ADC Telecommunications DLC0802A Digivance 800 MHz 20 Watts System User Manual 75150
ADC Telecommunications Inc Digivance 800 MHz 20 Watts System 75150
Contents
manual6
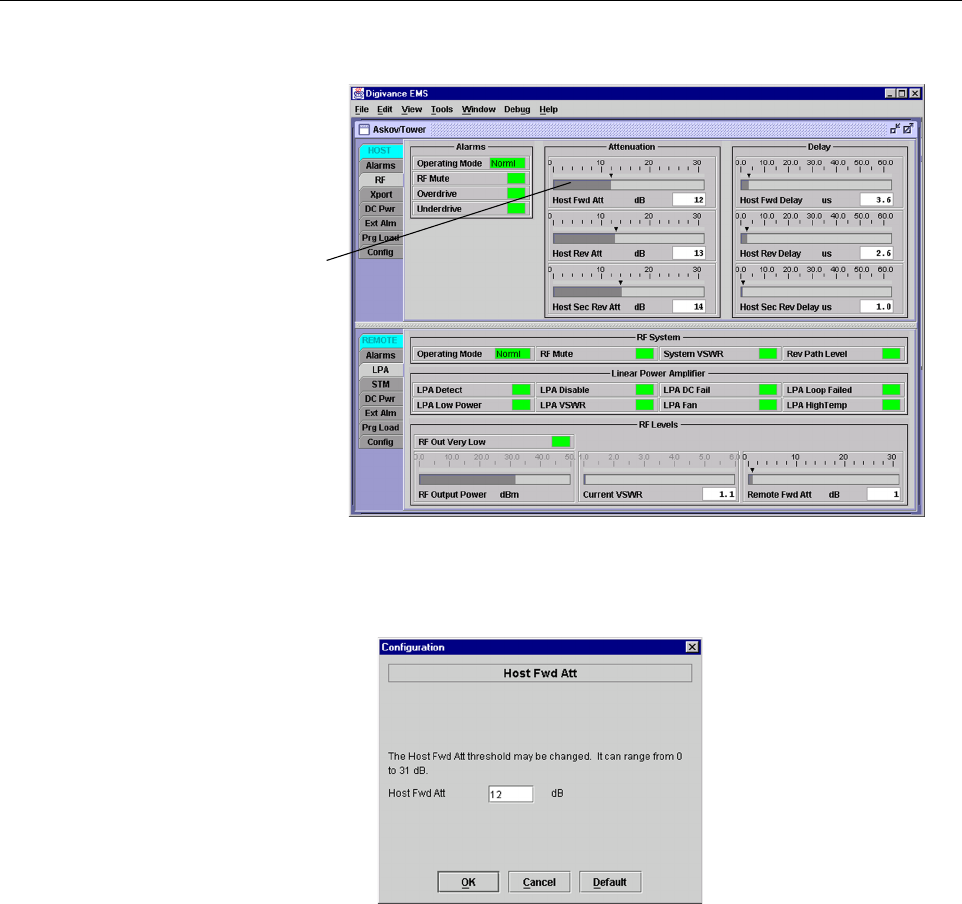
ADCP-75-150 • Preliminary Issue A • March 2003 • Section 4: Operation
Page 4-12
©2003, ADC Telecommunications, Inc.
Figure 4-8. HOST RF Display
Figure 4-9. Host Fwd Att Pop-Up Screen
2.6 Determine Output Signal Level at STM Antenna Port
The RF output signal level should be measured at the STM ANTENNA port to verify that
maximum composite signal level is at the required level. Use the following procedure to
determine the power level:
1. Verify that RF ON/OFF switch on the LPA in the OFF position.
2. Disconnect the antenna cable from the STM ANTENNA port.
3. Connect aspectrum analyzer or RF power meter to the STM ANTENNA port. (Check the
input rating of the test equipment. Insert a30 dB 100 Wattenuator if necessary.)
Right-click here
to open Host Fwd
Att pop-up screen
FCC ID: F8I-DLC0802A User Manual - Part 6
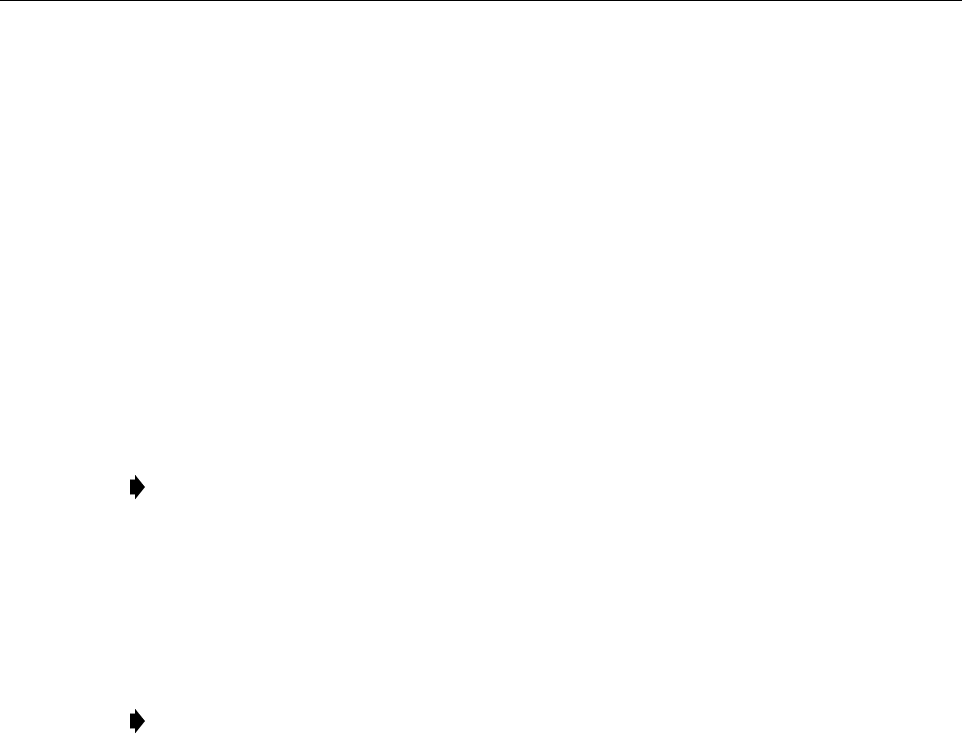
ADCP-75-150 • Preliminary Issue A • March 2003 • Section 4: Operation
Page 4-13
©2003, ADC Telecommunications, Inc.
4. Place the RF ON/OFF switch on the LPA in the ON position.
5. If using aspectrum analyzer, proceed to step 6. If using apower meter, measure the
composite signal power from the STM and then proceed to step 8.
6. Measure the RF level of asingle carrier, such as the control channel, in dBm. Make sure
the resolution bandwidth of the spectrum analyzer is 30 kHz.
7. Calculate the total composite signal power using the following formula:
Ptot = Pc+10Log N – (see Note)
Where,
Ptot is the total composite power in dBm
Pcis the power per carrier in dBm as measured in step 6, and
Nis the total number of channels.
8. Record the result measured in step 5or calculated in step 7.
9. Place the MUTE/NORM/RESET switch on the LPA in the OFF position.
10. Disconnect the spectrum analyzer or RF power meter from the STM ANTENNA port.
11. Re-connect the antenna cable to the STM ANTENNA port.
2.7 Enter Remote Forward Attenuation
The STM internal forward path attenuator setting is used to reduce the power level of the
composite output signal level at the STM antenna port. The maximum composite output signal
level at the STM antenna port is set using the Host internal forward attenuator (see Section 2.4).
However, component variations may result in the output power at the STM antenna port being
slightly above or below the required power per channel. If this is the case, the STM forward
attenuator may be used in conjunction with the Host forward attenuator to add or remove
attenuation to produce the required output signal level. If less power is required, the STM
forward attenuator may be used to reduce the power level. The default setting is 0dB. Use the
following procedure to change the STM forward attenuation:
1. Click on the REMOTE LPA tab. The REMOTE LPA display will open within the DEMS
main window as shown in Figure 4-10.
Note: If calculating the composite power for aCDMA system, reduce the initial result by
16.23 dBm
Note: To comply with Maximum Permissible Exposure (MPE) requirements, the
maximum composite output from the antenna cannot exceed 1000 Watts EIRP and the
antenna must be permanently installed in afixed location that provides at least 6meters
(20 feet) of separation from all persons.
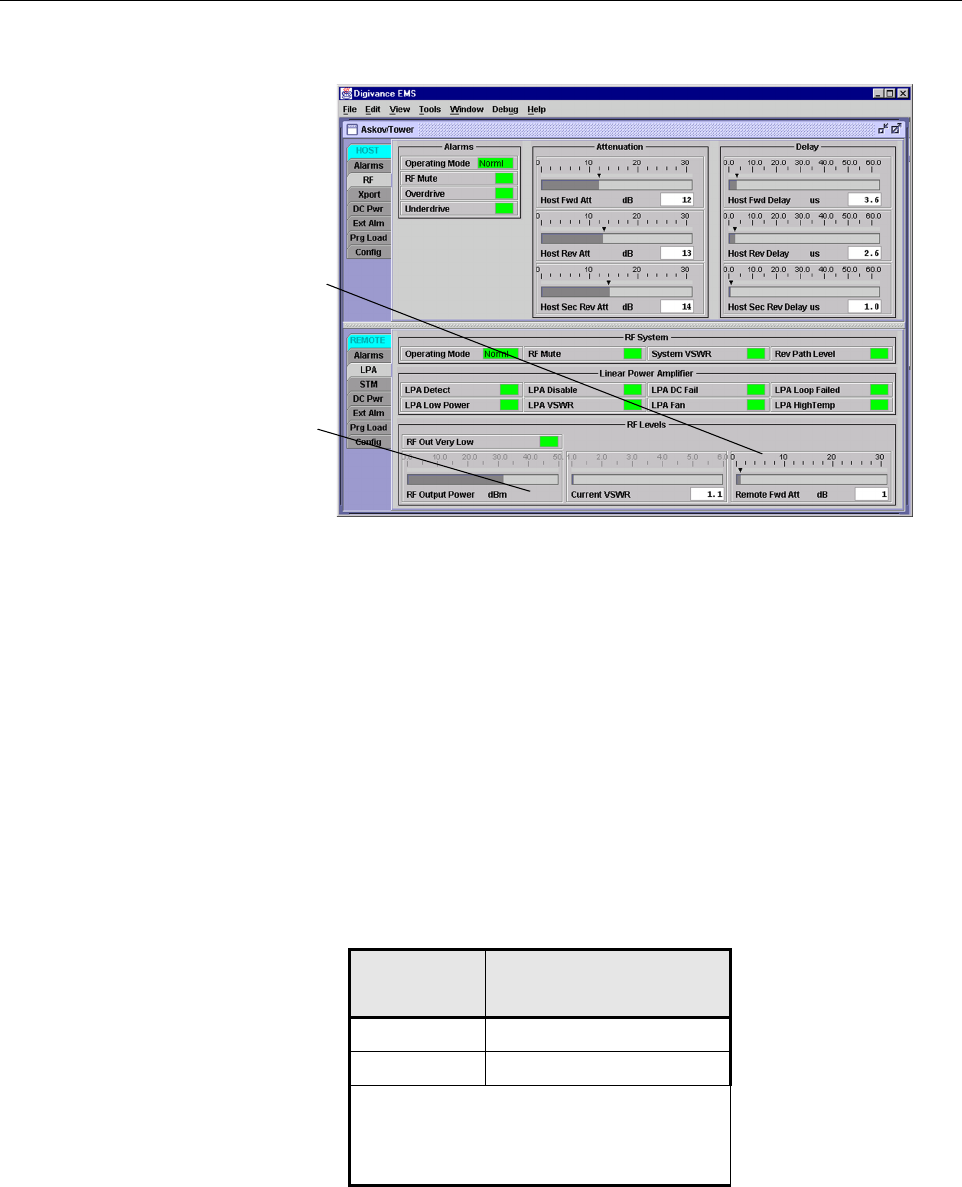
ADCP-75-150 • Preliminary Issue A • March 2003 • Section 4: Operation
Page 4-14
©2003, ADC Telecommunications, Inc.
Figure 4-10. REMOTE LPA Display
2. Check the level of the RF output signal (as determined in Section 2.6)against the system
design plan specifications. Table 4-1 shows the output signal level required to provide 5
watts per channel for systems with 1to 2channels. The maximum output signal level
permitted for the system is 40.5 dBm (11 Watts).
3. Determine if more or less attenuation is required to produce the required output signal level.
4. Right-click on the Remote Fwd Att section of the display (see Figure 4-10). The Remote
Fwd Att pop-up screen will open as shown in Figure 4-11.
5. Enter the required attenuation value and click OK to close the pop-up screen and to make
the changes take effect.
Table 4-1. Composite Output Signal Levels
NUMBER OF
CHANNELS
OUTPUT SIGNAL LEVEL
REQUIRED TO PROVIDE 5
WATTS PER CHANNEL
137dBm
240dBm
When there are three or more channels, each
channel will always be less than 5watts since
the system has amaximum power output of
11 watts (40.5 dBm).
Right-click here to
open the Remote Fwd
Att pop-up screen
RF output signal level
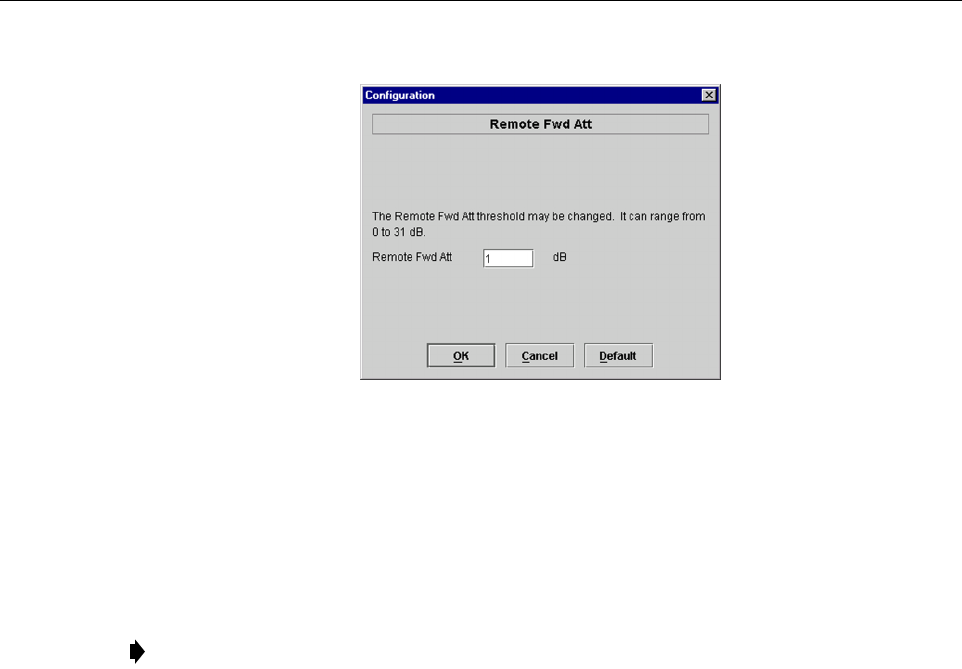
ADCP-75-150 • Preliminary Issue A • March 2003 • Section 4: Operation
Page 4-15
©2003, ADC Telecommunications, Inc.
