Olympus Medical Systems RU2020 Endoscope Reprocessor User Manual GT9882 0100 fm10
Olympus Medical Systems Corp. Endoscope Reprocessor GT9882 0100 fm10
Contents
Operation Manual 5
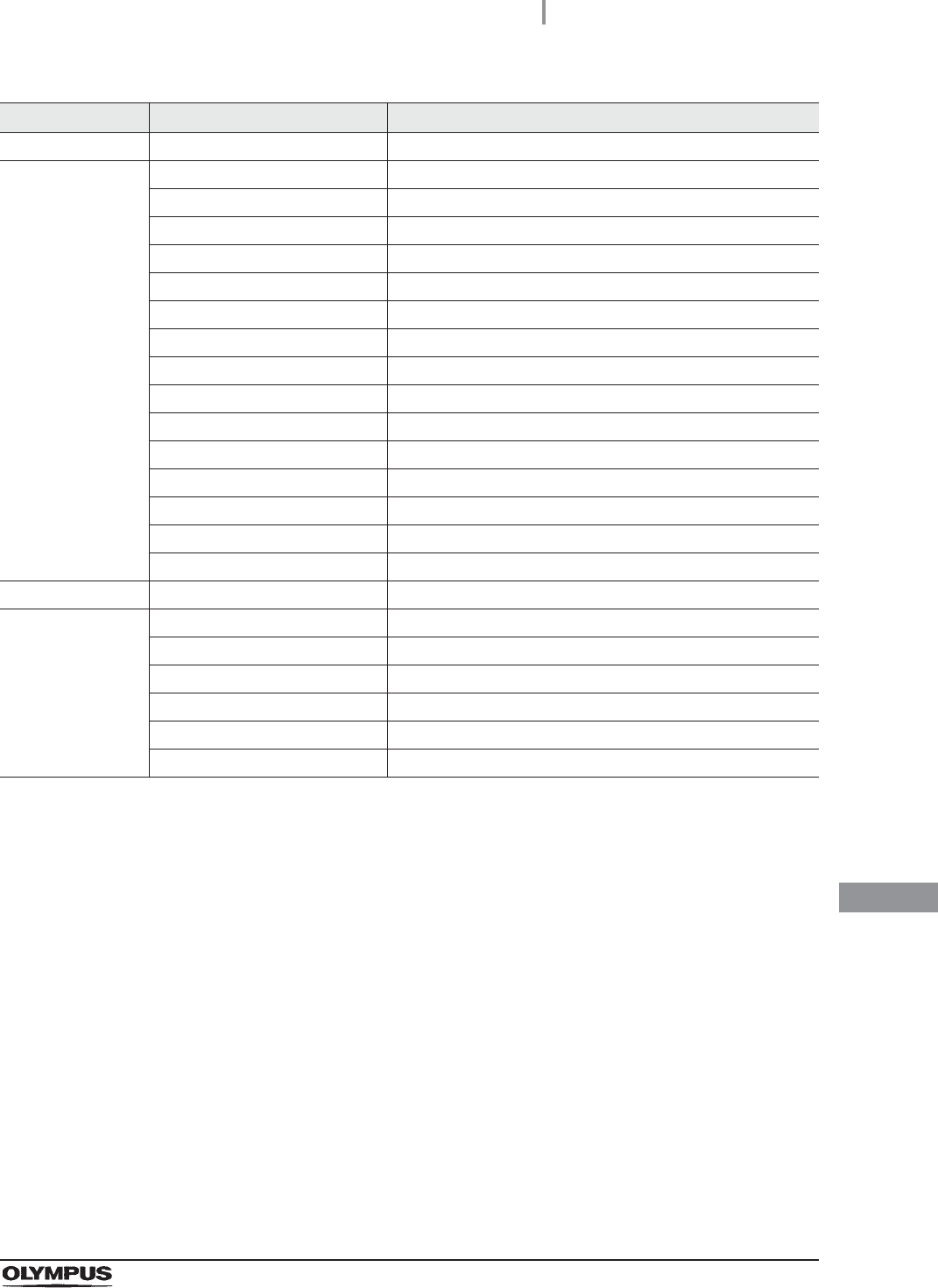
11.3 Log management with PC
543
OER-Elite OPERATION MANUAL
Ch.11
Table 11.3
5th level (Reprocessing) & 6th level (the others): Output range
The “ALL” folder is created when the data of all records are saved.
The “SetMonth” folder is created when the record data is saved by selecting a month.
The “SetPeriod” folder is created when the record data is saved by selecting a period.
The “Differential” folder is created when the record data that has not been output to the
portable memory is saved.
4th Level 5th Level Description
Reprocessing – The folder for Reprocessing record.
Function Air Purge The folder for air purge record.
Alcohol Flush The folder for alcohol flush record.
Alcohol Line Disinfection The folder for alcohol line disinfection record.
ALT Self-Check The folder for ALT self-check record.
Detergent Line Disinfection The folder for detergent line disinfection record.
Heat LCG The folder for heat LCG record.
Leaking Scope Decontamination The folder for leaking scope decontamination record.
Leak Test The folder for auto and manual leak test record.
Maintenance The folder for periodic maintenance and repair record.
Mix LCG The folder for Mix LCG record.
MRC Check Result The folder for MRC check result record.
Portable Memory The folder for portable memory record.
Rinse The folder for rinse record.
Self Disinfection The folder for self disinfection record.
WaterLine Disinfection The folder for water line disinfection record.
Error – The folder for error record.
ReplacementOf
ConsumableItems
Replace Air Filter The folder for replace air filter record.
Replace Detergent The folder for replace detergent record.
Replace Gas Filter (lid) The folder for replace gas filter (lid) record.
Replace Gas Filter (tank) The folder for replace gas filter (tank) record.
Replace LCG The folder for replace LCG record.
Replace Water Filter The folder for replace water filter record.
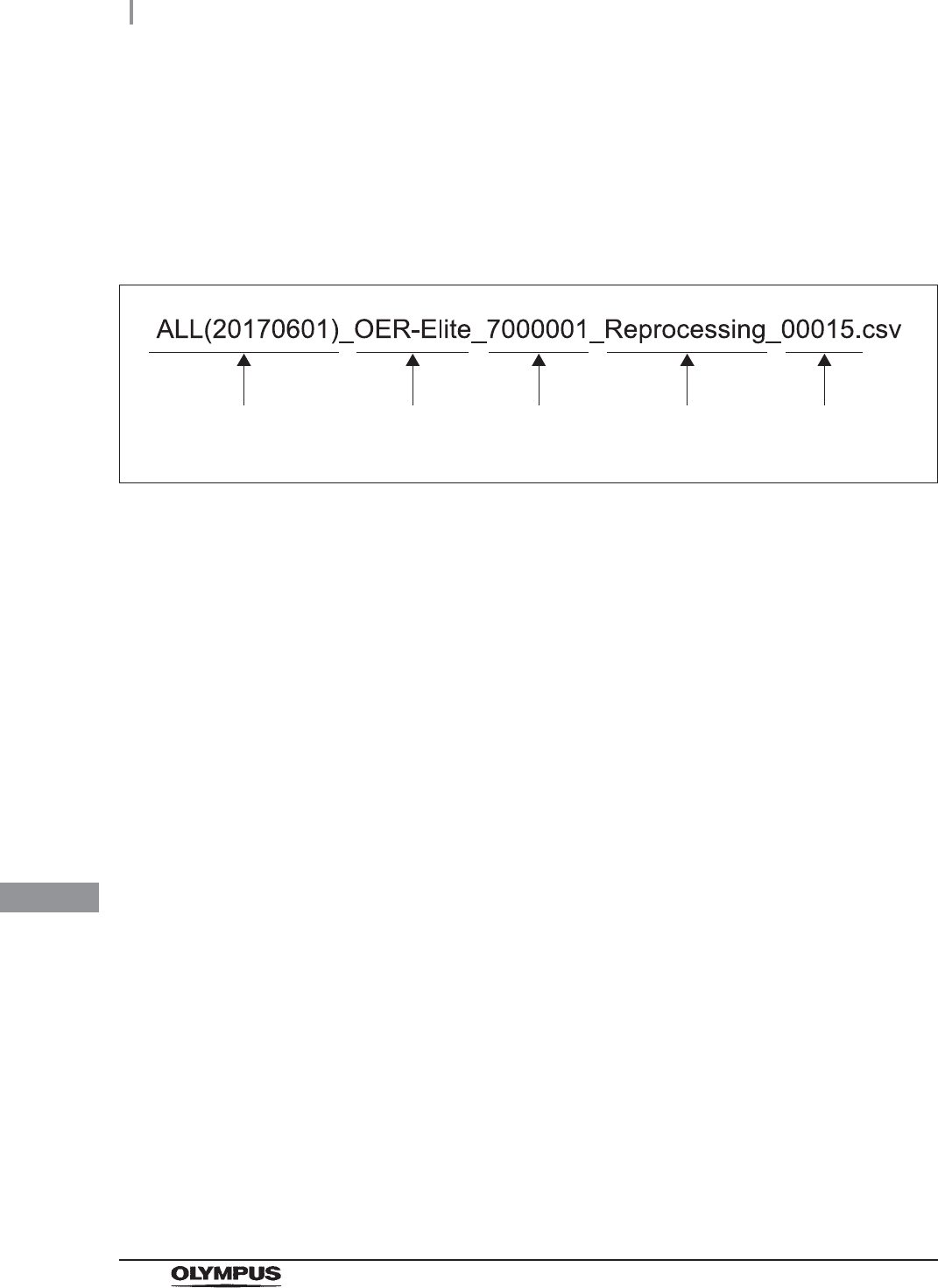
544
11.3 Log management with PC
OER-Elite OPERATION MANUAL
Ch.11
(b) File type
The record data in the CSV (Comma-Separated Values) format is saved.
(c) File names
The files are named based on the range selected when data is saved in the portable memory,
the type of record, etc.
Figure 11.18 Example
Selected period Reprocessor
name
Reprocessor
serial number
Process
name
Portable memory
save count
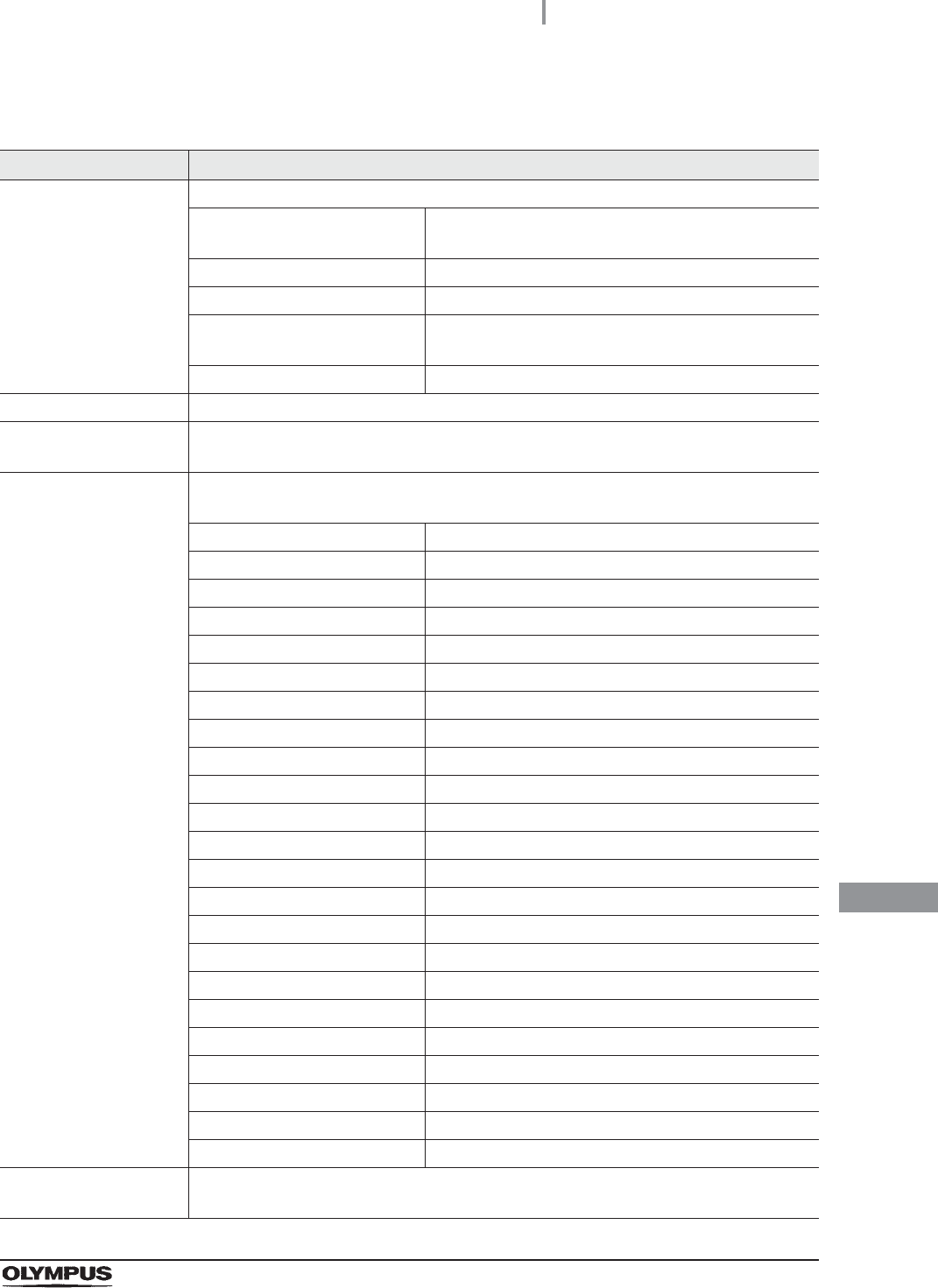
11.3 Log management with PC
545
OER-Elite OPERATION MANUAL
Ch.11
Table 11.4
Items constituting the file names
Item Description
Selected period This item indicates the output mode selected when downloading the records.
ALL (20170601) ALL data output setting. The figures inside the
parentheses indicate the date of downloading.
20170501 – 20170615 Selected period (when more than one day is specified)
20170501 Selected period (when one day is specified)
201706 Selected month (displayed according to the date
display format setting)
Diff (20170601) Data not output to portable memory
Reprocessor name OER-Elite
Reprocessor serial
number
1234567
Data type Type of the saved records.
Displayed record names
Reprocessing Reprocessing record
LeakTest Leak test record
ReplaceLCG Disinfectant replacement record
MRCCheckResult MRC check result record
HeatLCG Heat LCG record
MixLCG Mix LCG record
ReplaceWaterFilter Water filter replacement record
ReplaceAirFilter Air filter replacement record
ReplaceGasFilter(lid) Gas filter (lid) replacement record
ReplaceGasFilter(tank) Gas filter (tank) replacement record
ReplaceDetergent Detergent replacement record
WaterLineDisinfection Water line disinfection record
AlcoholLineDisinfection Alcohol line disinfection record
DetergentLineDisinfection Detergent line disinfection record
Rinse Rinse record
AirPurge Air purge record
AlcoholFlush Alcohol flush record
SelfDisinfection Self disinfection record
PortableMemory USB memory output record
Error Error record
ALTSelf-Check Auto Leak Test Self-check record
LeakingScopeDecontamination Leaking scope decontamination record
Maintenance Periodic Maintenance and repair records
Portable memory save
count
Total number of portable memory saving operations in 5 digits.
Range: 00001 to 65535. The count after 65535 becomes 00001.
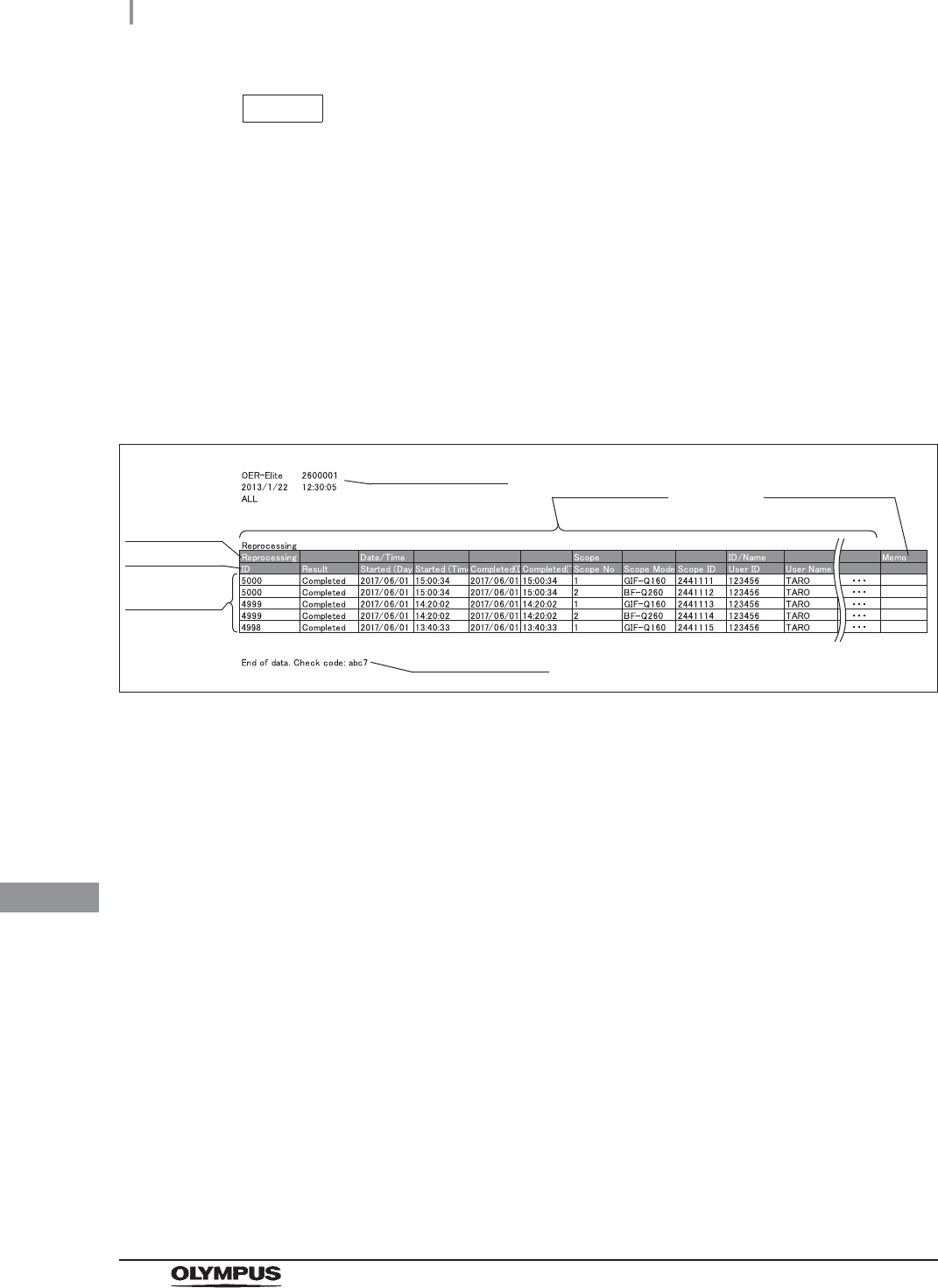
546
11.3 Log management with PC
OER-Elite OPERATION MANUAL
Ch.11
NOTE
If the same filename is already there in the folder, a number is appended to the end
of the filename of the new file (Example:
2120_02-01_1700_OER-Elite_2700000_Reprocessing_00010(2).csv). This
number is appended to prevent the edited file in the PC from being overwritten.
(d) Information in each file
Each file is saved in a portable memory in the CSV format.
Every file is composed of the header, data and footer sections. The header and footer sections
are common to all record data. The data section varies depending on the data type.
For detail of record data, refer to Figure 11.19. There is no color in each column of record data.
Figure 11.19
Header section Data section Memo section
Footer section
Description
Minor item
Major item
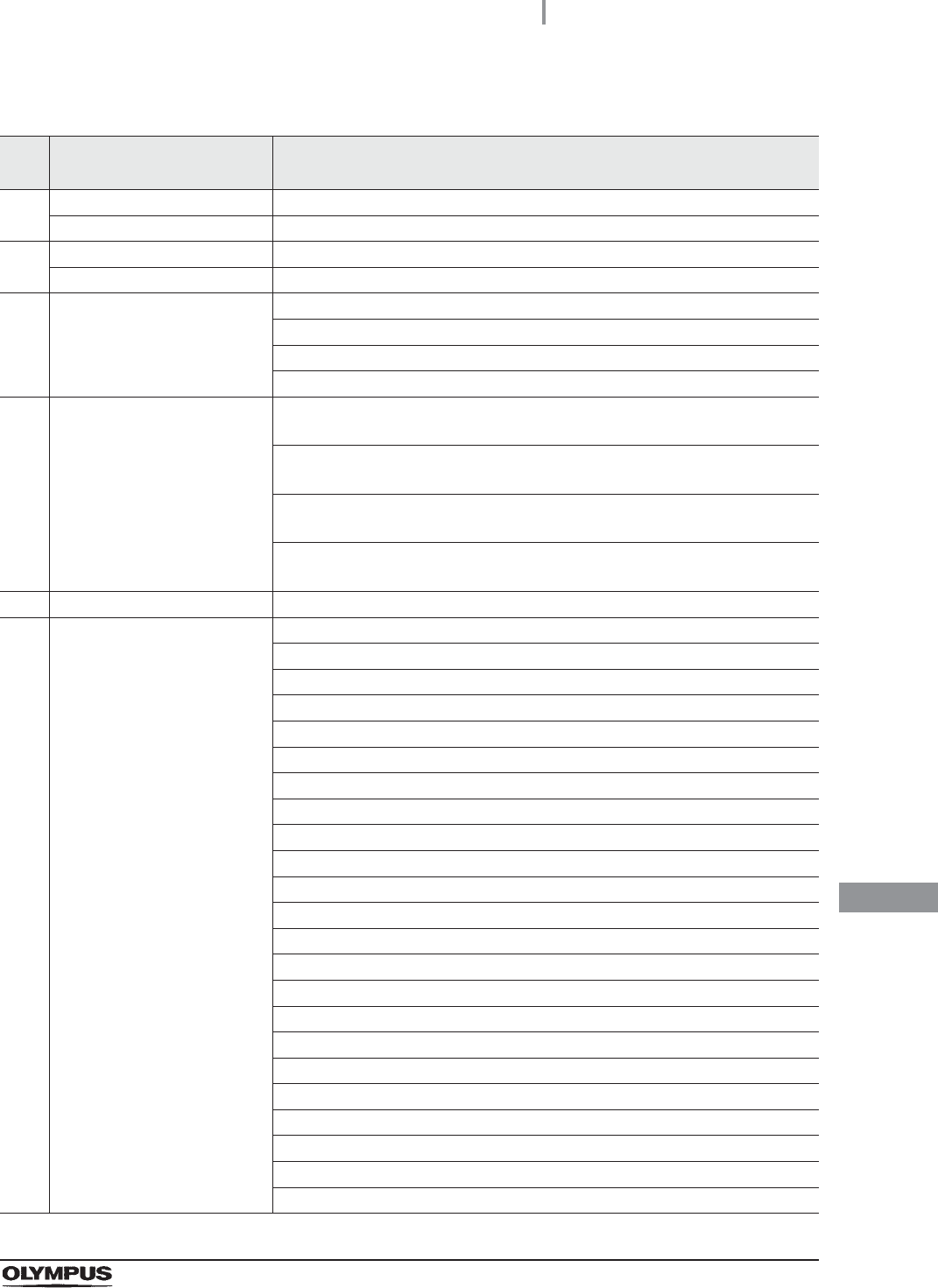
11.3 Log management with PC
547
OER-Elite OPERATION MANUAL
Ch.11
Table 11.5
Header section
Line
No. Information Example
1 Reprocessor name OER-Elite
Reprocessor serial number 1234567
2 File output date 06/01/2017
File output time 9:00:30 PM
3 Output mode All
Set period
Set month
Differential: Blank.
4 Output range Blank
(When output mode is All)
2017/05/01 – 2017/05/31
(When output mode is Set period and more than one day is specified)
2017/05/01
(When output mode is Set period and one day is specified)
2017/05
(When output mode is Set month)
5 – 7 Blanks
8 Process name Reprocessing
Leak Test
Replace LCG
MRC Check Result
Heat LCG
Mix LCG
Replace Water Filter
Replace Air Filter
Replace Gas Filter (lid)
Replace Gas Filter (tank)
Replace Detergent
Water Line Disinfection
Alcohol Line Disinfection
Detergent Line Disinfection
Rinse
Air Purge
Alcohol Flush
Self Disinfection & Water Sampling
Portable Memory
Error
ALT Self-Check
Leaking Scope Decontamination
Maintenance
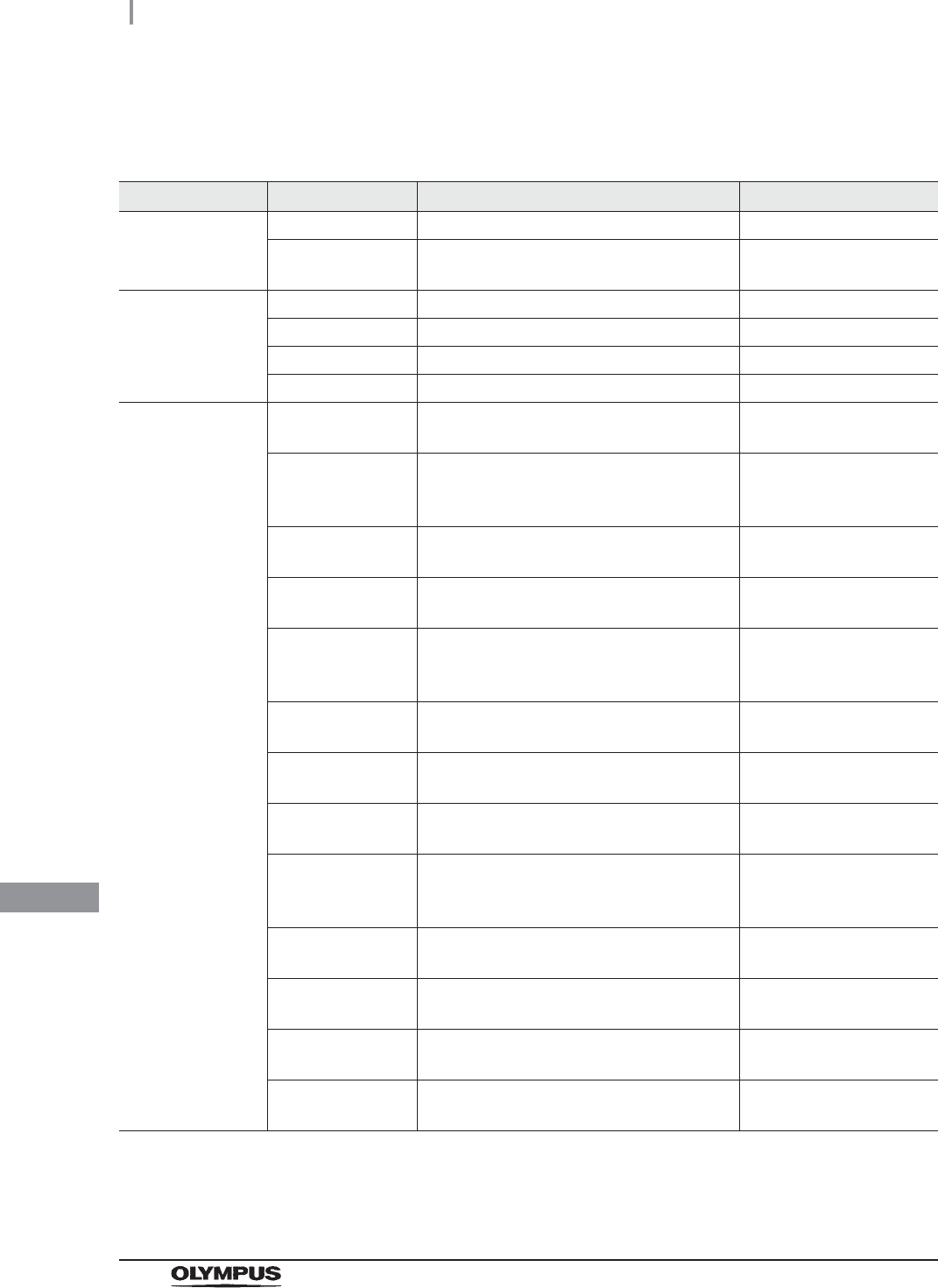
548
11.3 Log management with PC
OER-Elite OPERATION MANUAL
Ch.11
Data section
• Reprocessing records
Major item Minor item Description Examples
Reprocessing Record # Record number 5000, 4999, 4998, …
Reprocess Result Results of reprocessing Completed
E XXX (in case of error)
Date/Time Started (Day) Reprocessing start date 06/01/2017
Started (Time) Reprocessing start time 15:30:30
Completed (Day) Reprocessing completion date 06/01/2017
Completed (Time) Reprocessing completion time 16:00:30
ID/Name Scope No Endoscope number 1 (First endoscope)
2 (Second endoscope)
Scope Model Model number of endoscope GIF-H190
Master (Master card input)
– (Not input)
Scope ID Endoscope serial number 12800542
– (Not input)
User ID ID number of user installing the
endoscope(s)
12345678
– (Not input)
User Name Name of user installing the endoscope(s) User
Master (Master card input)
– (Not input)
Physician ID ID number of physician – (Not input)
12345678
Physician Name Name of physician – (Not input)
Physician
Patient ID ID number of patient – (Not input)
12345678
Patient Name Name of patient *****
– (Not input)
Patient
Procedure ID ID number of procedure – (Not input)
0123456
Procedure Name Name of procedure – (Not input)
ERCP
User3 ID ID number of user removing the
endoscope(s)
– (Not input)
1
User3 Name Name of user removing the endoscope(s) – (Not input)
User
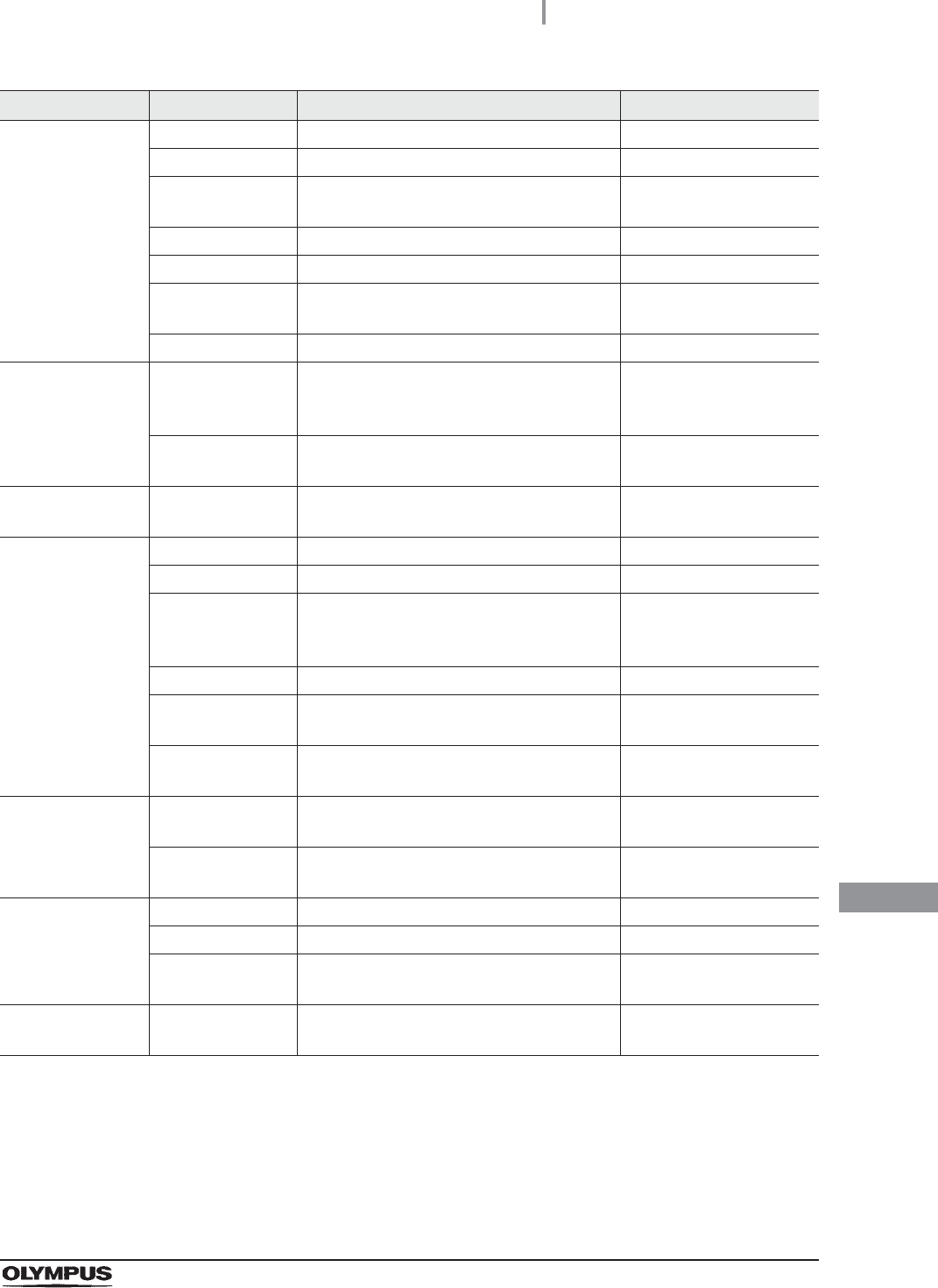
11.3 Log management with PC
549
OER-Elite OPERATION MANUAL
Ch.11
Table 11.6
Program Info. Cln time Cleaning time (minutes) 3
Dis Time Disinfection time (minutes) 7
ALT Auto leak test setting ON
OFF
Heat LCG Heat LCG setting ON
Alcohol Flush Alcohol flush setting ON
Channel Monitor Channel Monitoring setting Full
Partial
Program No. Program number 1, 2, 3, 4
Check Leak Test (Sink) Input result of leak test before manual
cleaning
– (Not input)
Pass
Fail
Manual Cleaning Input result of manual cleaning – (Not input)
Done
Function Result Leak Test Result Result of leak test during the reprocessing Pass
Fail
LCG Info. Expiry Expiry of disinfectant solution 08/30
Lot # Lot number of the disinfectant solution AA123
MRC Check Result Result of MRC check – (Not input)
Fail
Pass
Temp Disinfectant solution temperature 20
Cycle # Usage count of the disinfectant solution – (Not input)
1
Days Number of days that have elapsed since
preparation of the disinfectant solution
– (Not input)
1
Detergent Info. Expiry Expiry of the detergent solution – (Not input)
09/15
Lot # Lot number of the detergent solution – (Not input)
DD1234
AER Info. Model Name Reprocessor name OER-Elite
Serial No. Reprocessor serial number 1234567
Total Count Total number of reprocessing processes
performed
1
Memo Memorandum (Free input by user) – (Not input)
Free input by user
Major item Minor item Description Examples
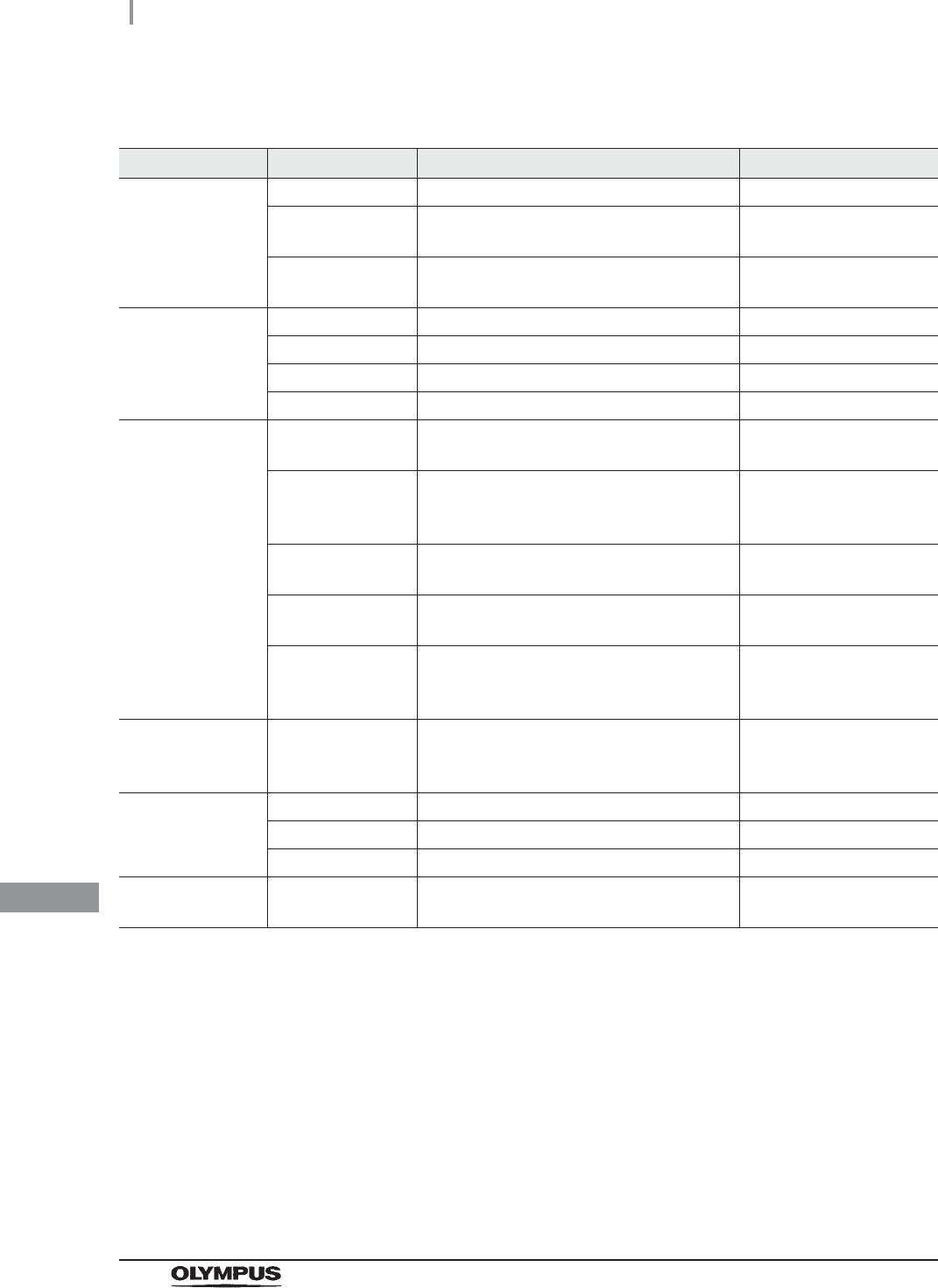
550
11.3 Log management with PC
OER-Elite OPERATION MANUAL
Ch.11
Table 11.7
• Leak test records
Major item Minor item Description Examples
Leak Test Record # Record number 5000, 4999, 4998, …
Process Result Result of leak test Complete
E XXX (in case of error)
Option Method of leak test Auto (Auto leak test)
Manual (Manual leak test)
Date/Time Started (Day) Start date of leak test 2017/06/01
Started (Time) Start time of leak test 15:30:30
Completed (Day) Completion date of leak test 2017/06/01
Completed (Time) Completion time of leak test 15:45:10
ID/Name Scope No Endoscope number 1 (First endoscope)
2 (Second endoscope)
Scope Model Model number of endoscope GIF-H190
Master (Master card input)
– (Not input)
Scope ID Endoscope serial number 12800542
– (Not input)
User ID ID number of user installing the
endoscope(s)
1
– (Not input)
User Name Name of user installing the endoscope(s) 1
Master (Master card input)
– (Not input)
Function Result Leak Test Result Result of leak test Pass
Fail
– (in case of error)
AER Info. Model Name Reprocessor name OER-Elite
Serial No. Reprocessor serial number 1234567
Total Leak Test # Total number of performing leak test 10
Memo Memorandum (Free input by user) – (Not input)
Free input by user
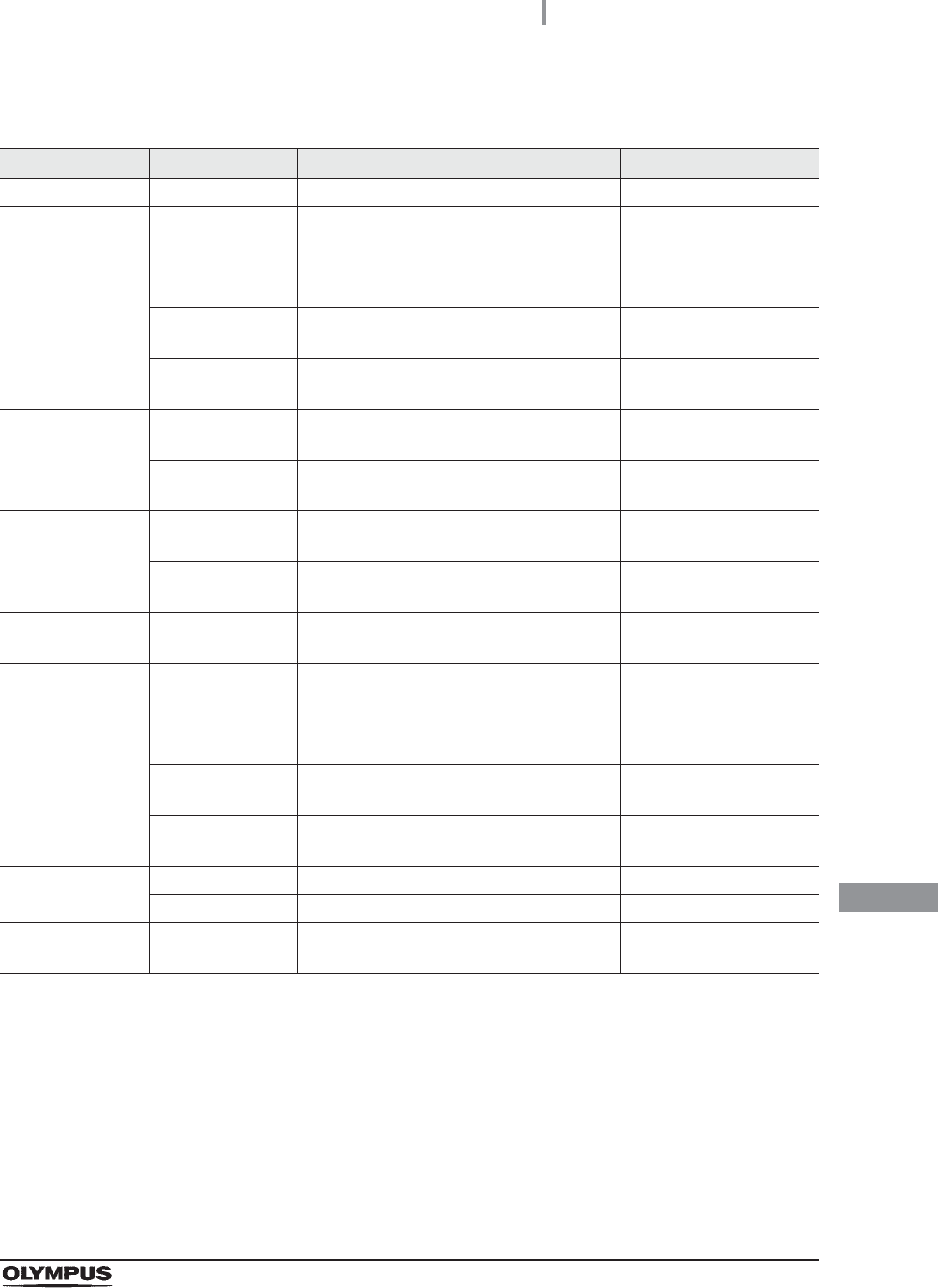
11.3 Log management with PC
551
OER-Elite OPERATION MANUAL
Ch.11
Table 11.8
• LCG replacement records
Major item Minor item Description Examples
Replace LCG Record # Record number 5000, 4999, 4998, …
Date/Time Loaded (Day) Completion date of preparation of
disinfectant solution
06/01/2017
Loaded (Time) Completion time of preparation of
disinfectant solution
08:45:30
Drained (Day) Completion date of discharge of disinfectant
solution
06/05/2017
Drained (Time) Completion time of draining disinfectant
solution
17:30:30
ID/Name
(Load LCG)
User ID ID number of user who prepared disinfectant
solution
– (Not input)
1
User Name Name of user who prepared disinfectant
solution
– (Not input)
User
ID/Name
(Drain LCG)
User ID ID of user who drained disinfectant solution – (Not input)
1
User Name Name of user who drained disinfectant
solution
– (Not input)
User
Option Method that discharged the disinfectant
solution
Drain
Collect
LCG Info. Cycle # Usage count of the disinfectant solution – (Not input)
20
Days Number of days that have elapsed since
preparation of the disinfectant solution
– (Not input)
5
Lot # Lot number of disinfectant solution – (Not input)
123456789
Expiry Expiration date of disinfectant solution – (Not input)
2013/09
AER Info. Model Name Reprocessor name OER-Elite
Serial No. Reprocessor serial number 1234567
Memo Memorandum (Free input by user) – (Not input)
Free input by user
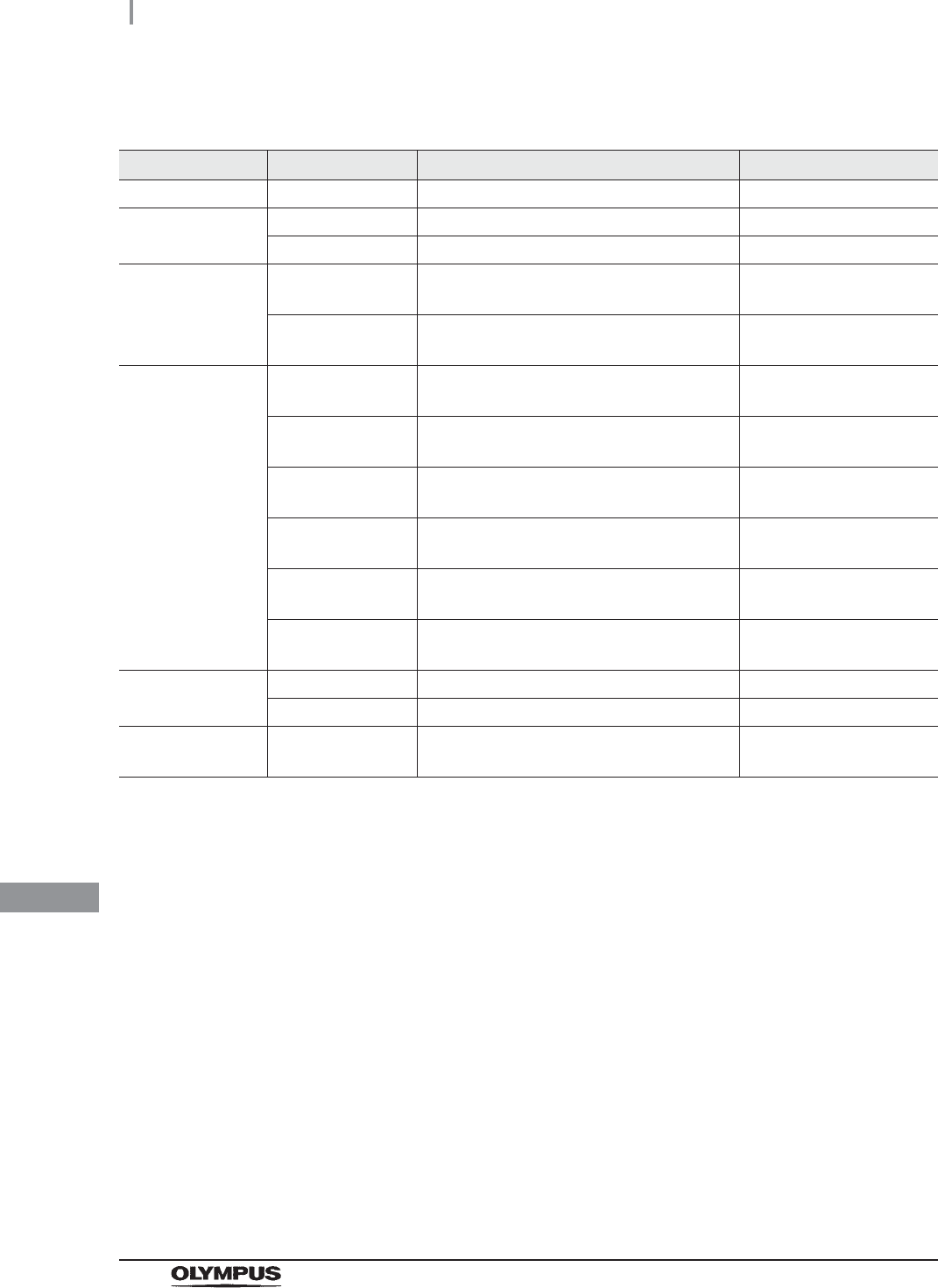
552
11.3 Log management with PC
OER-Elite OPERATION MANUAL
Ch.11
Table 11.9
MRC Check records
Major item Minor item Description Examples
MRC Check Result Record # Record number 5000, 4999, 4998, …
Date/Time Completed (Day) Completion date of MRC check 06/01/2017
Completed (Time) Completion time of MRC check 14:00:30
ID/Name User ID ID number of user who performed MRC
check
– (Not input)
1
User Name Name of user who performed MRC check – (Not input)
User
LCG Info. Expiry Expiration date of disinfectant solution – (Not input)
09/2013
Lot # Lot number of disinfectant solution – (Not input)
123456789
MRC Check Result Result of MRC check Fail
Pass
Temp Disinfectant solution temperature – (Not input)
20
Cycle # Disinfectant cycle count – (Not input)
1
Days Disinfectant day count – (Not input)
5
AER Info. Model Name Reprocessor name OER-Elite
Serial No. Reprocessor serial number 1234567
Memo Memorandum (Free input by user) – (Not input)
Free input by user
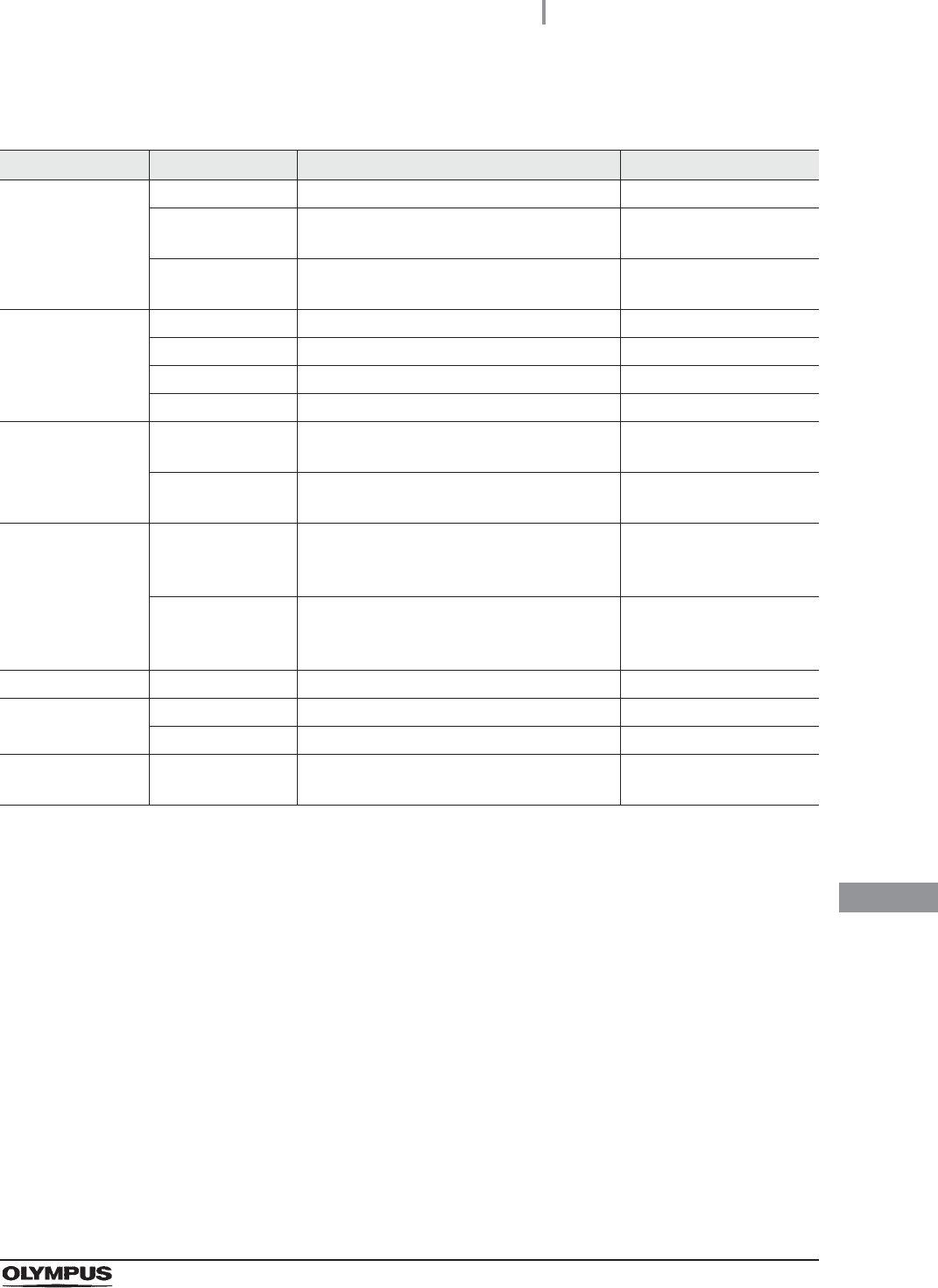
11.3 Log management with PC
553
OER-Elite OPERATION MANUAL
Ch.11
Table 11.10
Heat LCG records
Major item Minor item Description Examples
Heat LCG Record # Record number 5000, 4999, 4998, …
Process Result Result of Heat LCG Complete
E XXX (in case of error)
Option Method of Heat LCG Manual
Timer
Date/Time Started (Day) Start date of Heat LCG 06/01/2017
Started (Time) Start time of Heat LCG 08:30:30
Completed (Day) Completion date of Heat LCG 06/01/2017
Completed (Time) Completion time of Heat LCG 10:00:30
ID/Name User ID ID number of user performed Heat LCG – (Not input)
1
User Name Name of user performed Heat LCG – (Not input)
User
Timer Info. Setting Date Setting date of Heat LCG –
06/01/2017 (In case Heat
LCG Timer)
Setting Time Setting time of Heat LCG –
10:00 (In case Heat LCG
Timer)
LCG Info. Temp Disinfectant solution temperature 20
AER Info. Model Name Reprocessor name OER-Elite
Serial No. Reprocessor serial number 1234567
Memo Memorandum (Free input by user) – (Not input)
Free input by user
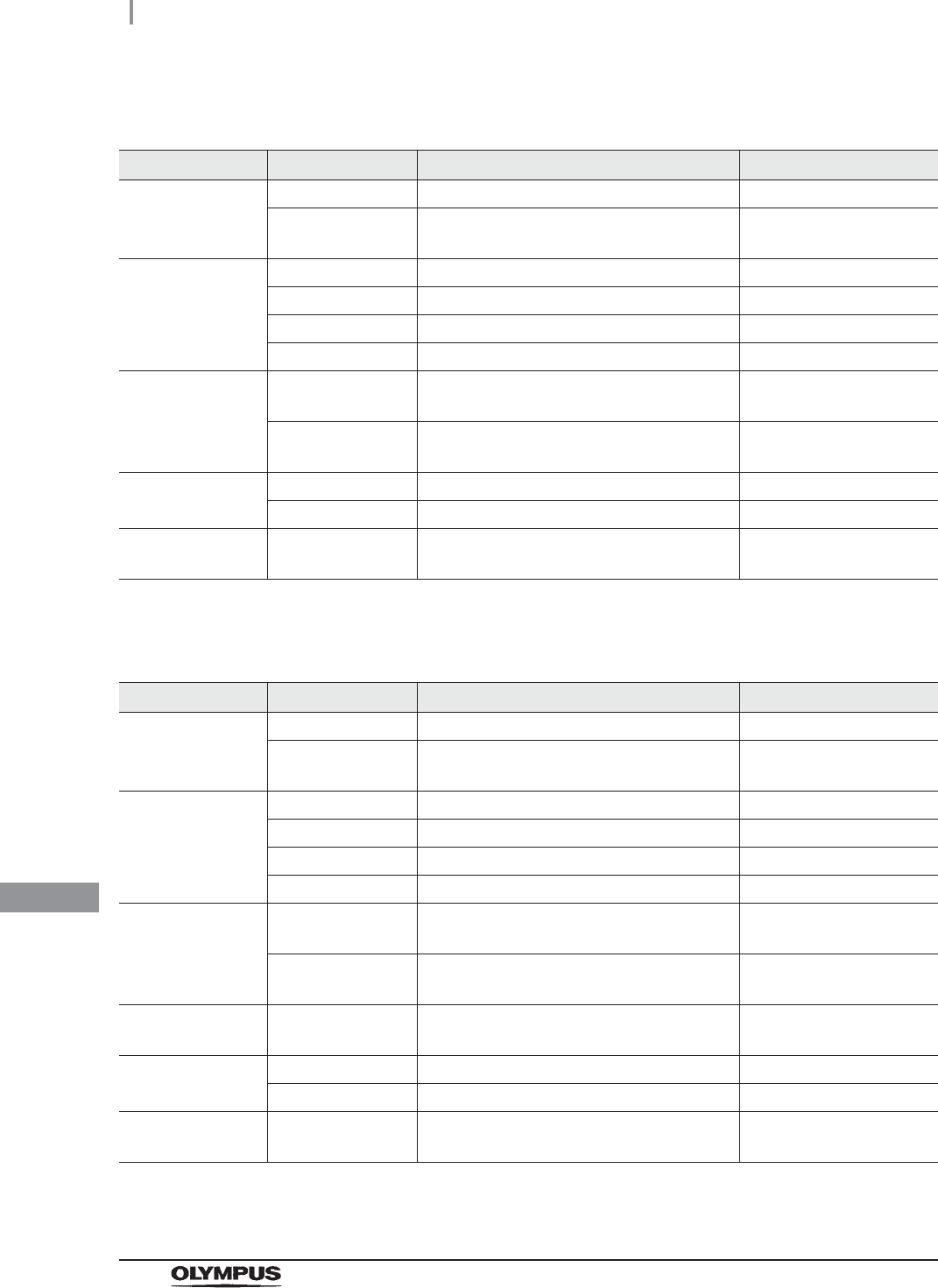
554
11.3 Log management with PC
OER-Elite OPERATION MANUAL
Ch.11
Table 11.11
Table 11.12
Mix LCG records
Major item Minor item Description Examples
Mix LCG Record # Record number 5000, 4999, 4998, …
Process Result Result of mix LCG Complete
E XXX (in case of error)
Date/Time Started (Day) Start date of mix LCG 06/01/2017
Started (Time) Start time of mix LCG 15:30:30
Completed (Day) Completion date of mix LCG 06/01/2017
Completed (Time) Completion time of mix LCG 15:45:10
ID/Name User ID ID number of user performed mix LCG – (Not input)
1
User Name ID number of user performed mix LCG – (Not input)
User
AER Info. Model Name Reprocessor name OER-Elite
Serial No. Reprocessor serial number 1234567
Memo Memorandum (Free input by user) – (Not input)
Free input by user
Water filter replacement records
Major item Minor item Description Examples
Replace Water
Filter
Record # Record number 5000, 4999, 4998, …
Process Result Result of Water filter replacement Complete
E XXX (in case of error)
Date/Time Started (Day) Start date of Water filter replacement 06/01/2017
Started (Time) Start time of Water filter replacement 08:30:00
Replaced (Day) Completion date of Water filter replacement 06/01/2017
Replaced (Time) Completion time of Water filter replacement 09:15:30
ID/Name User ID ID number of user who replaced water filter – (Not input)
1
User Name Name of user who replaced water filter – (Not input)
User
Filter Info. Lot # Lot number of water filter – (Not input)
2017/05
AER Info. Model Name Reprocessor name OER-Elite
Serial No. Reprocessor serial number 1234567
Memo Memorandum (Free input by user) – (Not input)
Free input by user
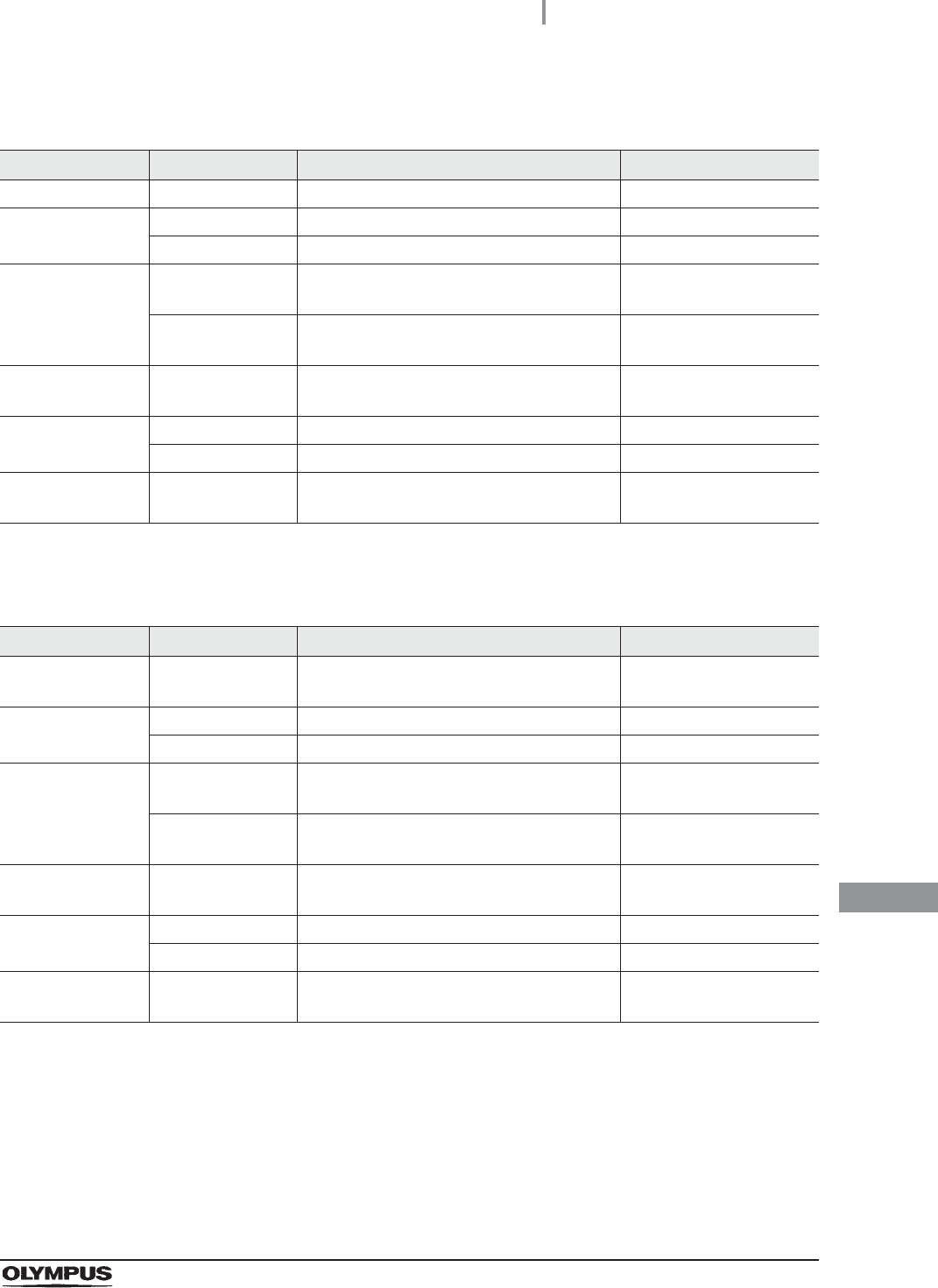
11.3 Log management with PC
555
OER-Elite OPERATION MANUAL
Ch.11
Table 11.13
Table 11.14
Air filter replacement records
Major item Minor item Description Examples
Replace Air Filter Record # Record number 5000, 4999, 4998, …
Date/Time Replaced (Day) Completion date of air filter replacement 06/01/2017
Replaced (Time) Completion time of air filter replacement 11:30:45
ID/Name User ID ID number of user who replaced air filter – (Not input)
1
User Name Name of user who replaced air filter – (Not input)
User
Filter Info. Lot # Lot number of air filter – (Not input)
987654321
AER Info. Model Name Reprocessor name OER-Elite
Serial No. Reprocessor serial number 1234567
Memo Memorandum (Free input by user) – (Not input)
Free input by user
Gas filter (lid) replacement records
Major item Minor item Description Examples
Replace Gas Filter
(lid)
Record # Record number 5000, 4999, 4998, …
Date/Time Replaced (Day) Completion date of gas filter replacement 06/01/2017
Replaced (Time) Completion time of gas filter replacement 12:15:30
ID/Name User ID ID number of user who replaced gas filter – (Not input)
1
User Name Name of user who replaced gas filter – (Not input)
User
Filter Info. Lot # Lot number of gas filter – (Not input)
2017/05
AER Info. Model Name Reprocessor name OER-Elite
Serial No. Reprocessor serial number 1234567
Memo Memorandum (Free input by user) – (Not input)
Free input by user
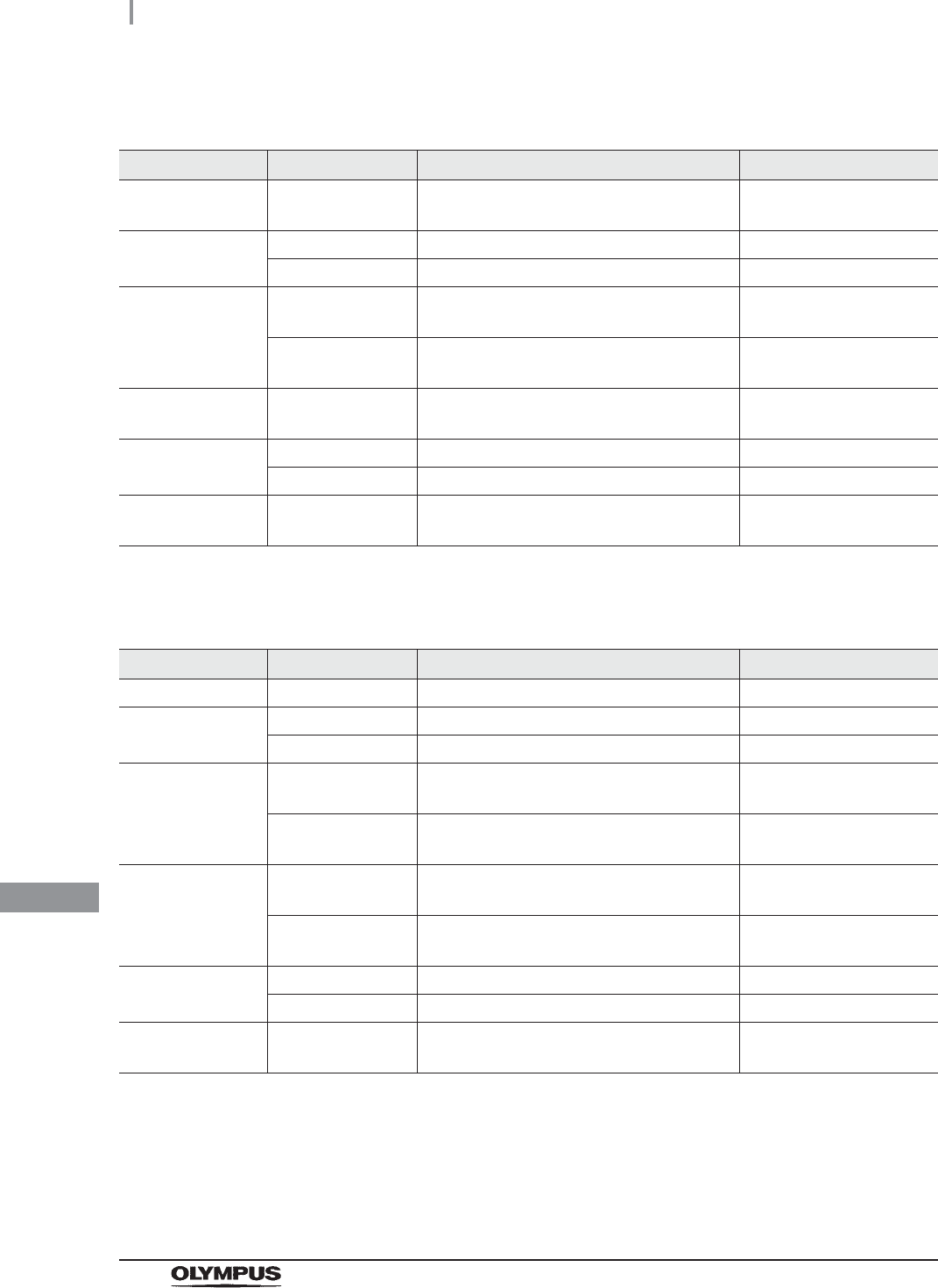
556
11.3 Log management with PC
OER-Elite OPERATION MANUAL
Ch.11
Table 11.15
Table 11.16
Gas filter (tank) replacement records
Major item Minor item Description Examples
Replace Gas Filter
(tank)
Record # Record number 5000, 4999, 4998, …
Date/Time Replaced (Day) Completion date of gas filter replacement 06/01/2017
Replaced (Time) Completion time of gas filter replacement 15:30:30
ID/Name User ID ID number of user who replaced gas filter – (Not input)
1
User Name Name of user who replaced gas filter – (Not input)
User
Filter Info. Lot # Lot number of gas filter – (Not input)
2017/05
AER Info. Model Name Reprocessor name OER-Elite
Serial No. Reprocessor serial number 1234567
Memo Memorandum (Free input by user) – (Not input)
Free input by user
Detergent replacement records
Major item Minor item Description Examples
Replace Detergent Record # Record number 5000, 4999, 4998, …
Date/Time Replaced (Day) Completion date of detergent replacement 06/01/2017
Replaced (Time) Completion time of detergent replacement 09:15:30
ID/Name User ID ID number of user who replaced detergent – (Not input)
1
User Name Name of user who replaced detergent – (Not input)
User
Detergent info. Expiry Expiration date of detergent – (Not input)
09/2017
Lot # Lot number of detergent – (Not input)
0987654321
AER Info. Model Name Reprocessor name OER-Elite
Serial No. Reprocessor serial number 1234567
Memo Memorandum (Free input by user) – (Not input)
Free input by user
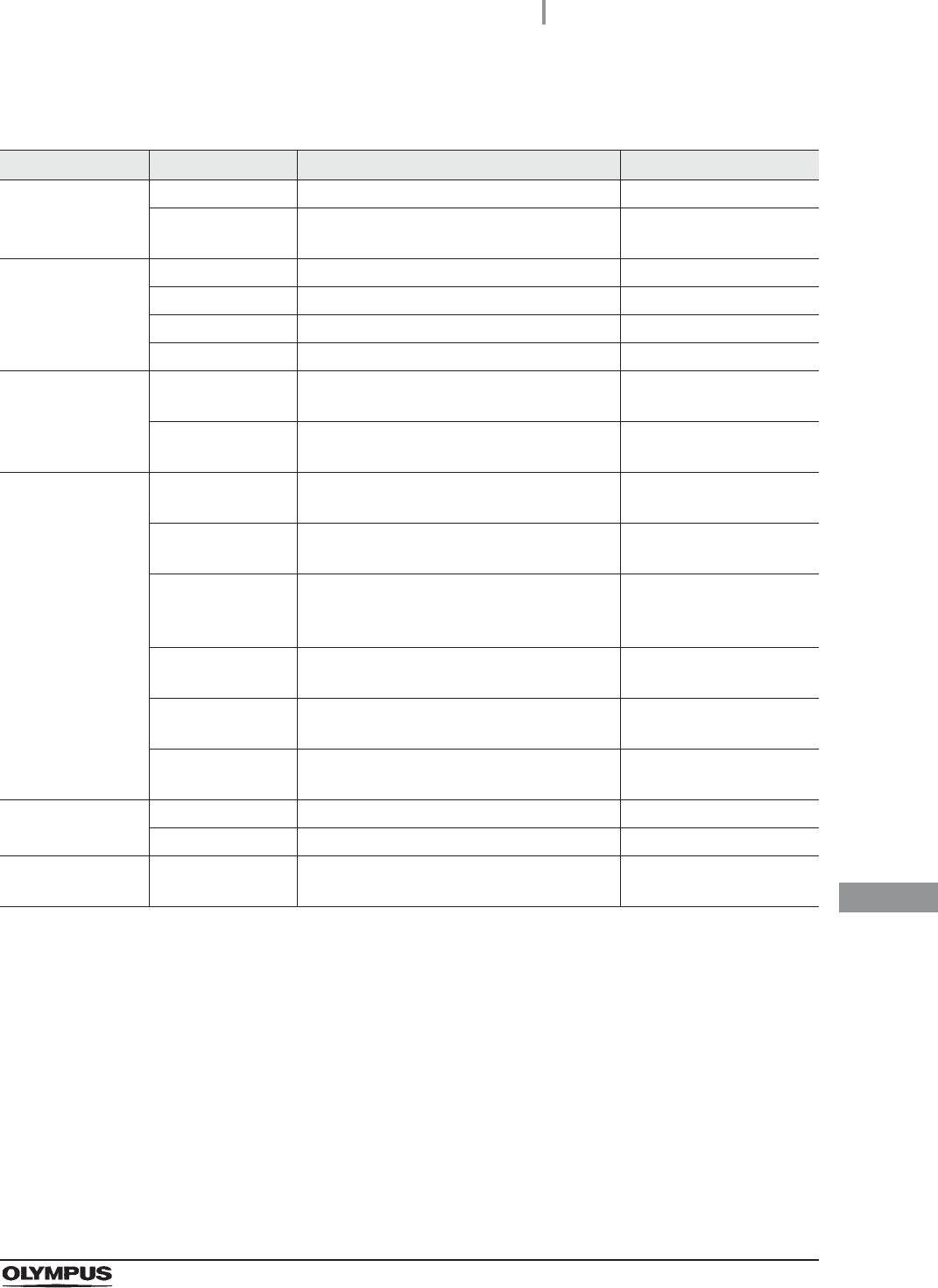
11.3 Log management with PC
557
OER-Elite OPERATION MANUAL
Ch.11
Table 11.17
Water line disinfection records
Major item Minor item Description Examples
Water Line
Disinfection
Record # Record number 5000, 4999, 4998, …
Process Result Result of water line disinfection Complete
E XXX (in case of error)
Date/Time Started (Day) Start date of water line disinfection 06/01/2017
Started (Time) Start time of water line disinfection 08:30:30
Completed (Day) Completion date of water line disinfection 06/01/2017
Completed (Time) Completion time of water line disinfection 10:00:30
ID/Name User ID ID number of user performed water line
disinfection
– (Not input)
1
User Name Name of user performed water line
disinfection
– (Not input)
User
LCG Info. Expiry Expiration date of disinfectant solution – (Not input)
09/2013
Lot # Lot number of disinfectant solution – (Not input)
123456789
MRC Check Result Result of MRC check – (Not input)
Fail
Pass
Temp Disinfectant solution temperature – (Not input)
20
Cycle # Disinfectant cycle count – (Not input)
1
Days Disinfectant day count – (Not input)
5
AER Info. Model Name Reprocessor name OER-Elite
Serial No. Reprocessor serial number 1234567
Memo Memorandum (Free input by user) – (Not input)
Free input by user
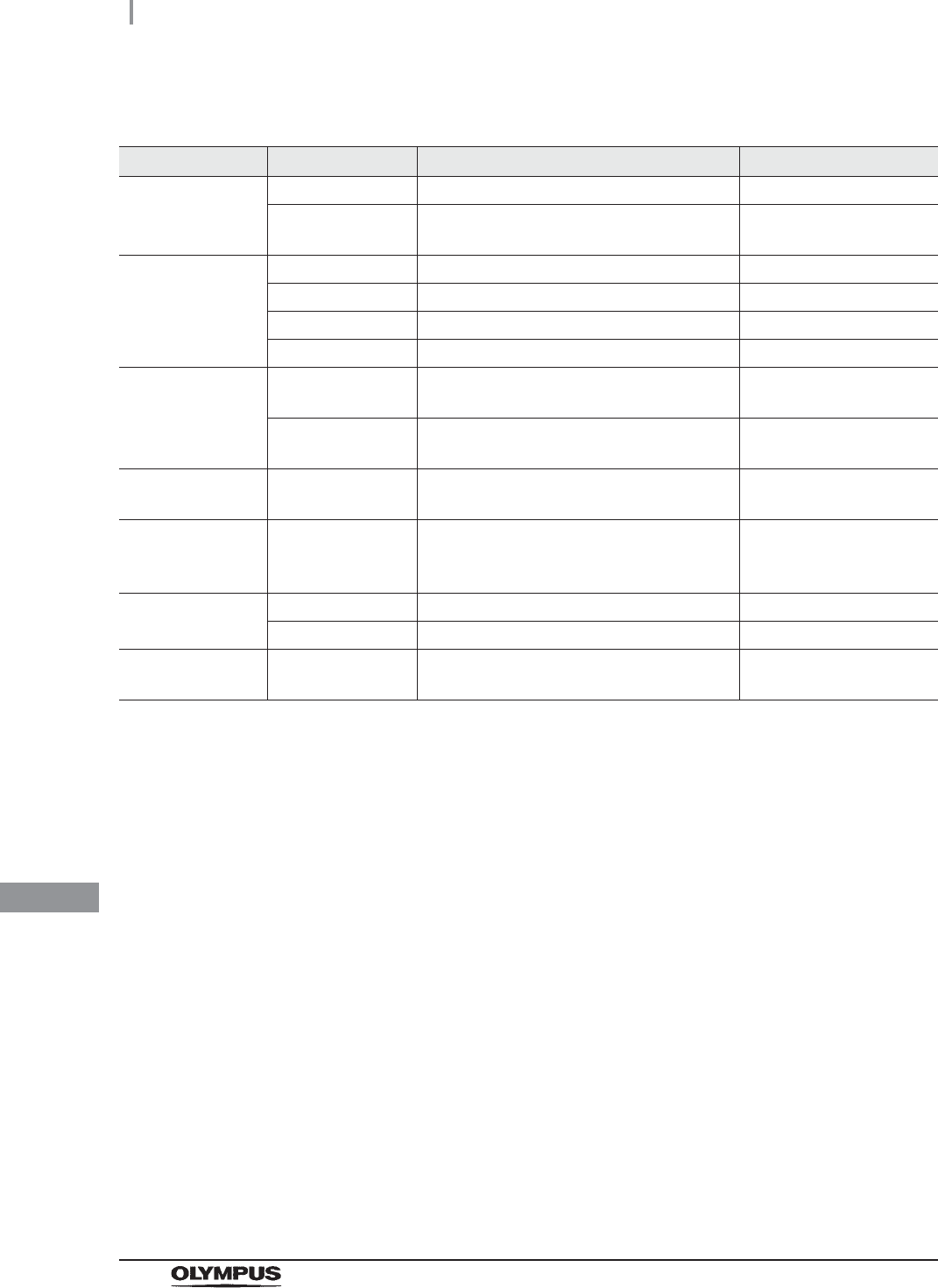
558
11.3 Log management with PC
OER-Elite OPERATION MANUAL
Ch.11
Table 11.18
Alcohol line disinfection records
Major item Minor item Description Examples
Alcohol Line
Disinfection
Record # Record number 5000, 4999, 4998, …
Process Result Result of alcohol line disinfection Complete
E XXX (in case of error)
Date/Time Started (Day) Start date of alcohol line disinfection 06/01/2017
Started (Time) Start time of alcohol line disinfection 08:30:30
Completed (Day) Completion date of alcohol line disinfection 06/01/2017
Completed (Time) Completion time of alcohol line disinfection 10:00:30
ID/Name User ID ID number of user performed alcohol line
disinfection
– (Not input)
1
User Name Name of user performed alcohol line
disinfection
– (Not input)
User
Program Dis Time Disinfection time – (Not input)
10
LCG Info. MRC Check Result Result of MRC check – (Not input)
Fail
Pass
AER Info. Model Name Reprocessor name OER-Elite
Serial No. Reprocessor serial number 1234567
Memo Memorandum (Free input by user) – (Not input)
Free input by user
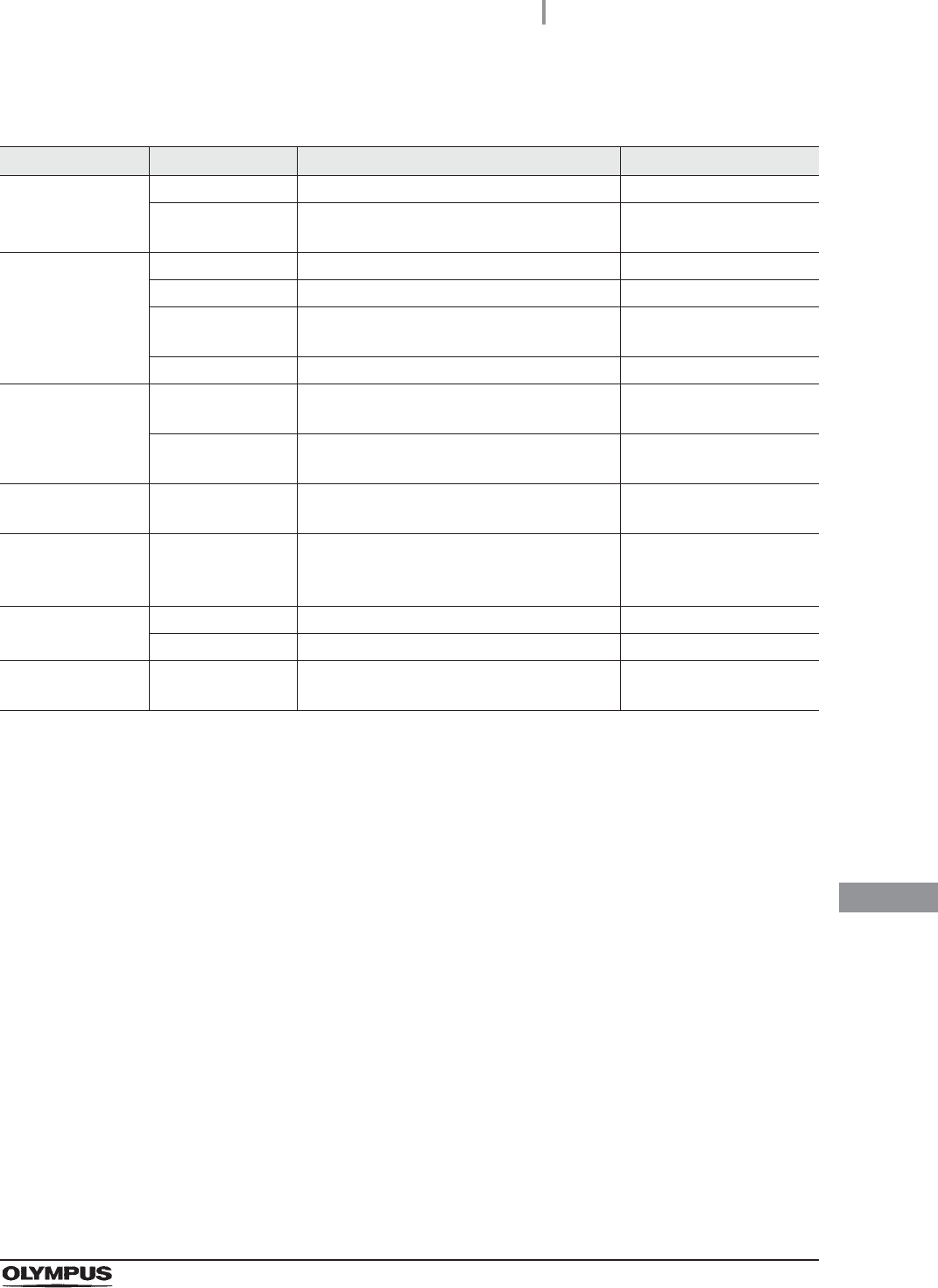
11.3 Log management with PC
559
OER-Elite OPERATION MANUAL
Ch.11
Table 11.19
Detergent line disinfection records
Major item Minor item Description Examples
Detergent Line
Disinfection
Record # Record number 5000, 4999, 4998, …
Process Result Result of detergent line disinfection Complete
E XXX (in case of error)
Date/Time Started (Day) Start date of detergent line disinfection 06/01/2017
Started (Time) Start time of detergent line disinfection 08:30:30
Completed (Day) Completion date of detergent line
disinfection
06/01/2017
Completed (Time) Completion time of detergent line disinfection 10:00:30
ID/Name User ID ID number of user performed detergent line
disinfection
– (Not input)
1
User Name Name of user performed detergent line
disinfection
– (Not input)
User
Program Dis Time Disinfection time – (Not input)
10
LCG Info. MRC Check Result Result of MRC check – (Not input)
Fail
Pass
AER Info. Model Name Reprocessor name OER-Elite
Serial No. Reprocessor serial number 1234567
Memo Memorandum (Free input by user) – (Not input)
Free input by user
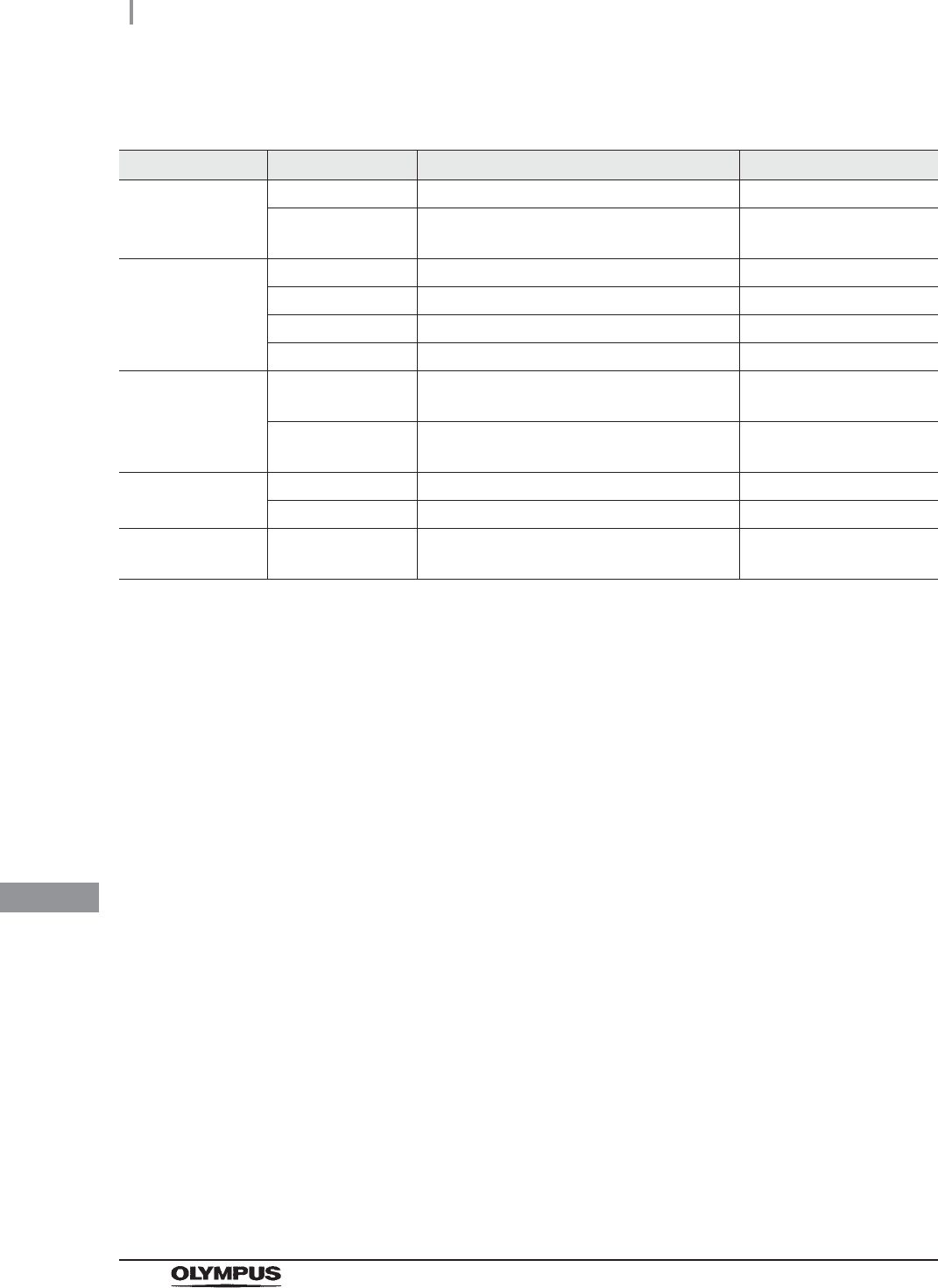
560
11.3 Log management with PC
OER-Elite OPERATION MANUAL
Ch.11
Table 11.20
Rinse records
Major item Minor item Description Examples
Rinse Record # Record number 5000, 4999, 4998, …
Process Result Result of rinse Complete
E XXX (in case of error)
Date/Time Started (Day) Start date of rinse 06/01/2017
Started (Time) Start time of rinse 08:30:30
Completed (Day) Completion date of rinse 06/01/2017
Completed (Time) Completion time of rinse 10:00:30
ID/Name User ID ID number of user performed rinse – (Not input)
1
User Name Name of user performed rinse – (Not input)
User
AER Info. Model Name Reprocessor name OER-Elite
Serial No. Reprocessor serial number 1234567
Memo Memorandum (Free input by user) – (Not input)
Free input by user
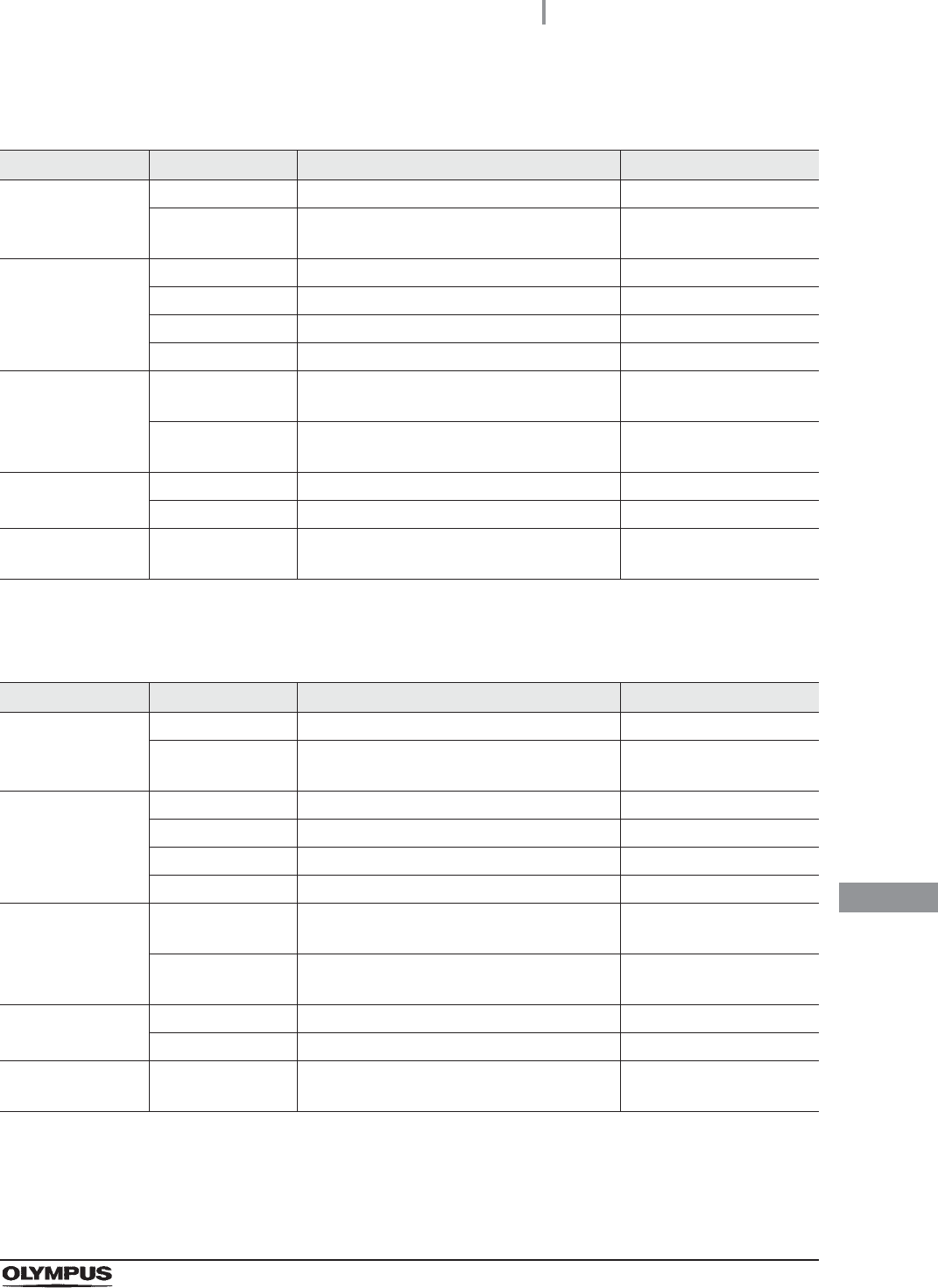
11.3 Log management with PC
561
OER-Elite OPERATION MANUAL
Ch.11
Table 11.21
Table 11.22
Air purge records
Major item Minor item Description Examples
Air Purge Record # Record number 5000, 4999, 4998, …
Process Result Result of air purge Complete
E XXX (in case of error)
Date/Time Started (Day) Start date of air purge 06/01/2017
Started (Time) Start time of air purge 08:30:30
Completed (Day) Completion date of air purge 06/01/2017
Completed (Time) Completion time of air purge 10:00:30
ID/Name User ID ID number of user performed air purge – (Not input)
1
User Name Name of user performed air purge – (Not input)
User
AER Info. Model Name Reprocessor name OER-Elite
Serial No. Reprocessor serial number 1234567
Memo Memorandum (Free input by user) – (Not input)
Free input by user
Alcohol flush records
Major item Minor item Description Examples
Alcohol flush Record # Record number 5000, 4999, 4998, …
Process Result Result of alcohol flush Complete
E XXX (in case of error)
Date/Time Started (Day) Start date of alcohol flush 06/01/2017
Started (Time) Start time of alcohol flush 08:30:30
Completed (Day) Completion date of alcohol flush 06/01/2017
Completed (Time) Completion time of alcohol flush 10:00:30
ID/Name User ID ID number of user performed alcohol flush – (Not input)
1
User Name Name of user performed alcohol flush – (Not input)
User
AER Info. Model Name Reprocessor name OER-Elite
Serial No. Reprocessor serial number 1234567
Memo Memorandum (Free input by user) – (Not input)
Free input by user
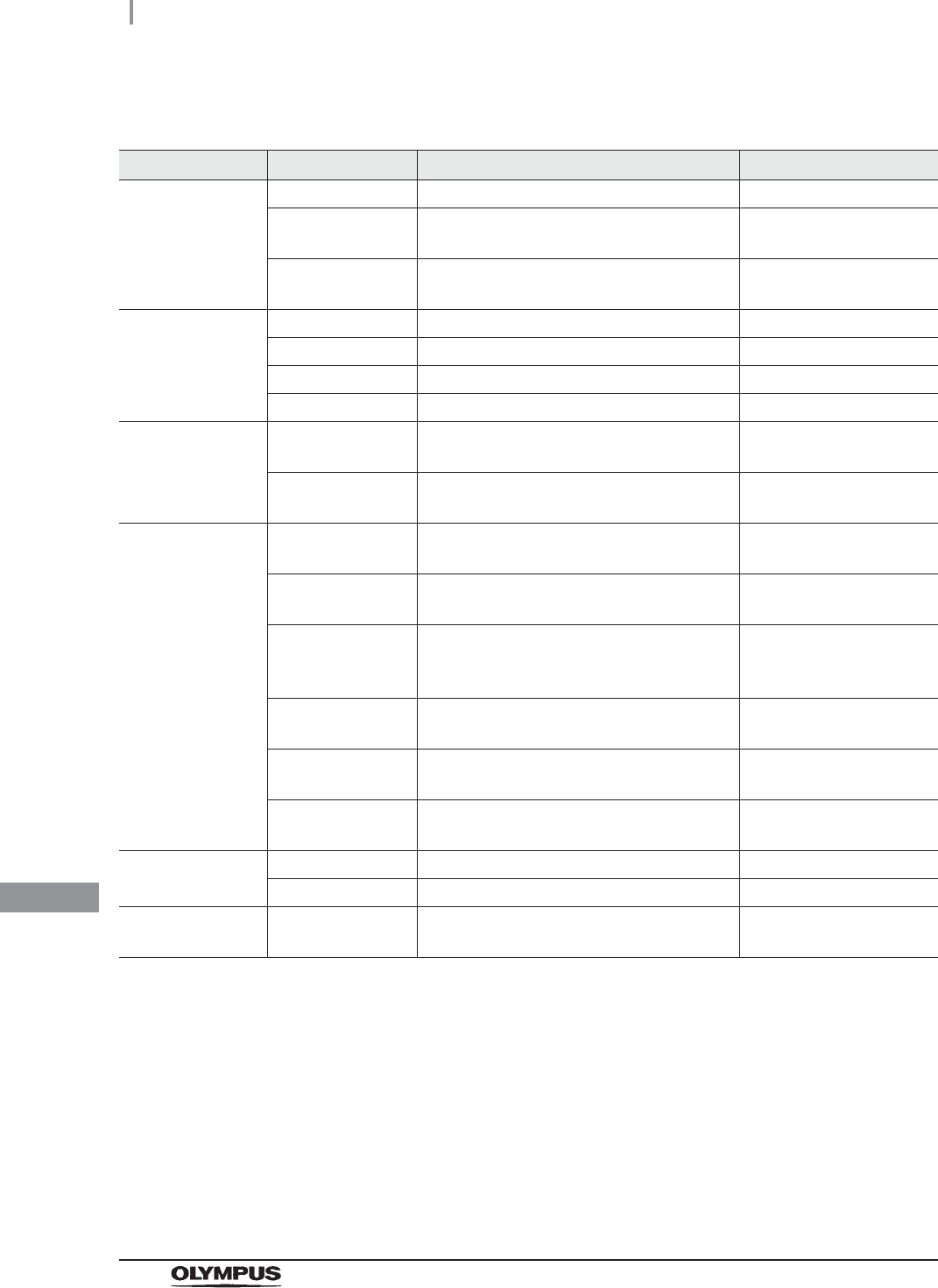
562
11.3 Log management with PC
OER-Elite OPERATION MANUAL
Ch.11
Table 11.23
Self disinfection and water sampling records
Major item Minor item Description Examples
Self Disinfection &
Water Sampling
Record # Record number 5000, 4999, 4998, …
Process Result Result of self-disinfection and water
sampling
Complete
E XXX (in case of error)
Water Sampling Whether water sampling was performed or
not.
