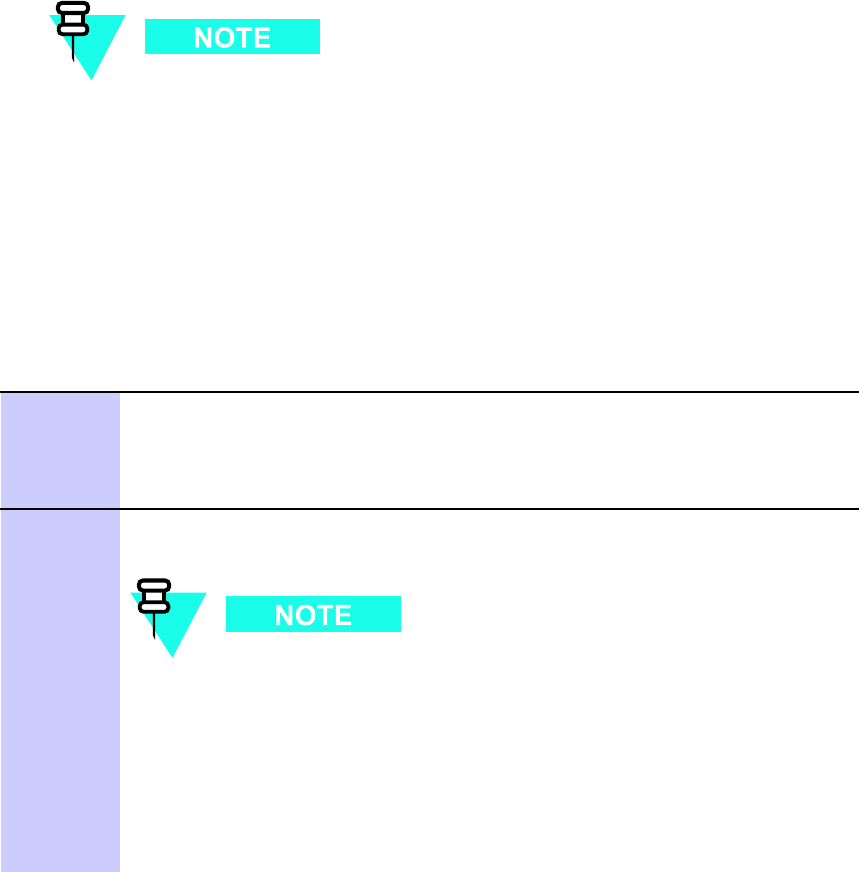
R20 1X UBS Macro B T S Hardw are Installation Mid -capacit y Expansion Interconnect Cabling
Required RX splitter to XMI RX RF cables
The required RX splitter to XMI RX RF cables are as follows:
•RX splitter to XMI 1 RX RF cable (Motorola part number 3088407T10)
•RX splitter to XMI 2 RX RF cable (Motorola part number 3088407T11)
Required RX share cable
The required RX share cable is as follows:
•RX share cable (Motorola part number SGLN6345 which includes: 3088407T09 cable)
The RX share cable connects XMI 1 RX EXP OUT to XMI 2 RX EXP IN and XMI
2RX EXP OUT to XMI 1 RX EXP IN .
RX splitter to XMI cabling procedure
P erform Procedure 3 -13 to install the RX splitter to XMI RX RF cables between RX splitter and
the two XMIs.
Procedure 3 -13 Installing RX splitter to XMI RX RF cables
1
Locate the following cables:
•RX splitter to XMI 1 RX RF cable (Motorola part number 3088407T10)
•RX splitter to XMI 2 RX RF cable (Motorola part number 3088407T11)
2
Install the RX splitter to XMI 1 RX RF cable (Motorola part number
3088407T10) as follows:
The 3088407T10 cable contains two separate cables bundled
together . The 3088407T10 cable has two connectors on each end
of the bundle. The ends of each separate cable can be determined
by observation.
1. P osition the 3088407T10 cable so that two connectors on one end of the
bundle are in front of XMI 1 (i.e., XMI end) and the two connectors on
the other end of the bundle are in front of the RX splitter .