Figure 4-11. Remote Fwd Att Pop-Up Screen
6. Verify that the appropriate RF output signal level appears in the RF Pwr-VSWR Low
section (see Figure 4-10). This is primarily areference value and should not take the place
of external test equipment when determining the power level of the composite RF output
signal. Depending on the modulation type and number of channels, the DEMS software
may report apower level that is higher or lower than the actual RF output signal.
2.8 Enter Host Reverse Attenuation
The level of the RF signal that should be input to the BTS will vary depending on the type of
BTS, the receive distribution, and the number of channels present. To interface with the BTS,
the reverse path signal level must be adjusted to provide the signal level required by the BTS.
The HU provides from 0dB of gain to +30 dB of gain in the reverse path. Use the following
procedure to set the reverse path gain:
1. Check the BTS manufacturer’s specifications to determine the composite signal level
required at the BTS reverse path input port.
2. Determine the overall gain and loss imposed on the signal by the antenna, antenna cable,
and by the cables that connect the HU to the BTS.
3. Determine the amount of gain required to raise the reverse path signal to the level required
at the BTS.
4. Click on the HOST RF tab. The HOST RF display will open within the DEMS main
window as shown in Figure 4-12.
Note: To comply with Maximum Permissible Exposure (MPE) requirements, the
maximum composite output from the antenna cannot exceed 1000 Watts EIRP and the
antenna must be permanently installed in afixed location that provides at least 6meters
(20 feet) of separation from all persons.
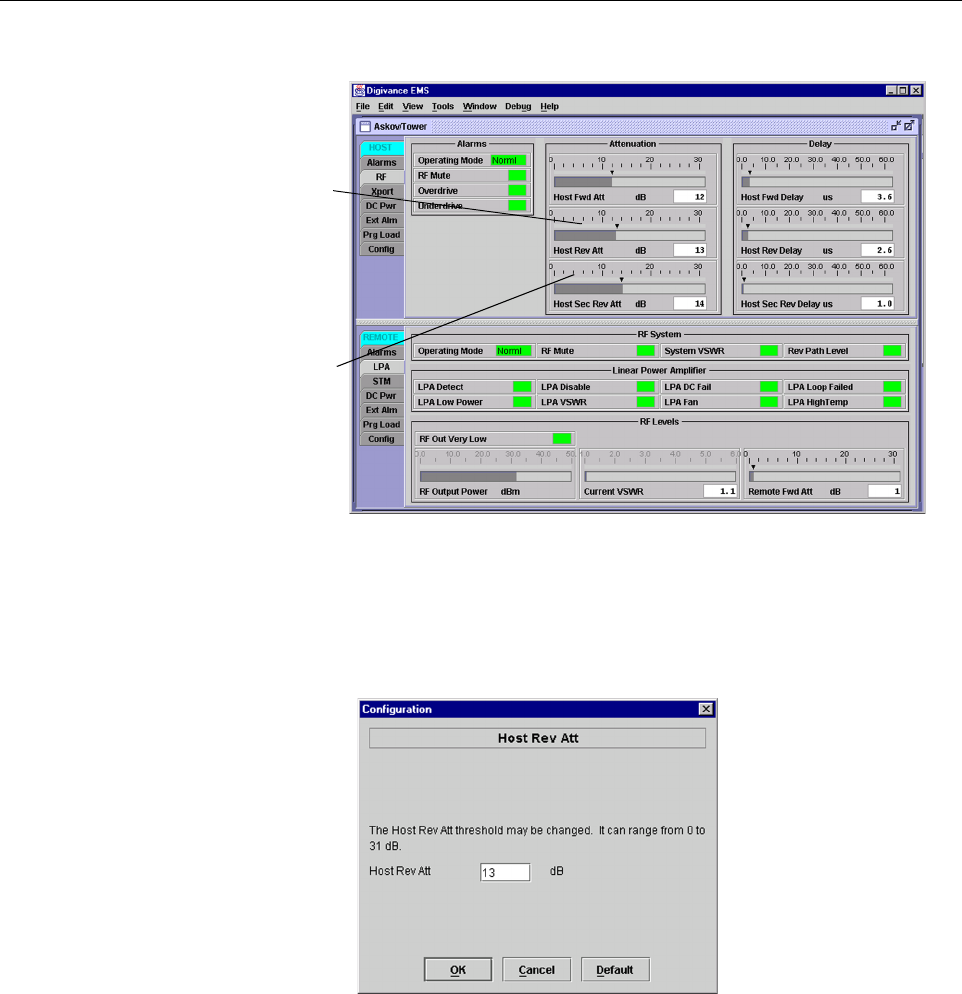
ADCP-75-150 • Preliminary Issue A • March 2003 • Section 4: Operation
Page 4-16
©2003, ADC Telecommunications, Inc.
Figure 4-12. HOST RF Display
5. Right-click on the Host Rev Att section of the display (see Figure 4-12). The Host Rev
Att pop-up screen will open as shown in Figure 4-13.
Figure 4-13. Host Rev Att Pop-Up Screen
6. Enter the attenuation value that will provide the required gain. Refer to Table 4-2 for the
attenuation values and the corresponding gain (nominal) values.
7. Click OK to close the pop-up screen and to make the changes take effect.
8. Click OK to close the pop-up screen and to make the changes take effect.
Right-click here to
open the Host Rev Att
pop-up screen
Right-click here to
open the Host Div Rev
Att pop-up screen
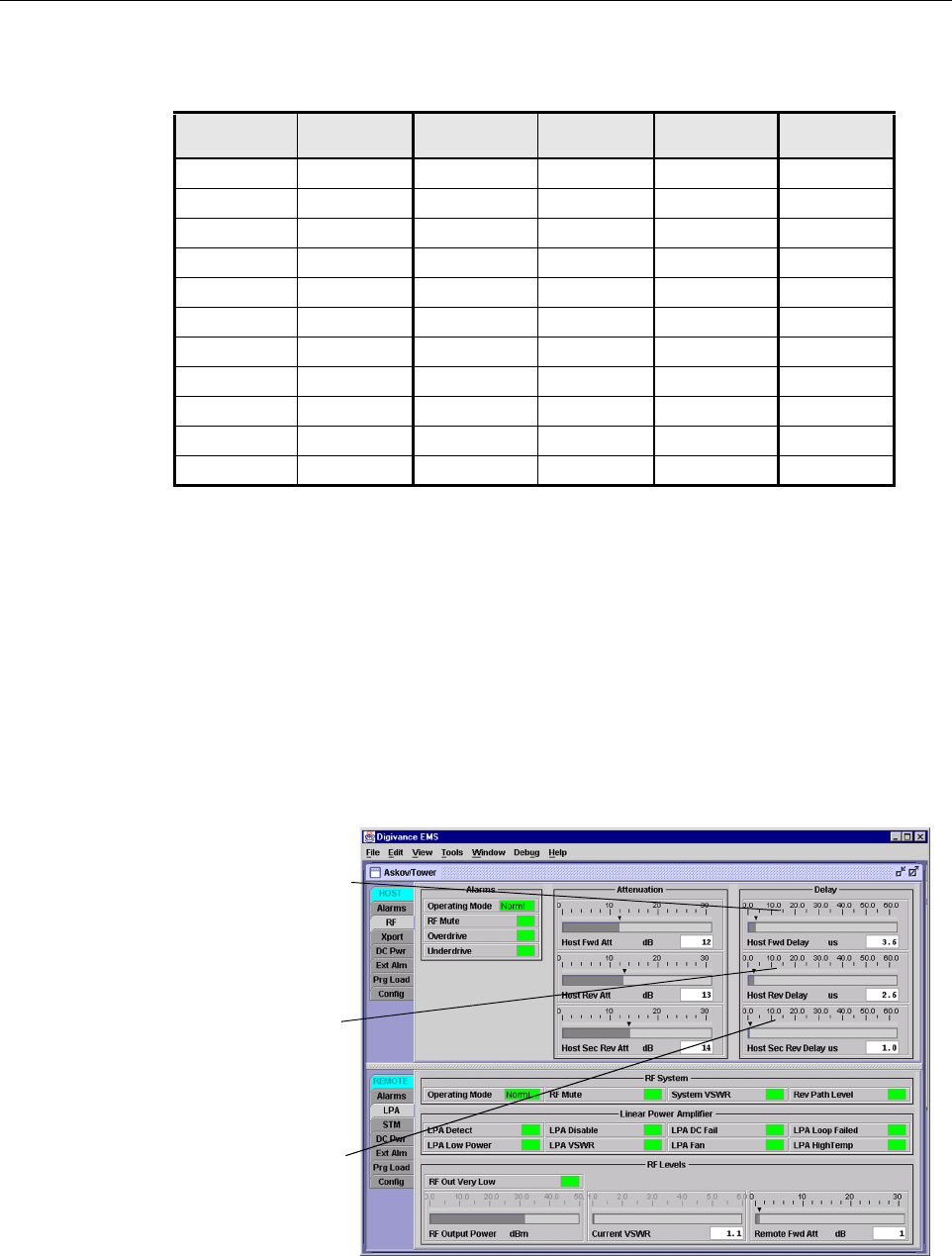
ADCP-75-150 • Preliminary Issue A • March 2003 • Section 4: Operation
Page 4-17
©2003, ADC Telecommunications, Inc.
2.9 Enter Host Forward and Reverse Delay
The forward and reverse delay function allows entry of from 0to 63 µsec of delay in the
forward and reverse paths. This feature is used when multiple systems are used to transport the
same channel and there is asignificant difference in the path delay between systems. Additional
delay may be entered to balance the overall system delay. The amount of delay required must be
calculated by the RF engineer and should be included in the system design plan. The default
setting is 0µsec. Use the following procedure to change the forward and reverse path delay:
1. Click on the HOST RF tab. The HOST RF display will open within the DEMS main
window as shown in Figure 4-14.
Figure 4-14. HOST RF Display
Table 4-2. Reverse Path Attenuation Settings and Nominal Gain Provided
ATTENUATION
SETTING
GAIN
PROVIDED
ATTENUATION
SETTING
GAIN
PROVIDED
ATTENUATION
SETTING
GAIN
PROVIDED
0dB →30 dB 11 dB →19 dB 22 dB →8dB
1dB 29 dB 12 dB 18 dB 23 dB 7 dB
2dB 28 dB 13 dB 17 dB 24 dB 6 dB
3dB 27 dB 14 dB 16 dB 25 dB 5 dB
4dB 26 dB 15 dB 15 dB 26 dB 4 dB
5dB 25 dB 16 dB 14 dB 27 dB 3 dB
6dB 24 dB 17 dB 13 dB 28 dB 2 dB
7dB 23 dB 18 dB 12 dB 29 dB 1 dB
8dB 22 dB 19 dB 11 dB 30 dB 0 dB
9dB 21 dB 20 dB 10 dB -- --
10 dB 20 dB 21 dB 9 dB -- --
Right-click here to
open the Host Fwd
Delay pop-up screen
Right-click here to
open the Host Rev
Delay pop-up screen
Right-click here to
open the Host Div Rev
Delay pop-up screen
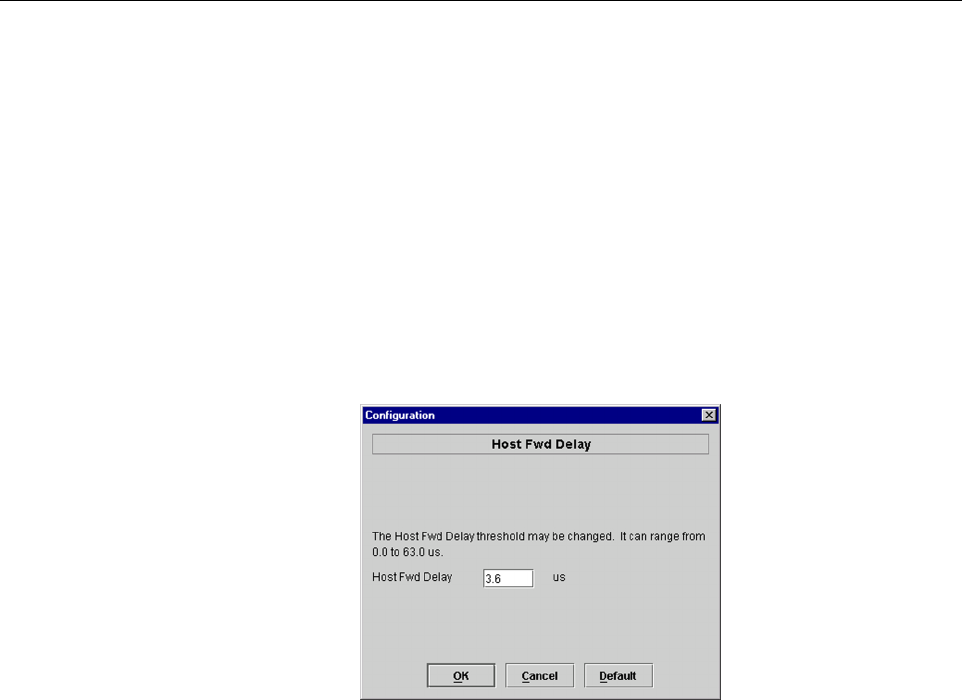
ADCP-75-150 • Preliminary Issue A • March 2003 • Section 4: Operation
Page 4-18
©2003, ADC Telecommunications, Inc.
2. Right-click on the Host Fwd Delay section of the display (see Figure 4-14). The Host
Fwd Delay pop-up screen will open as shown in Figure 4-15.
3. Obtain the value of the forward delay as specified in the system design plan. The delay is
adjustable in 0.1 µsec steps.
4. Enter the forward path delay value and click OK to close the pop-up screen and to make
the changes take effect.
5. Repeat the process for reverse delay and diversity reverse delay by right-clicking on the
appropriate delay section (see Figure 4-14)and then entering the required delay value in
the pop-up screen.
6. Click OK to close each pop-up screen and to make the changes take effect.
Figure 4-15. Host Fwd Delay Pop-Up Screen

ADCP-75-150 • Preliminary Issue A • March 2003 • Section 5: Maintenance
Page 5-1
©2003, ADC Telecommunications, Inc.