– (Not input)
Done
Date/Time Started (Day) Start date of self-disinfection 06/01/2017
Started (Time) Start time of self-disinfection 08:30:30
Completed (Day) Completion date of self-disinfection 06/01/2017
Completed (Time) Completion time of self-disinfection 10:00:30
ID/Name User ID ID number of user performed
self-disinfection
– (Not input)
1
User Name Name of user performed self-disinfection – (Not input)
User
LCG Info. Expiry Expiration date of disinfectant solution – (Not input)
09/2013
Lot # Lot number of disinfectant solution – (Not input)
123456789
MRC Check Result Result of MRC check – (Not input)
Fail
Pass
Temp Disinfectant solution temperature – (Not input)
20
Cycle # Disinfectant cycle count – (Not input)
1
Days Disinfectant day count – (Not input)
5
AER Info. Model Name Reprocessor name OER-Elite
Serial No. Reprocessor serial number 1234567
Memo Memorandum (Free input by user) – (Not input)
Free input by user
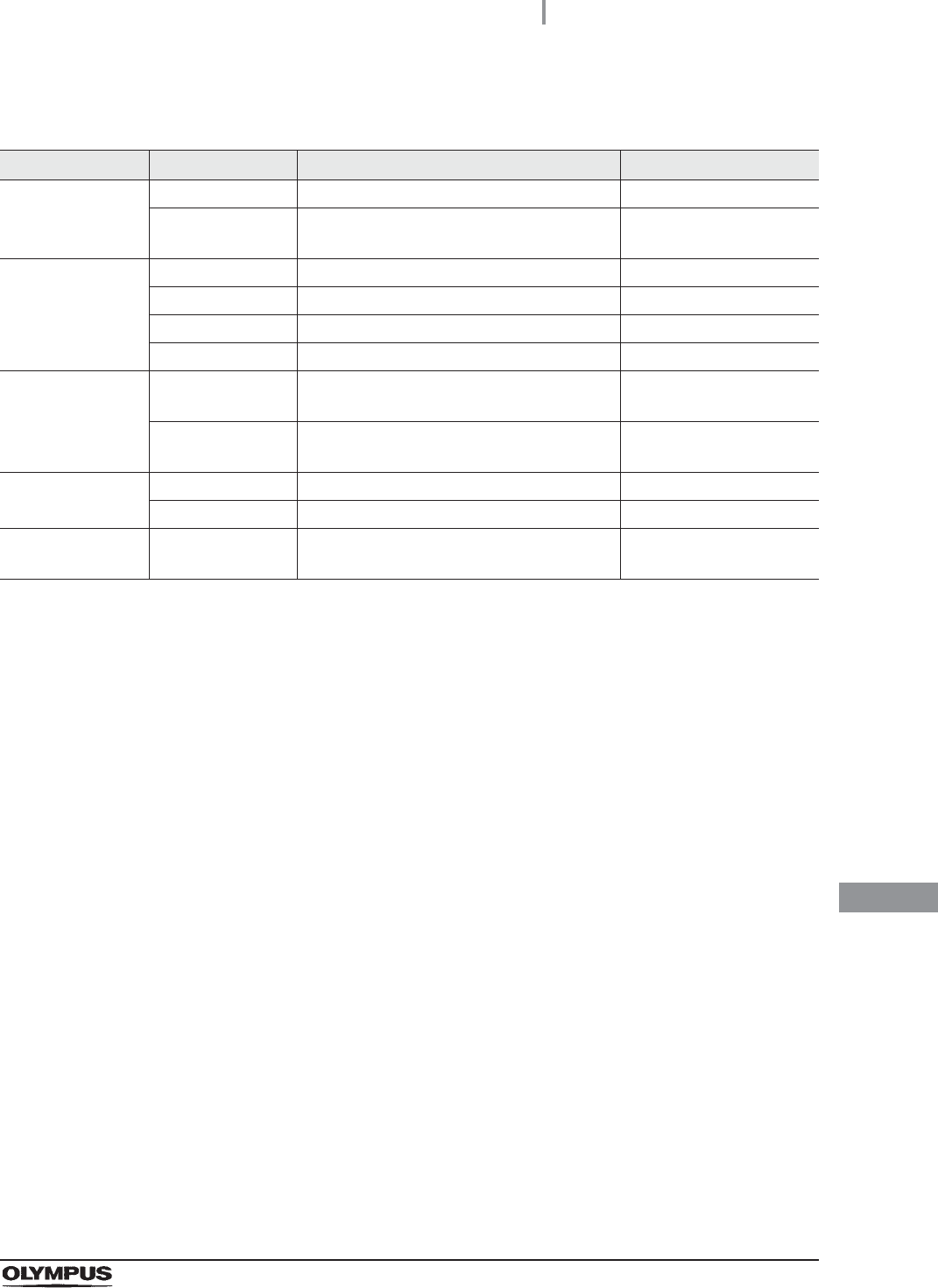
11.3 Log management with PC
563
OER-Elite OPERATION MANUAL
Ch.11
Table 11.24
Portable memory records
Major item Minor item Description Examples
Portable Memory Record # Record number 5000, 4999, 4998, …
Process Result Result of portable memory output Complete
E XXX (in case of error)
Date/Time Started (Day) Start date of portable memory output 06/01/2017
Started (Time) Start time of portable memory output 08:30:30
Completed (Day) Completion date of portable memory output 06/01/2017
Completed (Time) Completion time of portable memory output 10:00:30
ID/Name User ID ID number of user performed portable
memory output
– (Not input)
1
User Name Name of user performed portable memory
output
– (Not input)
User
AER Info. Model Name Reprocessor name OER-Elite
Serial No. Reprocessor serial number 1234567
Memo Memorandum (Free input by user) – (Not input)
Free input by user
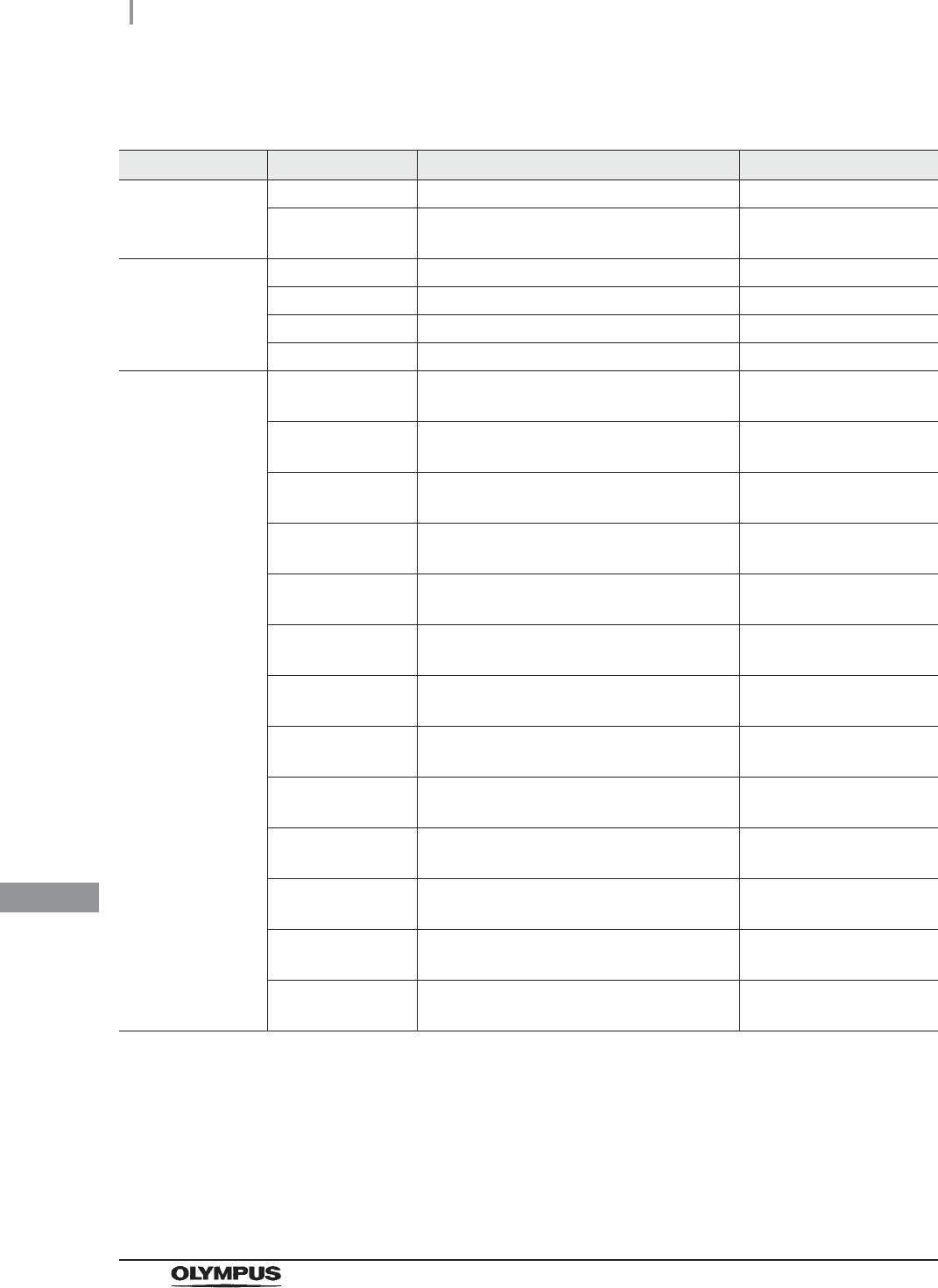
564
11.3 Log management with PC
OER-Elite OPERATION MANUAL
Ch.11
Error records
Major item Minor item Description Examples
Error Record # Record number 5000, 4999, 4998, …
Error code Error code of error – (Not input)
EXXX (in case of error)
Date/Time Started (Day) Start date of rinse 06/01/2017
Started (Time) Start time of rinse 08:30:30
Canceled (Day) Date of occurrence of error 06/01/2017
Canceled (Time) Time of occurrence of error 10:00:30
ID/Name Scope No Endoscope number 1 (First endoscope)
2 (Second endoscope)
Scope Model Model number of endoscope GIF-H190
– (Not input)
Scope ID Endoscope serial number 12800542
– (Not input)
User ID ID number of user installing the
endoscope(s)
– (Not input)
1
User Name Name of user installing the endoscope(s) – (Not input)
User
Physician ID ID number of physician – (Not input)
1
Physician Name Name of physician – (Not input)
Doctor
Patient ID ID number of patient – (Not input)
1
Patient Name Name of patient – (Not input)
Patient
Procedure ID ID number of procedure – (Not input)
0123456
Procedure Name Name of procedure – (Not input)
ERCP
User3 Name Name of user removing the endoscope(s) – (Not input)
User
User3 ID ID number of user removing the
endoscope(s)
– (Not input)
1
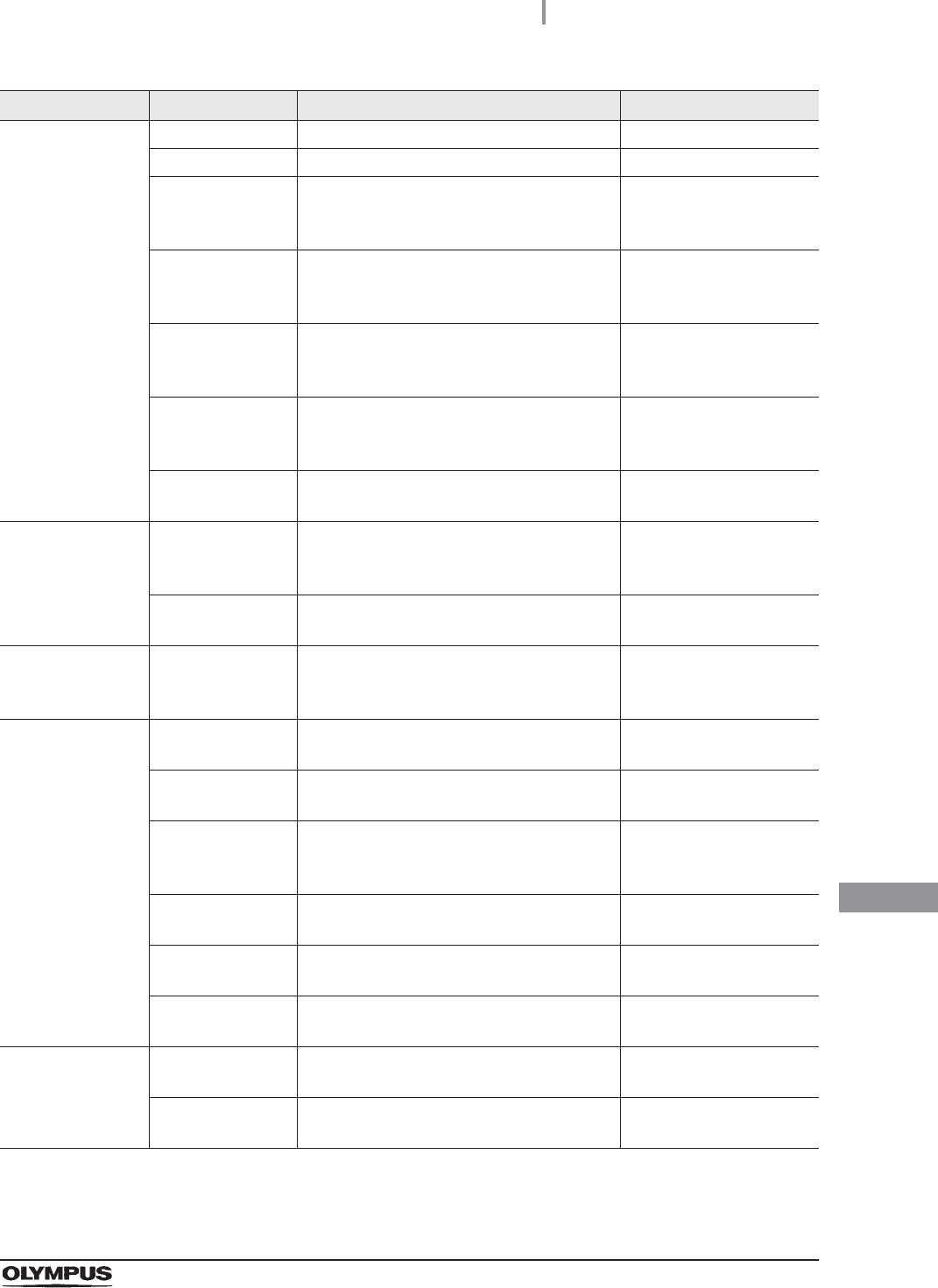
11.3 Log management with PC
565
OER-Elite OPERATION MANUAL
Ch.11
Program Info. Cln time Cleaning time (min.) 3
Dis Time Disinfection time (min.) 7
ALT Auto leak test setting – (Not input)
ON
OFF
Heat LCG Heat LCG setting – (Not input)
ON
OFF
Alcohol Flush Alcohol flush setting – (Not input)
ON
OFF
Channel Monitor Channel Monitoring setting – (Not input)
Full,
Partial
Program No. Program number – (Not input)
1, 2, 3, 4
Check Leak Test (Sink) Input result of leak test before manual
cleaning
– (Not input)
Pass
Fail
Manual Cleaning Input result of manual cleaning –
Done
Function Result Leak Test Result Result of leak test during the reprocessing – (Not input)
Fail
Pass
LCG Info. Expiry Expiration date of disinfectant solution – (Not input)
2017/05
Lot # Lot number of disinfectant solution – (Not input)
123456789
MRC Check Result Result of MRC check – (Not input)
Fail
Pass
Temp Disinfectant solution temperature – (Not input)
20
Cycle # Disinfectant cycle count – (Not input)
1
Days Disinfectant day count – (Not input)
1
Detergent Info. Expiry Expiry of the detergent solution – (Not input)
09/15
Lot # Lot number of the detergent solution – (Not input)
DD1234
Major item Minor item Description Examples
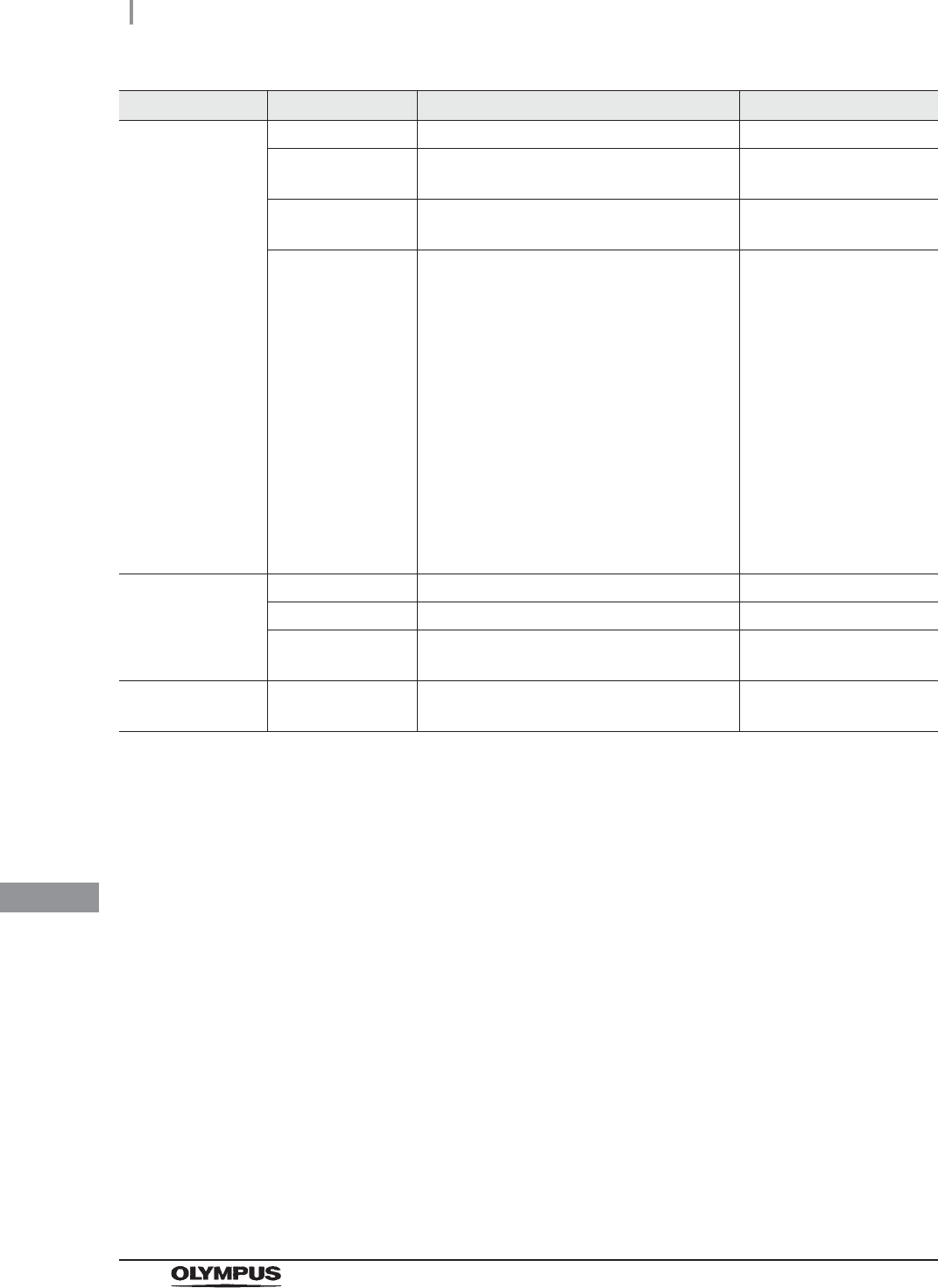
566
11.3 Log management with PC
OER-Elite OPERATION MANUAL
Ch.11
Table 11.25
ErrorDetails Process Name Process in which error is generated Cleaning, Heat LCG, etc.
Process No. Number associated with the process
(number is hexadecimal)
– (Not input)
0001, 0002
Process Time Elapsed time of the process – (Not input)
00:03:00
Error Information
1 – 38
Error value 1 – 38 – (Not input)
Pass
Fail
On
Off
No Connect
Connect
Unknown
Flow Side
Water Side
Moving
Actual measurement value
of each error(e.g., decimal
place from first to third)
AER Info. Model Name Reprocessor name OER-Elite
Serial No. Reprocessor serial number 1234567
Total Count Total accumulated of reprocessing process
count
4000
Memo Memorandum (Free input by user) – (Not input)
Free input by user
Major item Minor item Description Examples
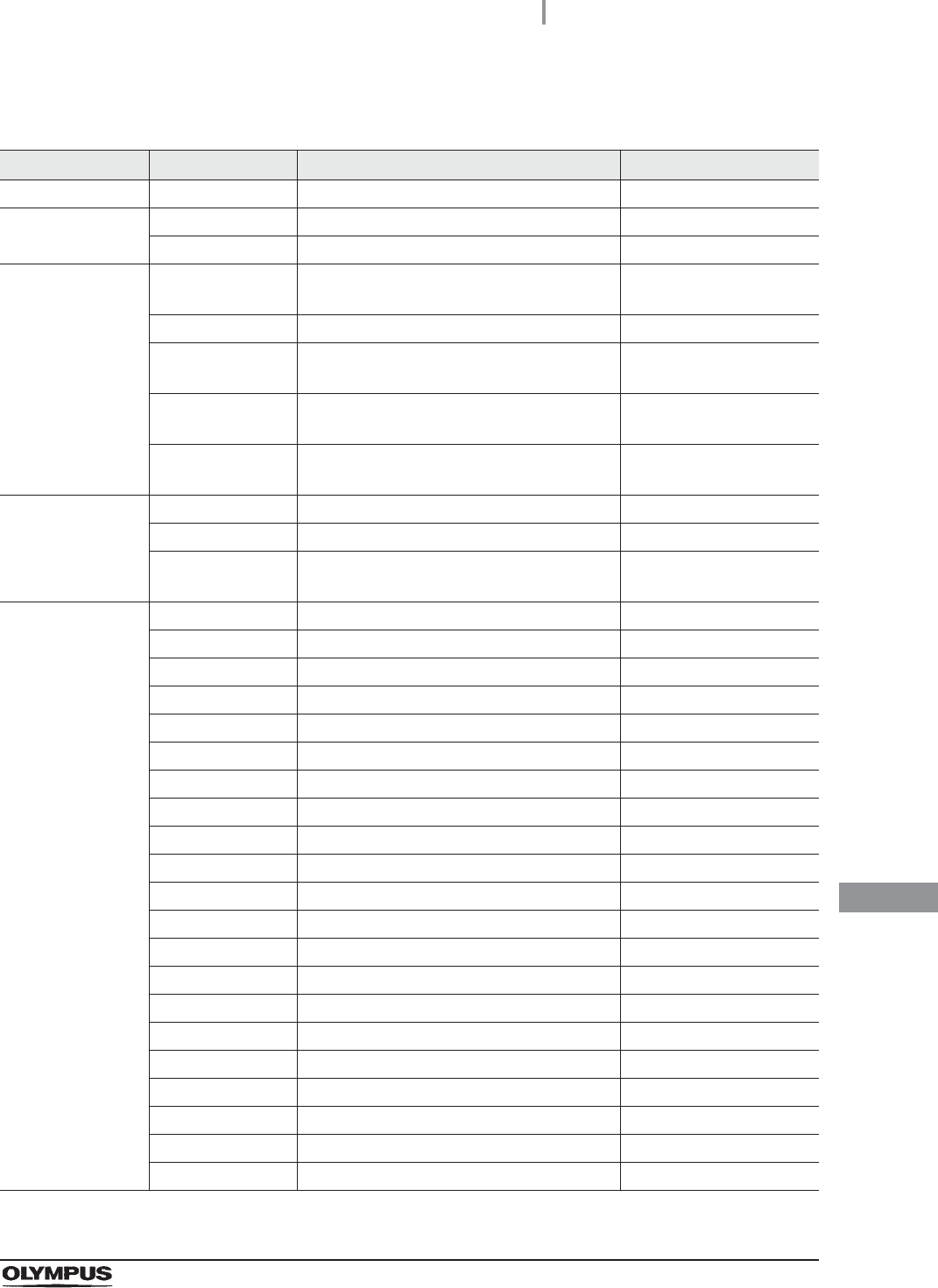
11.3 Log management with PC
567
OER-Elite OPERATION MANUAL
Ch.11
Periodic Maintenance and Repair
Major item Minor item Description Examples
Maintenance Record # Record number 5000, 4999, 4998, …
Date/Time Working (Day) Working date of Maintenance 06/01/2017
Working (Time) Working start time of Maintenance 8:30:30
Service Program Type Detail for working Periodic Maintenance
Repair
Person Working person name – (Not input), Person name
Scheduled PM
Cycle
Next Periodic Maintenance date 25000
Scheduled PM
Date
Number of Periodic Maintenance 06/01/2018
Maintenance Total
Count
Number of Periodic Maintenance 0
AER Info. Model Name Reprocessor name OER-Elite
Serial No. Reprocessor serial number 1234567
Total Count Total number of reprocessing processes
performed
1
Parts Operation
Count/Time
Water Supply Valve Water Supply Valve count 1
Channel Valve A1 Channel Valve A1 count 1
Channel Valve B1 Channel Valve B1 count 1
Channel Valve C1 Channel Valve C1 count 1
Channel Valve D1 Channel Valve D1 count 1
Channel Valve A2 Channel Valve A2 count 1
Channel Valve B2 Channel Valve B2 count 1
Channel Valve C2 Channel Valve C2 count 1
Channel Valve D2 Channel Valve D2 count 1
Bypass Valve Bypass Valve count 1
Adjust Valve Adjust Valve count 1
Relief Shutoff Valve Relief Shutoff Valve count 1
Pump Valve Pump Valve count 1
ALT Valve (Front) ALT Valve (Front) count 1
ALT Valve (Back) ALT Valve (Back) count 1
Drain Valve Drain Valve count 1
Collection Valve Collection Valve count 1
Three Port Valve Three Port Valve count 1
Alcohol Valve Alcohol Valve count 1
Channel Pump Channel Pump count 1
Channel Pump Channel Pump time (min) 1
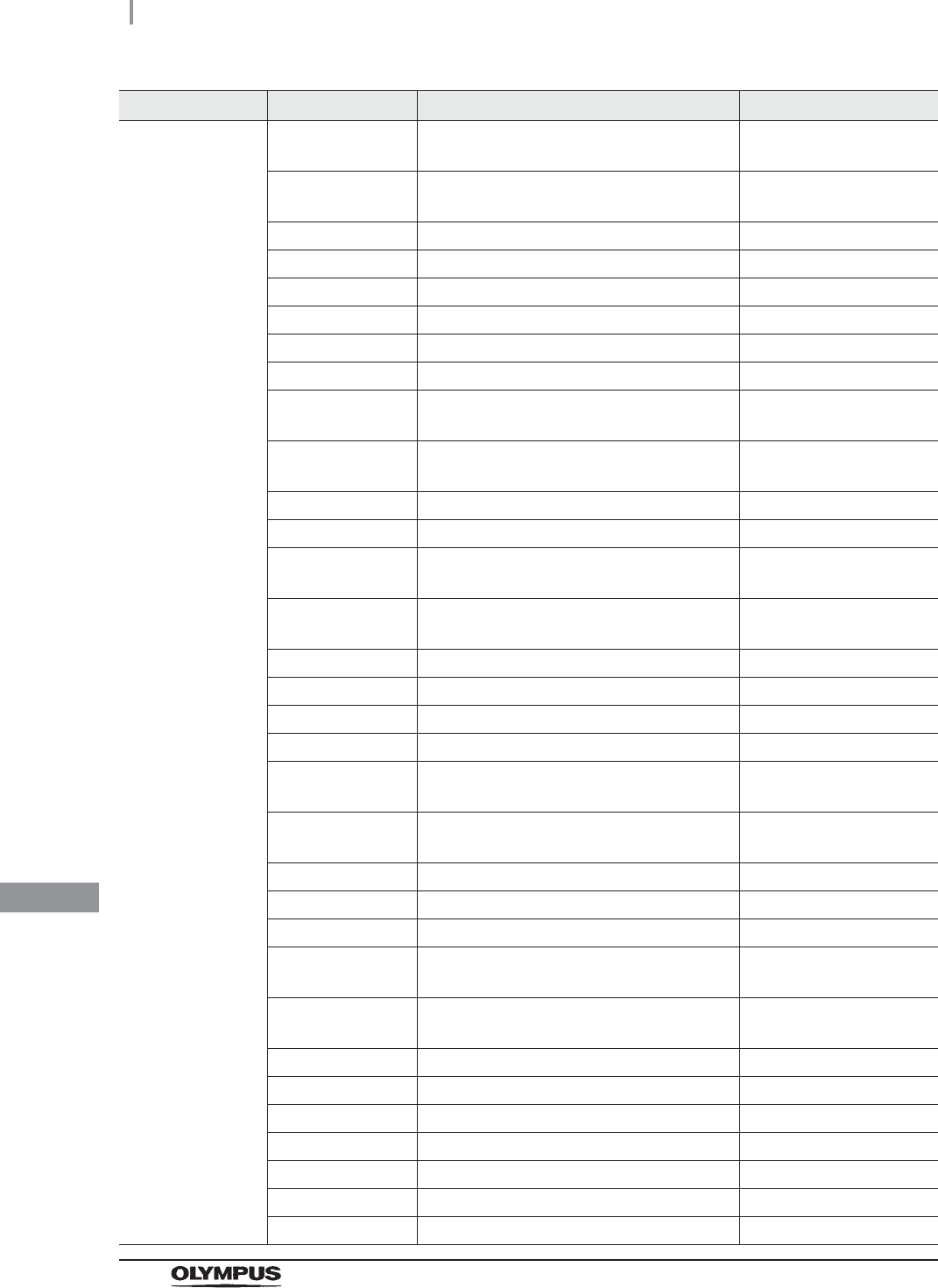
568
11.3 Log management with PC
OER-Elite OPERATION MANUAL
Ch.11
Parts Operation
Count/Time
Disinfectant
Solution Pump
Disinfectant Solution Pump count 1
Disinfectant
Solution Pump
Disinfectant Solution Pump time (min) 1
Drain Pump Drain Pump count 1
Drain Pump Drain Pump time (min) 1
Circulation Pump Circulation Pump count 1
Circulation Pump Circulation Pump time (min) 1
Alcohol Pump Alcohol Pump count 1
Alcohol Pump Alcohol Pump time (min) 1
Alkali Detergent
Pump
Alkali Detergent Pump count 1
Alkali Detergent
Pump
Alkali Detergent Pump time (min) 1
Compressor Compressor count 1
Compressor Compressor time (min) 1
Ultrasonic
Transducer
Ultrasonic Transducer count 1
Ultrasonic
Transducer
Ultrasonic Transducer time (min) 1
Basin Heater Basin Heater count 1
Basin Heater Basin Heater time (min) 1
Tank Heater Tank Heater count 1
Tank Heater Tank Heater time (min) 1
Solenoid Lock for
Lid
Solenoid Lock for Lid count 1
Solenoid Lock for
Cassette
Solenoid Lock for Cassette count 1
Print Print count 1
Start Button Start Button count 1
Stop Button Stop Button count 1
Heat LCG Timer
Button
Heat LCG Timer Button count 1
Touch Screen
Operation
Touch Screen Operation count 1
ALT Function ALT Function count 1
MLT Function MLT Function count 1
MLT Function MLT Function time (min) 1
ALT Self-Check ALT Self-Check count 1
LCD Backlight LCD Backlight time (min) 1
Battery Working Battery Working Days 1
Barcode Scan Barcode Scan count 1
Major item Minor item Description Examples
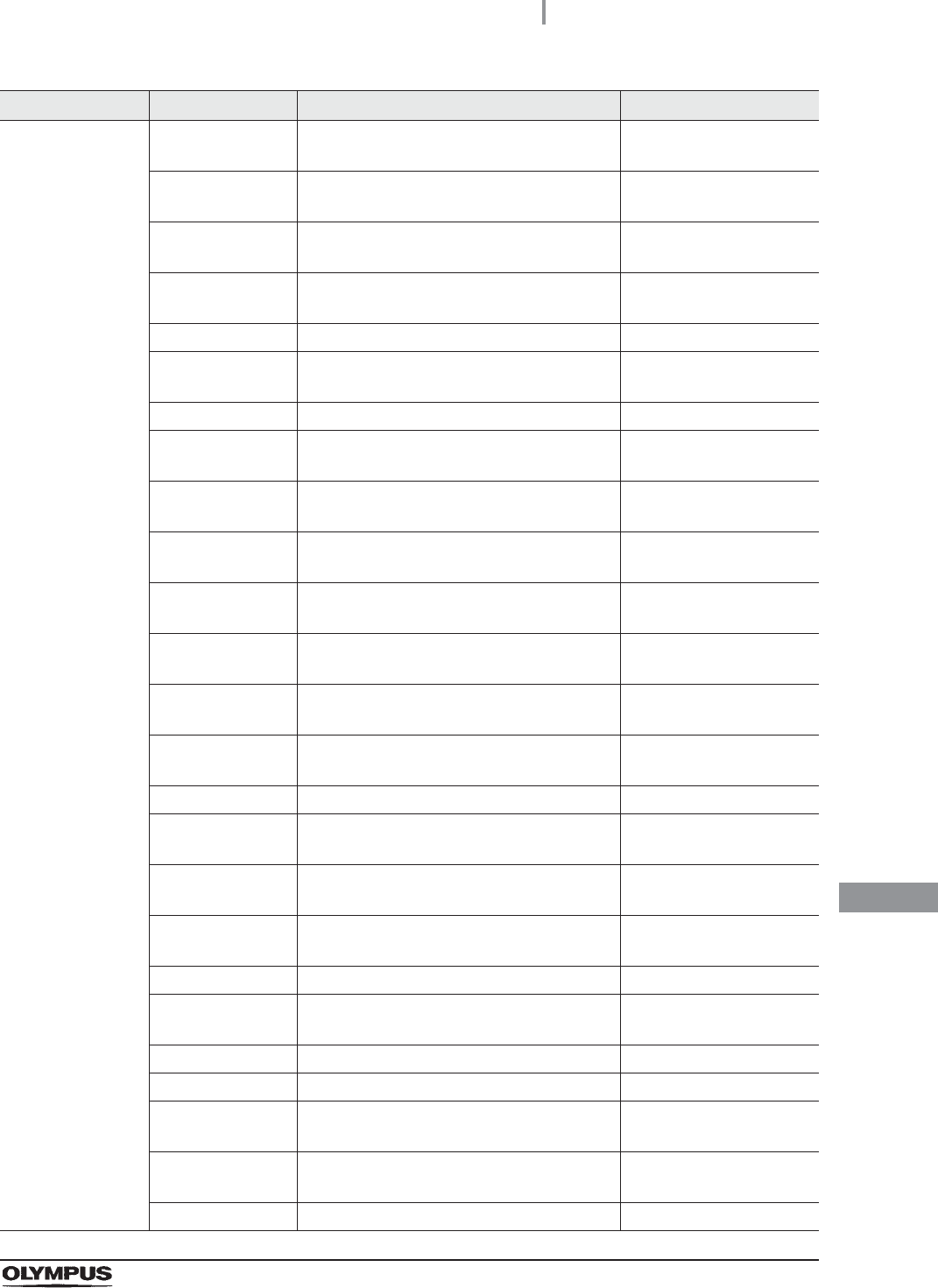
11.3 Log management with PC
569
OER-Elite OPERATION MANUAL
Ch.11
Parts Replacement Water Supply Valve With or without replacement for water supply
valve
0, 1
Channel Valve 1 With or without replacement for Channel
Valve 1
0, 1
Channel Valve 2 With or without replacement for Channel
Valve 2
0, 1
Bypass Valve With or without replacement for Bypass
Valve
0, 1
Adjust Valve With or without replacement for Adjust Valve 0, 1
Relief Shutoff Valve With or without replacement for Relief
Shutoff Valve
0, 1
Pump Valve With or without replacement for Pump Valve 0, 1
ALT Valve (Front) With or without replacement for ALT Valve
(Front)
0, 1
ALT Valve (Back) With or without replacement for ALT Valve
(Back)
0, 1
Switching Valve With or without replacement for Switching
Valve
0, 1
Three Port Valve With or without replacement for Three Port
Valve
0, 1
Alcohol Valve With or without replacement for Alcohol
Valve
0, 1
Channel Pump With or without replacement for Channel
Pump
0, 1
Disinfectant
Solution Pump
With or without replacement for Disinfectant
Solution Pump
0, 1
Drain Pump With or without replacement for Drain Pump 0, 1
Circulation Pump With or without replacement for Circulation
Pump
0, 1
Alcohol Pump With or without replacement for Alcohol
Pump
0, 1
Alkali Detergent
Pump
With or without replacement for Alkali
Detergent Pump
0, 1
Compressor With or without replacement for Compressor 0, 1
Ultrasonic
Transducer
With or without replacement for Ultrasonic
Transducer
0, 1
Basin Heater With or without replacement for Basin Heater 0, 1
Tank Heater With or without replacement for Tank Heater 0, 1
Solenoid Lock for
Lid
With or without replacement for Solenoid
Lock for Lid
0, 1
Solenoid Lock for
Cassette
With or without replacement for Solenoid
Lock for Cassette
0, 1
Printer With or without replacement for Printer 0, 1
Major item Minor item Description Examples
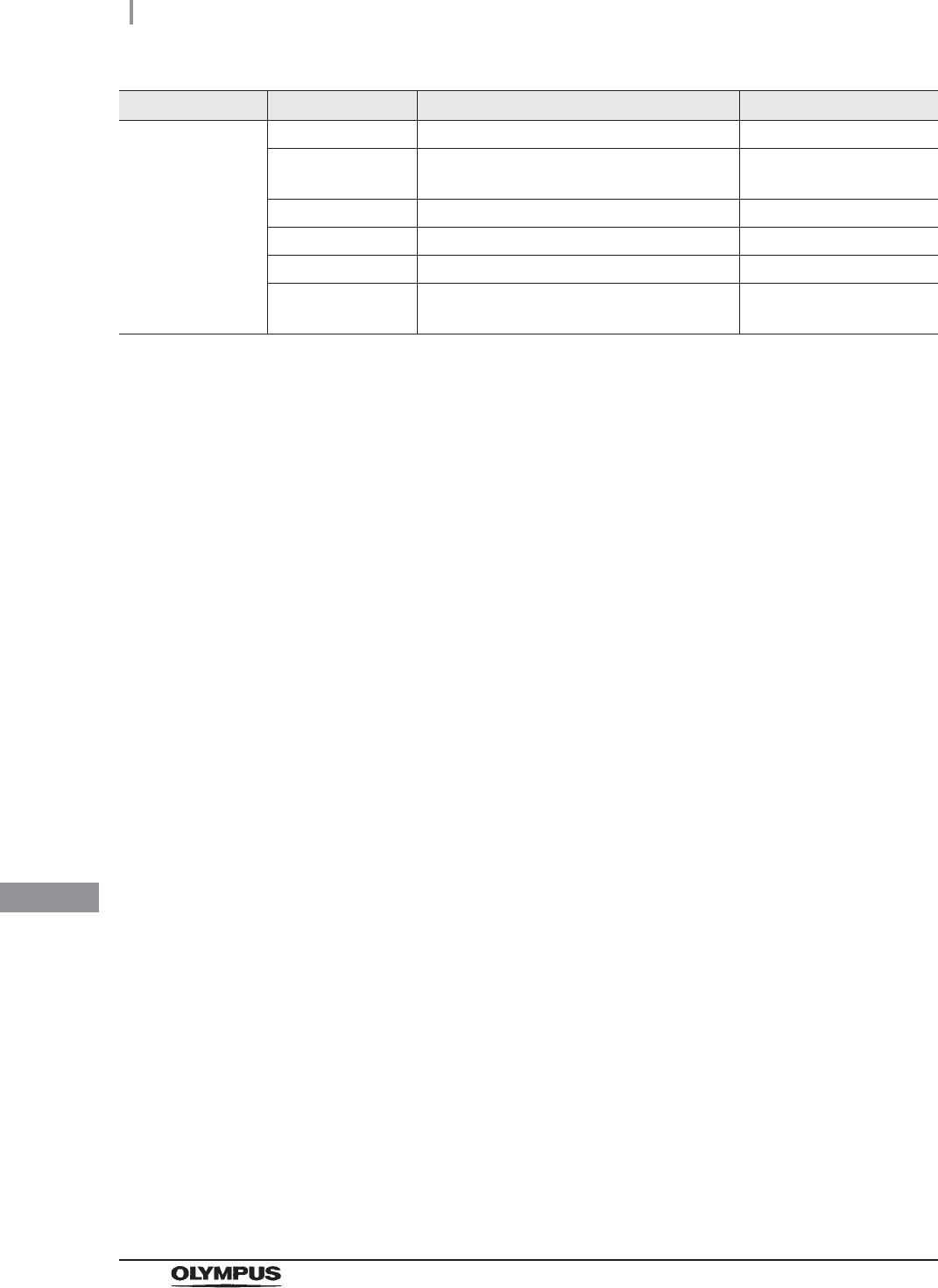
570
11.3 Log management with PC
OER-Elite OPERATION MANUAL
Ch.11
Table 11.26
Parts Replacement Panel Switch With or without replacement for Panel Switch 0, 1
Touch Screen With or without replacement for Touch
Screen
0, 1
ALT With or without replacement for ALT 0, 1
LCD With or without replacement for LCD 0, 1
Battery With or without replacement for Battery 0, 1
Barcode Scanner With or without replacement for Barcode
Scanner
0, 1
Major item Minor item Description Examples
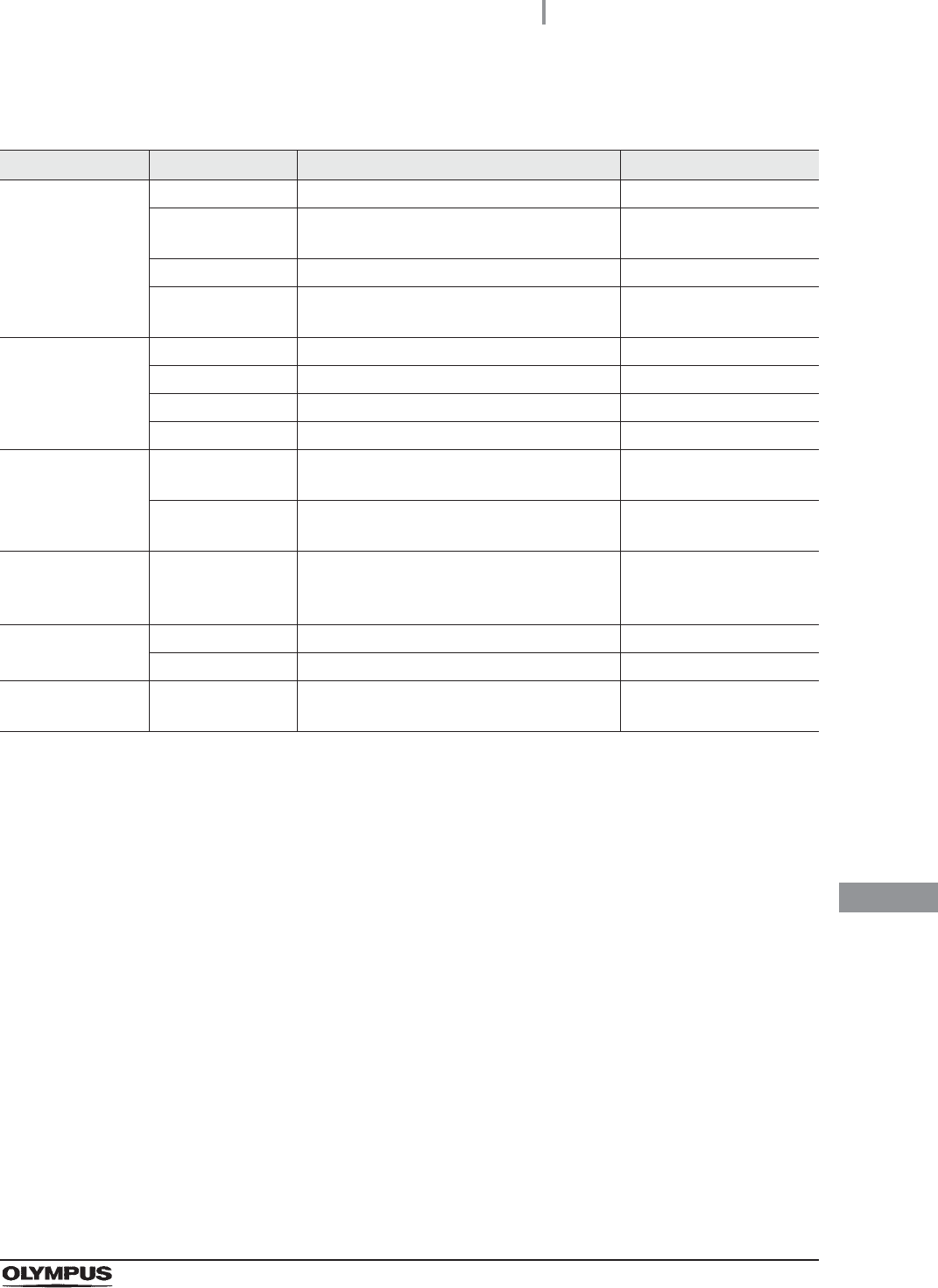
11.3 Log management with PC
571
OER-Elite OPERATION MANUAL
Ch.11
Table 11.27
ALT self check records
Major item Minor item Description Examples
ALT Self-Check Record # Record number 5000, 4999, 4998, …
Process Result Result of ALT self check Complete
E XXX (in case of error)
Option “Periodic (Auto)” or “Manual” is represented Periodic (Auto), Manual
Atmospheric
Pressure
Atmospheric pressure during ALT self check – (Not input)
101.3 kPa
Date/Time Started (Day) Start date of ALT self check 06/01/2017
Started (Time) Start time of ALT self check 08:30:30
Completed (Day) Completion date of ALT self check 06/01/2017
Completed (Time) Completion time of ALT self check 10:00:30
ID/Name User ID ID number of user performed ALT self check – (Not input)
1
User Name Name of user performed ALT self check – (Not input)
User
Function Result Self-Check Result Result of ALT self check – (Not input)
Pass
Fail
AER Info. Model Name Reprocessor name OER-Elite
Serial No. Reprocessor serial number 1234567
Memo Memorandum (Free input by user) – (Not input)
Free input by user
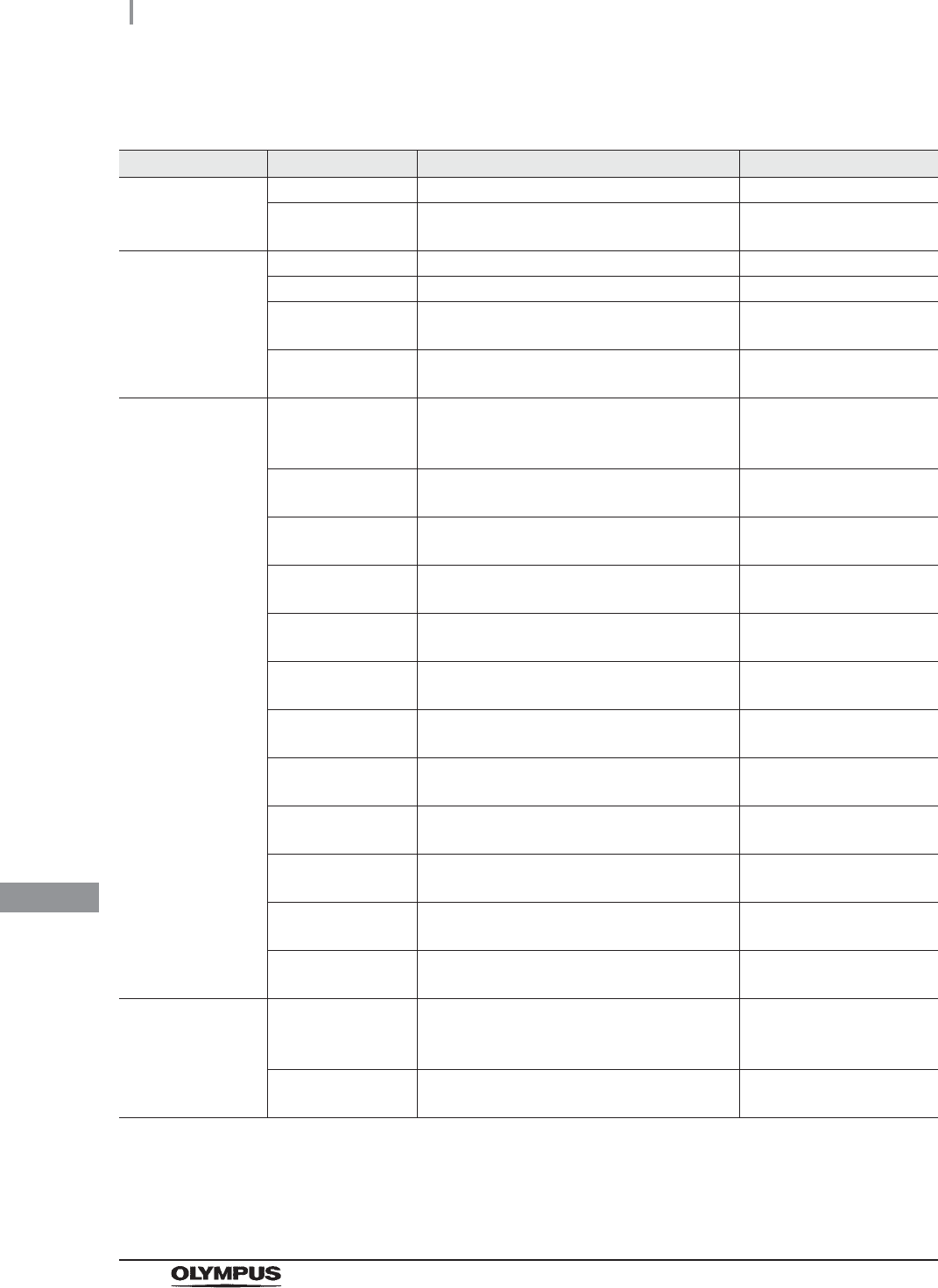
572
11.3 Log management with PC
OER-Elite OPERATION MANUAL
Ch.11
Leaking scope decontamination records
Major item Minor item Description Examples
Leaking Scope
Decontamination
Record # Record number 5000, 4999, 4998, …
Process Result Result of leaking scope decontamination Complete
E XXX (in case of error)
Date/Time Started (Day) Start date of leaking scope decontamination 06/01/2017
Started (Time) Start time of leaking scope decontamination 08:30:30
Completed (Day) Completion date of leaking scope
decontamination
06/01/2017
Completed (Time) Completion time of leaking scope
decontamination
10:00:30
ID/Name Scope Model Model number of endoscope. GIF-H190
Master (Master card input)
– (Not input)
Scope ID Endoscope serial number 12800542
– (Not input)
User ID ID number of user performed portable
memory output
– (Not input)
1
User Name Name of user performed portable memory
output
– (Not input)
User
Physician ID ID number of physician – (Not input)
1
Physician Name Name of physician – (Not input)
Physician
Patient ID ID number of patient – (Not input)
1
Patient Name Name of patient – (Not input)
Patient
Procedure ID ID number of procedure – (Not input)
0123456
Procedure Name Name of procedure – (Not input)
ERCP
User 2 Name Name of user removing the endoscope – (Not input)
User
User 2 ID ID number of user removing the endoscope – (Not input)
1
Check Leak Test (Sink) Input result of leak test before manual
cleaning
– (Not input)
Pass
Fail
Manual Cleaning Input result of manual cleaning – (Not input)
Done
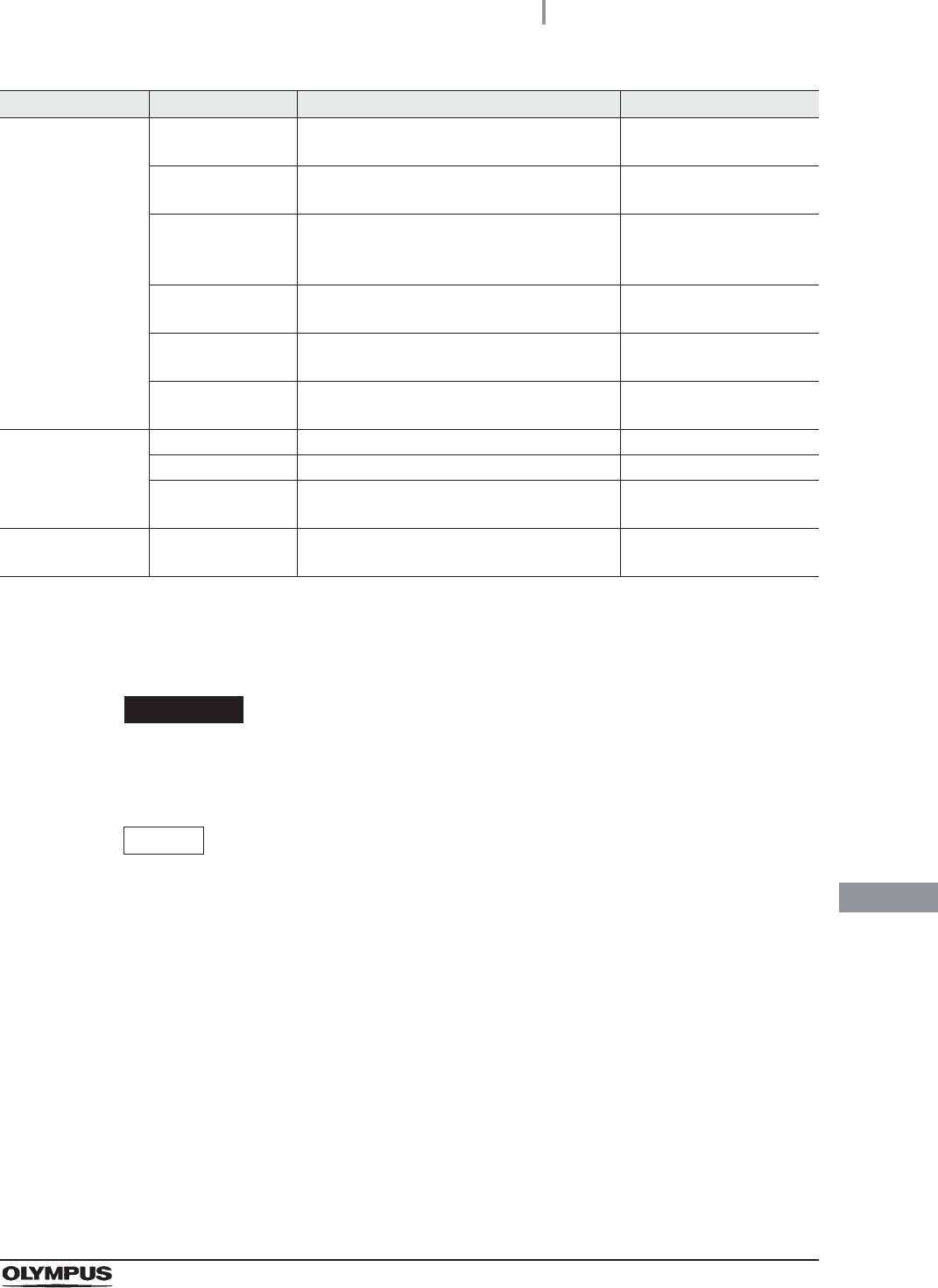
11.3 Log management with PC
573
OER-Elite OPERATION MANUAL
Ch.11
Table 11.28
Managing records on PC
CAUTION
The reprocessing data copied and saved in the “BackUp” folder in the PC becomes
the master data. Do not alter the master data.
NOTE
• For the operating environment of the portable memory, see the instructions
provided with it. To manage the record at the facility the use of a PC installed with
application software such as spreadsheet software that enables editing of a CSV
file is recommended.
• If a file exists in the “Work” folder in the portable memory from which data is
downloaded, a number is appended to the end of the filename
(Example: 2120_02-01_1700_OER-Elite_2700000_Reprocessing_00010(2).csv).
This number is appended to prevent the edited file in the PC from being
overwritten.
• After transferring data in the PC, delete the “OER-Elite” folder in the portable
memory. Otherwise, there would be a possibility that a file having a name identical
to a file already existing in the “Work” folder in the PC is saved with the same name
except for the number appended to the end of the filename.
LCG Info. Expiry Expiration date of disinfectant solution – (Not input)
07/01/2017
Lot # Lot number of disinfectant solution – (Not input)
123456789
MRC Check Result Result of MRC check – (Not input)
Fail
Pass
Temp Disinfectant solution temperature – (Not input)
20
Cycle # Disinfectant cycle count – (Not input)
1
Days Disinfectant day count – (Not input)
1
AER Info. Model Name Reprocessor name OER-Elite
Serial No. Reprocessor serial number 1234567
Total Count Total accumulated of reprocessing process
count
4000
Memo Memorandum (Free input by user) – (Not input)
Free input by user
Major item Minor item Description Examples
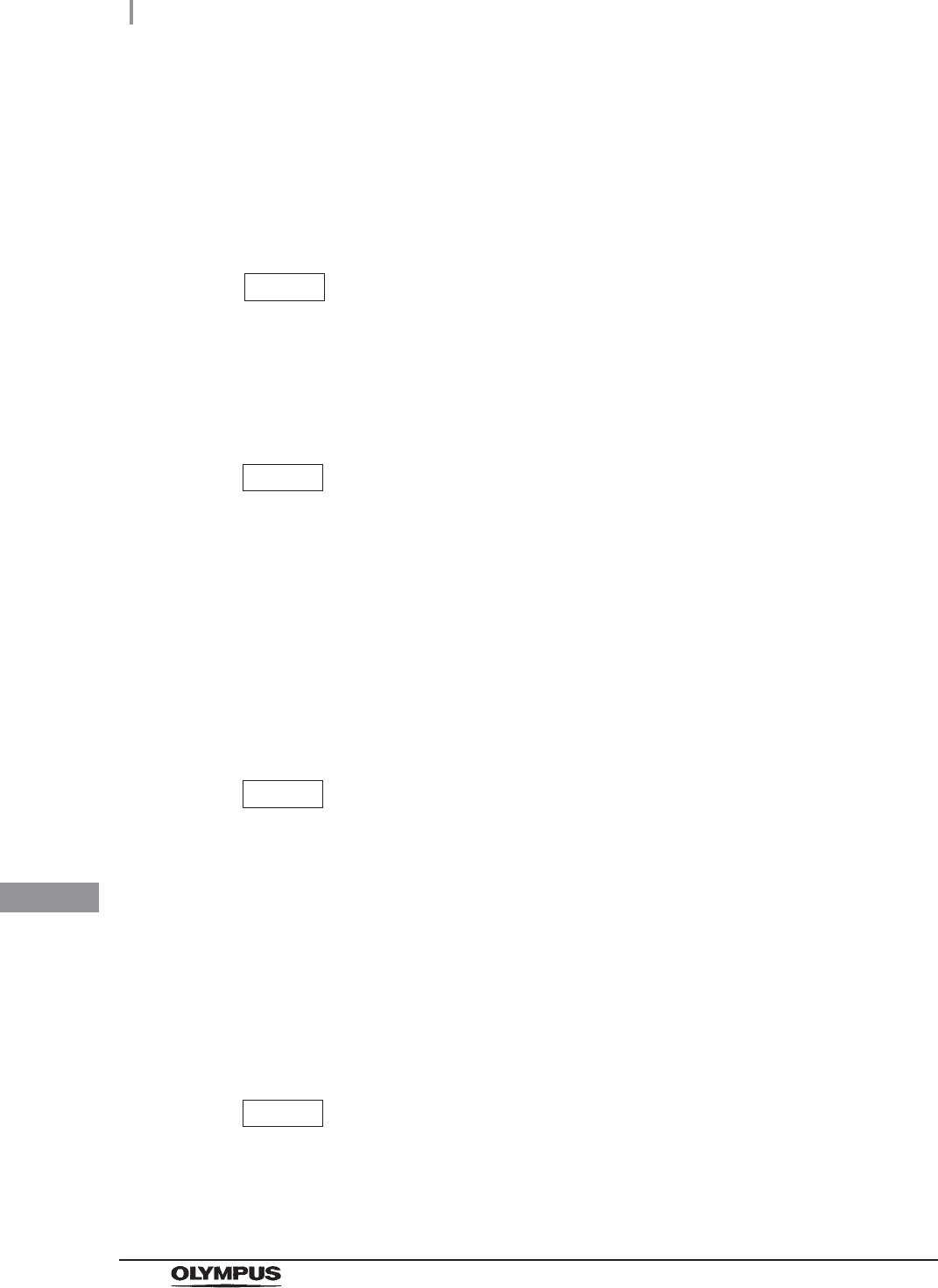
574
11.3 Log management with PC
OER-Elite OPERATION MANUAL
Ch.11
(a) Copying data in PC
NOTE
Also, refer to the instruction manual for the PC.
(b) Managing the record data
To manage the record data, use the record data in the “Work” folder copied to the PC. The
record data should be managed according to the purpose of application of data.
The records can be managed as shown in the following example.
NOTE
The following example uses Microsoft Excel for managing the CSV files. The
management tool can be selected from the desired application software including
statistical software according to the purpose and application of data.
NOTE
When editing a CSV file using application software such as statistical software,
there is a risk that the operation above cannot save the edited data. It is therefore
recommended to save the edited data in the dedicated file format of the software in
use.
When saving data in a PC for the backup purpose
1Attach the portable memory containing record data to the PC.
2Copy the “OER-Elite” folder in the portable memory to the PC.
NOTE
If a message confirming overwriting of a folder or file is displayed when you
attempt to copy data in the PC, select “Overwrite” in any case.
3After completion of the copying, remove the portable memory from the PC.
Example of record management (Reference)
1Open the “Work” folder copied to the PC.
2Open the file to be edited, check the header and data sections, and enter desired
information in the edit section.
3When the entry completes, save the edited file. Do not need rename file name.
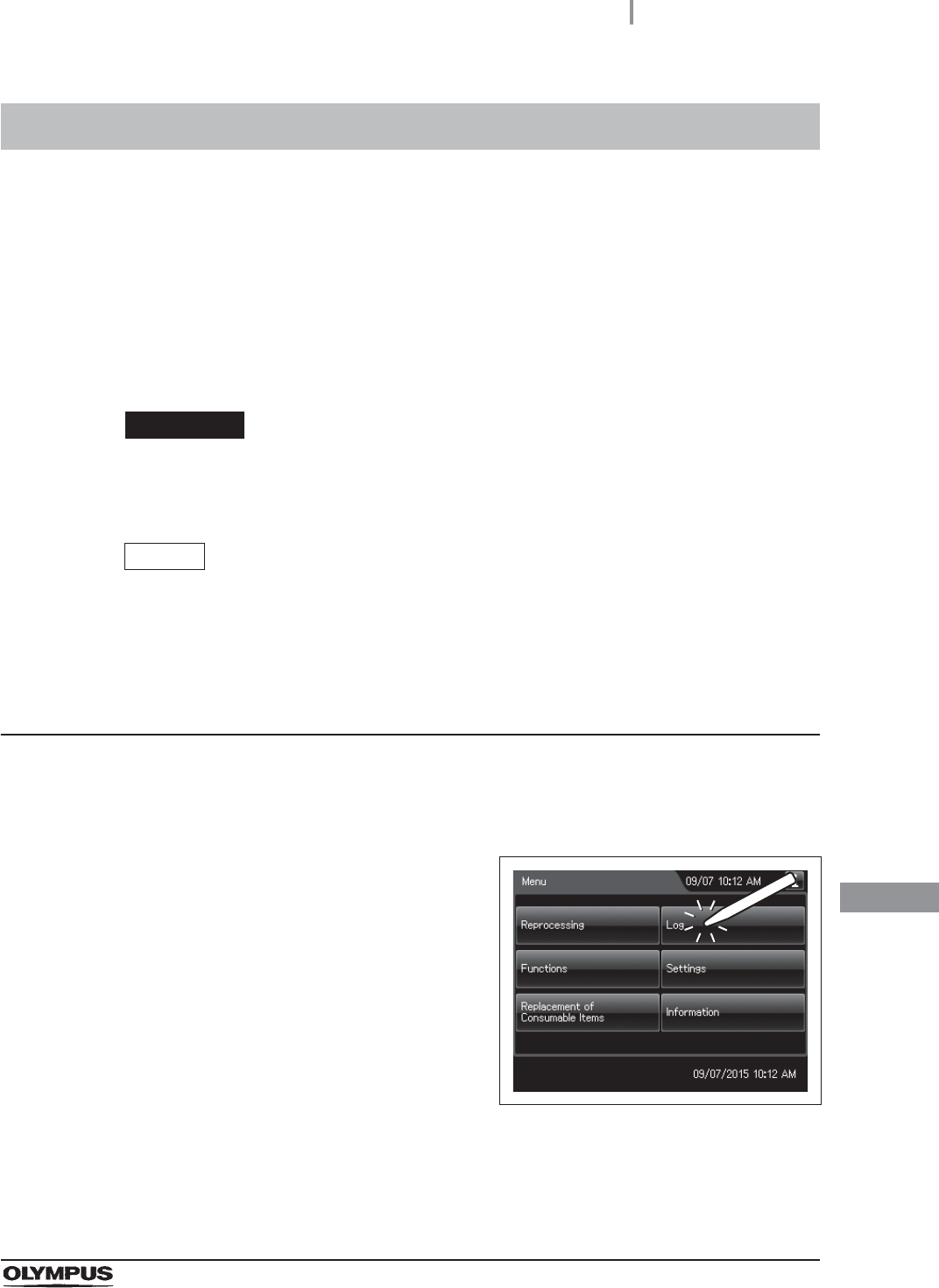
11.4 Printing records
575
OER-Elite OPERATION MANUAL
Ch.11
The records of the following processes can be printed with the MAJ-1937 printer included in the
optional MAJ-2144 printer set.
• Reprocessing process: The record of reprocessing process, including errors.
• Leak test processes (auto, manual): The record of auto and manual leak tests performed on
the reprocessor.
• Leaking scope decontamination process: The record of leaking scope decontamination
process.
CAUTION
Pay attention to handle the portable memory and printed paper that include patient
information exported from the OER-Elite.
NOTE
Printing records is also possible on the record details screens. Refer to the record
details in 11.2 Log display for the details.
Printing
This section is defined method for printing of daily basis. For other printing method, refer to page 232.
11.4 Printing records
1Turn this reprocessor and the printer ON.
2Press the “Log” button on the Menu screen.
Figure 11.20
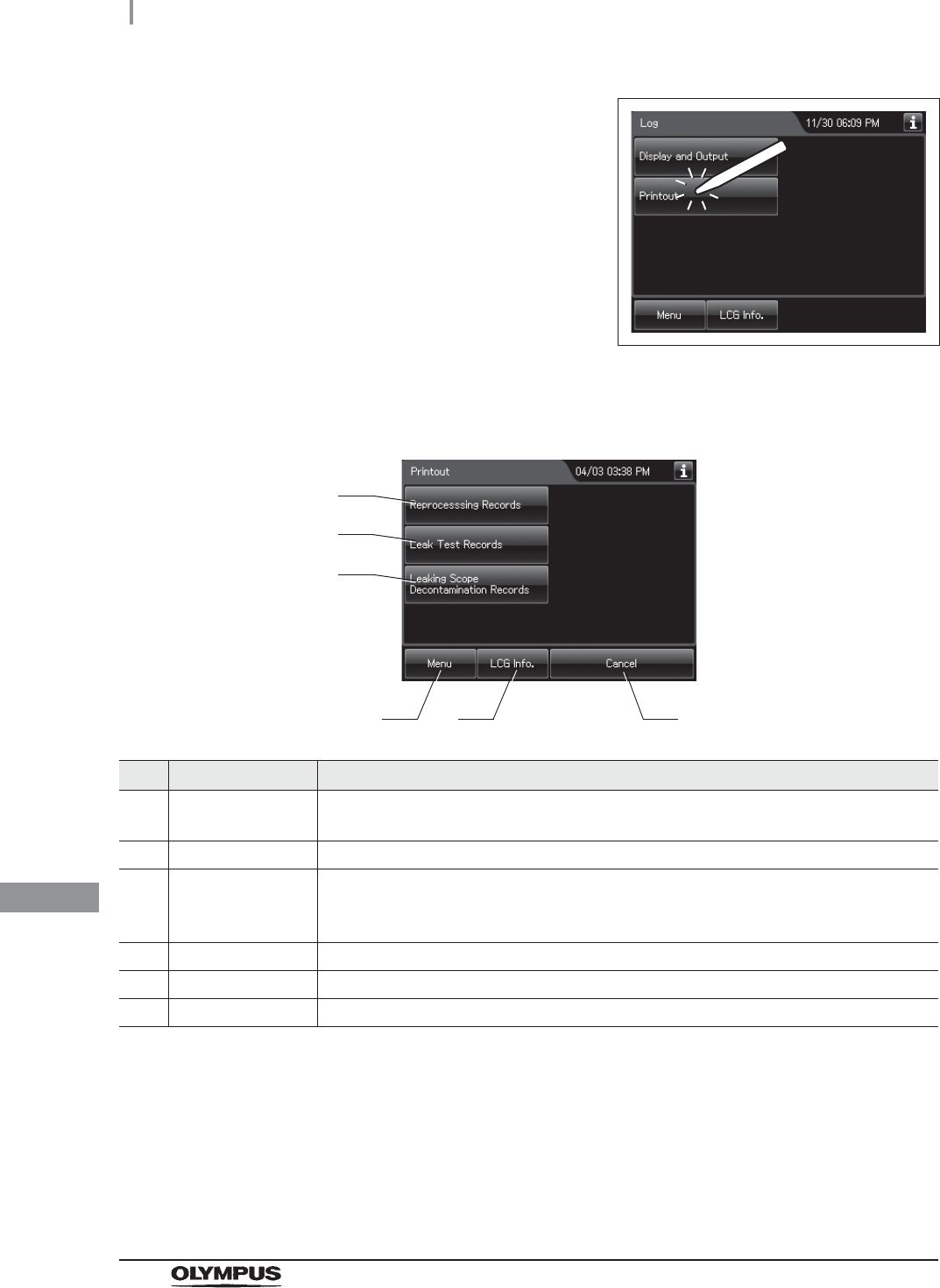
576
11.4 Printing records
OER-Elite OPERATION MANUAL
Ch.11
3Press the “Printout” button.
Figure 11.21
4Select the record to be printed.
No. Button Description
1 Reprocessing
Records
Prints the records of the reprocessing processes.
2 Leak Test Records Prints the records of the leak tests.
3 Leaking Scope
Decontamination
Records
Prints the records of the leaking scope decontamination.
4 Menu Returns to the Menu screen.
5 LCG info. Opens the disinfectant information screen.
6 Cancel Returns to the previous screen.
4 6
1
2
3
5
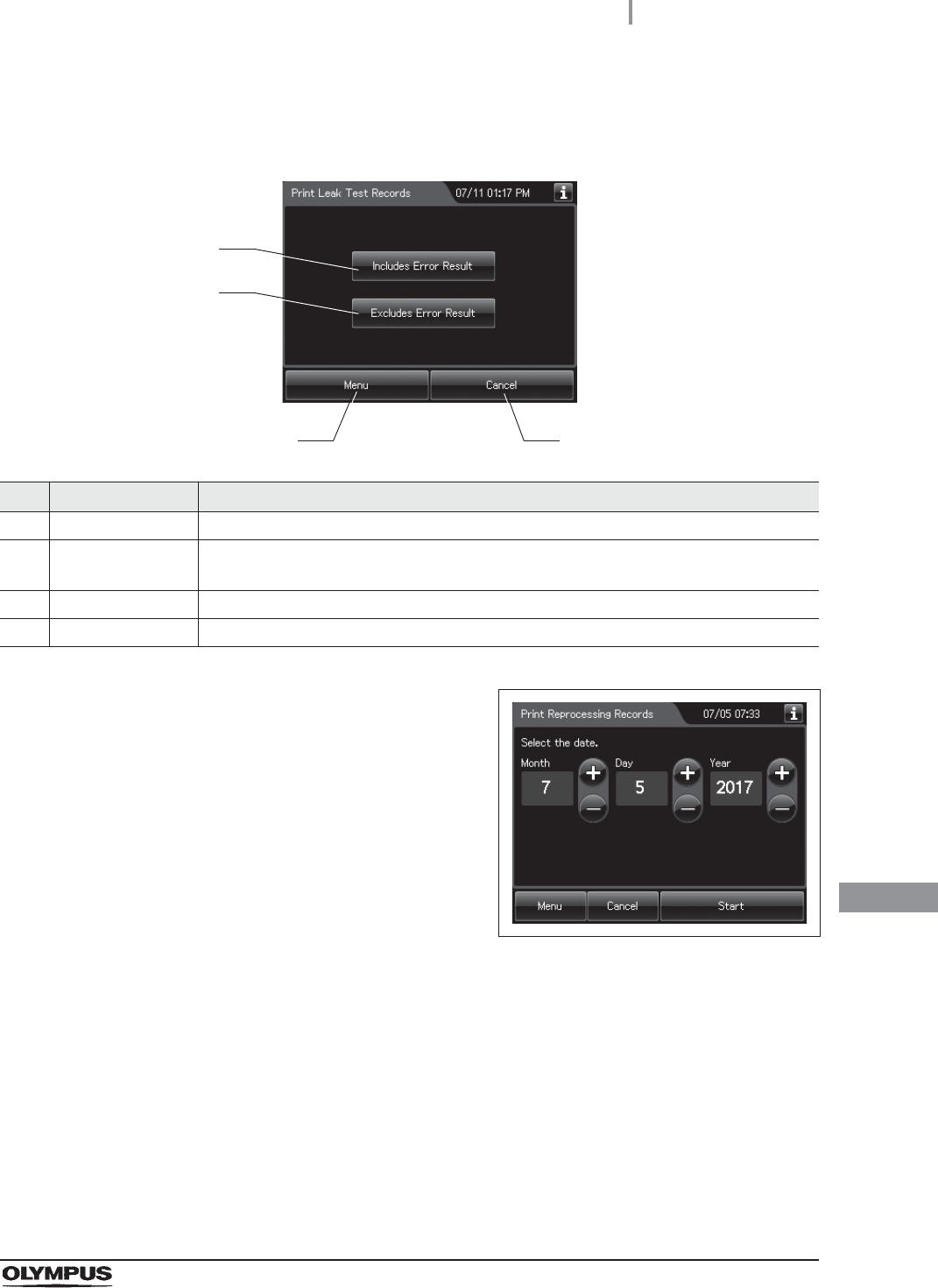
11.4 Printing records
577
OER-Elite OPERATION MANUAL
Ch.11
5Select whether or not the error records are to be printed.
No. Button Description
1 Include error results Records are printed including error records.
2 Excludes error
results
Records are printed without error records. (Only the records of successfully completed
operations are printed.)
3 Menu Returns to the menu.
4 Return Returns to the previous screen.
6Set the date of the records to be printed by
pressing the “+” or “–” button.