Continued
68P09283A62 -3 3 -31
PRELIMINARY A UG 2007

Mid -capacit y Expansion Interconnect Cabling Chapter 3: Low -to -Mid Capacit y Fr ame Expansion Procedures
Procedure 3 -13 Installing RX splitter to XMI RX RF cables (Continued)
2. Connect an XMI end connector to the RX EXP OUT connector on the
XMI 1 front panel.
3. Connect the loose end of the same separate cable to the XMI 1 RX EXP
IN connector on the RX splitter front panel.
4. Connect the remaining XMI end connector to the RX EXP IN connector
on the XMI 1 front panel.
5. Connect the loose end of the same separate cable to the XMI 1 RX EXP
OUT connector on the RX splitter front panel.
3
Install the RX splitter to XMI 2 RX RF cable (Motorola part number
3088407T11) as follows:
The 3088407T11 cable contains two separate cables bundled
together . The 3088407T11 cable has two connectors on each end
of the bundle. The ends of each separate cable can be determined
by observation.
1. P osition the 3088407T11 cable so that two connectors on one end of the
bundle are in front of XMI 2 (i.e., XMI end) and the two connectors on
the other end of the bundle are in front of the RX splitter .
2. Connect an XMI end connector to the RX EXP OUT connector on the
XMI 2 front panel.
3. Connect the loose end of the same separate cable to the XMI 2 RX EXP
IN connector on the RX splitter front panel.
4. Connect the remaining XMI end connector cable to the RX EXP OUT
connector on the XMI 2 front panel.
5. Connect the loose end of the same separate cable to the XMI 2 RX EXP
IN connector on the RX splitter front panel.
XMI 1 to XMI 2 RX cabling procedure
P erform Procedure 3 -14 to install the RX share cable to interconnect RX RF signals between
XMI 1 and XMI 2.
Procedure 3 -14 Installing RX share cable
Continued
3 -32 68P09283A62 -3
PRELIMINARY A UG 2007
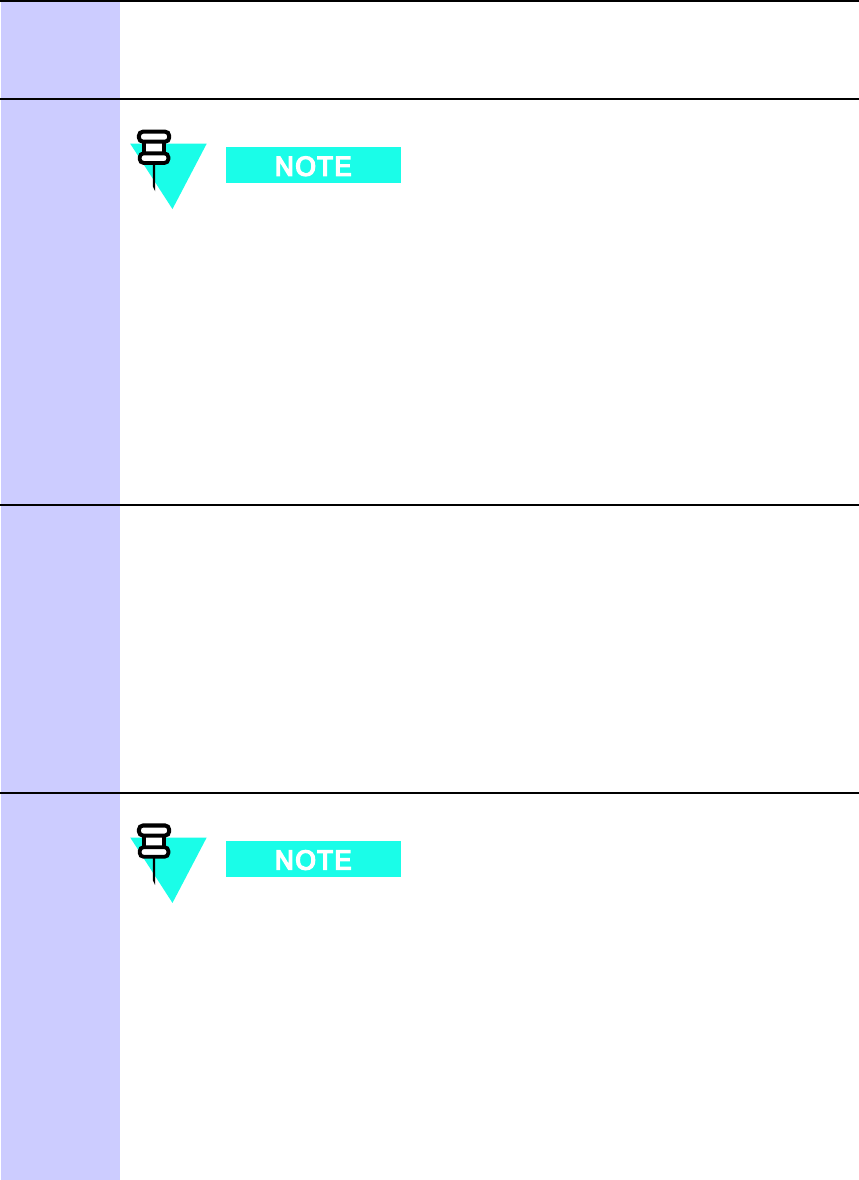
R20 1X UBS Macro B T S Hardw are Installation Mid -capacit y Expansion Interconnect Cabling
Procedure 3 -14 Installing RX share cable (Continued)
1
Locate the following cable:
•RX share cable (Motorola part number SGLN6345 which includes:
3088407T09 cable)
The 3088407T09 cable contains two separate cables bundled
together . The 3088407T09 cable has four ends with a connector on
each end.
The ends of the RX share cable are labeled as follows:
•XMI 1 OUT
•XMI 1 IN
•XMI 2 OUT
•XMI 2 IN
2
Install the RX share cable as follows:
1. Connect the XMI 1 OUT cable connector to the RX EXP OUT connector
on the XMI 1 front panel.
2. Connect the XMI 1 IN cable connector to the RX EXP IN connector
on the XMI 1 front panel.
3. Connect the XMI 2 OUT cable connector to the RX EXP OUT connector
on the XMI 2 front panel.
4. Connect the remaining XMI 2 IN cable connector to the RX EXP IN
connector on the XMI 2 front panel.
3
Because it is possible to incorrectly connect the the RX share
cable between XMI 1 and XMI 2, it is necessary to verify these
connections.
V erify that the RX share cable is properly connected between XMI 1 and
XMI 2 as follows:
•The cable ends labeled XMI 1 OUT and XMI 1 IN must be connected to
XMI 1.
•The cable ends labeled XMI 2 OUT and XMI 2 IN must be connected to
XMI 2.
Continued
68P09283A62 -3 3 -33
PRELIMINARY A UG 2007

Mid -capacit y Expansion Interconnect Cabling Chapter 3: Low -to -Mid Capacit y Fr ame Expansion Procedures
Procedure 3 -14 Installing RX share cable (Continued)
•The cable ends with the word OUT in its label must be connected to XMI
connectors labeled RX EXP OUT .
•The cable ends with the word IN in its label must be connected to XMI
connectors labeled RX EXP IN .
3 -34 68P09283A62 -3
PRELIMINARY A UG 2007
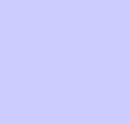
C h a p t e r
4
What’s Next■■■■■■■■■■■■■■■■■■■■■■■■■■■■■■■■■■■■■■■■■■■■■■■■■■■■■■■■■■■■■■
■
■
■
■
68P09283A62 -3 4 -1
A UG 2007 PRELIMINARY
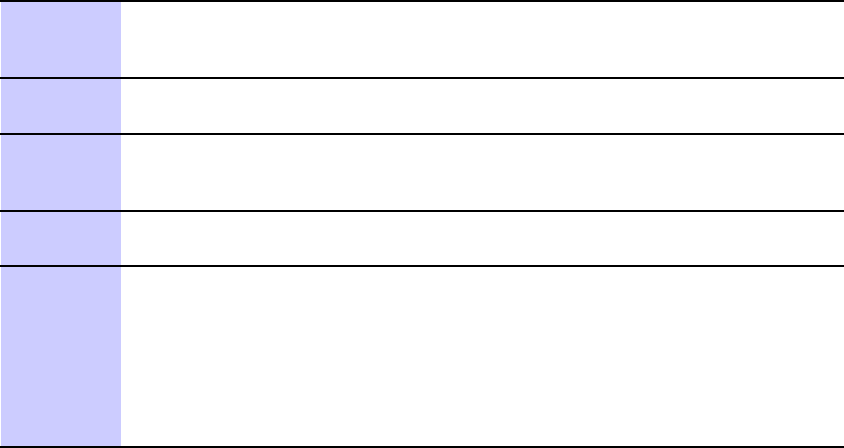
Installation completion Chapter 4: What ’ s Next
Installation completion■■■■■■■■■■■■■■■■■■■■■■■■■■■■■■■■■■■■■■■■■■■■■■■■■■■■■■■■■■■■■■
■
■
A t this point the hardware installation is complete. P erform the following tasks to complete the
system installation.