SECTION 5: MAINTENANCE
1 SYSTEM MAINTENANCE OVERVIEW . . . . . . . . . . . . . . . . . . . . . . . . . . . . . . . . . . . . . . . . . . . . . . . . . . . . . . . . . .5-1
1.1 Tools and Materials . . . . . . . . . . . . . . . . . . . . . . . . . . . . . . . . . . . . . . . . . . . . . . . . . . . . . . . . . . . . . . .5-1
2 FAULT DETECTION AND ALARM REPORTING. . . . . . . . . . . . . . . . . . . . . . . . . . . . . . . . . . . . . . . . . . . . . . . . . . . .5-2
3 FAULT ISOLATION AND TROUBLESHOOTING. . . . . . . . . . . . . . . . . . . . . . . . . . . . . . . . . . . . . . . . . . . . . . . . . . . .5-5
4 TEST PROCEDURES . . . . . . . . . . . . . . . . . . . . . . . . . . . . . . . . . . . . . . . . . . . . . . . . . . . . . . . . . . . . . . . . . . . . 5-10
4.1 Optical Power Test. . . . . . . . . . . . . . . . . . . . . . . . . . . . . . . . . . . . . . . . . . . . . . . . . . . . . . . . . . . . . . . 5-10
4.2 Optical Loopback Test . . . . . . . . . . . . . . . . . . . . . . . . . . . . . . . . . . . . . . . . . . . . . . . . . . . . . . . . . . . . 5-12
5 MAINTENANCE PROCEDURES . . . . . . . . . . . . . . . . . . . . . . . . . . . . . . . . . . . . . . . . . . . . . . . . . . . . . . . . . . . . . 5-13
5.1 Scheduled Maintenance . . . . . . . . . . . . . . . . . . . . . . . . . . . . . . . . . . . . . . . . . . . . . . . . . . . . . . . . . . . 5-13
5.2 Remote Unit Outdoor Cabinet Filters Cleaning Procedure . . . . . . . . . . . . . . . . . . . . . . . . . . . . . . . . . . . .5-14
5.3 Host Unit Fan Replacement Procedure . . . . . . . . . . . . . . . . . . . . . . . . . . . . . . . . . . . . . . . . . . . . . . . . . 5-15
5.4 Spectrum Transport Module Fan Replacement Procedure . . . . . . . . . . . . . . . . . . . . . . . . . . . . . . . . . . . . 5-16
5.5 Linear Power Amplifier Fan Replacement Procedure . . . . . . . . . . . . . . . . . . . . . . . . . . . . . . . . . . . . . . .5-19
_________________________________________________________________________________________________________
1 SYSTEM MAINTENANCE OVERVIEW
This section explains the Digivance system fault detection and alarm reporting system, provides
amethod for isolating and troubleshooting faults, and provides test and maintenance
procedures. The Digivance system requires minimal regular maintenance to insure continuous
and satisfactory operation. Components that require regular replacement, cleaning, or testing
include the HU and RU fans and the RU outdoor cabinet air-filters.
Maintenance also includes diagnosing and correcting service problems as they occur. When an
alarm is reported, it will be necessary to follow asystematic troubleshooting procedure to locate
the problem. Once the source of the problem is isolated, the appropriate corrective action can be
taken to restore service. The only internal components that can be replaced are the cooling fans
which mount in the HU, RU, and LPA. The failure of any other component within aunit will
required replacement of that unit.
1.1 Tools and Materials
The following tools and materials are required in order to complete the procedures in this
section:
•ESDwrist strap
•IRfiltering safety glasses
• Patch cords with SC connectors
•15dB in-line SC optical attenuators
•Opticalpower meter (1550 and 1310 nm)
•TORXscrewdriver (with T10 bit)

ADCP-75-150 • Preliminary Issue A • March 2003 • Section 5: Maintenance
Page 5-2
©2003, ADC Telecommunications, Inc.
2 FAULT DETECTION AND ALARM REPORTING
The Digivance system on-board embedded software detects various unit and system faults and
reports them as either Major or Minor alarms. AMajor alarm indicates that the system has
failed in away that directly affects RF transport performance. This usually means that some
calls or perhaps all calls cannot be made over the system. AMinor alarm means that system
performance is not affected or in some cases, that the performance may no longer be optimal.
Four types of faults cause aminor alarm to be reported: overtemperature, fan failure, diversity
path failure, and an external minor fault (user defined fault). All other faults are reported as a
Major alarm.
Reporting of Major and Minor alarms is accomplished through the HU alarm contacts, the unit
front panel LED’s, the DEMS software Graphical User Interface (GUI), and the Network
Operations Center -Network Element Manager (NOC/NEM) interface.
The HU is equipped with aset of both normally open (NO) and normally closed (NC) alarm
contacts which are used to report both Major and Minor alarms to an external alarm system. The
alarm contacts summarize the inputs so that any Major or Minor alarm will trigger an alarm
report to the external alarm system.
The HU, STM, and LPA front panel LED indicators are used to report specific alarms which are
reflected in the LED colors: Green, Red, Yellow, and Off. Adescription of the Host Unit, Linear
Power Amplifier, and Spectrum Transport Module LED indicators is provided respectively in
Table 5-1,Table 5-2,and Table 5-3.
The DEMS software GUI provides both asummary and amore detailed list of alarm
information that includes unit and module level faults, circuit faults, and measured value faults
such as voltages, RF power, and temperature. Asummary showing alist of all systems and their
current alarm status is presented through the Alarm OverView display. Adetailed list of alarm
information is presented through the HOST alarm display and the REMOTE alarm display. All
the inputs that the system reports as alarms are shown in the HOST and REMOTE alarm
displays.
The NOC/NEM interface provides the same summary and detailed list of alarm information as
the DEMS software GUI but in an ASCII text string format. Sending the command GET
ALARM SUMMARY produces alist of all systems and their current alarm status. Sending the
command GET ALARM ALL for aspecific system will produce adetailed list of alarm
information for the specified system.
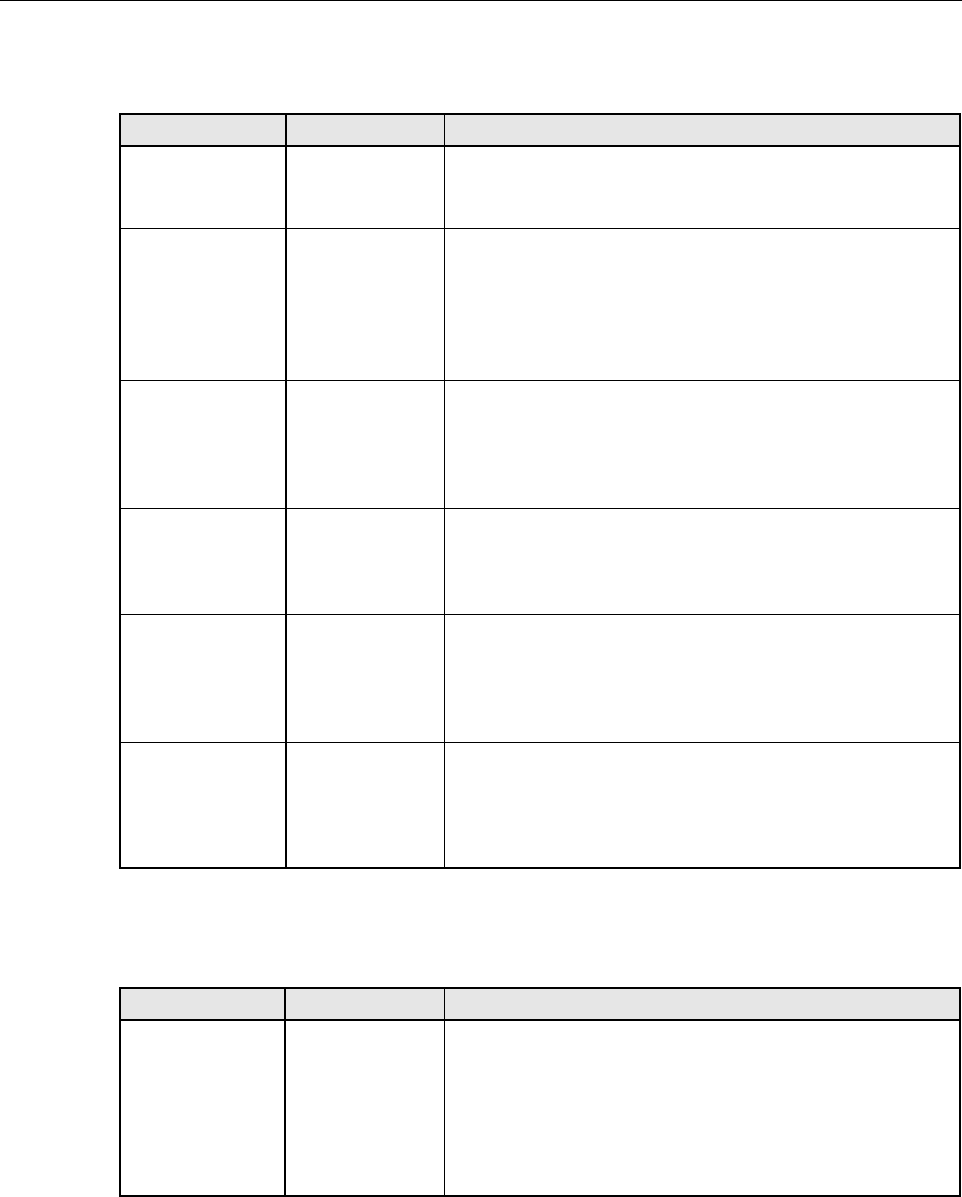
ADCP-75-150 • Preliminary Issue A • March 2003 • Section 5: Maintenance
Page 5-3
©2003, ADC Telecommunications, Inc.
Table 5-1. Host Unit LED Indicators
INDICATOR COLOR DESCRIPTION
POWER
Green
Off
Indicates if the HU is powered or un-powered.
The DC power source is on.
The DC power source is off.
STANDBY
Green (blinking)
Yellow (blinking)
Red (blinking)
Off
Indicates if the system is in the standby, normal, test, or
program load mode.
The HU is in the standby mode.
The HU is in the program load mode.
The HU is in the test mode.
The HU is in the normal mode.
HOST UNIT
Green
Yellow
Red
Indicates if the HU is normal, over temperature, or if a
fault is detected.
The HU is normal.
High temperature detected in HU.
Fault detected by the HU or HU/RU band mismatch.
REMOTE UNIT
Green
Yellow
Red
Indicates if an alarm is detected at the RU.
No alarms detected at the RU.
Aminor alarm is detected at the RU.
Amajor alarm is detected at the RU.
DRIVE
Green
Yellow
Red
Indicates if the forward path RF signal level is normal,
above overdrive threshold, or below underdrive threshold.
The RF signal level is normal
The RF signal level is below the underdrive threshold.
The RF signal level is above the overdrive threshold.
PORT 1/PORT 2
Green
Red
Indicates if the reverse path optical signal received from
the RU is normal or if errors are detected.
The reverse path optical signal is normal.
Excessive errors are detected in the reverse path optical signal
or the HU can’t communicate with the STM.
Table 5-2. Linear Power Amplifier LED Indicator
INDICATOR COLOR DESCRIPTION
STATUS
Green (blinking)
Green
Yellow (blinking)
Yellow
Red
Indicates the operational state of the LPA and whether or
not any faults are detected.
The LPA is in the normal state.
The LPA is in aforced shutdown state, no faults detected.
The LPA is in the normal state, minor fault detected.
The LPA is initializing.
The LPA is in an internal shutdown state, major fault detected.
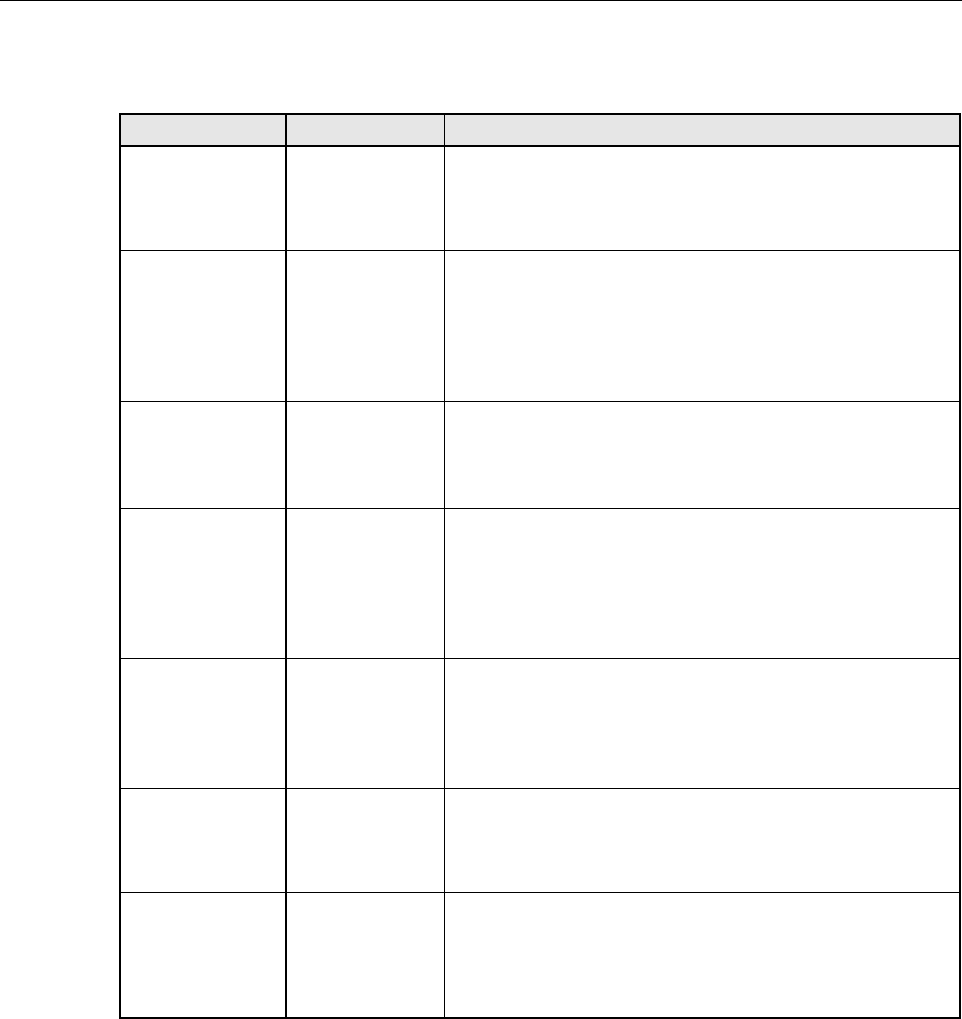
ADCP-75-150 • Preliminary Issue A • March 2003 • Section 5: Maintenance
Page 5-4
©2003, ADC Telecommunications, Inc.
Table 5-3. Spectrum Transport Module LED Indicators
INDICATOR COLOR DESCRIPTION
AC POWER
Green
Red
Indicates if the STM is powered by the AC power source or
the back-up battery system.
The STM is powered by the AC power source.
The STM is powered by the back-up battery system.
STANDBY
Green (blinking)
Yellow (blinking)
Red (blinking)
Off
Indicates if the system is in the standby, normal, test, or
program load mode.
The STM is in the standby mode.
The STM is in the program load mode.
The STM is in the test mode.
The STM is in the normal mode.
HOST UNIT
Green
Yellow
Red
Indicates if an alarm is detected at the HU.
No alarms detected at the HU.
Aminor alarm is detected at the HU.
Amajor alarm is detected at the HU.
STM
Green
Yellow
Red
Indicates if the STM is normal, over temperature, or if a
fault is detected.
The STM is normal.
The STM is over temperature due to high ambient temperature
or the fan has failed.
Fault detected by the STM or HU/RU band mismatch.
PA
Green
Yellow
Red
Indicates if the LPA is normal, over temperature, has afan
failure, or is faulty.
The LPA is normal.
The LPA is over temperature or the fan has failed.
Internal fault detected in the LPA.
VSWR
Green
Red
Indicates if the forward path VSWR is above or below the
threshold.
The VSWR is below the threshold.
The VSWR is above the threshold.