Figure 11.22
4
1
3
2
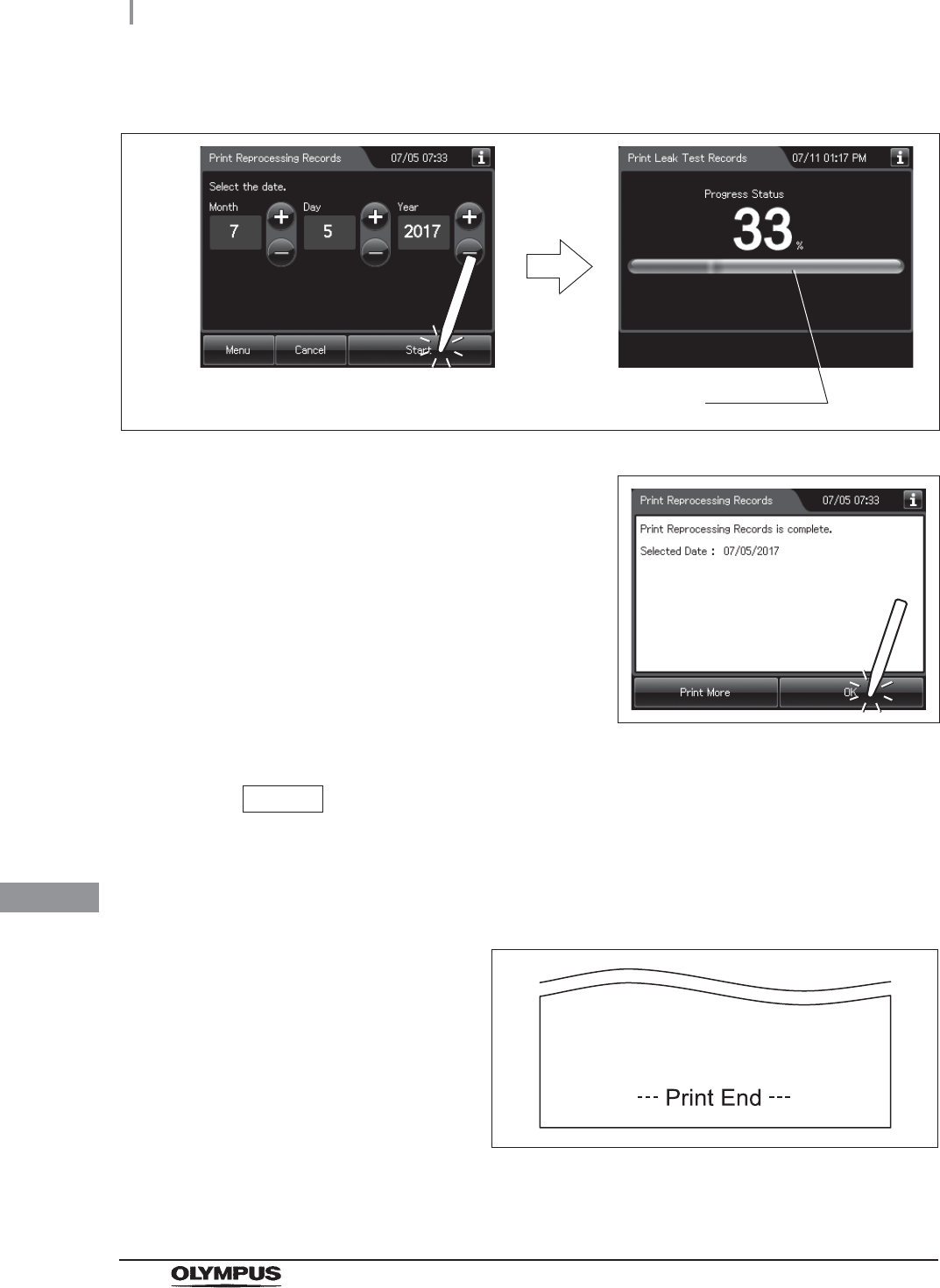
578
11.4 Printing records
OER-Elite OPERATION MANUAL
Ch.11
NOTE
• Characters “PRINT END” are printed at the end of each print session. If they are
not printed, not all the records of the selected period are printed out. Restart
printing from the beginning.
• Records are printed according to the time.
Figure 11.25
7Press the “Start” button. Printing starts and the touch screen displays the progress.
Figure 11.23
8When the printing completes, the following
screen appears. Press the “OK” button.
Figure 11.24
Progress bar
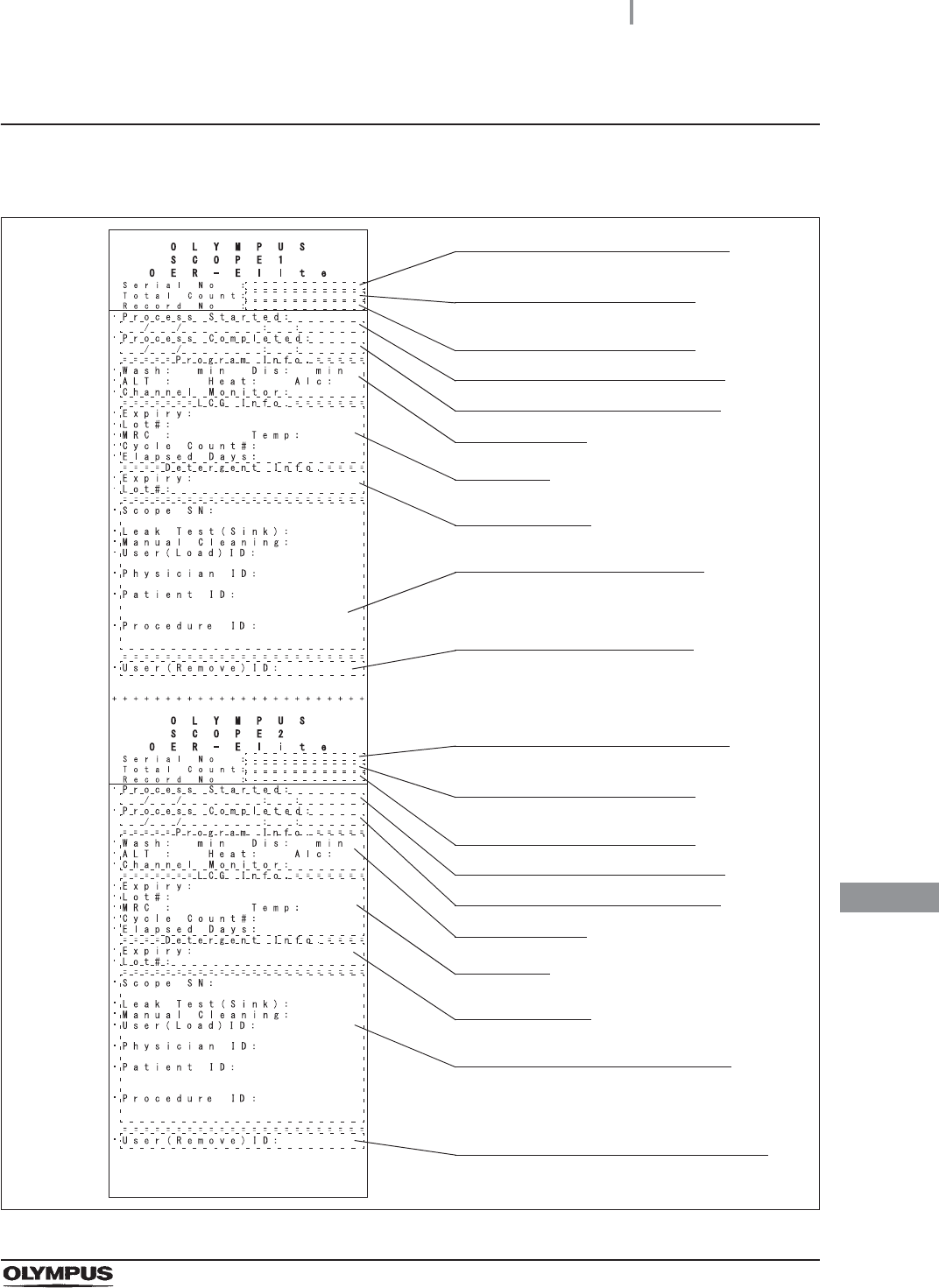
11.4 Printing records
579
OER-Elite OPERATION MANUAL
Ch.11
Print format
Reprocessing – Normal (Separate)
Figure 11.26
Serial number of this reprocessor
Date and time of start of process
Date and time of end of process
Information of first endoscope
User ID (remove) of the end of
process of first endoscope
Total accumulated of
reprocessing process count
Number given to each record
in the order of occurrence
Setting details
LCG Info.
Detergent Info.
Serial number of this reprocessor
Date and time of start of process
Date and time of end of process
Information of second endoscope
User ID (remove) of the end of process
Total accumulated of
reprocessing process count
Number given to each record
in the order of occurrence
Setting details
LCG Info.
Detergent Info.
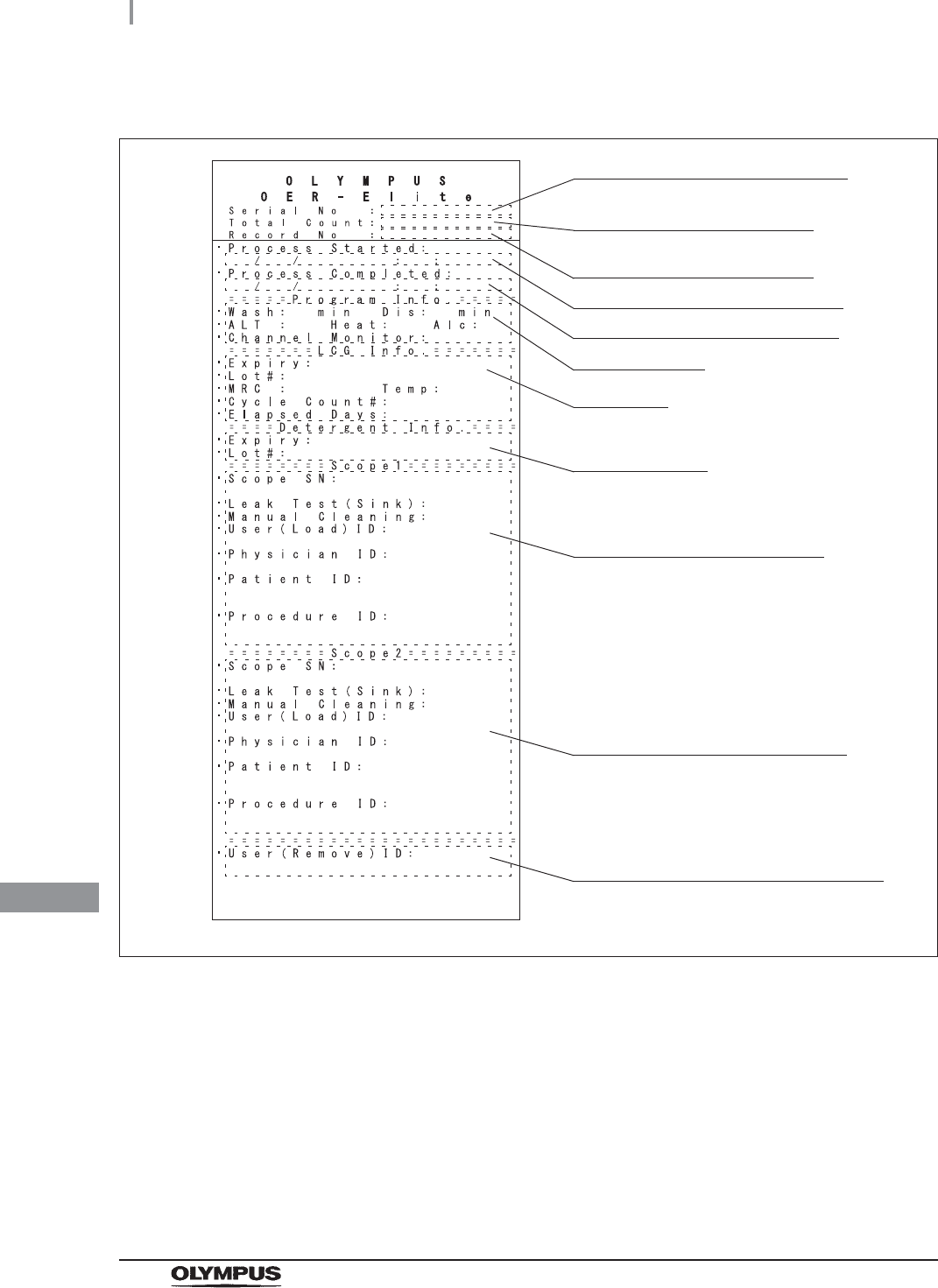
580
11.4 Printing records
OER-Elite OPERATION MANUAL
Ch.11
Reprocessing – Normal (Combine)
Figure 11.27
Serial number of this reprocessor
Date and time of start of process
Date and time of end of process
Total accumulated of
reprocessing process count
Number given to each record
in the order of occurrence
Setting details
LCG Info.
Detergent Info.
Information of first endoscope
Information of second endoscope
User ID (remove) of the end of process
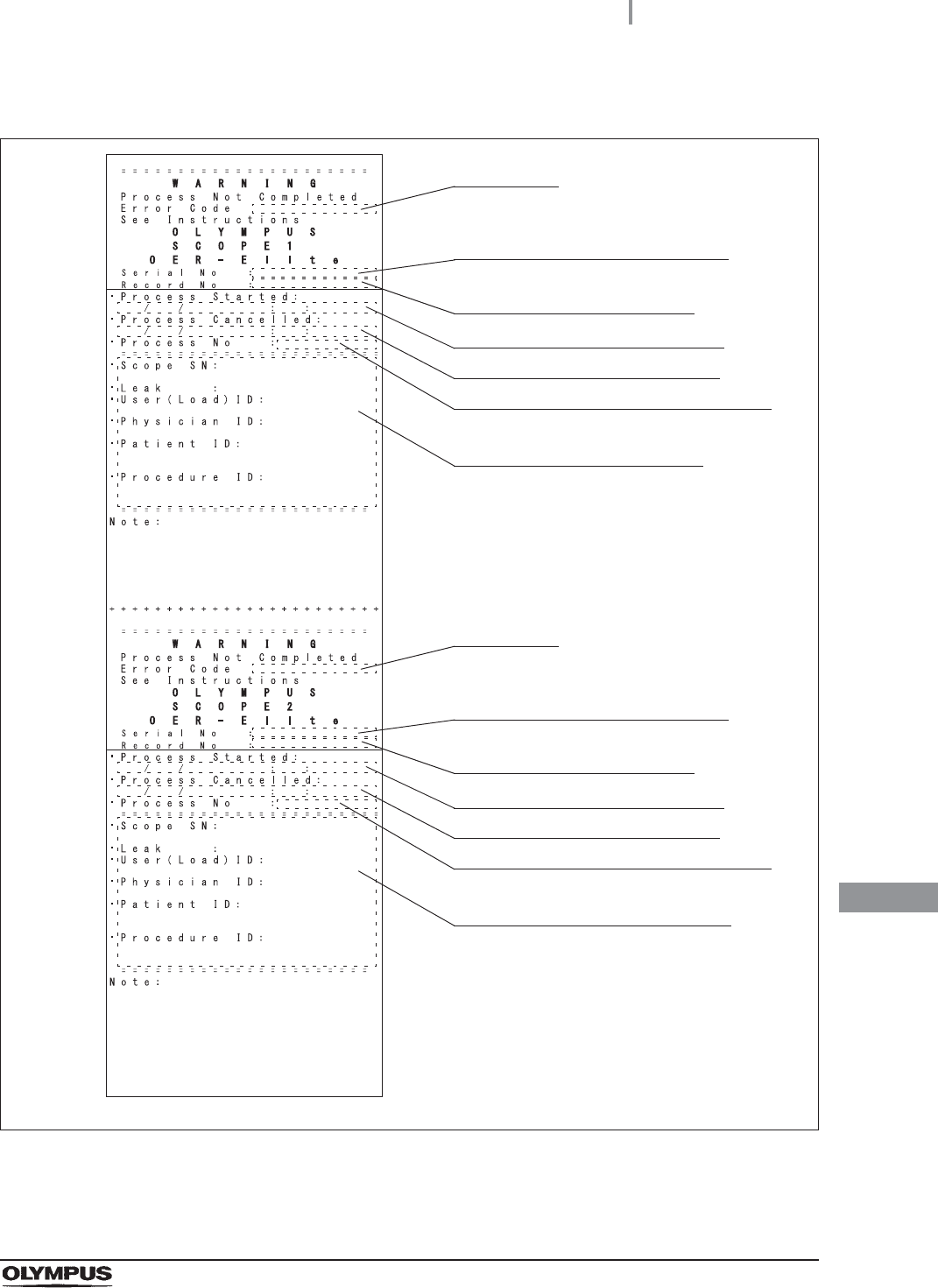
11.4 Printing records
581
OER-Elite OPERATION MANUAL
Ch.11
Reprocessing – Error (Separate)
Figure 11.28
Serial number of this reprocessor
Date and time of start of process
Date and time of end of process
Information of first endoscope
Number given to each record
in the order of occurrence
Error code
Process number of occurrence of error
Serial number of this reprocessor
Date and time of start of process
Date and time of end of process
Information of second endoscope
Number given to each record
in the order of occurrence
Error code
Process number of occurrence of error
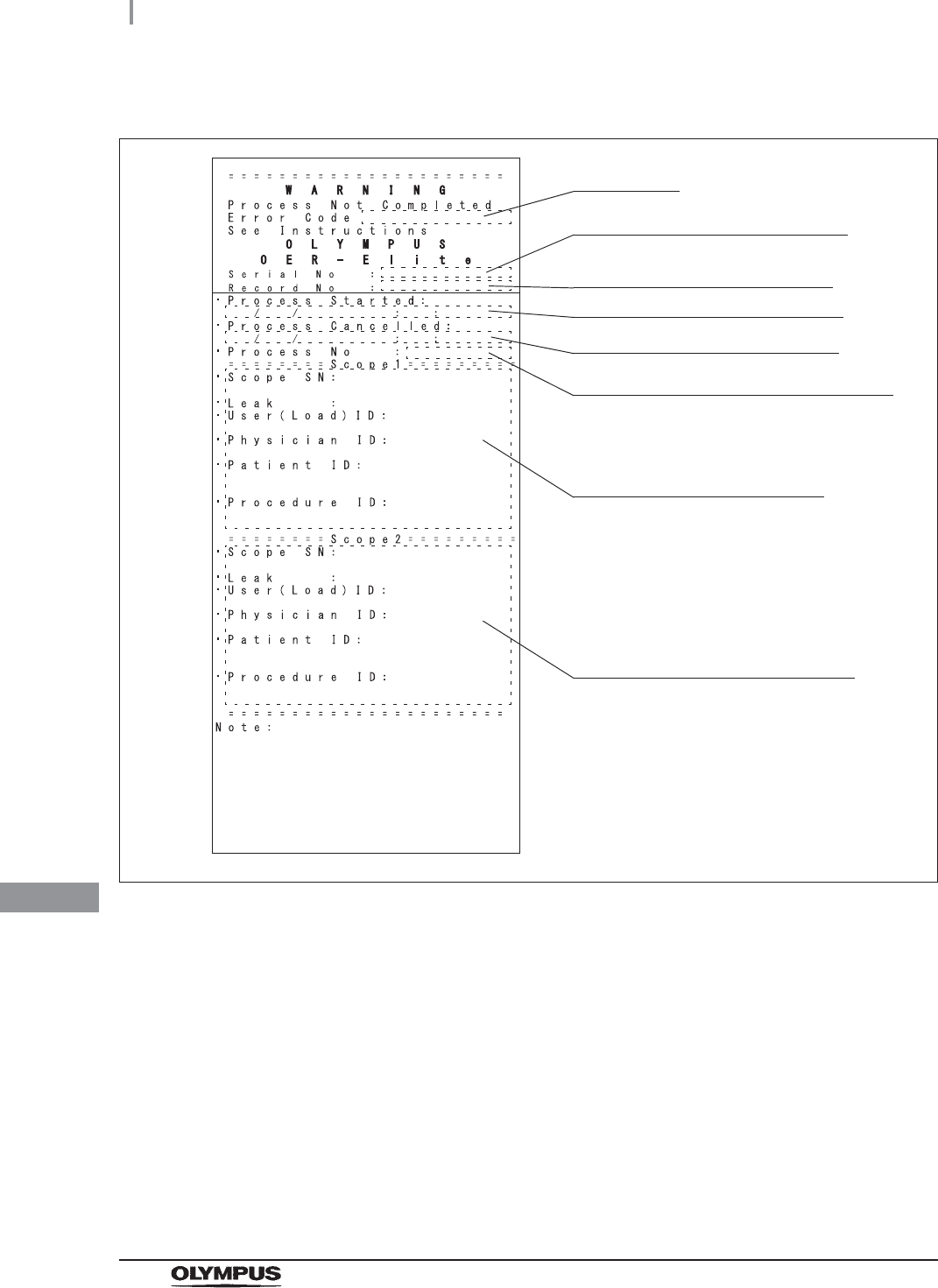
582
11.4 Printing records
OER-Elite OPERATION MANUAL
Ch.11
Reprocessing – Error (Combine)
Figure 11.29
Serial number of this reprocessor
Date and time of start of process
Date and time of end of process
Process number of occurrence of error
Information of first endoscope
Error code
Number given to each record in
the order of occurrence
Information of second endoscope
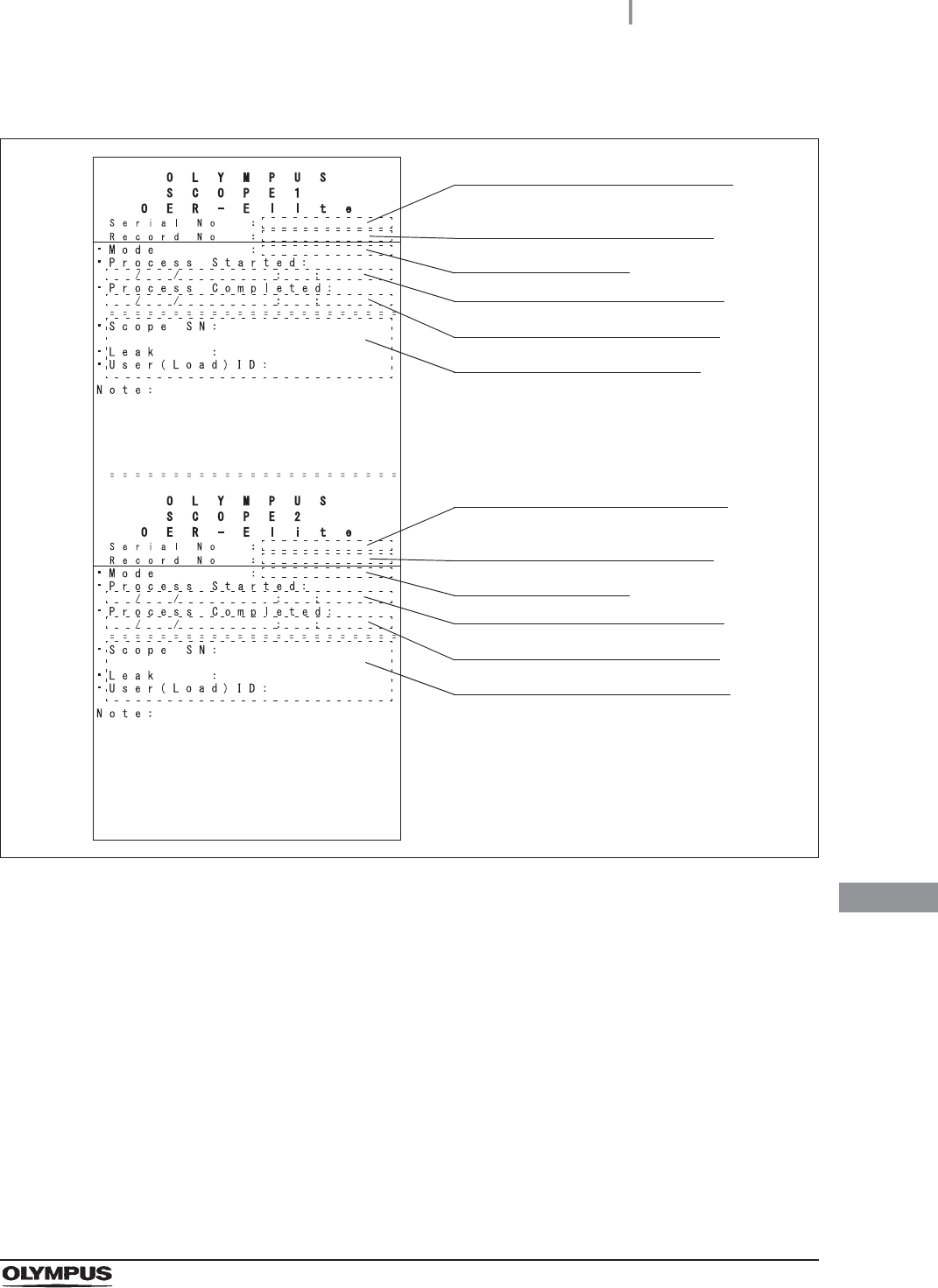
11.4 Printing records
583
OER-Elite OPERATION MANUAL
Ch.11
Leak test – Normal (Separate)
Figure 11.30
Serial number of this reprocessor
Date and time of start of process
Date and time of end of process
Information of first endoscope
Number given to each record in
the order of occurrence
Type of the leak test
Serial number of this reprocessor
Date and time of start of process
Date and time of end of process
Information of second endoscope
Number given to each record in
the order of occurrence
Type of the leak test
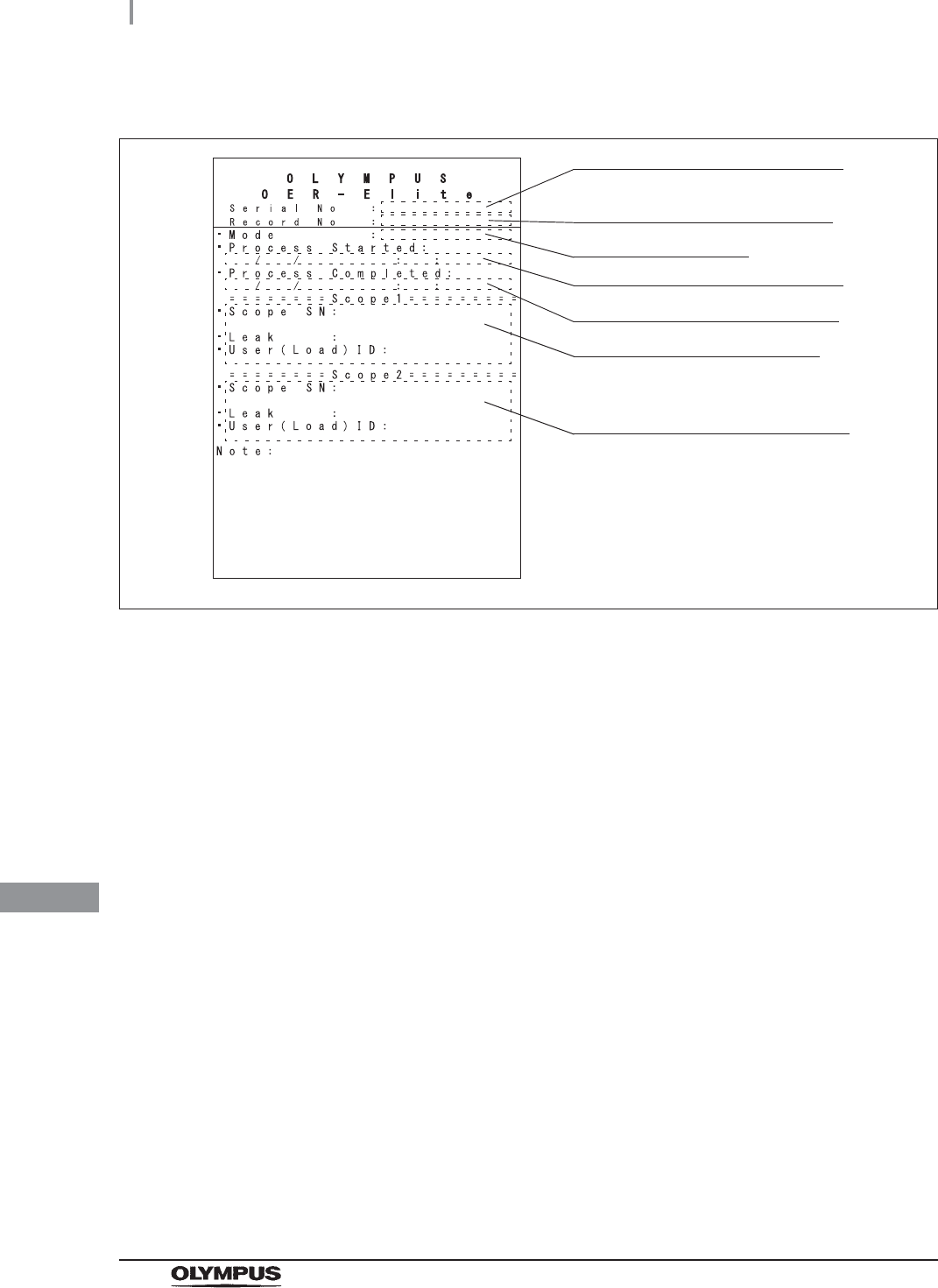
584
11.4 Printing records
OER-Elite OPERATION MANUAL
Ch.11
Leak test – Normal (Combine)
Figure 11.31
Serial number of this reprocessor
Date and time of start of process
Date and time of end of process
Information of first endoscope
Number given to each record in
the order of occurrence
Type of the leak test
Information of second endoscope
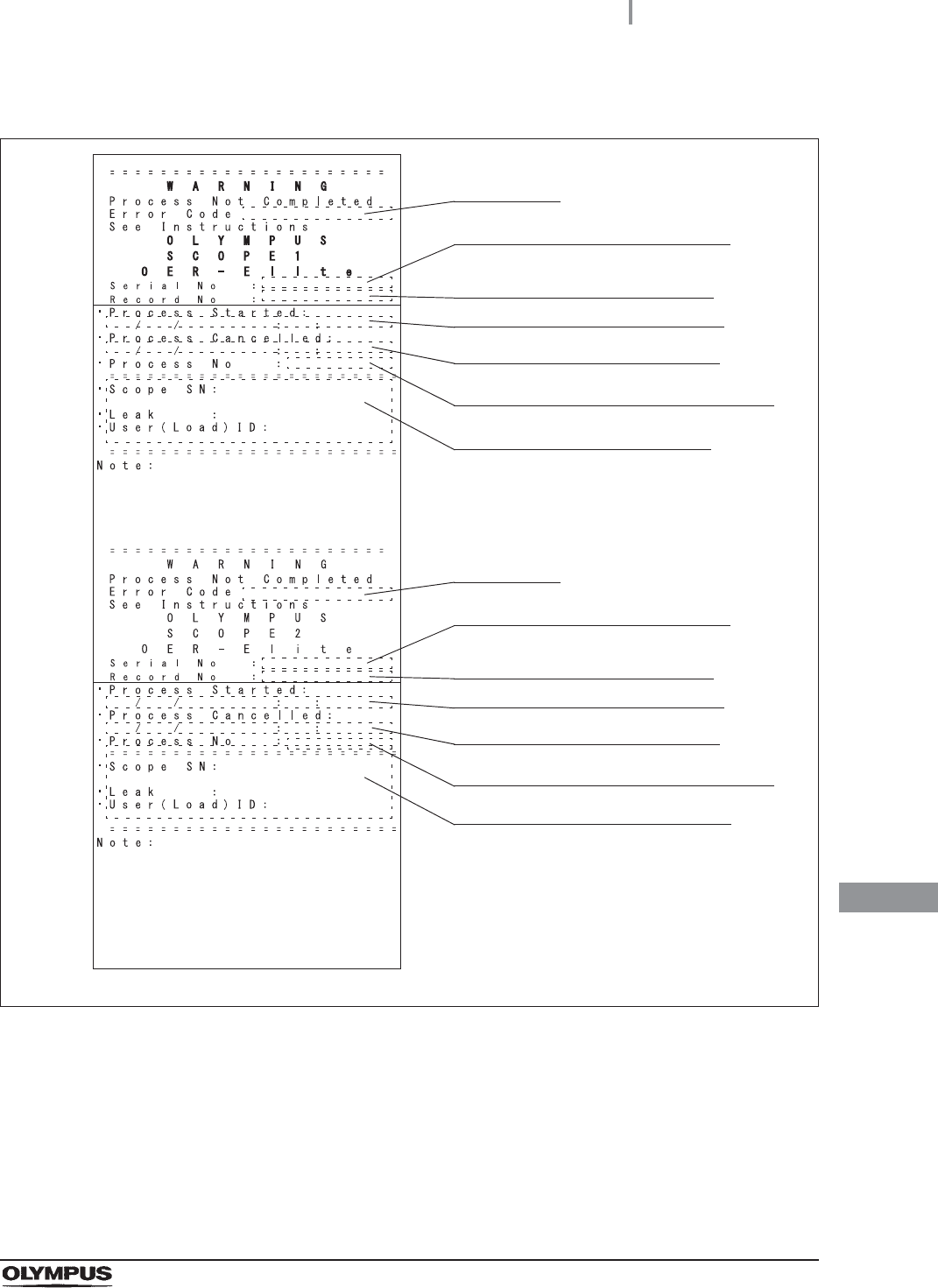
11.4 Printing records
585
OER-Elite OPERATION MANUAL
Ch.11
Leak test – Error (Separate)
Figure 11.32
Serial number of this reprocessor
Date and time of start of process
Date and time of end of process
Process number of occurrence of error
Information of first endoscope
Error code
Number given to each record in
the order of occurrence
Serial number of this reprocessor
Date and time of start of process
Date and time of end of process
Process number of occurrence of error
Information of second endoscope
Error code
Number given to each record in
the order of occurrence
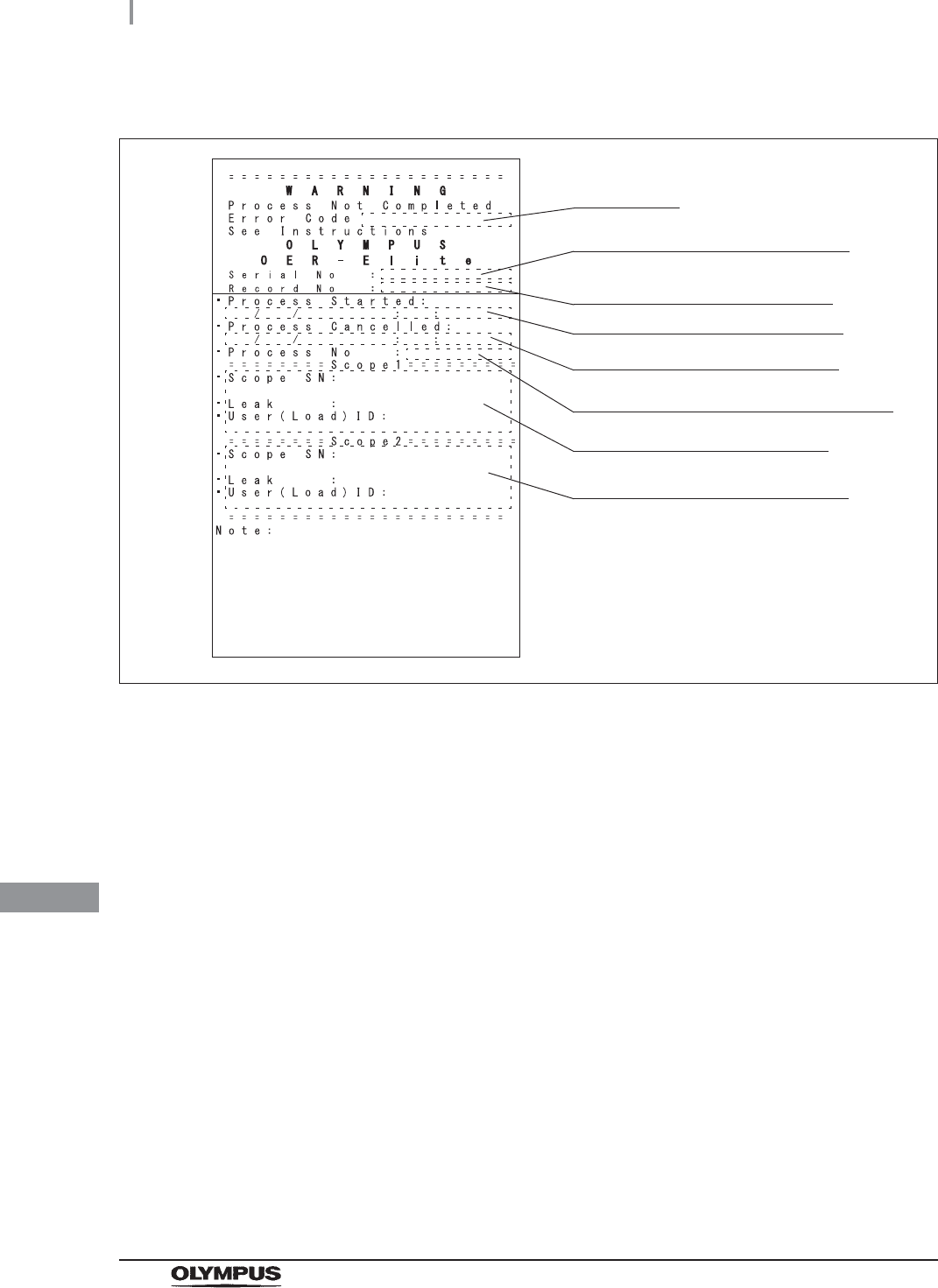
586
11.4 Printing records
OER-Elite OPERATION MANUAL
Ch.11
Leak test – Error (Combine)
Figure 11.33
Serial number of this reprocessor
Date and time of start of process
Date and time of end of process
Process number of occurrence of error
Information of first endoscope
Error code
Number given to each record in
the order of occurrence
Information of second endoscope
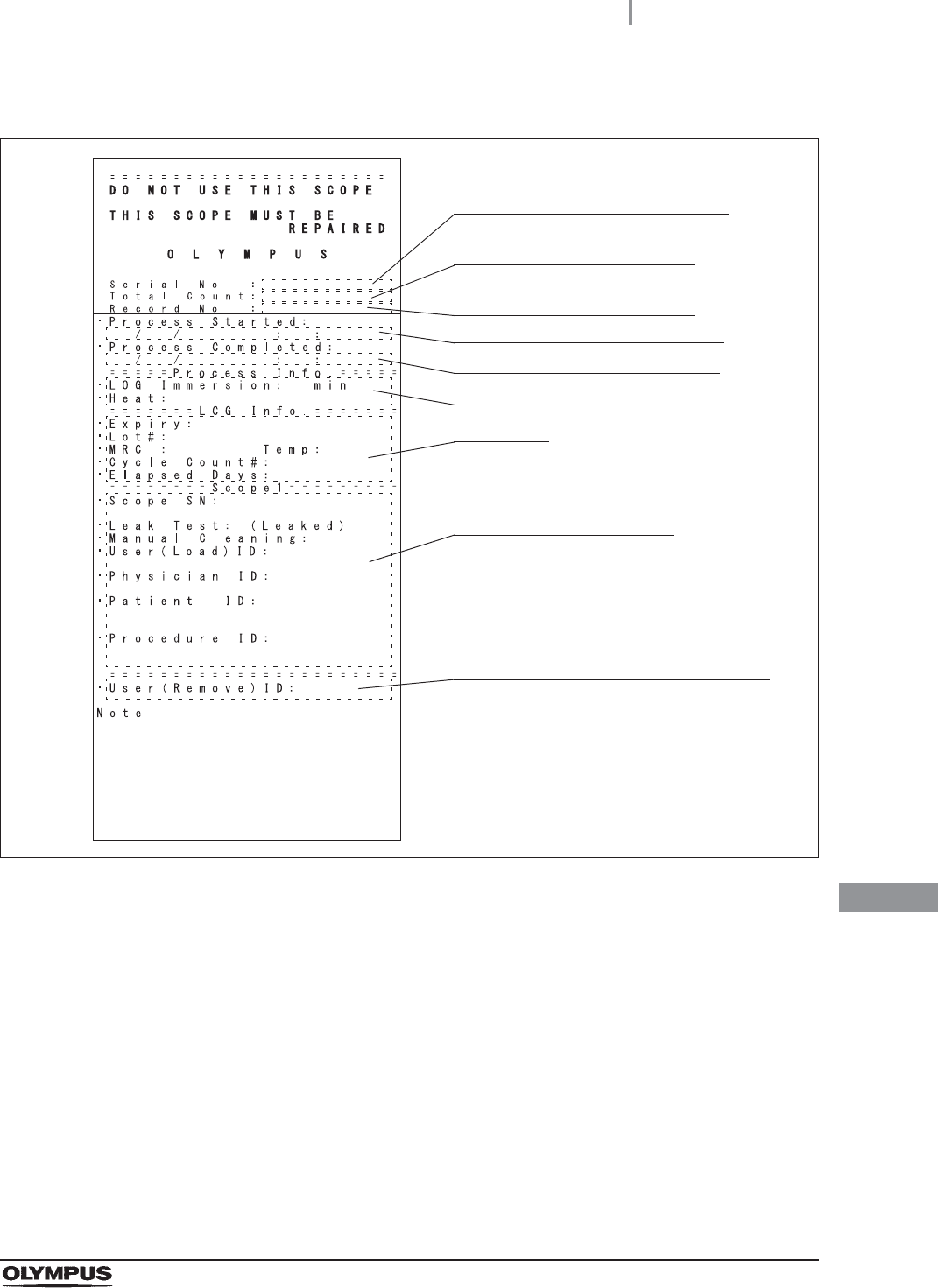
11.4 Printing records
587
OER-Elite OPERATION MANUAL
Ch.11
Leaking scope decontamination – Normal
Figure 11.34
Serial number of this reprocessor
Date and time of start of process
Date and time of end of process
Information of endoscope
User ID (remove) of the end of process
Total accumulated of
reprocessing process count
Number given to each record
in the order of occurrence
Setting details
LCG Info.
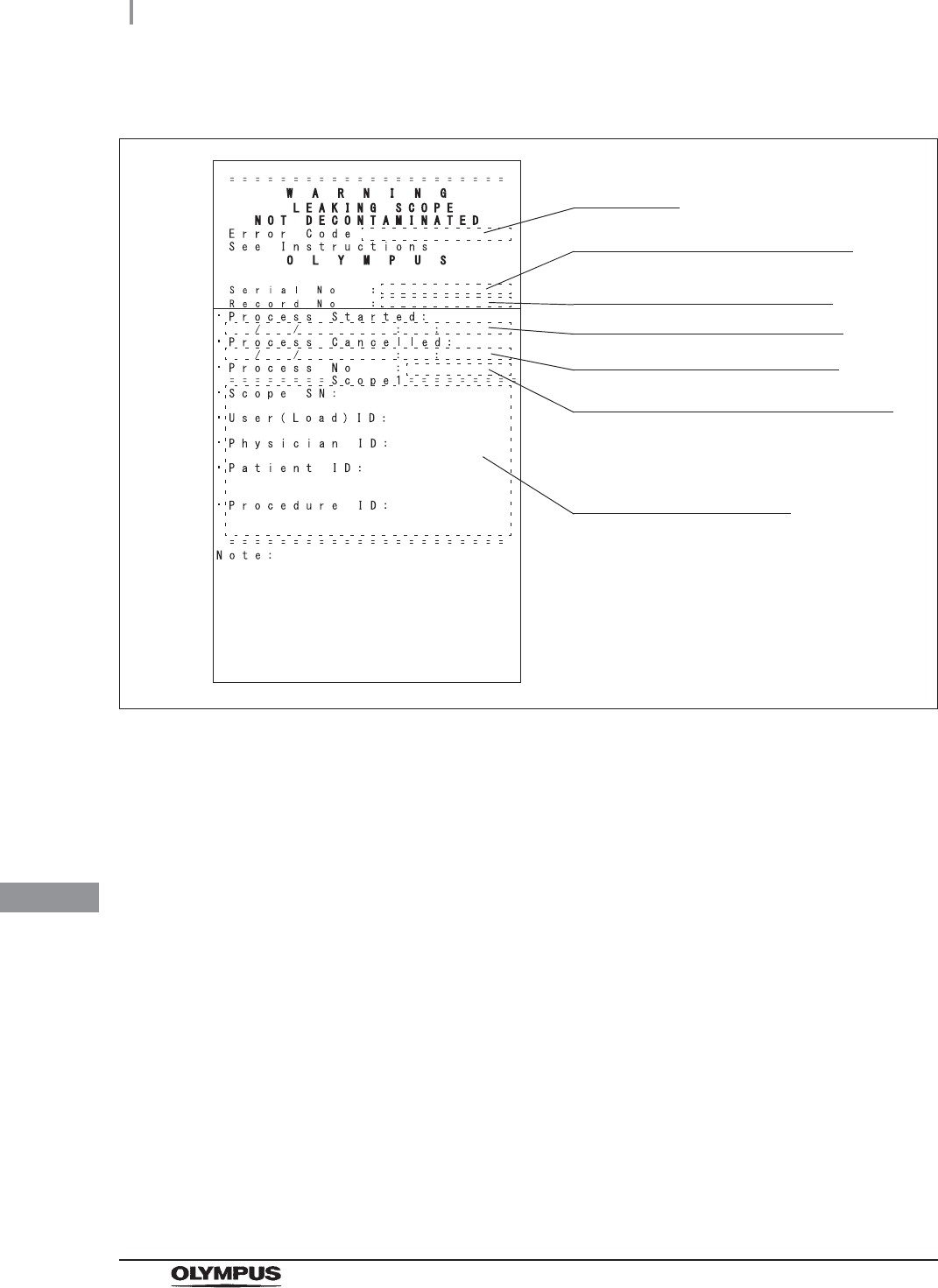
588
11.4 Printing records
OER-Elite OPERATION MANUAL
Ch.11
Leaking scope decontamination – Error
Figure 11.35
Serial number of this reprocessor
Date and time of start of process
Date and time of end of process
Process number of occurrence of error
Information of endoscope
Error code
Number given to each record in
the order of occurrence
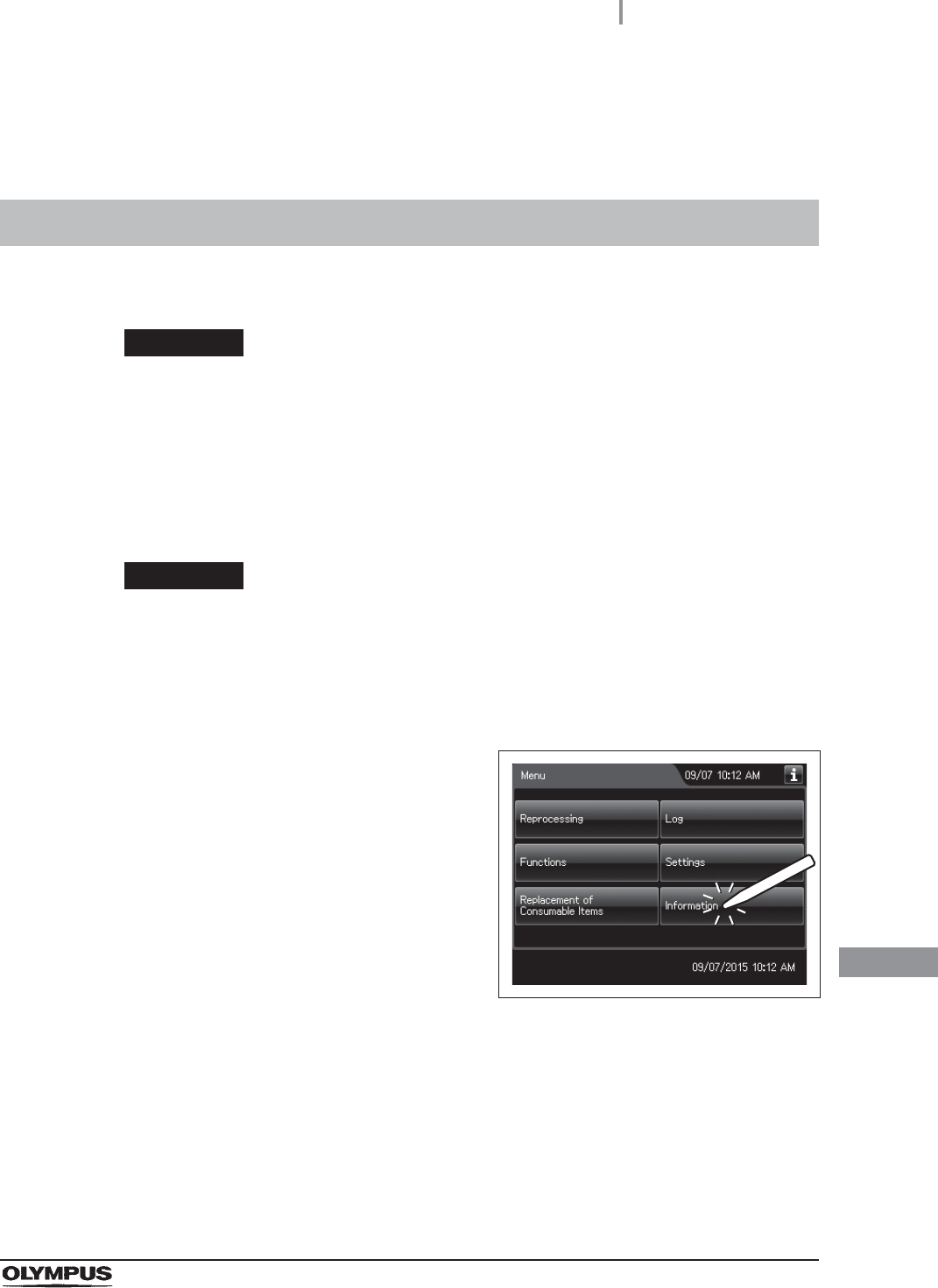
12.1 RFID data check
589
OER-Elite OPERATION MANUAL
Ch.12
Chapter 12 Information Menu Screen
This function is to check the RFID data of Scope, User, and Physician.
WARNING
If electromagnetic interference is caused by the radio wave radiated from the RFID
reader of this reprocessor, immediately move the interfered device apart from the
RFID reader or turn the reprocessor OFF. If you still do not feel well, consult a
physician. The radio wave radiated from the RFID reader of this reprocessor may
cause malfunction of medical devices such as a pacemaker or other electronic
equipment.
CAUTION
An electromagnetic interference with other devices may shorten the
communications distance of the designated ID tag and cause signals to become
unreadable. Try to take mitigation measures such as keeping the affecting device
away from this reprocessor.
12.1 RFID data check
1Press the “Information” button on the Menu
screen.
Figure 12.1
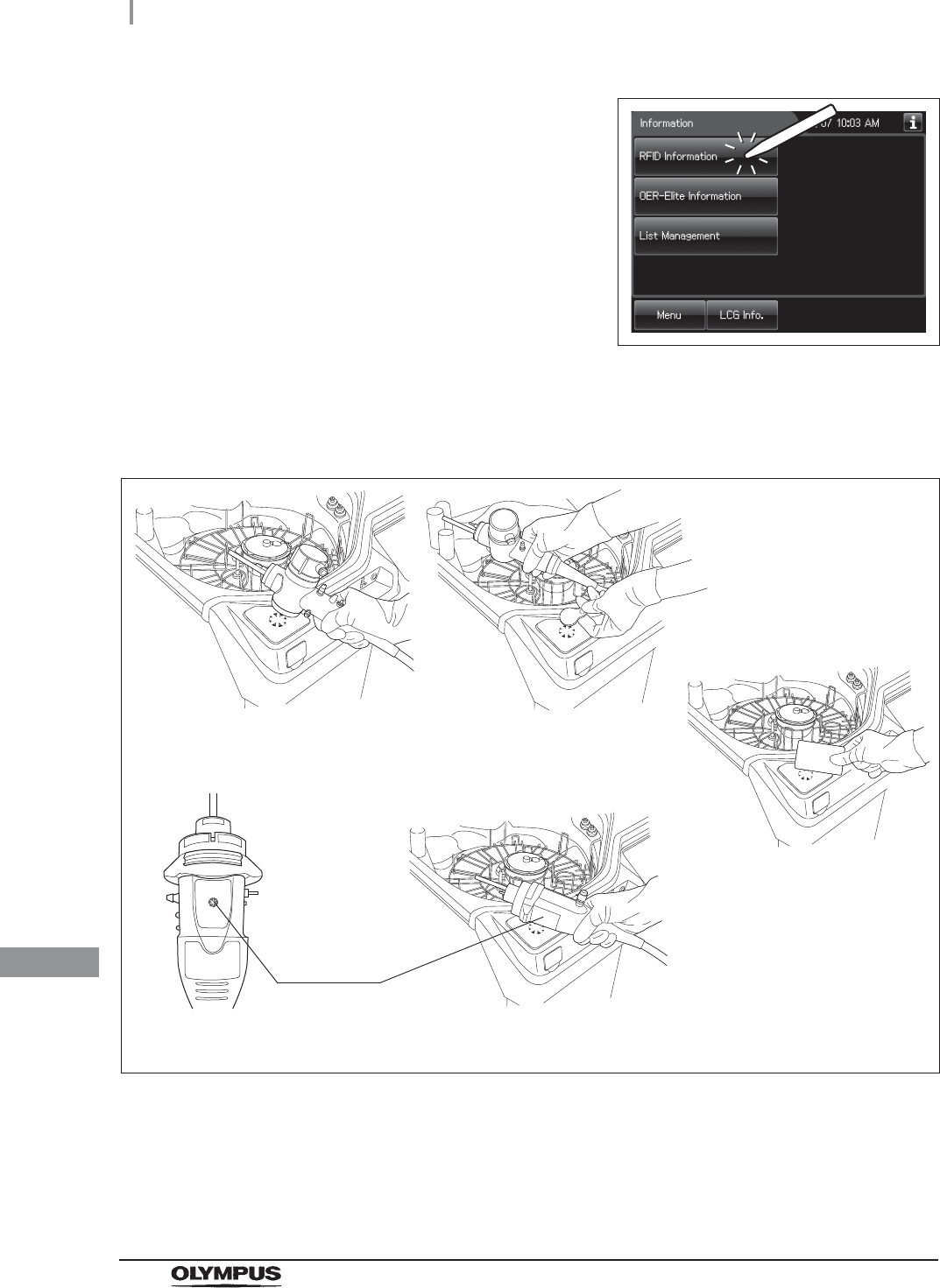
590
12.1 RFID data check
OER-Elite OPERATION MANUAL
Ch.12
2Press the “RFID Information” button on the
Information menu.
Figure 12.2
3Hold the internal ID endoscope connector, the external ID tag of endoscope, the user
ID card, or the physician ID card to the RFID reader of the reprocessor, and scan the
tag with the reader until a short beep sounds.
Figure 12.3
For internal ID endoscope
(For example 180 series
endoscope)
For external ID tag
For internal ID endoscope
(190 series endoscope)
Scope ID
mark
For user ID card or
physician ID card
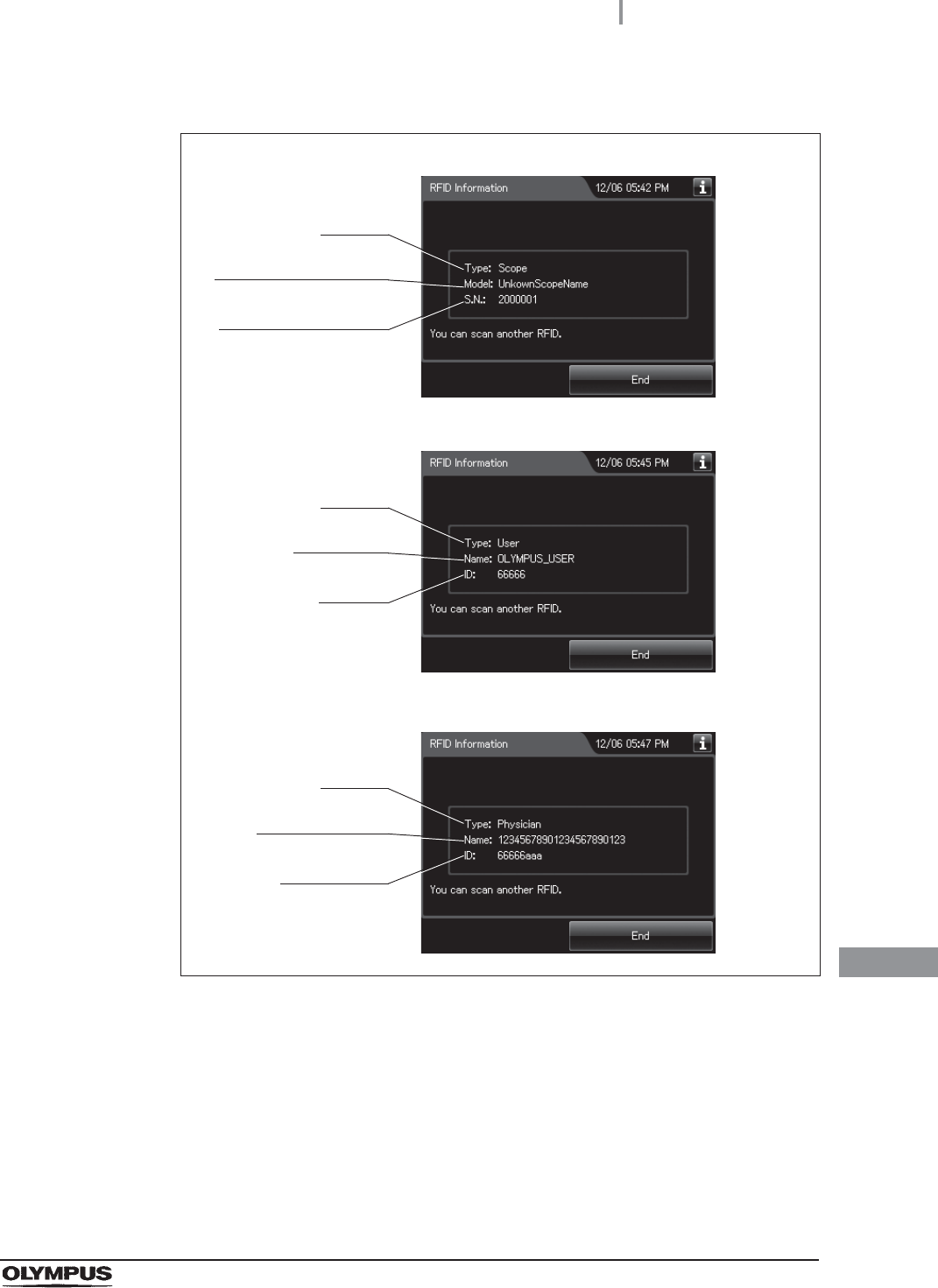
12.1 RFID data check
591
OER-Elite OPERATION MANUAL
Ch.12
4The touch screen displays the RFID data.
Figure 12.4
5Repeat Step 4 to remove current display information if check another RFID data.
Scope model number
Scope ID data
Scope serial number
User ID data
Physician ID data
ID type
User name
User ID
ID type
Physician name
Physician ID
ID type
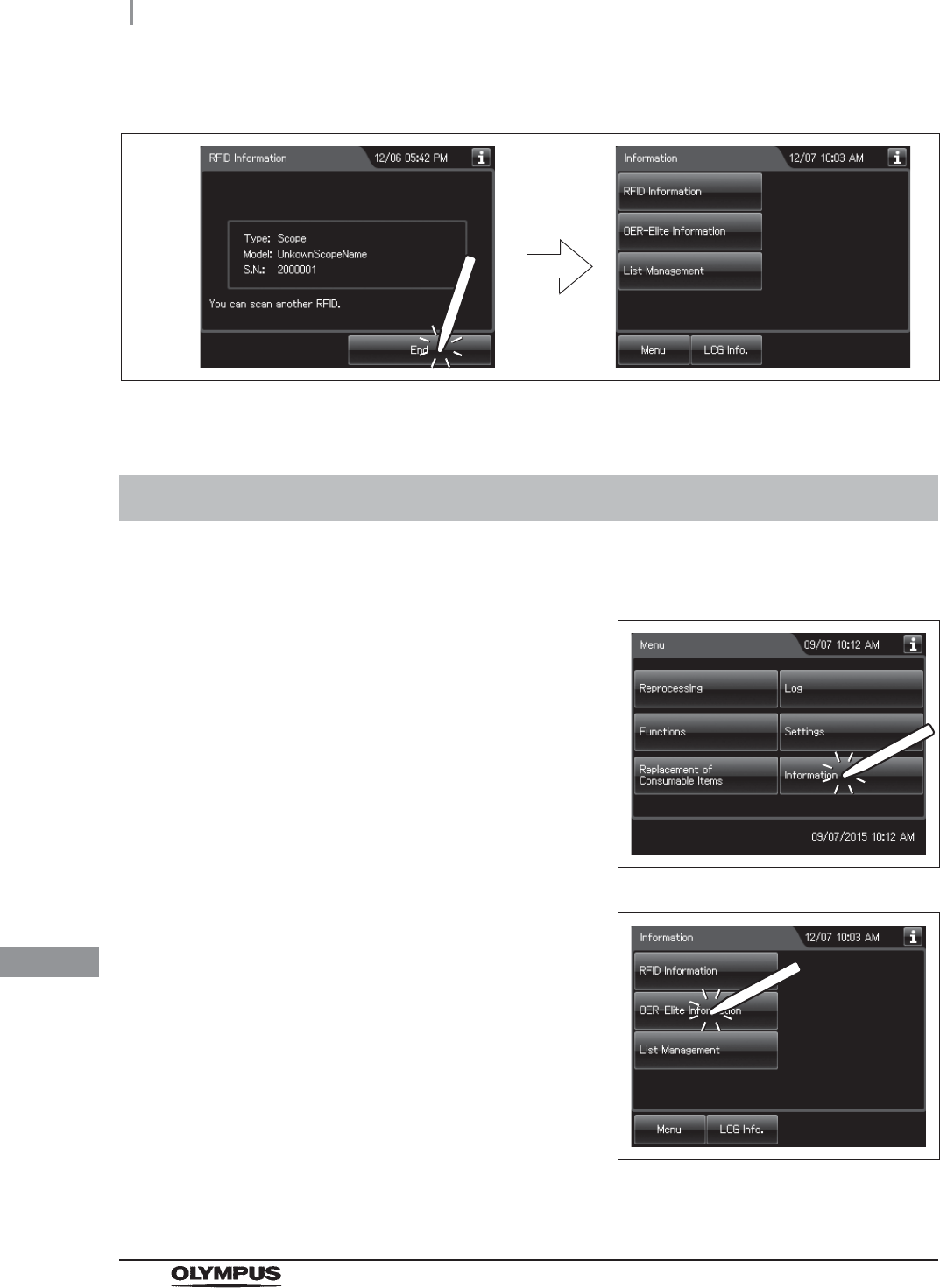
592
12.2 Reprocessor information check
OER-Elite OPERATION MANUAL
Ch.12
This function is used to check the information on the reprocessor.
6Press the “End” button to go back to the Information menu.
Figure 12.5
12.2 Reprocessor information check
1Press the “Information” button on the Menu
screen.
Figure 12.6
2Press the “OER-Elite Information” button on the
Information menu.
Figure 12.7
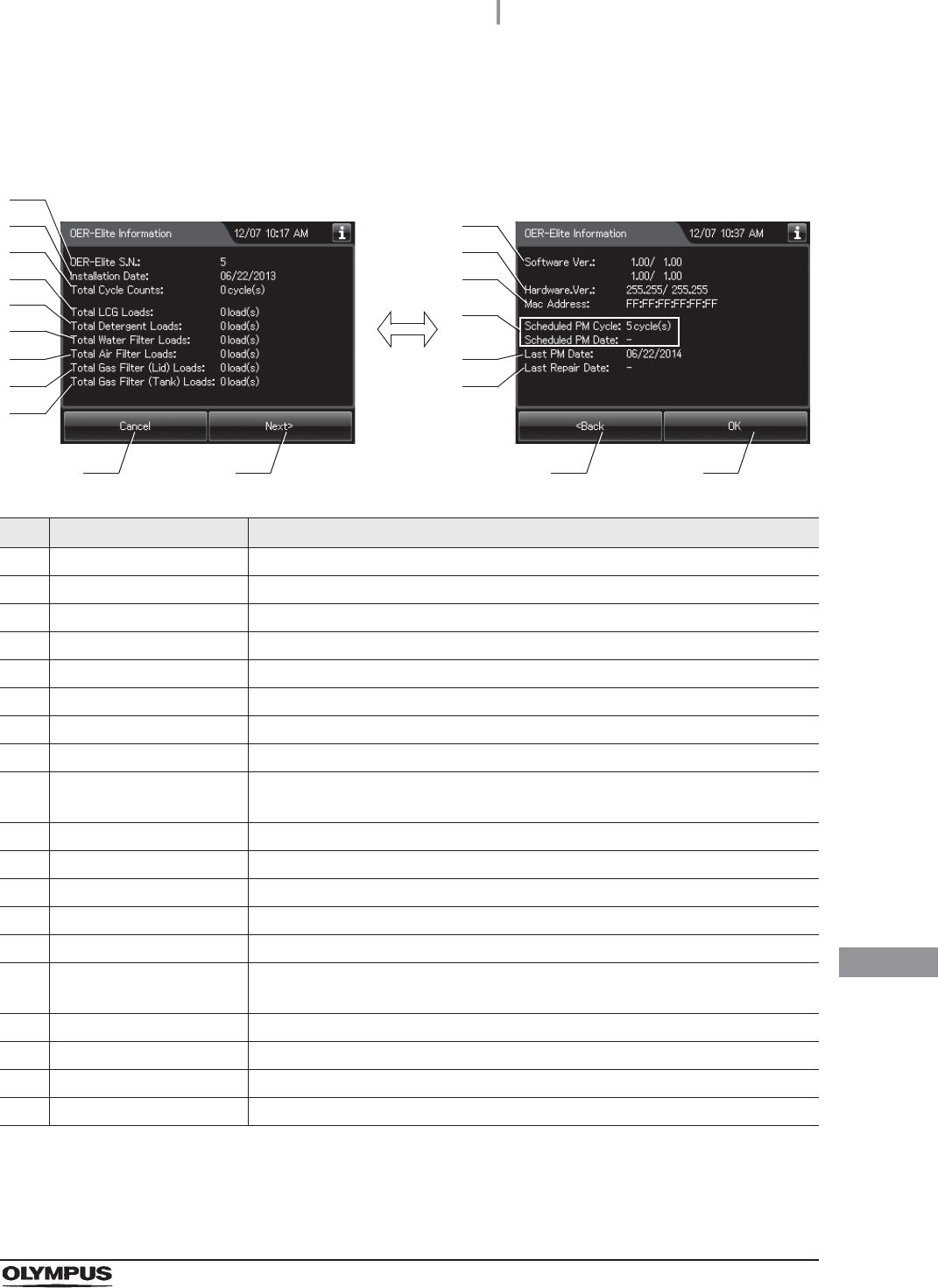
12.2 Reprocessor information check
593
OER-Elite OPERATION MANUAL
Ch.12
3The touch screen displays the OER-Elite Information.
No. Item/Button Description
1 Body number Body number of the reprocessor.
2 Installation Date Date of installation of the reprocessor.
3 Total Cycle Counts Total count of reprocessing cycles performed on the reprocessor.
4 Total LCG Loads Total count of loading disinfectant solution on the reprocessor.
5 Total Detergent Loads Total count of loading detergent solution on the reprocessor.
6 Total Water Filter Loads Total count of loading water filter on the reprocessor.
7 Total Air Filter Loads Total count of loading air filter on the reprocessor.
8 Total Gas Filter (Lid) Loads Total count of loading gas filter on the lid on the reprocessor.
9 Total Gas Filter (Tank)
Loads
Total count of loading gas filter on the tank on the reprocessor.
10 Cancel button Returns to information menu screen.
11 Next button Goes to the next information screen.
12 Software version Version number of the software used in the reprocessor.
13 Hardware version Version number of the hardware used with the reprocessor.
14 MAC address MAC address of the reprocessor.
15 Scheduled PM
Cycles/Date
Information of the next periodic maintenance.
16 Last PM Date Date of the last periodic maintenance.
17 Last Repair Date Date of the last repair.
18 Back button Goes to the previous information screen.
19 OK button Returns to information menu screen.
1
10
2
3
4
5
6
7
8
9
11 18 19
12
13
14
15
16
17
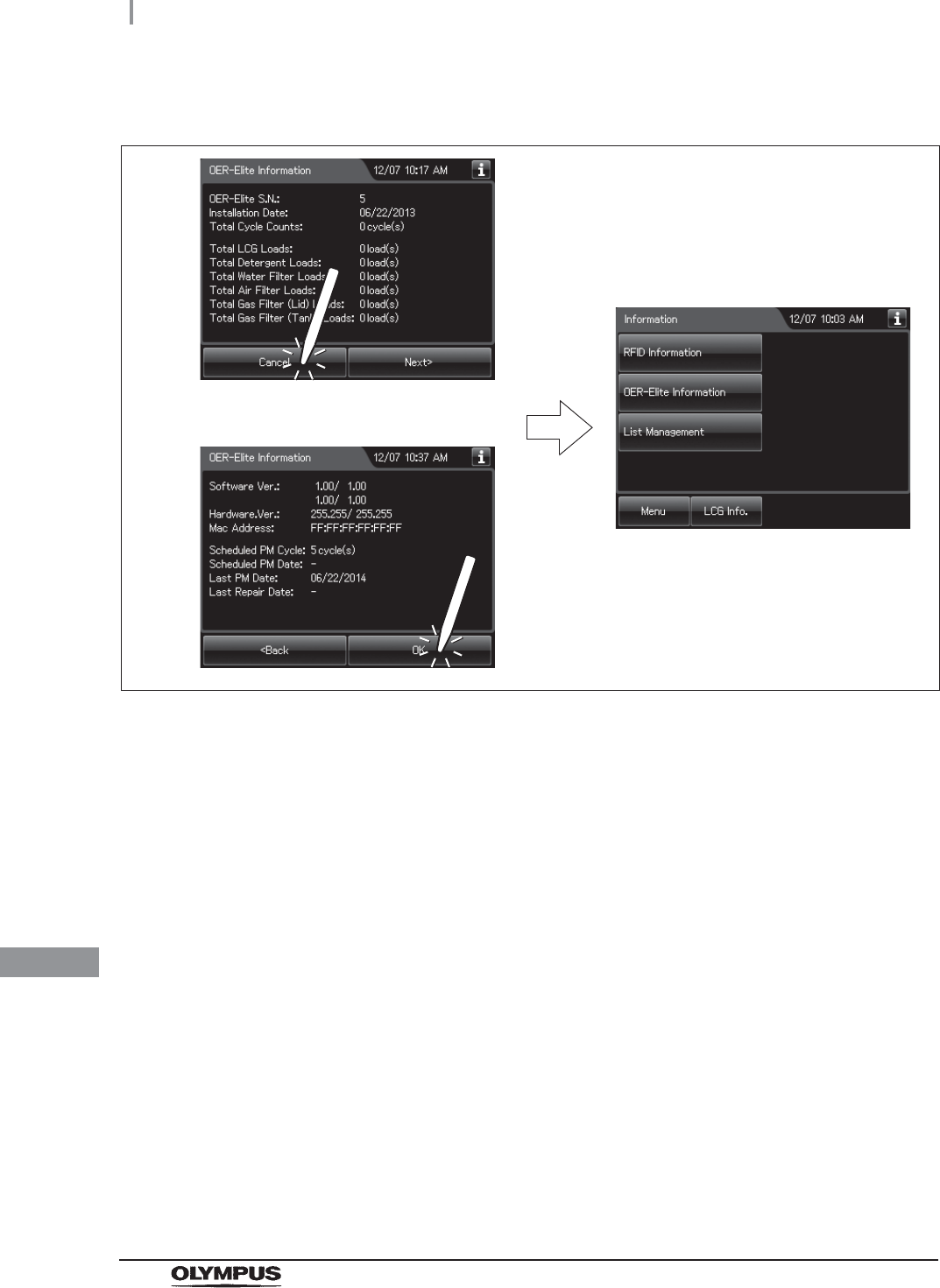
594
12.2 Reprocessor information check
OER-Elite OPERATION MANUAL
Ch.12
4Press the “Cancel” button or “OK” button to go back to the information menu screen.
Figure 12.8

12.3 List management
595
OER-Elite OPERATION MANUAL
Ch.12
This section is to edit the ID list. The IDs edited here can be used in the step “(b) Recalling the
pre-registered ID” on page 54.
NOTE
The ID list contains the following IDs
Scope ID
User ID
Physician ID
Procedure ID
12.3 List management
1Press the “Information” button on the Menu screen.
2Press the “List Management” button.
Figure 12.9
3After selecting the ID list to edit, the ID list
appears.
Figure 12.10
4On the ID select screen, press the “Edit” button to be input. The ID input screen
(software keyboard) will appear.
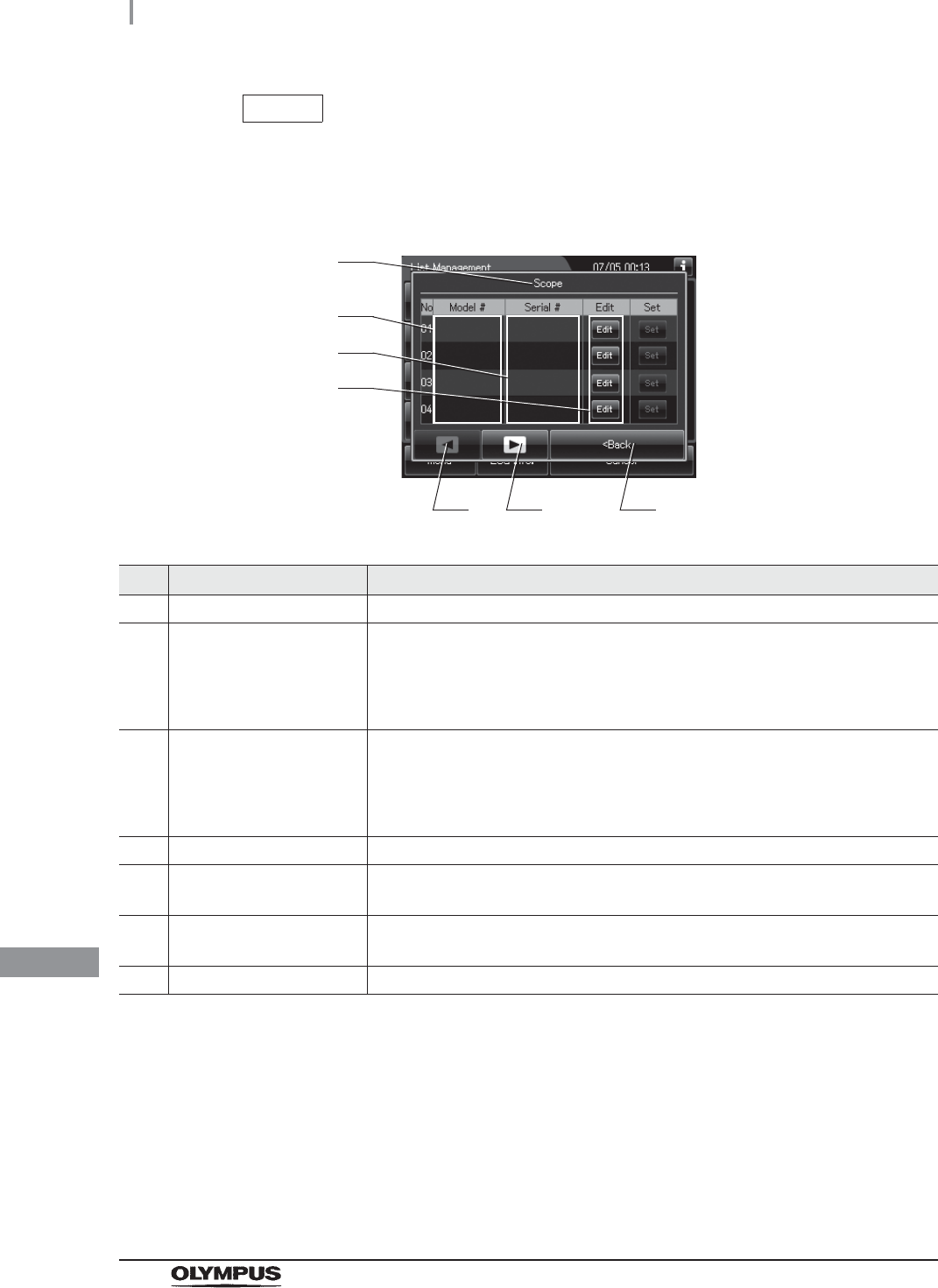
596
12.3 List management
OER-Elite OPERATION MANUAL
Ch.12
NOTE
Fifty IDs can be registered for each ID type.
No. Item/Button Description
1 ID type Type of the currently edited ID.
2 Model # or Name Scope ID list: Displays the model numbers of the endoscopes.
User ID list: Displays the user names.
Physician ID list: Displays the physician names.
Procedure ID list: Displays the procedure names.
3 Serial # or ID Scope ID list: Displays the serial numbers of the endoscopes.
User ID list: Displays the ID number of users.
Physician ID list: Displays the ID number of physicians.
Procedure ID list: Displays the ID number of procedures.
4 Edit buttons Press one of the buttons to open the ID information edit screen.
5 Previous page button Press to go to the next page. When there is no further page to go forward to, the
button turns gray and becomes unavailable.
6 Next page button Press to return to the next page. When there is no further page to turn back to,
the button turns gray and becomes unavailable.
7 Back Press to close the ID select screen.
5Enter the name on the software keyboard displayed on the touch screen.
1
2
5
3
4
6 7
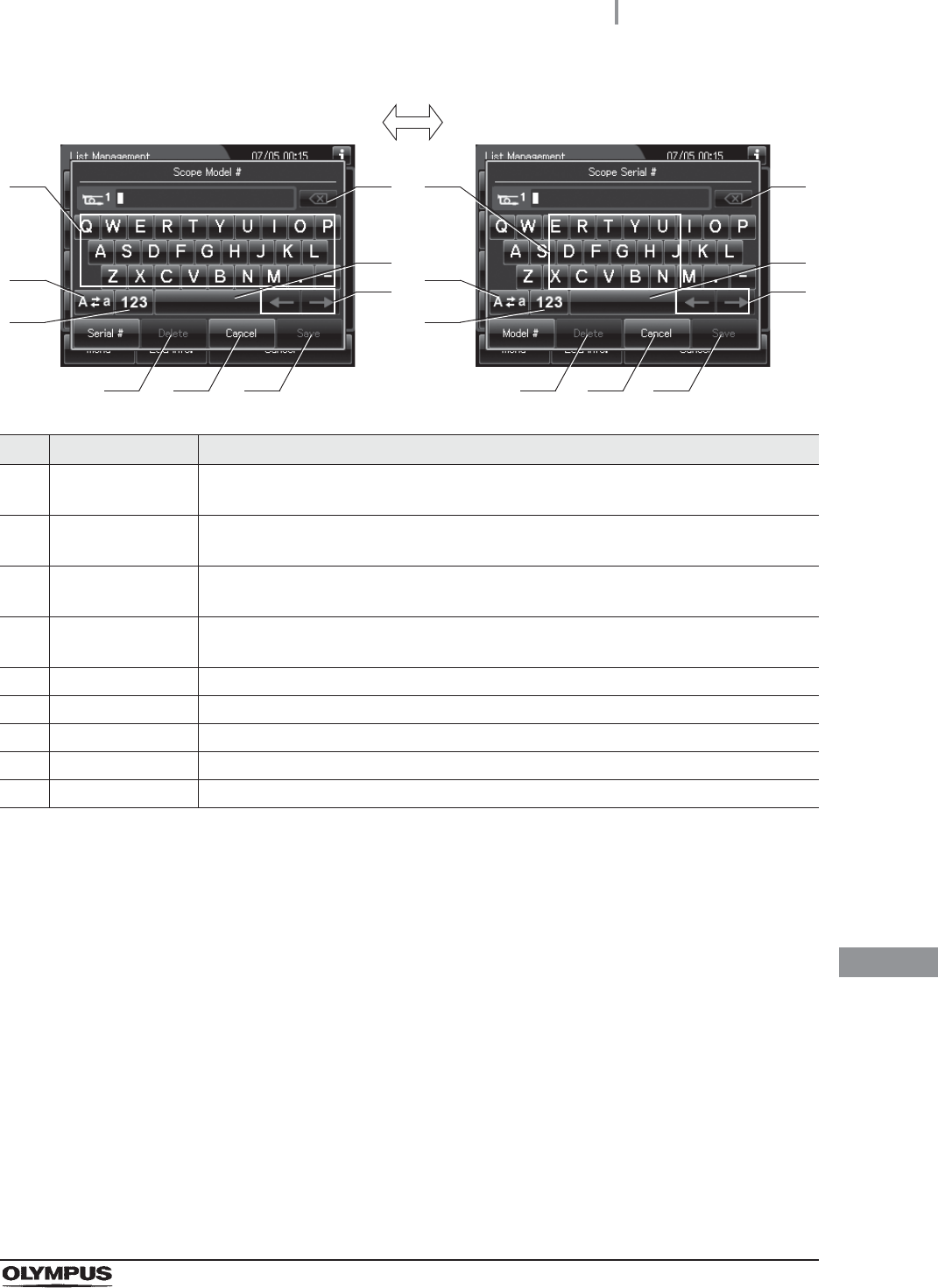
12.3 List management
597
OER-Elite OPERATION MANUAL
Ch.12
No. Button Note
1 Alphabet/
Numeral key
Enter an alphabet or a numeral.
2 Uppercase/
Lowercase
Press “Uppercase/lowercase” button to switch alphabet character on the soft keyboard
between uppercase characters and lowercase characters.
3 Numeric/
Alphabetic
Press “Numeric or Alphabetic” button to switch the input mode between a numeral and
the alphabet.
4 Backspace Press the “Backspace” button to delete the left character of a cursor.
When a cursor is on the left edge, this button turns gray and becomes unavailable.
5 Space Press the “Space” button to insert a space character.
6 Cursor move Press the “Cursor move” button to move the cursor left or right.
7 Delete Press the “Delete” button to delete about all information.
8 Cancel Return to the previous screen without saving the setting value.
9 Save Return to the previous screen and save the entered value.
6Press the “Save” button to save the selected setting.
7Press the “Back” button.
41
2
3
5
6
8 9
41
2
3
5
6
8 9
Alphabet input Numeral input
7 7
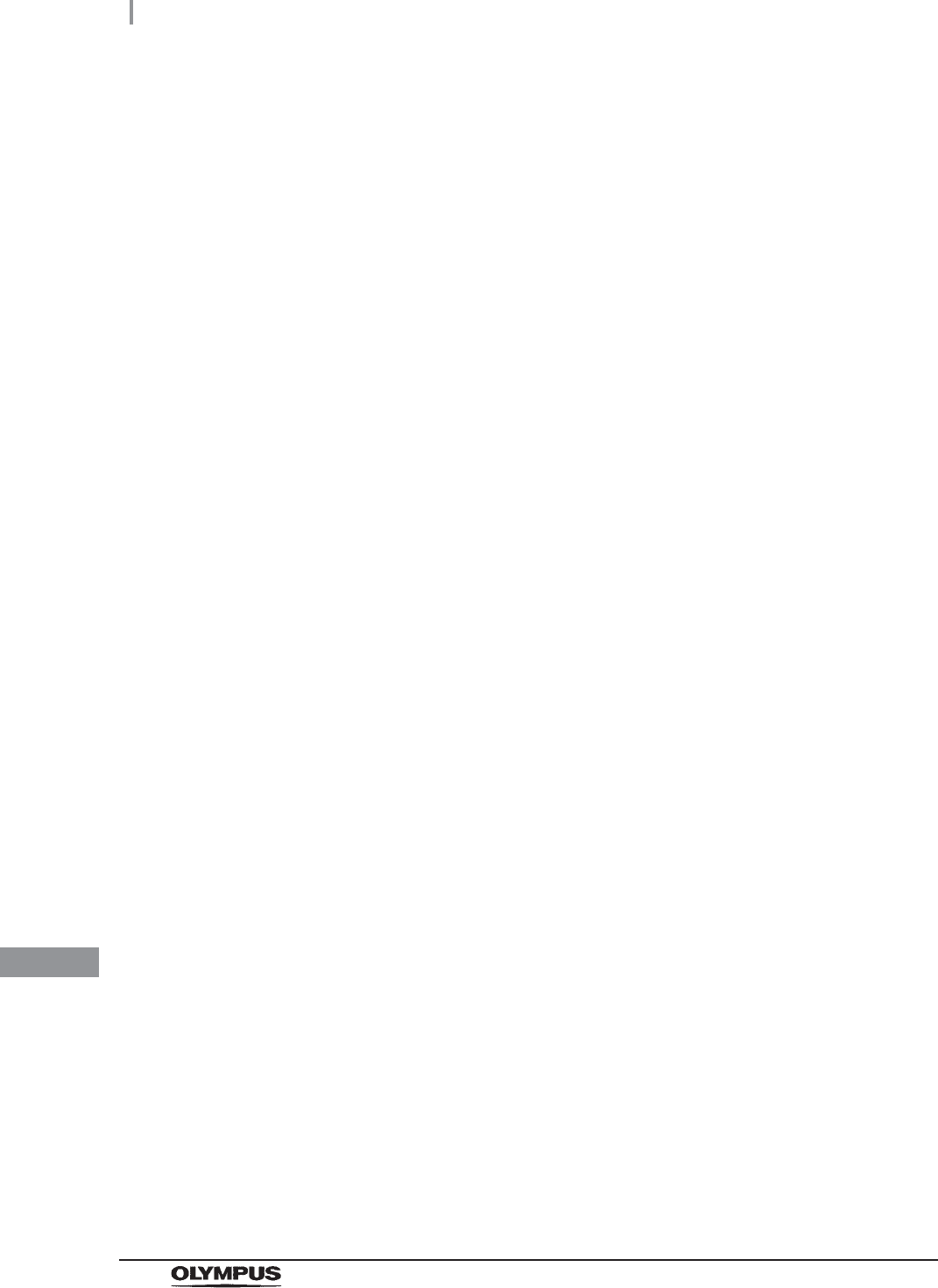
598
12.3 List management
OER-Elite OPERATION MANUAL
Ch.12
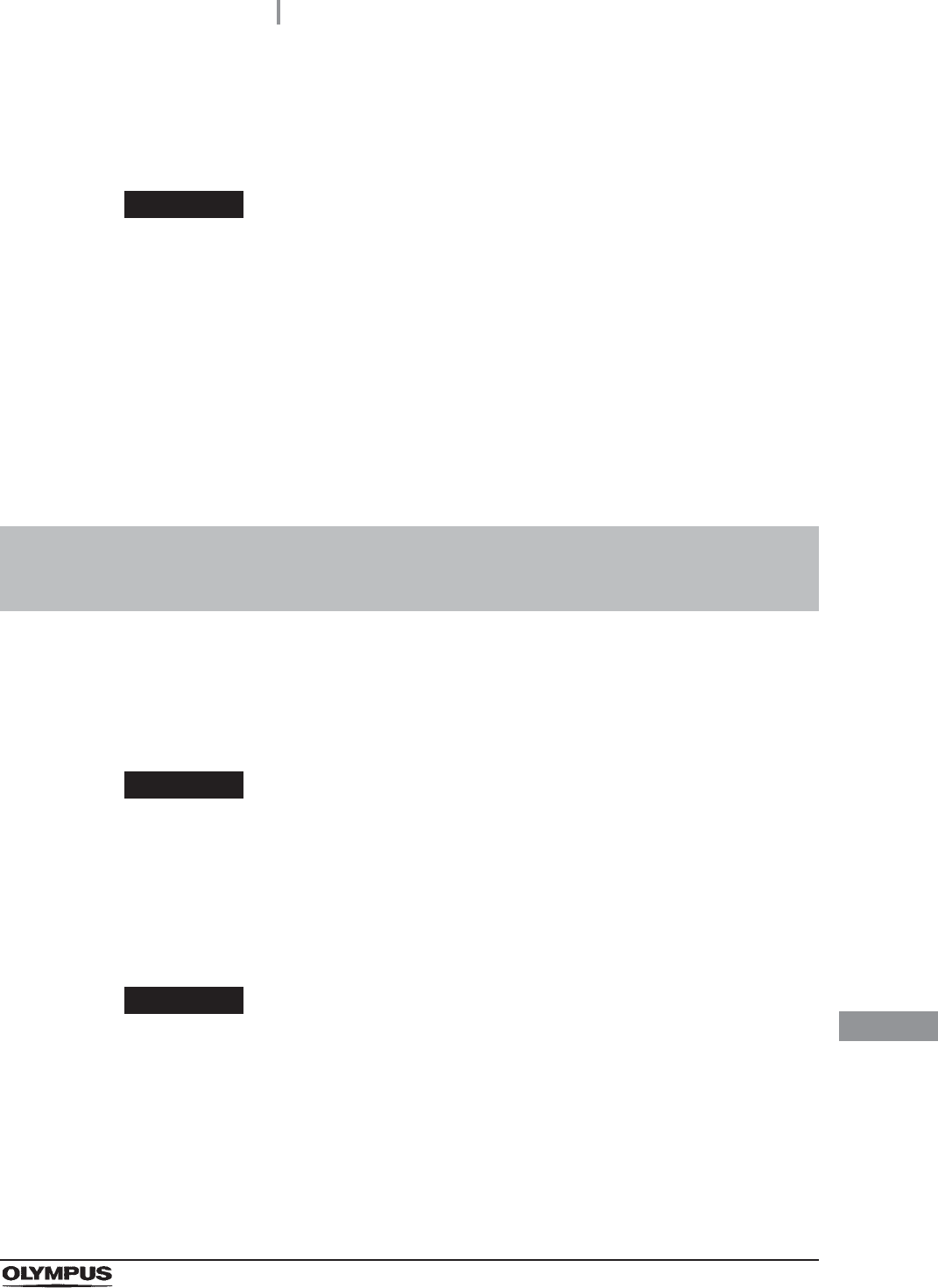
13.1 Emergency stop and automatic processing after stopping
599
OER-Elite OPERATION MANUAL
Ch.13
Chapter 13 Troubleshooting and Repair
WARNING
If the reprocessing process is interrupted, the endoscopes will not be properly
reprocessed. In this case, reprocessing in the OER-Elite should be started again
from the beginning.