•Clean up the site
•Fill out the installation completion checklist
•Record As -Built information
•P erform the A TP s
•Load the software
P erform the clean up of the site and fill out the checklist, first. Then perform the rest of the
tasks or perform them later .
Clean up the site
Clean up the site by following the instructions given in Procedure 4 -1 .
Procedure 4 -1 Cleaning the site
1
Remove protective covering
Remove any cardboard from the walls that was used to protect the walls.
Remove any antistatic plastic or cloth sheet used to cover the equipment.
2
Lighting fixtures
Remove any masking tape from the fluorescent light fixtures.
3
T ools
Place all hand and power tools in the installation tool kit or other appropriate
place. Check for any tools requiring replacement, cleaning, or adjustment.
4
Materials
Place any leftover materials in a location specified by the site manager .
5
Remove debris
T o remove the debris, perform the following:
•Remove any packing material.
•Ensure that all scrap materials are removed from any tables or stands.
•Clean/sweep the floor . Ensure all chalk -line marks are removed.
Continued
4 -2 68P09283A62 -3
PRELIMINARY A UG 2007
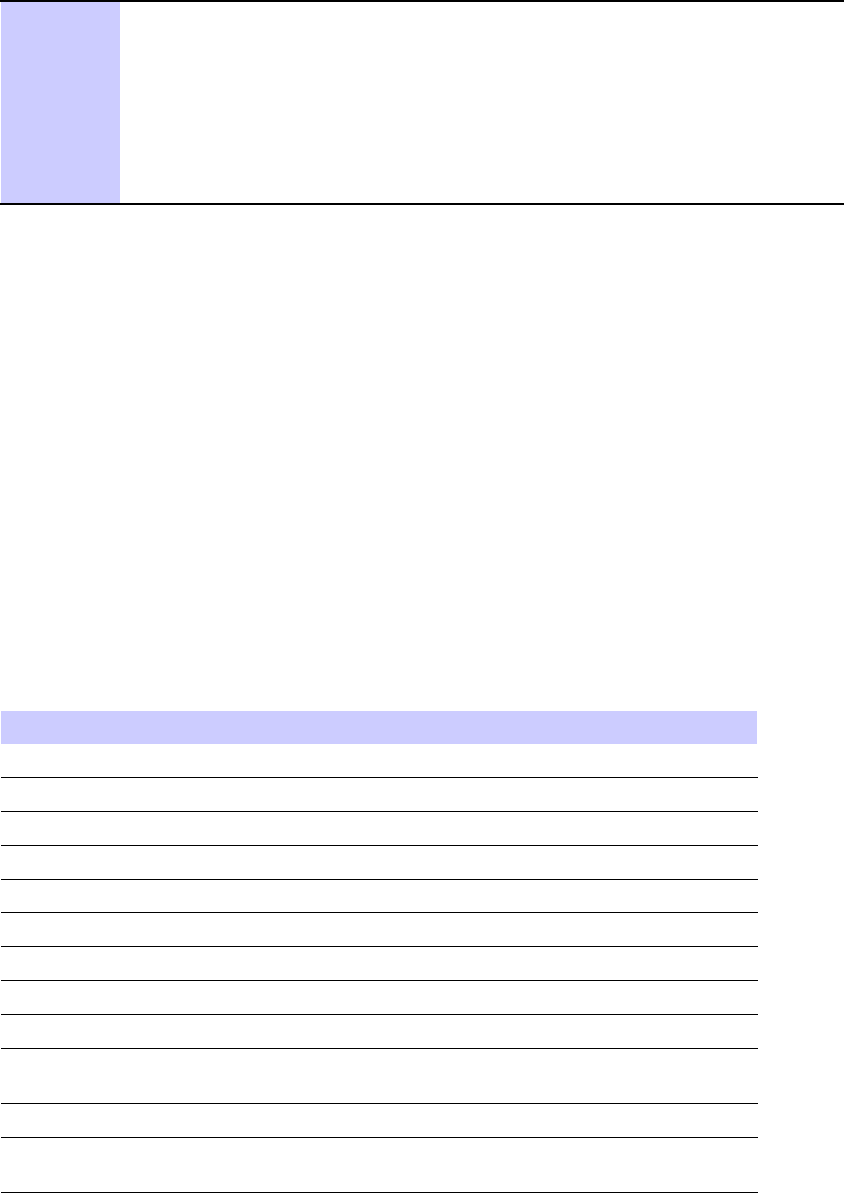
R20 1X UBS Macro B T S Hardw are Installation Installation completion
Procedure 4 -1 Cleaning the site (Continued)
6
Environment
P erform the following to check the environment:
•Check whether all covers, frame doors and fan housings are in place.
•Confirm all power connections are tight.
•Organize any items (such as manuals, materials, etc.) left on site and
place them in a safe location specified by the site manager .
Fill out the installation completion checklist
A fter the site is cleaned up, fill out the installation completion checklist and make any necessary