PORT 1/PORT 2
Green
Red
Indicates if the forward path optical signal received from
the HU is normal or if errors are detected.
The forward path optical signal is normal.
Excessive errors are detected in the forward path optical signal
or the STM can’t communicate with the HU.
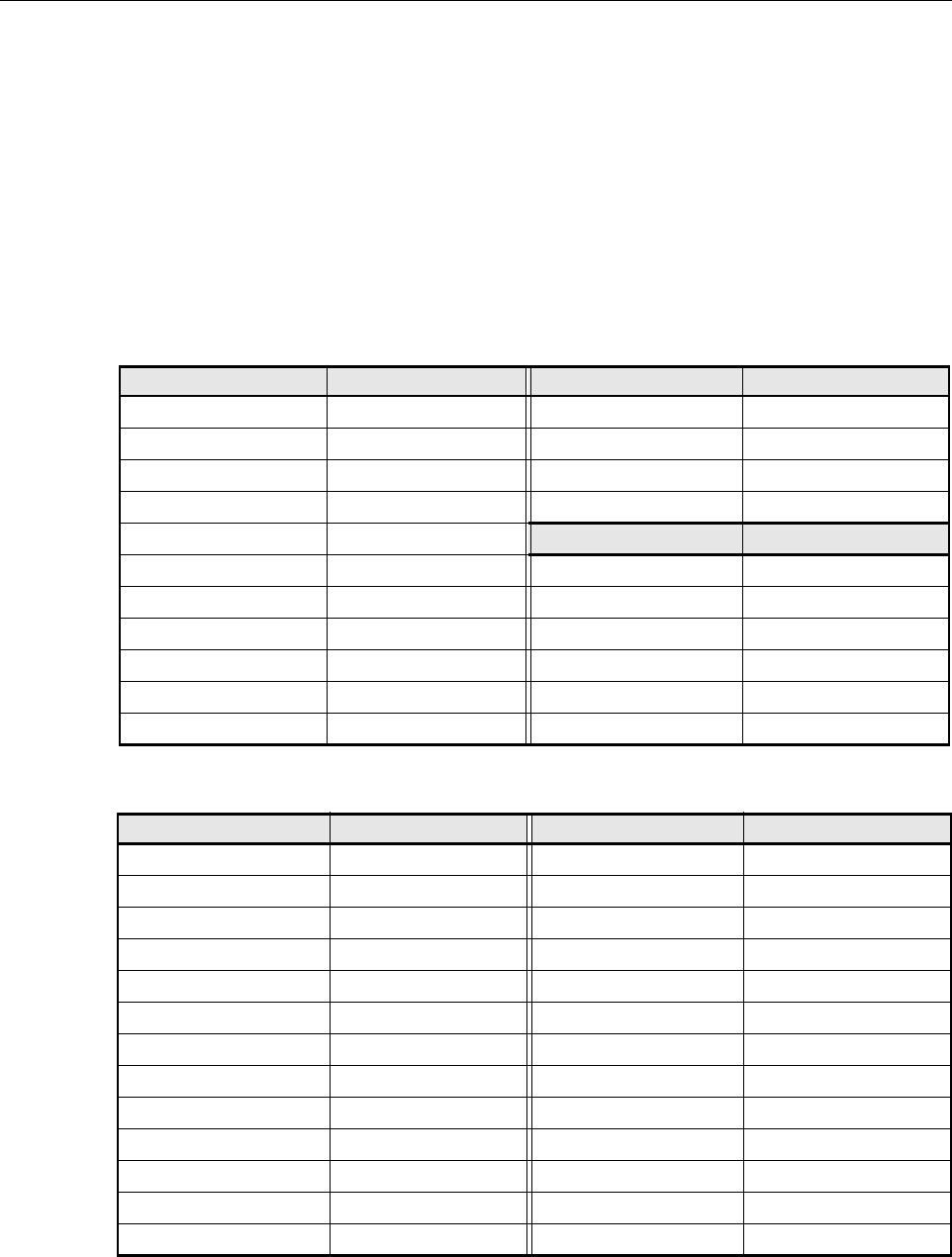
ADCP-75-150 • Preliminary Issue A • March 2003 • Section 5: Maintenance
Page 5-5
©2003, ADC Telecommunications, Inc.
3 FAULT ISOLATION AND TROUBLESHOOTING
Alarm information may be accessed and faults isolated using the information provided by the
unit front panel LED indicators, the DEMS software GUI alarm displays, or the NOC-EMS
interface. Because the alarm information provided by the DEMS GUI and the NOC-EMS
interface is very detailed, refer to Table 5-4,Table 5-5,or Table 5-6 to determine the unit LED
indicator (Host Unit, Remote Unit, or LPA) that corresponds to the indicated alarm. Then refer
to Table 5-7,Table 5-8,or Table 5-9 to identify the problem, check out the possible causes, and
take corrective action.
Table 5-4. Host Unit Major and Minor Alarms
MAJOR ALARM LED INDICATOR MAJOR ALARM LED INDICATOR
Operating Mode (Does not apply) Fwd Synth Lock HOST UNIT
8Volt HOST UNIT RF Mute (Does not apply)
Pri No Light (Not implemented) Major Extern Output (Does not apply)
Pri Fwd Mux Lock HOST UNIT Companion Lost PORT 1/PORT 2
Pri Rev Synth Lock HOST UNIT MINOR ALARMS LED INDICATOR
Overdrive DRIVE Temperature HOST UNIT
Unit Mismatch HOST UNIT Sec No Light (Does not apply)
Link Alarm (Does not apply) Sec Errors (Does not apply)
3.8 Volt HOST UNIT Sec Rev Synth Lock HOST UNIT
Pri Laser Fail HOST UNIT Underdrive DRIVE
Pri Errors PORT 1/PORT 2MinorExtern Output (Does not apply)
Table 5-5. Remote Unit Major Alarms
MAJOR ALARM LED INDICATOR MAJOR ALARM LED INDICATOR
Operating Mode (Does not apply) Battery Vo l t a g e ( D o es not apply)
3.8 Volt STM Pri Laser Fail STM
Pri Errors PORT 1/PORT 2FwdSynth Lock STM
Reference Synth Lock STM System VSWR VSWR
LPA DC Fail PA LPA Low Power PA
LPA VSWR PA Unit Mismatch STM
Link Alarm (Does not apply) Converter STM
AC Fail AC POWER Pri No Light PORT 1/PORT 2
8Volt STM Pri Rev Synth Lock STM
Pri Rev Mux Lock STM LPA Detect PA
RF Mute (Does not apply) LPA Over Power PA
LPA Loop Failed PA Companion Lost PORT 1/PORT 2
Major Extern Alarm Inp (Does not apply) – –
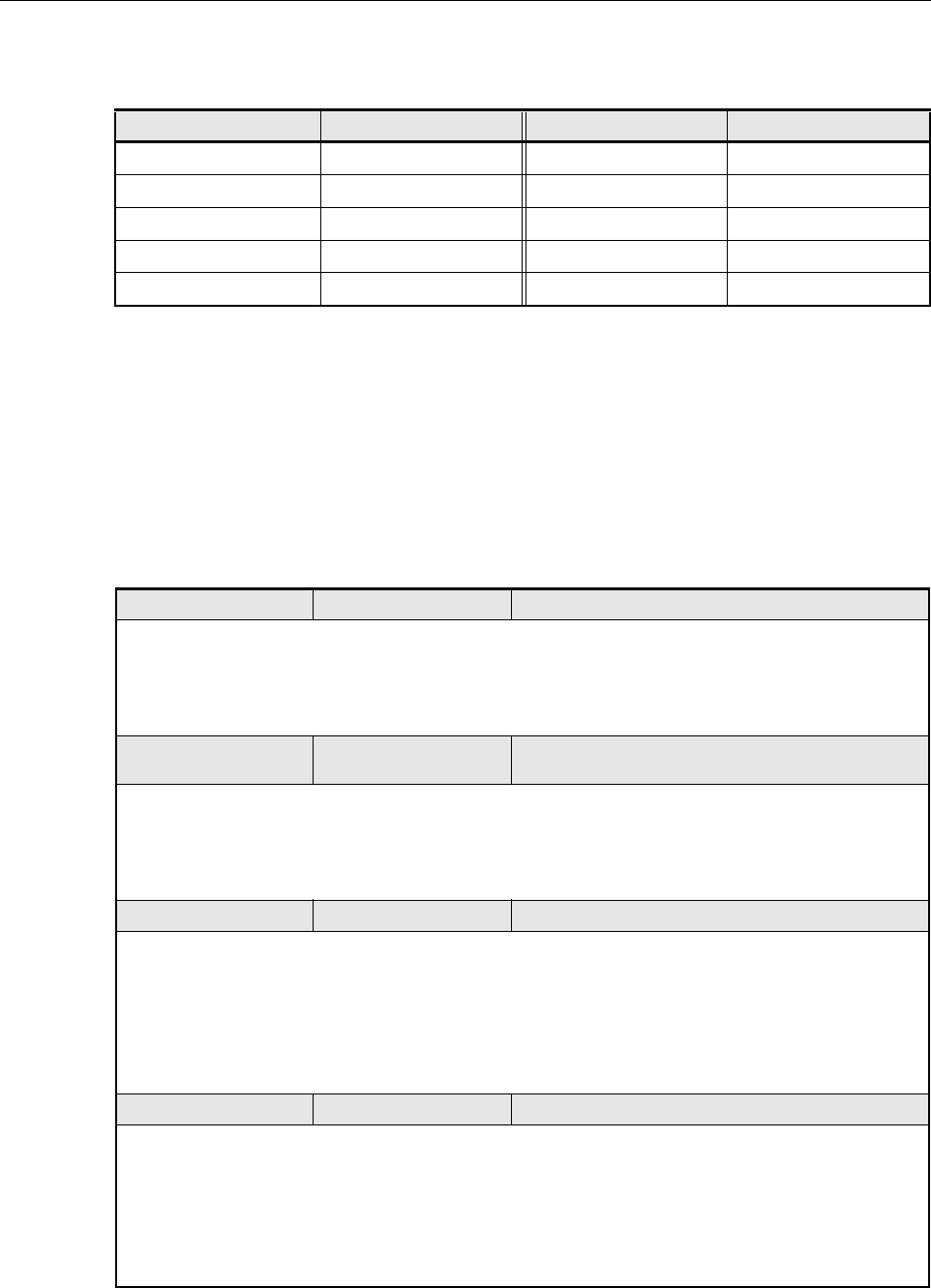
ADCP-75-150 • Preliminary Issue A • March 2003 • Section 5: Maintenance
Page 5-6
©2003, ADC Telecommunications, Inc.
During normal HU operation, all LED’s should be green except the STANDBY LED which
should be Off.When aMinor alarm occurs, one or more of the LED’s will turn yellow.When a
Major alarm occurs, one or more of the LED’s will turn red.
It is recommended that whenever there are multiple alarms, the optical alarms should be
checked and cleared first. Because the host and remote units function as asystem, afault in the
fiber optic link will cause various unit alarms to be reported.
Table 5-6. Remote Unit Minor Alarms
MINOR ALARM LED INDICATOR MINOR ALARM LED INDICATOR
Temperature STM Sec Laser Fail (Does not apply)
Sec Rev Mux Lock (Does not apply) Sec Rev Synth Lock (Does not apply)
Rev Path Level (Does not apply) LPA Disable STATUS (LPA)
LPA Fan PA LPA High Temp PA
Minor Extern Alarm Inp (Does not apply) RF Out Ve ry Low (Does not apply)
Table 5-7. Host Unit Fault Isolation and Troubleshooting
LED: POWER Color: Off Alarm Type: Major
PROBLEM: The HU is not powered.
POSSIBLE CAUSE CORRECTIVE ACTION/COMMENTS
1. The fuse is open or removed from the fuse
panel. 1. Replace or reinstall fuse at fuse panel.
LED: STANDBY Color: Green (blinking) or
Yellow (blinking)
Alarm Type: None
PROBLEM: The HU is out of service.
POSSIBLE CAUSE CORRECTIVE ACTION/COMMENTS
1. The HU is in the standby (green) or program
load (yellow) mode. 1. Use DEMS to place the HU in the normal (off)
mode.
LED: HOST UNIT Color: Yellow Alarm Type: Minor
PROBLEM: The HU is overheating.
POSSIBLE CAUSE CORRECTIVE ACTION/COMMENTS
1. Air intake or exhaust opening to HU chassis
is blocked
2. Ambient temperature >> 50º C/122º F.
3. Faulty fan.
1. Remove cause of air-flow blockage.
2. Reduce ambient temperature.
3. Replace HU fan (See Section 5.3).
LED: HOST UNIT Color: Red Alarm Type: Major
PROBLEM: A major alarm fault detected by HU.
POSSIBLE CAUSE CORRECTIVE ACTION/COMMENTS
1. Fiber optic link fault.
2. HU and STM band mismatch.
3. The HU has failed.
1. Follow procedure specified when the PORT 1/
PORT 2LED is red.
2. Replace HU or STM with correct unit.
3. Replace the HU.

ADCP-75-150 • Preliminary Issue A • March 2003 • Section 5: Maintenance
Page 5-7
©2003, ADC Telecommunications, Inc.
LED: REMOTE UNIT Color: Yellow Alarm Type: Minor
PROBLEM: A minor alarm fault is detected at the RU.
POSSIBLE CAUSE CORRECTIVE ACTION/COMMENTS
1. The STM or LPA is overheating. 1. Check RU LED indicators and refer to Table 5-8
LED: REMOTE UNIT Color: Red Alarm Type: Major
PROBLEM: A major alarm fault is detected at the RU.
POSSIBLE CAUSE CORRECTIVE ACTION/COMMENTS
1. Fiber optic link fault.
2. AC power failure at RU.
3. High VSWR.
4. The RU cabinet door is open or the STM or
LPA has failed.
1. Check RU LED indicators and refer to Table 5-8.
2. Check RU LED indicators and refer to Table 5-8.
3. Check RU LED indicators and refer to Table 5-8.
4. Check RU LED indicators and refer to Table 5-8.
LED: DRIVE Color: Yellow Alarm Type: Minor
PROBLEM: The RF input signal level is below the underdrive threshold.
POSSIBLE CAUSE CORRECTIVE ACTION/COMMENTS
1. Faulty BTS or faulty coaxial connection
between the HU and the BTS.
2. Incorrect attenuation in forward path RF coax-
ial link.
1. Check forward path signal level at the HU.
2. Check Host Forward Attenuator setting and
adjust if attenuation is too high.
LED: DRIVE Color: Red Alarm Type: None
PROBLEM: The RF signal is above the overdrive threshold.
POSSIBLE CAUSE CORRECTIVE ACTION/COMMENTS
1. Composite output signal level from BTS is too
high.
2. Incorrect attenuation in forward path RF
coaxial link.
1. Check BTS composite output signal level and
adjust if too high.
2. Check Forward Attenuator setting and adjust if
attenuation is too low.
LED: PORT 1/PORT 2 Color: Red Alarm Type: Major
PROBLEM: Excessive errors are detected in the reverse path optical signal.
POSSIBLE CAUSE CORRECTIVE ACTION/COMMENTS
1. Faulty reverse path optical fiber.
2. Faulty optical transmit port at the STM or
faulty optical receive port at the HU
1. Test optical fiber. Clean connector if dirty. Repair
or replace optical fiber if faulty. (See Section 4.1).