If any irregularity is detected during an inspection or if the reprocessor is clearly malfunctioning, do not
use it. Contact Olympus for repair.
Some malfunctions may be corrected by referring to the Section 13.2, “Troubleshooting guide”. If the
problem cannot be resolved by the described remedial action, do not use the reprocessor and contact
Olympus.
The OER-Elite can be stopped at any time during operation by pressing the STOP button on the main
control panel. The touch screen will display error code [E000] at this time. When the reprocessor is
stopped, it identifies the situation in which it was stopped and automatically performs the required
operations (including draining of the reprocessing basin), to return the unit to an idle state.
WARNING
• When a process is interrupted, be sure to execute it again from the beginning. An
endoscope that has not been subjected to a complete, error-free process is not
safe for patient use. Otherwise, the endoscope reprocessing may be insufficient.
• If the process is stopped because of a problem with the reprocessor, contact
Olympus.
CAUTION
Do not press the power switch OFF during operation. Otherwise, fluid will remain in
the reprocessing basin without automatic draining and Air Purge, and the
reprocessor may malfunction.
Treatment after automatic processing has completed
Remove the cause of the reprocessor stoppage, and start the process again from the beginning.
13.1 Emergency stop and automatic processing after
stopping
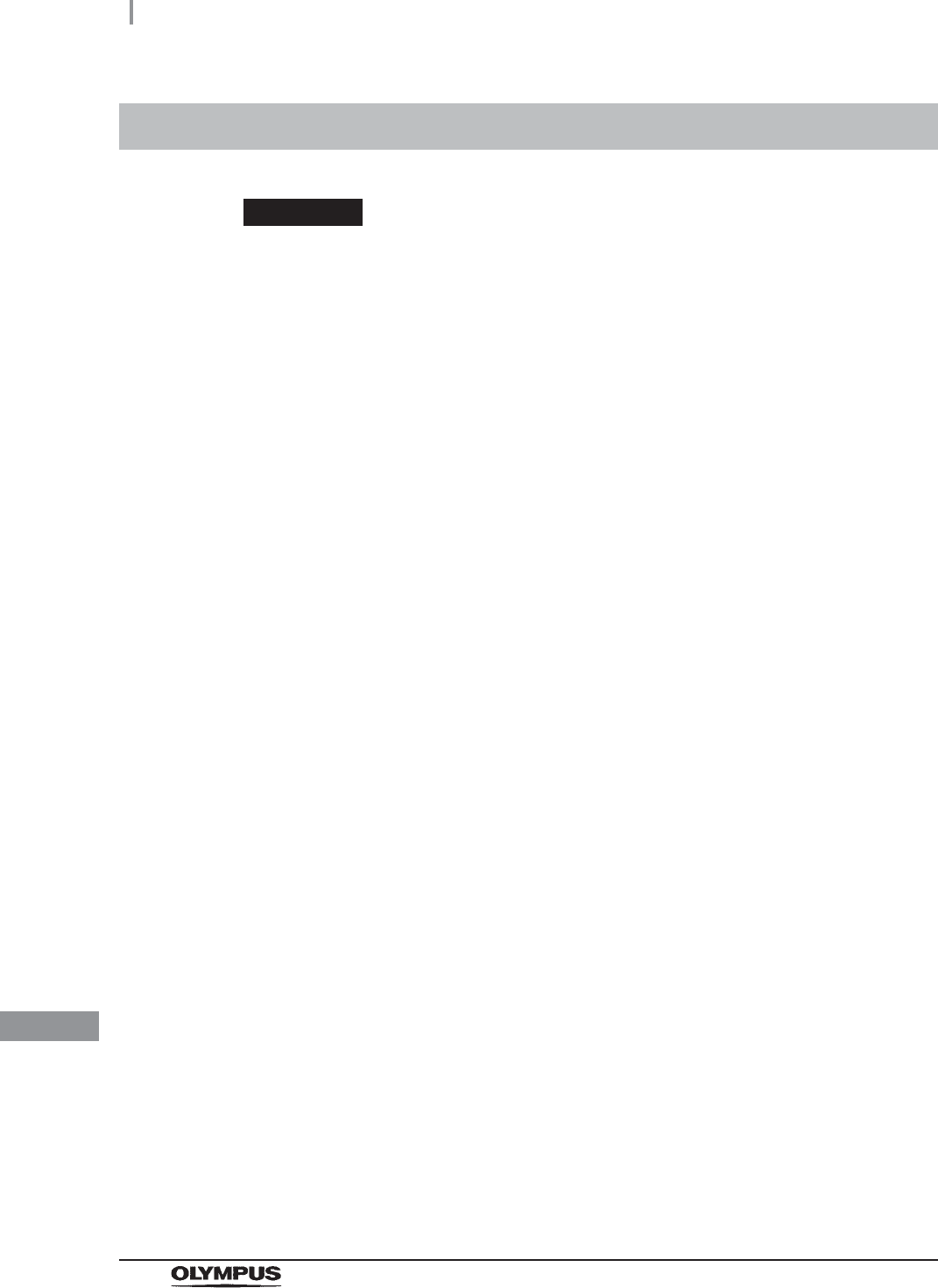
600
13.2 Troubleshooting guide
OER-Elite OPERATION MANUAL
Ch.13
WARNING
• Before handling the disinfectant solution, read the cautions carefully and use it as
instructed. It is especially important to know what to do if the disinfectant solution
comes in contact with your skin and eyes.
• When handling the disinfectant solution, wear personal protective equipment to
prevent any disinfectant from getting on your skin and eyes or being inhaled. Avoid
direct physical contact and inhalation of vapors. If any disinfectant solution gets in
your eyes, immediately rinse with a large amount of fresh water and then consult a
medical specialist. Personal protective equipment, such as eyewear, face mask,
moisture-resistant clothing, and chemical-resistant gloves that fit properly and are
long enough so that your skin and eyes is not exposed. All personal protective
equipment should be inspected before use and replaced periodically before it is
damaged.
• Do not put your hand behind the disinfectant solution bottle drawer. Irritation of skin
due to contact with concentrated disinfectant solution, injury by touching a
projection, or malfunction of this reprocessor may result.
• In the event, in case the process stops and fluid remains in the reprocessing basin
due to a power failure or malfunction, keep the lid closed and do not contact with
fluid in the basin. Also, do not put the fluid close to fire. Otherwise, adverse physical
effects caused by inhalation of disinfectant vapor or physical contact with
chemicals, or fire hazard from the residual alcohol may occur.
13.2 Troubleshooting guide
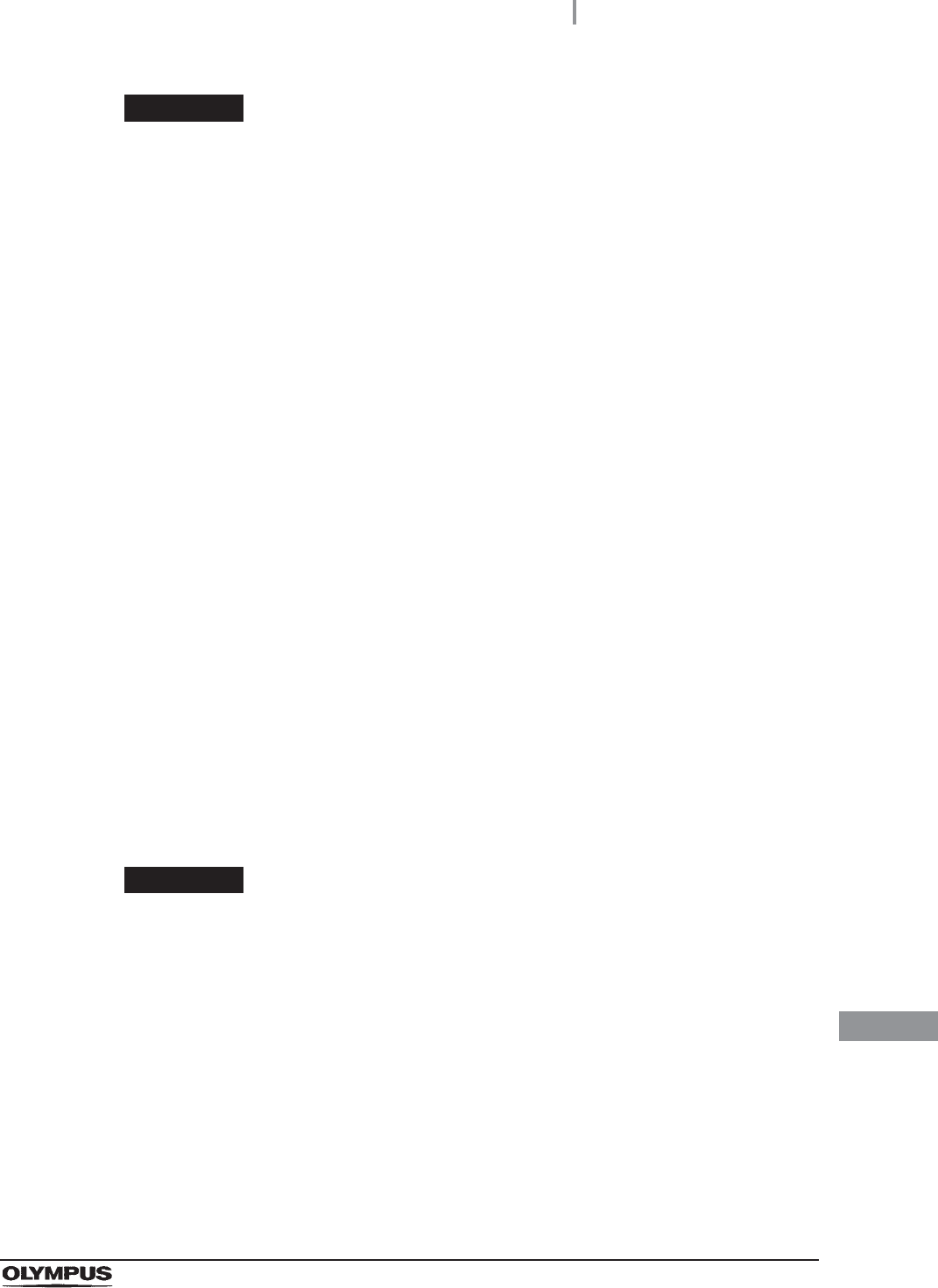
13.2 Troubleshooting guide
601
OER-Elite OPERATION MANUAL
Ch.13
WARNING
• When using disinfectant solution and alcohol, Olympus recommends the use of gas
filters and operating this reprocessor in a well-ventilated area.
Wear a face mask, gloves, and protective clothes to minimize aspiration and
skin contact.
Wear goggles for eye protection.
Refer to the following association’s guidelines related to ventilation:
If the person operating the reprocessor exhibits an allergic reaction or symptoms,
no matter how slight, they should discontinue the task they are performing and
vacate the room.
• In the event, in case the process stops and fluid remains in the reprocessing basin
due to a power failure or malfunction, keep the lid closed and do not contact with
fluid in the basin. Also, do not put the fluid close to fire. Otherwise, adverse physical
effects caused by inhalation of disinfectant vapor or physical contact with
chemicals, or fire hazard from the residual alcohol may occur.
CAUTION
• If a rinse is performed while an error is actively being displayed and disinfectant
solution is still in the reprocessing basin, the rinse process will drain the disinfectant
out of the reprocessor. To prevent this, refer to “Error codes and remedial
actions” on page 602 for instructions for collecting the disinfectant.
• Do not press the power switch OFF when an error code is displayed. Doing so may
result in malfunction. The reprocessor will automatically start a process to address
the error code. (The error code will blink during automatic processing.) After the
error code starts blinking, follow the instructions in “Error codes and remedial
actions” below.
SGNA (Society of Gastroenterology Nurses and Associates)
ASGE (American Society of Gastroenterological Endoscopy)
APIC (Association for Professionals of Infection Control and Epidemiology)
AORN (Association of Preoperative Registered Nurses)
ASTM (American Society for Testing and Materials)
OSHA (Occupational Safety and Health Administration)
ACGIH (American Conference of Governmental Industrial Hygienists)
NIOSH (National Institute for Occupational Safety and Health)
AIA (American Institute of Architects)
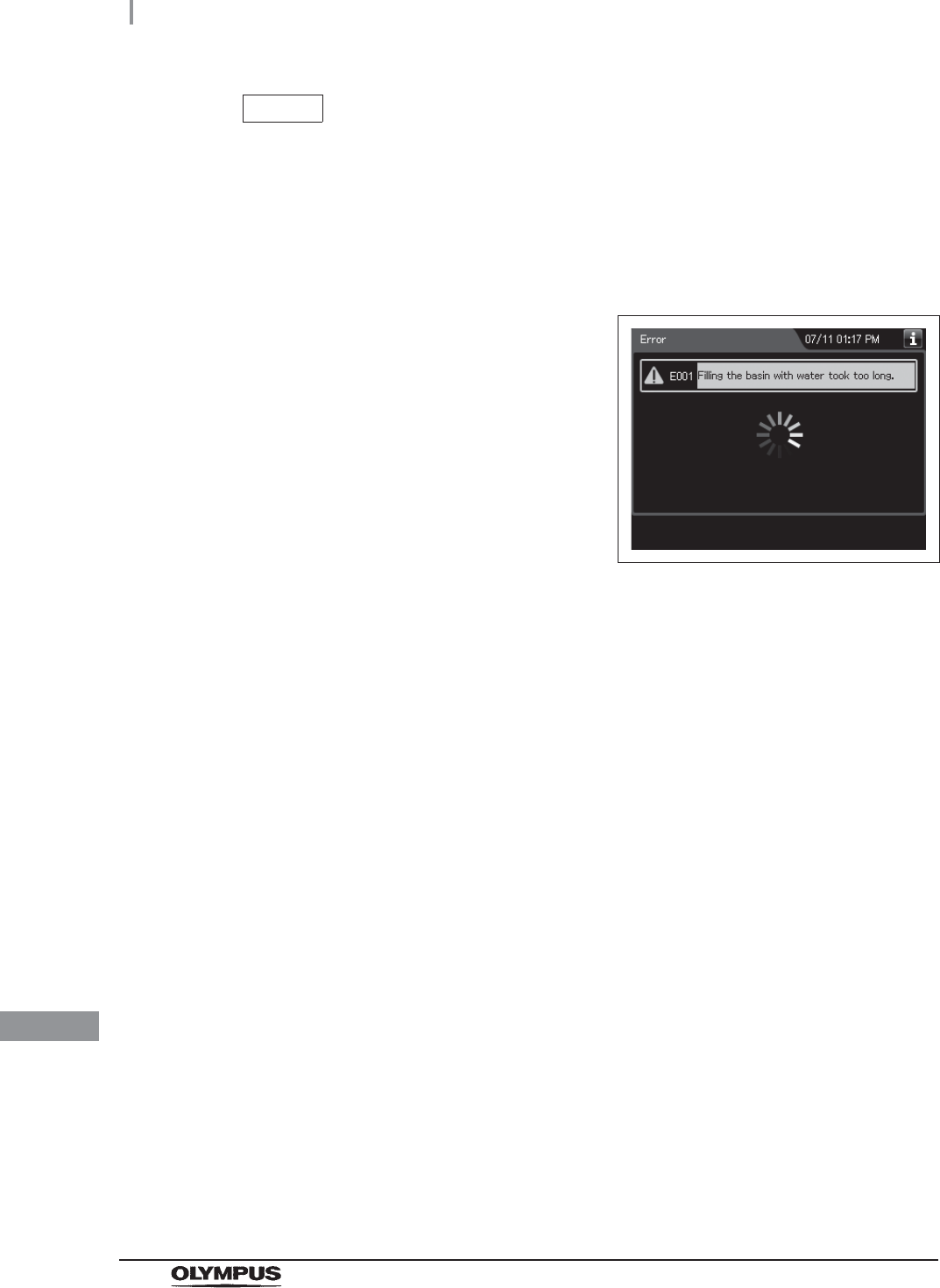
602
13.2 Troubleshooting guide
OER-Elite OPERATION MANUAL
Ch.13
NOTE
To complete the process properly, some process cannot be stopped with STOP
button.
Error codes and remedial actions
1If the reprocessor detects irregularity, buzzer
beeps for three seconds and the error code will
be displayed on the touch screen. While the
touch screen displays the following screen, the
reprocessor executes the automatic
processing.
Figure 13.1
2When the automatic processing is completed, the buzzer beeps for three second and
the touch screen displays the possible cause or the remedial action. The error code
remains on the touch screen and the buzzer beeps intermittently until the error code is
cleared. If the touch screen displays possible causes, press the “OK” button to display
the remedial actions.
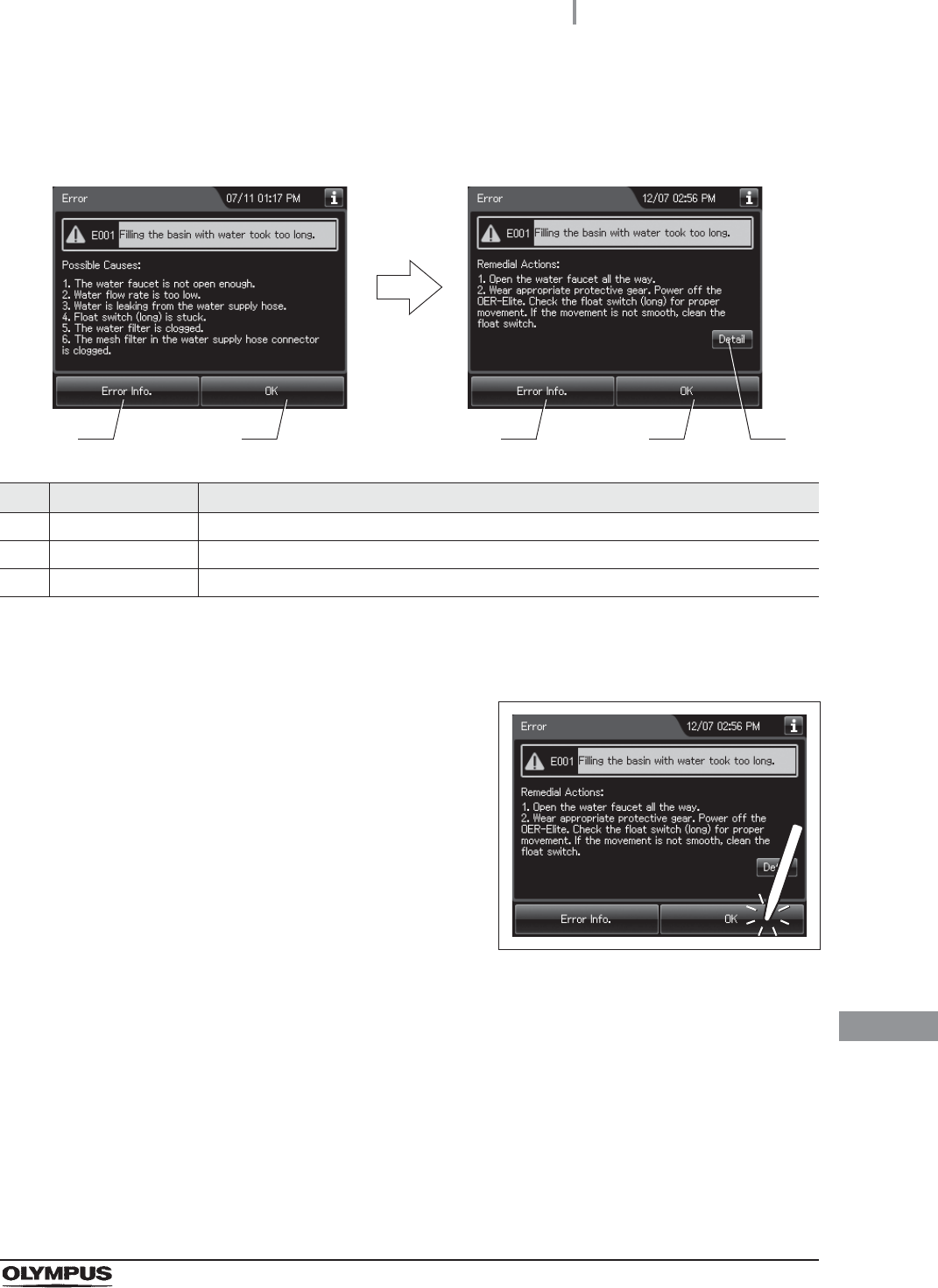
13.2 Troubleshooting guide
603
OER-Elite OPERATION MANUAL
Ch.13
No. Button Description
1 Error Info. Press to display the error info screen.
2 OK Press to go to the next screen.
3 Detail Press to display the details of remedial actions.
3Perform remedial actions according to the instruction described in the table on
page 605 through 613 or the instructions displayed on the touch screen.
4Press the “OK” button.
Figure 13.2
5Read the instructions displayed on the touch screen and conduct the processes. Then
Press the “OK” button to clear the error code.
1
Possible causes screen Remedial action screen
2 1 2 3
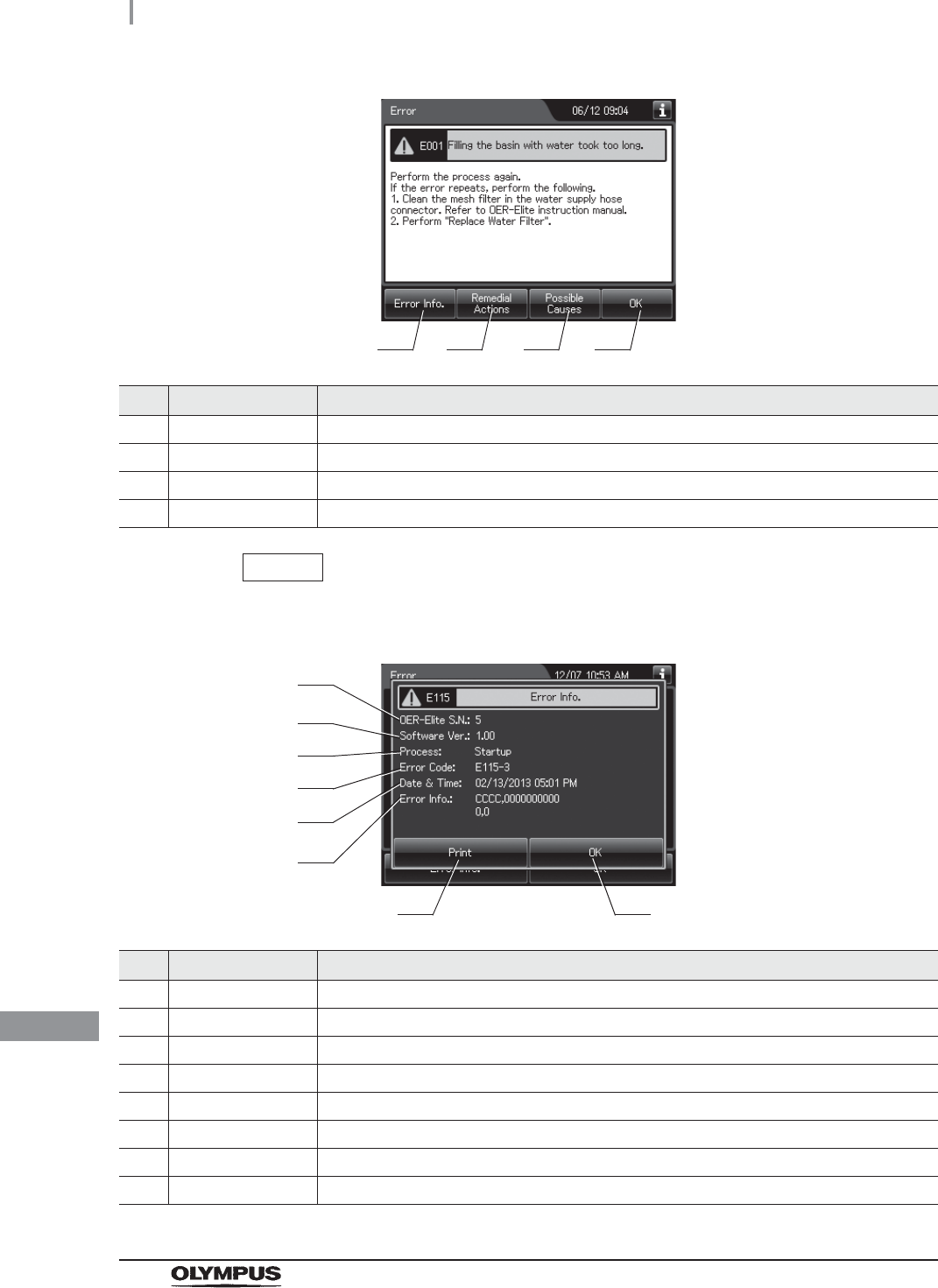
604
13.2 Troubleshooting guide
OER-Elite OPERATION MANUAL
Ch.13
NOTE
For the error info screen, see the following figure.
No. Button Description
1 Error Info. Press to display the error info screen.
2 Remedial Actions Press to display the remedial actions.
3 Possible Causes Press to display the possible causes.
4 OK Press to clear the error.
No. Item/Button Description
1 Serial number Serial number of the reprocessor.
2 Software Ver. Version number of the software used in the reprocessor.
3 Process Process in which error is generated.
4 Error Code Error code of error.
5 Date & Time Date and time of occurrence of error.
6 Error Info. Information required for contacting Olympus.
7 Print button Press to print information of the error.
8 OK button Press to close the error info screen.
1 2 3 4
7 8
1
2
3
4
5
6
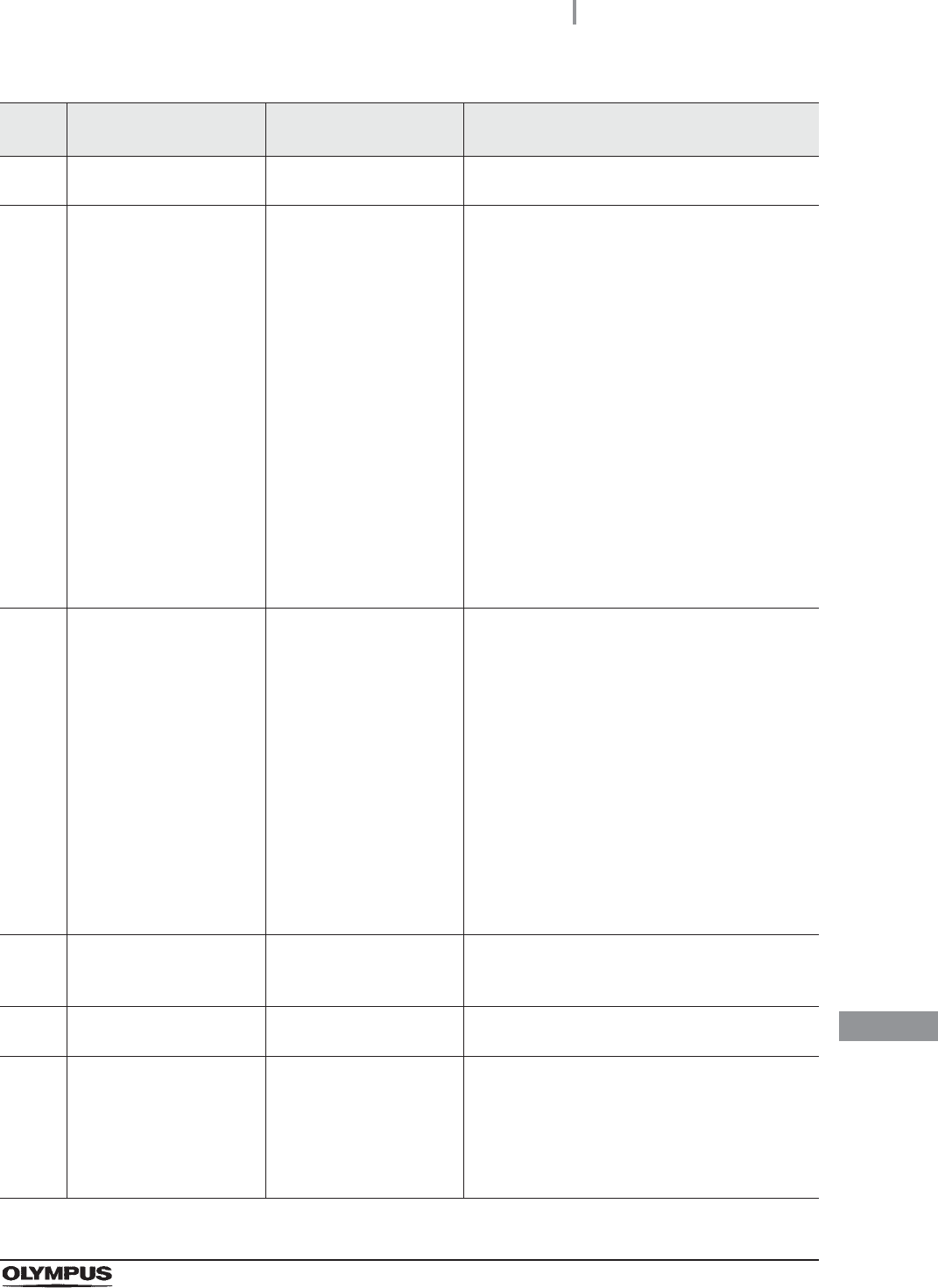
13.2 Troubleshooting guide
605
OER-Elite OPERATION MANUAL
Ch.13
Error
code Problem Possible causes Remedial actions
E000 Process was interrupted. Stop button was pressed
during the process.
Perform the process again.
E001 Filling the basin with
water took too long
(water supply time is
beyond maximum
setting).
• The water faucet is not
open enough.
• Water flow rate is too
low.
• Water is leaking from
the water supply hose.
• Float switch (long) is
stuck.
• The water filter is
clogged.
• The mesh filter in the
water supply hose
connector is clogged.
1 Perform the following.
Open the water faucet all the way.
Check if water is leaking from the water
supply hose.
Power off the OER-Elite and check the
float switch (long) for a proper movement.
If not, clean that.
2 Perform the process again. If the error
repeats, perform the following.
Replace the water filter.
oRefer to Section 8.4, “Replacing the
water filter (MAJ-824 or MAJ-2318)”.
Clean the mesh filter in the water supply
hose connection port.
oRefer to Section 9.7, “Cleaning the
mesh filter in the water supply hose
connector”.
E002 Cleaning fluid is not
discharged.
• Drain hose is
improperly installed.
• Drain port mesh filter in
basin is clogged.
1 Check the drain hose for proper installation.
(Height of the drain hose should be less than
60 cm.)
2 Wait until the fluid in the basin drained
completely.
3 Wear appropriate protective gear and clean
the drain port mesh filter basin. oRefer to
Section 10.3, “Cleaning the mesh filters”.
4 Close the lid by pushing until it clicks and
perform the air purge to remove water.
oRefer to Section 7.6, “Air purge”.
5 Perform “Rinse”. oRefer to Section 7.5,
“Rinse”.
6 Perform the process again.
E004 Cleaning fluid decreases
during the cleaning
process.
Internal problem with the
reprocessor.
Contact Olympus.
E005 Basin fluid level is too
high.
Irregularity in the fluid
level sensor.
1 Close the water faucet.
2 Contact Olympus.
E006 Fluid level sensor
malfunctions.
Float switch (short) or
float switch (long) is
stuck.
1 Clean the float switches.
oRefer to Section 10.4, “Cleaning the float
switches”.
2 Perform “Rinse”.oRefer to Section 7.5,
“Rinse”.
3 Perform the process again.
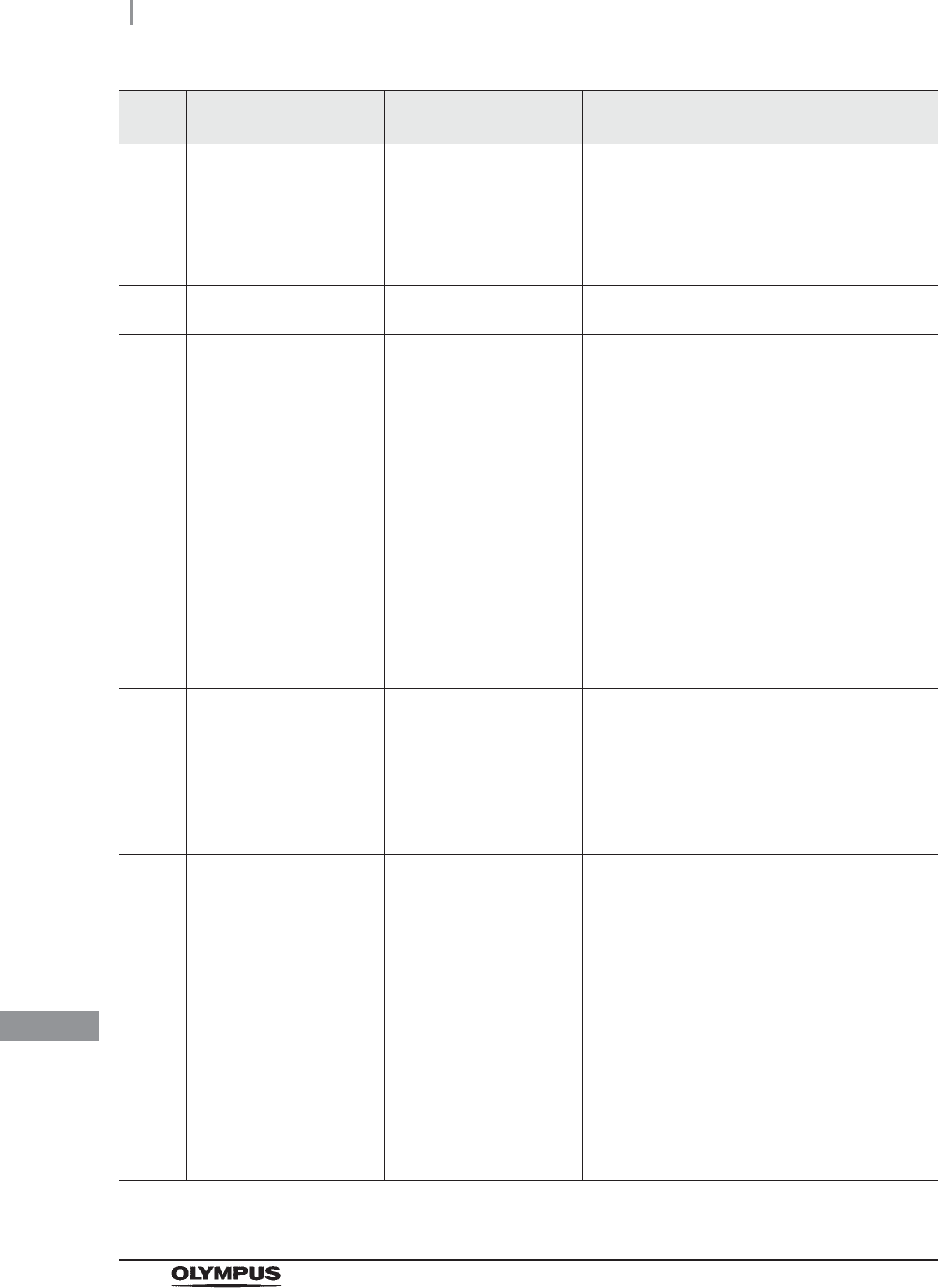
606
13.2 Troubleshooting guide
OER-Elite OPERATION MANUAL
Ch.13
E007 Fluid level sensor
malfunctions.
Float switch (short) is
stuck.
1 Clean the float switches.
oRefer to Section 10.4, “Cleaning the float
switches”.
2 Perform “Rinse”. oRefer to Section 7.5,
“Rinse”.
3 Perform the process again.
E008 Inappropriate water
temperature.
Water temperature is too
high.
Check the water temperature is in the range of
5 – 28 qC (41 – 82 qF. )
E011 There is too much LCG in
the disinfectant solution
tank.
• Irregularity in the drain
hose.
• Clogging of the drain
port of the
reprocessing basin.
• Close the lid if it is open. Automatic
Processing will start after the lid is closed.
• Perform the following.
1 Check the drain hose for proper installation
(height of the drain hose should be less than
60 cm.)
2 Wear appropriate protective gear and clean
the mesh filter in the drain port of the basin.
oRefer to Section 10.3, “Cleaning the mesh
filters”.
3 Perform “Rinse”. oRefer to Section 7.5,
“Rinse”.
4 Perform MRC check. oRefer to Section 4.3,
“MRC check setting”.
5 Perform the process again.
E012 There is insufficient
amount of LCG in the
disinfectant solution tank.
Blockage of the
ventilation openings on
the gas filter case (lid).
1 Check that the ventilation openings on the
gas filter case (lid) are not blocked.
2 Perform “Drain LCG”. oRefer to Section 8.2,
“Replacing the disinfectant solution”.
3 Perform “Load LCG”. oRefer to Section 8.2,
“Replacing the disinfectant solution”.
4 Perform the process again.
E013 Basin exists a rinse
water.
• Drain hose is
improperly installed.
• Drain port mesh filter in
basin is clogged.
1 Check the drain hose for proper installation.
(Height of the drain hose should be less than
60 cm.)
2 Wait until the fluid is drained completely.
3 Wear appropriate protective gear and clean
the drain port mesh filter in basin.
4 Perform “Rinse”. oRefer to Section 7.5,
“Rinse”.
5 If the quantity of LCG in the disinfectant
solution tank is not sufficient, perform “Drain
LCG”, then “Load LCG”. oRefer to
Section 8.2, “Replacing the disinfectant
solution”.
6 Perform the process again.
Error
code Problem Possible causes Remedial actions
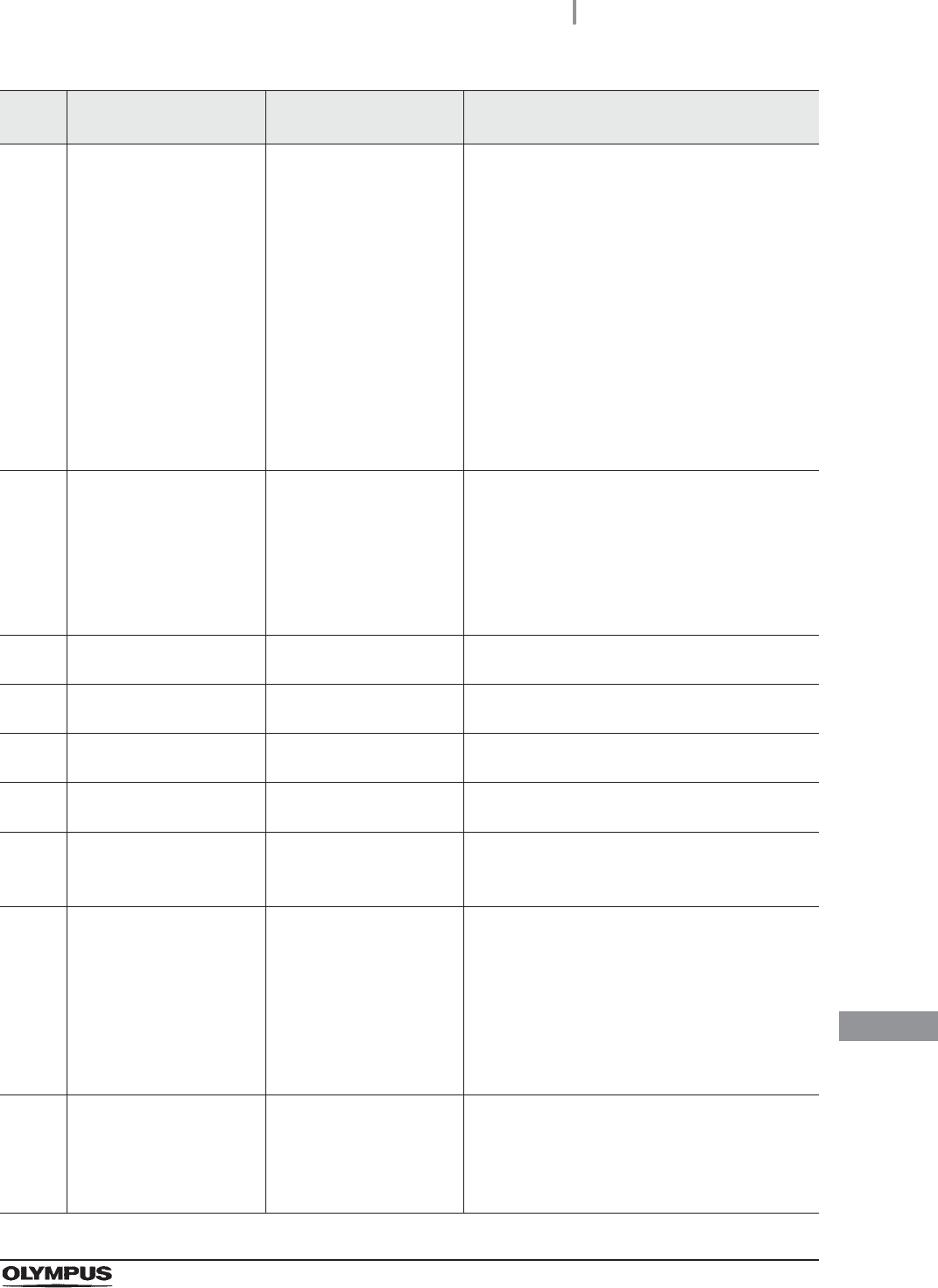
13.2 Troubleshooting guide
607
OER-Elite OPERATION MANUAL
Ch.13
E014 LCG cannot be returned
to the tank.
• Blockage of the
ventilation openings on
the gas filter case (lid).
• Drain port mesh filter in
basin is clogged.
1 Check that the ventilation openings on the
gas filter case (lid) are not blocked.
2 Wait until the fluid in the basin collected
completely.
3 Wear appropriate protective gear and clean
the drain port mesh filter in basin.
4 Perform “Rinse”. oRefer to Section 7.5,
“Rinse”.
5 If the quantity of LCG in the disinfectant
solution tank is not sufficient, perform “Drain
LCG”, then “Load LCG”. oRefer to
Section 8.2, “Replacing the disinfectant
solution”.
6 Perform the process again.
E015 Fluid level sensor
malfunctions.
Float switch (short) is
stuck.
1 Power off the OER-Elite. Wear appropriate
protective gear and check the float switch
(short) for proper function. If not clean, clean
the fluid level sensor”.
2 Perform “Rinse”. oRefer to Section 7.5,
“Rinse”.
3 Perform the process again.
E016 It takes too long to fill the
basin with LCG.
Internal problem with the
reprocessor.
Contact Olympus.
E017 LCG cannot be heated. Internal problem with the
reprocessor.
Contact Olympus.
E018 Temperature sensor
malfunctions.
Internal problem with the
reprocessor.
Contact Olympus.
E019 LCG temperature out of
range.
Internal problem with the
reprocessor.
1 Power off the OER-Elite.
2 Contact Olympus.
E020 Heat LCG Timer could
not be executed.
• OER-Elite was
powered off.
• Power loss.
Perform “Heat LCG”. oRefer to Section 7.2,
“Heat LCG”.
E021 Insufficient air purge
pressure.
• Air filter is not installed
properly.
• Air filter is clogged.
1 Check if the air filter is firmly attached.
2 If the air filter is firmly attached, the air filter
may be clogged. Perform “Replacing the air
filter”. oRefer to Section 8.5, “Replacing the
air filter (MAJ-823)”.
3 Perform the air purge. oRefer to Section 7.6,
“Air purge”.
4 Perform the process again.
E022 Insufficient fluid pressure. The circulation port mesh
filter in basin is clogged.
1 Wear appropriate protective gear and clean
the circulation port mesh filter in basin.
oRefer to Section 10.3, “Cleaning the mesh
filters”.
2 Perform the process again.
Error
code Problem Possible causes Remedial actions
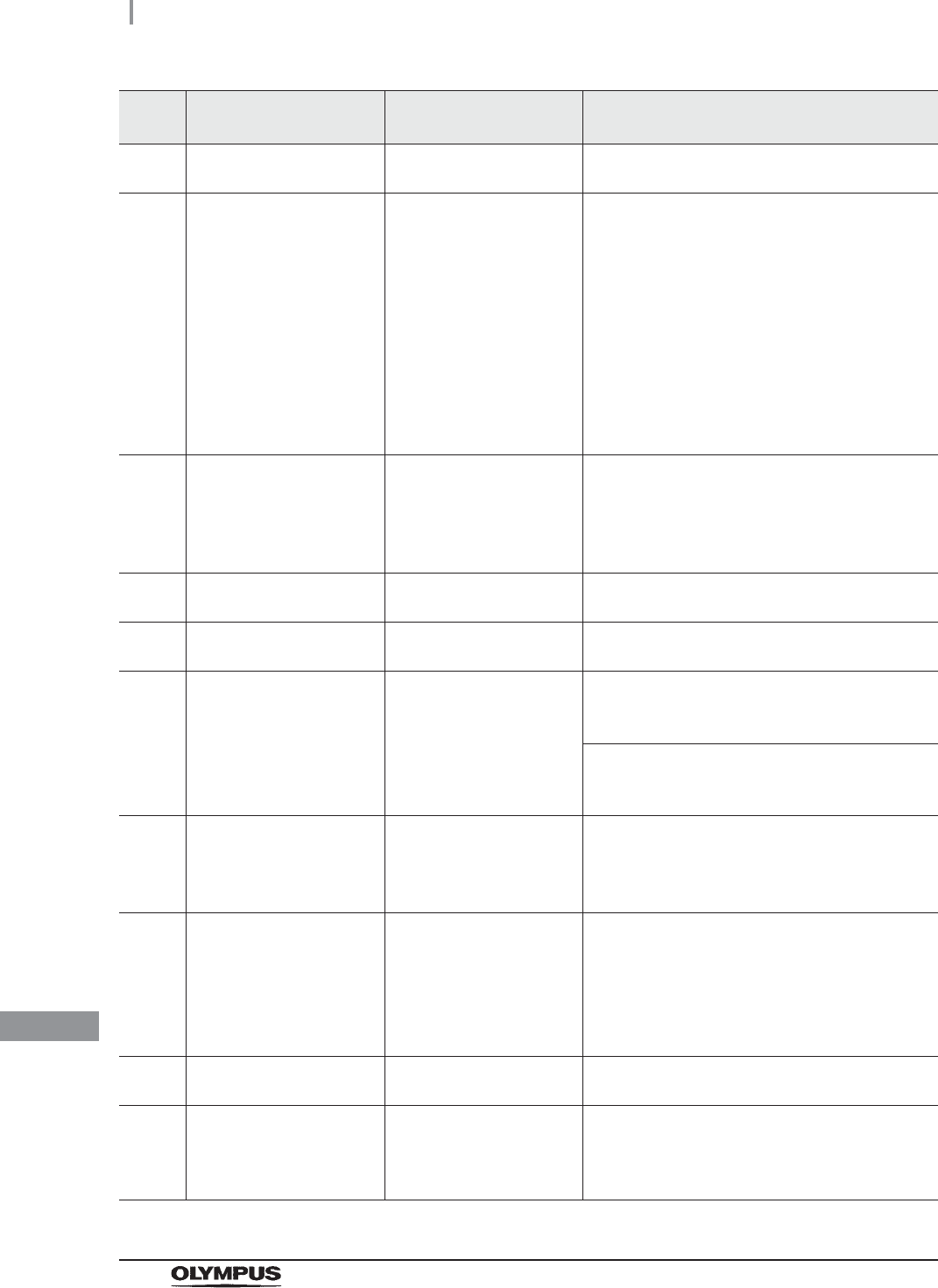
608
13.2 Troubleshooting guide
OER-Elite OPERATION MANUAL
Ch.13
E023 Excessive fluid pressure. Internal problem with the
reprocessor.
Contact Olympus.
E024 Channel Monitor Error • Connecting tubes are
not connected.
• Leak test air tube is not
connected.
• Endoscope’s suction
channel is clogged.
• Unnecessary
connecting tubes are
connected to
connectors in the
reprocessing basin.
Take optimum remedial actions as described in
“When the error code [E024] is displayed
during the reprocessing process” on page 614.
E026 Insufficient fluid flow rate. The circulation port mesh
filter in basin is clogged.
1 Wear appropriate protective gear and clean
the circulation port mesh filter in basin.
oRefer to Section 10.3, “Cleaning the mesh
filters”.
2 Perform the process again.
E027 Internal valves
malfunction.
Internal problem with the
reprocessor.
Contact Olympus.
E031 The lid is open. Internal problem with the
reprocessor.
Contact Olympus.
E041 The power was lost
during the process.
• Power loss.
• OER-Elite was
powered off.
1 Check that the power cord is connected
firmly.
2 Perform the process again.
Note:
Do not power off the OER-Elite during the
process.
E051 Fluid leakage inside the
OER-Elite.
Internal problem with the
reprocessor.
1 Close the water faucet.
2 Turn the power off.
3 Disconnect the power cord from the outlet.
4 Contact Olympus.
E052 Fluid leakage inside the
OER-Elite.
Internal problem with the
reprocessor.
1 Close the water faucet.
2 Turn the power off.
3 Disconnect the power cord from the outlet.
4 Check the O-ring of leak test connector is
firmly attached.
5 Contact Olympus.
E061 Ultrasonic cleaning is not
functioning.
Irregularity in the
ultrasonic oscillator.
Contact Olympus.
E071 Abnormalities with the
disinfectant bottle drawer
sensor.
Internal problem with the
reprocessor.
Contact Olympus.
If the odor of disinfectant solution increases,
wear appropriate personal protective
reprocessor.
Error
code Problem Possible causes Remedial actions
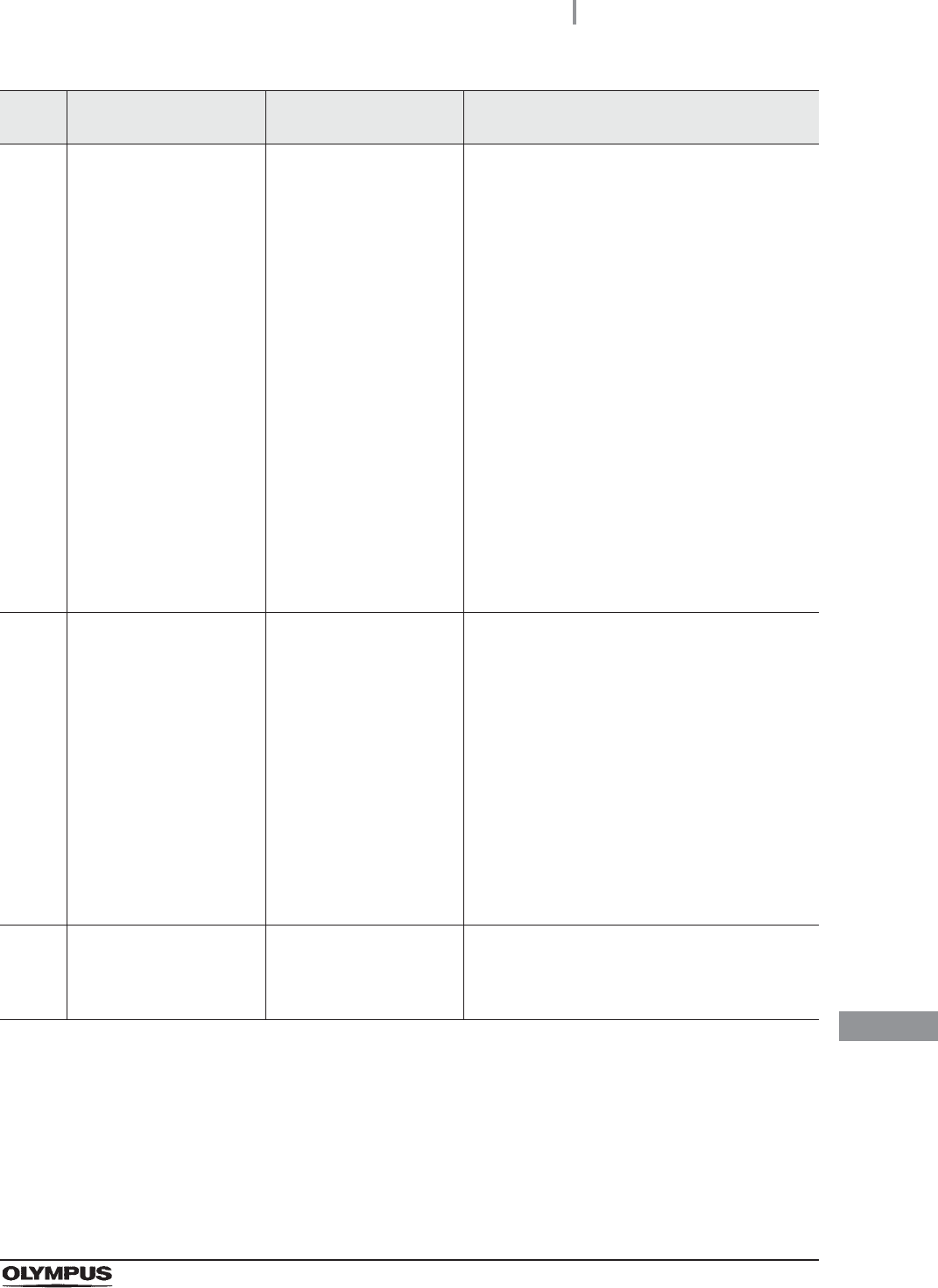
13.2 Troubleshooting guide
609
OER-Elite OPERATION MANUAL
Ch.13
E072 LCG in the tank cannot
be discharged.
• Disinfectant collection
hose is improperly
connected.
• Drain port mesh filter in
basin is clogged.
• Drain hose is
improperly installed.
• When draining through the disinfectant
collection hose is selected
1 Check the disinfectant collection hose for
proper connection.
2 Perform “Drain LCG” again. oRefer to
Section 8.2, “Replacing the disinfectant
solution”.
• When draining through the drain hose is
selected.
1 Check the drain hose for proper installation.
(Height of the drain hose should be less than
60 cm.)
2 Wait until the fluid in the basin drained
completely.
3 Wear appropriate protective gear and clean
the drain port mesh filter in basin. oRefer to
Section 10.3, “Cleaning the mesh filters”.
4 Perform “Drain LCG” again. oRefer to
Section 8.2, “Replacing the disinfectant
solution”.
E073 Water supply irregularity
during the Load LCG
process.
• The water faucet is not
open enough.
• Drain port mesh filter in
basin is clogged.
• Water flow rate is too
low.
• Water is leaking from
the water supply hose.
• The water filter is
clogged.
• The mesh filter in the
water supply hose
connector is clogged.
1 Open the water faucet all the way.
2 Wear appropriate protective gear and clean
the drain port mesh filter in basin.
3 Check if water is leaking from the water
supply hose.
4 Close the lid by pushing until it clicks and
restart “Load LCG” according to the guide on
the touch screen.
E074 LCG in the cassette
bottles is not supplied to
the disinfectant solution
tank.
Internal problem with the
reprocessor.
Contact Olympus.
Error
code Problem Possible causes Remedial actions
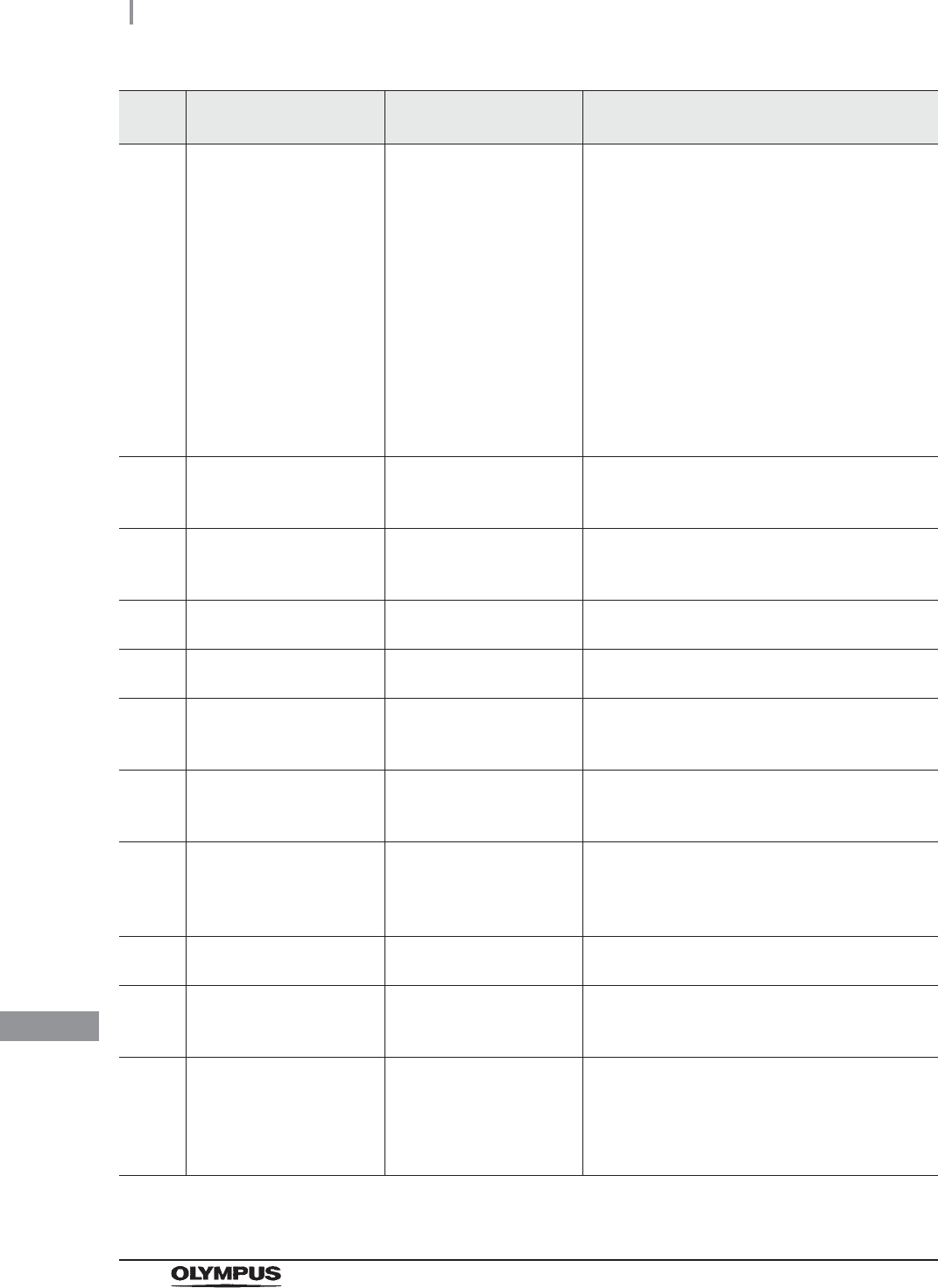
610
13.2 Troubleshooting guide
OER-Elite OPERATION MANUAL
Ch.13
E075 Water supply irregularity
during the Load LCG
process.
• The water faucet is not
open enough.
• Drain port mesh filter in
basin is clogged.
• Water flow rate is too
low.
• Water is leaking from
the water supply hose.
• The water filter is
clogged.
• The mesh filter in the
water supply hose
connector is clogged.
1 Open the water faucet all the way.
2 Wear appropriate protective gear and clean
the drain port mesh filter in basin.
3 Check if water is leaking from the water
supply hose.
4 Close the lid by pushing until it clicks and
restart “Load LCG” according to the guide on
the touch screen.
E076 Irregularity of the fluid
level sensor in the
disinfectant solution tank.
Internal problem with the
reprocessor.
Contact Olympus.
E077 Incomplete positioning of
the disinfectant bottle
drawer.
Disinfectant bottle drawer
is not completely closed.
Ensure that the disinfectant bottle drawer is
completely closed.
E078 Cassette bottles are
empty.
Empty cassette bottles
were installed.
Perform the “Load LCG” with new cassette
bottles.
E081 The process cannot be
properly controlled.
Irregularity in the valve
inside the reprocessor.
Contact Olympus.
E082 Internal irregularity in the
OER-Elite.
Irregularity in the
electrical circuitry inside
the reprocessor.
Contact Olympus.
E083 The process cannot be
properly controlled.
Irregularity in the
electrical circuitry inside
the reprocessor.
Contact Olympus.
E084 Malfunction of the RFID
reader.
Irregularity in the
electrical circuitry inside
reprocessor.
Contact Olympus.
To continue using the OER-Elite, and manually
input the ID information via the touch screen.
RFID will be disabled.
E086 Internal irregularity in the
OER-Elite.
Irregularity in the pump
inside the reprocessor.
Contact Olympus.
E087 Internal irregularity in the
OER-Elite.
Irregularity in the flow
sensor inside the
reprocessor.
Contact Olympus.
E088 Insufficient fluid flow. The circulation port mesh
filter in the basin is
clogged.
1 Wear appropriate protective gear and clean
the circulation port mesh filter in basin.
oRefer to Section 10.3, “Cleaning the mesh
filters”.
2 Perform the process again.
Error
code Problem Possible causes Remedial actions
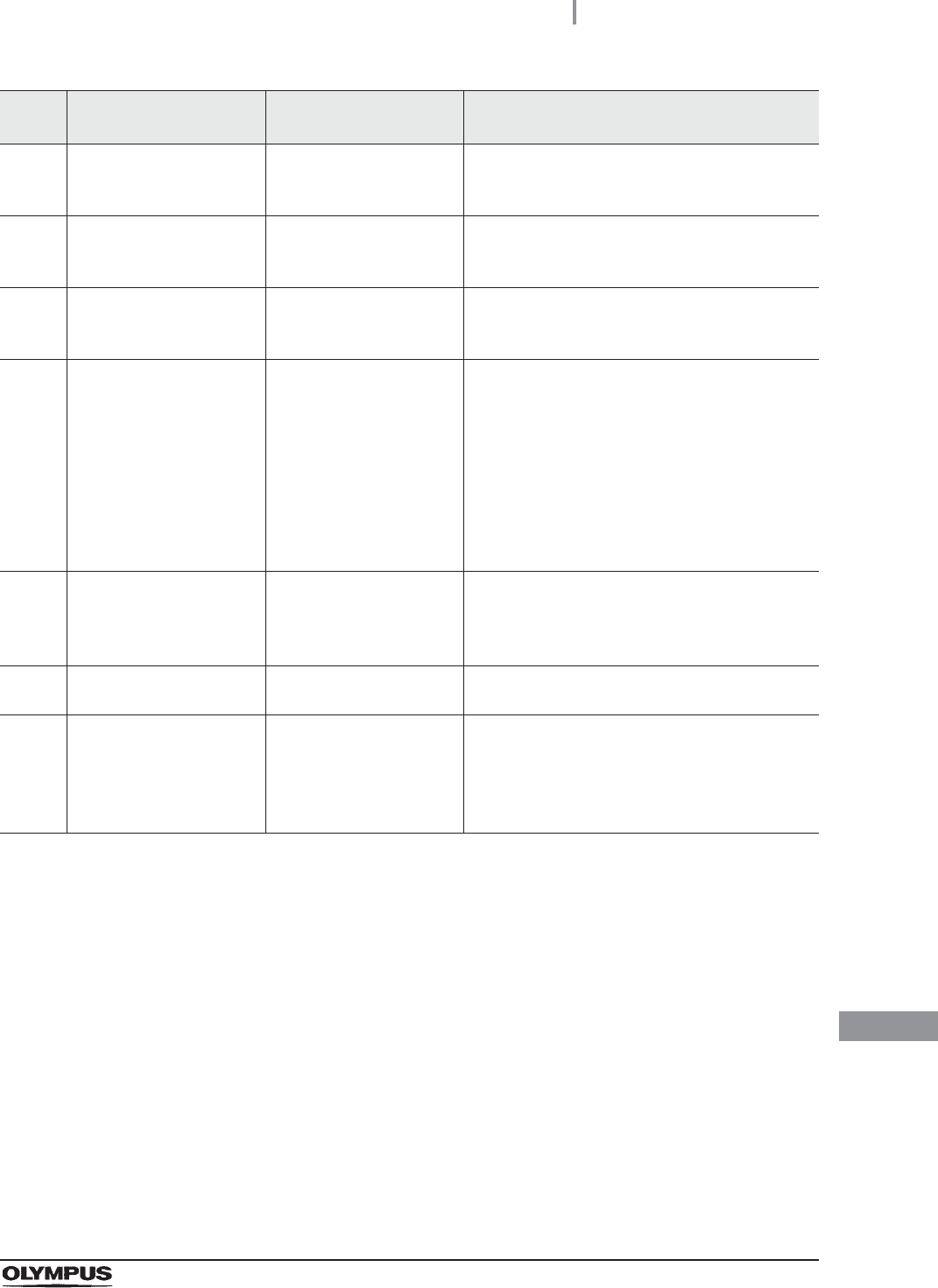
13.2 Troubleshooting guide
611
OER-Elite OPERATION MANUAL
Ch.13
E089 Internal irregularity in the
OER-Elite.
Irregularity in the
electrical circuitry inside
the reprocessor.
Contact Olympus.
E092 Manual leak test time has
been exceeded.
Manual leak test time of
10 minutes has been
exceeded.
Perform manual leak test again.
E093 Alcohol cannot be
supplied during the
process.
Clogging of the alcohol
piping.
Refer to Section 7.14, “Alcohol flush”.
E094 Date cannot be printed. • Printer is not properly
connected to the
OER-Elite.
• Printer paper roll has
run out.
• Malfunction of printer.
1 If the printer paper runs out, replace the
printer paper roll.
2 If the paper cover is open, close the cover.
3 Check the power LED of the printer lights up.
If not, press power button on the operational
panel of the printer to ON.
4 Check the interface cable is connected
properly.
5 Print the data again.
E095 Detergent cannot be
supplied during the
process.
Clogging of the detergent
piping.
• Refer to “If the message screen “Message
093” is displayed again after replacing the
detergent tank and restarting the
reprocessing process:” on page 638.
E111 Internal irregularity in the
OER-Elite.
Internal problem with the
reprocessor.
Contact Olympus.
E112 ALT Self-Check Error Leak test air tube was
connected during the
ALT Self-Check.
1 Confirm the leak test air tube is not
connected.
2 Perform “ALT Self-Check” again.
oRefer to Section 7.13, “Self-check of auto
leak test”.
Error
code Problem Possible causes Remedial actions
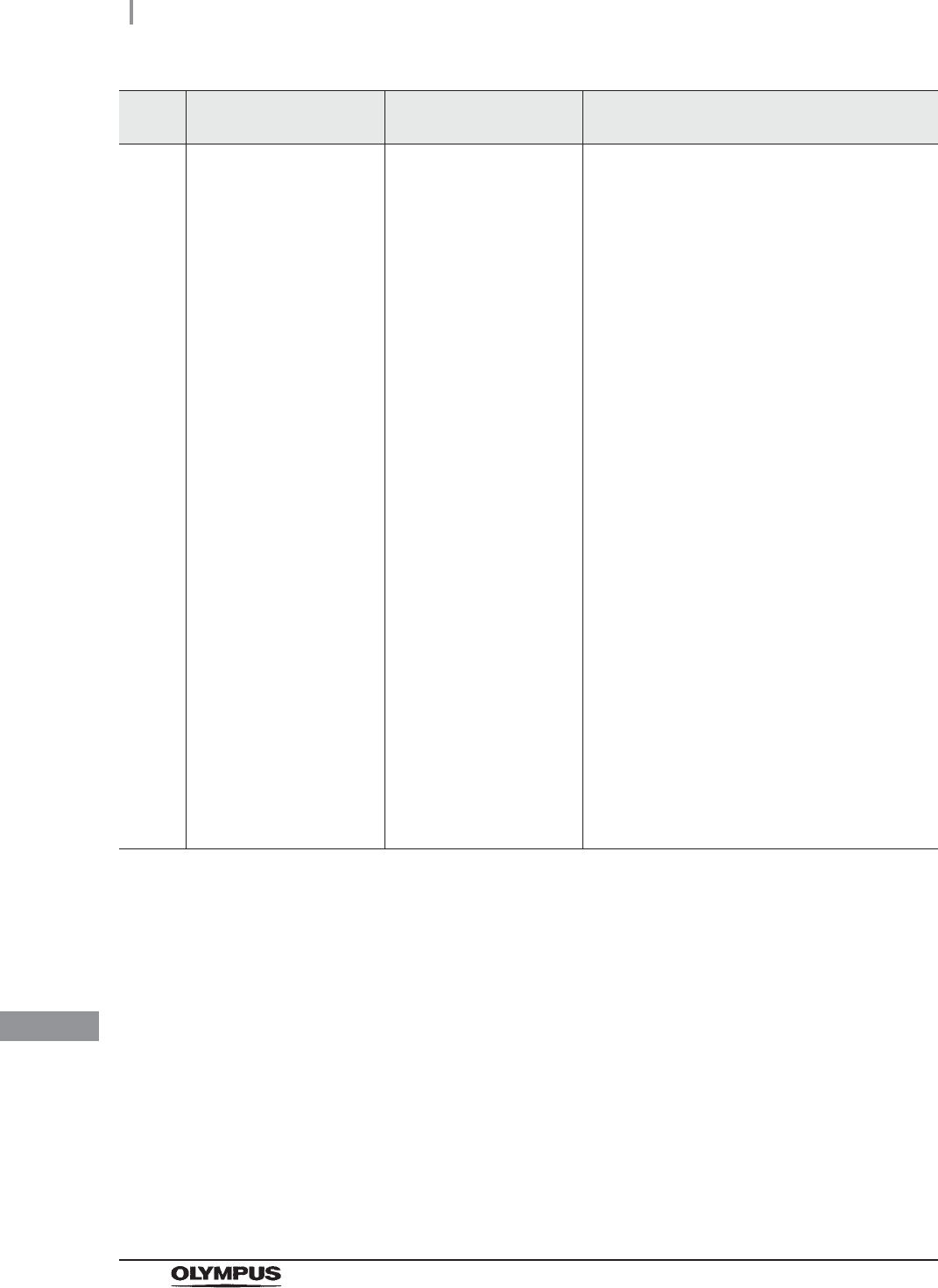
612
13.2 Troubleshooting guide
OER-Elite OPERATION MANUAL
Ch.13
E114 Leak detected during
ALT process.
• There is a leak within
the endoscope.
• Leak test air tube is
broken.
When the ALT is incorporated in the beginning
of the reprocessing process:
1 If warm water was used in manual cleaning,
the auto leak test may be erroneous because
the temperature of endoscope(s) may
change drastically after the manual cleaning.
If the auto leak test is to be performed at the
start of reprocessing, begin the reprocessing
after the endoscope temperature has
returned to the room temperature. Wait more
than 15 minutes after manual cleaning for the
endoscope temperature to return to room
temperature.
2 If warm water was not used in manual
cleaning, perform the following.
Identify the endoscope with leak from the
scope IDs displayed on the touch screen.
Start the process again for the
non-leaking endoscope.
Be sure to perform “Leaking Scope
Decontamination” with the leaking
endoscope before returning for repair.
When the ALT is incorporated in the end of the
reprocessing process:
1 Identify the endoscope with leak from the
scope IDs displayed on the touch screen.
2 Remove the leaking endoscope from the
OER-Elite, then start the process again for
the non-leaking endoscope.
3 Return the leaking endoscope for repair.
Error
code Problem Possible causes Remedial actions

13.2 Troubleshooting guide
613
OER-Elite OPERATION MANUAL
Ch.13
E115 Leak test air pressure is
low.
• Irregularities of leak
test air tube.
• Irregularities of the
O-ring of the leak test
connector.
• Excessive leak exists
within the endoscope.
Perform the manual leak test to check if the
endoscope or the leak test air tube leaks.
If a leak point exists on the leak test air
tube, replace it with new one and retry the
process.
If a leak point exists between the
connector of the leak test air tube and the
leak test connector (E1 or E2), or
between the metallic connector and the
venting connector of the endoscope,
contact Olympus.
If a leak point exists on the outer surface,
stop it with a piece of tape and perform
the leaking scope decontamination. After
it, send the scope for servicing. If a leak
cannot be reduced by taping and this
error occurs, contact Olympus.
If the leak point exists in a position where
taping is impossible, do not execute this
process but contact Olympus.
E117 Excessive leak test air
pressure.
Internal problem with the
reprocessor.
1 Contact Olympus.
2 If you wish to continue reprocessing, disable
the ALT function.
E118 Cannot release the
pressure of endoscope.
Internal problem with the
reprocessor.
Contact Olympus.
E119 Auto leak test system
malfunction.
Irregularity in the
electrical circuitry inside
the reprocessor.
1 Contact Olympus.
2 If you wish to continue reprocessing, disable
the ALT function.
E124 Auto leak test system
malfunction.
Irregularity in the
electrical circuitry inside
the reprocessor.
1 Contact Olympus.
2 If you wish to continue reprocessing, disable
the ALT function.
E131 Portable memory was
disconnected.
Portable memory was
disconnected while the
data was exported.
Re-insert the portable memory and export data
again.
E132 Cannot write to portable
memory.
• Improper connection of
the portable memory.
• Abnormalities of the
portable memory.
Use another portable memory and export data
again.
E134 Portable memory port
malfunction.
Irregularity in the
electrical circuitry inside
the reprocessor.
Contact Olympus.
Error
code Problem Possible causes Remedial actions
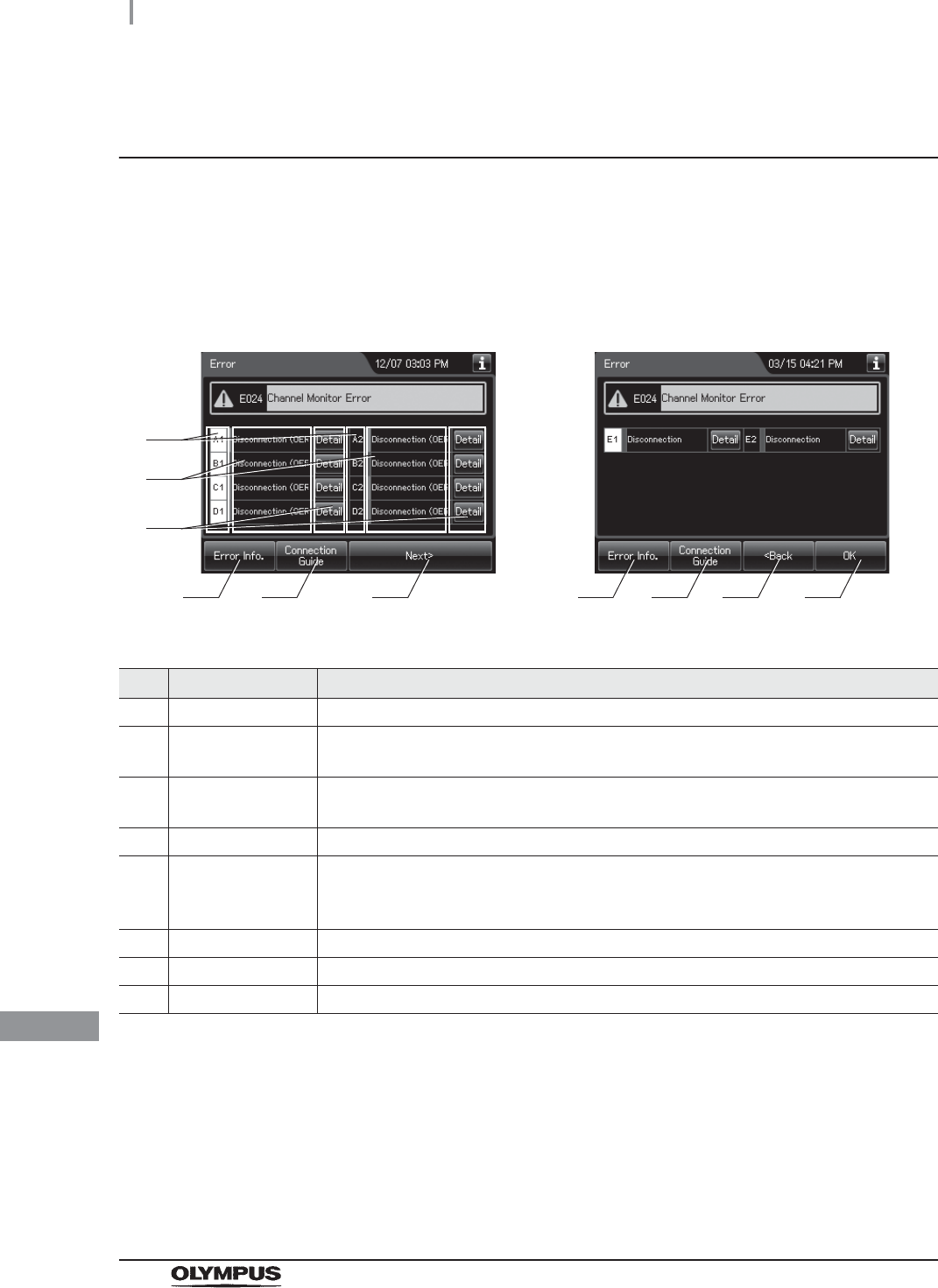
614
13.2 Troubleshooting guide
OER-Elite OPERATION MANUAL
Ch.13
When the error code [E024] is displayed during the
reprocessing process
If an error such as clogging of an endoscope channel or connection irregularity of the connecting tube
or leak test air tubes occurs during the process, the error code [E024] is displayed on the touch screen
and the reprocessor will stop the process. After the auto processing, the touch screen displays the
following screen.
No. Item/Button Description
1 Connector Show Connector in the reprocessing basin.
2 Detection result Displays a detection result if any irregularity is detected to a connector. Blank cell means
that there are not any irregularities with the connector.
3 Detail button Press to display the remedial actions of a connector that detected an irregularity. The
button is unavailable if there are not any irregularities with the connector.
4 Error Info. button Press to display the error information.
5 Connection Guide
button
Press to display the connection guide screen. For detail, refer to “Connection guide of
first endoscope” on page 179, “Connection guide of second endoscope” on
page 206.
6 Next button Press to display the next screen.
7 Back button Press to return to the first page.
8 OK button Press to go to the next page.
4
1st page 2nd page
6
2
3
1
4 7 85 5
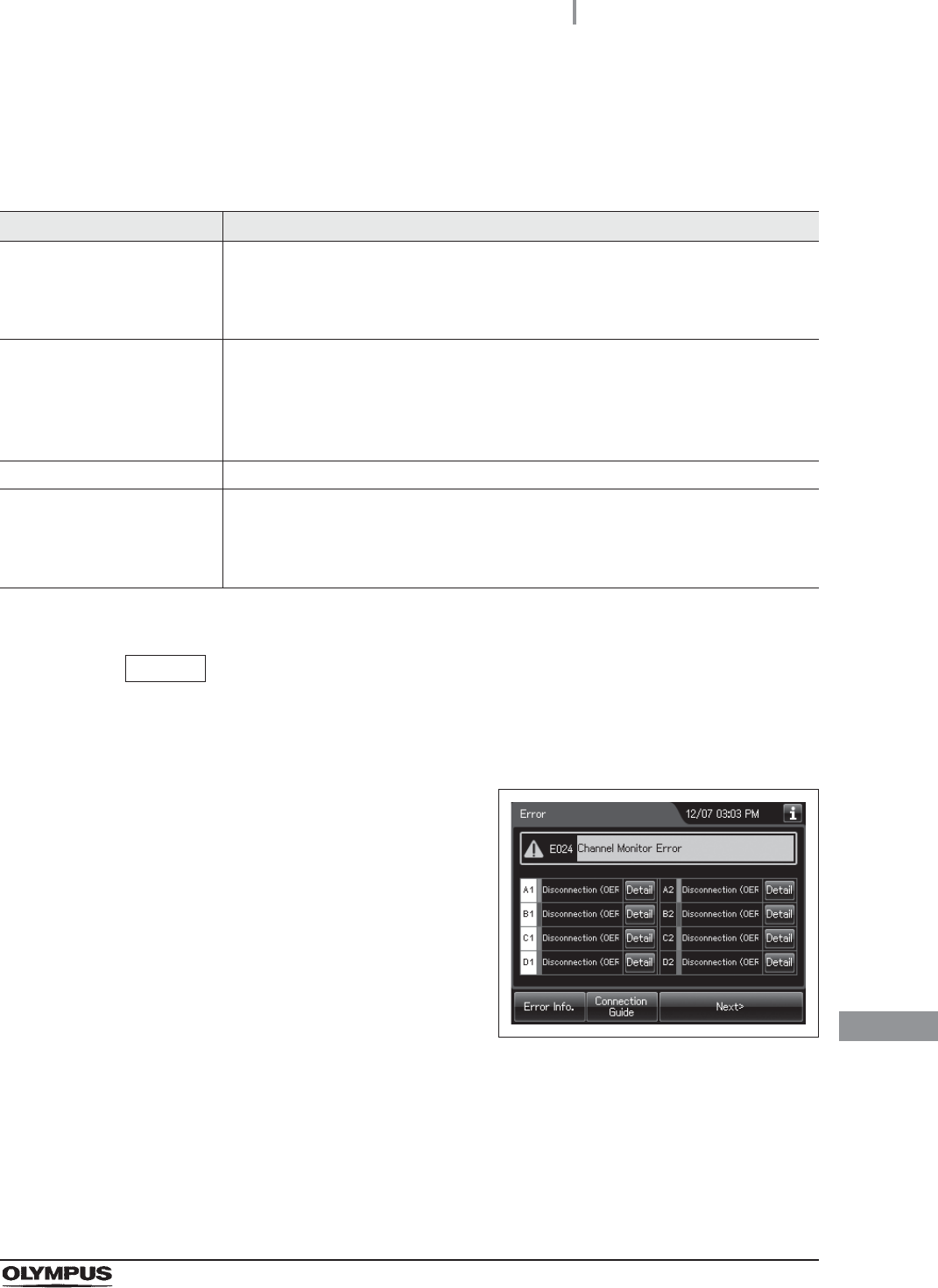
13.2 Troubleshooting guide
615
OER-Elite OPERATION MANUAL
Ch.13
Tab le 1 3. 1
1Step on the foot pedal to open the lid.
2According to the detection result displayed on the touch screen, corrects as follows.
Detection Result Remedial actions
Disconnection
(OER-Elite side)
1 Check the connecting tube is not kinked.
2 Check the connectivity between the connecting tube and OER-Elite.
3 Remove the endoscope and perform manual cleaning. Refer to “Reprocessing
manual” of the endoscope for details.
Blocked Channel 1 Check the correct connecting tube is used.
2 Check the connecting tube is connected to the correct connector in the basin.
3 Check the connecting tube is not kinked.
4 Remove the endoscope and perform manual cleaning. Refer to “Reprocessing
manual” of the endoscope for details.
Wrong connection 1 Disconnect the connecting tube and confirm the correct connecting tube is used.
Disconnection (Scope side) 1 Check the correct connecting tube is used.
2 Check the connecting tube is connected to the correct connector in the basin.
3 Check the connectivity between the connecting tube and the endoscope.
4 Check the connectivity between the leak test air tube and the OER-Elite.
NOTE
If the Detail button is pressed, the remedial actions can be displayed on the touch
screen.
3Press the “Next” button on the first page to
display the second page.
Figure 13.3
4According to the detection result displayed on the touch screen, corrects as Step 2.
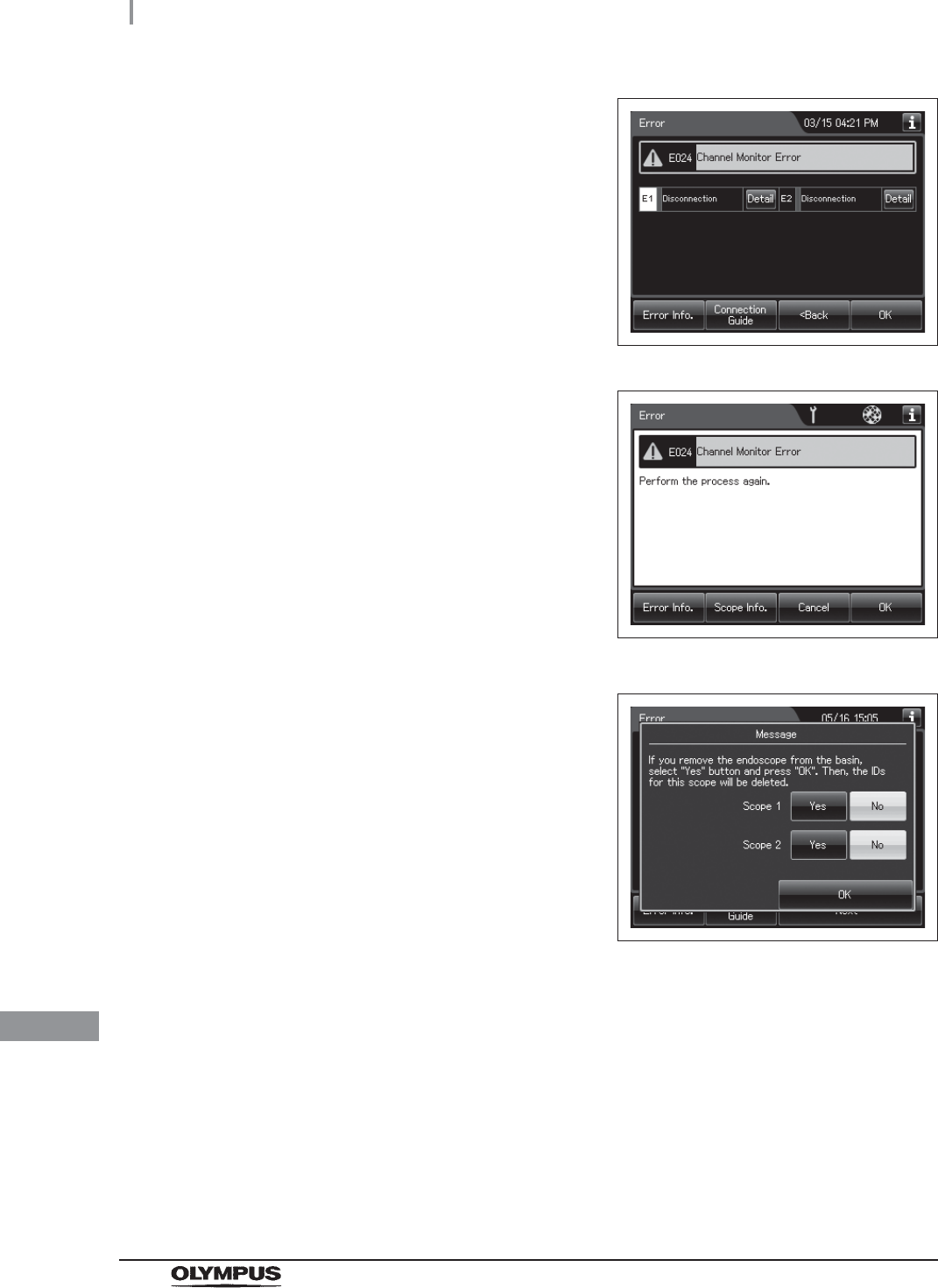
616
13.2 Troubleshooting guide
OER-Elite OPERATION MANUAL
Ch.13
5Press the “OK” button on the second page.
Figure 13.4
6Press the “OK” button to finish remedial
actions. If the endoscope will be removed from
the reprocessing basin, select “Yes” button and
press “OK”. Then, the IDs for this scope will be
deleted.
Figure 13.5
Figure 13.6
7Start the reprocessing process and rinse from the beginning.