copies. Copy this check sheet as required.
Installation completion checklist
Date Hardware Installation Completed: _________________
Site: _________________
BTS Frame Serial Number: _________________
Checklist Completed By: _________________
Checklist Reviewed By: _________________
Table 4 -1 Installation completion checklist
Status
No. Item Notes
1
Frames are bolted down.
2
DC power cabling completed.
3
Each frame has its own earth ground.
4
RX RF cables installed.
5
TX RF cables installed.
6
Span line cables installed.
7
Alarm cables installed.
8
RGPS head installed (if required).
9
RGPS cabling installed (if required).
10
All connectors (power , signal, RF ,
internal and external) are tight.
11
All cables dressed and tied.
12
Installation and site specific manuals at
site.
Continued
68P09283A62 -3 4 -3
PRELIMINARY A UG 2007
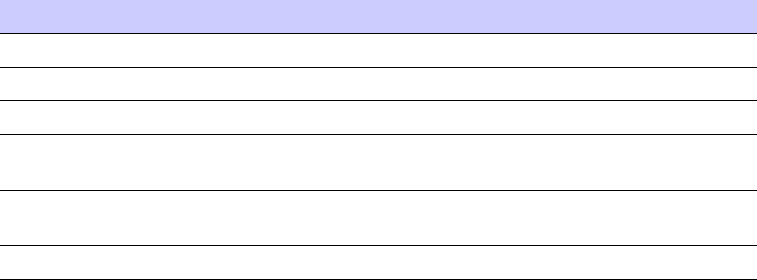
Installation completion Chapter 4: What ’ s Next
Table 4 -1 Installation completion checklist (Continued)
Status
No. Item Notes
13
Cable racks properly grounded.
14 Static wrist straps are present.
15
Site cleaned, swept, and trash removed.
16
Any deficiencies reported to the
appropriate people.
17
Correct polarity has been maintained
from the DC power source to the frame.
18
P ower has not been applied to any frame.
Record “As -Built” information
Record the site specific information on how the unit was installed and cabled.
Performing the ATPs
This manual does not cover the procedure of performing the A TP s. F or this procedure, refer to
the
1X UBS Macro BTS Optimization/A TP
(68P09283A63) manual.
Loading the software
This manual does not cover the procedure for loading the software. Refer to the appropriate
software release manual for procedure for loading the software.
4 -4 68P09283A62 -3
PRELIMINARY A UG 2007