2. Test optical ports. Replace HU or STM if port is
faulty (See Section 4.2).
Table 5-7. Host Unit Fault Isolation and Troubleshooting, continued
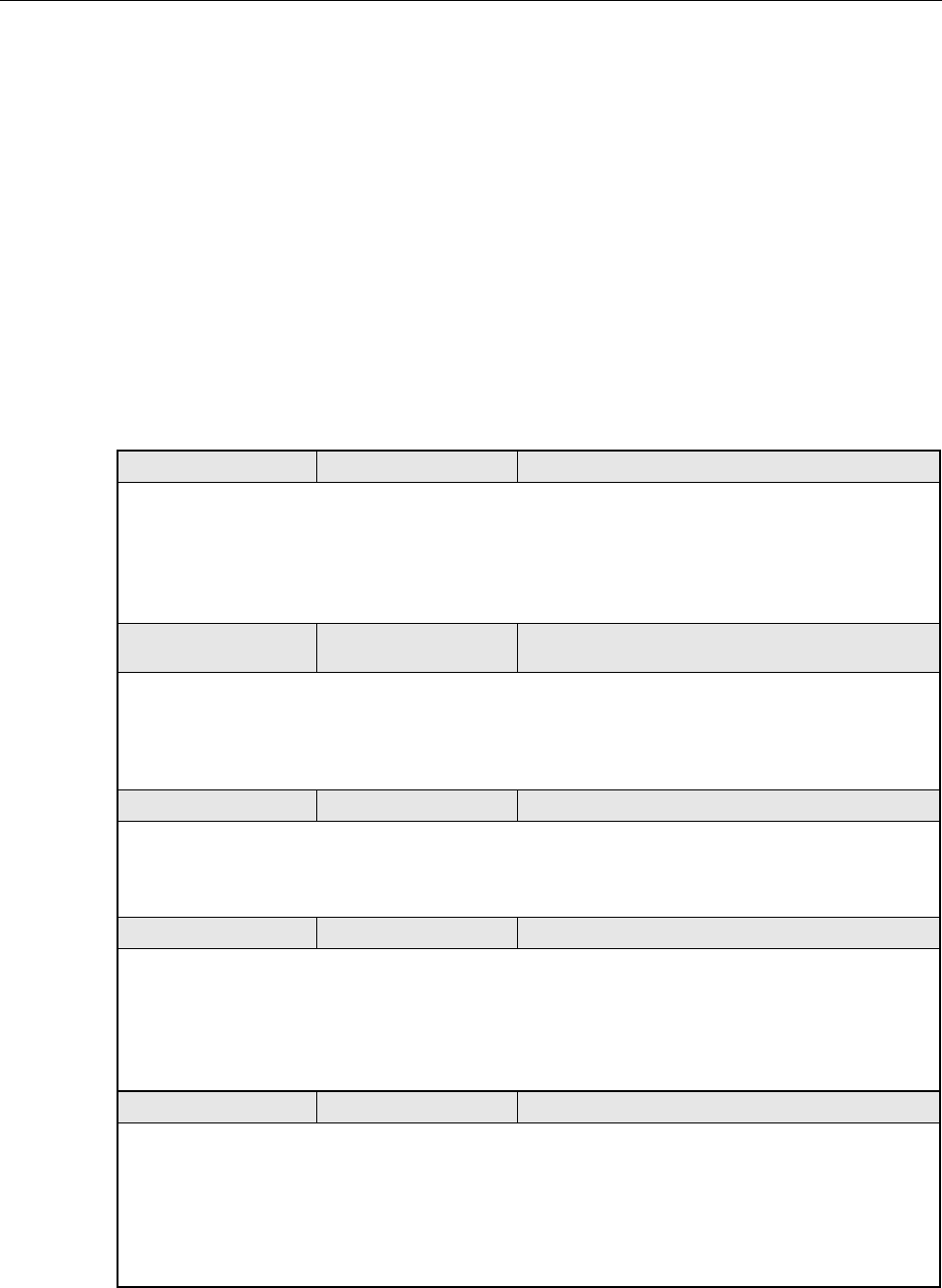
ADCP-75-150 • Preliminary Issue A • March 2003 • Section 5: Maintenance
Page 5-8
©2003, ADC Telecommunications, Inc.
During normal STM operation, all LED’s should be green except the STANDBY LED which
should be Off.When aMinor alarm occurs, one or more of the LED’s will turn yellow.When a
Major alarm occurs, one or more of the LED’s will turn red.
It is recommended that whenever there are multiple alarms, the optical alarms should be
checked and cleared first. Because the host and remote units function as asystem, afault in the
fiber optic link will cause various unit alarms to be reported.
Table 5-8. STM Fault Isolation and Troubleshooting
LED: AC POWER Color: Off Alarm Type: Major
PROBLEM: The RU is powered by the battery back-up system.
POSSIBLE CAUSE CORRECTIVE ACTION/COMMENTS
1. The AC power system circuit breaker is open
or the AC power has failed.
2. The STM has failed.
1. Check the AC power system, repair as needed,
and reset circuit breaker.
2. Replace the STM.
LED: STANDBY Color: Green (blinking) or
Yellow (blinking)
Alarm Type: None
PROBLEM: The RU is out of service.
POSSIBLE CAUSE CORRECTIVE ACTION/COMMENTS
1. The RU is in the standby (green) or program
load (yellow) mode. 1. Use DEMS to place the RU in the normal (off)
mode.
LED: HOST UNIT Color: Yellow Alarm Type: Minor
Problem: A minor alarm fault is detected at the HU.
POSSIBLE CAUSE CORRECTIVE ACTION/COMMENTS
1. The HU is overheating. 1. Check HU LED indicators and refer to Table 5-7
LED: HOST UNIT Color: Red Alarm Type: Major
PROBLEM: A major alarm fault is detected at the HU.
POSSIBLE CAUSE CORRECTIVE ACTION/COMMENTS
1. Fiber optic link fault.
2. The HU is not powered.
3. The HU has failed.
1. Check HU LED indicators and refer to Table 5-7.
2. Check HU LED indicators and refer to Table 5-7.
3. Check HU LED indicators and refer to Table 5-7.
LED: STM Color: Yellow Alarm: Minor
PROBLEM: The STM is overheating.
POSSIBLE CAUSE CORRECTIVE ACTION/COMMENTS
1. Air intake or exhaust opening to the remote
unit cabinet is blocked
2. Ambient temperature >> 50º C/122º F.
3. Faulty fan.
1. Remove cause of air-flow blockage.
2. Reduce ambient temperature.
3. Replace STM fan (See Section 5.4).
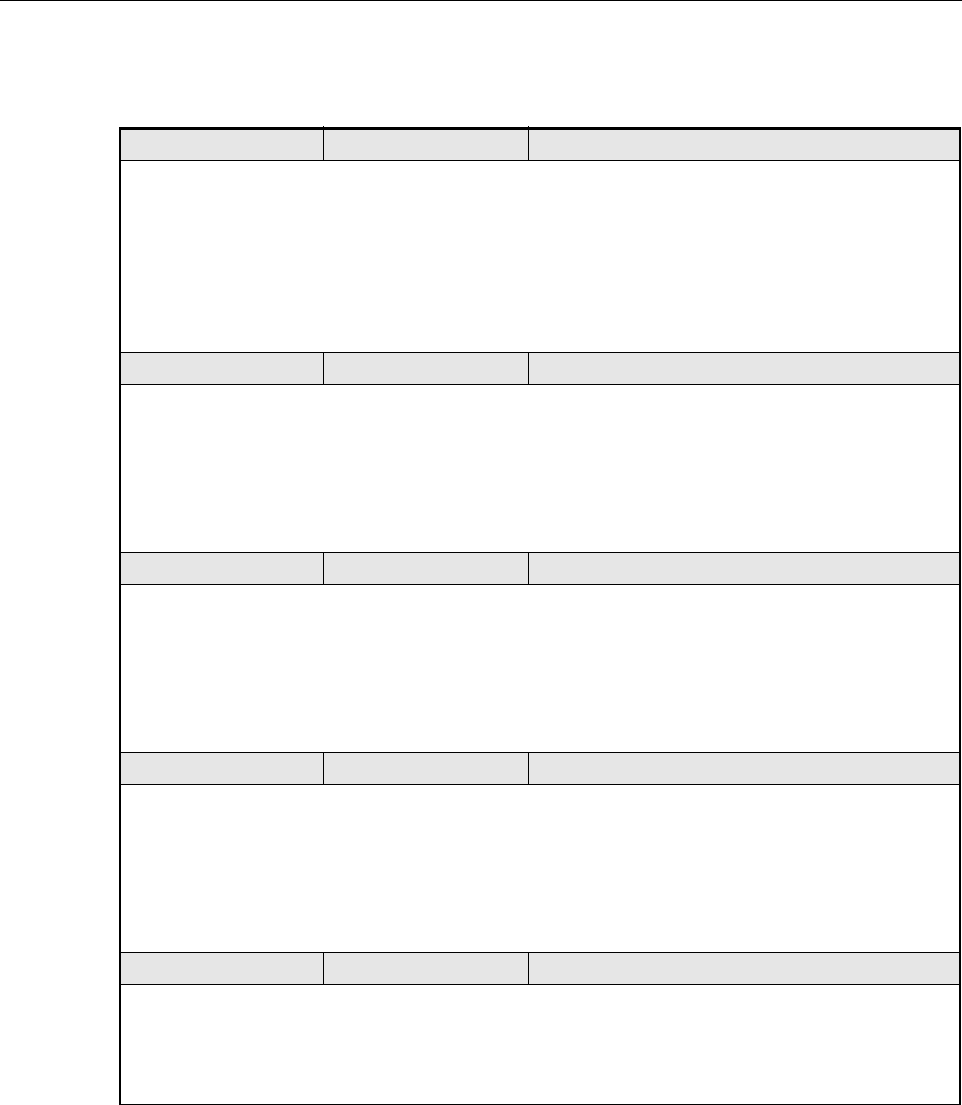
ADCP-75-150 • Preliminary Issue A • March 2003 • Section 5: Maintenance
Page 5-9
©2003, ADC Telecommunications, Inc.
LED: STM Color: Red Alarm Type: Major
PROBLEM: A major alarm fault detected by the STM.
POSSIBLE CAUSE CORRECTIVE ACTION/COMMENTS
1. Fiber optic link fault.
2. The HU is not powered.
3. HU and STM band mismatch.
4. The STM has failed.
1. Follow procedure specified when the PORT 1/
PORT 2LED is red.
2. Check HU LED indicators and refer to Table 5-7
3. Replace HU or STM with correct unit.
4. Replace the STM.
LED: PA Color: Yellow Alarm Type: Minor
PROBLEM: The LPA is overheating.
POSSIBLE CAUSE CORRECTIVE ACTION/COMMENTS
1. Air intake or exhaust opening to the remote
unit cabinet is blocked
2. Ambient temperature >50º C/122º F.
3. Faulty fan.
1. Remove cause of air-flow blockage.
2. Reduce ambient temperature.
3. Replace LPA fan (See Section 5.5).
LED: PA Color: Red Alarm Type: Major
PROBLEM: A major alarm fault is detected by the LPA.
POSSIBLE CAUSE CORRECTIVE ACTION/COMMENTS
1. The STM to LPA connecting cable is faulty.
2. The LPA has failed.
3. The STM has failed.
1. Inspect cable and repair or replace if faulty.
2. Check LPA and refer to Table 5-9.Replace the
LPA if it is faulty.
3. Replace the STM.
LED: VSWR Color: Red Alarm Type: Major
PROBLEM: The forward path VSWR is above the threshold.
POSSIBLE CAUSE CORRECTIVE ACTION/COMMENTS
1. Faulty antenna or antenna system.
2. Faulty antenna cable.
3. The STM has failed.
1. Check the antenna circuit for shorts or opens
(including lightning protector).
2. Check the antenna cable for faulty connections.
3. Replace the STM.
LED: PORT 1/PORT 2 Color: Red Alarm Type: Major
PROBLEM: Excessive errors are detected in the forward path optical signal.
POSSIBLE CAUSE CORRECTIVE ACTION/COMMENTS
1. Faulty forward path optical fiber. 1. Test optical fiber. Clean connector if dirty. Repair
or replace optical fiber if faulty. (See Section 4.1).
Table 5-8. STM Fault Isolation and Troubleshooting, continued
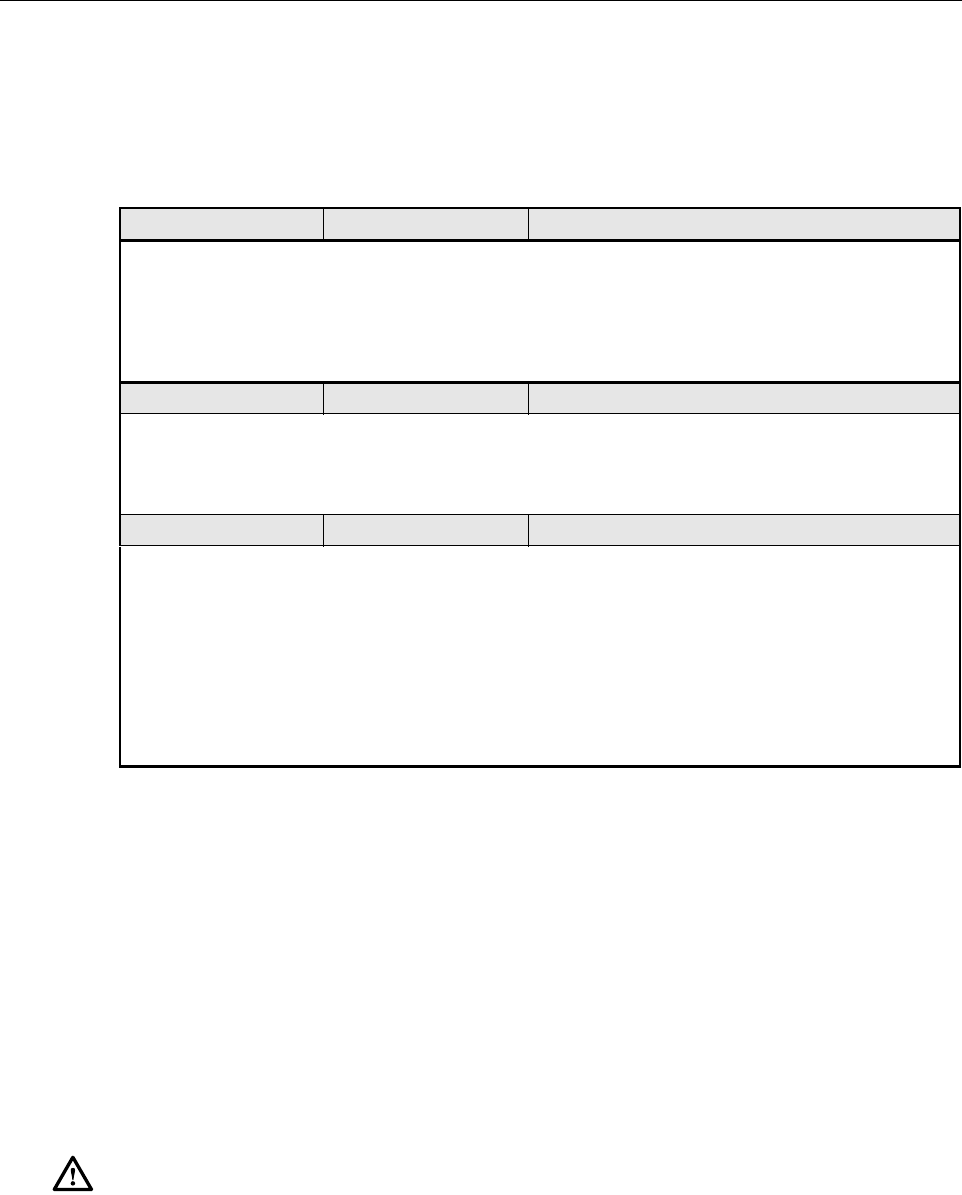
ADCP-75-150 • Preliminary Issue A • March 2003 • Section 5: Maintenance
Page 5-10
©2003, ADC Telecommunications, Inc.