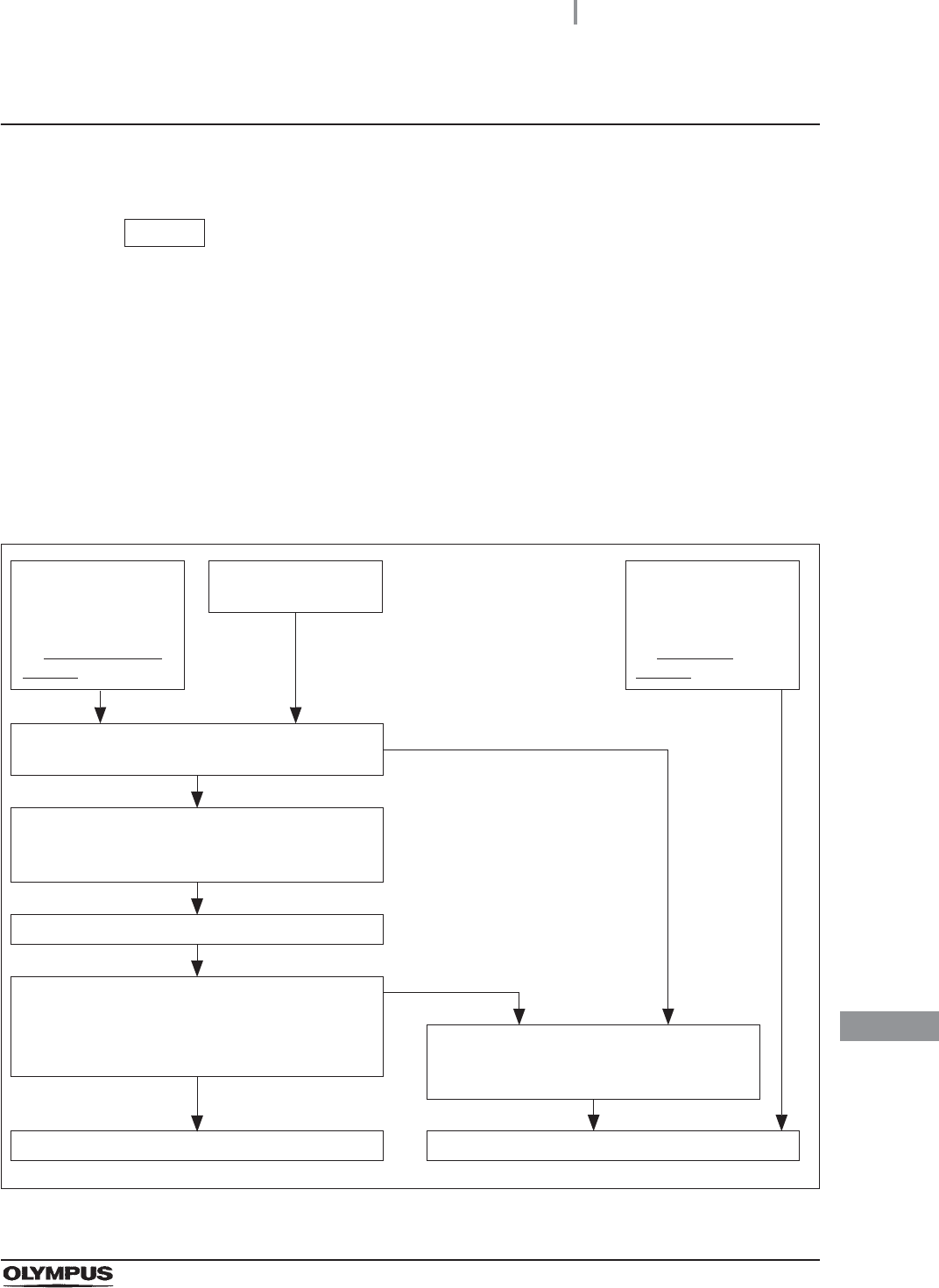
13.2 Troubleshooting guide
617
OER-Elite OPERATION MANUAL
Ch.13
When any leaks are detected
When the error code [E114] or [E115] is displayed on the touch screen, the result of auto leak test is
“Leaked”, or any leaks are detected during manual leak test, perform following.
NOTE
• When the error code [E114] is displayed, leak detected during ALT process at the
reprocessing process.
• When the error code [E115] is displayed, leak test air pressure is low.
• When these errors frequently occur, perform self-check of auto leak test. For detail,
refer to Section 7.13, “Self-check of auto leak test”.
Workflow when the error code [E114] is displayed, or the result
of auto leak test is “Leaked”
Figure 13.7
The error code [E114]
is displayed during
reprocessing process.
(The auto leak setting
is “Beginning of the
process”).
The result of auto
leak test is “Leaked”.
The error code [E114]
is displayed during
reprocessing process.
(The auto leak setting
is “End of the
process”).
Did each process perform immediately after
completing manual cleaning using warm water?
Wait for more than 15 minutes (In the case of the
ultrasonic endoscope, wait for more than
30 minutes) after completing manual cleaning.
Yes
Retry reprocessing process or auto leak test.
Is the following occurred again?
• The error code [E114] is displayed during
reprocessing process.
• The result of auto leak test is “Leaked”.
No
The endoscope has no leaks.
Perform the leaking scope decontamination.
Refer to Section 7.15, “Leaking scope
decontamination”.
Contact Olympus to repair the endoscope.
No
Yes
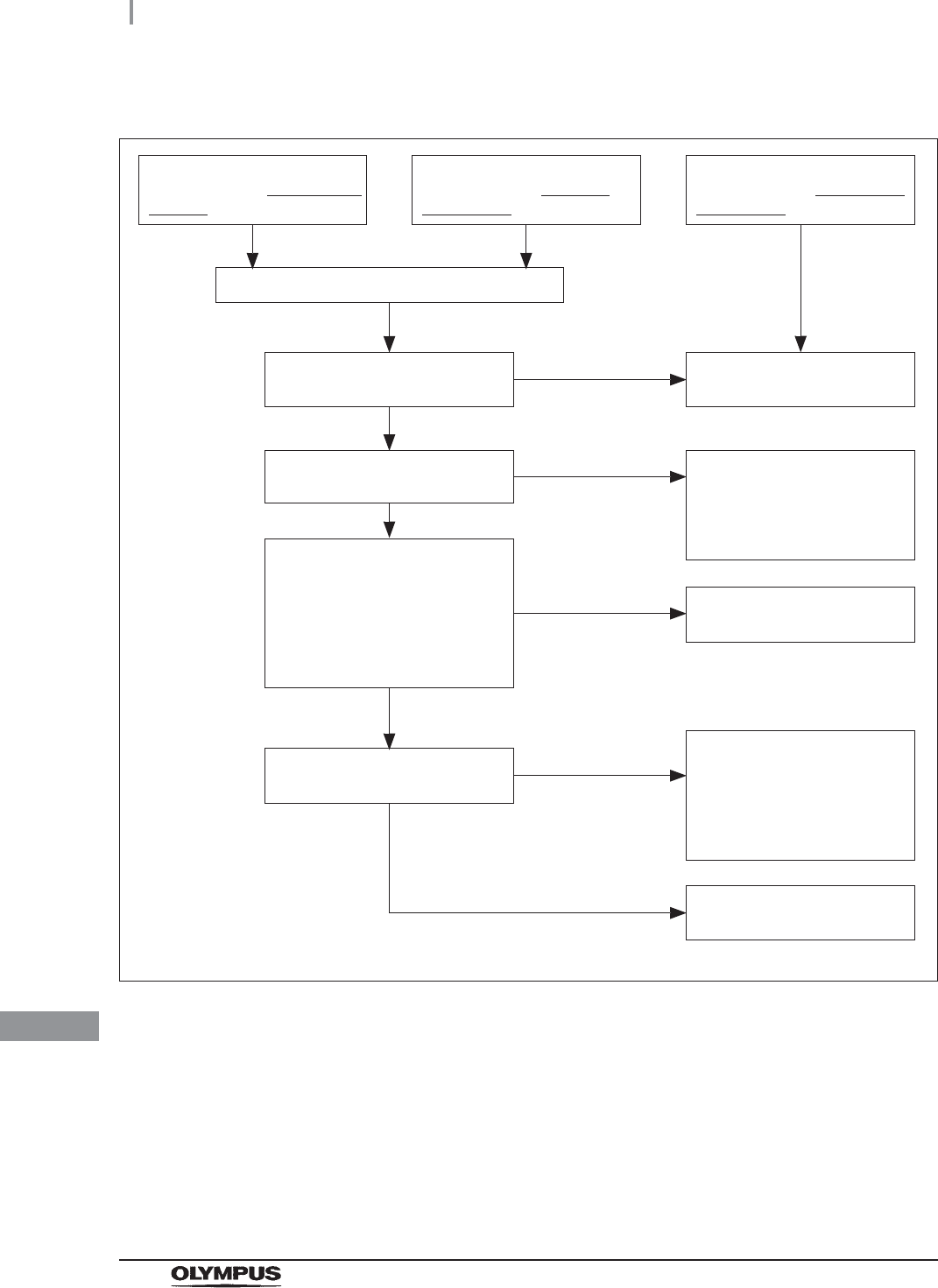
618
13.2 Troubleshooting guide
OER-Elite OPERATION MANUAL
Ch.13
Workflow when the error code [E115] is displayed
Figure 13.8
The error code [E115] is
displayed during reprocessing
process.
Perform the manual leak test.
The error code [E115] is
displayed during auto leak
test function.
The error code [E115] is
displayed during manual leak
test function.
Contact Olympus to repair the
reprocessor.
• Replace the leak test air
tube with a new one.
• If there are no more leak test
tube, contact Olympus.
Contact Olympus to replace a
new O-ring.
Refer to “Workflow when
any leaks are detected during
manual leak test” on
page 619. Then contact
Olympus to repair the
endoscope.
Contact Olympus to repair the
reprocessor.
Is the error code [E115]
displayed again?
Is there leak on the tube section
of the leak test air tube?
Is there leak between the
connector of the leak test air
tube and the leak test connector
(E1 or E2), or between the
metallic connector and the
venting connector of the
endoscope?
Is there leak from the
endoscope?
YES
YES
YES
YES
NO
NO
NO
NO
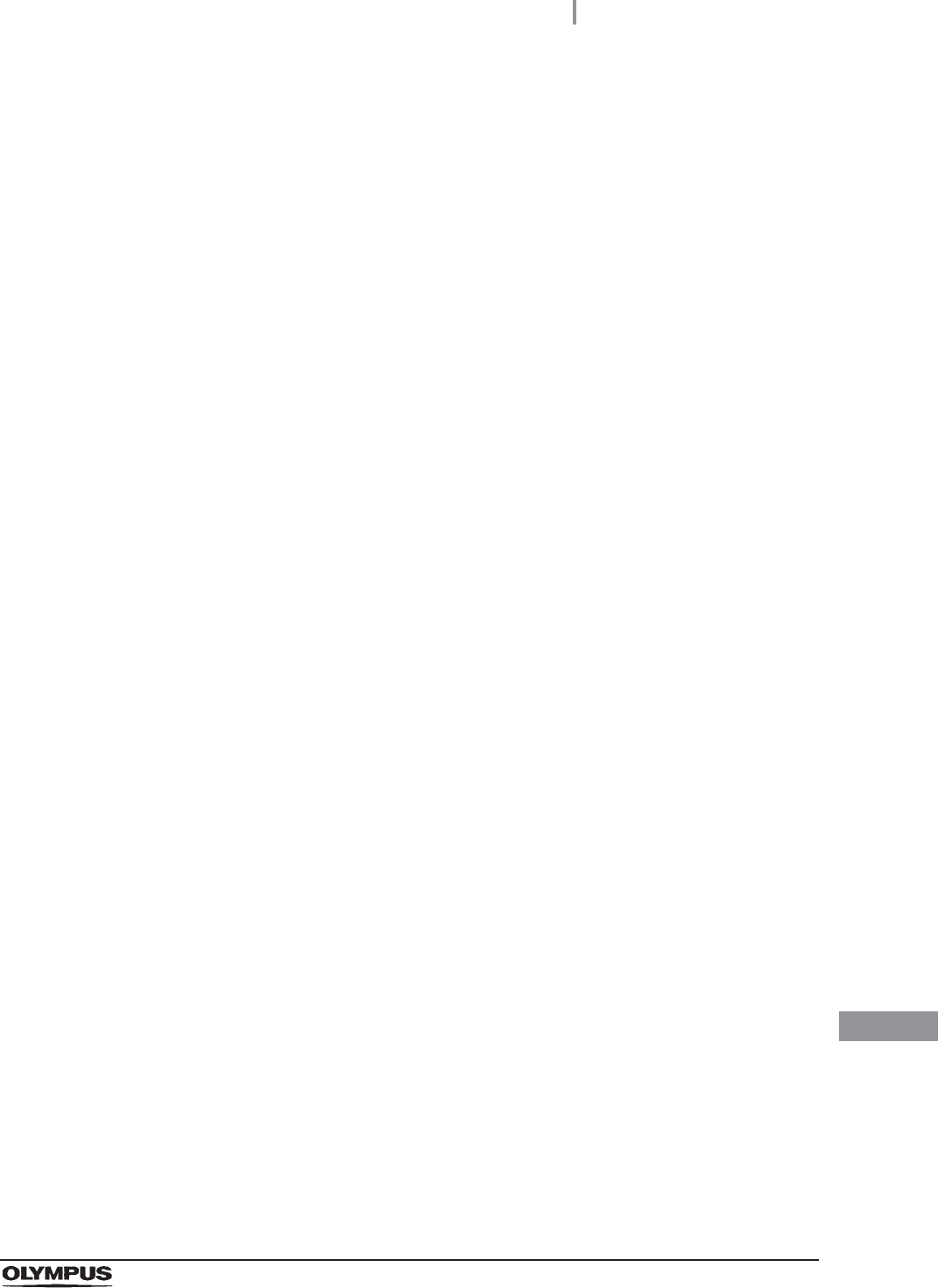
13.2 Troubleshooting guide
619
OER-Elite OPERATION MANUAL
Ch.13
Workflow when any leaks are detected during manual leak test
Manual decontamination for leaking endoscope
(a) Manual cleaning for leaking endoscope
1Perform the leaking scope decontamination. For the detail, refer to Section 7.15,
“Leaking scope decontamination”.
2If the leaking scope decontamination is completed without errors, contact Olympus to
repair the endoscope.
If any errors occur, perform manual decontamination for leaking endoscope below.
Then, contact Olympus to repair the endoscope.
1For a leak detected in the covering of the insertion tube, bending section, or universal
cord, dry the leaking area thoroughly and wipe with alcohol. Tape over the location of
the leak with a piece of electrical tape or other waterproof tape prior to immersing in
detergent solution. Wrap the tape tightly. For leaks detected in other locations (e.g.,
internal channel), proceed with the instructions provided below.
2Fill a basin with detergent solution at the temperature and concentration
recommended by the detergent manufacturer. Use a basin that is at least 40 cm by
40 cm (16” by 16”) in size and deep enough to allow the endoscope to be completely
immersed.
3Insert the leakage tester connector into the output socket of the maintenance unit
such as MU-1 or the light source and turn the maintenance unit or the light source
ON. Set the light source’s airflow regulator switch to “HIGH” or “3”.
4Connect the leakage tester’s connector cap to the venting connector of the
water-resistant cap.
5Immerse the endoscope in the detergent solution.
6Perform manual cleaning according to the instructions provided in the reprocessing
manual. Minimize unnecessary flexion of the insertion tube and universal cord during
cleaning.
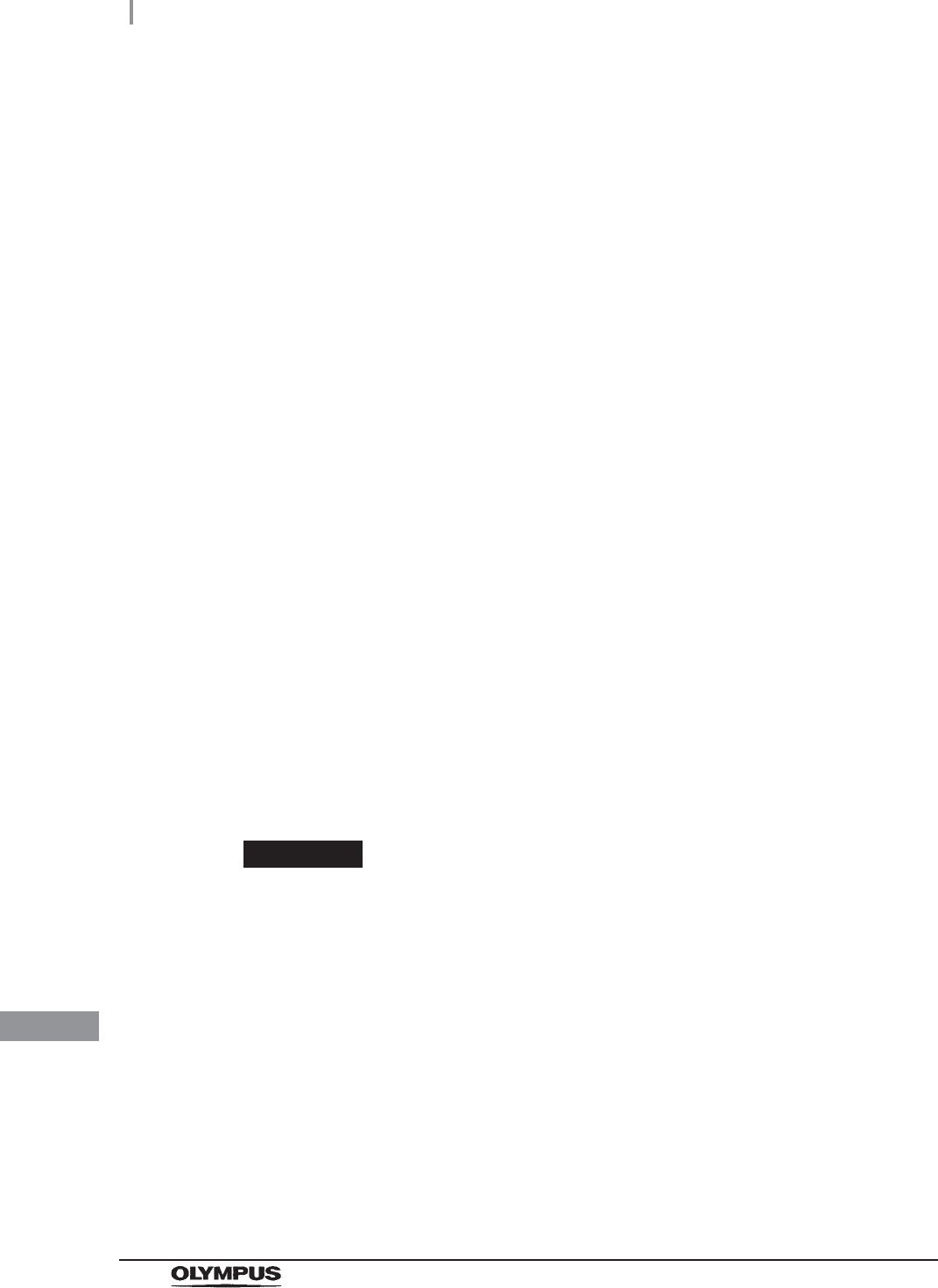
620
13.2 Troubleshooting guide
OER-Elite OPERATION MANUAL
Ch.13
(b) Sterilization for leaking endoscope
(c) High-level disinfection for leaking endoscope
WARNING
This process is intended to treat the endoscope with water leak before sending it
for servicing. It does not guarantee the reprocessing of the endoscope and its
accessories after this process. After completing this process, do not use the
endoscope and its accessories in examination but send it for servicing.
Following manual cleaning, the preferred method of rendering a leaking endoscope
safe to handle is ethylene oxide sterilization. Ethylene oxide sterilization should be
performed according to the instruction provided in the reprocessing manual. If
electrical tape was applied to a leak detected in the endoscope’s external surface,
remove the tape and wipe with 70% ethyl or isopropyl alcohol prior to ethylene oxide
sterilization. If ethylene oxide sterilization is not possible, perform high-level
disinfection according to the instructions provided below.
1Fill a basin with disinfectant solution at the temperature and concentration
recommended by the disinfectant manufacturer. Use a basin that is at least 40 cm by
40 cm (16” by 16”) in size and deep enough to allow the endoscope to be completely
immersed.
2Insert the leakage tester connector into the output socket of the maintenance unit or
the light source and turn the maintenance unit or the light source ON. Set the light
source’s airflow regulator switch to “HIGH” or “3”.
3Connect the leakage tester’s connector cap to the venting connector of the
water-resistant cap.
4Immerse the endoscope in the disinfectant solution.
5Perform high-level disinfection according to the instructions provided in the
reprocessing manual. Minimize unnecessary flexion of the insertion tube and
universal cord during reprocessing.
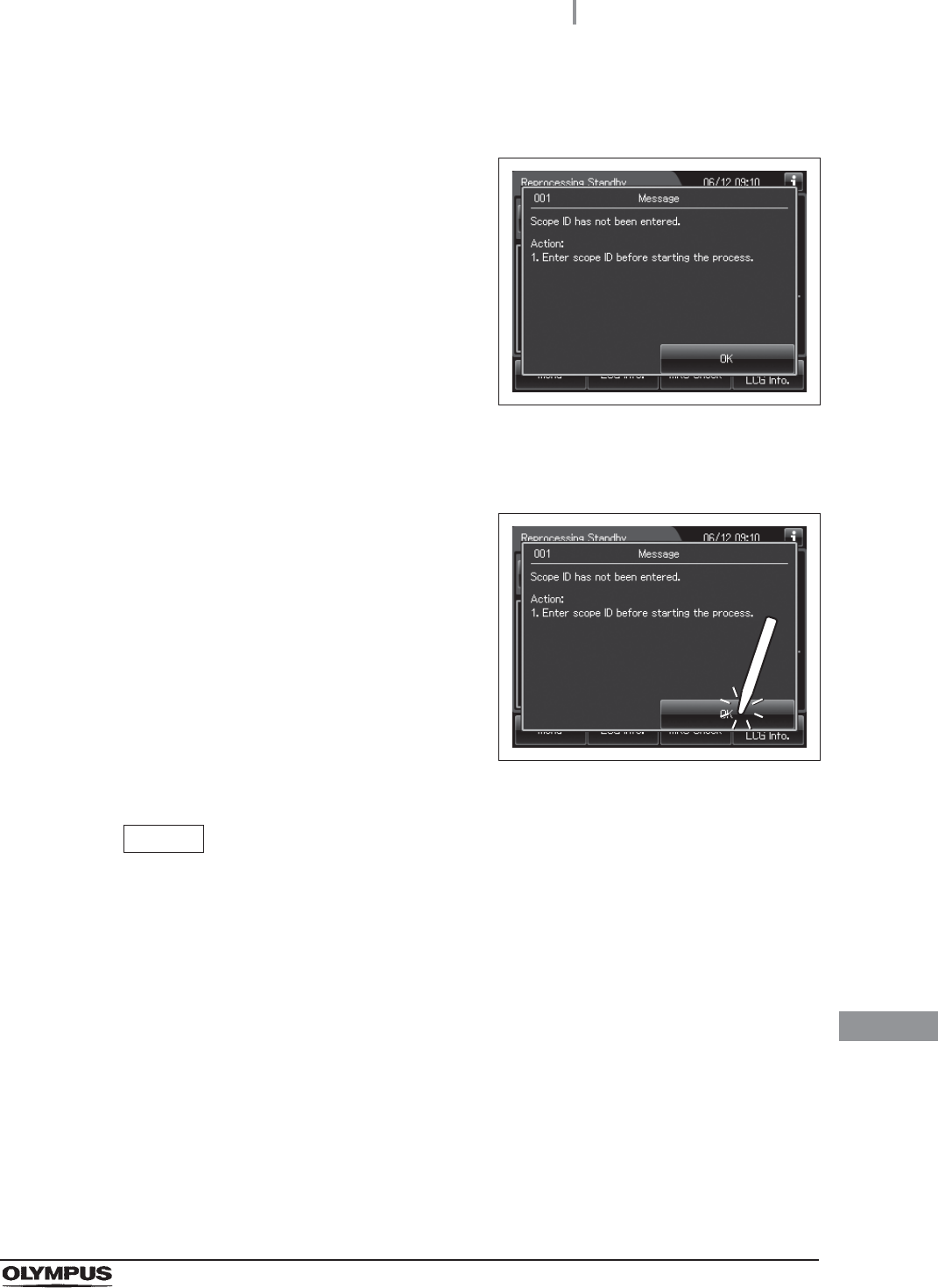
13.2 Troubleshooting guide
621
OER-Elite OPERATION MANUAL
Ch.13
Message, caution, and warning screens
NOTE
• The button for resuming a process varies based on message screens displayed on
the touch screen.
• The message cannot record to logs.
1If the reprocessor requires operator action, the
buzzer beeps and the message screen will be
displayed on the touch screen.
Figure 13.9
2Perform remedial actions according to the instruction described in the table below or
the instructions displayed on the touch screen.
3Press the “OK” button to resume a process.
Figure 13.10
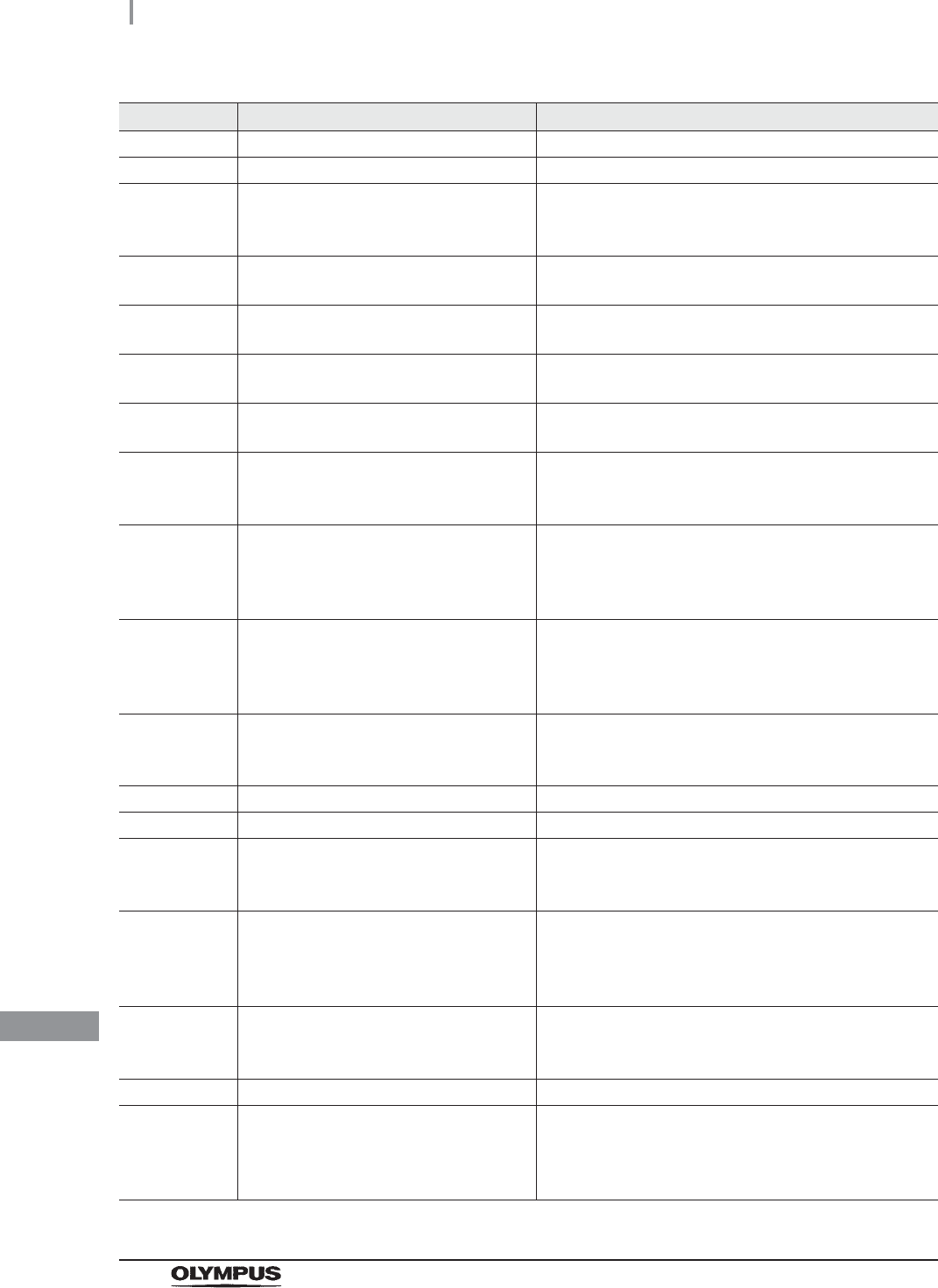
622
13.2 Troubleshooting guide
OER-Elite OPERATION MANUAL
Ch.13
No. Message Remedial actions
Message 001 Scope ID has not been entered. Enter scope ID before starting the process.
Message 002 User ID has been entered. Enter user ID before starting the process.
Message 003 OER-Elite cannot accept more than two
user IDs per reprocessing cycle.
1 Verify the entered user ID information is correct.
2 Delete the incorrect user information. Re-enter user
ID.
Message 004 ID entry for 1st endoscope has not
been completed.
Before entering the 2nd endoscope ID, enter the
remaining IDs for the 1st endoscope.
Message 005 User ID Setting has not been activated. To enter user ID, go to Menu screen, then change the
User ID Setting.
Message 005 Patient ID Setting has not been
activated.
To enter patient ID, go to Menu screen, then change
the Patient ID Setting.
Message 005 Physician ID Setting has not been
activated.
To enter physician ID, go to Menu screen, then change
the Physician ID Setting.
Message 006 OER-Elite cannot accept more than two
Scope IDs per reprocessing cycle.
1 Verify the entered scope ID information is correct.
2 Delete the incorrect scope information. Re-enter
scope ID.
Message 008 Scope ID master has been entered.
Channel Monitoring, auto leak testing
and Connection Guide will be disabled.
Refer to the “List of compatible
Endoscopes/Connecting Tubes <OER-Elite>” to
confirm the correct connecting tubes for this
endoscope.
Message 009 Scope ID has been entered from the
touch screen. Channel monitoring, auto
leak testing and connection guide will
be disabled.
Refer to the “List of compatible
Endoscopes/Connecting Tubes <OER-Elite>” to
confirm the correct connecting tubes for this
endoscope.
Message
010, 011
This endoscope is incompatible for auto
leak testing. Auto leak testing will be
disabled.
No additional action is required.
Message 014 Patient ID has not been entered. Enter patient ID before starting the process.
Message 015 Physician ID has not been entered. Enter physician ID before starting the process.
Message 016 OER-Elite cannot accept more than two
patient IDs per reprocessing cycle.
1 Verify the entered patient ID information is correct.
2 Delete the incorrect patient information. Re-enter
patient ID.
Message 017 OER-Elite cannot accept more than two
physician IDs per reprocessing cycle.
1 Verify the entered physician ID information is
correct.
2 Delete the incorrect physician information. Re-enter
physician ID.
Message 018 Malfunction of the RFID reader. 1 Manually input the ID information via the touch
screen.
2 Contact Olympus.
Message 019 Procedure ID has not been entered. Enter procedure ID before starting the process.
Message 020 This endoscope is incompatible for
channel connectivity
monitoring.Channel connectivity
monitoring will be disabled.
No additional action is required.
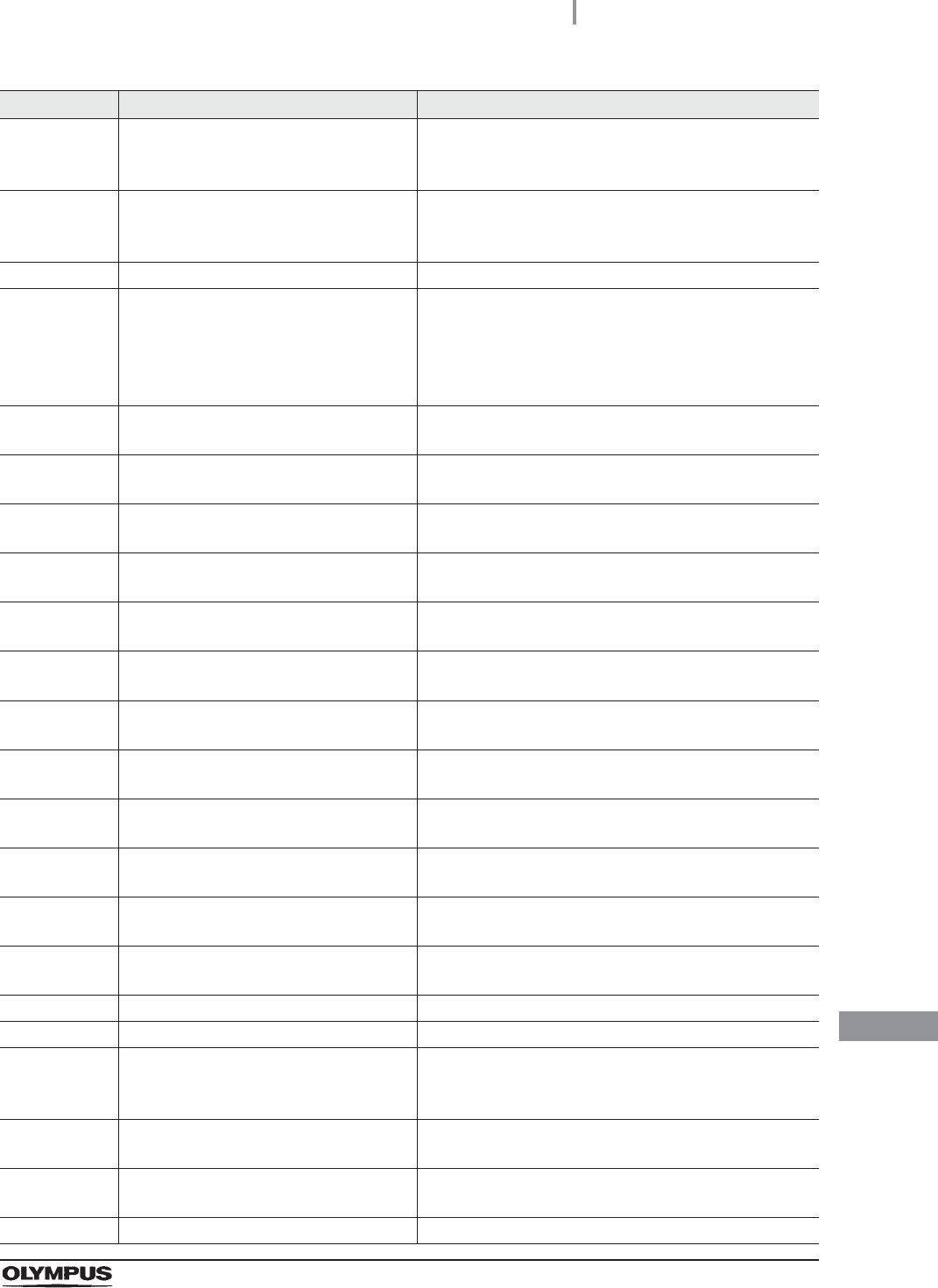
13.2 Troubleshooting guide
623
OER-Elite OPERATION MANUAL
Ch.13
Message 021 This endoscope is incompatible for
channel blockage monitoring.Channel
blockage monitoring will be disabled.
No additional action is required.
Message 022 This endoscope is incompatible for
channel monitoring. Channel
monitoring will be disabled.
No additional action is required.
Message 023 Refer to the Message 008 Refer to the Message 008.
Message 024 Scope ID of endoscope that cannot be
reprocessed simultaneously has been
entered. OER-Elite cannot accept more
than one User ID per reprocessing
cycle.
1 Verify the entered user ID information is correct.
2 Delete the incorrect user information. Re-enter user
ID.
Message 025 This endoscope combination is
incompatible for auto leak testing.
Perform “Auto Leak Test” separately for second scope.
Message 031 LCG cycle count/usage exceeds the set
value.
Perform MRC check before performing the process.
Message 032 There is no LCG in the disinfectant
solution tank.
Perform “Load LCG”.
Message 034 Load LCG cannot be performed with
LCG in the disinfectant solution tank.
Perform “Drain LCG”, then “Load LCG”.
Message 035 Drain LCG cannot be performed with no
LCG in the disinfectant solution tank.
No additional action is required.
Message 036 An invalid set time for Heat LCG Timer
has been entered.
1 Enter a minimum time of at least 2.5 hours.
2 Enter a date of less than 5 days.
Message 037 The LCG temperature is already above
the specified temperature.
No additional action is required.
Message 038 Cannot activate the Heat LCG Timer.
System clock battery low.
Contact Olympus.
Message 047 More than 1 hour has passed since the
MRC check result has been entered.
Perform MRC check again and enter the result.
Message 048 MRC check result has not been
entered.
Perform MRC check again and enter the result.
Message 050 There is no LCG in the disinfectant
solution tank.
Perform “Load LCG” before MRC check.
Message 061 Portable memory is full, cannot Export
data.
Insert portable memory that has sufficient capacity. At
least 100MB capacity is necessary.
Message 062 No record exists for the selected period. Confirm the dates for the period selected.
Message 070 The lid is open. Close the lid to perform the process.
Message 071 Cannot drain LCG through the
disinfectant collection hose with the lid
closed.
1 Verify the collection method selected is correct.
2 Follow the prompts on the OER-Elite.
Message 080 Time for periodic maintenance. The time for regularly scheduled maintenance is near.
Contact Olympus to perform the maintenance.
Message 081 Water filter usage exceeds the set
value.
Perform “Replace Water Filter”.
Message 081 Air filter usage exceeds the set value. Perform “Replace Air Filter”.
No. Message Remedial actions
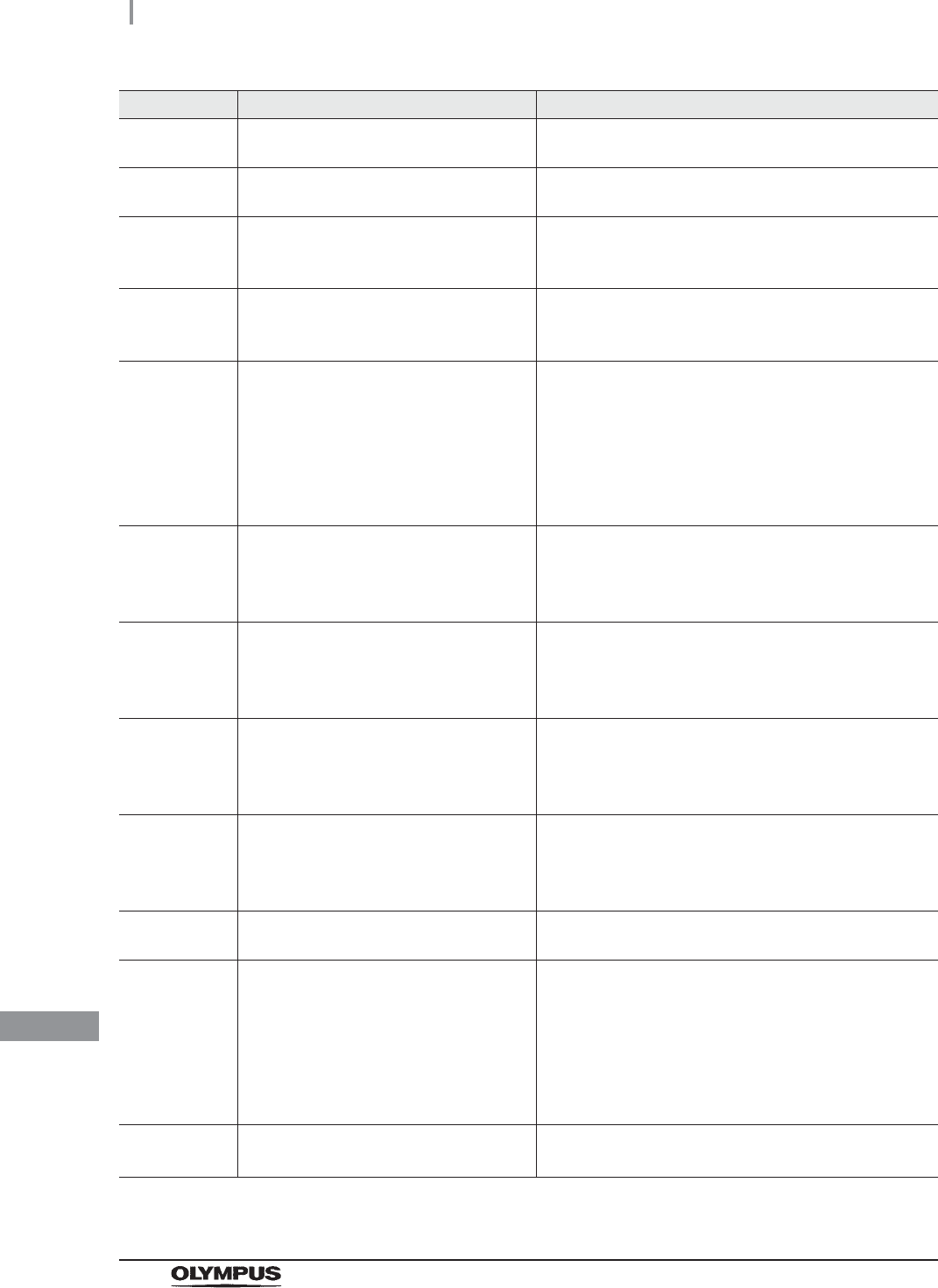
624
13.2 Troubleshooting guide
OER-Elite OPERATION MANUAL
Ch.13
Message 081 Gas filter usage exceeds the set value. Perform “Replace Gas Filter on the Lid” or perform
“Replace Gas Filter on the Tank”.
Message 082 The OER-Elite has not been used for
more than 14 days.
Perform “Self-Disinfection” and “Water Line
Disinfection”.
Message 083 ALT Self-check failed. Contact Olympus. To continue reprocessing, choose a
program with the ALT Setting disabled. (Program 3 or
4)
Message 086 “Leak” has been selected as a manual
leak test result.
1 Close the lid by pushing until it clicks. The water will
automatically be discharged from the basin.
2 Perform “Leaking Scope Decontamination”.
Message 087 Alcohol cannot be supplied. 1 Confirm the amount of alcohol in the alcohol tank. If
no alcohol is remaining, replenish the alcohol.
2 Confirm the alcohol tubing is not bent and press
“Restart”.
3 To cancel the process, press “Stop”.
Refer to Section 5.9, “Inspecting and replenishing
alcohol”.
Message 088 Fluid cannot be drained from the
alcohol line.
1 Confirm the nozzle of the cap is out of the beaker.
2 Confirm the alcohol tubing is not bent and press
“Restart”.
3 To cancel the process, press “Stop”.
Message 088 Fluid cannot be drained from the
detergent line.
1 Confirm the nozzle of the cap is out of the beaker.
2 Confirm the detergent tubing is not bent and press
“Restart”.
3 To cancel the process, press “Stop”.
Message 089 Fluid cannot be supplied from the
alcohol line.
1 Confirm the nozzle of the cap is in the beaker.
2 Confirm the alcohol tubing is not bent and press
“Restart”.
3 To cancel the process, press “Stop”.
Message 089 Fluid cannot be supplied from the
detergent line.
1 Confirm the nozzle of the cap is in the beaker.
2 Confirm the detergent tubing is not bent and press
“Restart”.
3 To cancel the process, press “Stop”.
Message 091 To enable the mode setting, turn the
power off and boot with service mode.
No additional action is required.
Message 093 Detergent cannot be supplied. 1 Confirm the amount of detergent in the detergent
tank. If no detergent is remaining, replace a new
detergent tank.
2 Confirm the detergent tube is not bent and press
“Restart”.
3 To cancel the process, press “Stop”.
Refer to Section 8.3, “Replacing the detergent tank”.
Message 095 An invalid time has been entered. Set the time within following range.
Range: 1/1/2012 00:00 – 12/31/2087 23:59
No. Message Remedial actions
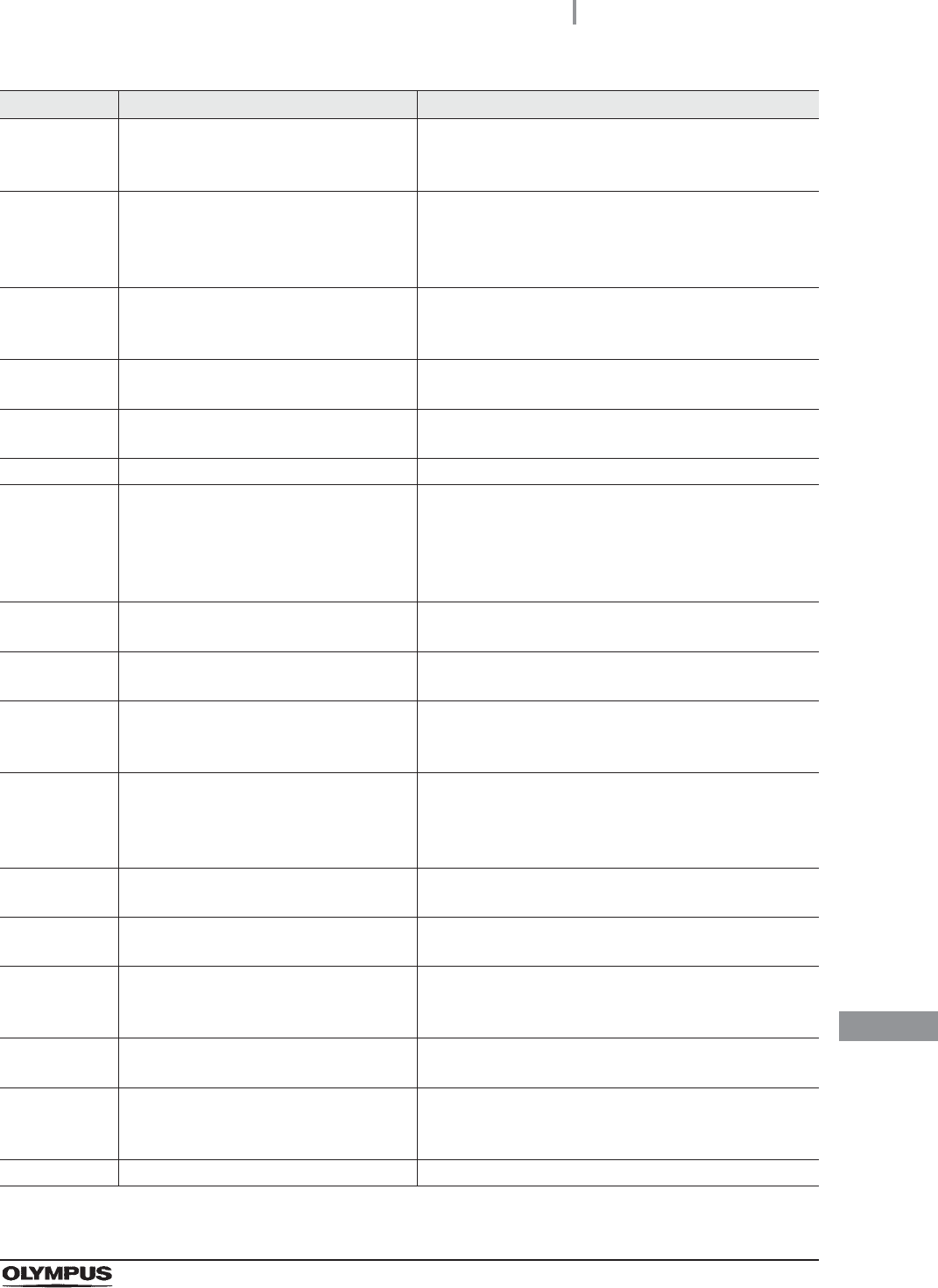
13.2 Troubleshooting guide
625
OER-Elite OPERATION MANUAL
Ch.13
Message 100 Leak test air tube for scope 1 has not
been connected within 5 minutes.
1 Enter scope ID for scope 1 again.
2 Within 5 minutes, connect the leak test air tube for
scope 1 to the E1 connector.
Message 101 Leak test air tube has been connected
to the endoscope before entering scope
ID.
1 Disconnect the leak test air tube from the connector.
2 Enter scope ID for scope 1 again.
3 Connect the leak test air tube for scope 1 to the E1
connector.
Message 102 Program has been changed and
OER-Elite cannot detect the proper
connection of leak test air tube.
1 Disconnect the leak test air tube from the connector.
2 Press “OK”.
Message 110 Process interrupted before rinse.
Chemical may remain in the basin.
1 Press “Rinse” to continue now.
2 Press “OK” to perform “Rinse” later.
Message 120 Detergent cycle count/usage exceeds
the set value.
Perform “Replace Detergent”.
Message 132 An invalid date has been entered. Set the expiration date properly.
Warning 026 This endoscope requires special
procedures for reprocessing in the
OER-Elite.
Before reprocessing the endoscope in the OER-Elite,
thoroughly review and follow the procedures described
in the respective endoscope reprocessing manual or
the OER-Elite Instructions – Operation Manual.
Otherwise, reprocessing may be insufficient.
Warning 096 “ALT Self-Check” has not been
performed.
1 Press “ALT Self-Check” to continue now.
2 Press “OK” to perform ALT Self-Check later.
Warning 121 Detergent has expired based on its
shelf life expiration date.
Perform “Replace Detergent”.
Caution 007 Incompatible combination of
endoscope.
Refer to the “List of compatible
Endoscopes/Connecting Tubes <OER-Elite>” to
confirm the applicable combination of endoscopes.
Caution 013 This endoscope is incompatible with
OER-Elite.
1 Reprocess this endoscope using another method.
2 For a list of compatible endoscopes, refer to the
“List of compatible Endoscopes/Connecting Tubes
<OER-Elite>”.
Caution 033 LCG has expired based on its shelf life
expiration date.
Perform “Drain LCG”, then “Load LCG”.
Caution 039 Load LCG has not been completed
properly.
Perform “Drain LCG”, then “Load LCG”.
Caution 040 “Fail” has been entered as an MRC
check result, cannot perform the
process.
Perform “Drain LCG”, then “Load LCG”.
Caution 041 “Mix LCG” has not been performed. 1 Press “Mix LCG” to continue now.
2 Press “OK” to perform Mix LCG later.
Caution 046 More than 4 hours has passed since
the last cycle. To ensure accurate MRC
testing, perform “Mix LCG”.
1 Press “Mix LCG” to continue now.
2 Press “OK” to perform Mix LCG later.
Caution 084 System clock battery has run out. Contact Olympus.
No. Message Remedial actions
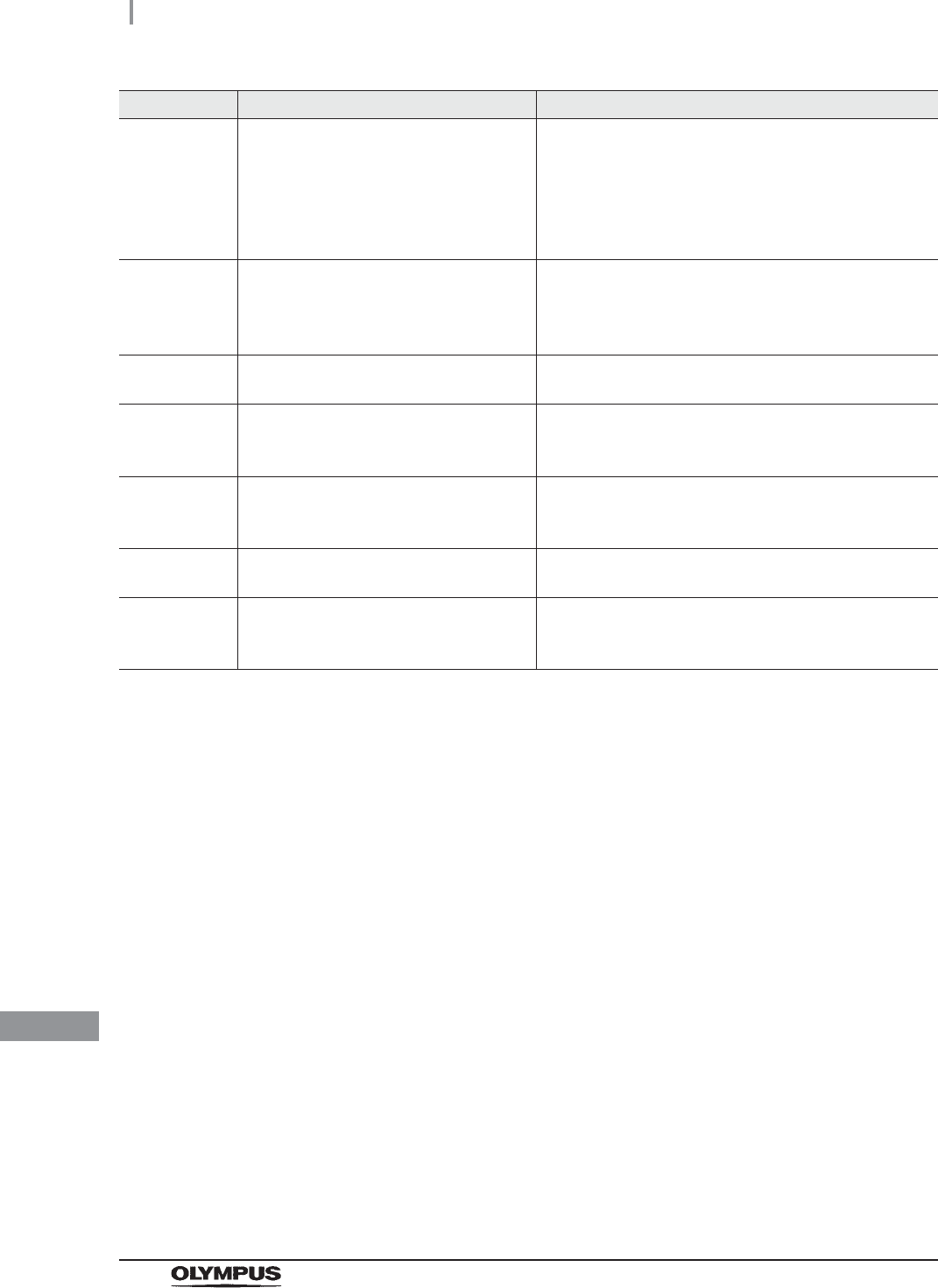
626
13.2 Troubleshooting guide
OER-Elite OPERATION MANUAL
Ch.13
Caution 085 System clock battery low. 1 Contact Olympus.
2 To continue using the OER-Elite, make sure the
system clock indicates the actual current date and
time. If not, perform “Date and Time setting” and set
the current date and time. The system clock will
function until OER-Elite is powered off.
Caution 092 “No” has been selected as the result of
manual cleaning and leak test for scope
1.
1 Perform leak test and manual cleaning before
starting reprocessing.
2 If a leak has been detected, perform “Leaking
Scope Decontamination”.
Caution 092 “No” has been selected as the result of
manual cleaning for scope 1.
Perform manual cleaning before starting reprocessing.
Caution 092 “No” has been selected as the result of
leak test for scope 1.
1 Perform leak test before starting reprocessing.
2 If a leak has been detected, perform “Leaking
Scope Decontamination”.
Caution 092 “Pass” has been selected as the result
of leak test. “No” has been selected as
the result of manual cleaning.
Perform manual cleaning before starting reprocessing.
(Do not use leaking scope decontamination for this
endoscope)
Caution 092 “Pass” has been selected as the result
of leak test.
Perform reprocessing. (Do not use leaking scope
decontamination for this endoscope.)
Caution 094 Water Line Disinfection has not been
completed after replacing the water
filter.
Perform “Water Line Disinfection”.
No. Message Remedial actions
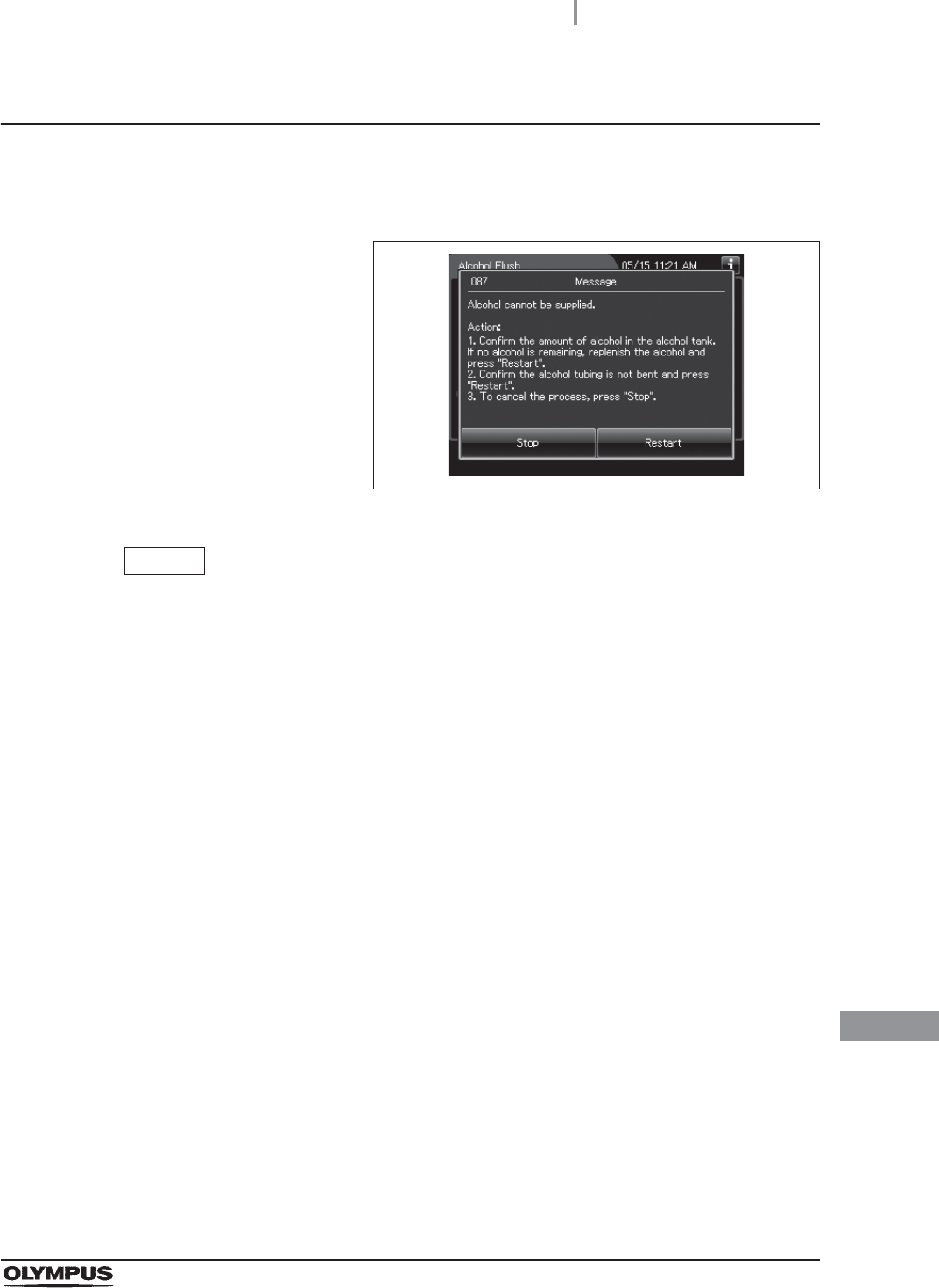
13.2 Troubleshooting guide
627
OER-Elite OPERATION MANUAL
Ch.13
When the message screen “Message 087” is displayed
If alcohol has run out and the message screen “Message 087” is displayed, the reprocessor will stop
the process. In this case, you can restart the process from the “alcohol flush” by implementing the
following procedure.
Figure 13.11
NOTE
• The reprocessing process can be restarted from the “alcohol flush” if the “Restart”
button is pressed in Message 087. In that case, the reprocessing record is
recorded as normal.
• The lid will remain locked until the message screen is cleared, and you cannot
access the reprocessing basin even after pressing the foot pedal. If you want to
interrupt the reprocessing process, press STOP button and follow the procedure
described in Section 13.1, “Emergency stop and automatic processing after
stopping”.
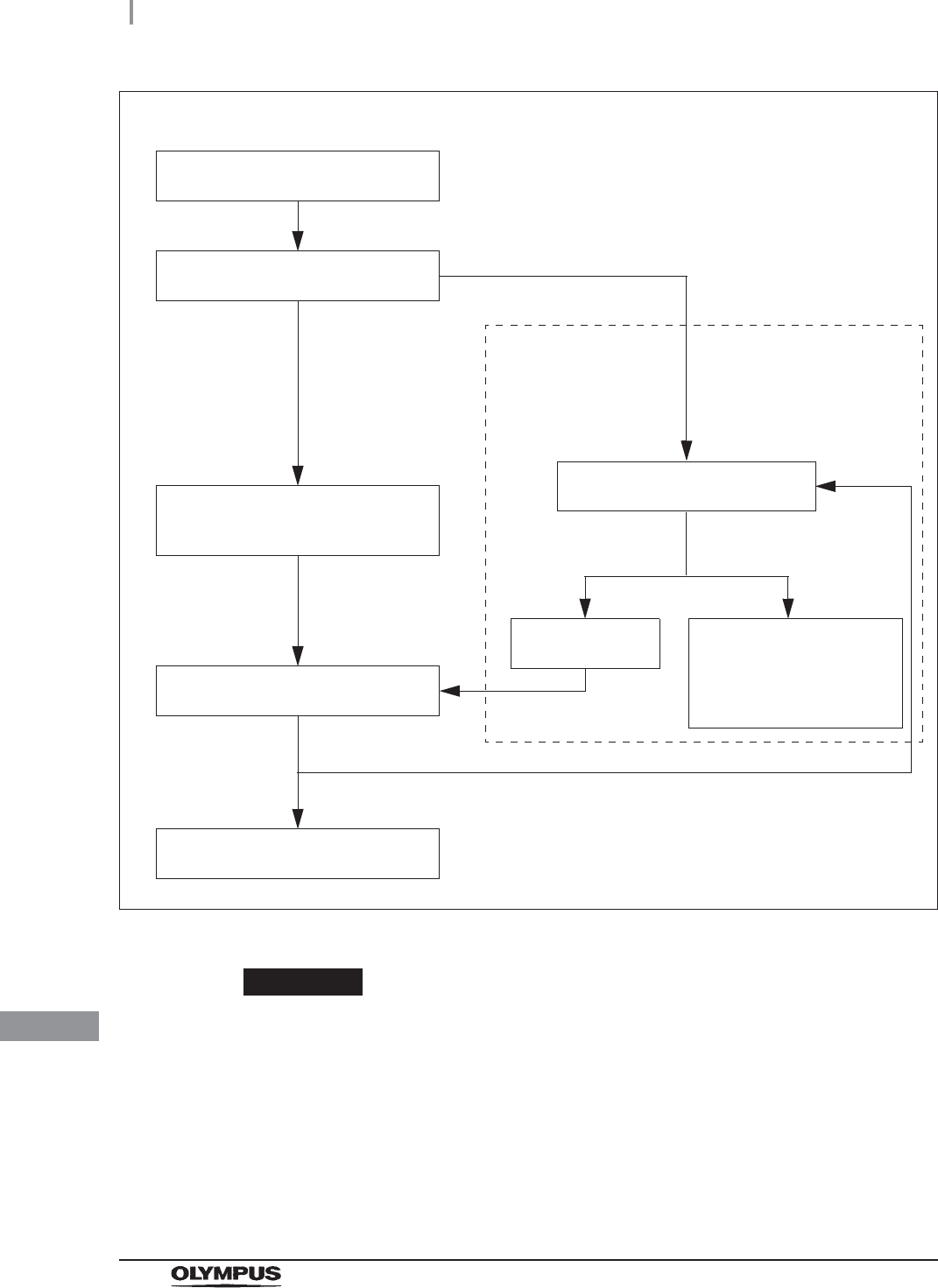
628
13.2 Troubleshooting guide
OER-Elite OPERATION MANUAL
Ch.13
Figure 13.12
WARNING
• The alcohol used with the reprocessor must be 70% ethyl alcohol or 70% isopropyl
alcohol. Using any other kind of alcohol may result in malfunction of the
reprocessor or the endoscope, difficulty drying the endoscope, fire hazard, or a
hazard due to toxic vapor emitted from the alcohol.
• Alcohol is flammable and should be handled with extra care.
• Remove the alcohol in the alcohol tank and replace it with new alcohol at least once
a week. Otherwise, the alcohol in the alcohol tank may degrade.
• Before handling the alcohol, read the cautions carefully and use it as instructed.
When the Message 087 is displayed during the alcohol flush process
Message 087 “Alcohol cannot be
supplied” is displayed.
Confirm whether alcohol still
present in the alcohol tank.
1.
Replenish alcohol.
(Refer to Section 5.9, “Inspecting
and replenishing alcohol”.)
2.
Press the “Restart” button to restart
the reprocessing cycle.
3.
Reprocessing process restarts
from alcohol flush process.
4.
If no alcohol remain
in the tank.
If alcohol still present
in the tank.
Refer to “If the “Message
087” is displayed again after
replenishing alcohol and
restarting the alcohol flush
process:” on page 629.
Inspect the tube and connector
connected to the alcohol tank.
Correct
irregularities.
Press the “Stop” button to
cancel the reprocessing
process and perform
remedial actions of E093 to
resolve the problem.
If any irregularity
is found.
If no irregularity is
found.
If the message screen is displayed again.
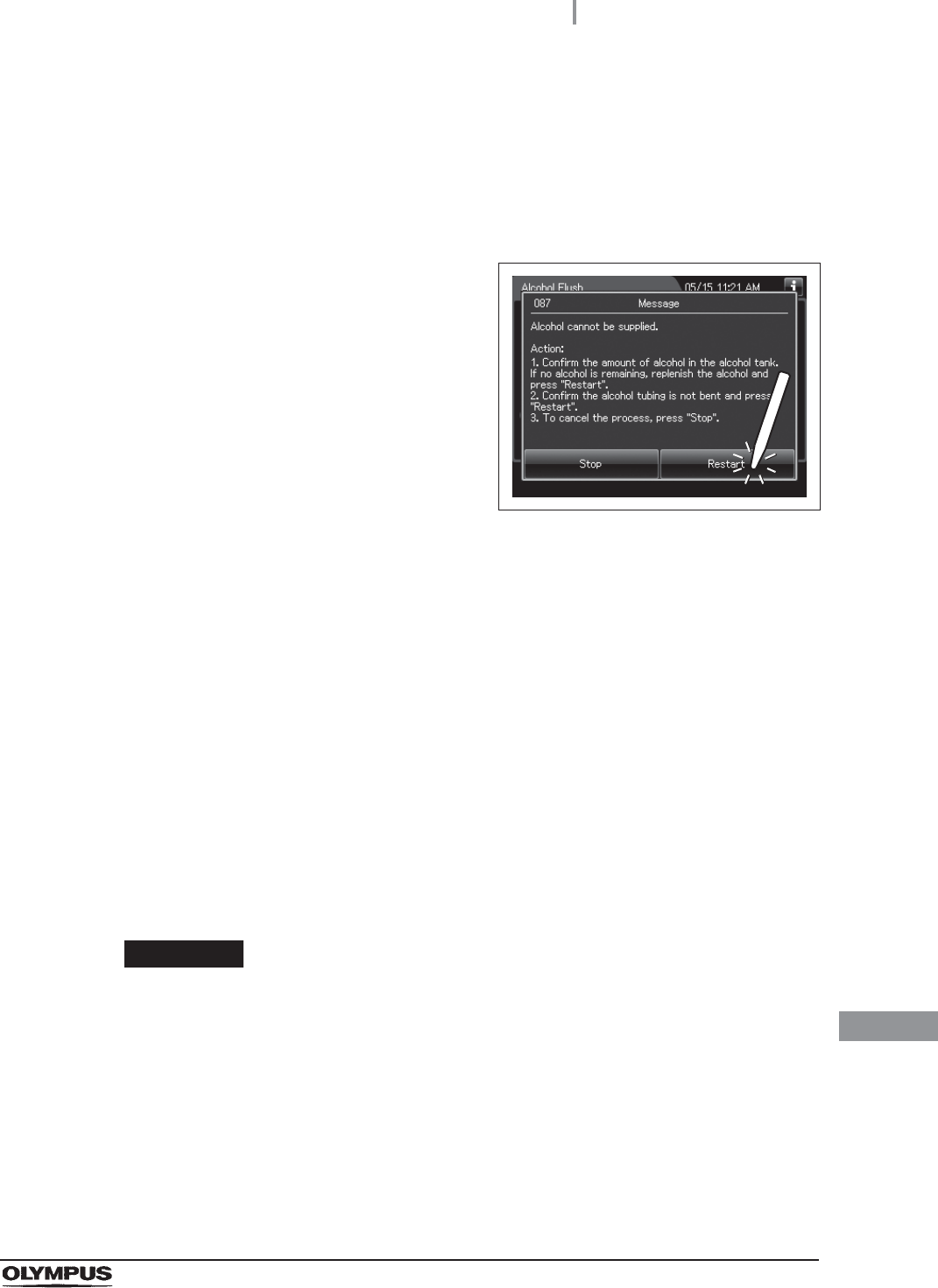
13.2 Troubleshooting guide
629
OER-Elite OPERATION MANUAL
Ch.13
If the “Message 087” is displayed again after replenishing
alcohol and restarting the alcohol flush process:
When message screen “Alcohol cannot be supplied” is displayed again after restarting the
reprocessing process, check that there is no irregularity regarding the following points.
• The tube connected to the alcohol tank is not kinked.
• The connector of alcohol tank is attached firmly.
If any irregularity is found by inspection, correct these points and press the “Restart” button on
the touch screen to restart the alcohol flush process.
If no irregularity is found during an inspection or the message screen is displayed again, internal
problem with the reprocessor may be suspected. In this case, follow the procedure below.
WARNING
• The alcohol used with the reprocessor must be 70% ethyl alcohol or 70% isopropyl
alcohol. Using any other kind of alcohol may result in malfunction of the
reprocessor or the endoscope, difficulty drying the endoscope, fire hazard, or a
hazard due to toxic vapor emitted from the alcohol.
• Alcohol is flammable and should be handled with extra care.
• Remove the alcohol in the alcohol tank and replace it with new alcohol at least once
a week. Otherwise, the alcohol in the alcohol tank may degrade.
• Before handling the alcohol, read the cautions carefully and use it as instructed.
1Inspect the alcohol tank. If alcohol is still present in the alcohol tank, go to the
procedure of “If the “Message 087” is displayed again after replenishing alcohol
and restarting the alcohol flush process:” on page 629 described in this section.
2Replenish alcohol into the alcohol tank as described in Section 5.9, “Inspecting and
replenishing alcohol”.
3Press Restart button on the touch screen to
restart the reprocessing process.
Figure 13.13
4Reprocessing process restarts from alcohol flush process.
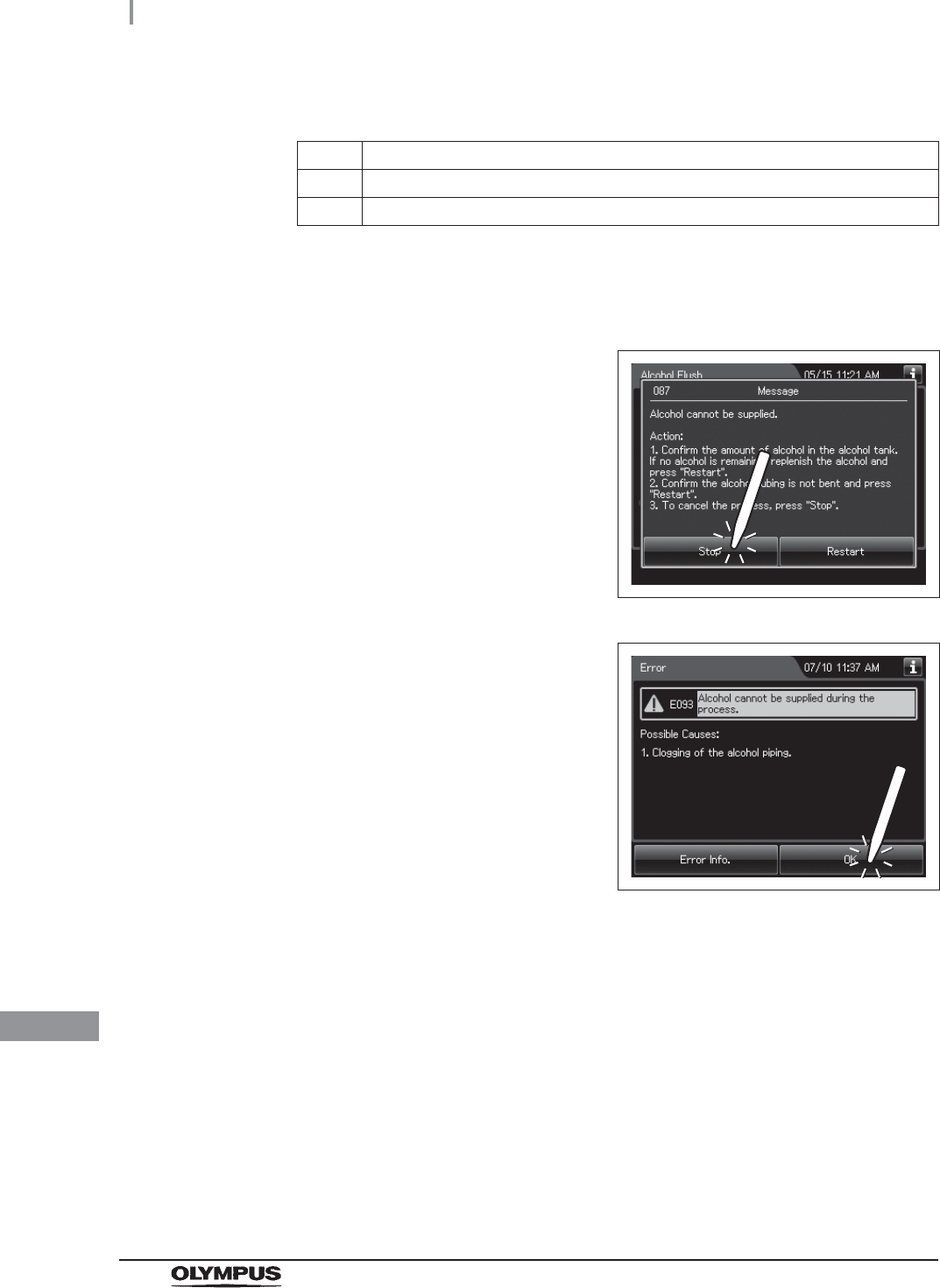
630
13.2 Troubleshooting guide
OER-Elite OPERATION MANUAL
Ch.13
(a) Required items
Table 13.2
(b) Remedial actions
Check Required items
Syringe
Tube
1Press the “Stop” button on the touch screen to
cancel the reprocessing process.
Figure 13.14
2The touch screen displays the error code
[E093]. Press the “OK” button. Then,
troubleshooting guide is displayed on the touch
screen.
Figure 13.15
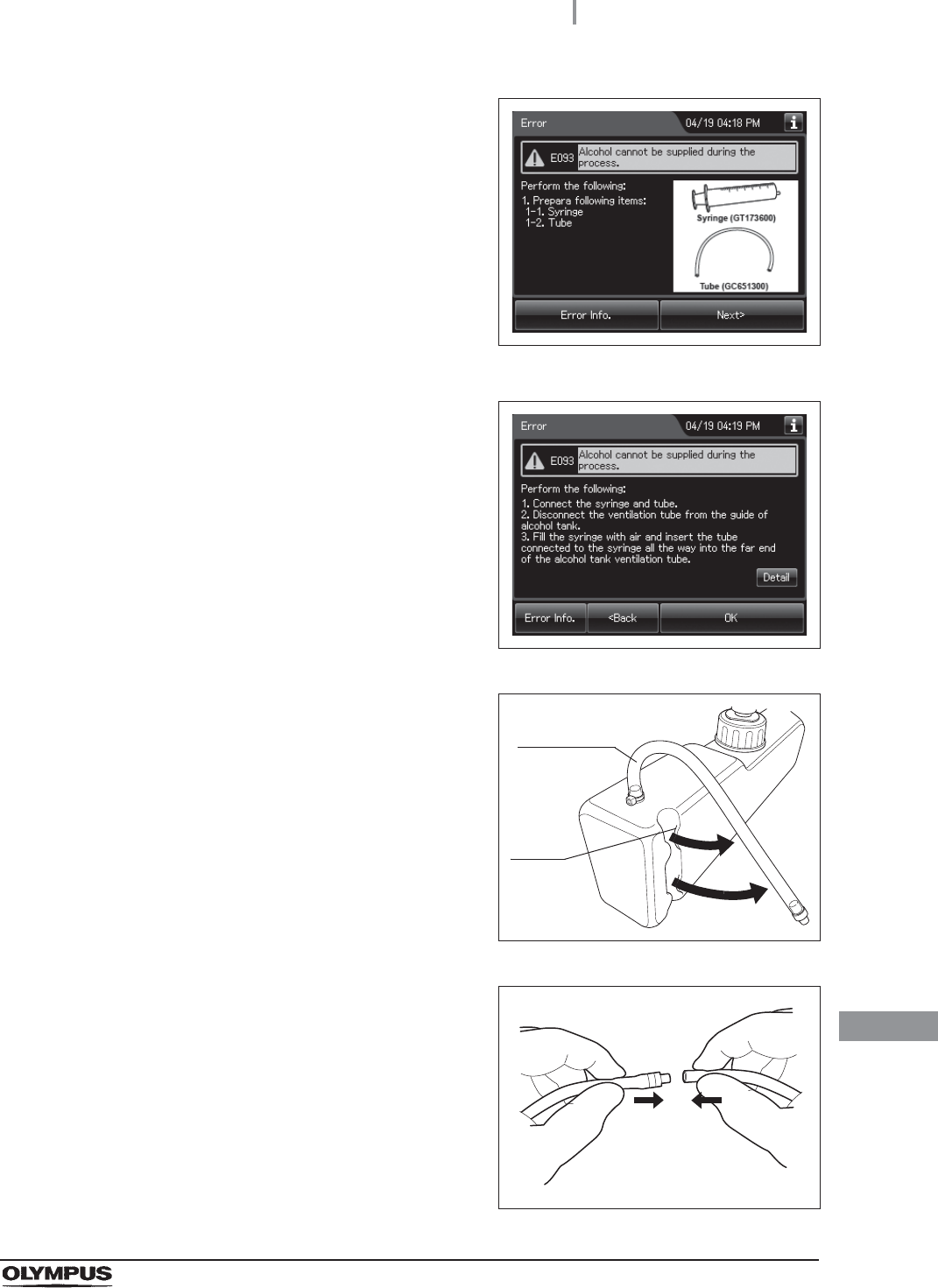
13.2 Troubleshooting guide
631
OER-Elite OPERATION MANUAL
Ch.13
3Connect the provided syringe and tube. For
detail, refer the detail button on E093 on the
touch screen.
Figure 13.16
Figure 13.17
4Disconnect the ventilation tube from the guide
of the alcohol tank.
Figure 13.18
5Fill the syringe with air and insert the tube
connected to the syringe all the way into the far
end of the alcohol tank ventilation tube.
Figure 13.19
Ventilation
tube
Guide
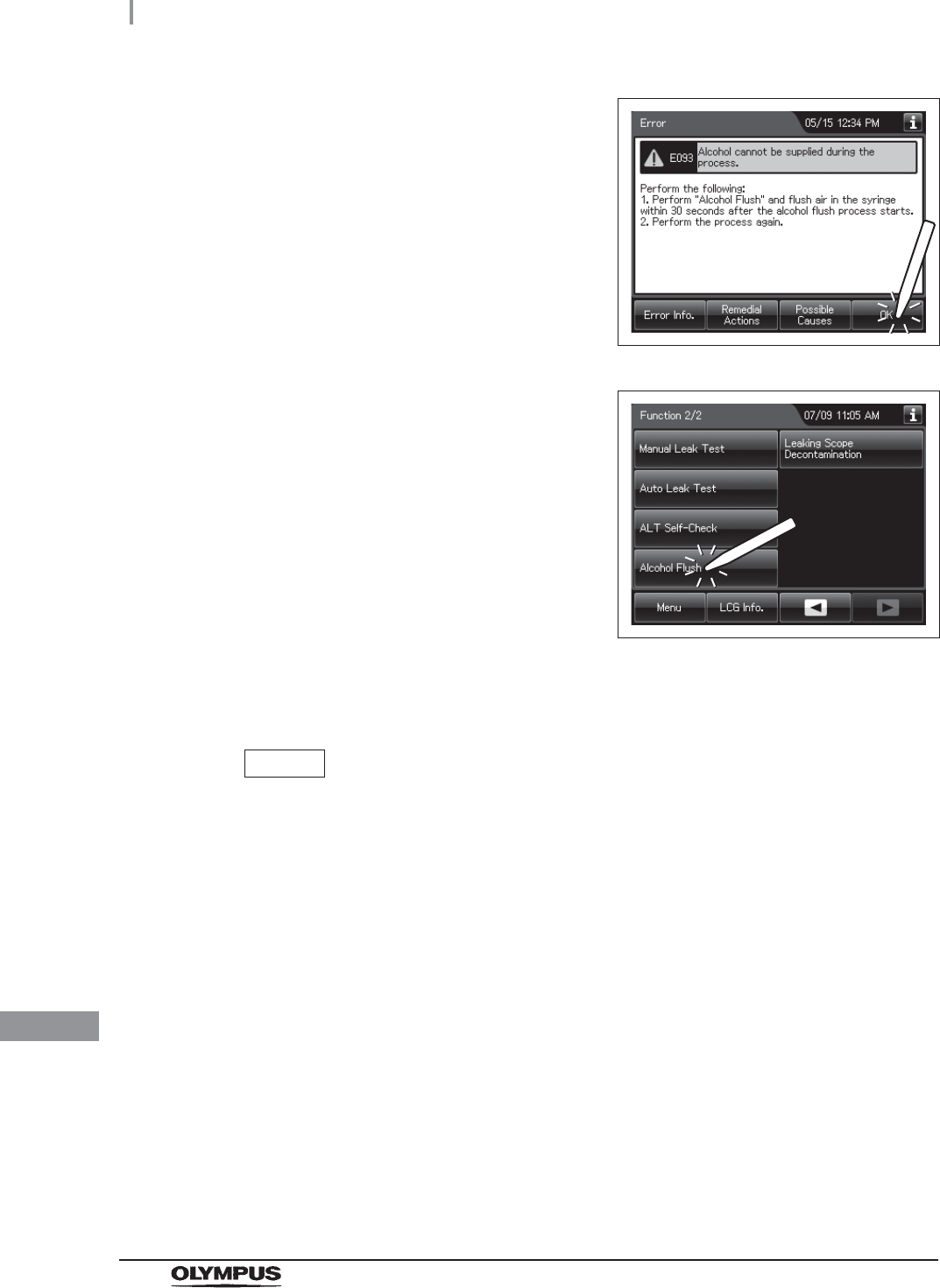
632
13.2 Troubleshooting guide
OER-Elite OPERATION MANUAL
Ch.13
6Press the “OK” button repeatedly until error
screen is closed.
Figure 13.20
7Go to the Function menu. Press the “Alcohol
Flush” button on the second page.
Figure 13.21
8Enter the operator's user ID. For entering ID, refer to Section 3.6, “Entering ID” (If
applicable).
NOTE
The input of the user ID can be omitted by modifying the “User ID Setting”. For
details, refer to Section 4.5, “User ID Setting”.
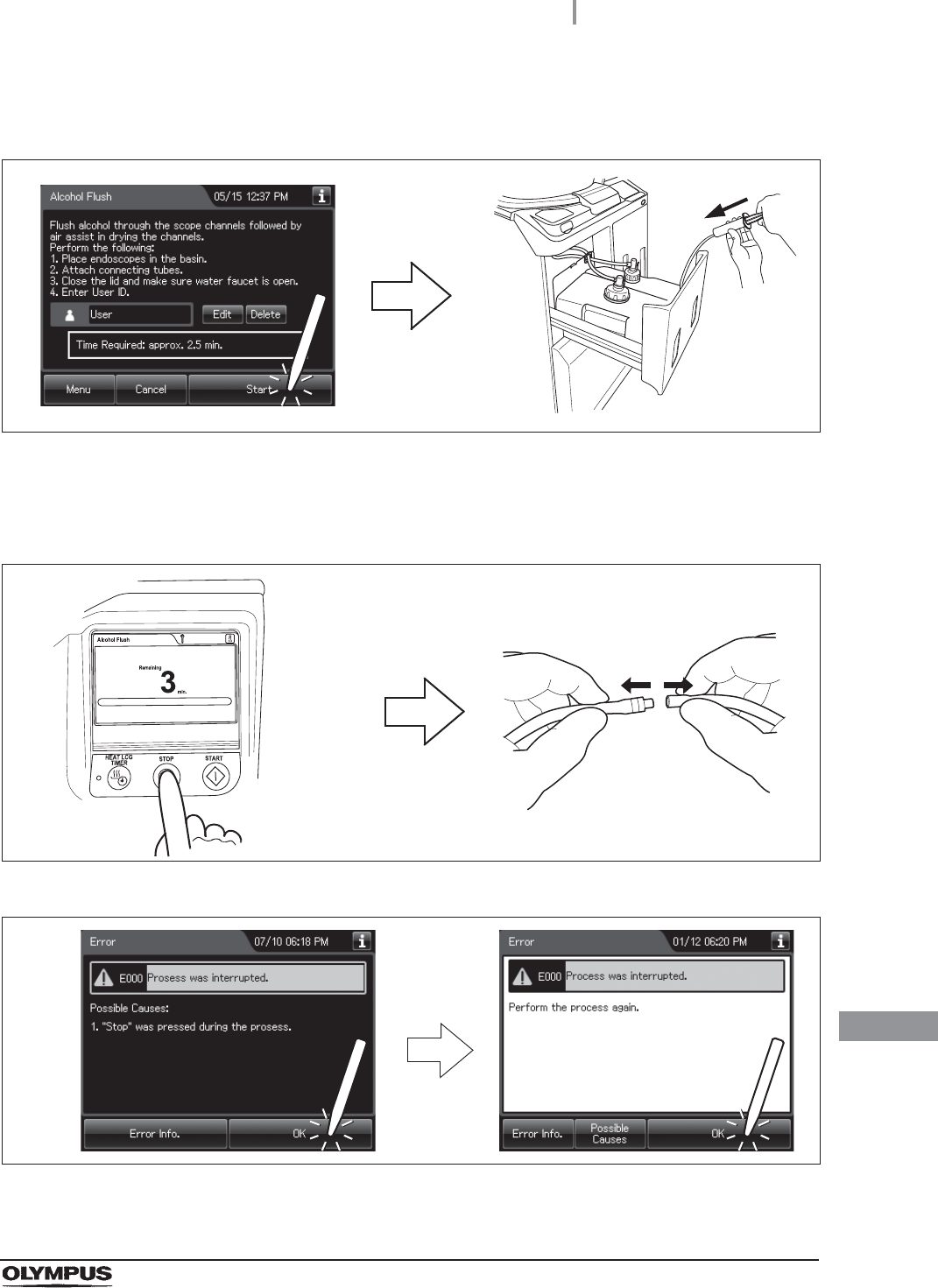
13.2 Troubleshooting guide
633
OER-Elite OPERATION MANUAL
Ch.13
9Press the “Start” button on the touch screen. Flush air in the syringe within
30 seconds.
Figure 13.22
10 Press the “Stop” button to stop the alcohol flush. Then, error code E000 is displayed
on the touch screen. After confirming that, disconnect the syringe's tube from the
ventilation tube.