During normal LPA operation, the STATUS LED should be blinking green (normal operation)
or blinking yellow (minor fault).
4 TEST PROCEDURES
This section provides procedures for common troubleshooting and maintenance tests. Refer to
these procedures as needed when specified in the Fault Isolation and Troubleshooting tables in
Section 3.
4.1 Optical Power Test
Abreak in an optical fiber or afault with the optical connector will interrupt communications
between linked components or generate excessive errors. Use the following procedure to isolate
aproblem with an optical fiber or connector.
Table 5-9. LPA Fault Isolation and Troubleshooting
LED: STATUS Color: Green Alarm Type: None
PROBLEM: The LPA is in the forced shutdown state.
POSSIBLE CAUSES
1.The MUTE/NORM/RESET switch is in the
MUTE position or the LPA was set in the dis
-able mode through the DEMS computer.
1.Place MUTE/NORM/RESET switch in the
NORM position or use DEMS to enable the LPA.
LED: STATUS Color: Yellow (blinking) Alarm Type: Minor
PROBLEM: The LPA detects a minor fault.
POSSIBLE CAUSE CORRECTIVE ACTION/COMMENTS
1. The LPA fan has failed. 1. Replace LPA fan. (see Section 5.5)
LED: STATUS Color: Red Alarm Type: Major
PROBLEM: The LPA is in a forced shutdown state.
POSSIBLE CAUSE CORRECTIVE ACTION/COMMENTS
1. The STM to LPA connecting cable is faulty.
2. The LPA fan has failed allowing overheating.
3. Air intake or exhaust opening to the remote
unit outdoor cabinet is blocked.
4. Ambient temperature >50º C/122º F.
5. The LPA is faulty.
1. Inspect cable and repair or replace if faulty.
2. Replace LPA fan. (see Section 5.5)
3. Remove cause of air-flow blockage.
4. Reduce ambient temperature
5. Replace LPA.
Danger: This equipment uses aClass 1Laser according to FDA/CDRH rules. Laser radiation
can seriously damage the retina of the eye. Do not look into the ends of any optical fiber. Do not
look directly into the optical transmitter of any unit or exposure to laser radiation may result.
An optical power meter should be used to verify active fibers. Aprotective cap or hood MUST
be immediately placed over any radiating transmitter or optical fiber connector to avoid the
potential of dangerous amounts of radiation exposure. This practice also prevents dirt particles
from entering the connector.
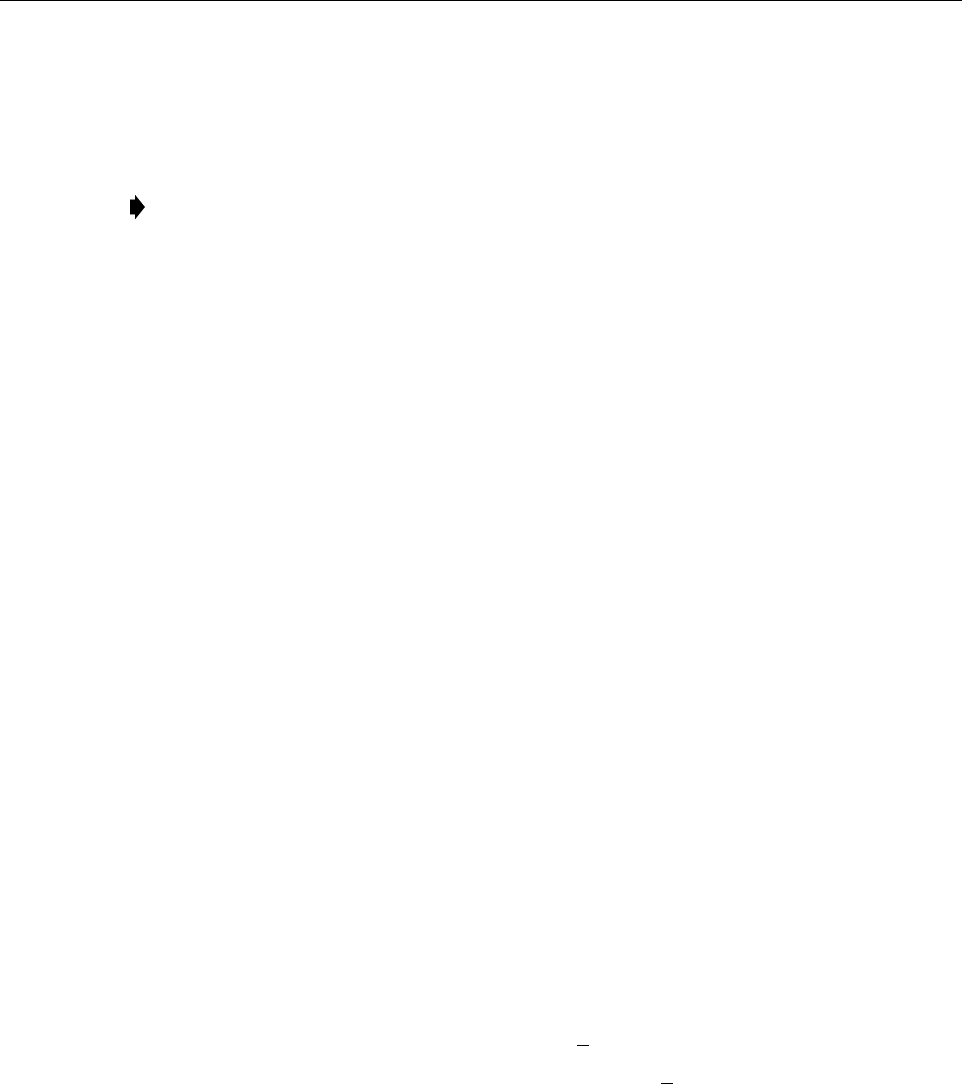
ADCP-75-150 • Preliminary Issue A • March 2003 • Section 5: Maintenance
Page 5-11
©2003, ADC Telecommunications, Inc.
1. Put on the IR filtering safety glasses.
2. Notify the NOC or alarm monitoring system operator that the system is going offline.
3. At the HU and at the STM, place the On/Off switches in the OFF position (press O).
4. Disconnect the optical fiber connectors for the fiber to be tested at the HU and the STM.
5. Inspect the optical connectors. Verify that connectors are clean and that no scratches or
imperfections are visible on the fiber end. Clean and polish the optical connectors if necessary.
6. Connect the optical power meter to the output (receiver) end of the optical fiber. If an
attenuator was included in the fiber link, make sure the attenuator is installed.
7. Connect the input (transmitter) end of the optical fiber to the far end HU or STM.
8. At the far end HU or STM, place the On/Off switch in the ON position (press I).
9. Using the far end HU or STM as an optical light source, measure the optical power at the
near end of the optical fiber. The power level of the optical input signal at the HU or STM
must fall within the following ranges:
STM Forward Path Input Signal (Port 1): –15 to –25 dBm (with attenuator installed)
HU Reverse Path Input Signal (Port 2): –15 to –23 dBm (with attenuator installed)
If the power level of the received optical signal is within the specified range, the optical
fiber and the far end unit are good. If the power level of the received signal is not with
the specified range, either the optical fiber is faulty or the far end unit optical transmitter
is faulty. Continue with test procedure to isolate the problem
10. At the far end HU or STM, place the On/Off switch in the OFF position (press O).
11. Disconnect the optical power meter from the near end of the optical fiber.
12. Connect the optical power meter to the far end HU (Port 1) or STM (Port 2).
13. At the far end HU or STM, place the On/Off switch in the ON position (press I).
14. Measure the optical output power of the far end HU or STM. The power level of the
optical output signal from the HU or STM must meet the following specification:
HU Forward Path Output Signal (Port 1): 0 + 1dBm
STM Reverse Path Output Signal (Ports 2and 3): +2 +1dBm
If the power level of the optical output signal is within specifications, the optical fiber is
faulty. If the power level of the optical signal is not within specifications, the far end
HU or STM optical transmitter is faulty.
15. At the far end HU or STM, place the On/Off switch in the OFF position (press O).
16. Disconnect the optical power meter from the far end HU or STM.
17. Reconnect the optical fibers at the HU and the STM.
Note: Turning off the HU and STM disables the respective lasers which is necessary in
order to safely inspect and clean the optical connectors.
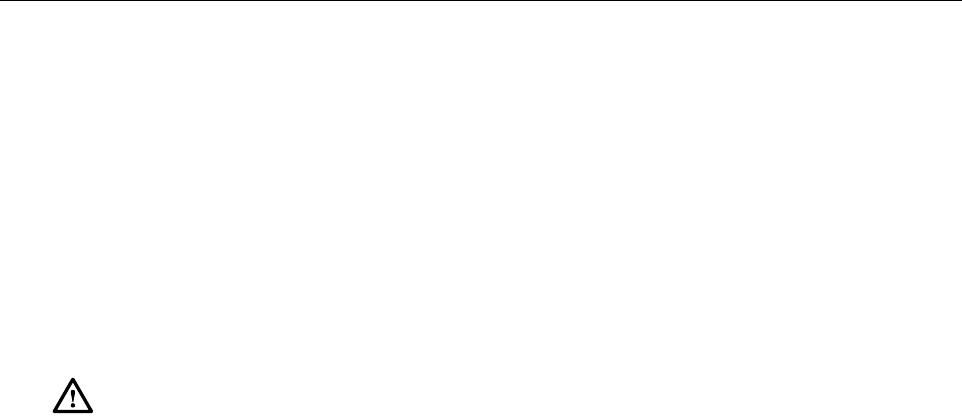
ADCP-75-150 • Preliminary Issue A • March 2003 • Section 5: Maintenance
Page 5-12
©2003, ADC Telecommunications, Inc.
18. Repeat steps 3through 17 for each optical fiber that requires testing.
19. When ready to put the system back into service, place the On/Off switch in the ON
position (press I)at both the HU and STM.
20. Notify the NOC or alarm monitoring service that the system is going back online.
4.2 Optical Loopback Test
The following procedures provide tests to determine if an optical port fault exists with the Host
Unit or with the STM.
4.2.1 Host Loopback Test
1. Put on the IR filtering safety glasses.
2. Notify the NOC or alarm monitoring system operator that the system is going offline.
3. At the HU, place the On/Off switch in the OFF position (press O).
4. Disconnect the optical fiber connectors from the PORT 1and PORT 2optical ports and
place adust cap over each connector.
5. Plug a15 dB in-line optical attenuator into the PORT 1optical port.
6. Connect apatch cord between the optical attenuator and the PORT 2optical port.
7. Place the On/Off switch in the ON position (press I)and observe the PORT 1/PORT 2
LED indicator.
8. The PORT 1/PORT 2LED indicator will turn either red or green. If the LED turns red,
either the PORT 1optical transmitter or the PORT 2receiver is faulty. If the LED turns
green, both PORT 1and PORT 2optical ports are good.
9. Place the On/Off switch in the OFF position (press O).
10. Remove the dust caps from the optical fiber connectors.
11. Clean each connector (follow connector supplier’s recommendations) and then insert each
connector into the appropriate optical port.
12. When ready to put the unit back into service, place the On/Off switch in the ON position
(press I).
13. Notify the NOC or alarm monitoring service that the system is going back online.
Danger: This equipment uses aClass 1Laser according to FDA/CDRH rules. Laser radiation
can seriously damage the retina of the eye. Do not look into the ends of any optical fiber. Do not
look directly into the optical transmitter of any unit or exposure to laser radiation may result.
An optical power meter should be used to verify active fibers. Aprotective cap or hood MUST
be immediately placed over any radiating transmitter or optical fiber connector to avoid the
potential of dangerous amounts of radiation exposure. This practice also prevents dirt particles
from entering the connector.

ADCP-75-150 • Preliminary Issue A • March 2003 • Section 5: Maintenance
Page 5-13
©2003, ADC Telecommunications, Inc.
4.2.2 STM Loopback Test
1. Put on the IR filtering safety glasses.
2. Notify the NOC or alarm monitoring system operator that the system is going offline.
3. At the STM, place the On/Off switch in the OFF position (press O).
4. Disconnect the optical fiber connectors from the PORT 1and PORT 2optical ports and
place adust cap over each connector.
5. Plug a15 dB in-line optical attenuator into the PORT 1optical port.
6. Connect apatch cord between the optical attenuator and the PORT 2optical port.
7. Place the On/Off switch in the ON position (press I)and observe the PORT 1/PORT2 LED
indicator.
8. The PORT 1/PORT 2LED indicator will turn either red or green. If the LED turns red,
either the PORT 1receiver is faulty or the PORT 2transmitter is faulty. If the LED turns
green, both PORT 1and PORT 2optical ports are good.
9. Place the On/Off switch in the OFF position (press O).
10. Remove the dust caps from the optical fiber connectors.
11. Clean each connector (follow connector supplier’s recommendations) and then insert each
connector into the appropriate optical port.
12. When ready to put the unit back into service, place the On/Off switch in the ON position
(press I).
13. Notify the NOC or alarm monitoring service that the system is going back online.
5 MAINTENANCE PROCEDURES
This section specifies the system maintenance requirements and provides the procedures for the
required maintenance tasks. Refer to these procedures as needed when specified in the
Scheduled Maintenance table.
5.1 Scheduled Maintenance
Table 5-10 lists the items that require regular maintenance and the recommended maintenance
interval. Refer to the section specified in the table for the required maintenance or test
procedure.

ADCP-75-150 • Preliminary Issue A • March 2003 • Section 5: Maintenance
Page 5-14
©2003, ADC Telecommunications, Inc.
5.2 Remote Unit Outdoor Cabinet Filters Cleaning Procedure
The RU outdoor cabinet filters clean the RU intake air before it enters the cabinet. The filters
should be cleaned approximately once per year and more often in extremely dirty environments.
If the cabinet temperature gradually rises over along period of time and there are no fan
failures, it is possible that the filter is dirty and requires cleaning. Use the following procedure
to clean the RU outdoor cabinet filters:
1. Open the RU outdoor cabinet door as shown in Figure 5-1.
2. TBD
3. TBD
4. TBD
5. TBD
Figure 5-1. Air Filter Removal and Replacement
Table 5-10. Scheduled Maintenance
INTERVAL ITEM REQUIREMENT
12 months RU outdoor cabinet
filters* Remove and clean the RU outdoor cabinet filters. Refer to
Section 5.2 for the required procedure.