Figure 13.23
Figure 13.24
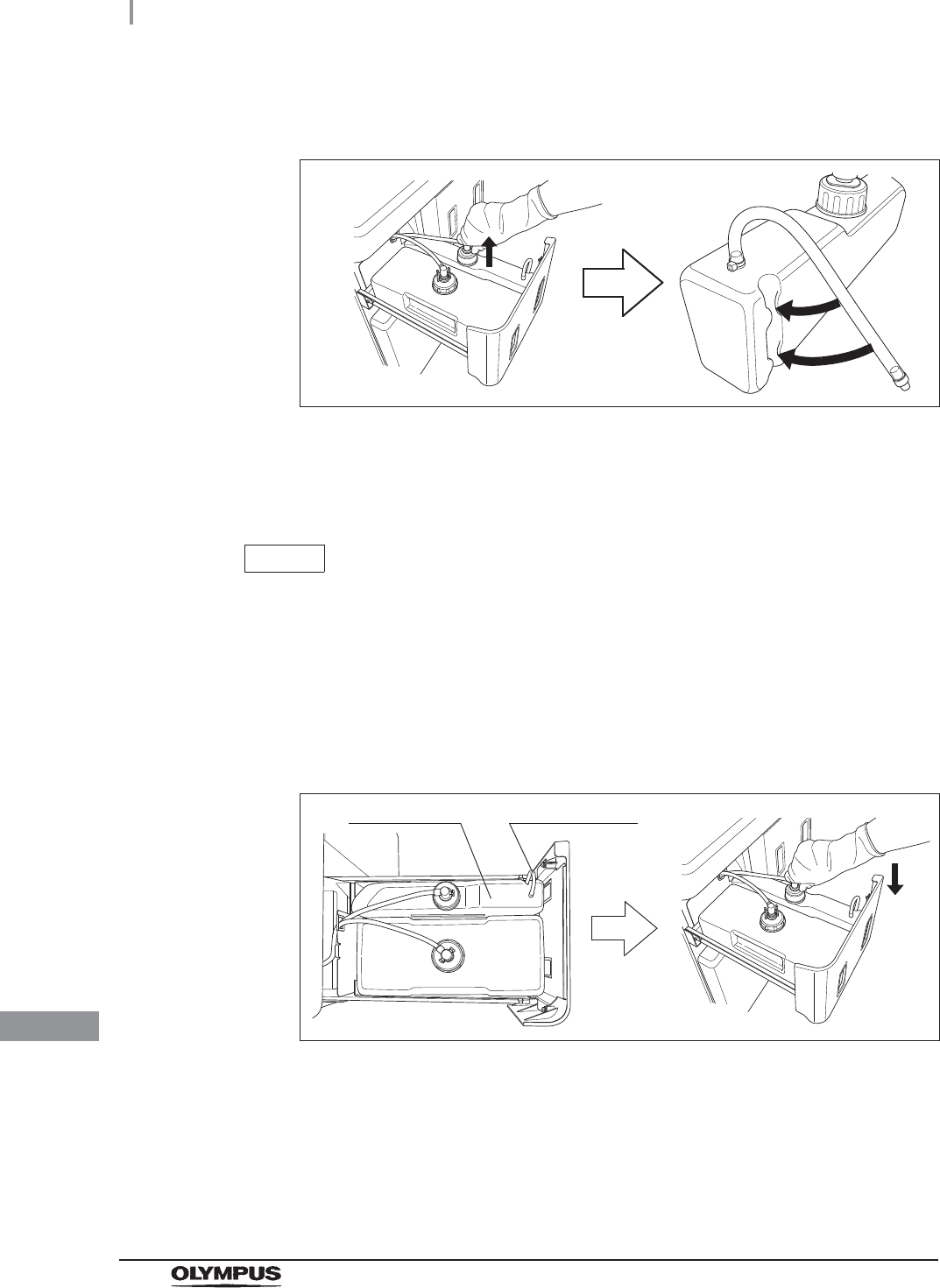
634
13.2 Troubleshooting guide
OER-Elite OPERATION MANUAL
Ch.13
11 Disconnect the tube from the cap on the alcohol tank, remove the tank from the
detergent/alcohol drawer and insert the ventilation tube into the guide.
Figure 13.25
12 Carefully pour the 70% ethyl alcohol or 70% isopropyl alcohol into the alcohol tank
until it is level with the line inside the tank. If any alcohol is spilled from the tank, wipe
it with a clean cloth. Replace the cap on the alcohol tank, making sure that it is tight.
NOTE
When the alcohol tank is filled to the line, it will hold about 1 L (33 ounces) of
alcohol (enough for about 20 alcohol flushes).
13 After confirming that alcohol has not spilled from the alcohol tank and there is enough
alcohol remaining in the alcohol tank, place the alcohol tank in the detergent/alcohol
drawer and connect the tube that is designed to be connected to the cap of the
alcohol tank.
Figure 13.26
14 Close the detergent/alcohol drawer. Rinse the syringe and tube with running water,
dry them completely, and store in a clean place.
15 Perform the “alcohol flush” again from the beginning.
Alcohol tank Ventilation tube
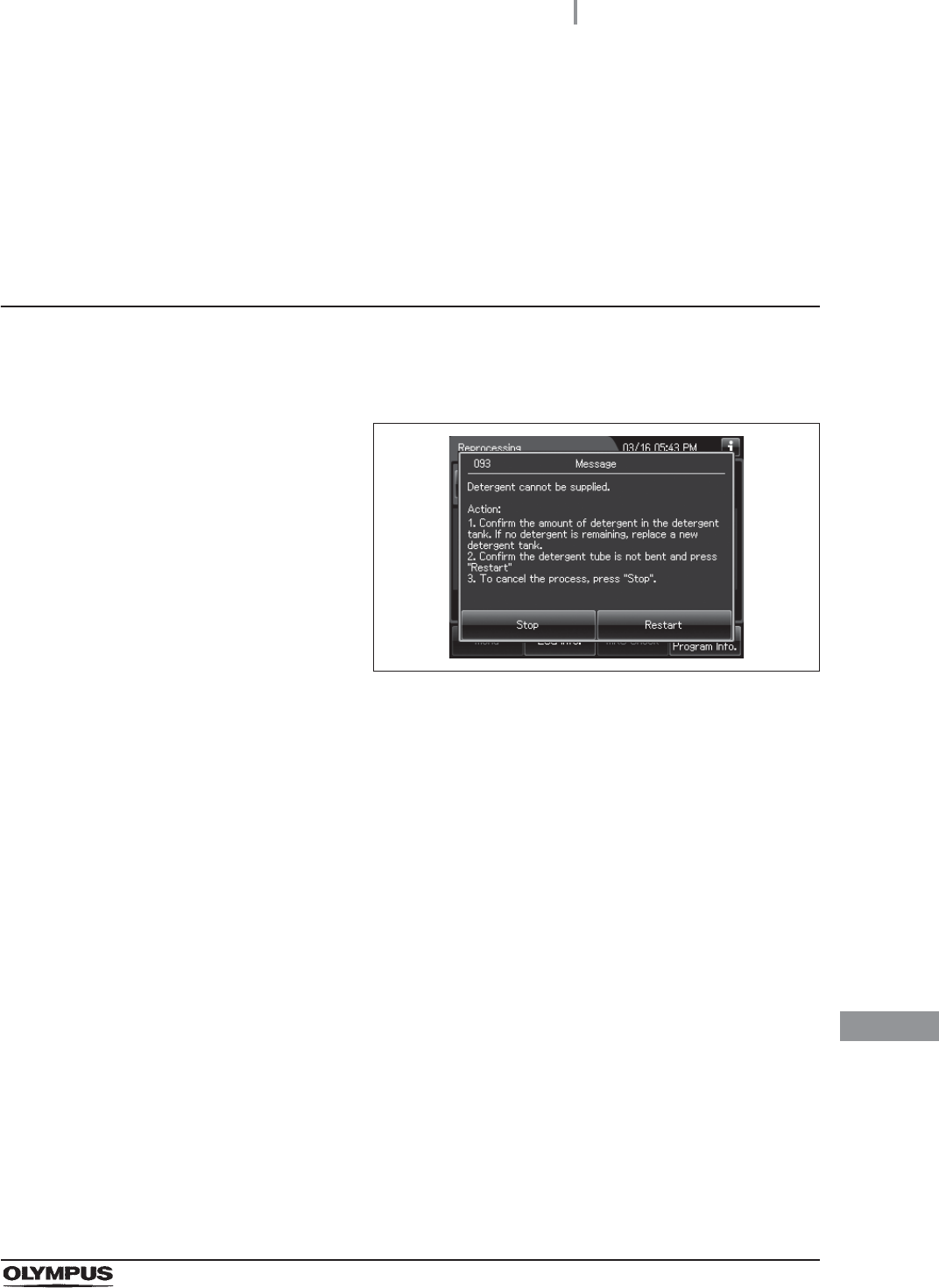
13.2 Troubleshooting guide
635
OER-Elite OPERATION MANUAL
Ch.13
When the “Message 093” is displayed
If detergent has run out and the message screen “Detergent cannot be supplied” is displayed, the
reprocessor will stop the process. In this case, reprocessing can be restarted by implementing the
following procedure.
Figure 13.27
16 If alcohol flush is successfully completed, the problem is resolved and alcohol flush
was performed with the endoscopes. If the “Message 087” is displayed again, the
reprocessor component malfunction is suspected. In this case, do not use the
reprocessor and contact Olympus. Remove endoscope(s) from the basin and perform
alcohol flush again by another method.
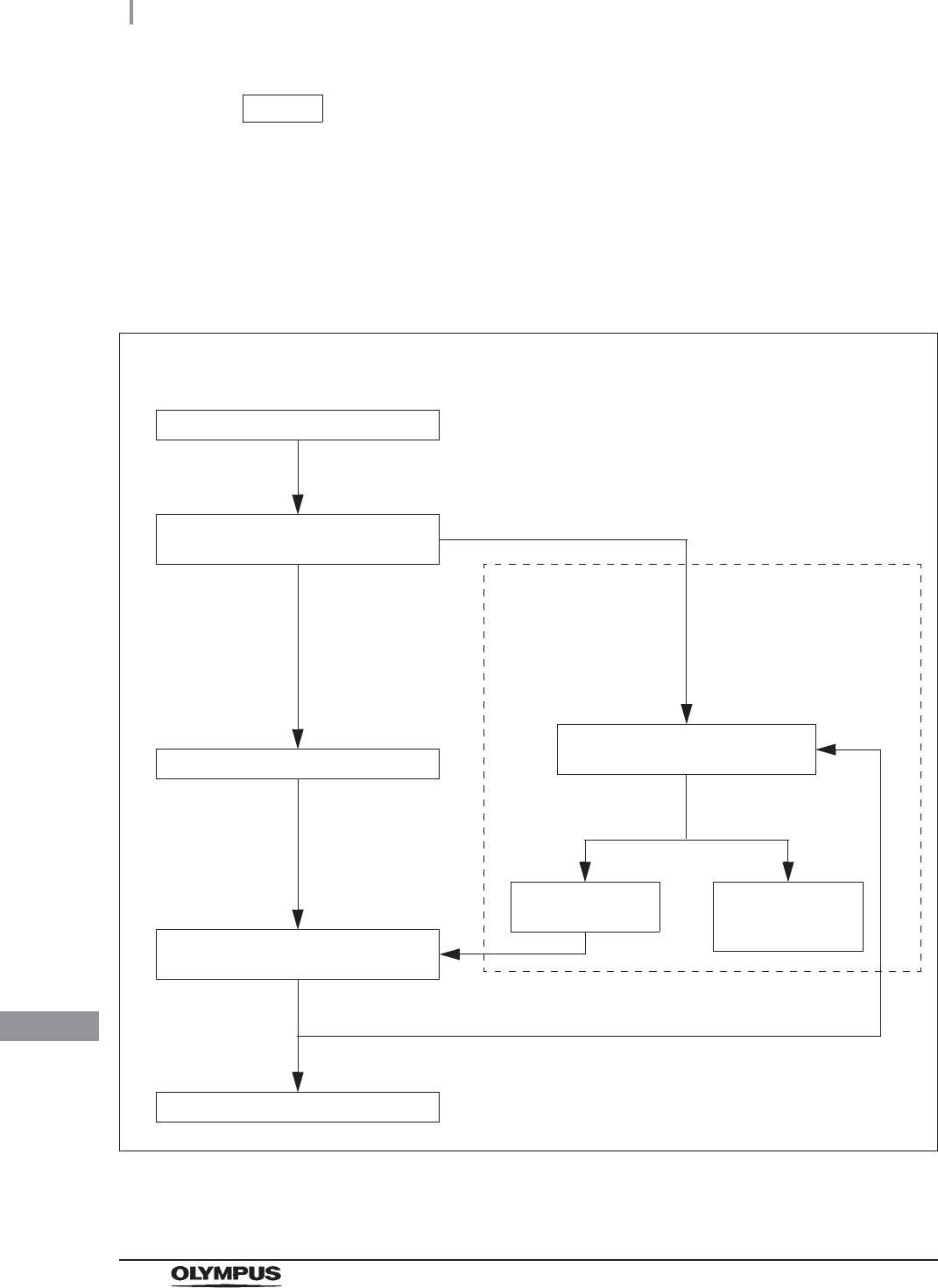
636
13.2 Troubleshooting guide
OER-Elite OPERATION MANUAL
Ch.13
NOTE
• The reprocessing process can be restarted only when the message screen
“Detergent cannot be supplied during the process” is displayed.
• The lid will remain locked until the error is cleared, and you cannot access the
reprocessing basin even after pressing the foot pedal. If you want to interrupt the
reprocessing process, press the “Stop” button and follow the procedure described
in Section 13.1, “Emergency stop and automatic processing after stopping”.
Figure 13.28
When the message 093 is displayed during the reprocessing process
Message screen is displayed.
Confirm whether the detergent still
present in the detergent tank.
1.
Replace the detergent tank.
2.
Press the “Restart” button to restart
the reprocessing process.
3.
Restarted process is completed.
4.
If no detergent
remain in the tank.
If detergent still
present in the tank.
Refer to “If the message
screen “Message 093” is
displayed again after
replacing the detergent
tank and restarting the
reprocessing process:” on
page 638.
Inspect the tube and connector
connected to the detergent tank.
Correct
irregularities.
Perform remedial
action to resolve
the problem.
If any irregularity
is found.
If no irregularity is
found.
If the same message screen is displayed again.
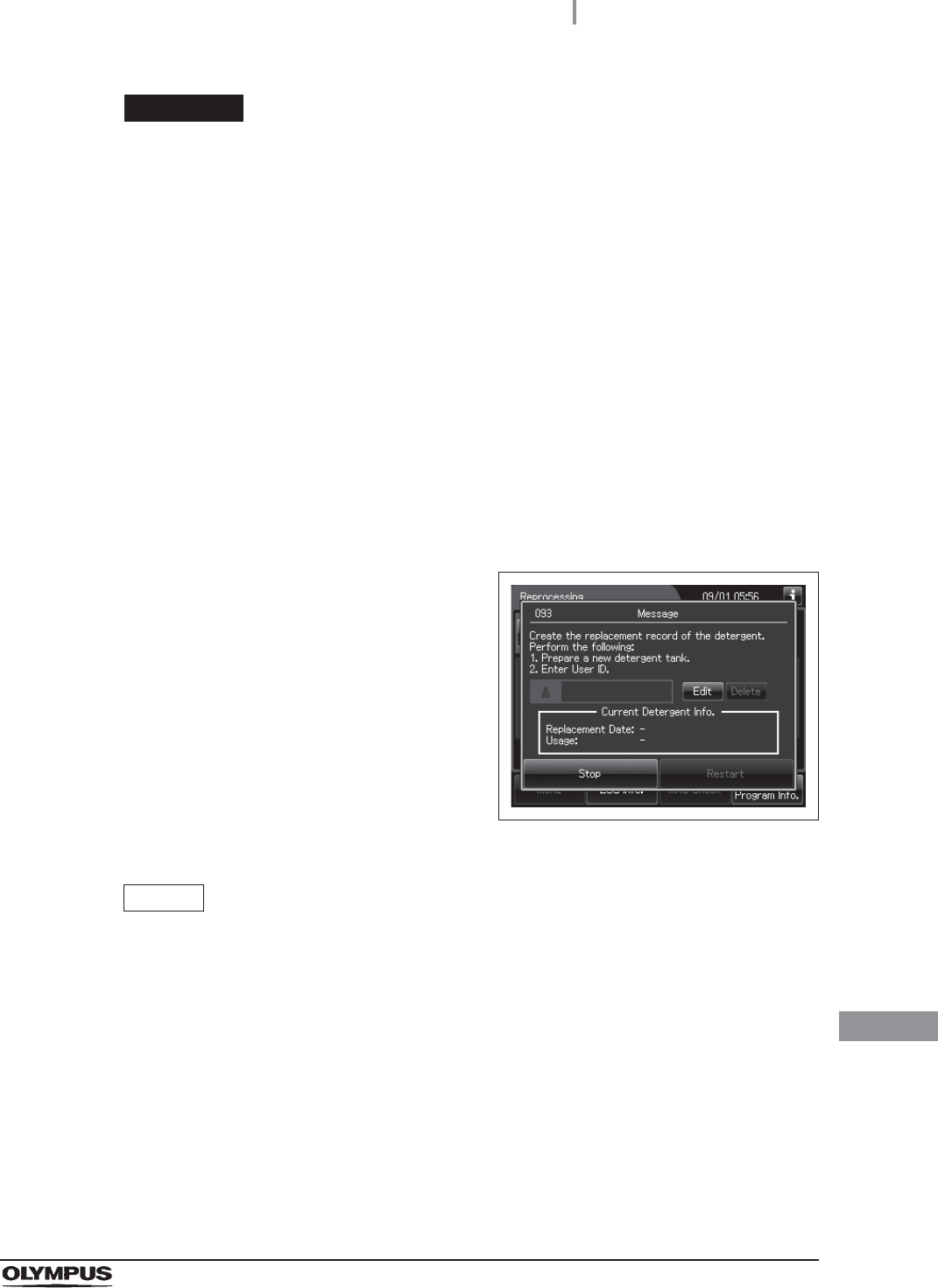
13.2 Troubleshooting guide
637
OER-Elite OPERATION MANUAL
Ch.13
WARNING
• Before handling the detergent, read the cautions carefully and use it as instructed.
It is especially important to know what to do if the detergent solution comes in
contact with your skin and eyes.
• When handling the detergent, always wear appropriate personal protective
equipment, such as eyewear, face mask, moisture-resistant clothing, and
chemical-resistant gloves that fit properly and are long enough so that your skin
and eyes is not exposed. All personal protective equipment should be inspected
before use and replaced periodically before it is damaged.
NOTE
• The input of the user ID can be omitted by modifying the user ID input setting. For
details, refer to Section 4.5, “User ID Setting”.
• When the “Delete” button is pressed, the entered ID is deleted.
• When the detergent lot and shelf-life management setting are activated, the touch
screen displays the lot entry screen or shelf-life entry screen. For details, refer to
“When entering the lot number of detergent and shelf life:” on page 372.
1Inspect the detergent tank. If detergent is still present in the detergent tank, go to the
procedure of “If the message screen “Message 093” is displayed again after
replacing the detergent tank and restarting the reprocessing process:” on page 638
described in this section.
2Replace the detergent tank as described in Section 5.8, “Inspecting the remaining
detergent”.
3Enter the operator’s user ID. For the detailed
procedure, refer Section 3.6, “Entering ID” (If
applicable). Then, press the “Restart” button to
restart the process.
Figure 13.29
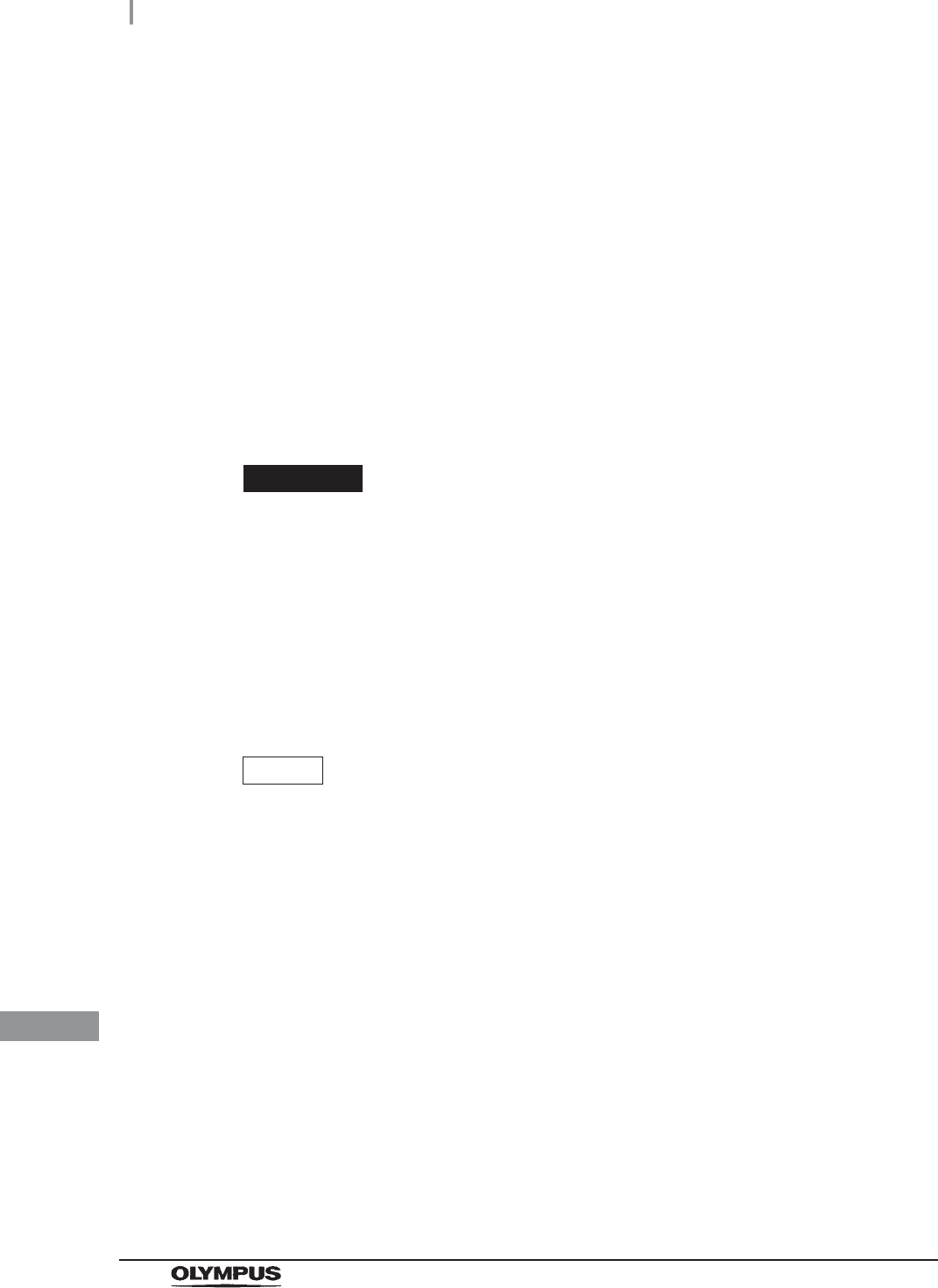
638
13.2 Troubleshooting guide
OER-Elite OPERATION MANUAL
Ch.13
If the message screen “Message 093” is displayed again after
replacing the detergent tank and restarting the reprocessing
process:
When the message screen “Detergent cannot be supplied” is displayed again after restarting the
process, check that there is no irregularity regarding the following points.
• The tube connected to the detergent tank is not kinked.
• The connector of detergent tank is attached firmly.
If any irregularity is found by inspection, correct these points and press start button to restart the
process.
If no irregularity is found during an inspection or the “Detergent cannot be supplied” is displayed
again, internal problem with the reprocessor may be suspected. In this case, follow the
procedure below.
WARNING
• Before handling the detergent, read the cautions carefully and use it as instructed.
It is especially important to know what to do if the detergent solution comes in
contact with your skin and eyes.
• When handling the detergent, always wear appropriate personal protective
equipment, such as eyewear, face mask, moisture-resistant clothing, and
chemical-resistant gloves that fit properly and are long enough so that your skin
and eyes is not exposed. All personal protective equipment should be inspected
before use and replaced periodically before it is damaged.
NOTE
Detergent replacement indicator is turned off when running a reprocessing program
after performing 1 to 11 below to fill detergent in the detergent supply piping.
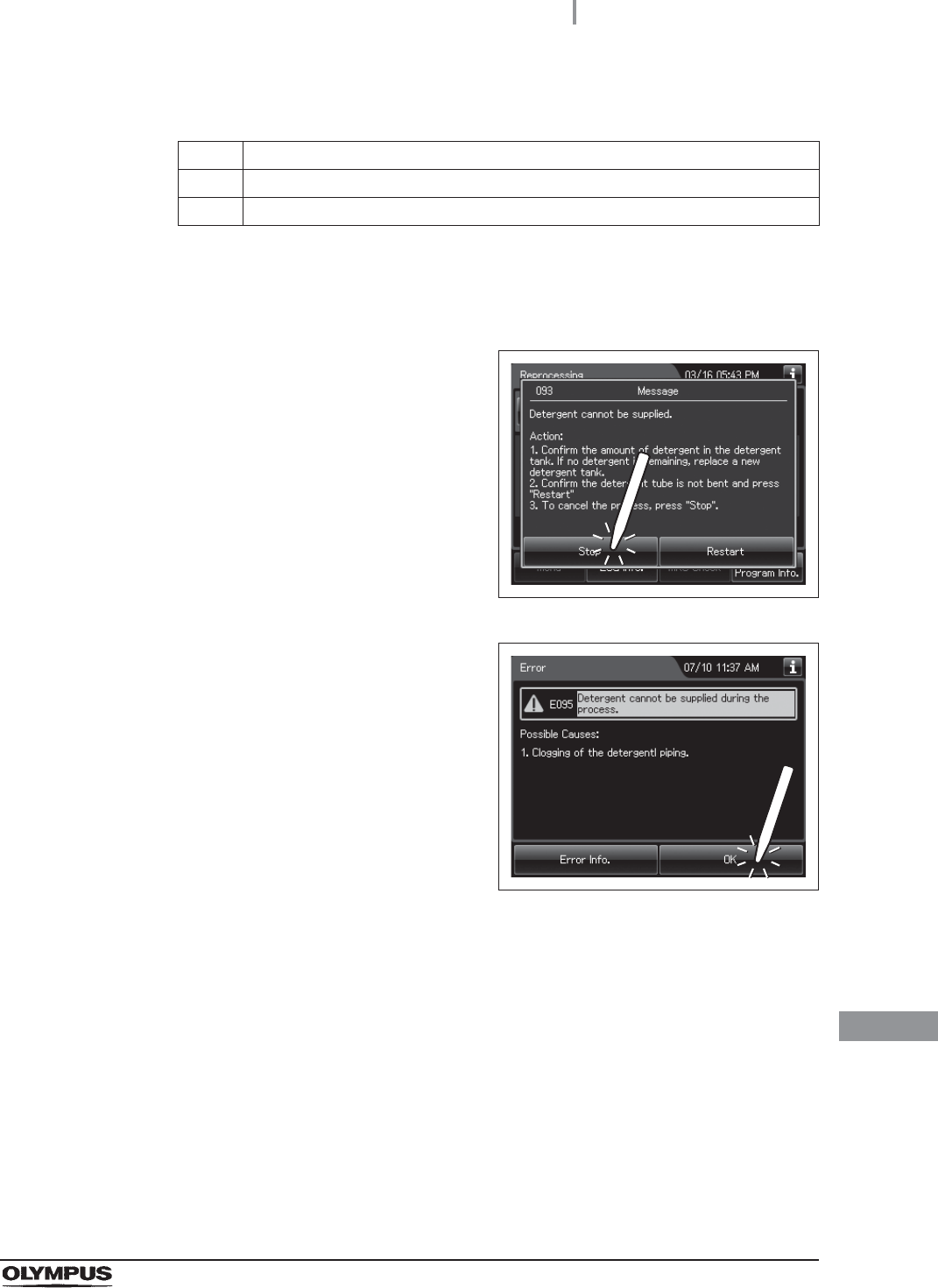
13.2 Troubleshooting guide
639
OER-Elite OPERATION MANUAL
Ch.13
(a) Required items
Tab le 1 3. 3
(b) Remedial actions
Check Required items
Syringe
Tube
1Press the “Stop” button.
Figure 13.30
2The touch screen displays the error code
[E095]. Press the “OK” button. Then,
troubleshooting guide is displayed on the touch
screen.
Figure 13.31
3Step on the foot pedal to open the lid.
4Prepare the provided syringe and the provided tube.
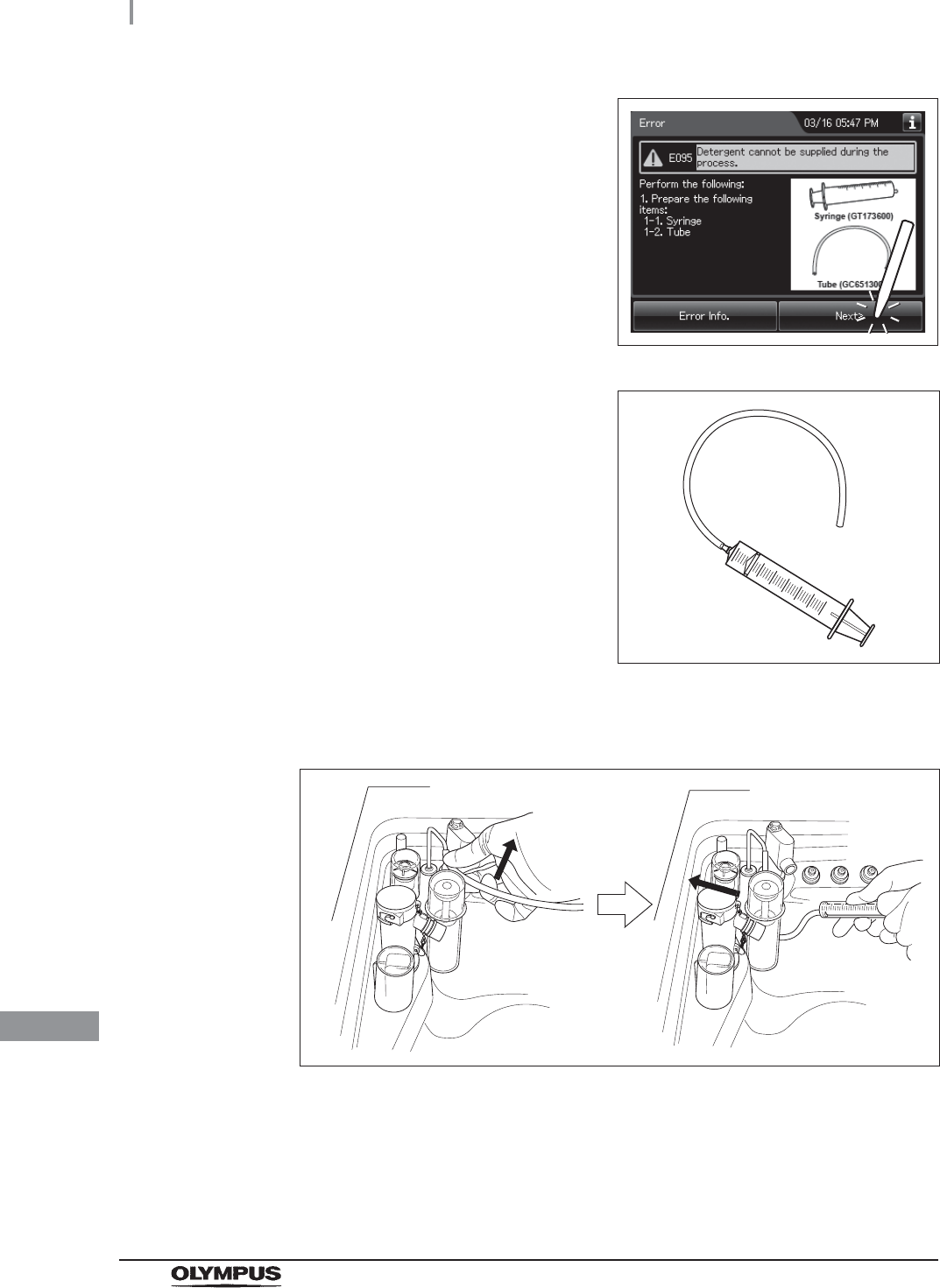
640
13.2 Troubleshooting guide
OER-Elite OPERATION MANUAL
Ch.13
5Press the “Next” button.
Figure 13.32
6Connect the provided syringe and tube.
Figure 13.33
7Connect the tube to the detergent nozzle inside the reprocessing basin and suction it
with the syringe until detergent comes out.
Figure 13.34
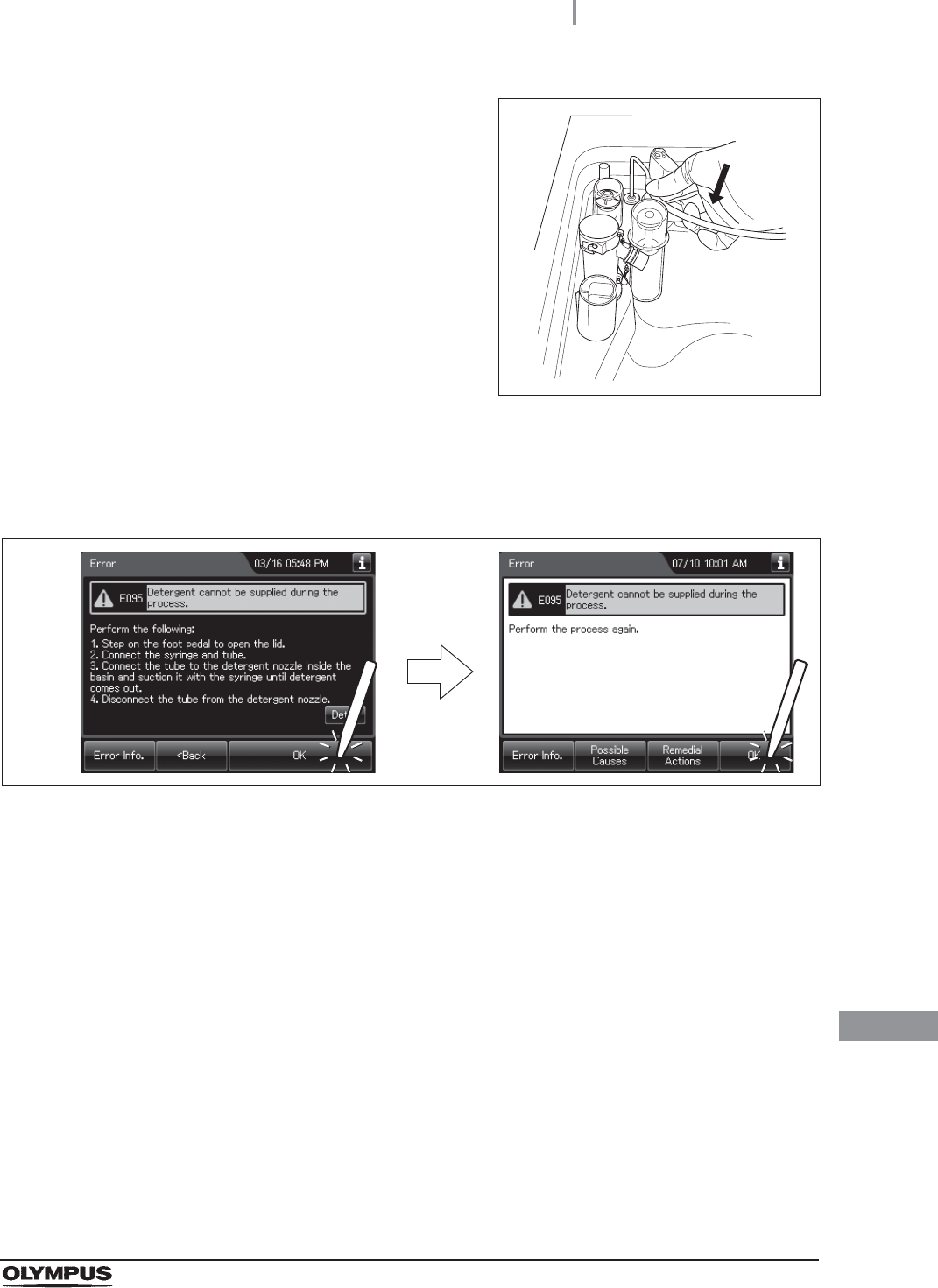
13.2 Troubleshooting guide
641
OER-Elite OPERATION MANUAL
Ch.13
8Pinch the tube at the closest point to the
detergent nozzle with your fingers and
disconnect the tube from the detergent nozzle.
Figure 13.35
9Rinse the syringe and tube thoroughly in running water, dry them well, and store in a
clean place.
10 Press the “OK” button repeatedly until the error screen is closed.
Figure 13.36
11 Start the reprocessing process from the beginning.
12 If the reprocessing process is successfully completed, the problem is resolved and
reprocessing process was performed with the endoscopes. If the “Message 093” is
displayed again, the reprocessor component malfunction is suspected. In this case,
do not use the reprocessor and contact Olympus. Remove endoscope(s) from the
basin and perform reprocessing process again by another method.
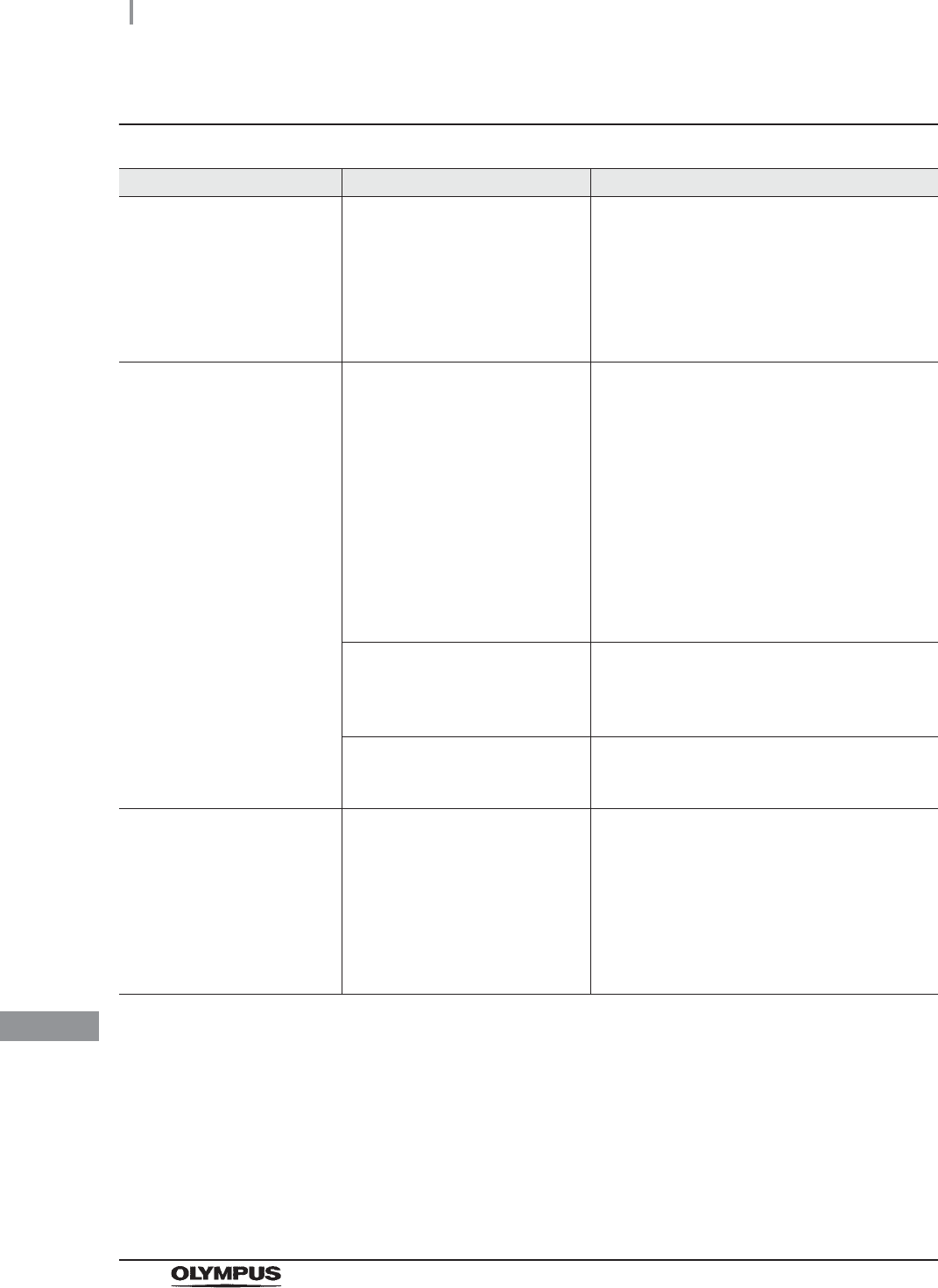
642
13.2 Troubleshooting guide
OER-Elite OPERATION MANUAL
Ch.13
Other problems and remedial actions
Problem Possible causes Remedial actions
The odor of the disinfectant
solution is stronger than
expected.
• The gas filter has expired.
• Disinfectant solution is
leaking.
• Replace the gas filter as described in
Section 8.6, “Replacing the gas filter
(MAJ-822)”. If the problem persists after
replacement, contact Olympus.
• Check if disinfectant solution is leaking. If it
is, do not use the reprocessor and contact
Olympus.
Water leak from the
reprocessor.
Improper installation of water
filter housing.
Stop the current process and reattach the
water filter housing as described in
Section 8.4, “Replacing the water filter
(MAJ-824 or MAJ-2318)”.
However, the STOP button may not work if
stopping the water might cause a hazardous
situation, for example during disinfectant
solution replacement. In this case, close the
water faucet, tighten the water filter housing,
then open the water faucet again and continue
the process. If an error code is displayed, take
the appropriate remedial action for that error.
Irregularity in the lid packing Inspect the lid packing.
oRefer to Section 5.5, “Inspecting the lid and
lid packing”.
If the lid packing is abnormal, contact Olympus.
Internal problem with the
reprocessor.
Close the water faucet, set the power switch to
OFF, disconnect the power cord plug from the
wall mains outlet and contact Olympus.
Fluid leak from the
disinfectant removal port.
Something is clogging the
disinfectant removal port.
Connect the drain connector as described in to
Section 3.7, “Checking the MRC level and
entering the check result”, push the valve on
the connector several times so that the
material stuck in the port is removed. If leakage
is still detected, attach the rubber cap to the
disinfectant solution drain port and contact
Olympus.
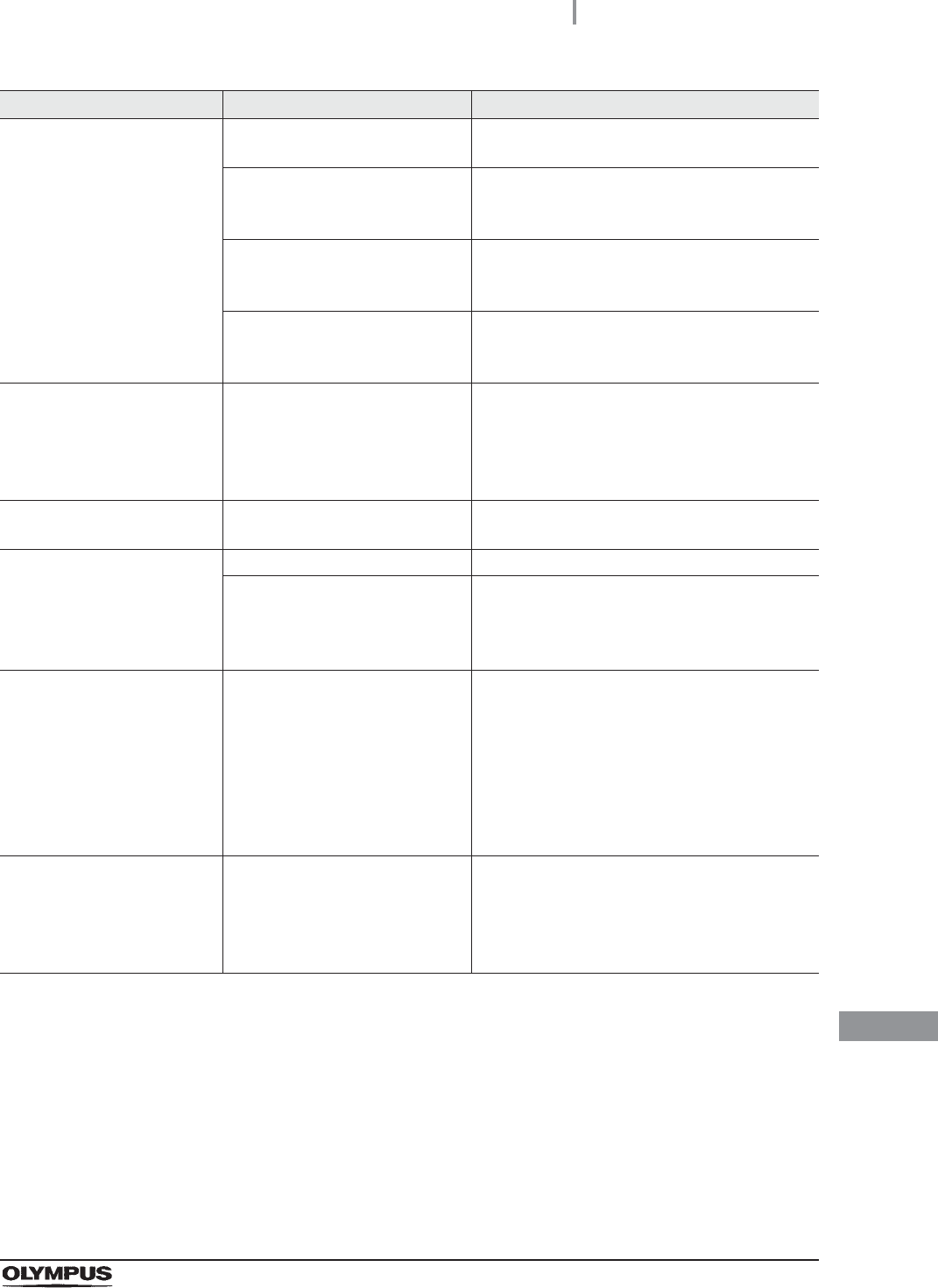
13.2 Troubleshooting guide
643
OER-Elite OPERATION MANUAL
Ch.13
Flow of the water in the
reprocessing basin is weaker
than before.
Incomplete opening of the water
faucet.
Open the water faucet fully.
Improper installation of water
filter.
Reattach the water filter as described in
Section 8.4, “Replacing the water filter
(MAJ-824 or MAJ-2318)”.
Clogging of water filter. Replace the water filter as described in
Section 8.4, “Replacing the water filter
(MAJ-824 or MAJ-2318)”.
Clogging of the mesh filter in the
water supply hose connector.
Clean the mesh filter as described in
Section 9.7, “Cleaning the mesh filter in the
water supply hose connector”.
The disinfectant bottle
drawer cannot be pulled out.
The disinfectant bottle drawer is
locked.
After draining the disinfectant solution from the
reprocessor as described in Section 8.2,
“Replacing the disinfectant solution”, perform
“Load LCG” and unlock the disinfectant bottle
drawer.
Connecting tube cannot be
connected.
Not using the appropriate
connecting tube.
Consult the List Of Compatible
Endoscopes/Connecting Tubes <OER-Elite>.
The lid cannot be closed. The lid is locked. Step on the foot pedal to unlock the lid.
Internal components are
pressing against the lid.
Check that the lid is not pushed by the fluid
level sensor, washing case or endoscope
inside the basin. If it is pushed out of position,
correct its positioning.
Disinfectant solution remains
in the reprocessing basin.
STOP button was pressed
during disinfection process to
force it to stop.
If an error code is displayed, take the
corresponding remedial action. Collect or drain
the disinfectant solution and then rinse the
basin as described in Section 7.5, “Rinse”.
Since the endoscopes may not be properly
disinfected, they should be put through the
reprocessing process again from the
beginning.
Cleaning fluid remains in the
reprocessing basin.
STOP button was pressed
during cleaning process to force
it to stop.
Rinse the basin as described in Section 7.5,
“Rinse”. Since the endoscopes may not be
properly disinfected, they should be put
through the reprocessing process again from
the beginning.
Problem Possible causes Remedial actions
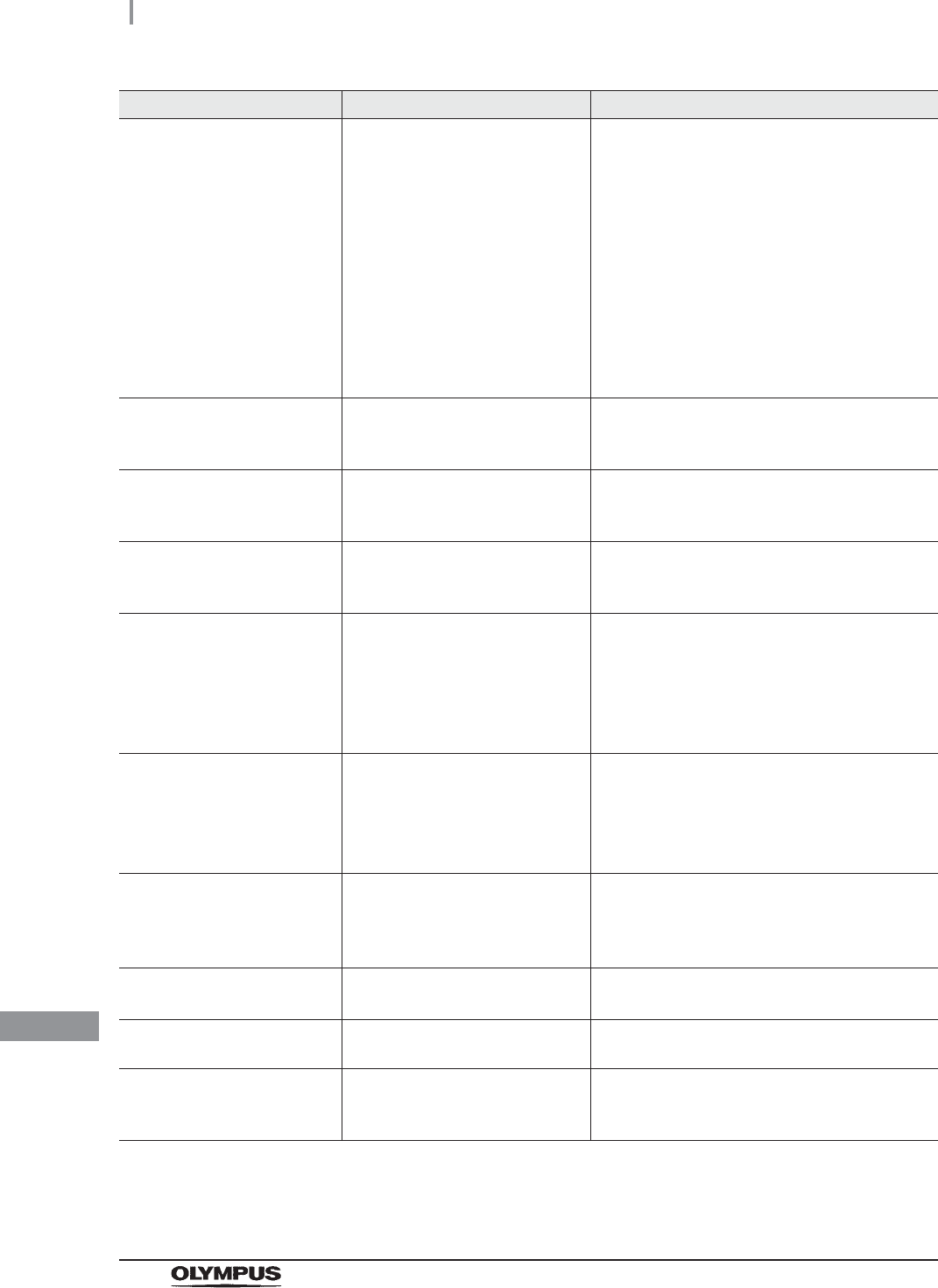
644
13.2 Troubleshooting guide
OER-Elite OPERATION MANUAL
Ch.13
The touch screen appears to
turn off completely during an
operation.
• The Heat LCG Timer process
started.
• Power cord is disconnected
from the power outlet.
• Circuit breaker is activated.
• A power failure has occurred.
• Check that the Heat LCG Timer indicator on
the control panel is lit. If it is lit, pressing the
touch screen or a button will cause the touch
screen to display a screen.
• Perform the checks described in Section 5.3,
“Inspecting the power activation”. Error code
[E041] will be displayed when the
reprocessor is turned ON.
After checking, release the error code. Note
that, however, any button is disabled during
collection of the disinfectant solution from the
reprocessing basin to the tank.
Power indicator does not
light when the reprocessor is
turned on.
Power switch is set to ON
immediately after it was set to
OFF.
Set the power switch to OFF, wait for a few
seconds or more and set the power switch to
ON again.
Reprocessing operator feels
sick during work.
The operator may be allergic to
the disinfectant, detergent or
alcohol.
Stop doing any reprocessing, move away from
the reprocessor and consult a medical
specialist.
Disinfectant solution is
judged to be ineffective with
the test strip.
Expiration of the service life of
the disinfectant solution.
Replace the solution as described in
Section 8.2, “Replacing the disinfectant
solution”.
Bacteria were detected as a
result of culture test of a
reprocessed endoscope.
• Expiration of service life of
filters, degradation of
disinfectant solution, etc.
• Water supply piping is not
disinfected.
Inspect the reprocessor as described in
Chapter 5, “Inspection and Preparation Before
Use”, preclean the endoscope and put it
through the reprocessing process again from
the beginning. If bacteria are detected again in
the next culture test, contact Olympus.
Bacteria were detected as a
result of culture test of rinse
water collected from the
reprocessor.
• Expiration of service life of
filters, degradation of
disinfectant solution, etc.
• Water supply piping is not
disinfected.
Inspect the reprocessor as described in
Chapter 5, “Inspection and Preparation Before
Use”. If bacteria are detected again in the next
culture test, contact Olympus.
Endoscopes were not
precleaned before being
reprocessed. –
Inspect the reprocessor as described in
Chapter 5, “Inspection and Preparation Before
Use”. Then, preclean the endoscopes and
reprocess them again from the beginning.
Printed paper is not output
from the printer.
• Printer paper roll has run out.
• Paper jam.
Take the remedial action by referring to the
MAJ-2144 instruction manual for printer.
Abnormal noise from the
reprocessor.
Internal problem with the
reprocessor.
Contact Olympus.
Non-connected status is
displayed (yellow indicator)
on the touch screen.
The connection with a network is
not established.
Check the connection of the network cable and
the network setting of the reprocessor.
Problem Possible causes Remedial actions
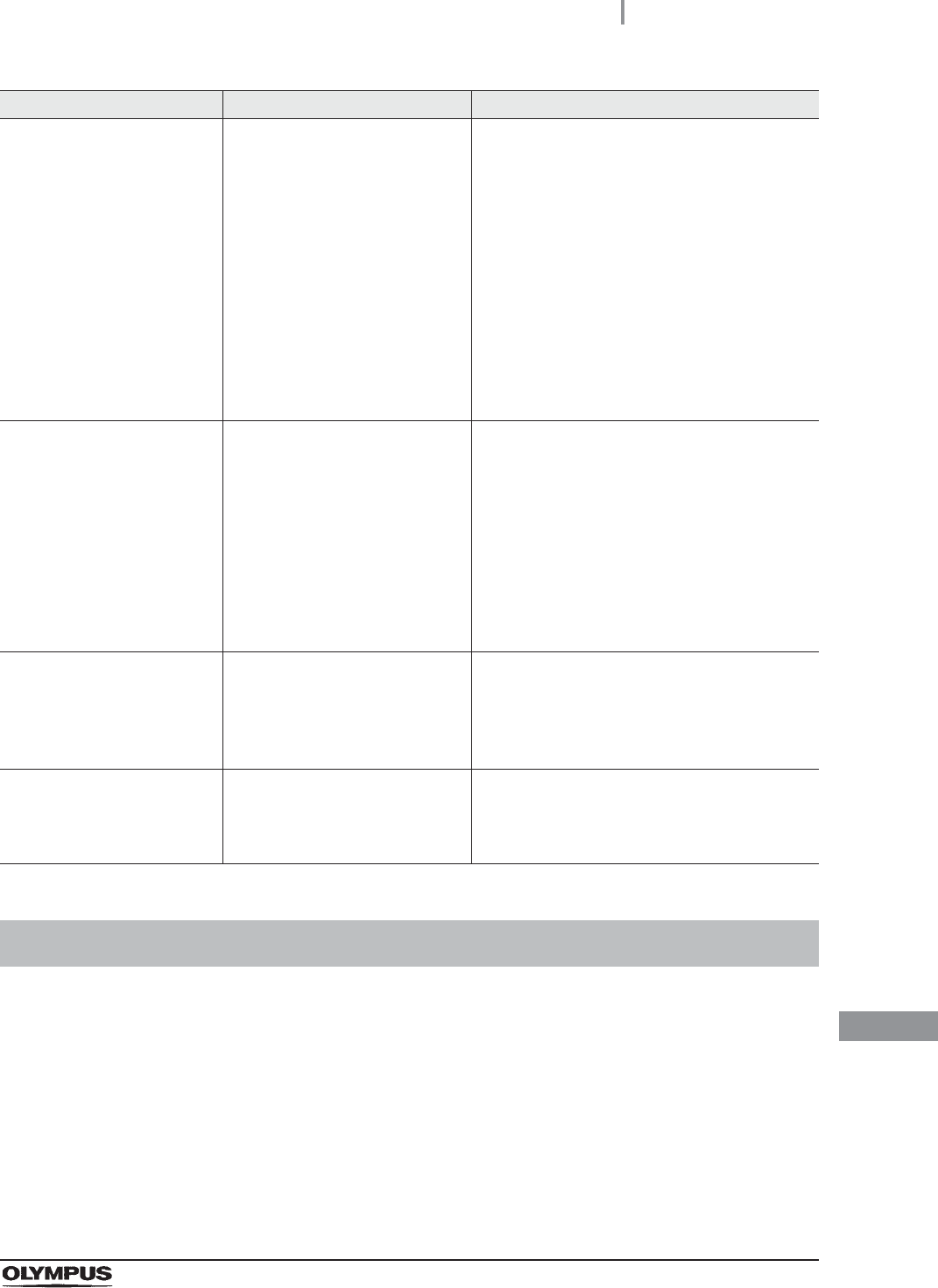
13.3 OER-Elite return
645
OER-Elite OPERATION MANUAL
Ch.13
Contact Olympus for information about packing and shipping the reprocessor for return. When you
return the reprocessor, include a description of the malfunction or damage and how it occurred.
Auto leak test conducted
independently gave the
“Leaked” judgment result.
• Water leak of an endoscope.
• Irregularity with the leak test
air tube.
• Endoscope is warm because it
was cleaned manually with
warm water.
• Check if the endoscope has a water leaking
point with manual leak test. If a leak point
exists on the outer surface, stop it with a
piece of tape and perform the leaking scope
decontamination as described in
Section 7.15, “Leaking scope
decontamination”. After it, return the
endoscope to Olympus for servicing. If the
leak point exists in a position where taping is
impossible, do not execute this process but
contact Olympus.
• Perform the ALT self-check. If an error is
detected, contact Olympus.
Do not know how to return
the leaking endoscope to
Olympus for servicing.
– Check the leaking point of the endoscope with
manual leak test. If the leak point exists on the
outer surface, stop it with a piece of tape and
perform the leaking scope decontamination as
described in Section 7.15, “Leaking scope
decontamination”. After it, return the
endoscope to Olympus for servicing. If the leak
point exists in a position where taping is
impossible, do not execute this process but
contact Olympus.
Leaking scope
decontamination is
performed without attaching
connector jigs.
Connection of connector jigs
was forgotten.
If the leaking scope decontamination is already
completed, return the endoscope to Olympus
for servicing. Do not retry leaking scope
decontamination, as this may cause excessive
water leak inside the endoscope.
Error code [E115] is
generated several times
during leaking scope
decontamination.
Water leak from the endoscope
is serious (the leaking hole is
big).
Contact Olympus.
13.3 OER-Elite return
Problem Possible causes Remedial actions

646
13.3 OER-Elite return
OER-Elite OPERATION MANUAL
Ch.13
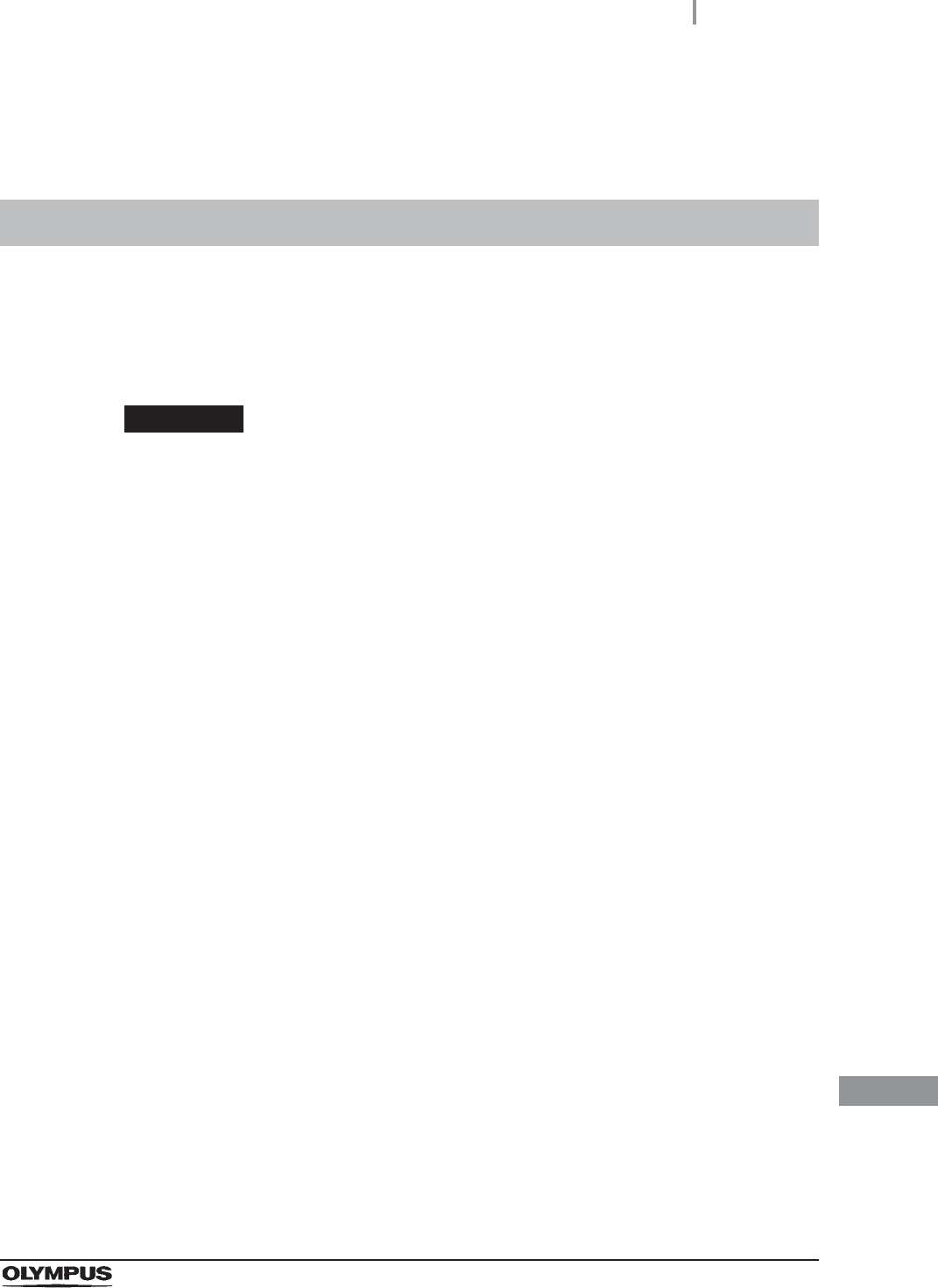
App.
System chart
647
OER-Elite OPERATION MANUAL
Appendix
The recommended combinations of equipment and accessories that can be used with this reprocessor
are listed below. Some items may not be available in some areas. New products released after the
introduction of this reprocessor may also be compatible with this equipment. For further details, contact
Olympus.
WARNING
If combinations of equipment other than those shown below are used, Olympus
cannot guarantee that the device will perform as expected. Nor can Olympus
guarantee the safety of patients and operators. Nor can the durability of the device
be guaranteed when nondesignated equipment is used. Any damage resulting from
improper combinations will not be serviced or repaired free of charge.
System chart
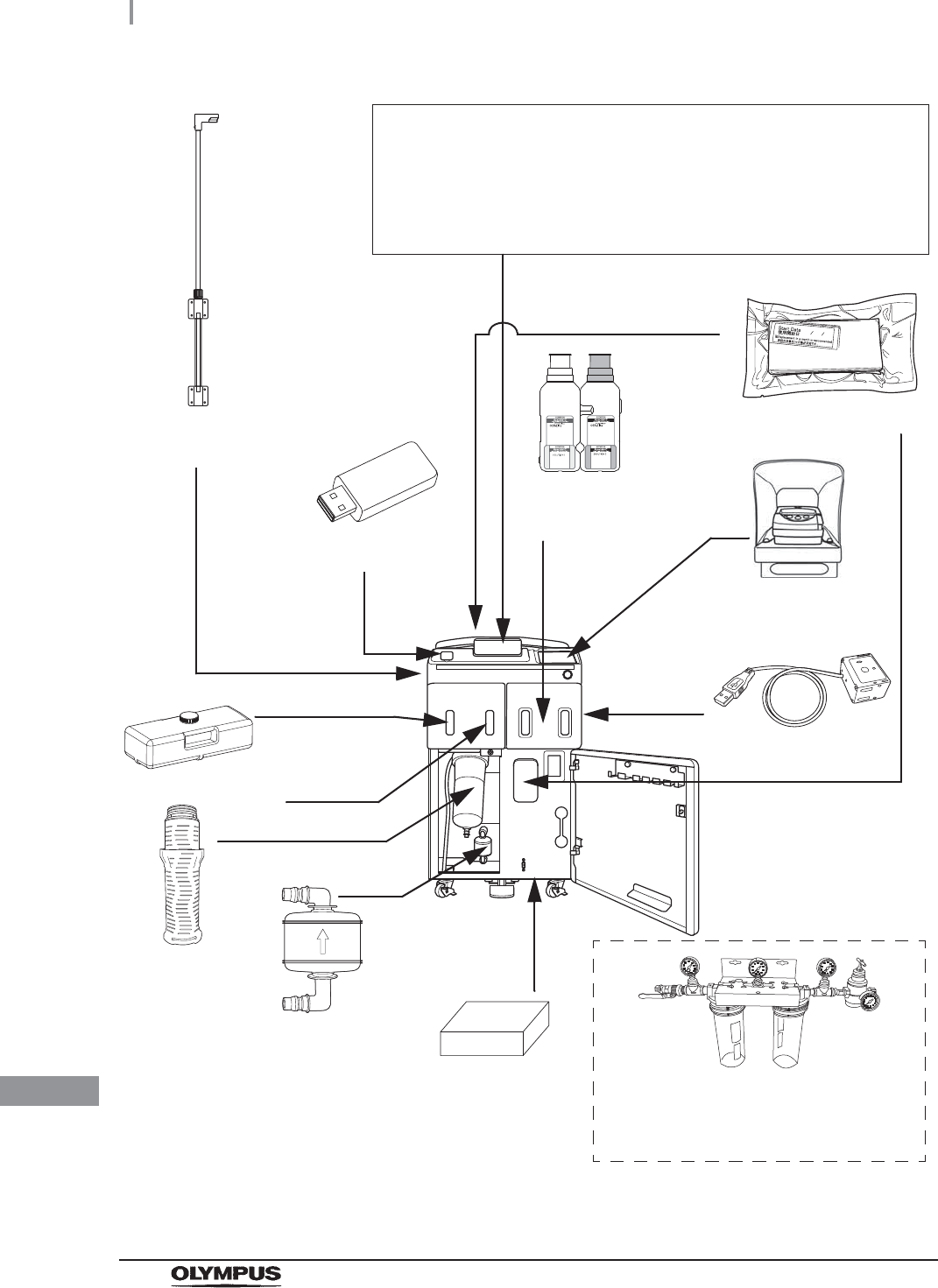
App.
648
System chart
OER-Elite OPERATION MANUAL
Reprocessing basin
Olympus endoscopes (for compatible models, refer to the separately
provided “List of Compatible Endoscopes/Connecting Tubes
<OER-Elite>”).
Connecting tubes (for the connecting tubes compatible to each
endoscope model, also refer to the “List of Compatible
Endoscopes/Connecting Tubes <OER-Elite>”).
Connector hanger
(MAJ-865)
Olympus-validated
detergent
Water filter
(MAJ-824 or
MAJ-2318)
Alcohol
Gas filter (MAJ-822)
Air filter (MAJ-823)
Endoscope
reprocessor
(OER-Elite)
Water pre-filtration system
Using a prefilter can extend the life of
the water filter.
Olympus-validated
concentrated
disinfectant solution
1 Always use Olympus designated external devices for communication with OER-Elite. If not, Olympus
cannot guarantee that the device will perform as expected. For more details on external devices available
in your area, contact Olympus.
Olympus-designated
external devices
(for communication
with OER-Elite)*1
Portable memory
(MAJ-1925)
Bar code reader
(MAJ-2130)
Printer set
(MAJ-2144)
This device is
connected to
back side.
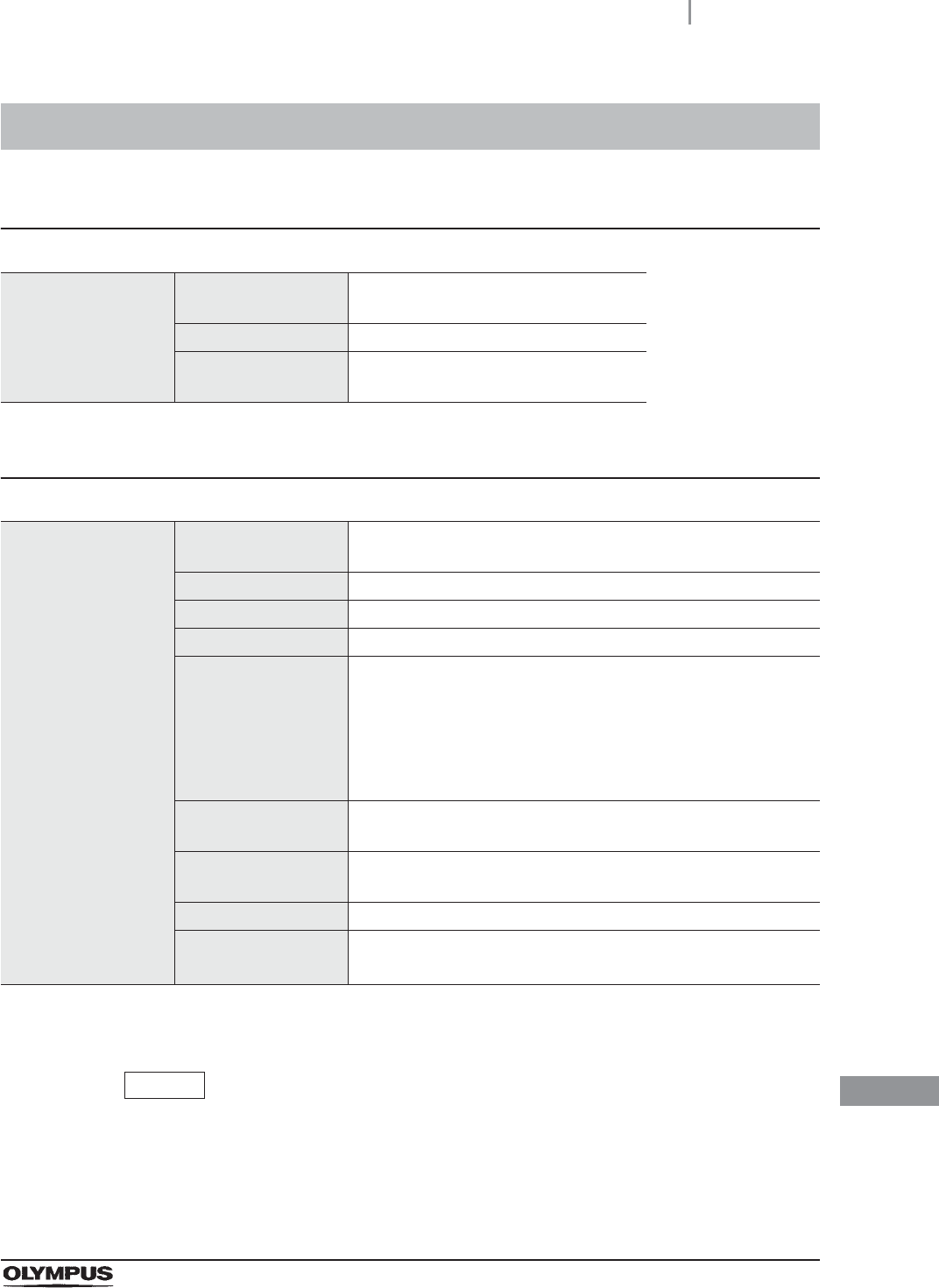
App.
Specifications
649
OER-Elite OPERATION MANUAL
Shipping environment
Operating environment
NOTE
• Purified water is water that has been produced through the methods of either
reverse osmosis (RO), deionization (DI), distillation or other methods that meet
USP standards to remove impurities.
• When the water supply flow is less than 18 l/min, the reprocessing process time is
extended.
Specifications
Shipping
environment
Ambient
temperatures –47 to +60qC (–52 to +140qF)
Relative humidity 10 – 95
Atmospheric
pressure 700 – 1060 hPa
Operating
environment
Ambient
temperatures 10 – 40qC (50 – 104qF)
Relative humidity 30 – 85
Elevation 3000 meters
Designed for use Indoors
Water supply flow • Minimum quantity of water supply (from the water
supply/circulation nozzle) to complete a reprocessing process:
6 L/min or more
• Recommended quantity of water supply (from the water
supply/circulation nozzle) to achieve the minimum reprocessing
time: 18 L/min
Water supply
pressure 0.1 – 0.5 MPa (include water hammer)
Water supply
temperature 5 – 28qC (41 – 82qF)
Water type Potable water, softened water or purified water
Water hardness 0 – 400 ppm
0 – 150 ppm (Recommended value) *1
*1 The recommended value is in reference to AAMI TIR34: 2014 “Water for the reprocessing of medical
devices”.
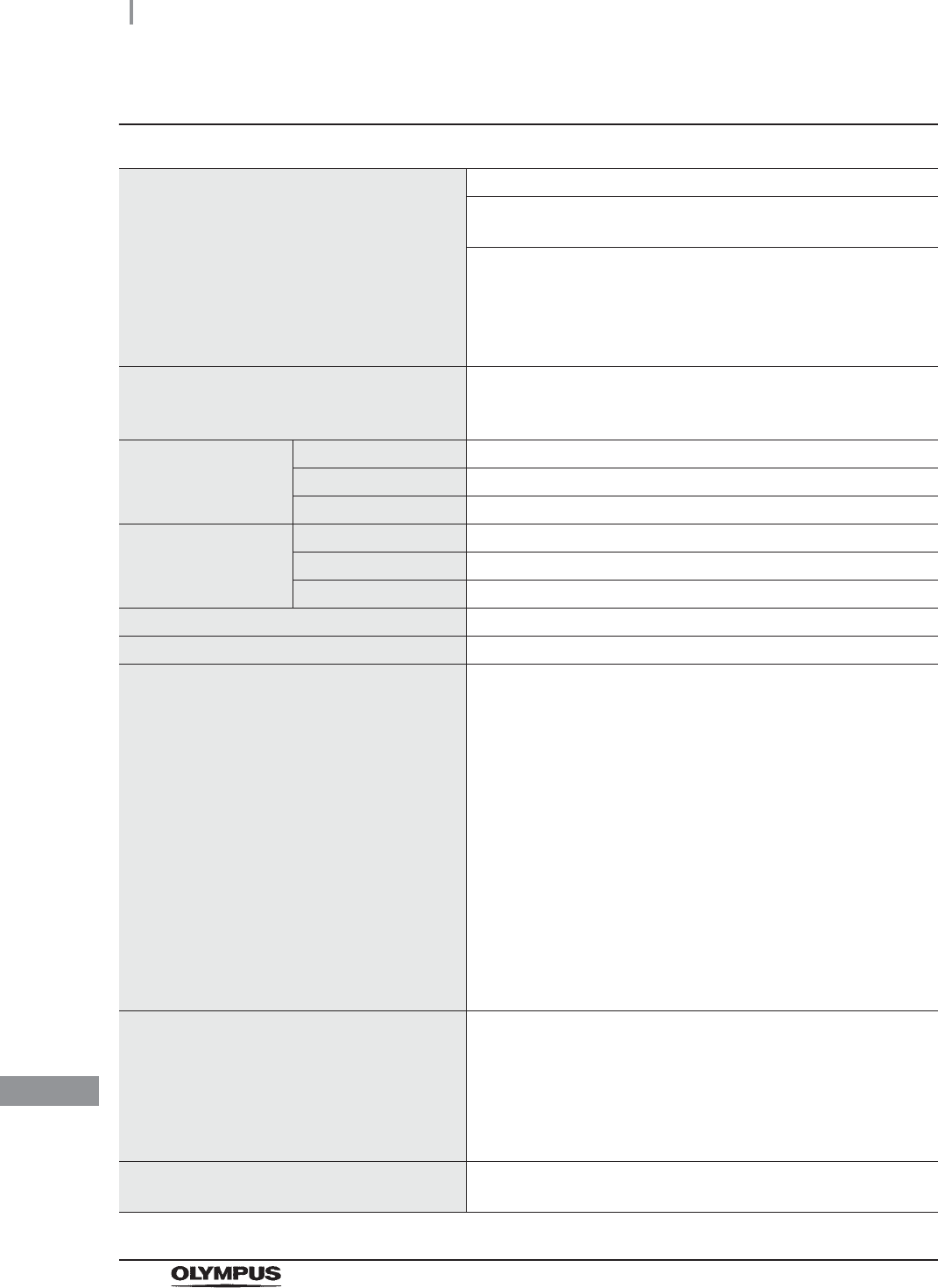
App.
650
Specifications
OER-Elite OPERATION MANUAL
Specifications
Compatible endoscopes Olympus flexible endoscopes
(Refer to the “List of Compatible Endoscopes/Connecting Tubes
<OER-Elite>” for details)
Note:
The OER-Elite does not sterilize endoscopes. Therefore, after
cleaning/disinfecting an endoscope that requires sterilization,
always sterilize the endoscope as instructed in its instruction
manual.
Number of reprocessed endoscopes Max. 2 (1 with certain models)
(Refer to the “List of Compatible Endoscopes/Connecting Tubes
<OER-Elite>” for combinations)
Cleaning method Exterior surfaces Ultrasonic cleaning, turbulent bath
Channel interiors Fluid flushing
Valves Ultrasonic cleaning, fluid flushing
Disinfection method Exterior surfaces Disinfectant solution immersion
Channel interiors Disinfectant solution flushing and filling
Valves Disinfectant solution immersion
Cleaning time setting 3 minutes
Disinfection time setting 7 minutes
Heat LCG setting Heating immediately before disinfection process in a reprocessing
program.
20qC (68qF)
(If the temperature of disinfectant solution is below 20qC, it is
heated to 20qC (68qF).)
Heating before the start of a reprocessing program.
22qC (72qF)
(If the temperature of disinfectant solution is below 20qC, it is
heated to 22qC (72qF).)
Heating by the timer.
22qC (72qF)
(If the temperature of disinfectant solution is below 20qC, it is
heated to 22qC (72qF).)
Heat LCG method Built-in heater in the disinfectant solution tank.
1 Heating before the start of a reprocessing program.
2 Heating by the timer.
Built-in heater in the reprocessing basin.
1 Heating immediately before disinfection process in a
reprocessing program.
Water discharge method Forced draining using a pump (The top of the drain hose should be
60 cm or less. A floor drain is recommended.)
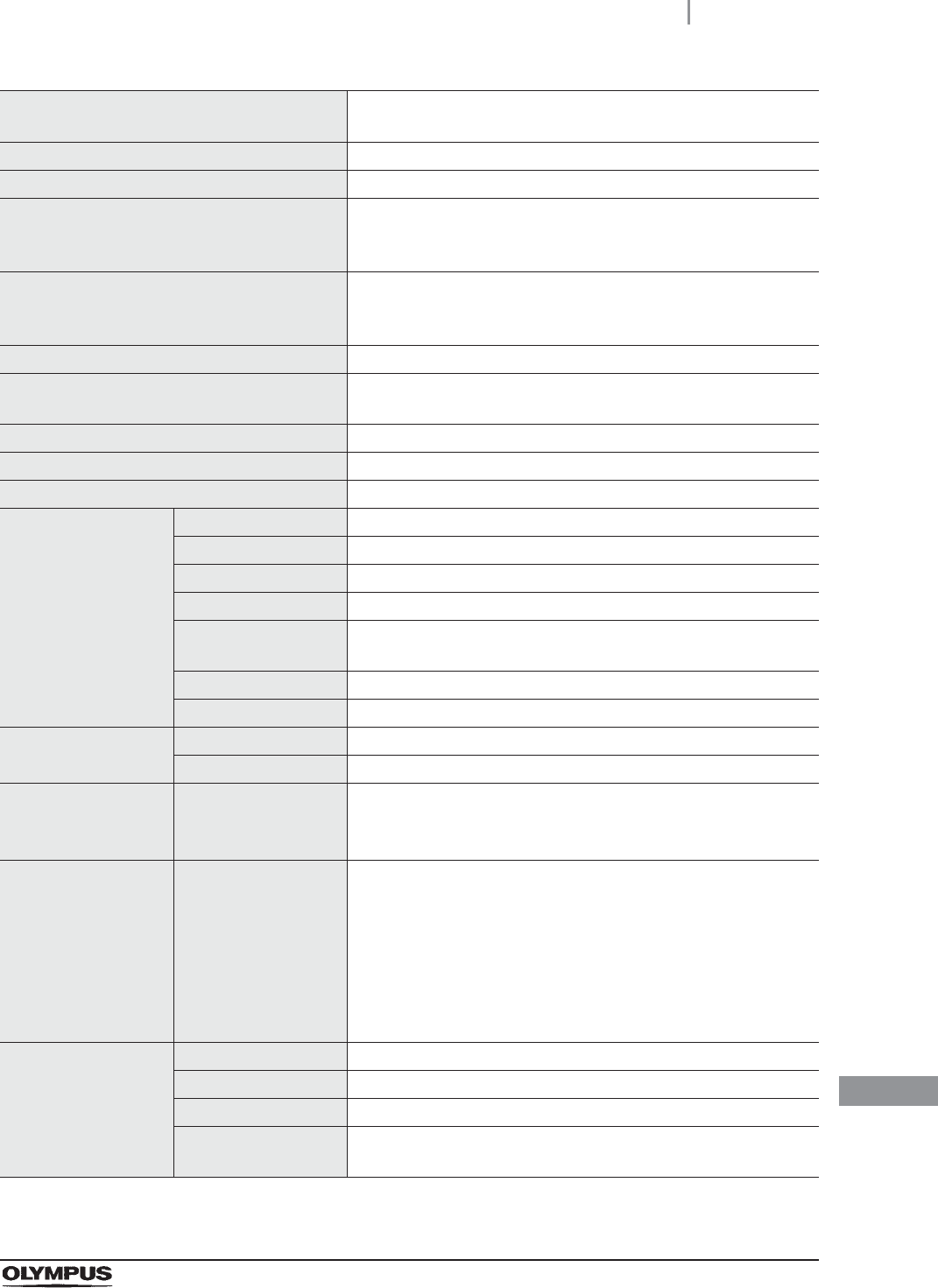
App.
Specifications
651
OER-Elite OPERATION MANUAL
Disinfectant solution discharge method 1 Draining through disinfectant collection hose
2 Draining through drain hose
Reprocessing basin capacity Approximately 17.9 L
Disinfectant solution tank capacity Approximately 21.1 L
Disinfectant solution Olympus-validated disinfectant solution
(Refer to Section 2.8, “Consumable accessories (Optional)” for
Olympus-validated disinfectant solution.)
Detergent Olympus-validated detergent
(Refer to Section 2.8, “Consumable accessories (Optional)” for
Olympus-validated disinfectant solution.)
Manual leak test Visual inspection of bubble during immersion.
Auto leak test Detects automatically for a pin hole by feeding air into the
endoscope and computing a changed air pressure.
Alcohol flush Automatic flushing/draining using a pump and compressor
Dimensions 500 (W) u 945 (H) u 774 (D) mm
Weight 133 kg (dry condition)
Power supply Voltage 120 V AC
Frequency 60 Hz
Rated input 660 VA
Voltage fluctuation Within r10
Frequency
fluctuation
Within r1Hz
Fuse rating 10 A, 250 V
Fuse size ø5 × 20 mm
Ultrasonic wave Frequency 36 r2kHz
Power 100 W
EMC Applied standard IEC 61326-1: 2012
• CISPR 11 of emission:
Group 1, Class B
Electrical safety Applied standard UL 61010-1: 2012
CSA C22.2 No. 61010-1: 2012
CSA C22.2 No. 61010-2-040: 2016
IEC 61010-1: 2010
IEC 61010-2-040: 2015
• Installation category: II
Pollution degree: 2
Radio transmitter Compliance ISO/IEC 18000-3 (Mode1)
Center frequency 13.56 MHz
Modulation ASK
Effective radiated
power 200 mWr20
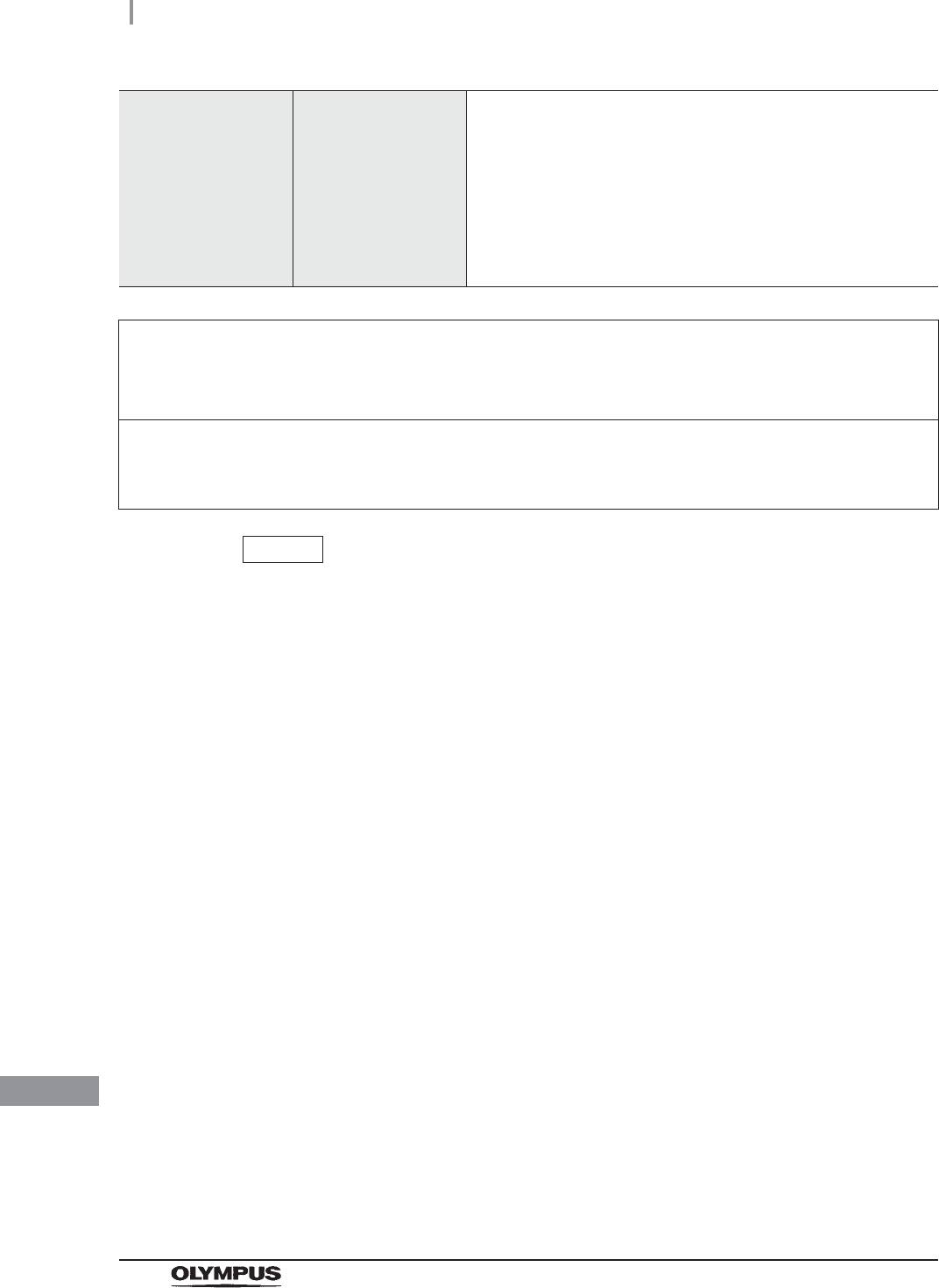
App.