60 months HU Fans
STM Fan
LPA Fan
Remove and replace the cooling fans in the HU, STM, and
LPA. Refer to specified section for the required procedures:
HU see Section 5.3,Section 5.4,and LPA see Section 5.5.
*Though it is not recommended that the RU be installed in asalt-air environment, if done so, clean the
cabinet filter on amonthly basis instead of on a12 month basis. In addition, the RU should be
inspected for corrosion due to salt, particularly near the fans and around the connectors. The MTBF of
the RU may be impacted if the RU is exposed to salt-air.
Drawing not available
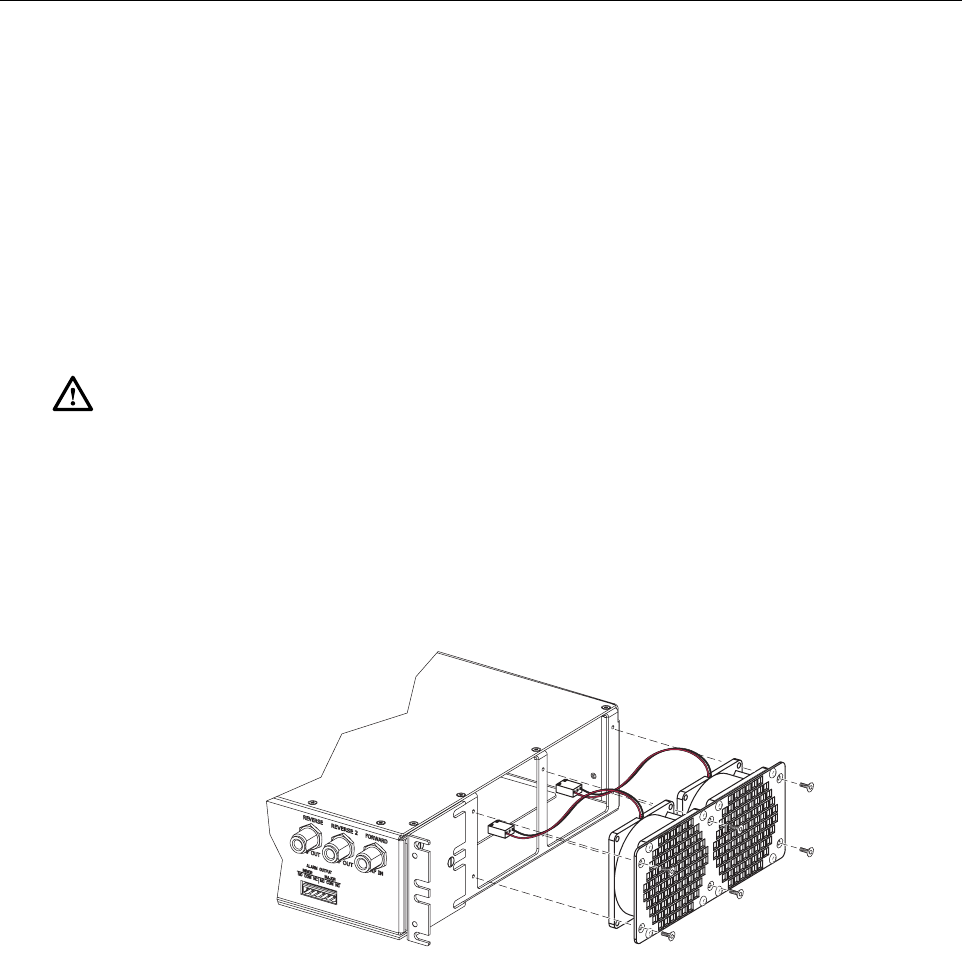
ADCP-75-150 • Preliminary Issue A • March 2003 • Section 5: Maintenance
Page 5-15
©2003, ADC Telecommunications, Inc.
5.3 Host Unit Fan Replacement Procedure
The HU is equipped with two cooling fans which are located on the right side of the HU
enclosure. The cooling fans blow cool air into the enclosure. Heated air is exhausted through the
vent openings on the left side of the enclosure. Replacement of the fans requires that the HU be
turned off for ashort period of time. Use the following procedure to remove and replace the HU
cooling fans:
1. Before working on the HU or handling afan, slip on an Electro-Static Discharge (ESD)
wrist strap and connect the ground wire to an earth ground source. Wear the ESD wrist
strap while completing each section of the fan installation procedure.
2. Notify the NOC or alarm monitoring system operator that the system is going offline.
3. Place the HU On/Off switch in the OFF position (press O).
4. Remove the six flat-head screws (requires TORX screwdriver with T10 bit) that secure the
fan/grill assembly to the right side of the HU enclosure as shown in Figure 5-2.Save
screws for reuse.
Figure 5-2. Host Unit Fan/Grill Assembly Removal
5. Carefully withdraw the fan/grill assembly from the enclosure until the wiring harness is
exposed and the connectors are accessible.
6. Lift the small latch on each wiring harness connector and carefully unplug each connector
from the circuit board connector.
7. Remove the plastic rivets that secure each fan to the grill by pushing outward on the rivet
center post until the rivet can be withdrawn from the grill as shown in Figure 5-3.
Warning: Electronic components can be damaged by static electrical discharge. To prevent
ESD damage, always wear an ESD wrist strap when working on the HU, STM, or LPA and
when handling electronic components.
16986-A

ADCP-75-150 • Preliminary Issue A • March 2003 • Section 5: Maintenance
Page 5-16
©2003, ADC Telecommunications, Inc.
Figure 5-3. Removing Host Unit Fans From Grill
8. Remove both fans from the grill
9. Use the rivets removed in step 7to secure the replacement fans to the grill. Orient each fan
so the wiring harness is on the top and the arrow on the fan points into the enclosure.
10. Connect the two wiring harness connectors to the circuit board connectors.
11. Secure the fan/grill assembly to the side of the enclosure (see Figure 5-2)using the six
flat-head screws removed in step 4.
12. Place the HU On/Off switch in the ON position (press I).
13. Verify that the fans run properly following power-up.
14. Notify the NOC or alarm monitoring system operator that the system is going back online.
5.4 Spectrum Transport Module Fan Replacement Procedure
The STM is equipped with arear cooling fan that exhausts heated air from the STM enclosure.
Cool air enters the STM through vent openings on the side of the enclosure. Replacement of the
fan requires that the STM be turned off for ashort period of time and that the STM be removed
from the cabinet. Use the following procedure to remove and replace the STM cooling fan.
1. Before working on the STM or handling afan, slip on an Electro-Static Discharge (ESD)
wrist strap and connect the ground wire to an earth ground source. Wear the ESD wrist
strap while completing each section of the fan installation procedure.
2. Notify the NOC or alarm monitoring system operator that the system is going offline.
3. Place the STM On/Off switch in the OFF position (press O).
4. Disconnect the various power, fiber optic, service, alarm wiring, and coaxial cable
connectors from the STM front panel as specified in Figure 5-4.
Warning: Electronic components can be damaged by static electrical discharge. To prevent
ESD damage, always wear an ESD wrist strap when working on the HU, STM, or LPA and
when handling electronic components.
16173-B
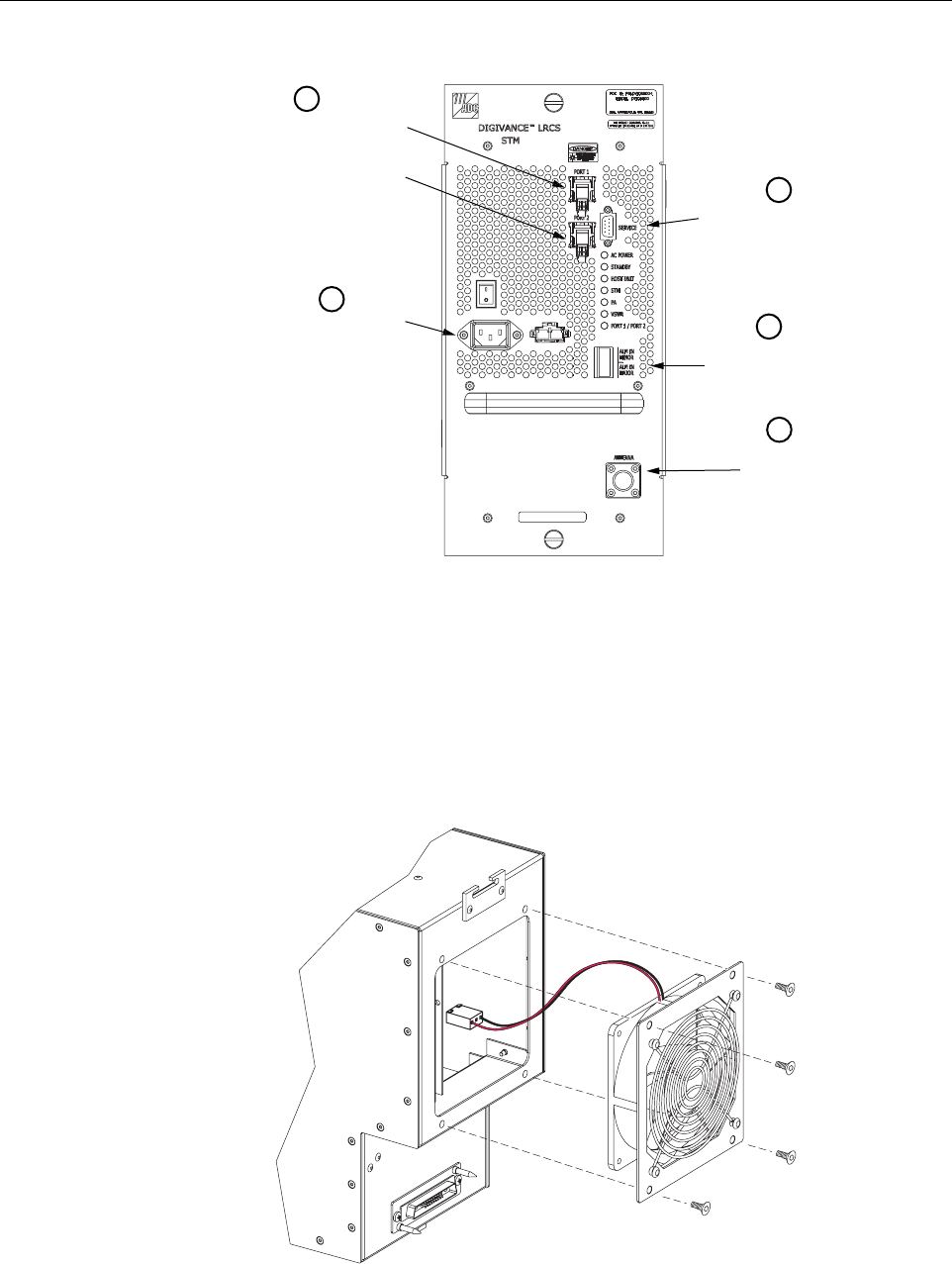
ADCP-75-150 • Preliminary Issue A • March 2003 • Section 5: Maintenance
Page 5-17
©2003, ADC Telecommunications, Inc.
Figure 5-4. Spectrum Transport Module Cable Connections
5. Loosen the captive screws that secure the STM to the RU cabinet mounting shelf and
carefully withdraw the STM from the cabinet.
6. Remove the four pan-head screws (requires TORX screwdriver with T10 bit) that secure
the fan/grill assembly to rear side of the STM enclosure as shown in Figure 5-5.Save
screws for reuse.
Figure 5-5. STM Fan/Grill Assembly Removal
18661-A
Disconnect AC
power connector Disconnect alarm
connector
Disconnect antenna
connector
1
2
3
4
5
Disconnect optical fiber
connectors. Place a dust
cap over each cable
connector and port adapter.
Disconnect service
connector (if present)
16992-A
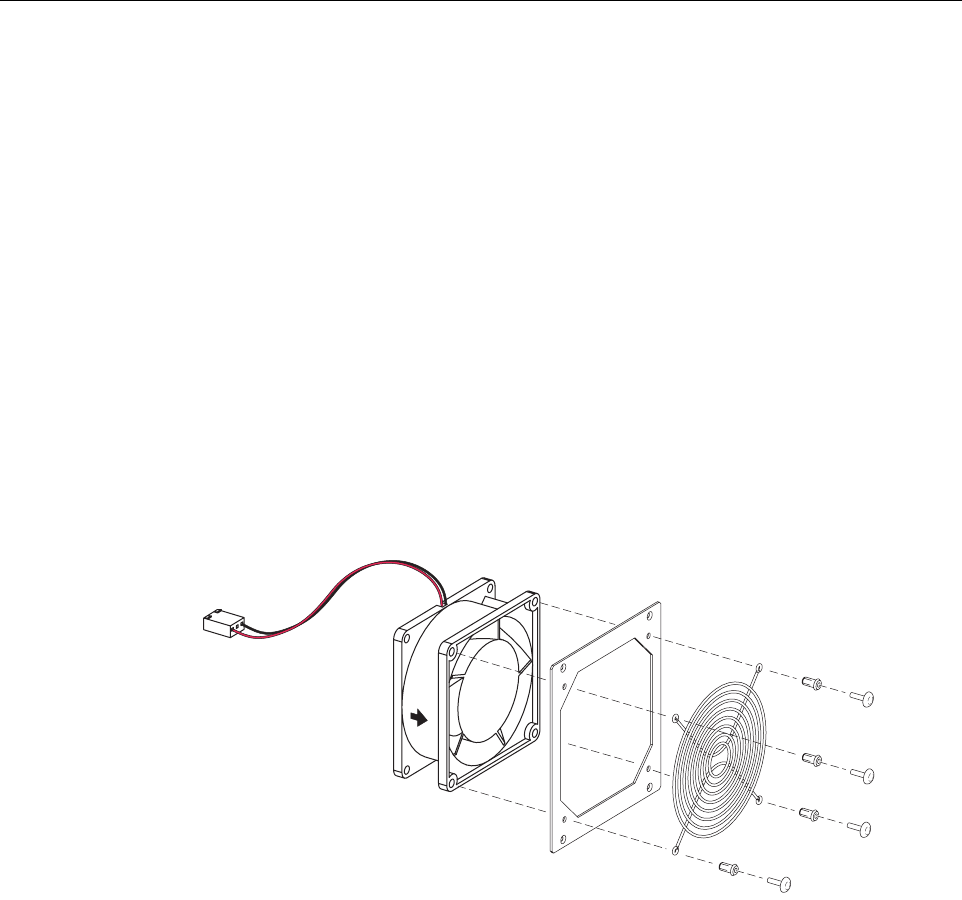
ADCP-75-150 • Preliminary Issue A • March 2003 • Section 5: Maintenance
Page 5-18
©2003, ADC Telecommunications, Inc.
7. Carefully withdraw the fan/grill assembly from the enclosure until the wiring harness is
exposed and the connector is accessible.
8. Lift the small latch on the wiring harness connector and carefully unplug the connector
from the circuit board connector.
9. Remove the plastic rivets that secure the fan to the mounting plate and grill by pushing
outward on the rivet center post until the rivet can be withdrawn as shown in Figure 5-6.