652
Specifications
OER-Elite OPERATION MANUAL
NOTE
This equipment has been tested and found to comply with the limits for a Class B
digital device, pursuant to part 15 of the FCC Rules. These limits are designed to
provide reasonable protection against harmful interference in a residential
installation. This equipment generates, uses, and can radiate radio frequency
energy and, if not installed and used in accordance with the instructions, may
cause harmful interference to radio communications. However, there is no
guarantee that interference will not occur in a particular installation. If this
equipment does cause harmful interference to radio or television reception, which
can be determined by turning the equipment off and on, the user is encouraged to
try to correct the interference by one or more of the following measures:
Reorient or relocate the receiving antenna.
Increase the separation between the equipment and receiver.
Connect the equipment into an outlet on a circuit different from that to which the
receiver is connected.
Consult the dealer or an experienced radio/TV technician for help.
UDI label Indication A label required by some countries’ regulations regarding
identification of medical device also known as Unique Device
Identification (UDI).
The following information is being coded in the 2-dimensional
barcode (GS1 Date Matrix):
(01) 14-digit GS1 Global Trade Item Number;
(11) 6-digit date of manufacture;
(21) 7-digit serial number.
FCC and IC information
This equipment complies with part15 of the FCC rules and the IC RSS210. FCC ID: S8Q-RU2020
IC: 4763B-RU2020
FCC WARNING
Change or modifications not expressly approved by the party responsible for compliance could void the user’s
authority to operate the equipment.
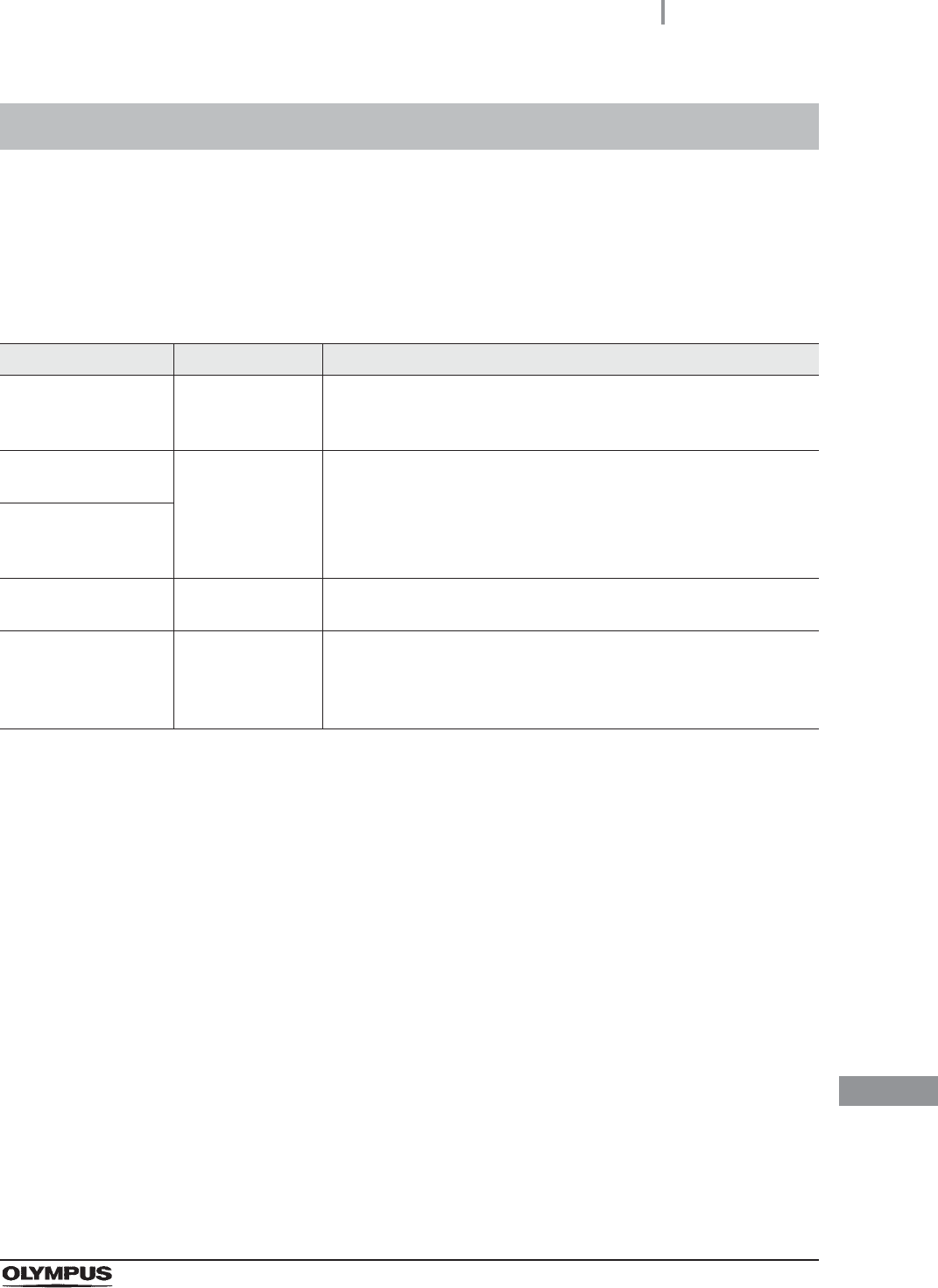
App.
EMC information
653
OER-Elite OPERATION MANUAL
Guidance and manufacturer’s declaration — Electromagnetic
emissions
This model is intended for use in the electromagnetic environment specified below. The
customer or the user of this model should assure that it is used in such an environment.
EMC information
Emissions test Compliance Electromagnetic environment — Guidance
RF emissions
CISPR 11
Group 1 This instrument uses RF (Radio Frequency) energy only for its
internal function. Therefore, its RF emissions are very low and are not
likely to cause any interference in nearby electronic equipment.
Radiated emissions
CISPR 11
Class B This instrument’s RF emissions are very low and are not likely to
cause any interference in nearby electronic equipment.
Main terminal
conducted emissions
CISPR 11
Harmonic emissions
IEC 61000-3-2
Not applicable Power supply specification of this instrument is less than 220 VAC,
and this instrument is exempt from requirements of IEC 61000-3-2.
Voltage
fluctuations/flicker
emissions
IEC 61000-3-3
Not applicable Power supply specification of this instrument is less than 220 VAC,
and this instrument is exempt from requirements of IEC 61000-3-3.
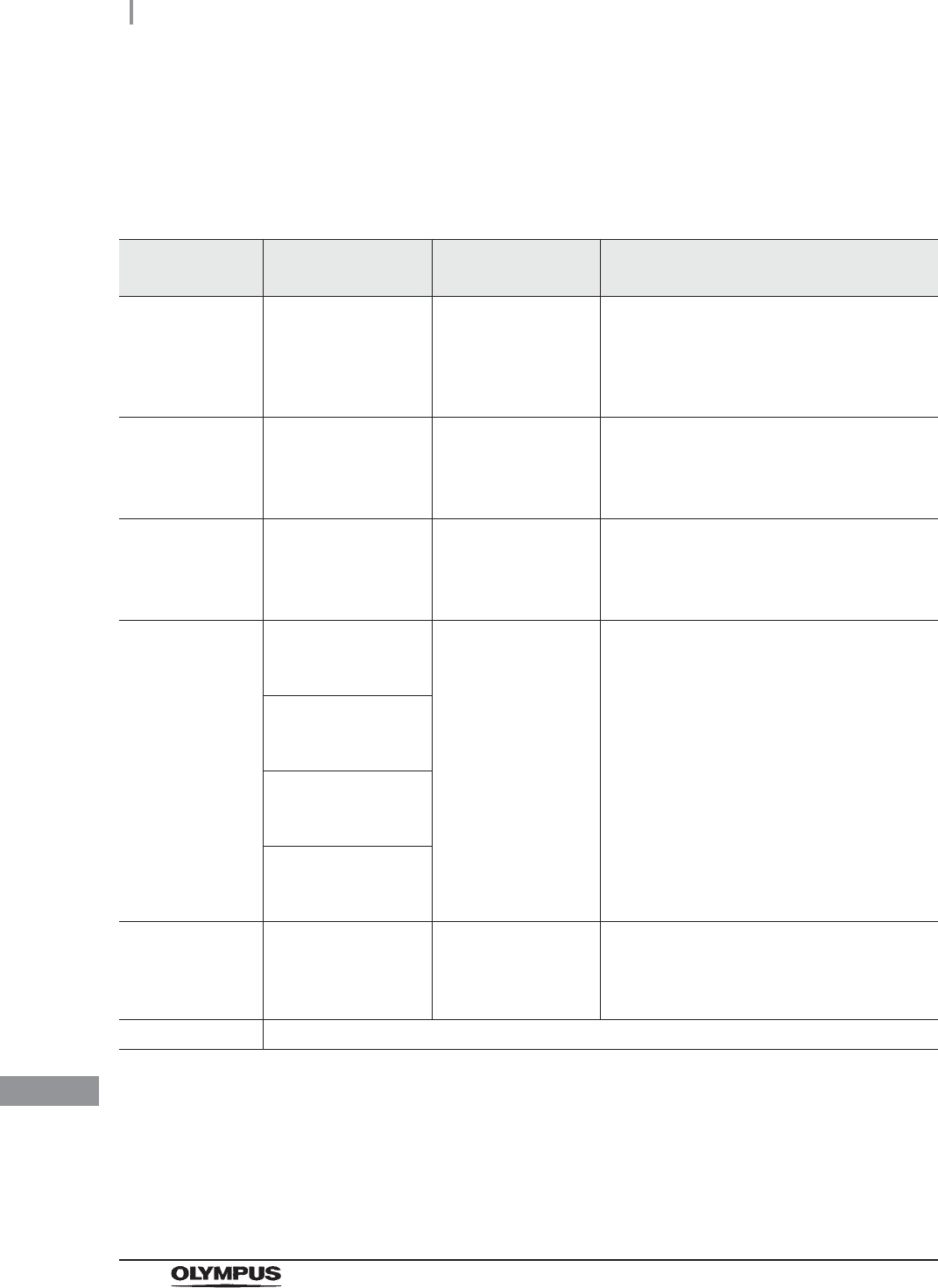
App.
654
EMC information
OER-Elite OPERATION MANUAL
Guidance and manufacturer’s declaration — Electromagnetic
immunity
This model is intended for use in the electromagnetic environment specified below. The
customer or the user of this model should assure that it is used in such an environment.
Immunity test IEC 61326-1
test level Compliance level Electromagnetic environment —
Guidance
Electrostatic
discharge (ESD)
IEC 61000-4-2
Contact:
r2, r4kV
Air:
r2, r4, r8kV
Same as left Floors should be made of wood, concrete, or
ceramic tile that hardly produces static. If
floors are covered with synthetic material that
tends to produce static, the relative humidity
should be at least 30%.
Electrical fast
transient/burst
IEC 61000-4-4
r2kV
for power supply lines
r1kV
for input/output lines
Same as left Mains power quality should be that of a typical
commercial (original condition feeding the
facilities) or hospital environment.
Surge
IEC 61000-4-5
Differential mode:
r1kV
Common mode:
r1, r2kV
Same as left Mains power quality should be that of a typical
commercial or hospital environment.
Voltage dips, short
interruptions, and
voltage variations
on power supply
input lines
IEC 61000-4-11
0% UT
(100% dip in UT)
for 1 cycle
Same as left Mains power quality should be that of a typical
commercial or hospital environment. If the
user of this instrument requires continued
operation during power mains interruptions, it
is recommended that this instrument be
powered from an uninterruptible power supply
or a battery.
40% UT
(60% dip in UT)
for 200 ms
70% UT
(30% dip in UT)
for 500 ms
0% UT
(100% dip in UT)
for 5 seconds
Power frequency
(50/60 Hz)
magnetic field
IEC 61000-4-8
30 A/m Same as left It is recommended to use this instrument by
maintaining enough distance from any
equipment that operates with high current.
Definition UT is the a.c. mains voltage prior to application of the test level.
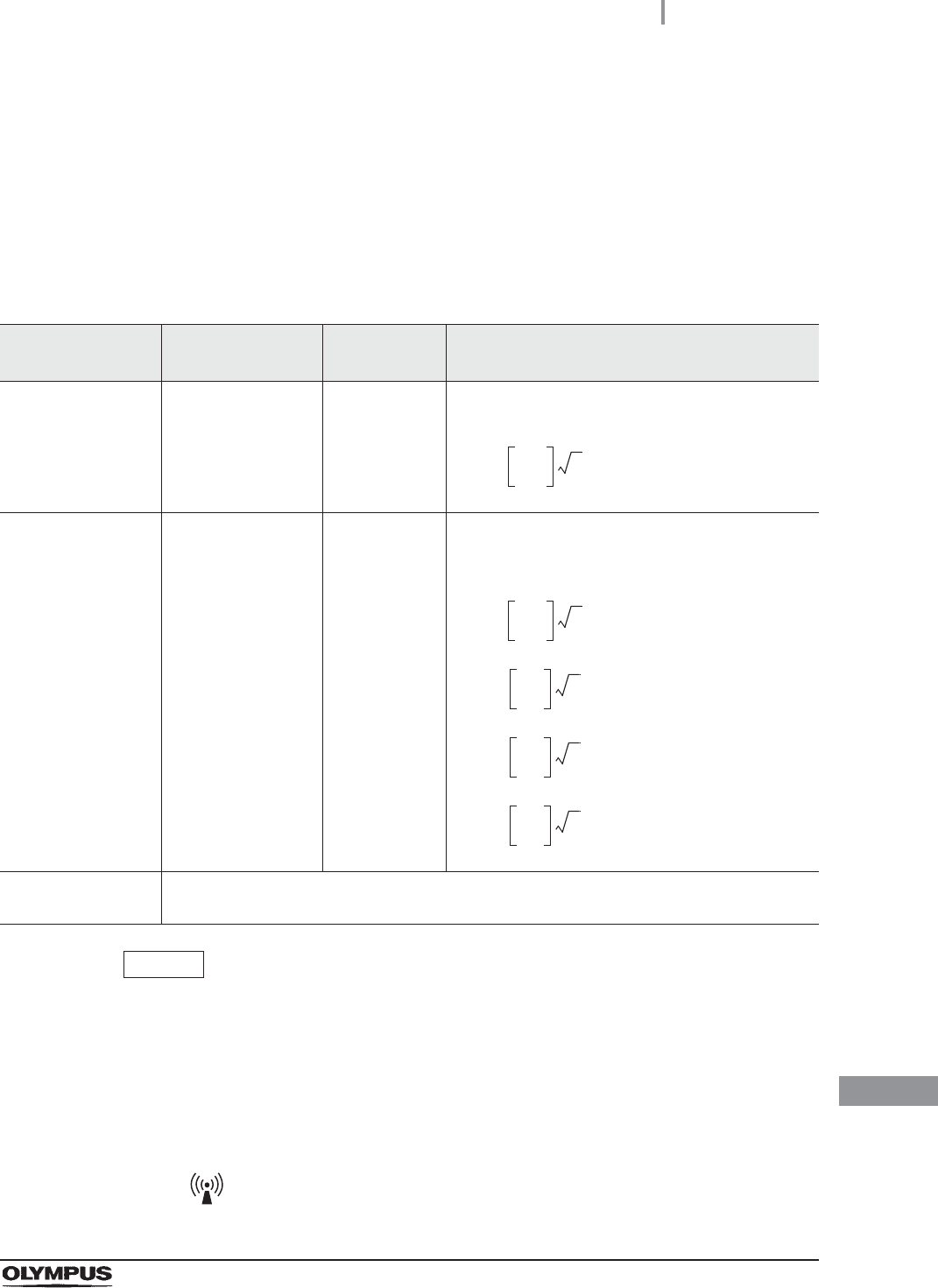
App.
EMC information
655
OER-Elite OPERATION MANUAL
Guidance and manufacturer’s declaration — Electromagnetic
immunity
This model is intended for use in the electromagnetic environment specified below. The
customer or the user of this model should assure that it is used in such an environment.
Portable and mobile RF communications equipment should be used no closer to any part of this
model, including cables, than the recommended separation distance calculated from the
equation applicable to the frequency of the transmitter.
NOTE
• At 80 MHz and 800 MHz, the higher frequency range applies.
• These guidelines may not apply in all situations. Electromagnetic propagation is
affected by absorption and reflection from structures, objects and people.
• Electromagnetic interference may occur in the vicinity of high-frequency
electrosurgical equipment and/or other equipment marked with the following
symbol:
Immunity test IEC 61326-1
test level
Compliance
level Electromagnetic environment — Guidance
Recommended separation distance
(V1=3 according to the compliance level)
Conducted RF
IEC 61000-4-6
3 Vrms
(150 kHz – 80 MHz)
3V (V
1)
Recommended separation distance
(E1=10, E2=3, E3=1 according to the compliance
level)
Radiated RF
IEC 61000-4-3
10V/m
(80MHz – 1GHz)
3V/m
(1.4 GHz – 2 GHz)
1V/m
(2 GHz – 2.7 GHz)
10 V/m (E1)
3 V/m (E2)
1 V/m (E3)80 MHz – 800 MHz
800 MHz – 1 GHz
1.4 GHz – 2 GHz
2GHz – 2.7GHz
Definition Where “P” is the maximum output power rating of the transmitter in watts (W) according to
the transmitter manufacturer and “d” is the recommended separation distance in meters (m).
d3.5
V1
------- P=
d3.5
E1
------- P=
d7
E1
------P=
d7
E2
------P=
d7
E3
------P=
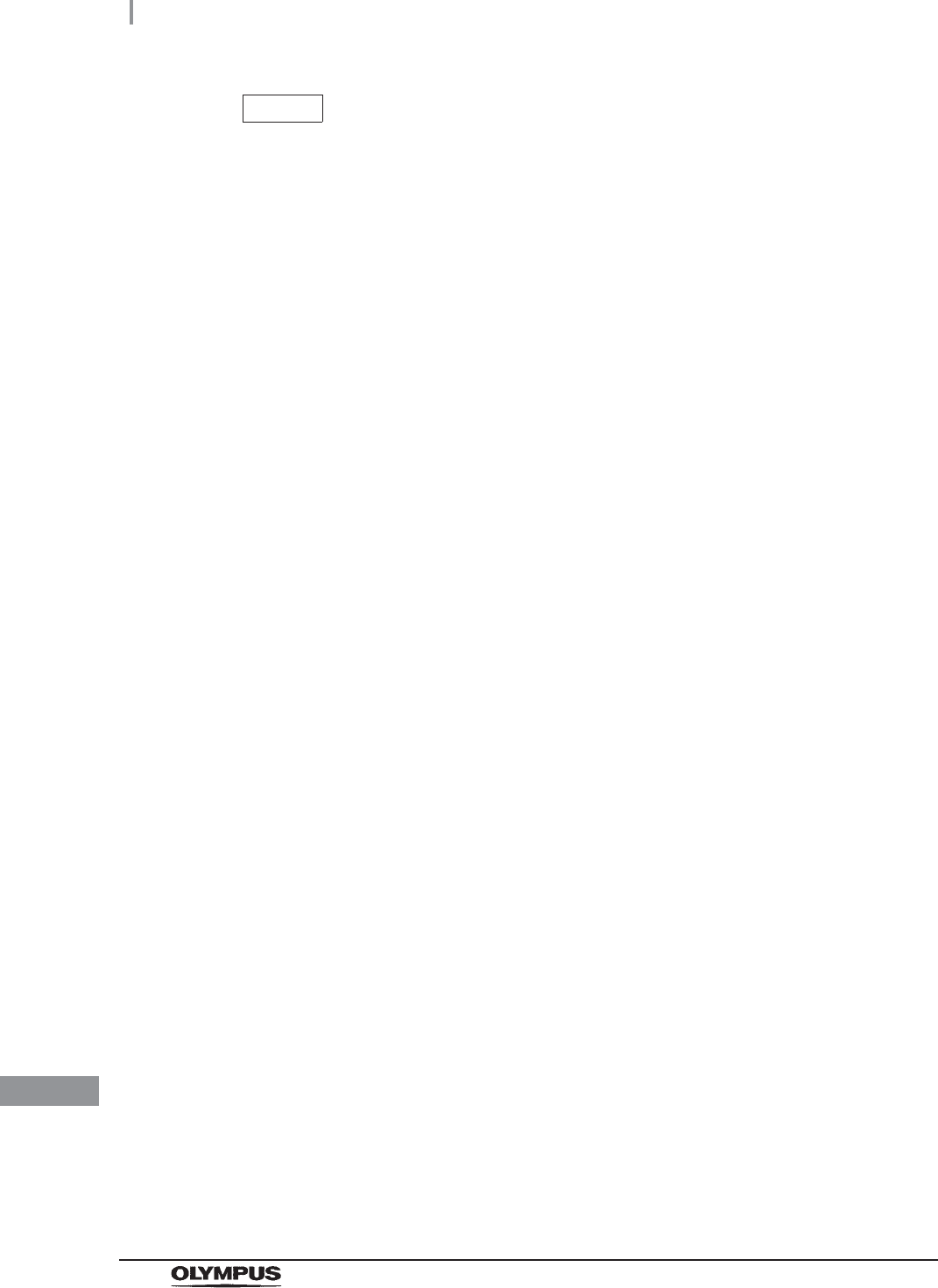
App.
656
EMC information
OER-Elite OPERATION MANUAL
NOTE
• Field strength from fixed RF transmitters as determined by an electromagnetic site
surveya) should be less than the compliance level in each frequency rangeb).
a) Field strength from fixed transmitters, such as base stations for radio
(cellular/cordless) telephones and land mobile radios, amateur radio, AM
and FM radio broadcast and TV broadcast cannot be predicted theoretically
with accuracy. To assess the electromagnetic environment due to fixed RF
transmitters, an electromagnetic site survey should be considered. If the
measured field strength in the location in which this model is used exceeds
the applicable RF compliance level above, this model should be observed to
verify normal operation. If abnormal performance is observed, additional
measures may be necessary, such as re-orienting or relocating this model.
b) Over the frequency range 150 kHz to 80 MHz, field strength should be less
than 3 V/m.
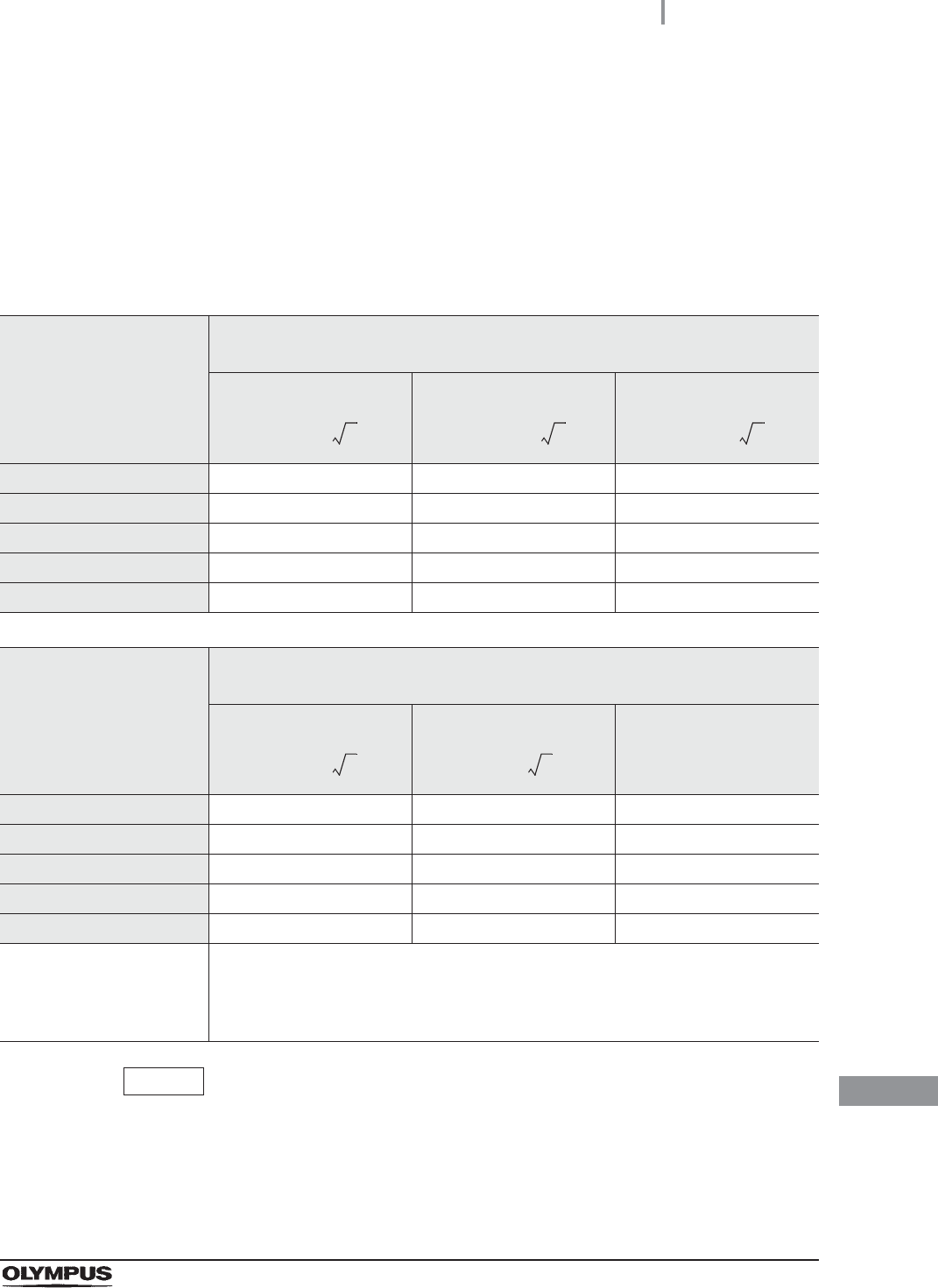
App.
EMC information
657
OER-Elite OPERATION MANUAL
Recommended separation distances between portable and
mobile RF communications equipment and this model
This model is intended for use in an electromagnetic environment in which radiated RF
disturbances are controlled. The customer or the user of this model can help prevent
electromagnetic interference by maintaining a minimum distance between portable and mobile
RF communications equipment (transmitters) and this model as recommended below, according
to the maximum output power of the communications equipment.
NOTE
• At 80 MHz and 800 MHz, the separation distance for the higher frequency range
applies.
• These guidelines may not apply in all situations. Electromagnetic propagation is
affected by absorption and reflection from structures, objects and people.
Rated maximum output
power of transmitter
P (W)
Separation distance according to frequency of transmitter (m)
(calculated as V1=3, E1=10, E2=3 and E3=1)
150 kHz – 80 MHz 80 MHz – 800 MHz 800MHz – 1GHz
0.01 0.12 0.04 0.07
0.1 0.38 0.12 0.23
11.2 0.35 0.70
10 3.8 1.2 2.3
100 12 3.5 7
Rated maximum output
power of transmitter
P (W)
Separation distance according to frequency of transmitter (m)
(calculated as V1=3, E1=10, E2=3 and E3=1)
1.4 GHz – 2 GHz 2 GHz – 2.7 GHz
0.01 0.24 0.7
0.1 0.76 2.3
12.4 7
10 7.6 23
100 24 70
Others For transmitters rated at a maximum output power not listed above, the recommended
separation distance ‘d’ in metres (m) can be estimated using the equation applicable
to the frequency of the transmitter, where ‘p’ is the maximum output power rating of
the transmitter in watts (W) according to the transmitter manufacturer.
d1.2 P=
d0.35 P=
d0.7 P=
d2.4 P=
d7P=
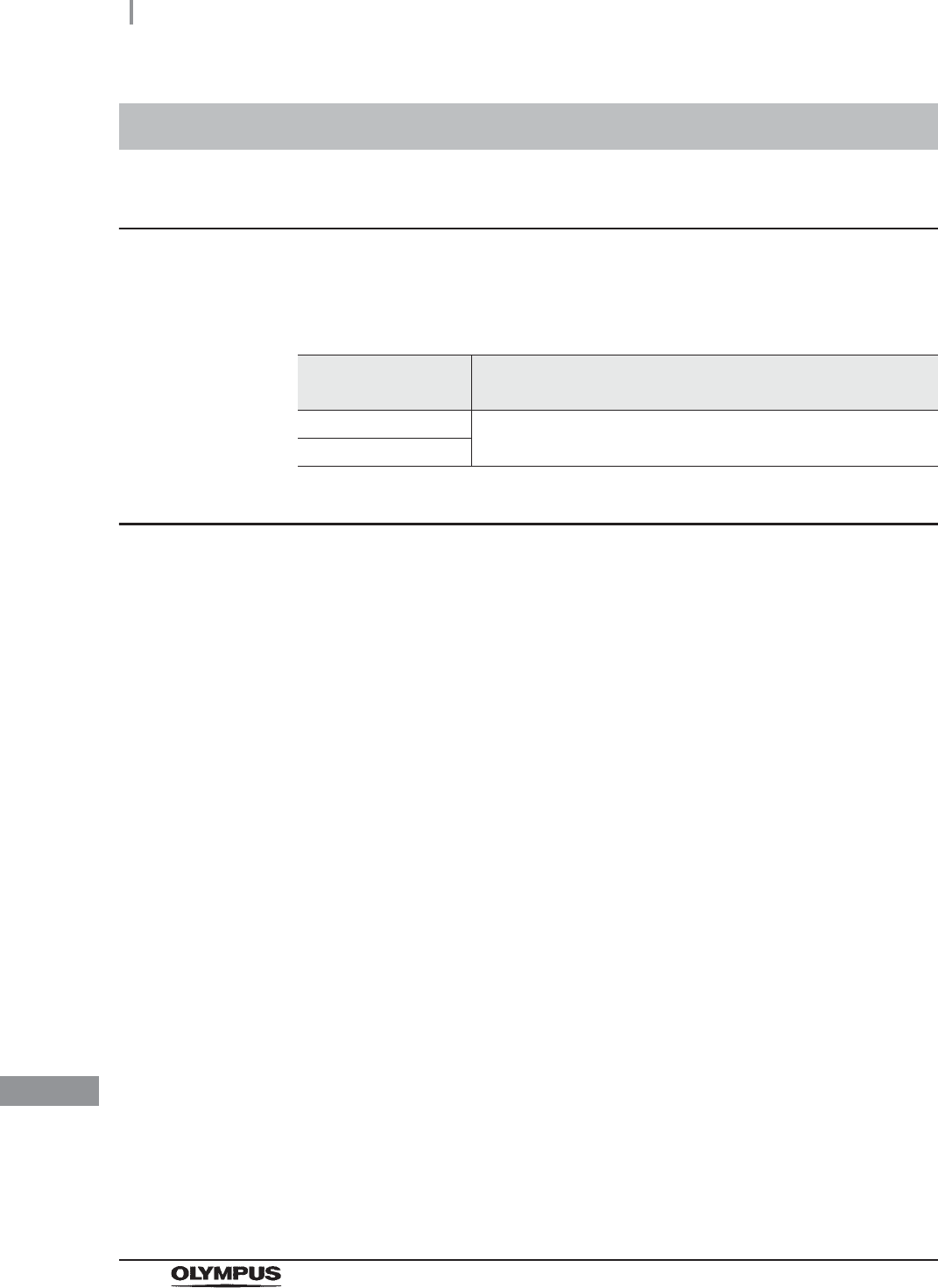
App.
658
License information of Open Source Software
OER-Elite OPERATION MANUAL
GNU GPL
This product uses software modules licensed under the terms of the GNU GENERAL PUBLIC
LICENSE(“GPL”).
Please see the following table for the software module made the target.
z
End User License Agreement of Open Source Software modules
This section must not be translated by any language and must not be changed from original text.
Because these license description must be described original description in English according to these
license.
GNU GENERAL PUBLIC LICENSE Version 2 with Exception
About libgcc and libstdc++, those are licensed under the terms of the GNU GENERAL PUBLIC LICENSE
Version 2 with special exception or additional permission to show in the following.
a) libstdc++
The libstdc++ source code is distributed under the GNU General Public License version 2, with the
so-called “Runtime Exception” as follows (or see any header or implementation file).
As a special exception, you may use this file as part of a free software library without restriction.
Specifically, if other files instantiate templates or use macros or inline functions from this file, or you
compile this file and link it with other files to produce an executable, this file does not by itself cause the
resulting executable to be covered by the GNU General Public License. This exception does not however
invalidate any other reasons why the executable file might be covered by the GNU General Public License.
b) libgcc
GCC is free software; you can redistribute it and/or modify it under the terms of the GNU General Public
License as published by the Free Software Foundation; either version 2, or (at your option) any later
version.
License information of Open Source Software
Software modules
concerned End User License Agreement of software modules
libgcc GNU GENERAL PUBLIC LICENSE Version 2 with Exception
libstdc++
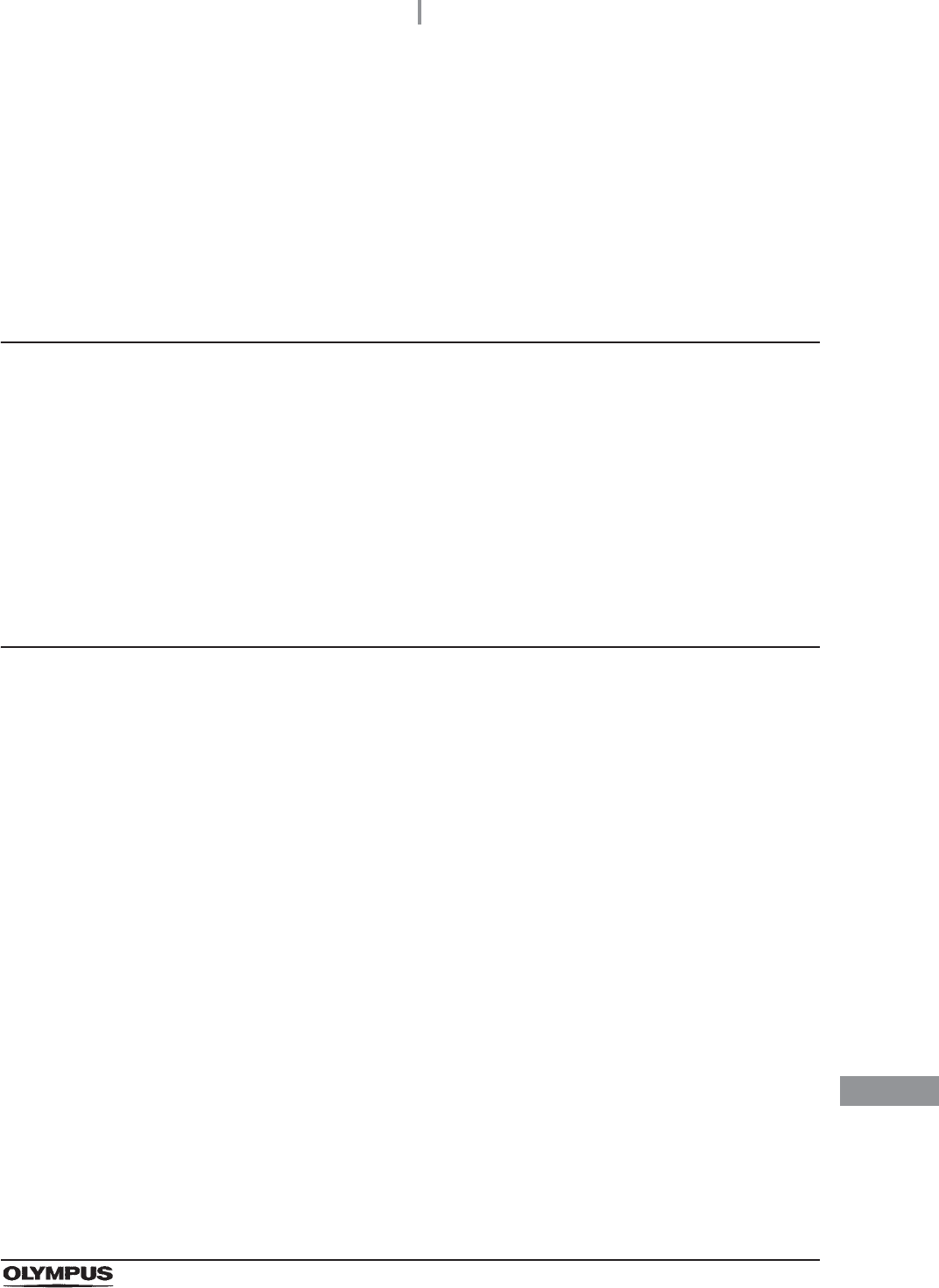
App.
License information of Open Source Software
659
OER-Elite OPERATION MANUAL
In addition to the permissions in the GNU General Public License, the Free Software Foundation gives you
unlimited permission to link the compiled version of this file into combinations with other programs, and to
distribute those combinations without any restriction coming from the use of this file. (The General Public
License restrictions do apply in other respects; for example, they cover modification of the file, and
distribution when not linked into a combined executable.) GCC is distributed in the hope that it will be
useful, but WITHOUT ANY WARRANTY; without even the implied warranty of MERCHANTABILITY or
FITNESS FOR A PARTICULAR PURPOSE. See the GNU General Public License for more details.
Others
• This instrument contains software modules which are not licensed under the terms of GPL. This section
must not be translated by any language and must not be changed from original text. Because these
license description must be described original description in English according to these license.
• The Licensed Software may include (i) some open source software and (ii) other third party software
(collectively, “Third Party Software”). Regarding the use of the Third Party Software, you shall follow the
license terms and conditions applied to such Third Party Software. Any part of this License Agreement
does not restrict, change or alter any of your rights and obligations imposed by the license terms and
conditions of the Third Party Software.
newlib
This product uses the open source software program “newlib” which applies the terms and conditions
provided by owner of the copyright to the “newlib”.
The newlib subdirectory is a collection of software from several sources.
Each file may have its own copyright/license that is embedded in the source file.
(1) Red Hat Incorporated
Copyright (c) 1994-2007 Red Hat, Inc. All rights reserved.
This copyrighted material is made available to anyone wishing to use, modify, copy, or redistribute it
subject to the terms and conditions of the BSD License. This program is distributed in the hope that it will
be useful, but WITHOUT ANY WARRANTY expressed or implied, including the implied warranties of
MERCHANTABILITY or FITNESS FOR A PARTICULAR PURPOSE. A copy of this license is available at
http://www.opensource.org/licenses. Any Red Hat trademarks that are incorporated in the source code or
documentation are not subject to the BSD License and may only be used or replicated with the express
permission of Red Hat, Inc.
(2) University of California, Berkeley
Copyright (c) 1981-2000 The Regents of the University of California.
All rights reserved.
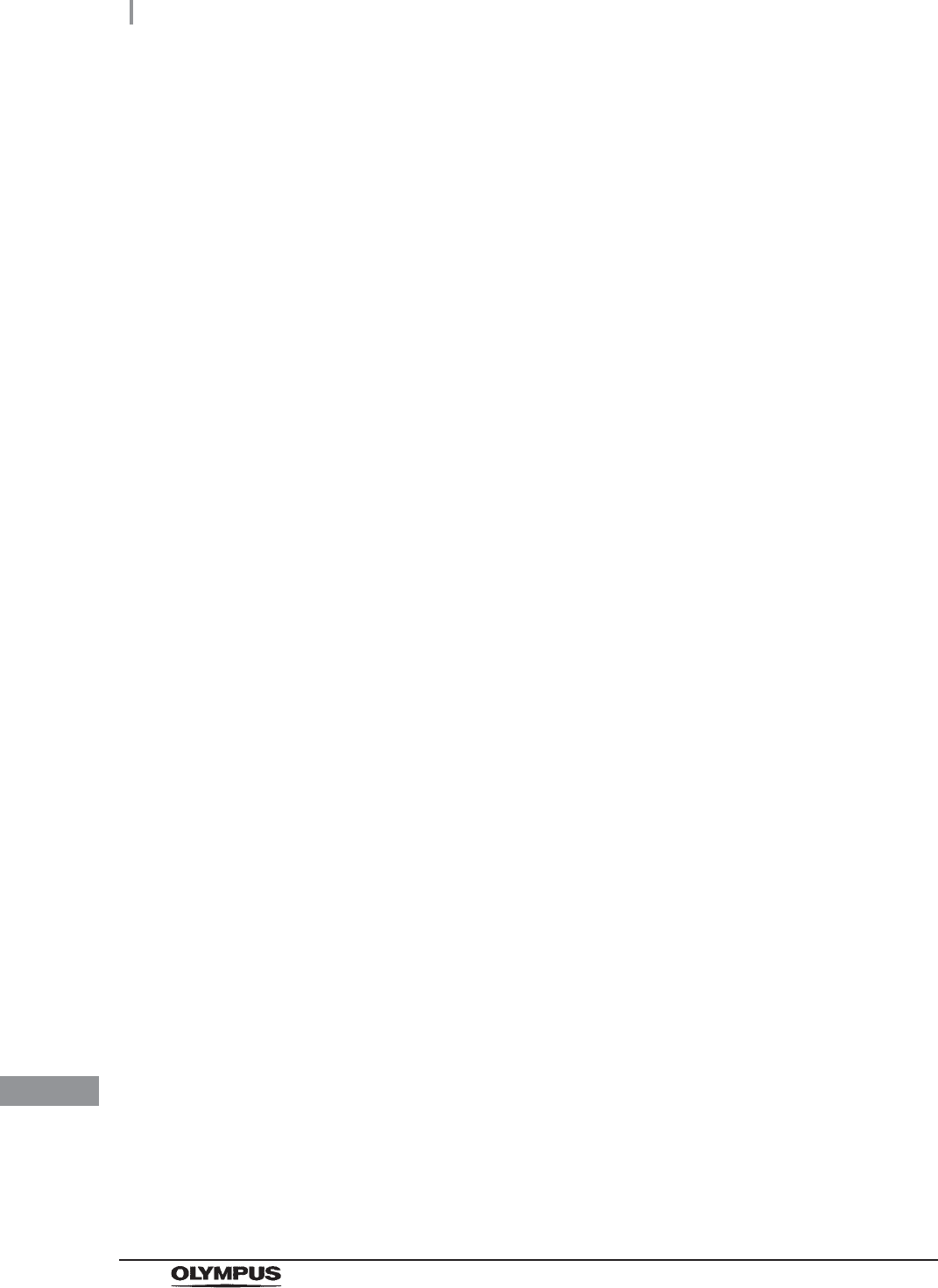
App.
660
License information of Open Source Software
OER-Elite OPERATION MANUAL
Redistribution and use in source and binary forms, with or without modification, are permitted provided that
the following conditions are met:
* Redistributions of source code must retain the above copyright notice, this list of conditions and the
following disclaimer.
* Redistributions in binary form must reproduce the above copyright notice, this list of conditions and the
following disclaimer in the documentation and/or other materials provided with the distribution.
* Neither the name of the University nor the names of its contributors may be used to endorse or promote
products derived from this software without specific prior written permission.
THIS SOFTWARE IS PROVIDED BY THE COPYRIGHT HOLDERS AND CONTRIBUTORS “AS IS” AND
ANY EXPRESS OR IMPLIED WARRANTIES, INCLUDING, BUT NOT LIMITED TO, THE IMPLIED
WARRANTIES OF MERCHANTABILITY AND FITNESS FOR A PARTICULAR PURPOSE ARE
DISCLAIMED.
IN NO EVENT SHALL THE COPYRIGHT OWNER OR CONTRIBUTORS BE LIABLE FOR ANY DIRECT,
INDIRECT, INCIDENTAL, SPECIAL, EXEMPLARY, OR CONSEQUENTIAL DAMAGES (INCLUDING,
BUT NOT LIMITED TO, PROCUREMENT OF SUBSTITUTE GOODS OR SERVICES; LOSS OF USE,
DATA, OR PROFITS; OR BUSINESS INTERRUPTION) HOWEVER CAUSED AND ON ANY THEORY
OF LIABILITY, WHETHER IN CONTRACT, STRICT LIABILITY, OR TORT (INCLUDING NEGLIGENCE
OR OTHERWISE) ARISING IN ANY WAY OUT OF THE USE OF THIS SOFTWARE, EVEN IF ADVISED
OF THE POSSIBILITYOF SUCH DAMAGE.
(3) David M. Gay at AT&T
The author of this software is David M. Gay.
Copyright (c) 1991 by AT&T.
Permission to use, copy, modify, and distribute this software for any purpose without fee is hereby granted,
provided that this entire notice is included in all copies of any software which is or includes a copy or
modification of this software and in all copies of the supporting documentation for such software.
THIS SOFTWARE IS BEING PROVIDED “AS IS”, WITHOUT ANY EXPRESS OR IMPLIED WARRANTY.
IN PARTICULAR, NEITHER THE AUTHOR NOR AT&T MAKES ANY REPRESENTATION OR
WARRANTY OF ANY KIND CONCERNING THE MERCHANTABILITY OF THIS SOFTWARE OR ITS
FITNESS FOR ANY PARTICULAR PURPOSE.
-------------------------------------------------------------------
The author of this software is David M. Gay.
Copyright (C) 1998-2001 by Lucent Technologies
All Rights Reserved
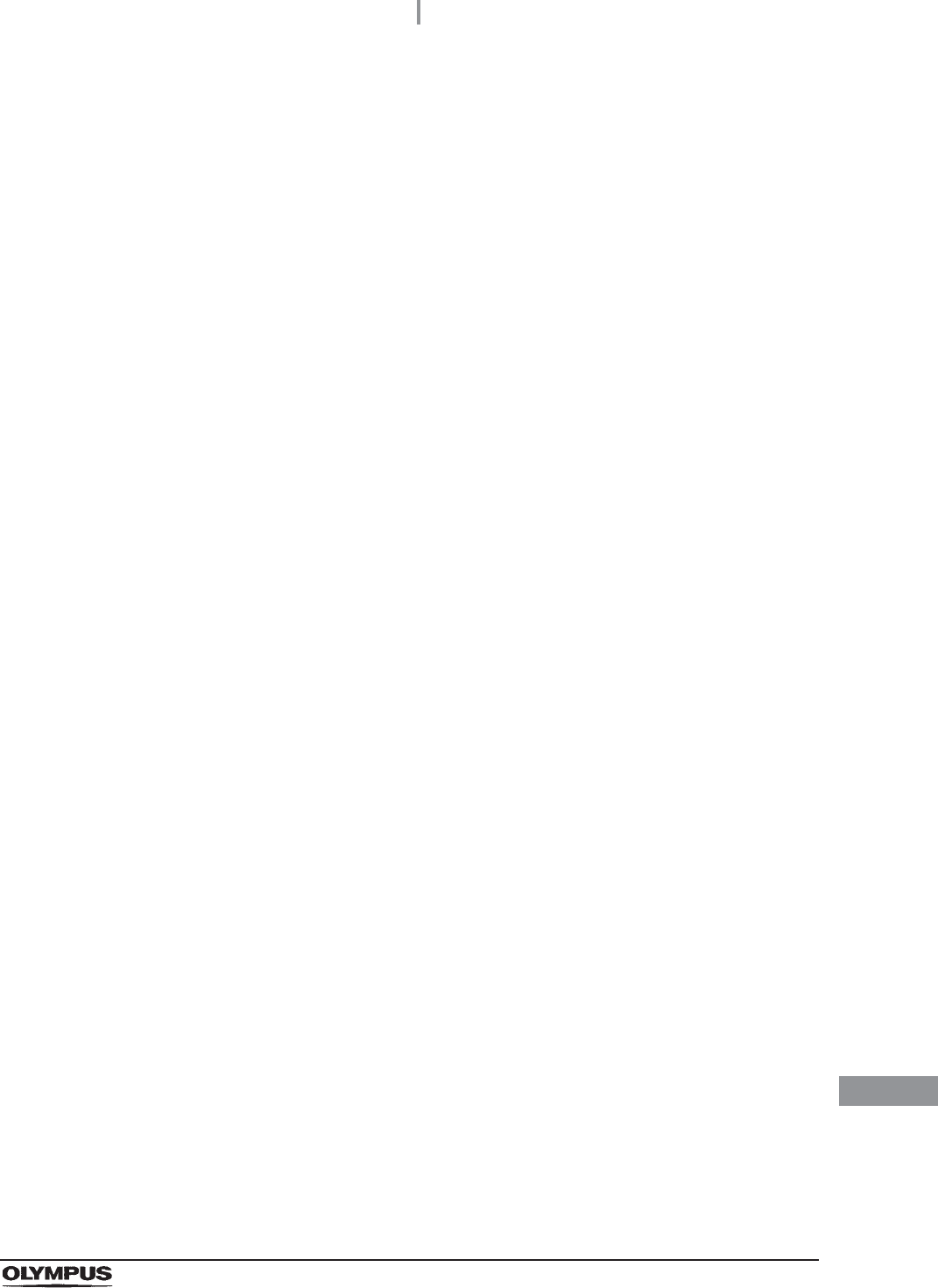
App.
License information of Open Source Software
661
OER-Elite OPERATION MANUAL
Permission to use, copy, modify, and distribute this software and its documentation for any purpose and
without fee is hereby granted, provided that the above copyright notice appear in all copies and that both
that the copyright notice and this permission notice and warranty disclaimer appear in supporting
documentation, and that the name of Lucent or any of its entities not be used in advertising or publicity
pertaining to distribution of the software without specific, written prior permission.
LUCENT DISCLAIMS ALL WARRANTIES WITH REGARD TO THIS SOFTWARE, INCLUDING ALL
IMPLIED WARRANTIES OF MERCHANTABILITY AND FITNESS.
IN NO EVENT SHALL LUCENT OR ANY OF ITS ENTITIES BE LIABLE FOR ANY SPECIAL, INDIRECT
OR CONSEQUENTIAL DAMAGES OR ANY DAMAGES WHATSOEVER RESULTING FROM LOSS OF
USE, DATA OR PROFITS, WHETHER IN AN ACTION OF CONTRACT, NEGLIGENCE OR OTHER
TORTIOUS ACTION, ARISING OUT OF OR IN CONNECTION WITH THE USE OR PERFORMANCE OF
THIS SOFTWARE.
(4) Advanced Micro Devices
Copyright 1989, 1990 Advanced Micro Devices, Inc.
This software is the property of Advanced Micro Devices, Inc (AMD) which specifically grants the user the
right to modify, use and distribute this software provided this notice is not removed or altered. All other
rights are reserved by AMD.
AMD MAKES NO WARRANTY OF ANY KIND, EXPRESS OR IMPLIED, WITH REGARD TO THIS
SOFTWARE. IN NO EVENT SHALL AMD BE LIABLE FOR INCIDENTAL OR CONSEQUENTIAL
DAMAGES IN CONNECTION WITH OR ARISING FROM THE FURNISHING, PERFORMANCE, OR USE
OF THIS SOFTWARE.
So that all may benefit from your experience, please report any problems or suggestions about this
software to the 29K Technical Support Center at 800-29-29-AMD (800-292-9263) in the USA, or
0800-89-1131 in the UK, or 0031-11-1129 in Japan, toll free. The direct dial number is 512-462-4118.
Advanced Micro Devices, Inc.
29K Support Products
Mail Stop 573
5900 E. Ben White Blvd.
Austin, TX 78741
800-292-9263
(5) C.W. Sandmann
Copyright (C) 1993 C.W. Sandmann
This file may be freely distributed as long as the author's name remains.
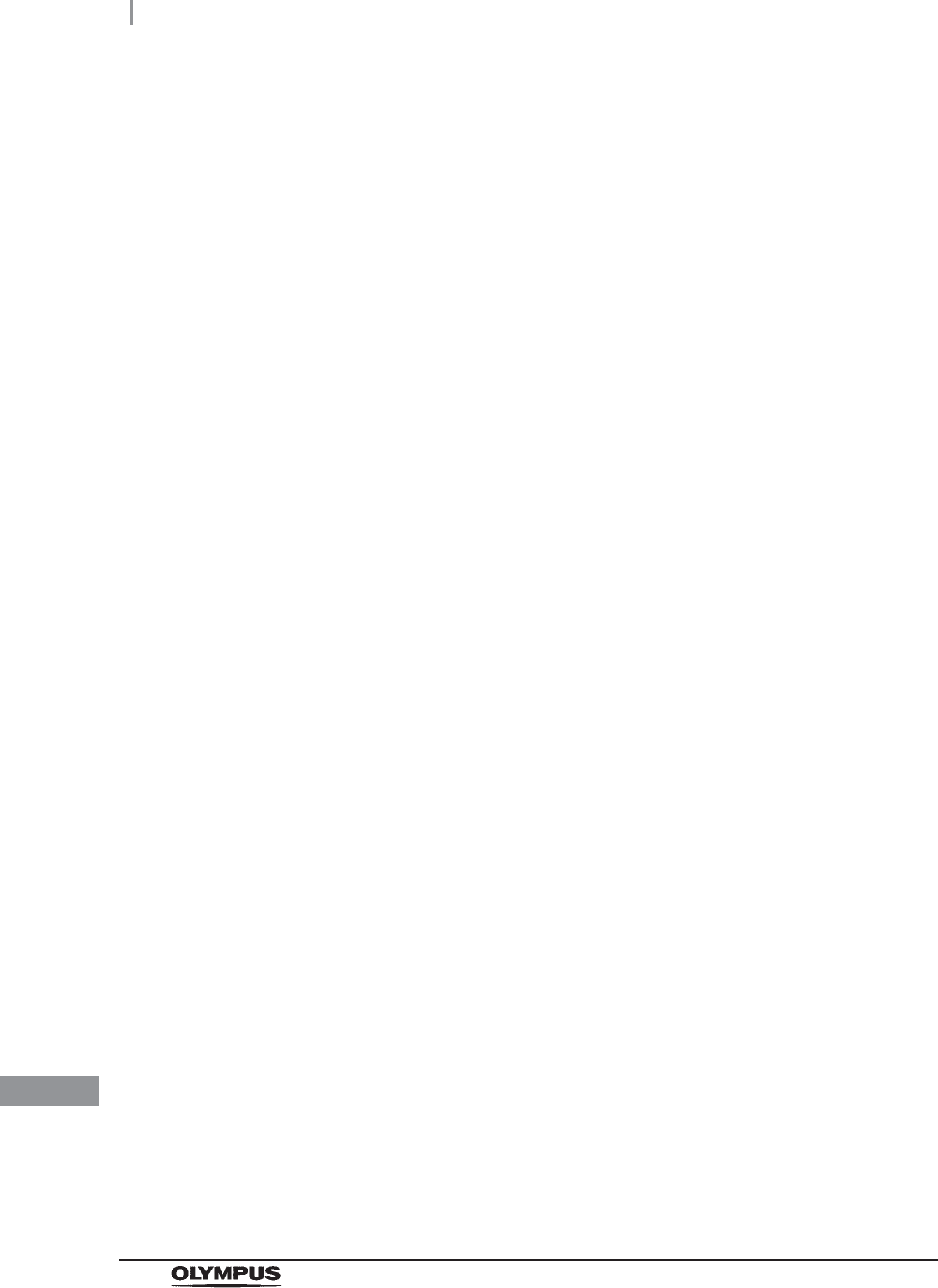
App.
662
License information of Open Source Software
OER-Elite OPERATION MANUAL
(6) Eric Backus
(C) Copyright 1992 Eric Backus
This software may be used freely so long as this copyright notice is left intact.
There is no warrantee on this software.
(7) Sun Microsystems
Copyright (C) 1993 by Sun Microsystems, Inc. All rights reserved.
Developed at SunPro, a Sun Microsystems, Inc. business.
Permission to use, copy, modify, and distribute this software is freely granted, provided that this notice is
preserved.
(8) Hewlett Packard
(c) Copyright 1986 HEWLETT-PACKARD COMPANY
To anyone who acknowledges that this file is provided “AS IS” without any express or implied warranty:
permission to use, copy, modify, and distribute this file for any purpose is hereby granted without fee,
provided that the above copyright notice and this notice appears in all copies, and that the name of
Hewlett-Packard Company not be used in advertising or publicity pertaining to distribution of the software
without specific, written prior permission.
Hewlett-Packard Company makes no representations about the suitability of this software for any purpose.
(9) Hans-Peter Nilsson
Copyright (C) 2001 Hans-Peter Nilsson
Permission to use, copy, modify, and distribute this software is freely granted, provided that the above
copyright notice, this notice and the following disclaimer are preserved with no changes.
THIS SOFTWARE IS PROVIDED “AS IS” AND WITHOUT ANY EXPRESS OR IMPLIED WARRANTIES,
INCLUDING, WITHOUT LIMITATION, THE IMPLIED WARRANTIES OF MERCHANTABILITY AND
FITNESS FOR A PARTICULAR PURPOSE.
(11) Christopher G. Demetriou
Copyright (c) 2001 Christopher G. Demetriou
All rights reserved.
Redistribution and use in source and binary forms, with or without modification, are permitted provided that
the following conditions are met:
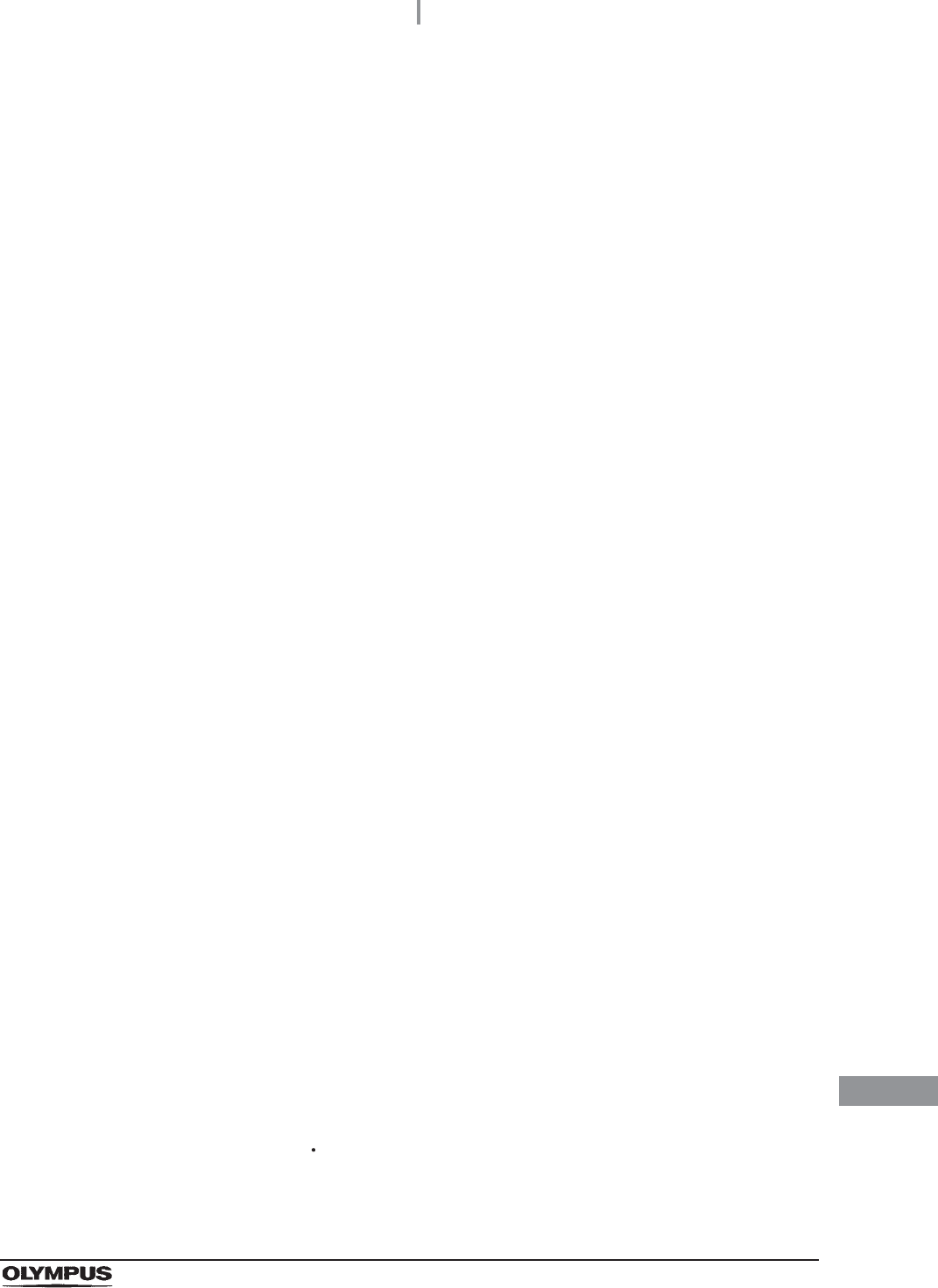
App.
License information of Open Source Software
663
OER-Elite OPERATION MANUAL
1. Redistributions of source code must retain the above copyright notice, this list of conditions and the
following disclaimer.
2. Redistributions in binary form must reproduce the above copyright notice, this list of conditions and the
following disclaimer in the documentation and/or other materials provided with the distribution.
3. The name of the author may not be used to endorse or promote products derived from this software
without specific prior written permission.
THIS SOFTWARE IS PROVIDED BY THE AUTHOR “AS IS” AND ANY EXPRESS OR IMPLIED
WARRANTIES, INCLUDING, BUT NOT LIMITED TO, THE IMPLIED WARRANTIES OF
MERCHANTABILITY AND FITNESS FOR A PARTICULAR PURPOSE ARE DISCLAIMED.
IN NO EVENT SHALL THE AUTHOR BE LIABLE FOR ANY DIRECT, INDIRECT, INCIDENTAL,
SPECIAL, EXEMPLARY, OR CONSEQUENTIAL DAMAGES (INCLUDING, BUT NOT LIMITED TO,
PROCUREMENT OF SUBSTITUTE GOODS OR SERVICES; LOSS OF USE, DATA, OR PROFITS; OR
BUSINESS INTERRUPTION) HOWEVER CAUSED AND ON ANY THEORY OF LIABILITY, WHETHER
IN CONTRACT, STRICT LIABILITY, OR TORT (INCLUDING NEGLIGENCE OR OTHERWISE) ARISING
IN ANY WAY OUT OF THE USE OF THIS SOFTWARE, EVEN IF ADVISED OF THE POSSIBILITY OF
SUCH DAMAGE.
(12) SuperH, Inc.
Copyright 2002 SuperH, Inc. All rights reserved
This software is the property of SuperH, Inc (SuperH) which specifically grants the user the right to modify,
use and distribute this software provided this notice is not removed or altered. All other rights are reserved
by SuperH.
SUPERH MAKES NO WARRANTY OF ANY KIND, EXPRESS OR IMPLIED, WITH REGARD TO THIS
SOFTWARE. IN NO EVENT SHALL SUPERH BE LIABLE FOR INDIRECT, SPECIAL, INCIDENTAL OR
CONSEQUENTIAL DAMAGES IN CONNECTION WITH OR ARISING FROM THE FURNISHING,
PERFORMANCE, OR USE OF THIS SOFTWARE.
So that all may benefit from your experience, please report any problems or suggestions about this
software to the SuperH Support Center via e-mail at softwaresupport@superh.com .
SuperH, Inc.
405 River Oaks Parkway
San Jose
CA 95134
USA
(13) Royal Institute of Technology
Copyright (c) 1999 Kungliga Tekniska H skolan (Royal Institute of Technology, Stockholm, Sweden).
All rights reserved.
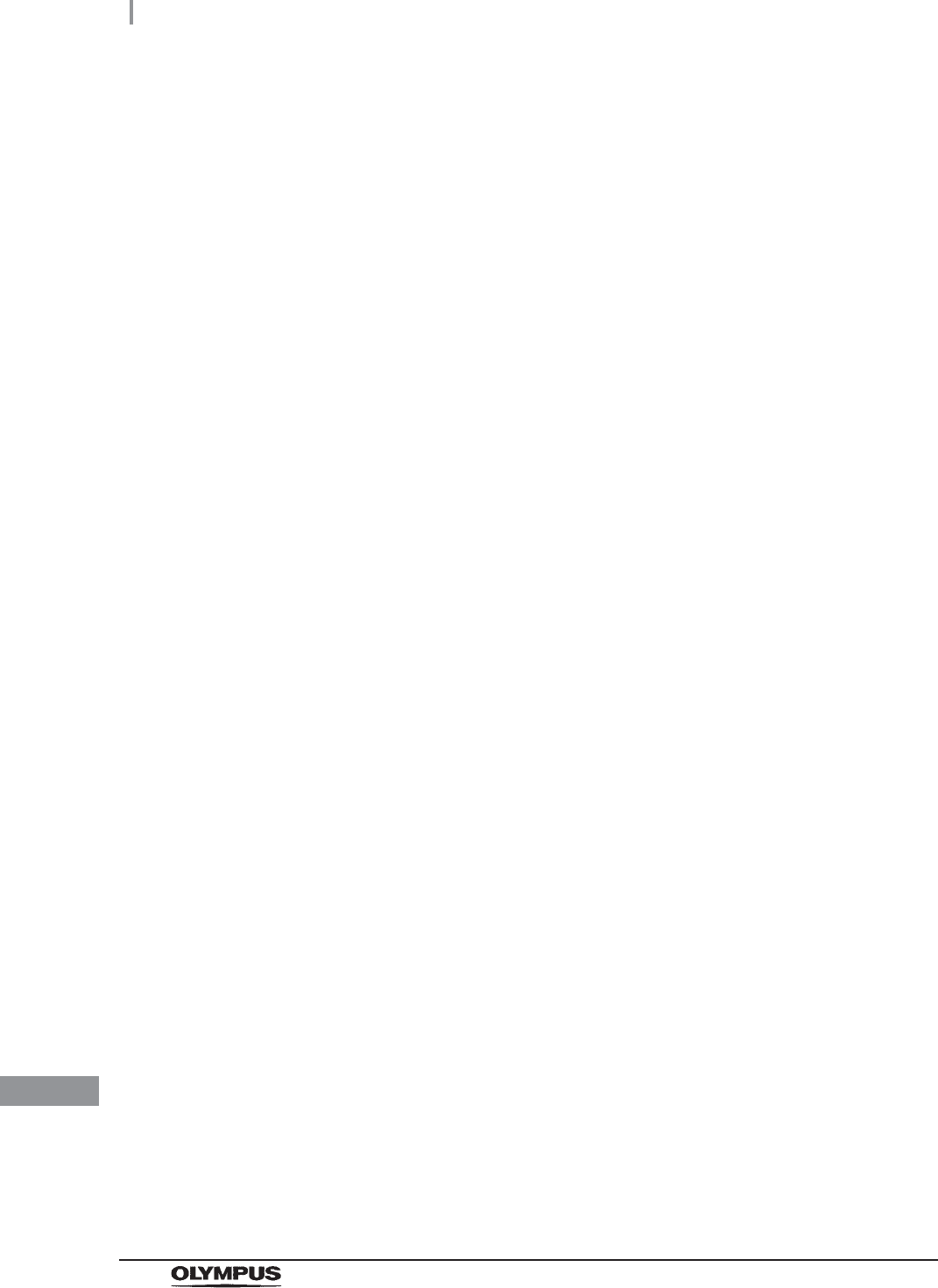
App.
664
License information of Open Source Software
OER-Elite OPERATION MANUAL
Redistribution and use in source and binary forms, with or without modification, are permitted provided that
the following conditions are met:
1. Redistributions of source code must retain the above copyright notice, this list of conditions and the
following disclaimer.
2. Redistributions in binary form must reproduce the above copyright notice, this list of conditions and the
following disclaimer in the documentation and/or other materials provided with the distribution.
3. Neither the name of KTH nor the names of its contributors may be used to endorse or promote products
derived from this software without specific prior written permission.
THIS SOFTWARE IS PROVIDED BY KTH AND ITS CONTRIBUTORS “AS IS” AND ANY EXPRESS OR
IMPLIED WARRANTIES, INCLUDING, BUT NOT LIMITED TO, THE IMPLIED WARRANTIES OF
MERCHANTABILITY AND FITNESS FOR A PARTICULAR PURPOSE ARE DISCLAIMED. IN NO EVENT
SHALL KTH OR ITS CONTRIBUTORS BE LIABLE FOR ANY DIRECT, INDIRECT, INCIDENTAL,
SPECIAL, EXEMPLARY, OR CONSEQUENTIAL DAMAGES (INCLUDING, BUT NOT LIMITED TO,
PROCUREMENT OF SUBSTITUTE GOODS OR SERVICES; LOSS OF USE, DATA, OR PROFITS; OR
BUSINESS INTERRUPTION) HOWEVER CAUSED AND ON ANY THEORY OF LIABILITY, WHETHER
IN CONTRACT, STRICT LIABILITY, OR TORT (INCLUDING NEGLIGENCE OR OTHERWISE) ARISING
IN ANY WAY OUT OF THE USE OF THIS SOFTWARE, EVEN IF ADVISED OF THE POSSIBILITY OF
SUCH DAMAGE.
(14) Alexey Zelkin
Copyright (c) 2000, 2001 Alexey Zelkin <phantom@FreeBSD.org>
All rights reserved.
Redistribution and use in source and binary forms, with or without modification, are permitted provided that
the following conditions are met:
1. Redistributions of source code must retain the above copyright notice, this list of conditions and the
following disclaimer.
2. Redistributions in binary form must reproduce the above copyright notice, this list of conditions and the
following disclaimer in the documentation and/or other materials provided with the distribution.
THIS SOFTWARE IS PROVIDED BY THE AUTHOR AND CONTRIBUTORS “AS IS” AND ANY
EXPRESS OR IMPLIED WARRANTIES, INCLUDING, BUT NOT LIMITED TO, THE IMPLIED
WARRANTIES OF MERCHANTABILITY AND FITNESS FOR A PARTICULAR PURPOSE ARE
DISCLAIMED. IN NO EVENT SHALL THE AUTHOR OR CONTRIBUTORS BE LIABLE FOR ANY
DIRECT, INDIRECT, INCIDENTAL, SPECIAL, EXEMPLARY, OR CONSEQUENTIAL DAMAGES
(INCLUDING, BUT NOT LIMITED TO, PROCUREMENT OF SUBSTITUTE GOODS OR SERVICES;
LOSS OF USE, DATA, OR PROFITS; OR BUSINESS INTERRUPTION) HOWEVER CAUSED AND ON
ANY THEORY OF LIABILITY, WHETHER IN CONTRACT, STRICT LIABILITY, OR TORT (INCLUDING
NEGLIGENCE OR OTHERWISE) ARISING IN ANY WAY OUT OF THE USE OF THIS SOFTWARE,
EVEN IF ADVISED OF THE POSSIBILITY OF SUCH DAMAGE.

App.
License information of Open Source Software
665
OER-Elite OPERATION MANUAL
(15) Andrey A. Chernov
Copyright (C) 1997 by Andrey A. Chernov, Moscow, Russia.
All rights reserved.
Redistribution and use in source and binary forms, with or without modification, are permitted provided that
the following conditions are met:
1. Redistributions of source code must retain the above copyright notice, this list of conditions and the
following disclaimer.
2. Redistributions in binary form must reproduce the above copyright notice, this list of conditions and the
following disclaimer in the documentation and/or other materials provided with the distribution.
THIS SOFTWARE IS PROVIDED BY THE AUTHOR “AS IS” AND ANY EXPRESS OR IMPLIED
WARRANTIES, INCLUDING, BUT NOT LIMITED TO, THE IMPLIED WARRANTIES OF
MERCHANTABILITY AND FITNESS FOR A PARTICULAR PURPOSE ARE DISCLAIMED. IN NO EVENT
SHALL THE REGENTS OR CONTRIBUTORS BE LIABLE FOR ANY DIRECT, INDIRECT, INCIDENTAL,
SPECIAL, EXEMPLARY, OR CONSEQUENTIAL DAMAGES (INCLUDING, BUT NOT LIMITED TO,
PROCUREMENT OF SUBSTITUTE GOODS OR SERVICES; LOSS OF USE, DATA, OR PROFITS; OR
BUSINESS INTERRUPTION) HOWEVER CAUSED AND ON ANY THEORY OF LIABILITY, WHETHER
IN CONTRACT, STRICT LIABILITY, OR TORT (INCLUDING NEGLIGENCE OR OTHERWISE) ARISING
IN ANY WAY OUT OF THE USE OF THIS SOFTWARE, EVEN IF ADVISED OF THE POSSIBILITY OF
SUCH DAMAGE.
(16) FreeBSD
Copyright (c) 1997-2002 FreeBSD Project.
All rights reserved.
Redistribution and use in source and binary forms, with or without modification, are permitted provided that
the following conditions are met:
1. Redistributions of source code must retain the above copyright notice, this list of conditions and the
following disclaimer.
2. Redistributions in binary form must reproduce the above copyright notice, this list of conditions and the
following disclaimer in the documentation and/or other materials provided with the distribution.
THIS SOFTWARE IS PROVIDED BY THE AUTHOR AND CONTRIBUTORS “AS IS” AND ANY
EXPRESS OR IMPLIED WARRANTIES, INCLUDING, BUT NOT LIMITED TO, THE IMPLIED
WARRANTIES OF MERCHANTABILITY AND FITNESS FOR A PARTICULAR PURPOSE ARE
DISCLAIMED. IN NO EVENT SHALL THE AUTHOR OR CONTRIBUTORS BE LIABLE FOR ANY
DIRECT, INDIRECT, INCIDENTAL, SPECIAL, EXEMPLARY, OR CONSEQUENTIAL DAMAGES
(INCLUDING, BUT NOT LIMITED TO, PROCUREMENT OF SUBSTITUTE GOODS OR SERVICES;
LOSS OF USE, DATA, OR PROFITS; OR BUSINESS INTERRUPTION) HOWEVER CAUSED AND ON
ANY THEORY OF LIABILITY, WHETHER IN CONTRACT, STRICT LIABILITY, OR TORT (INCLUDING
NEGLIGENCE OR OTHERWISE) ARISING IN ANY WAY OUT OF THE USE OF THIS SOFTWARE,
EVEN IF ADVISED OF THE POSSIBILITY OF SUCH DAMAGE.
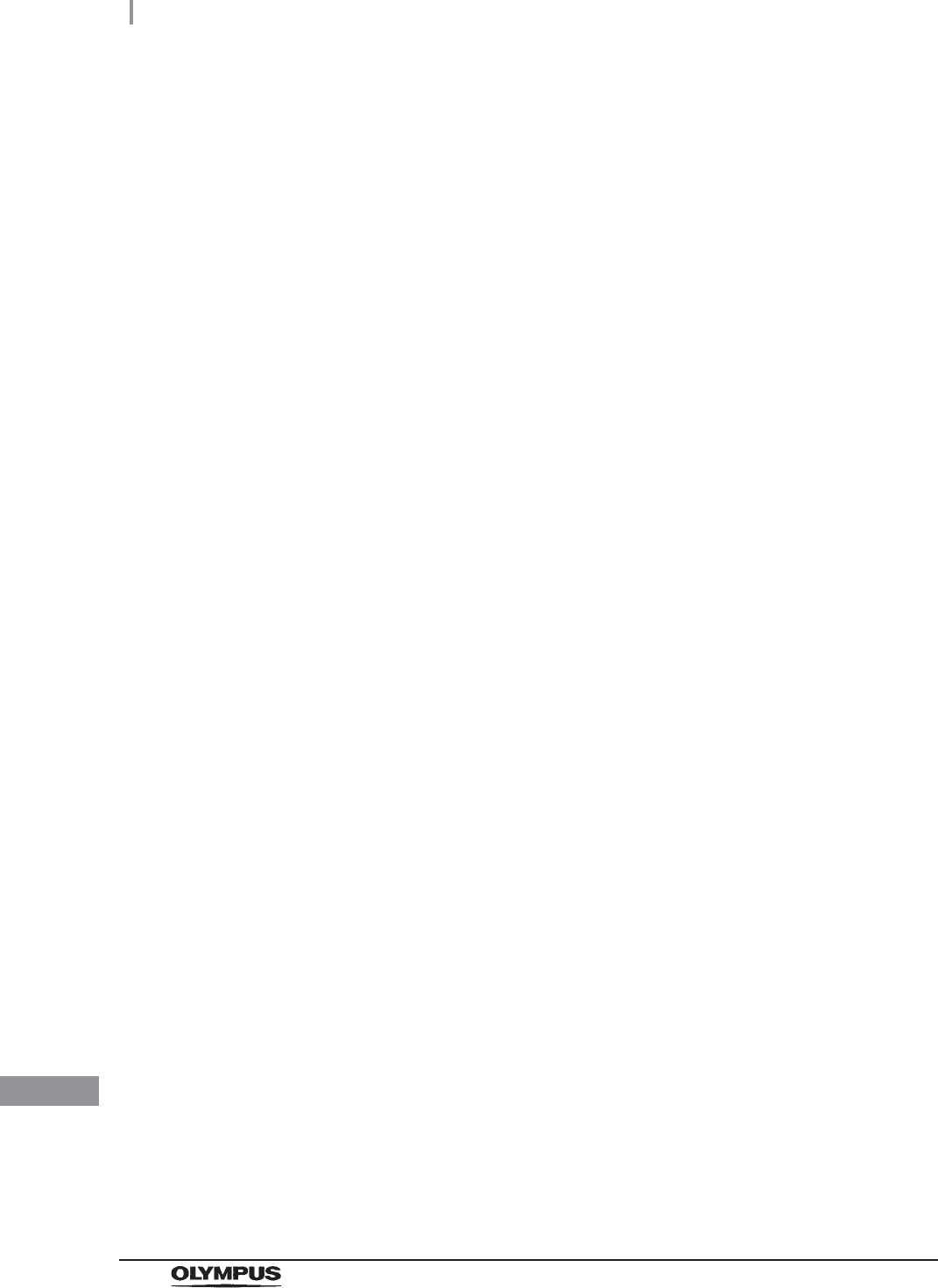
App.
666
License information of Open Source Software
OER-Elite OPERATION MANUAL
(17) S. L. Moshier
Author: S. L. Moshier.
Copyright (c) 1984,2000 S.L. Moshier
Permission to use, copy, modify, and distribute this software for any purpose without fee is hereby granted,
provided that this entire notice is included in all copies of any software which is or includes a copy or
modification of this software and in all copies of the supporting documentation for such software.
THIS SOFTWARE IS BEING PROVIDED “AS IS”, WITHOUT ANY EXPRESS OR IMPLIED WARRANTY.
IN PARTICULAR, THE AUTHOR MAKES NO REPRESENTATION OR WARRANTY OF ANY KIND
CONCERNING THE MERCHANTABILITY OF THIS SOFTWARE OR ITS FITNESS FOR ANY
PARTICULAR PURPOSE.
(18) Citrus Project
Copyright (c)1999 Citrus Project, All rights reserved.
Redistribution and use in source and binary forms, with or without modification, are permitted provided that
the following conditions are met:
1. Redistributions of source code must retain the above copyright notice, this list of conditions and the
following disclaimer.
2. Redistributions in binary form must reproduce the above copyright notice, this list of conditions and the
following disclaimer in the documentation and/or other materials provided with the distribution.
THIS SOFTWARE IS PROVIDED BY THE AUTHOR AND CONTRIBUTORS “AS IS” AND ANY
EXPRESS OR IMPLIED WARRANTIES, INCLUDING, BUT NOT LIMITED TO, THE IMPLIED
WARRANTIES OF MERCHANTABILITY AND FITNESS FOR A PARTICULAR PURPOSE ARE
DISCLAIMED. IN NO EVENT SHALL THE AUTHOR OR CONTRIBUTORS BE LIABLE FOR ANY
DIRECT, INDIRECT, INCIDENTAL, SPECIAL, EXEMPLARY, OR CONSEQUENTIAL DAMAGES
(INCLUDING, BUT NOT LIMITED TO, PROCUREMENT OF SUBSTITUTE GOODS OR SERVICES;
LOSS OF USE, DATA, OR PROFITS; OR BUSINESS INTERRUPTION) HOWEVER CAUSED AND ON
ANY THEORY OF LIABILITY, WHETHER IN CONTRACT, STRICT LIABILITY, OR TORT (INCLUDING
NEGLIGENCE OR OTHERWISE) ARISING IN ANY WAY OUT OF THE USE OF THIS SOFTWARE,
EVEN IF ADVISED OF THE POSSIBILITY OF SUCH DAMAGE.
(19) Todd C. Miller
Copyright (c) 1998 Todd C. Miller <Todd.Miller@courtesan.com>
All rights reserved.
Redistribution and use in source and binary forms, with or without modification, are permitted provided that
the following conditions are met:
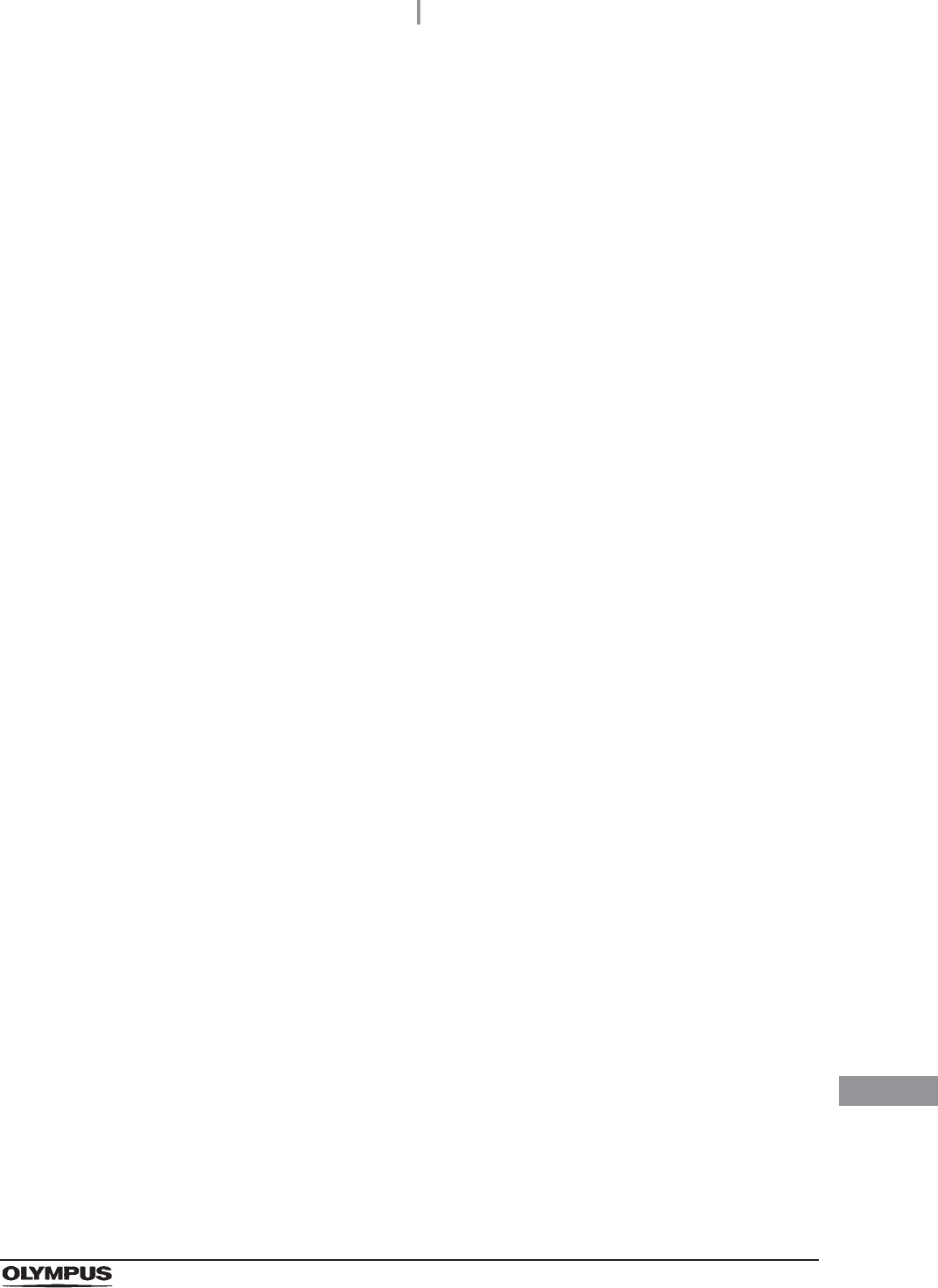
App.
License information of Open Source Software
667
OER-Elite OPERATION MANUAL
1. Redistributions of source code must retain the above copyright notice, this list of conditions and the
following disclaimer.
2. Redistributions in binary form must reproduce the above copyright notice, this list of conditions and the
following disclaimer in the documentation and/or other materials provided with the distribution.
3. The name of the author may not be used to endorse or promote products derived from this software
without specific prior written permission.
THIS SOFTWARE IS PROVIDED “AS IS” AND ANY EXPRESS OR IMPLIED WARRANTIES,
INCLUDING, BUT NOT LIMITED TO, THE IMPLIED WARRANTIES OF MERCHANTABILITY AND
FITNESS FOR A PARTICULAR PURPOSE ARE DISCLAIMED. IN NO EVENT SHALL THE AUTHOR BE
LIABLE FOR ANY DIRECT, INDIRECT, INCIDENTAL, SPECIAL, EXEMPLARY, OR CONSEQUENTIAL
DAMAGES (INCLUDING, BUT NOT LIMITED TO, PROCUREMENT OF SUBSTITUTE GOODS OR
SERVICES; LOSS OF USE, DATA, OR PROFITS; OR BUSINESS INTERRUPTION) HOWEVER
CAUSED AND ON ANY THEORY OF LIABILITY, WHETHER IN CONTRACT, STRICT LIABILITY, OR
TORT (INCLUDING NEGLIGENCE OR OTHERWISE) ARISING IN ANY WAY OUT OF THE USE OF
THIS SOFTWARE, EVEN IF ADVISED OF THE POSSIBILITY OF SUCH DAMAGE.
(26) Mike Barcroft
Copyright (c) 2001 Mike Barcroft <mike@FreeBSD.org>
All rights reserved.
Redistribution and use in source and binary forms, with or without modification, are permitted provided that
the following conditions are met:
1. Redistributions of source code must retain the above copyright notice, this list of conditions and the
following disclaimer.
2. Redistributions in binary form must reproduce the above copyright notice, this list of conditions and the
following disclaimer in the documentation and/or other materials provided with the distribution.
THIS SOFTWARE IS PROVIDED BY THE AUTHOR AND CONTRIBUTORS “AS IS” AND ANY
EXPRESS OR IMPLIED WARRANTIES, INCLUDING, BUT NOT LIMITED TO, THE IMPLIED
WARRANTIES OF MERCHANTABILITY AND FITNESS FOR A PARTICULAR PURPOSE ARE
DISCLAIMED. IN NO EVENT SHALL THE AUTHOR OR CONTRIBUTORS BE LIABLE FOR ANY
DIRECT, INDIRECT, INCIDENTAL, SPECIAL, EXEMPLARY, OR CONSEQUENTIAL DAMAGES
(INCLUDING, BUT NOT LIMITED TO, PROCUREMENT OF SUBSTITUTE GOODS OR SERVICES;
LOSS OF USE, DATA, OR PROFITS; OR BUSINESS INTERRUPTION) HOWEVER CAUSED AND ON
ANY THEORY OF LIABILITY, WHETHER IN CONTRACT, STRICT LIABILITY, OR TORT (INCLUDING
NEGLIGENCE OR OTHERWISE) ARISING IN ANY WAY OUT OF THE USE OF THIS SOFTWARE,
EVEN IF ADVISED OF THE POSSIBILITY OF SUCH DAMAGE.
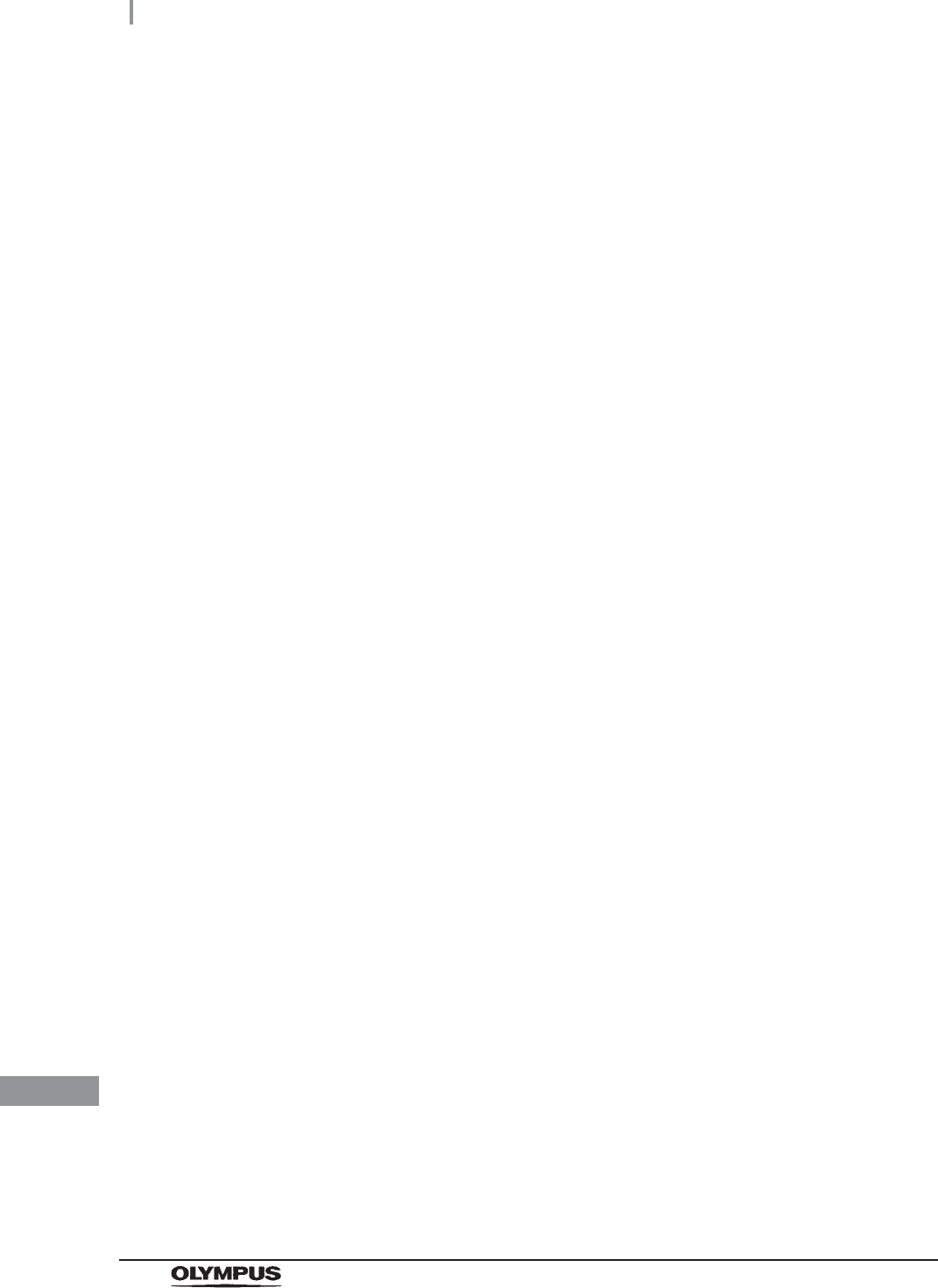
App.
668
License information of Open Source Software
OER-Elite OPERATION MANUAL
(27) Konstantin Chuguev (--enable-newlib-iconv)
Copyright (c) 1999, 2000 Konstantin Chuguev.
All rights reserved.
Redistribution and use in source and binary forms, with or without modification, are permitted provided that
the following conditions are met:
1. Redistributions of source code must retain the above copyright notice, this list of conditions and the
following disclaimer.
2. Redistributions in binary form must reproduce the above copyright notice, this list of conditions and the
following disclaimer in the documentation and/or other materials provided with the distribution.
THIS SOFTWARE IS PROVIDED BY THE AUTHOR AND CONTRIBUTORS “AS IS” AND ANY
EXPRESS OR IMPLIED WARRANTIES, INCLUDING, BUT NOT LIMITED TO, THE IMPLIED
WARRANTIES OF MERCHANTABILITY AND FITNESS FOR A PARTICULAR PURPOSE ARE
DISCLAIMED. IN NO EVENT SHALL THE AUTHOR OR CONTRIBUTORS BE LIABLE FOR ANY
DIRECT, INDIRECT, INCIDENTAL, SPECIAL, EXEMPLARY, OR CONSEQUENTIAL DAMAGES
(INCLUDING, BUT NOT LIMITED TO, PROCUREMENT OF SUBSTITUTE GOODS OR SERVICES;
LOSS OF USE, DATA, OR PROFITS; OR BUSINESS INTERRUPTION) HOWEVER CAUSED AND ON
ANY THEORY OF LIABILITY, WHETHER IN CONTRACT, STRICT LIABILITY, OR TORT (INCLUDING
NEGLIGENCE OR OTHERWISE) ARISING IN ANY WAY OUT OF THE USE OF THIS SOFTWARE,
EVEN IF ADVISED OF THE POSSIBILITY OF SUCH DAMAGE.
iconv (Charset Conversion Library) v2.0
(28) Artem Bityuckiy (--enable-newlib-iconv)
Copyright (c) 2003, Artem B. Bityuckiy, SoftMine Corporation.
Rights transferred to Franklin Electronic Publishers.
Redistribution and use in source and binary forms, with or without modification, are permitted provided that
the following conditions are met:
1. Redistributions of source code must retain the above copyright notice, this list of conditions and the
following disclaimer.
2. Redistributions in binary form must reproduce the above copyright notice, this list of conditions and the
following disclaimer in the documentation and/or other materials provided with the distribution.
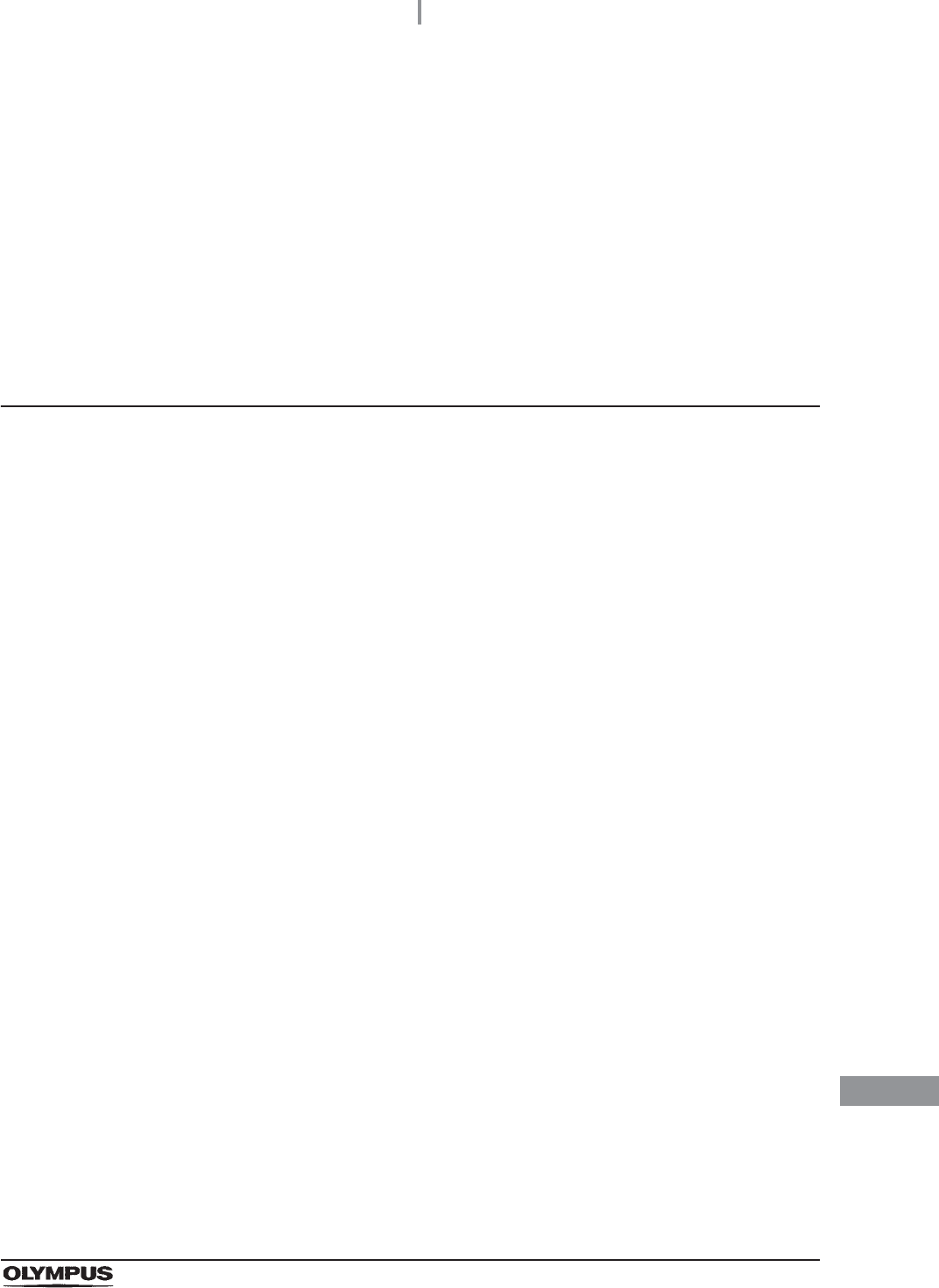
App.
License information of Open Source Software
669
OER-Elite OPERATION MANUAL
THIS SOFTWARE IS PROVIDED BY THE AUTHOR AND CONTRIBUTORS “AS IS” AND ANY
EXPRESS OR IMPLIED WARRANTIES, INCLUDING, BUT NOT LIMITED TO, THE IMPLIED
WARRANTIES OF MERCHANTABILITY AND FITNESS FOR A PARTICULAR PURPOSE ARE
DISCLAIMED. IN NO EVENT SHALL THE AUTHOR OR CONTRIBUTORS BE LIABLE FOR ANY
DIRECT, INDIRECT, INCIDENTAL, SPECIAL, EXEMPLARY, OR CONSEQUENTIAL DAMAGES
(INCLUDING, BUT NOT LIMITED TO, PROCUREMENT OF SUBSTITUTE GOODS OR SERVICES;
LOSS OF USE, DATA, OR PROFITS; OR BUSINESS INTERRUPTION) HOWEVER CAUSED AND ON
ANY THEORY OF LIABILITY, WHETHER IN CONTRACT, STRICT LIABILITY, OR TORT (INCLUDING
NEGLIGENCE OR OTHERWISE) ARISING IN ANY WAY OUT OF THE USE OF THIS SOFTWARE,
EVEN IF ADVISED OF THE POSSIBILITY OF SUCH DAMAGE.
libhal_bsp
This product uses the open source software program “libhal_bsp” which applies the terms and conditions
provided by owner of the copyright to the “libhal_bsp”.
Copyright (c) 2003 Altera Corporation, San Jose, California, USA.
All rights reserved.
Permission is hereby granted, free of charge, to any person obtaining a copy of this software and
associated documentation files (the “Software”), to deal in the Software without restriction, including
without limitation the rights to use, copy, modify, merge, publish, distribute, sublicense, and/or sell copies
of the Software, and to permit persons to whom the Software is furnished to do so, subject to the following
conditions:
The above copyright notice and this permission notice shall be included in all copies or substantial portions
of the Software.
THE SOFTWARE IS PROVIDED “AS IS”, WITHOUT WARRANTY OF ANY KIND, EXPRESS OR
IMPLIED, INCLUDING BUT NOT LIMITED TO THE WARRANTIES OF MERCHANTABILITY, FITNESS
FOR A PARTICULAR PURPOSE AND NONINFRINGEMENT. IN NO EVENT SHALL THE AUTHORS OR
COPYRIGHT HOLDERS BE LIABLE FOR ANY CLAIM, DAMAGES OR OTHER LIABILITY, WHETHER IN
AN ACTION OF CONTRACT, TORT OR OTHERWISE, ARISING FROM, OUT OF OR IN CONNECTION
WITH THE SOFTWARE OR THE USE OR OTHER DEALINGS IN THE SOFTWARE.
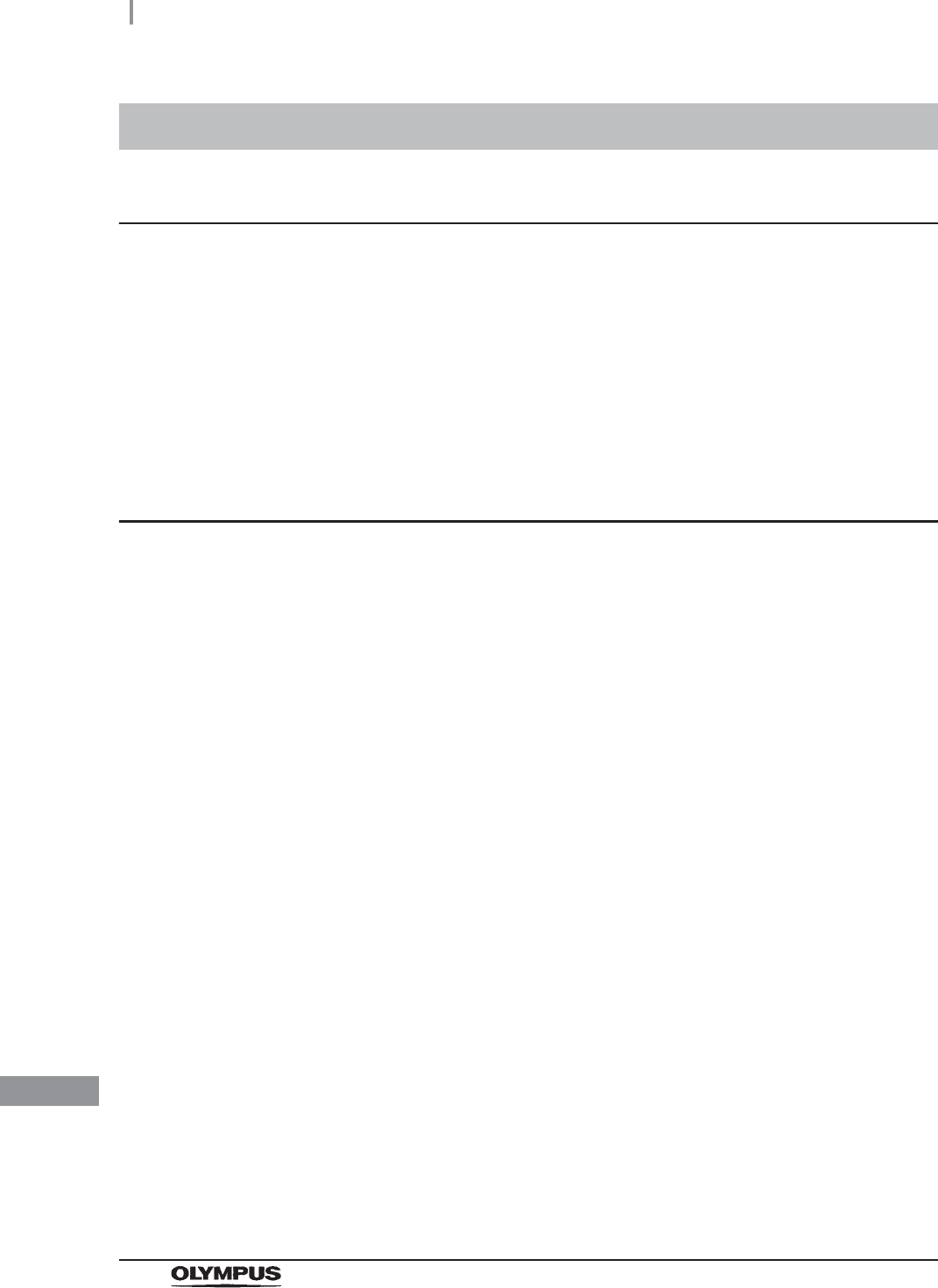
App.
670
License information of Open Source Software
OER-Elite OPERATION MANUAL
z
End User License Agreement of Open Source Software modules
• This instrument contains software modules which are not licensed under the terms of GPL. This section
must not be translated by any language and must not be changed from original text. Because these
license description must be described original description in English according to these license.
• The Licensed Software may include (i) some open source software and (ii) other third party software
(collectively, “Third Party Software”). Regarding the use of the Third Party Software, you shall follow the
license terms and conditions applied to such Third Party Software. Any part of this License Agreement
does not restrict, change or alter any of your rights and obligations imposed by the license terms and
conditions of the Third Party Software.
newlib
MAJ-2130, which is “NLV-3101” manufactured by OPTO ELECTORONICS CO.,LTD, uses the open
source software program “newlib” which applies the terms and conditions provided by owner of the
copyright to the “newlib”.
The newlib subdirectory is a collection of software from several sources.
Each file may have its own copyright/license that is embedded in the source file(s), the following copyright
notices will apply to the contents of the newlib subdirectory:
(1) Red Hat Incorporated
Copyright (c) 1994-2009 Red Hat, Inc. All rights reserved.
This copyrighted material is made available to anyone wishing to use, modify, copy, or redistribute it
subject to the terms and conditions of the BSD License. This program is distributed in the hope that it will
be useful, but WITHOUT ANY WARRANTY expressed or implied, including the implied warranties of
MERCHANTABILITY or FITNESS FOR A PARTICULAR PURPOSE. A copy of this license is available at
http://www.opensource.org/licenses. Any Red Hat trademarks that are incorporated in the source code or
documentation are not subject to the BSD License and may only be used or replicated with the express
permission of Red Hat, Inc.
(2) University of California, Berkeley
Copyright (c) 1981-2000 The Regents of the University of California.
All rights reserved.
License information of Open Source Software
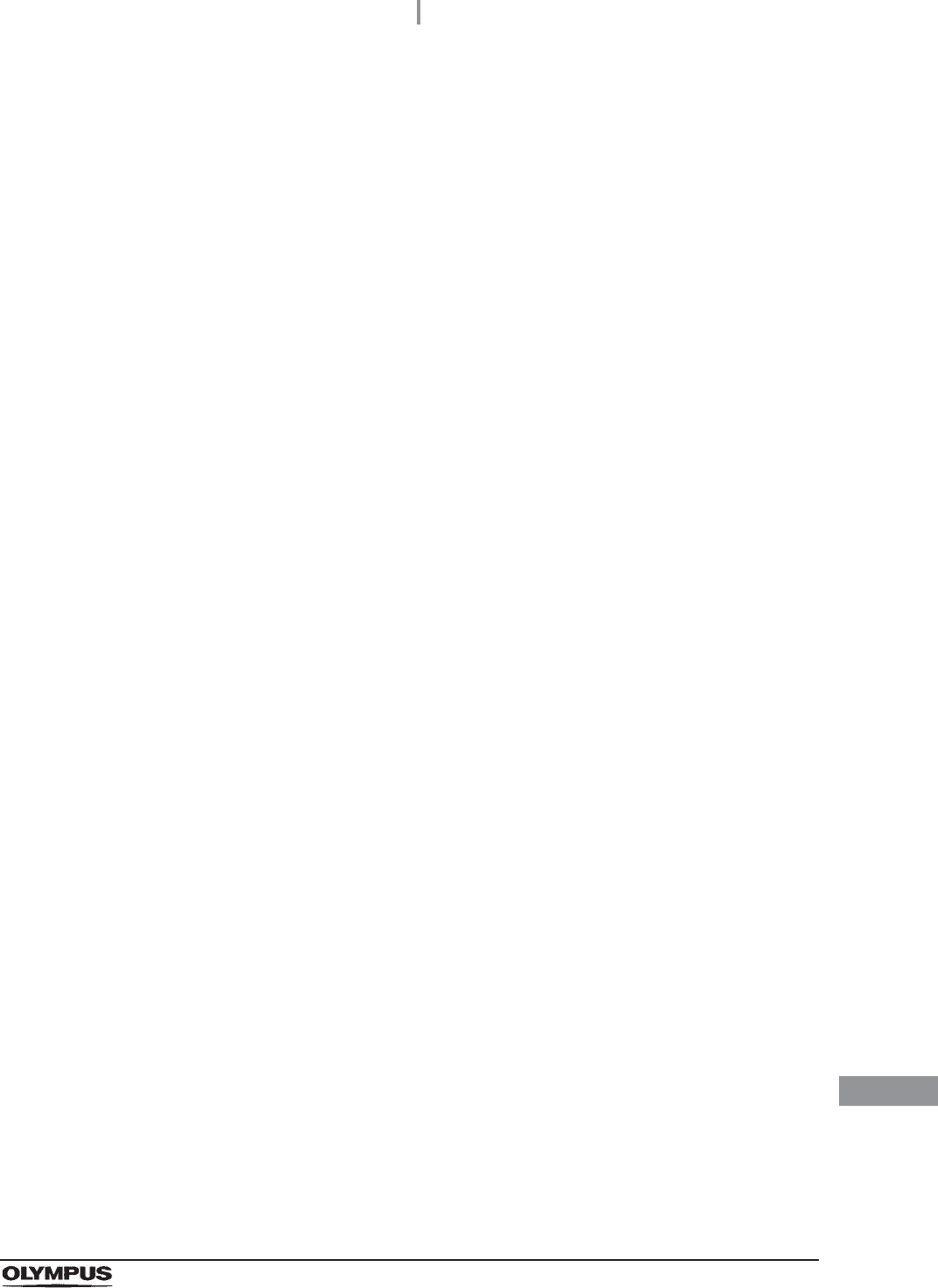
App.
License information of Open Source Software
671
OER-Elite OPERATION MANUAL
Redistribution and use in source and binary forms, with or without modification, are permitted provided that
the following conditions are met:
* Redistributions of source code must retain the above copyright notice, this list of conditions and the
following disclaimer.
* Redistributions in binary form must reproduce the above copyright notice, this list of conditions and the
following disclaimer in the documentation and/or other materials provided with the distribution.
* Neither the name of the University nor the names of its contributors may be used to endorse or promote
products derived from this software without specific prior written permission.
THIS SOFTWARE IS PROVIDED BY THE COPYRIGHT HOLDERS AND CONTRIBUTORS “AS IS” AND
ANY EXPRESS OR IMPLIED WARRANTIES, INCLUDING, BUT NOT LIMITED TO, THE IMPLIED
WARRANTIES OF MERCHANTABILITY AND FITNESS FOR A PARTICULAR PURPOSE ARE
DISCLAIMED.
IN NO EVENT SHALL THE COPYRIGHT OWNER OR CONTRIBUTORS BE LIABLE FOR ANY DIRECT,
INDIRECT, INCIDENTAL, SPECIAL, EXEMPLARY, OR CONSEQUENTIAL DAMAGES (INCLUDING,
BUT NOT LIMITED TO, PROCUREMENT OF SUBSTITUTE GOODS OR SERVICES; LOSS OF USE,
DATA, OR PROFITS; OR BUSINESS INTERRUPTION) HOWEVER CAUSED AND ON ANY THEORY
OF LIABILITY, WHETHER IN CONTRACT, STRICT LIABILITY, OR TORT (INCLUDING NEGLIGENCE
OR OTHERWISE) ARISING IN ANY WAY OUT OF THE USE OF THIS SOFTWARE, EVEN IF ADVISED
OF THE POSSIBILITYOF SUCH DAMAGE.
(3) David M. Gay at AT&T
The author of this software is David M. Gay.
Copyright (c) 1991 by AT&T.
Permission to use, copy, modify, and distribute this software for any purpose without fee is hereby granted,
provided that this entire notice is included in all copies of any software which is or includes a copy or
modification of this software and in all copies of the supporting documentation for such software.
THIS SOFTWARE IS BEING PROVIDED “AS IS”, WITHOUT ANY EXPRESS OR IMPLIED WARRANTY.
IN PARTICULAR, NEITHER THE AUTHOR NOR AT&T MAKES ANY REPRESENTATION OR
WARRANTY OF ANY KIND CONCERNING THE MERCHANTABILITY OF THIS SOFTWARE OR ITS
FITNESS FOR ANY PARTICULAR PURPOSE.
-------------------------------------------------------------------
The author of this software is David M. Gay.
Copyright (C) 1998-2001 by Lucent Technologies
All Rights Reserved
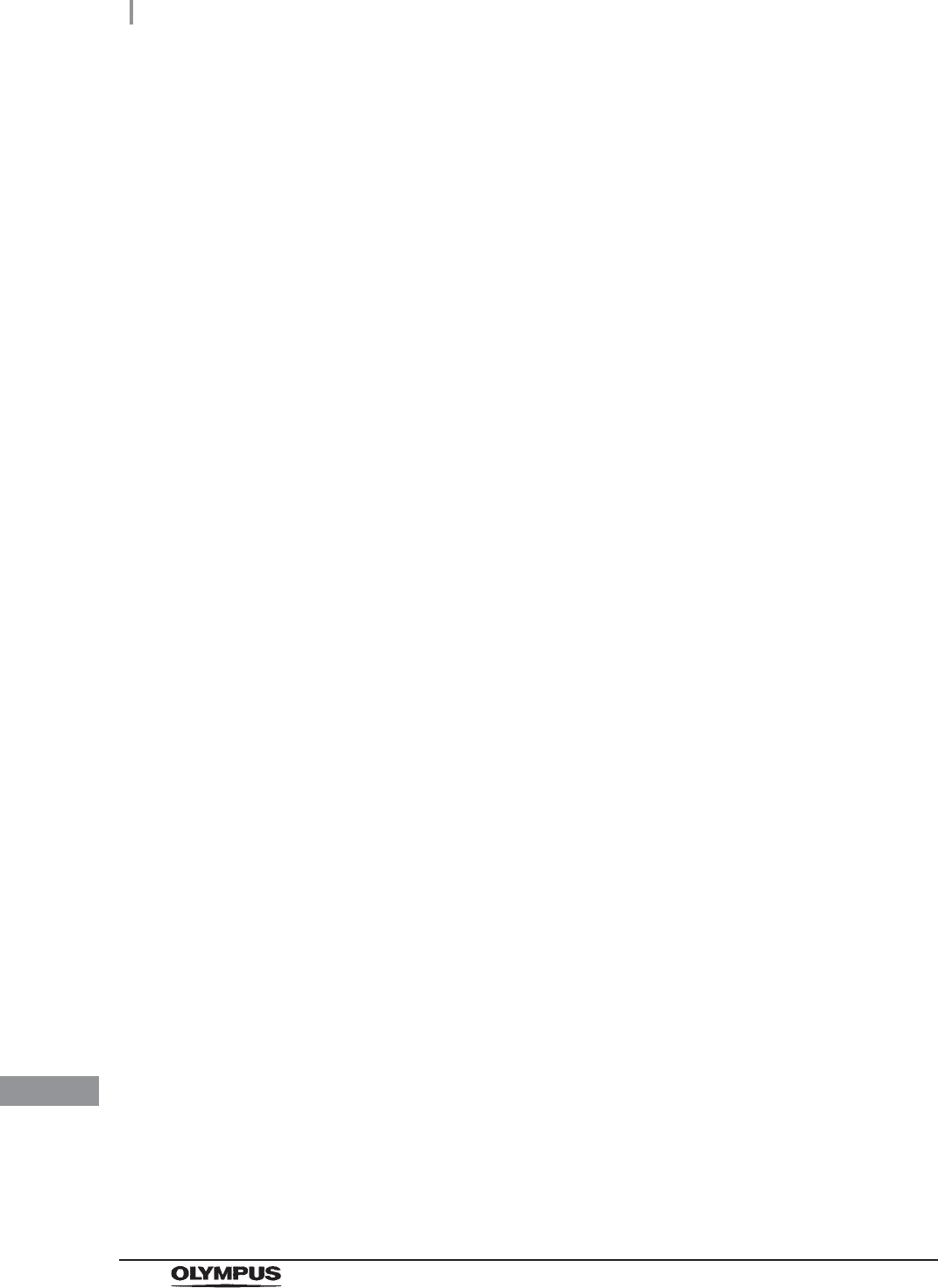
App.
672
License information of Open Source Software
OER-Elite OPERATION MANUAL
Permission to use, copy, modify, and distribute this software and its documentation for any purpose and
without fee is hereby granted, provided that the above copyright notice appear in all copies and that both
that the copyright notice and this permission notice and warranty disclaimer appear in supporting
documentation, and that the name of Lucent or any of its entities not be used in advertising or publicity
pertaining to distribution of the software without specific, written prior permission.
LUCENT DISCLAIMS ALL WARRANTIES WITH REGARD TO THIS SOFTWARE, INCLUDING ALL
IMPLIED WARRANTIES OF MERCHANTABILITY AND FITNESS.
IN NO EVENT SHALL LUCENT OR ANY OF ITS ENTITIES BE LIABLE FOR ANY SPECIAL, INDIRECT
OR CONSEQUENTIAL DAMAGES OR ANY DAMAGES WHATSOEVER RESULTING FROM LOSS OF
USE, DATA OR PROFITS, WHETHER IN AN ACTION OF CONTRACT, NEGLIGENCE OR OTHER
TORTIOUS ACTION, ARISING OUT OF OR IN CONNECTION WITH THE USE OR PERFORMANCE OF
THIS SOFTWARE.
(4) Advanced Micro Devices
Copyright 1989, 1990 Advanced Micro Devices, Inc.
This software is the property of Advanced Micro Devices, Inc (AMD) which specifically grants the user the
right to modify, use and distribute this software provided this notice is not removed or altered. All other
rights are reserved by AMD.
AMD MAKES NO WARRANTY OF ANY KIND, EXPRESS OR IMPLIED, WITH REGARD TO THIS
SOFTWARE. IN NO EVENT SHALL AMD BE LIABLE FOR INCIDENTAL OR CONSEQUENTIAL
DAMAGES IN CONNECTION WITH OR ARISING FROM THE FURNISHING, PERFORMANCE, OR USE
OF THIS SOFTWARE.
So that all may benefit from your experience, please report any problems or suggestions about this
software to the 29K Technical Support Center at 800-29-29-AMD (800-292-9263) in the USA, or
0800-89-1131 in the UK, or 0031-11-1129 in Japan, toll free. The direct dial number is 512-462-4118.
Advanced Micro Devices, Inc.
29K Support Products
Mail Stop 573
5900 E. Ben White Blvd.
Austin, TX 78741
800-292-9263
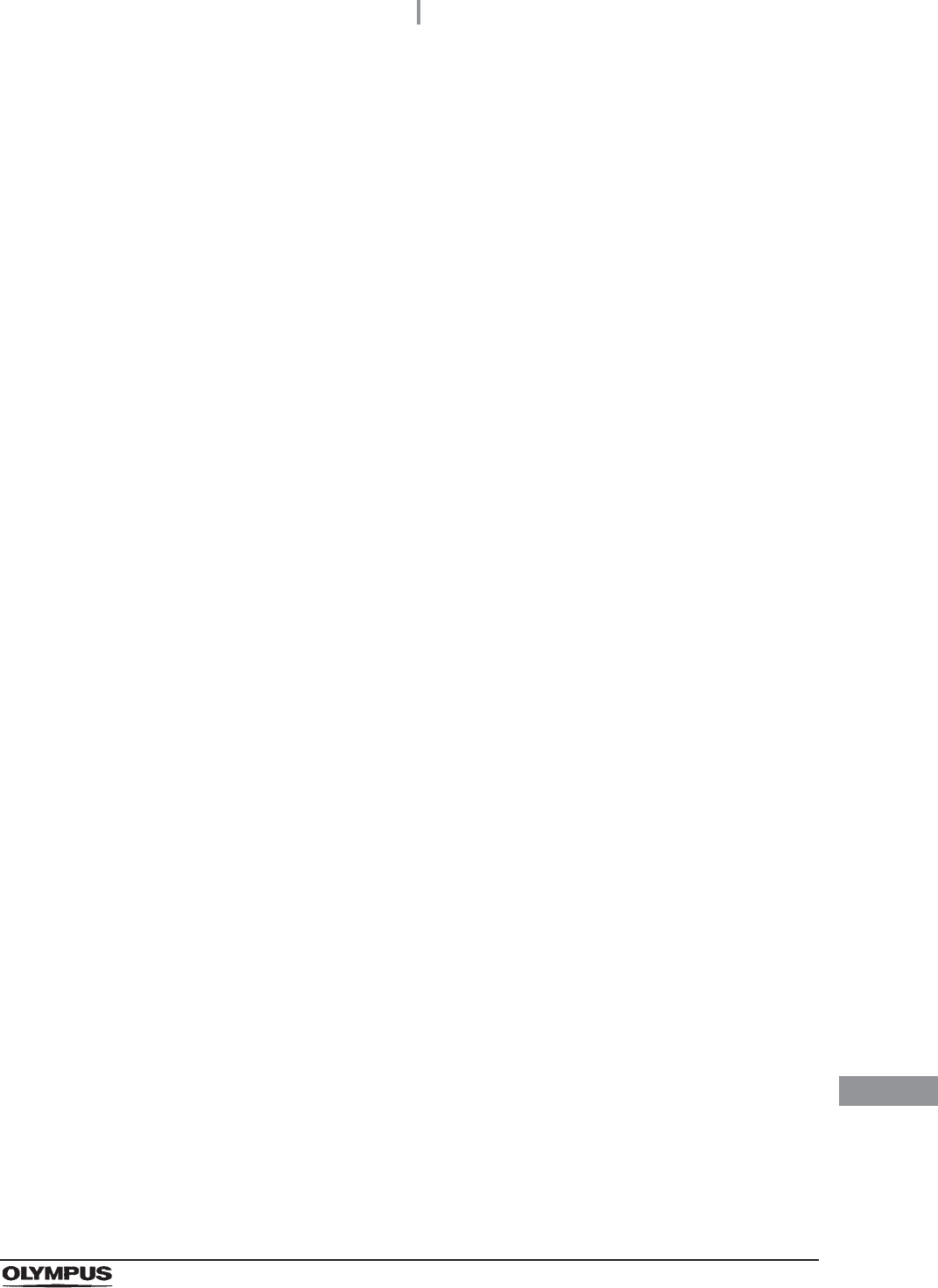
App.
License information of Open Source Software
673
OER-Elite OPERATION MANUAL
(7) Sun Microsystems
Copyright (C) 1993 by Sun Microsystems, Inc. All rights reserved.
Developed at SunPro, a Sun Microsystems, Inc. business.
Permission to use, copy, modify, and distribute this software is freely granted, provided that this notice is
preserved.
(8) Hewlett Packard
(c) Copyright 1986 HEWLETT-PACKARD COMPANY
To anyone who acknowledges that this file is provided “AS IS” without any express or implied warranty:
permission to use, copy, modify, and distribute this file for any purpose is hereby granted without fee,
provided that the above copyright notice and this notice appears in all copies, and that the name of
Hewlett-Packard Company not be used in advertising or publicity pertaining to distribution of the software
without specific, written prior permission.
Hewlett-Packard Company makes no representations about the suitability of this software for any purpose.
(9) Hans-Peter Nilsson
Copyright (C) 2001 Hans-Peter Nilsson
Permission to use, copy, modify, and distribute this software is freely granted, provided that the above
copyright notice, this notice and the following disclaimer are preserved with no changes.
THIS SOFTWARE IS PROVIDED “AS IS” AND WITHOUT ANY EXPRESS OR IMPLIED WARRANTIES,
INCLUDING, WITHOUT LIMITATION, THE IMPLIED WARRANTIES OF MERCHANTABILITY AND
FITNESS FOR A PARTICULAR PURPOSE.
(10) Stephane Carrez (m68hc11-elf/m68hc12-elf targets only)
Copyright (C) 1999, 2000, 2001, 2002 Stephane Carrez (stcarrez@nerim.fr)
The authors hereby grant permission to use, copy, modify, distribute, and license this software and its
documentation for any purpose, provided that existing copyright notices are retained in all copies and that
this notice is included verbatim in any distributions. No written agreement, license, or royalty fee is required
for any of the authorized uses.
Modifications to this software may be copyrighted by their authors and need not follow the licensing terms
described here, provided that the new terms are clearly indicated on the first page of each file where they
apply.
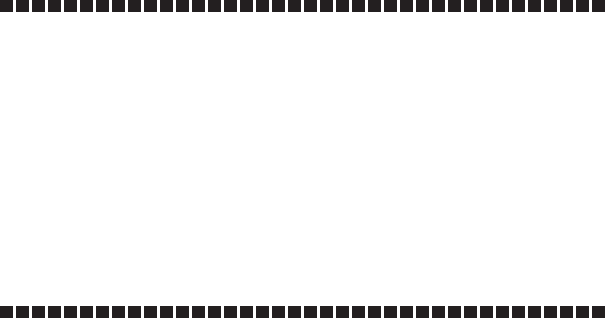
©2017 OLYMPUS MEDICAL SYSTEMS CORP. All rights reserved.
No part of this publication may be reproduced or distributed without the
express written permission of OLYMPUS MEDICAL SYSTEMS CORP.
OLYMPUS is a registered trademark of OLYMPUS CORPORATION.
Trademarks, product names, logos, or trade names used in this
document are generally registered trademarks or trademarks of each
company.
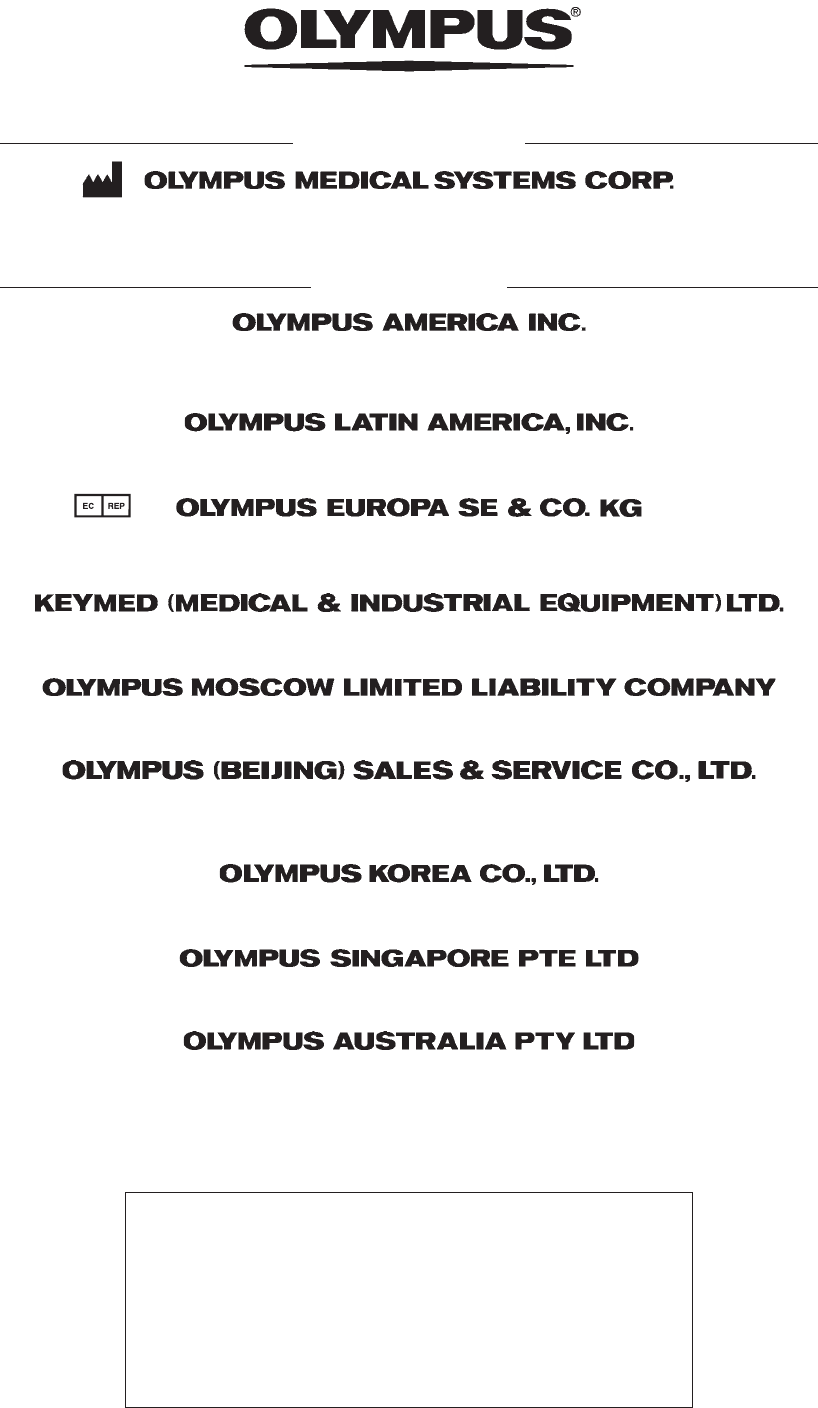
Printed in Japan 20170706 *0000
GT9882 01
Manufactured by
2951 Ishikawa-cho, Hachioji-shi, Tokyo 192-8507, Japan
Fax: (042)646-2429 Telephone: (042)642-2111
(Premises/Goods delivery) Wendenstrasse 14-18, 20097 Hamburg, Germany
(Letters) Postfach 10 49 08, 20034 Hamburg, Germany
3500 Corporate Parkway, P.O. Box 610, Center Valley, PA
18034-0610, U.S.A.
Fax: (484)896-7128 Telephone: (484)896-5000
KeyMed House, Stock Road, Southend-on-Sea, Essex SS2 5QH, United Kingdom
Fax: (01702)465677 Telephone: (01702)616333
491B, River Valley Road #12-01/04, Valley Point Office Tower, Singapore 248373
Fax: 6834-2438 Telephone: 6834-0010
A8F, Ping An International Financial Center, No. 1-3, Xinyuan South Road,
Chaoyang District, Beijing, 100027 P.R.C.
Fax: (86)10-5976-1299 Telephone: (86)10-5819-9000
Elektrozavodskaya str. 27 bld.8, 107023 Moscow, Russia
Fax: (7)495-663-8486 Telephone: (7)495-926-7077
3 Acacia Place, Notting Hill, VIC 3168, Australia
Fax: (03)9543-1350 Telephone: (03)9265-5400
5301 Blue Lagoon Drive, Suite 290 Miami, FL 33126-2097, U.S.A.
Fax: (305)261-4421 Telephone: (305)266-2332
Distributed by
Olympus Tower 9F, 446, Bongeunsa-ro, Gangnam-gu, Seoul, Korea 135-509
Fax: (02)6255-3494 Telephone: (02)6255-3210
Fax: (040)23773-4656 Telephone: (040)23773-0
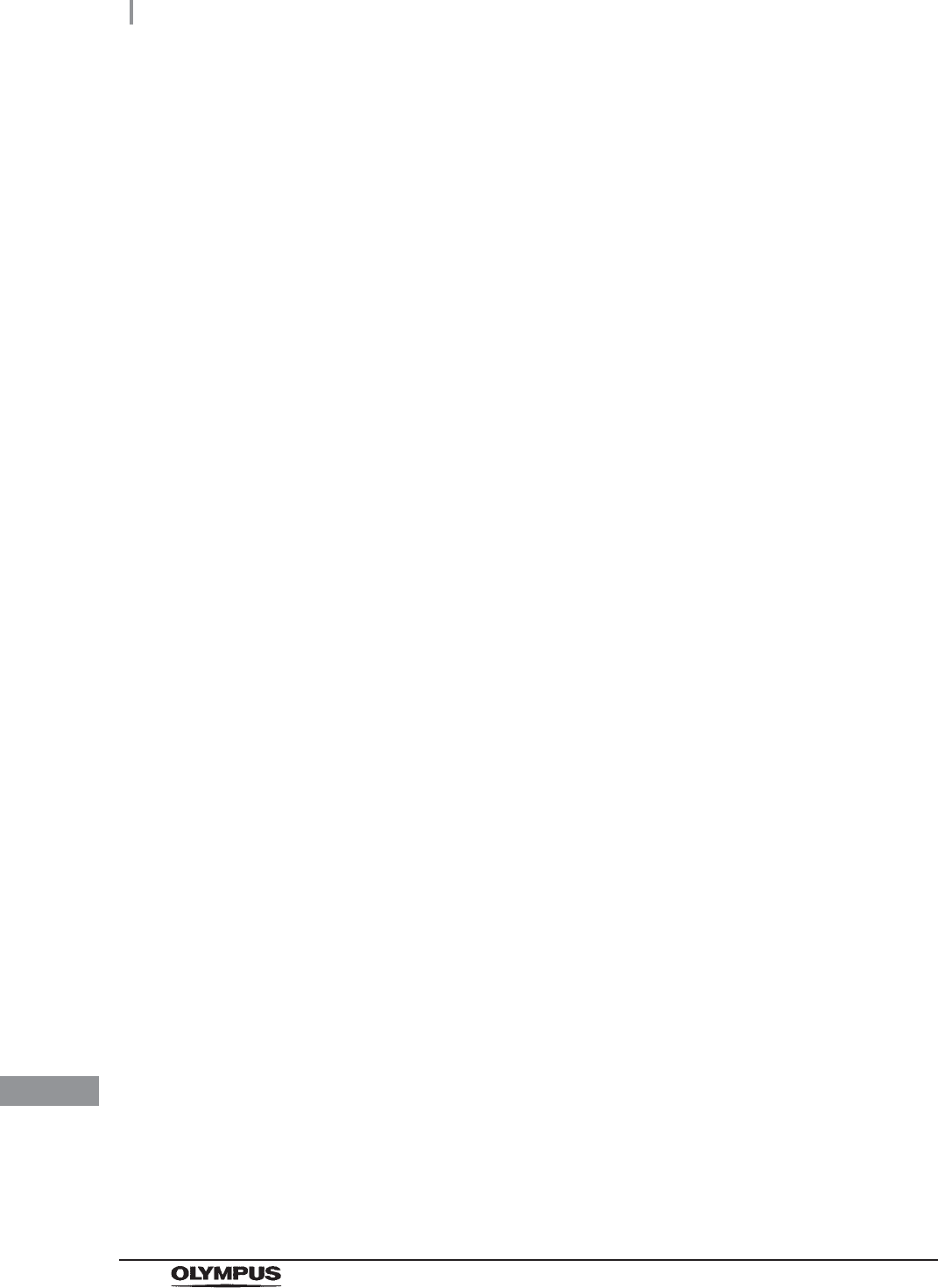
App.
674
License information of Open Source Software
OER-Elite OPERATION MANUAL
(11) Christopher G. Demetriou
Copyright (c) 2001 Christopher G. Demetriou
All rights reserved.
Redistribution and use in source and binary forms, with or without modification, are permitted provided that
the following conditions are met:
1. Redistributions of source code must retain the above copyright notice, this list of conditions and the
following disclaimer.
2. Redistributions in binary form must reproduce the above copyright notice, this list of conditions and the
following disclaimer in the documentation and/or other materials provided with the distribution.
3. The name of the author may not be used to endorse or promote products derived from this software
without specific prior written permission.
THIS SOFTWARE IS PROVIDED BY THE AUTHOR “AS IS” AND ANY EXPRESS OR IMPLIED
WARRANTIES, INCLUDING, BUT NOT LIMITED TO, THE IMPLIED WARRANTIES OF
MERCHANTABILITY AND FITNESS FOR A PARTICULAR PURPOSE ARE DISCLAIMED.
IN NO EVENT SHALL THE AUTHOR BE LIABLE FOR ANY DIRECT, INDIRECT, INCIDENTAL,
SPECIAL, EXEMPLARY, OR CONSEQUENTIAL DAMAGES (INCLUDING, BUT NOT LIMITED TO,
PROCUREMENT OF SUBSTITUTE GOODS OR SERVICES; LOSS OF USE, DATA, OR PROFITS; OR
BUSINESS INTERRUPTION) HOWEVER CAUSED AND ON ANY THEORY OF LIABILITY, WHETHER
IN CONTRACT, STRICT LIABILITY, OR TORT (INCLUDING NEGLIGENCE OR OTHERWISE) ARISING
IN ANY WAY OUT OF THE USE OF THIS SOFTWARE, EVEN IF ADVISED OF THE POSSIBILITY OF
SUCH DAMAGE.
(12) SuperH, Inc.
Copyright 2002 SuperH, Inc. All rights reserved
This software is the property of SuperH, Inc (SuperH) which specifically grants the user the right to modify,
use and distribute this software provided this notice is not removed or altered. All other rights are reserved
by SuperH.
SUPERH MAKES NO WARRANTY OF ANY KIND, EXPRESS OR IMPLIED, WITH REGARD TO THIS
SOFTWARE. IN NO EVENT SHALL SUPERH BE LIABLE FOR INDIRECT, SPECIAL, INCIDENTAL OR
CONSEQUENTIAL DAMAGES IN CONNECTION WITH OR ARISING FROM THE FURNISHING,
PERFORMANCE, OR USE OF THIS SOFTWARE.
So that all may benefit from your experience, please report any problems or suggestions about this
software to the SuperH Support Center via e-mail at softwaresupport@superh.com .
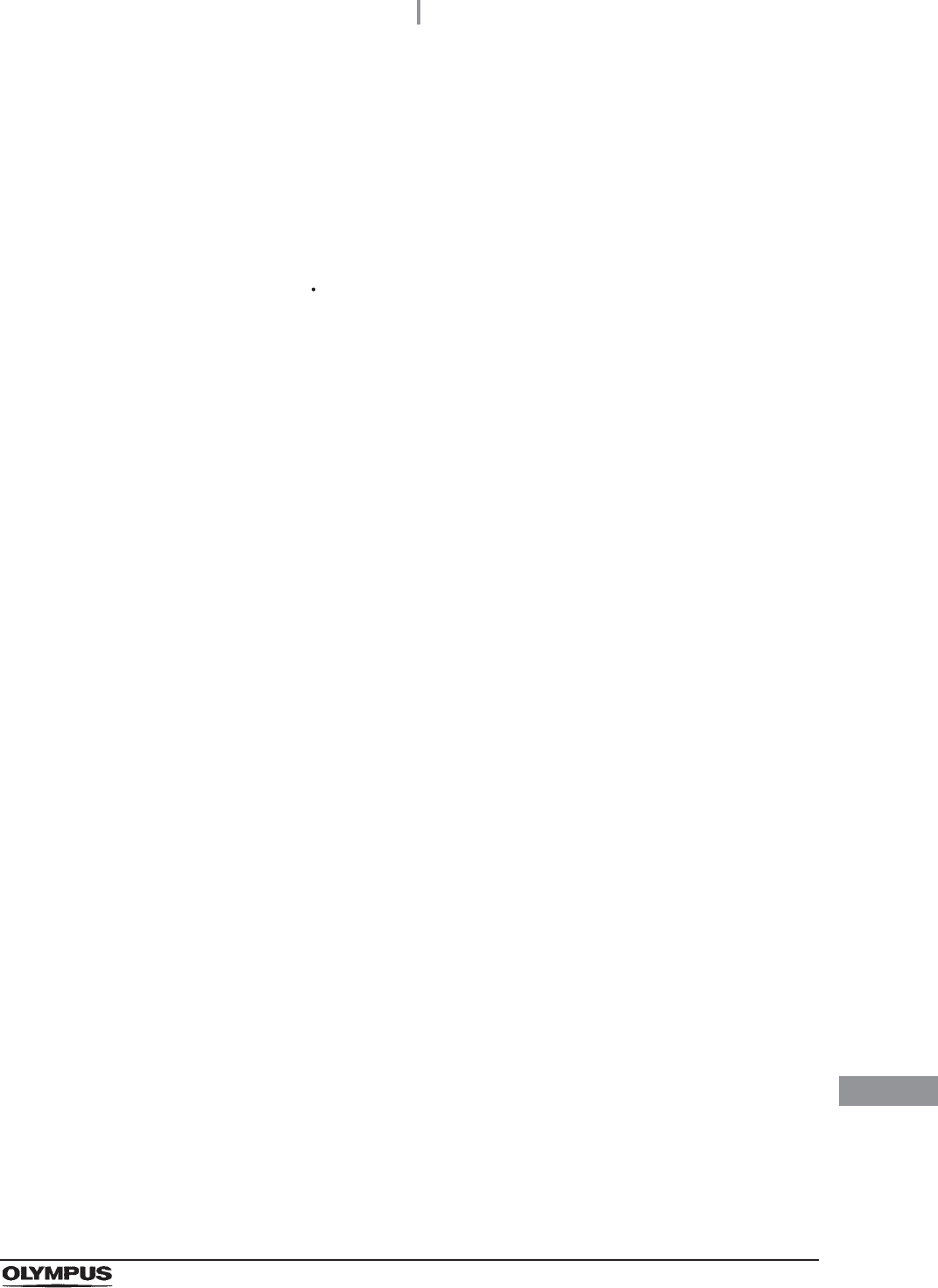
App.
License information of Open Source Software
675
OER-Elite OPERATION MANUAL
SuperH, Inc.
405 River Oaks Parkway
San Jose
CA 95134
USA
(13) Royal Institute of Technology
Copyright (c) 1999 Kungliga Tekniska H skolan (Royal Institute of Technology, Stockholm, Sweden).
All rights reserved.
Redistribution and use in source and binary forms, with or without modification, are permitted provided that
the following conditions are met:
1. Redistributions of source code must retain the above copyright notice, this list of conditions and the
following disclaimer.
2. Redistributions in binary form must reproduce the above copyright notice, this list of conditions and the
following disclaimer in the documentation and/or other materials provided with the distribution.
3. Neither the name of KTH nor the names of its contributors may be used to endorse or promote products
derived from this software without specific prior written permission.
THIS SOFTWARE IS PROVIDED BY KTH AND ITS CONTRIBUTORS “AS IS” AND ANY EXPRESS OR
IMPLIED WARRANTIES, INCLUDING, BUT NOT LIMITED TO, THE IMPLIED WARRANTIES OF
MERCHANTABILITY AND FITNESS FOR A PARTICULAR PURPOSE ARE DISCLAIMED. IN NO EVENT
SHALL KTH OR ITS CONTRIBUTORS BE LIABLE FOR ANY DIRECT, INDIRECT, INCIDENTAL,
SPECIAL, EXEMPLARY, OR CONSEQUENTIAL DAMAGES (INCLUDING, BUT NOT LIMITED TO,
PROCUREMENT OF SUBSTITUTE GOODS OR SERVICES; LOSS OF USE, DATA, OR PROFITS; OR
BUSINESS INTERRUPTION) HOWEVER CAUSED AND ON ANY THEORY OF LIABILITY, WHETHER
IN CONTRACT, STRICT LIABILITY, OR TORT (INCLUDING NEGLIGENCE OR OTHERWISE) ARISING
IN ANY WAY OUT OF THE USE OF THIS SOFTWARE, EVEN IF ADVISED OF THE POSSIBILITY OF
SUCH DAMAGE.
(14) Alexey Zelkin
Copyright (c) 2000, 2001 Alexey Zelkin <phantom@FreeBSD.org>
All rights reserved.
Redistribution and use in source and binary forms, with or without modification, are permitted provided that
the following conditions are met:
1. Redistributions of source code must retain the above copyright notice, this list of conditions and the
following disclaimer.
2. Redistributions in binary form must reproduce the above copyright notice, this list of conditions and the
following disclaimer in the documentation and/or other materials provided with the distribution.
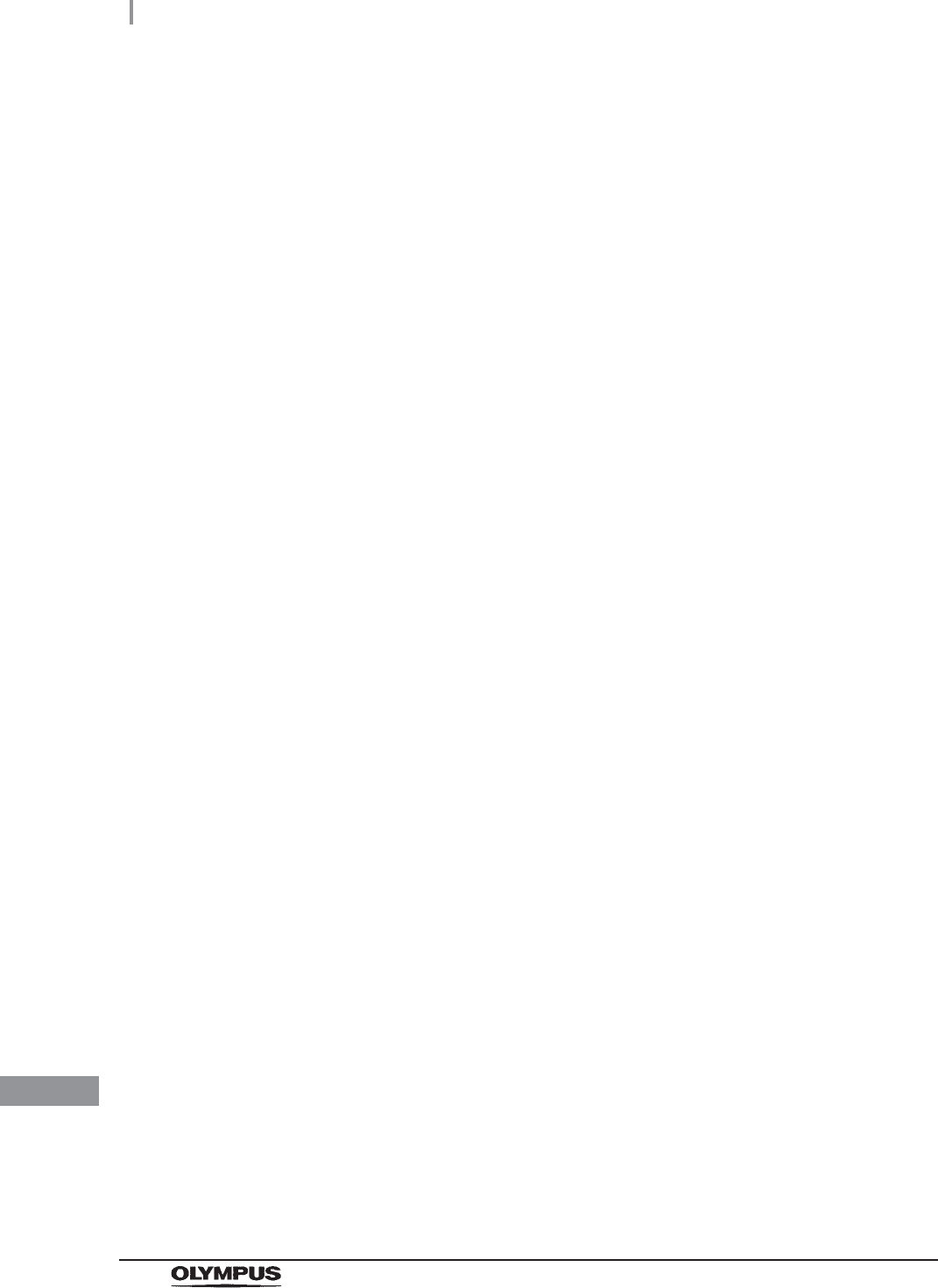
App.
676
License information of Open Source Software
OER-Elite OPERATION MANUAL
THIS SOFTWARE IS PROVIDED BY THE AUTHOR AND CONTRIBUTORS “AS IS” AND ANY
EXPRESS OR IMPLIED WARRANTIES, INCLUDING, BUT NOT LIMITED TO, THE IMPLIED
WARRANTIES OF MERCHANTABILITY AND FITNESS FOR A PARTICULAR PURPOSE ARE
DISCLAIMED. IN NO EVENT SHALL THE AUTHOR OR CONTRIBUTORS BE LIABLE FOR ANY
DIRECT, INDIRECT, INCIDENTAL, SPECIAL, EXEMPLARY, OR CONSEQUENTIAL DAMAGES
(INCLUDING, BUT NOT LIMITED TO, PROCUREMENT OF SUBSTITUTE GOODS OR SERVICES;
LOSS OF USE, DATA, OR PROFITS; OR BUSINESS INTERRUPTION) HOWEVER CAUSED AND ON
ANY THEORY OF LIABILITY, WHETHER IN CONTRACT, STRICT LIABILITY, OR TORT (INCLUDING
NEGLIGENCE OR OTHERWISE) ARISING IN ANY WAY OUT OF THE USE OF THIS SOFTWARE,
EVEN IF ADVISED OF THE POSSIBILITY OF SUCH DAMAGE.
(15) Andrey A. Chernov
Copyright (C) 1997 by Andrey A. Chernov, Moscow, Russia.
All rights reserved.
Redistribution and use in source and binary forms, with or without modification, are permitted provided that
the following conditions are met:
1. Redistributions of source code must retain the above copyright notice, this list of conditions and the
following disclaimer.
2. Redistributions in binary form must reproduce the above copyright notice, this list of conditions and the
following disclaimer in the documentation and/or other materials provided with the distribution.
THIS SOFTWARE IS PROVIDED BY THE AUTHOR “AS IS” AND ANY EXPRESS OR IMPLIED
WARRANTIES, INCLUDING, BUT NOT LIMITED TO, THE IMPLIED WARRANTIES OF
MERCHANTABILITY AND FITNESS FOR A PARTICULAR PURPOSE ARE DISCLAIMED. IN NO EVENT
SHALL THE REGENTS OR CONTRIBUTORS BE LIABLE FOR ANY DIRECT, INDIRECT, INCIDENTAL,
SPECIAL, EXEMPLARY, OR CONSEQUENTIAL DAMAGES (INCLUDING, BUT NOT LIMITED TO,
PROCUREMENT OF SUBSTITUTE GOODS OR SERVICES; LOSS OF USE, DATA, OR PROFITS; OR
BUSINESS INTERRUPTION) HOWEVER CAUSED AND ON ANY THEORY OF LIABILITY, WHETHER
IN CONTRACT, STRICT LIABILITY, OR TORT (INCLUDING NEGLIGENCE OR OTHERWISE) ARISING
IN ANY WAY OUT OF THE USE OF THIS SOFTWARE, EVEN IF ADVISED OF THE POSSIBILITY OF
SUCH DAMAGE.
(16) FreeBSD
Copyright (c) 1997-2002 FreeBSD Project.
All rights reserved.
Redistribution and use in source and binary forms, with or without modification, are permitted provided that
the following conditions are met:
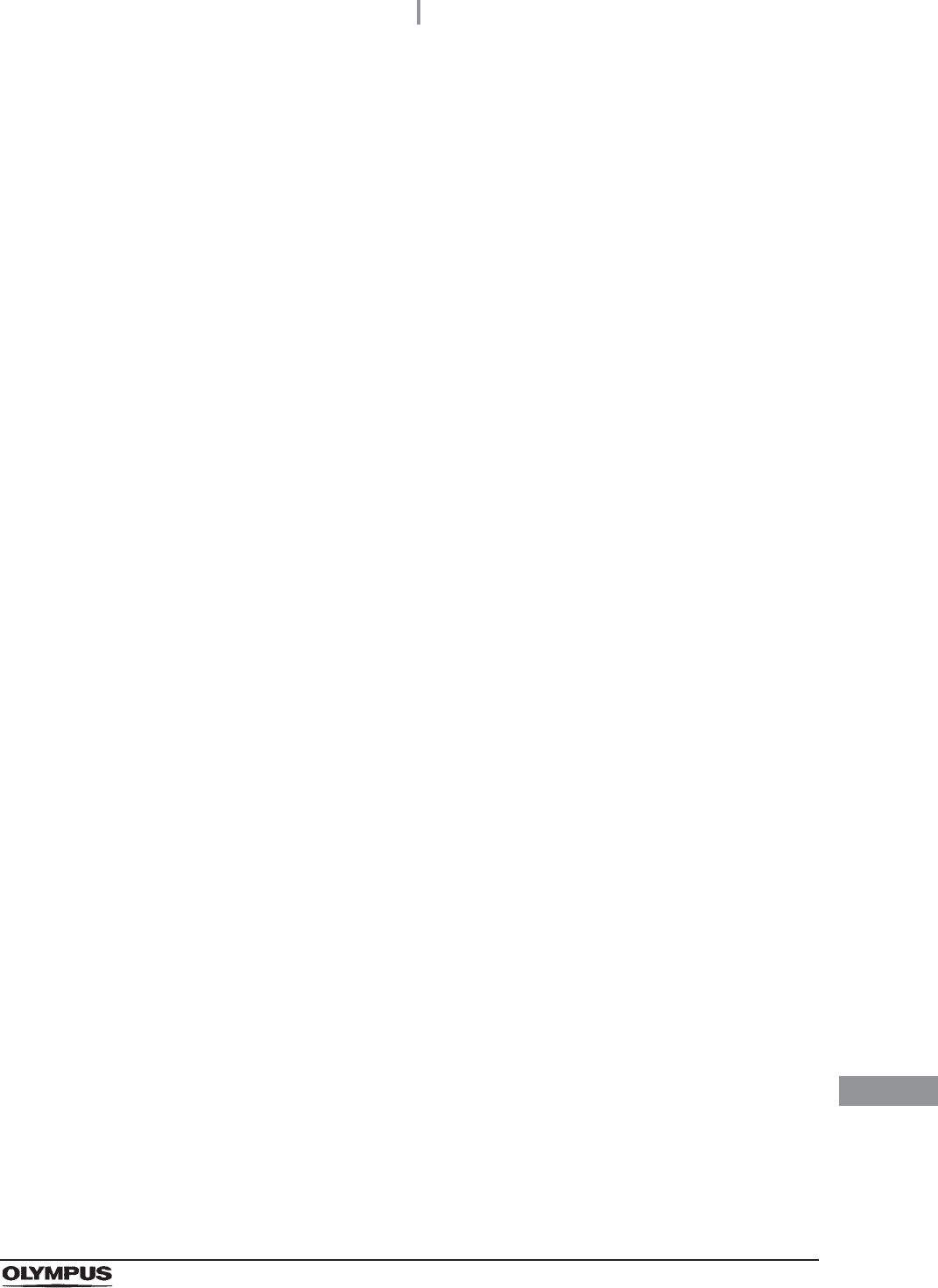
App.
License information of Open Source Software
677
OER-Elite OPERATION MANUAL
1. Redistributions of source code must retain the above copyright notice, this list of conditions and the
following disclaimer.
2. Redistributions in binary form must reproduce the above copyright notice, this list of conditions and the
following disclaimer in the documentation and/or other materials provided with the distribution.
THIS SOFTWARE IS PROVIDED BY THE AUTHOR AND CONTRIBUTORS “AS IS” AND ANY
EXPRESS OR IMPLIED WARRANTIES, INCLUDING, BUT NOT LIMITED TO, THE IMPLIED
WARRANTIES OF MERCHANTABILITY AND FITNESS FOR A PARTICULAR PURPOSE ARE
DISCLAIMED. IN NO EVENT SHALL THE AUTHOR OR CONTRIBUTORS BE LIABLE FOR ANY
DIRECT, INDIRECT, INCIDENTAL, SPECIAL, EXEMPLARY, OR CONSEQUENTIAL DAMAGES
(INCLUDING, BUT NOT LIMITED TO, PROCUREMENT OF SUBSTITUTE GOODS OR SERVICES;
LOSS OF USE, DATA, OR PROFITS; OR BUSINESS INTERRUPTION) HOWEVER CAUSED AND ON
ANY THEORY OF LIABILITY, WHETHER IN CONTRACT, STRICT LIABILITY, OR TORT (INCLUDING
NEGLIGENCE OR OTHERWISE) ARISING IN ANY WAY OUT OF THE USE OF THIS SOFTWARE,
EVEN IF ADVISED OF THE POSSIBILITY OF SUCH DAMAGE.
(17) S. L. Moshier
Author: S. L. Moshier.
Copyright (c) 1984,2000 S.L. Moshier
Permission to use, copy, modify, and distribute this software for any purpose without fee is hereby granted,
provided that this entire notice is included in all copies of any software which is or includes a copy or
modification of this software and in all copies of the supporting documentation for such software.
THIS SOFTWARE IS BEING PROVIDED “AS IS”, WITHOUT ANY EXPRESS OR IMPLIED WARRANTY.
IN PARTICULAR, THE AUTHOR MAKES NO REPRESENTATION OR WARRANTY OF ANY KIND
CONCERNING THE MERCHANTABILITY OF THIS SOFTWARE OR ITS FITNESS FOR ANY
PARTICULAR PURPOSE.
(18) Citrus Project
Copyright (c)1999 Citrus Project, All rights reserved.
Redistribution and use in source and binary forms, with or without modification, are permitted provided that
the following conditions are met:
1. Redistributions of source code must retain the above copyright notice, this list of conditions and the
following disclaimer.
2. Redistributions in binary form must reproduce the above copyright notice, this list of conditions and the
following disclaimer in the documentation and/or other materials provided with the distribution.
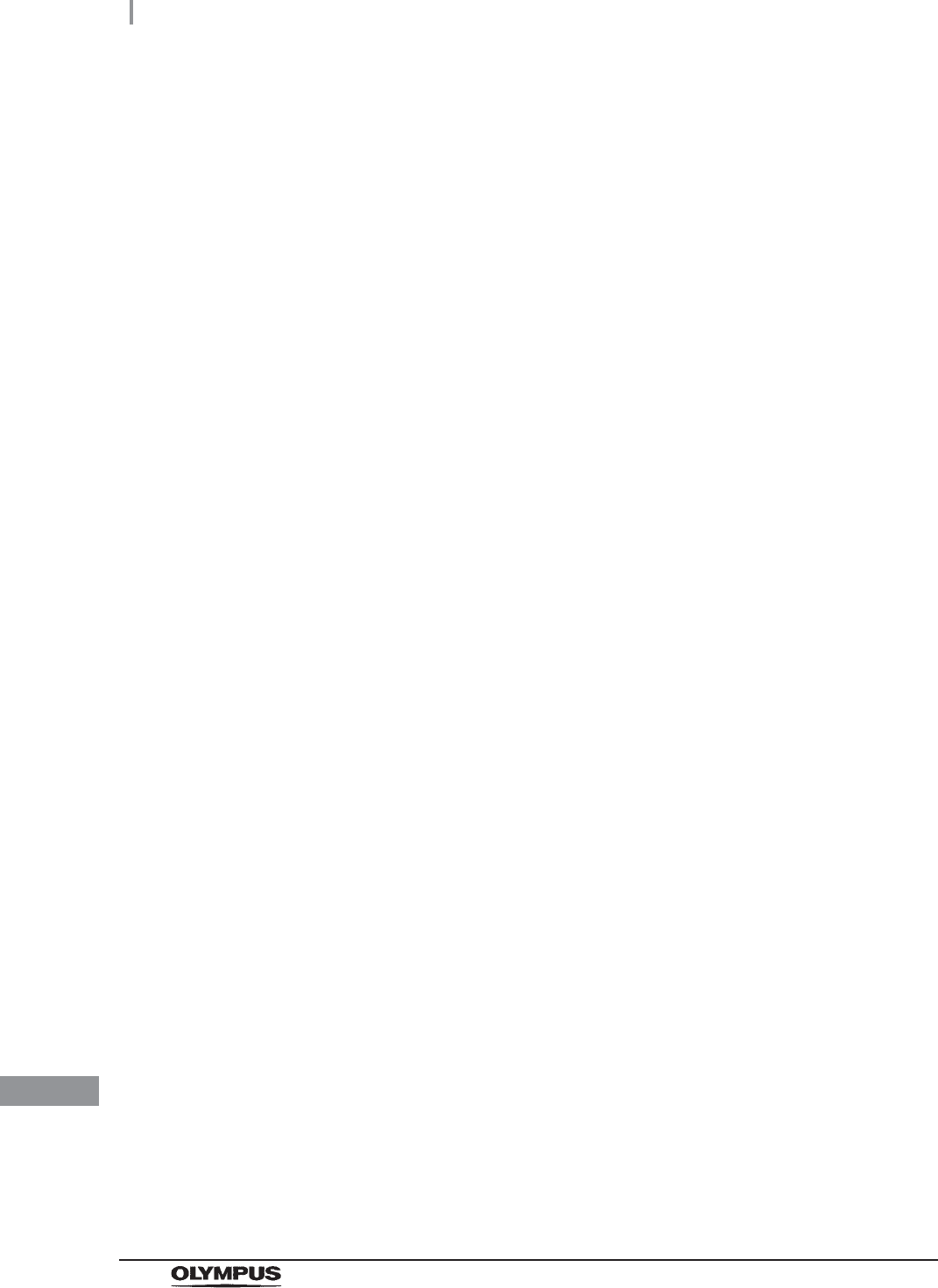
App.
678
License information of Open Source Software
OER-Elite OPERATION MANUAL
THIS SOFTWARE IS PROVIDED BY THE AUTHOR AND CONTRIBUTORS “AS IS” AND ANY
EXPRESS OR IMPLIED WARRANTIES, INCLUDING, BUT NOT LIMITED TO, THE IMPLIED
WARRANTIES OF MERCHANTABILITY AND FITNESS FOR A PARTICULAR PURPOSE ARE
DISCLAIMED. IN NO EVENT SHALL THE AUTHOR OR CONTRIBUTORS BE LIABLE FOR ANY
DIRECT, INDIRECT, INCIDENTAL, SPECIAL, EXEMPLARY, OR CONSEQUENTIAL DAMAGES
(INCLUDING, BUT NOT LIMITED TO, PROCUREMENT OF SUBSTITUTE GOODS OR SERVICES;
LOSS OF USE, DATA, OR PROFITS; OR BUSINESS INTERRUPTION) HOWEVER CAUSED AND ON
ANY THEORY OF LIABILITY, WHETHER IN CONTRACT, STRICT LIABILITY, OR TORT (INCLUDING
NEGLIGENCE OR OTHERWISE) ARISING IN ANY WAY OUT OF THE USE OF THIS SOFTWARE,
EVEN IF ADVISED OF THE POSSIBILITY OF SUCH DAMAGE.
(19) Todd C. Miller
Copyright (c) 1998 Todd C. Miller <Todd.Miller@courtesan.com>
All rights reserved.
Redistribution and use in source and binary forms, with or without modification, are permitted provided that
the following conditions are met:
1. Redistributions of source code must retain the above copyright notice, this list of conditions and the
following disclaimer.
2. Redistributions in binary form must reproduce the above copyright notice, this list of conditions and the
following disclaimer in the documentation and/or other materials provided with the distribution.
3. The name of the author may not be used to endorse or promote products derived from this software
without specific prior written permission.
THIS SOFTWARE IS PROVIDED “AS IS” AND ANY EXPRESS OR IMPLIED WARRANTIES,
INCLUDING, BUT NOT LIMITED TO, THE IMPLIED WARRANTIES OF MERCHANTABILITY AND
FITNESS FOR A PARTICULAR PURPOSE ARE DISCLAIMED. IN NO EVENT SHALL THE AUTHOR BE
LIABLE FOR ANY DIRECT, INDIRECT, INCIDENTAL, SPECIAL, EXEMPLARY, OR CONSEQUENTIAL
DAMAGES (INCLUDING, BUT NOT LIMITED TO, PROCUREMENT OF SUBSTITUTE GOODS OR
SERVICES; LOSS OF USE, DATA, OR PROFITS; OR BUSINESS INTERRUPTION) HOWEVER
CAUSED AND ON ANY THEORY OF LIABILITY, WHETHER IN CONTRACT, STRICT LIABILITY, OR
TORT (INCLUDING NEGLIGENCE OR OTHERWISE) ARISING IN ANY WAY OUT OF THE USE OF
THIS SOFTWARE, EVEN IF ADVISED OF THE POSSIBILITY OF SUCH DAMAGE.
(26) Mike Barcroft
Copyright (c) 2001 Mike Barcroft <mike@FreeBSD.org>
All rights reserved.
Redistribution and use in source and binary forms, with or without modification, are permitted provided that
the following conditions are met:
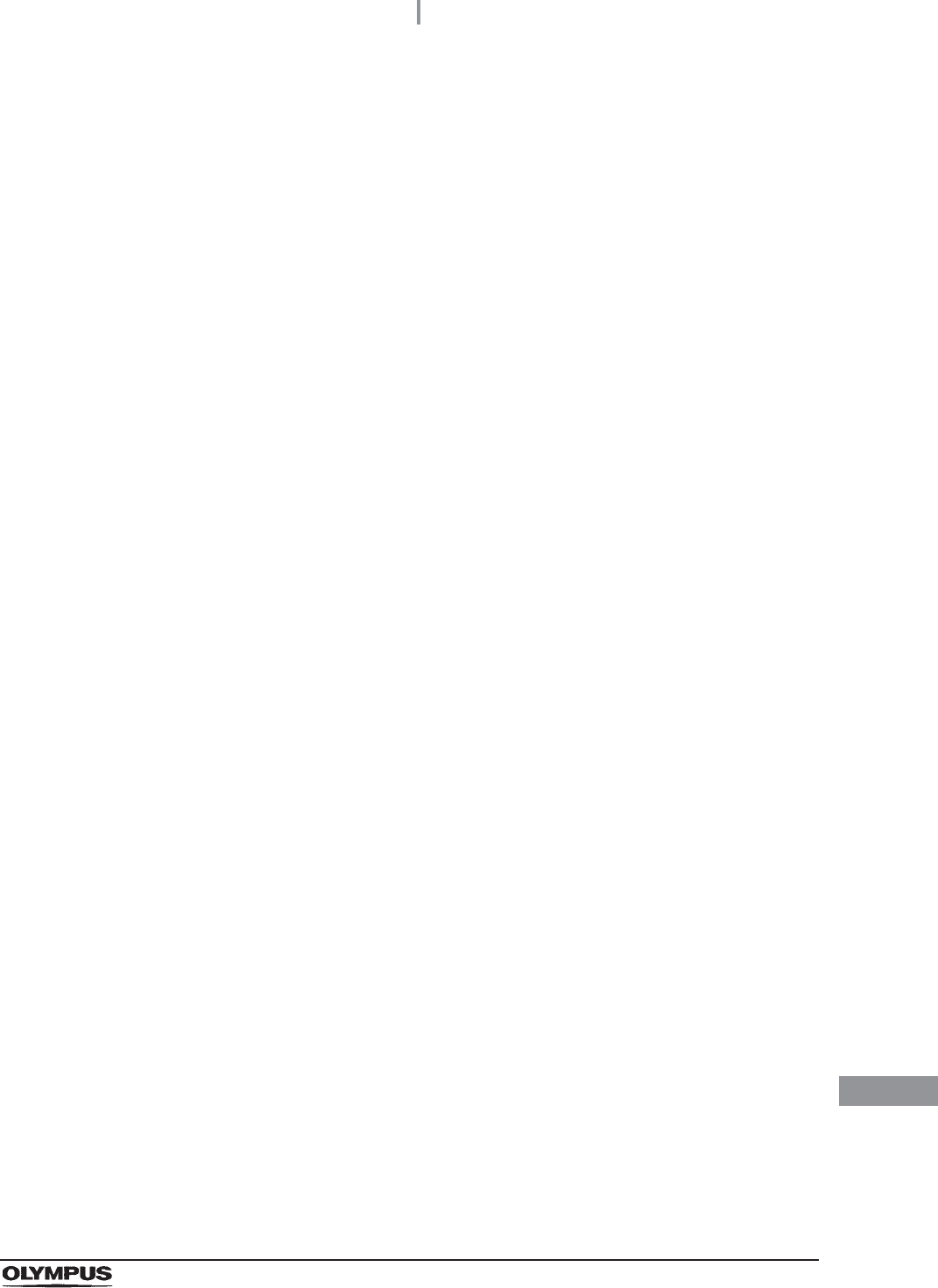
App.
License information of Open Source Software
679
OER-Elite OPERATION MANUAL
1. Redistributions of source code must retain the above copyright notice, this list of conditions and the
following disclaimer.
2. Redistributions in binary form must reproduce the above copyright notice, this list of conditions and the
following disclaimer in the documentation and/or other materials provided with the distribution.
THIS SOFTWARE IS PROVIDED BY THE AUTHOR AND CONTRIBUTORS “AS IS” AND ANY
EXPRESS OR IMPLIED WARRANTIES, INCLUDING, BUT NOT LIMITED TO, THE IMPLIED
WARRANTIES OF MERCHANTABILITY AND FITNESS FOR A PARTICULAR PURPOSE ARE
DISCLAIMED. IN NO EVENT SHALL THE AUTHOR OR CONTRIBUTORS BE LIABLE FOR ANY
DIRECT, INDIRECT, INCIDENTAL, SPECIAL, EXEMPLARY, OR CONSEQUENTIAL DAMAGES
(INCLUDING, BUT NOT LIMITED TO, PROCUREMENT OF SUBSTITUTE GOODS OR SERVICES;
LOSS OF USE, DATA, OR PROFITS; OR BUSINESS INTERRUPTION) HOWEVER CAUSED AND ON
ANY THEORY OF LIABILITY, WHETHER IN CONTRACT, STRICT LIABILITY, OR TORT (INCLUDING
NEGLIGENCE OR OTHERWISE) ARISING IN ANY WAY OUT OF THE USE OF THIS SOFTWARE,
EVEN IF ADVISED OF THE POSSIBILITY OF SUCH DAMAGE.
(35) - ARM Ltd (arm and thumb variant targets only)
Copyright (c) 2009 ARM Ltd
All rights reserved.
Redistribution and use in source and binary forms, with or without modification, are permitted provided
that the following conditions are met:
1. Redistributions of source code must retain the above copyright notice, this list of conditions and the
following disclaimer.
2. Redistributions in binary form must reproduce the above copyright notice, this list of conditions and the
following disclaimer in the documentation and/or other materials provided with the distribution.
3. The name of the company may not be used to endorse or promote products derived from this software
without specific prior written permission.
THIS SOFTWARE IS PROVIDED BY ARM LTD “AS IS” AND ANY EXPRESS OR IMPLIED
WARRANTIES, INCLUDING, BUT NOT LIMITED TO, THE IMPLIED WARRANTIES OF
MERCHANTABILITY AND FITNESS FOR A PARTICULAR PURPOSE ARE DISCLAIMED.
IN NO EVENT SHALL ARM LTD BE LIABLE FOR ANY DIRECT, INDIRECT, INCIDENTAL, SPECIAL,
EXEMPLARY, OR CONSEQUENTIAL DAMAGES (INCLUDING, BUT NOT LIMITED TO,
PROCUREMENT OF SUBSTITUTE GOODS OR SERVICES; LOSS OF USE, DATA, OR PROFITS; OR
BUSINESS INTERRUPTION) HOWEVER CAUSED AND ON ANY THEORY OF LIABILITY, WHETHER
IN CONTRACT, STRICT LIABILITY, OR TORT (INCLUDING NEGLIGENCE OR OTHERWISE) ARISING
IN ANY WAY OUT OF THE USE OF THIS SOFTWARE, EVEN IF ADVISED OF THE POSSIBILITY OF
SUCH DAMAGE.
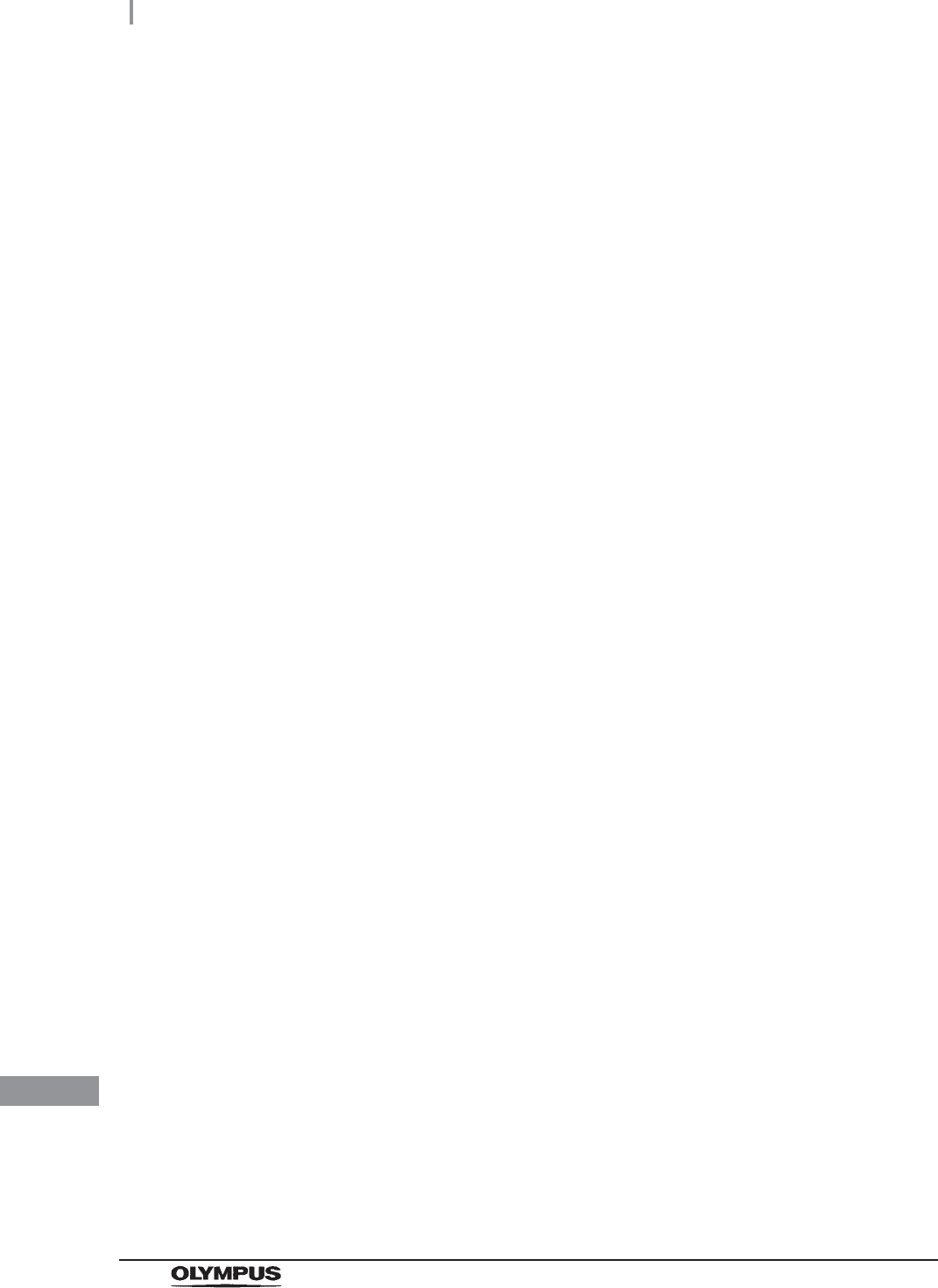
App.
680
License information of Open Source Software
OER-Elite OPERATION MANUAL
(41) Ed Schouten - Free BSD
Copyright (c) 2008 Ed Schouten <ed@FreeBSD.org>
All rights reserved.
Redistribution and use in source and binary forms, with or without modification, are permitted provided that
the following conditions are met:
1. Redistributions of source code must retain the above copyright notice, this list of conditions and the
following disclaimer.
2. Redistributions in binary form must reproduce the above copyright notice, this list of conditions and the
following disclaimer in the documentation and/or other materials provided with the distribution.
THIS SOFTWARE IS PROVIDED BY THE AUTHOR AND CONTRIBUTORS “AS IS” AND ANY
EXPRESS OR IMPLIED WARRANTIES, INCLUDING, BUT NOT LIMITED TO, THE IMPLIED
WARRANTIES OF MERCHANTABILITY AND FITNESS FOR A PARTICULAR PURPOSE ARE
DISCLAIMED. IN NO EVENT SHALL THE AUTHOR OR CONTRIBUTORS BE LIABLE FOR ANY
DIRECT, INDIRECT, INCIDENTAL, SPECIAL, EXEMPLARY, OR CONSEQUENTIAL DAMAGES
(INCLUDING, BUT NOT LIMITED TO, PROCUREMENT OF SUBSTITUTE GOODS OR SERVICES;
LOSS OF USE, DATA, OR PROFITS; OR BUSINESS INTERRUPTION)
HOWEVER CAUSED AND ON ANY THEORY OF LIABILITY, WHETHER IN CONTRACT, STRICT
LIABILITY, OR TORT (INCLUDING NEGLIGENCE OR OTHERWISE) ARISING IN ANY WAY OUT OF
THE USE OF THIS SOFTWARE, EVEN IF ADVISED OF THE POSSIBILITY OF SUCH DAMAGE.