10. Separate fan from the mounting plate and grill
11. Use the rivets removed in step 9to secure the replacement fan to the mounting plate and
grill. Orient the fan so the wiring harness is on the top and the arrow on the fan points
away from the enclosure. Make certain the rubber grommets are left in place on the
mounting plate.
12. Connect the wiring harness connector to the circuit board connector.
13. Secure the fan/grill assembly to the back of the enclosure (see Figure 5-5)using the four
pan-head screws removed in step 6. Do not overtighten the screws. The screw threads can
be easily stripped if too much torque is used to tighten the screws.
Figure 5-6. Removing STM Fan From Mounting Plate and Grill
14. Re-install the STM in the cabinet and then re-connect all cables in the reverse order in
which they were disconnected (see Figure 5-4).
15. Place the STM On/Off switch in the ON position (press I).
16. Verify that the fan runs properly following power-up.
17. Notify the NOC or alarm monitoring system operator that the system is going back online.
16993-A
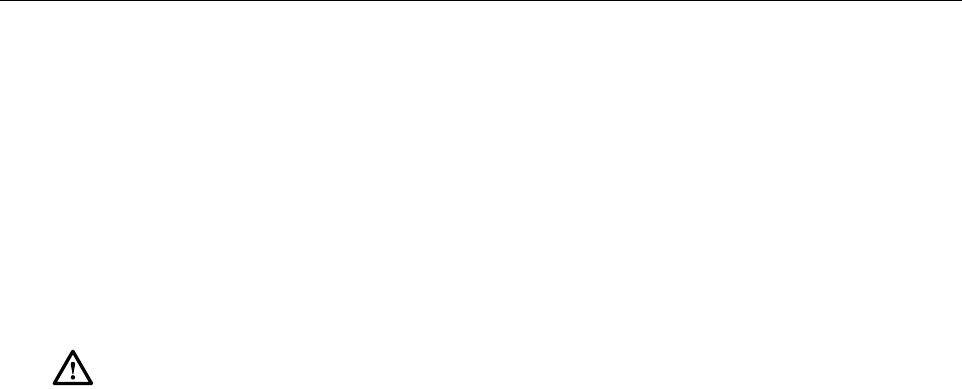
ADCP-75-150 • Preliminary Issue A • March 2003 • Section 5: Maintenance
Page 5-19
©2003, ADC Telecommunications, Inc.
5.5 Linear Power Amplifier Fan Replacement Procedure
The LPA is equipped with afront and cooling fan. The front fan draws cool air into the LPA
enclosure. Replacement of the fans requires that the STM be turned off for ashort period of
time and that the LPA be removed from the cabinet. Use the following procedure to remove and
replace the LPA cooling fans.
1. Before working on the LPA or handling afan, slip on an Electro-Static Discharge (ESD)
wrist strap and connect the ground wire to an earth ground source. Wear the ESD wrist
strap while completing each section of the fan installation procedure.
2. Notify the NOC or alarm monitoring system operator that the system is going offline.
3. Place the STM On/Off switch in the OFF position (press O).
4. Loosen the captive screws that secure the LPA to the RU cabinet/mounting shelf and
carefully withdraw the LPA from the cabinet.
5. Pull out the four retainers that secure the front fan to the LPA as shown in Figure 5-7 and
same for reuse.
Figure 5-7. LPA Fan Removal and Replacement
6. Carefully withdraw the fan assembly from the LPA until the wiring harness is exposed and
the RJ-45 wiring harness connector is accessible.
7. Disconnect the fan wiring harness connector from the LPA and lift the fan assembly away
from the LPA.
8. Place asmall amount of anti-corrosion gel on the connector of the replacement fan
assembly.
9. Orient the fan assembly so the air-flow arrow points into the LPA.
Warning: Electronic components can be damaged by static electrical discharge. To prevent
ESD damage, always wear an ESD wrist strap when working on the HU, STM, or LPA and
when handling electronic components.
Drawing not available

ADCP-75-150 • Preliminary Issue A • March 2003 • Section 5: Maintenance
Page 5-20
©2003, ADC Telecommunications, Inc.
10. Connect the fan assembly wiring harness connector to the LPA internal connector.
11. Secure the fan assembly to the LPA using the four retainers removed in step 5.
12. Place the STM On/Off switch in the ON position (press I)and verify that the fan operates
properly. The fan should draw air into the LPA.
13. Notify the NOC or alarm monitoring system operator that the system is going back online.

ADCP-75-150 • Preliminary Issue A • March 2003 • Section 6: General Information
Page 6-1
©2003, ADC Telecommunications, Inc.
SECTION 6: GENERAL INFORMATION
1 WARRANTY/SOFTWARE . . . . . . . . . . . . . . . . . . . . . . . . . . . . . . . . . . . . . . . . . . . . . . . . . . . . . . . . . . . . . . . . . .6-1
2 SOFTWARE SERVICE AGREEMENT. . . . . . . . . . . . . . . . . . . . . . . . . . . . . . . . . . . . . . . . . . . . . . . . . . . . . . . . . . .6-1
3 REPAIR/EXCHANGE POLICY . . . . . . . . . . . . . . . . . . . . . . . . . . . . . . . . . . . . . . . . . . . . . . . . . . . . . . . . . . . . . . .6-1
4 REPAIR CHARGES . . . . . . . . . . . . . . . . . . . . . . . . . . . . . . . . . . . . . . . . . . . . . . . . . . . . . . . . . . . . . . . . . . . . . .6-2
5 REPLACEMENT/SPARE PRODUCTS . . . . . . . . . . . . . . . . . . . . . . . . . . . . . . . . . . . . . . . . . . . . . . . . . . . . . . . . . .6-2
6 RETURNED MATERIAL . . . . . . . . . . . . . . . . . . . . . . . . . . . . . . . . . . . . . . . . . . . . . . . . . . . . . . . . . . . . . . . . . . .6-2
7 CUSTOMER INFORMATION AND ASSISTANCE . . . . . . . . . . . . . . . . . . . . . . . . . . . . . . . . . . . . . . . . . . . . . . . . . . .6-3
_________________________________________________________________________________________________________
1 WARRANTY/SOFTWARE
The Product and Software warranty policy and warranty period for all ADC Products is
published in ADC’s Warranty/Software Handbook. Contact the Technical Assistance Center at
1-800-366-3891, extension 73475 (in U.S.A. or Canada) or 952-917-3475 (outside U.S.A. and
Canada) for warranty or software information or for acopy of the Warranty/Software
Handbook.
2 SOFTWARE SERVICE AGREEMENT
ADC software service agreements for some ADC Products are available at anominal fee.
Contact the Technical Assistance Center at 1-800-366-3891, extension 73475 (in U.S.A. or
Canada) or 952-917-3475 (outside U.S.A. and Canada) for software service agreement
information.
3 REPAIR/EXCHANGE POLICY
All repairs of ADC Products must be done by ADC or an authorized representative. Any
attempt to repair or modify ADC Products without written authorization from ADC voids the
warranty.
If amalfunction cannot be resolved by the normal troubleshooting procedures, call the
Technical Assistance Center at 1-800-366-3891, extension 73475 (in U.S.A. or Canada) or
952-917-3475 (outside U.S.A. and Canada). Atelephone consultation can sometimes resolve a
problem without the need to repair or replace the ADC Product.
If, during atelephone consultation, ADC determines the ADC Product needs repair, ADC will
authorize the return of the affected Product for repair and provide aReturn Material
Authorization number and complete return shipping instructions. If time is critical, ADC can
arrange to ship the replacement Product immediately. In all cases, the defective Product must be
carefully packaged and returned to ADC.
Content Page

ADCP-75-150 • Preliminary Issue A • March 2003 • Section 6: General Information
Page 6-2
©2003, ADC Telecommunications, Inc.
4 REPAIR CHARGES
If the defect and the necessary repairs are covered by the warranty, and the applicable warranty
period has not expired, the Buyer’s only payment obligation is to pay the shipping cost to return
the defective Product. ADC will repair or replace the Product at no charge and pay the return
shipping charges.
Otherwise, ADC will charge apercentage of the current Customer Product price for the repair
or NTF (No Trouble Found). If an advance replacement is requested, the full price of anew unit
will be charged initially. Upon receipt of the defective Product, ADC will credit Buyer with 20
percent of full price charged for any Product to be Out-of-Warranty. Products must be returned
within thirty (30) days to be eligible for any advance replacement credit. If repairs necessitate a
visit by an ADC representative, ADC will charge the current price of afield visit plus round trip
transportation charges from Minneapolis to the Buyer’s site.
5 REPLACEMENT/SPARE PRODUCTS
Replacement parts, including, but not limited to, button caps and lenses, lamps, fuses, and patch
cords, are available from ADC on aspecial order basis. Contact the Technical Assistance Center
at 1-800-366-3891, extension 73475 (in U.S.A. or Canada) or 952-917-3475 (outside U.S.A.
and Canada) for additional information.
Spare Products and accessories can be purchased from ADC. Contact Sales Administration at
1-800-366-3891, extension 73000 (in U.S.A. or Canada) or 1-952-938-8080 (outside U.S.A.
and Canada) for aprice quote and to place your order.
6 RETURNED MATERIAL
Contact the ADC Product Return Department at 1-800-366-3891, extension 73748 (in U.S.A. or
Canada) or 952-917-3748 (outside U.S.A. and Canada) to obtain aReturn Material
Authorization number prior to returning an ADC Product.
All returned Products must have aReturn Material Authorization (RMA) number clearly
marked on the outside of the package. The Return Material Authorization number is valid for 90
days from authorization.
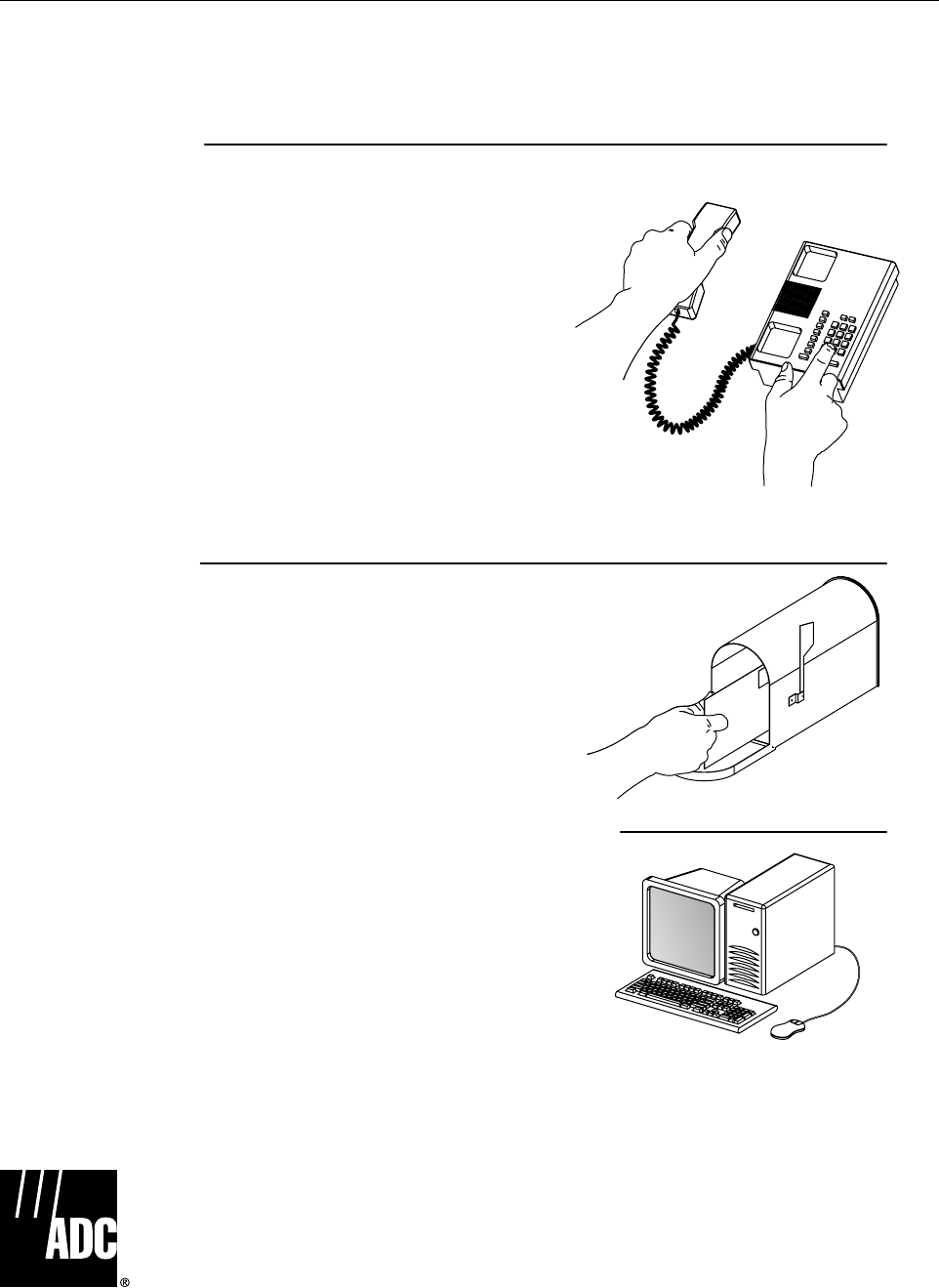
Page 6-3
ADCP-75-150 • Preliminary Issue A • March 2003 • Section 6: General Information
7 CUSTOMER INFORMATION AND ASSISTANCE
©2003, ADC Telecommunications, Inc.
All Rights Reserved
Printed in U.S.A .
13944-J
WRITE:
ADC TELECOMMUNICATIONS, INC
PO BOX 1101,
MINNEAPOLIS, MN 55440-1101, USA
ADC TELECOMMUNICATIONS (S'PORE) PTE. LTD.
100 BEACH ROAD, #18-01, SHAW TOWERS.
SINGAPORE 189702.
ADC EUROPEAN CUSTOMER SERVICE, INC
BELGICASTRAAT 2,
1930 ZAVENTEM, BELGIUM
PHONE:
EUROPE
Sales Administration: +32-2-712-65 00
Technical Assistance: +32-2-712-65 42
EUROPEAN TOLL FREE NUMBERS
UK: 0800 960236
Spain: 900 983291
France: 0800 914032
Germany: 0180 2232923
U.S.A. OR CANADA
Sales: 1-800-366-3891 Extension 73000
Technical Assistance: 1-800-366-3891 Extension 73475
ASIA/PACIFIC
Sales Administration: +65-6294-9948
Technical Assistance: +65-6393-0739
ELSEWHERE
Sales Administration: +1-952-938-8080
Technical Assistance: +1-952-917-3475
PRODUCT INFORMATION AND TECHNICAL ASSISTANCE:
Contents herein are current as of the date of publication. ADC reserves the right to change the contents without prior notice.
In no event shall ADC be liable for any damages resulting from loss of data, loss of use, or loss of profits and ADC further
disclaims any and all liability for indirect, incidental, special, consequential or other similar damages. This disclaimer of
liability applies to all products, publications and services during and after the warranty period. This publication may be
verified at any time by contacting ADC's Technical Assistance Center.
euro_tac@adc.com
asiapacific_tac@adc.com
connectivity_tac@adc.com

i
www.adc.com